CSW75
Monumental System Engineered For The Most Demanding Applications

- Unit heights up to 10′ 6″ (3200 mm) are possible
- Mix and match from three frameless system options
- Exterior capabilities
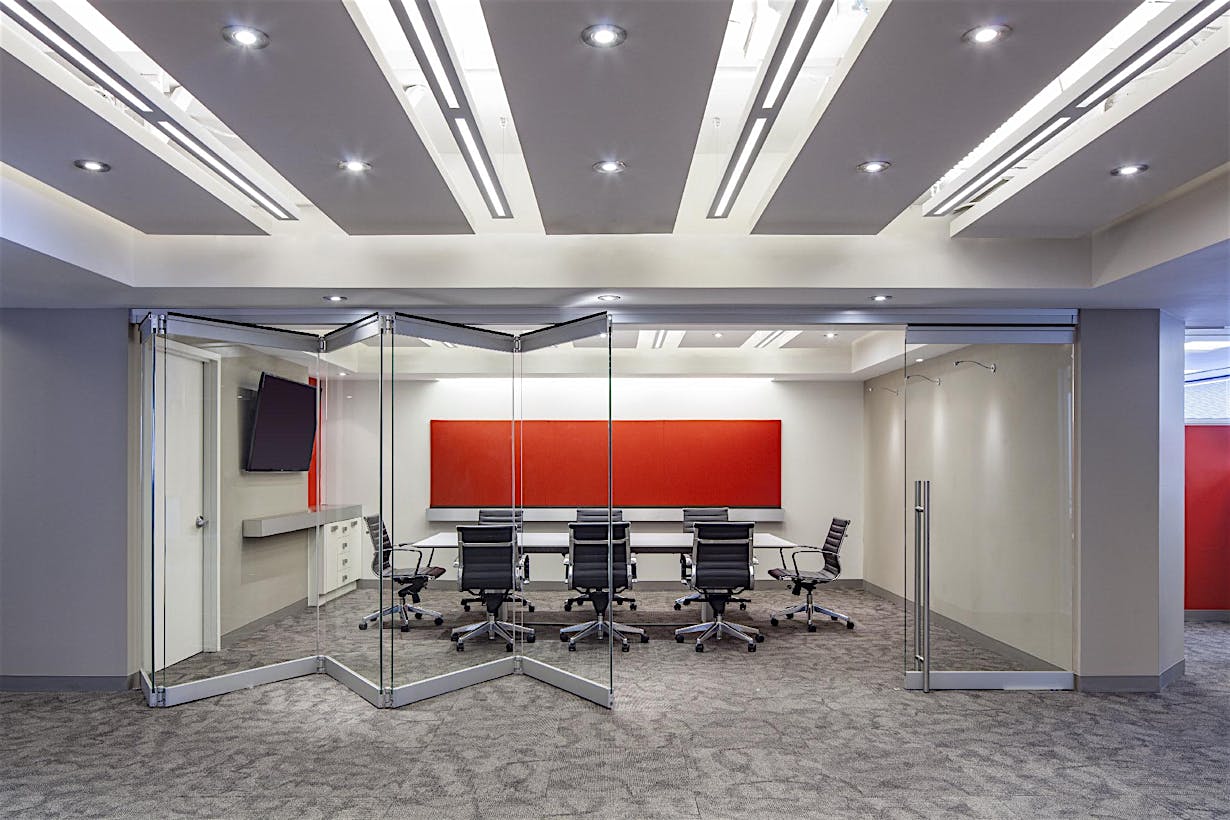
Frameless Center Pivot Folding Systems for Space Management
Create an unlimited span of top-hung center pivot folding panels with the addition of paired panels to optimize space management or to solve unique design challenges between support columns. CSW75 does not require the use of a floor track.
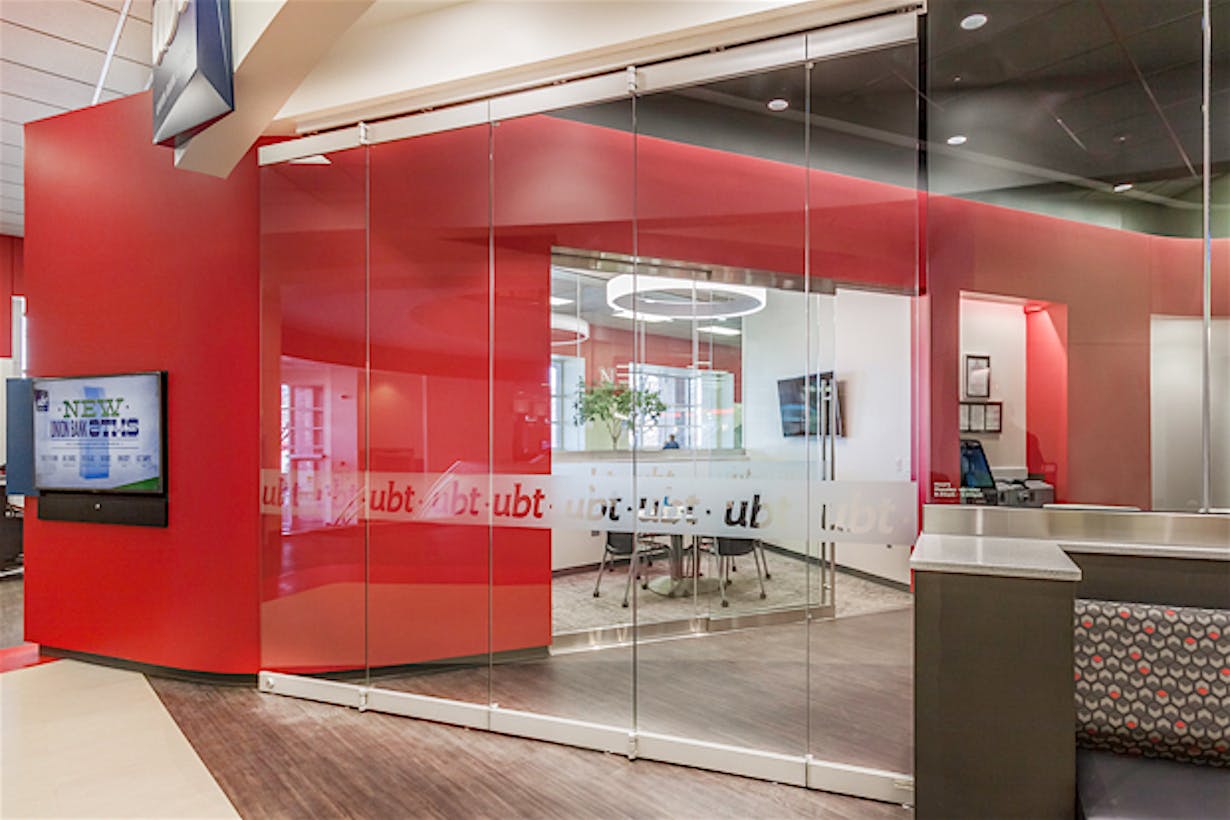
3 15/16" Continuous Rail for Outstanding Aesthetics
The CSW75 system comes standard with a 3 15/16" (100 mm) continuous top and bottom horizontal rail, allowing for a beautiful aesthetic and maximum glass. Customized rail options are available in increments of 3/16" (5mm) from 5 1/4" (133mm) to 7 13/16" (198mm). To meet ADA requirements, two options are offered: a 10" (254 mm) bottom rail or a 4 3/4" (120 mm) chamfer bottom rail.
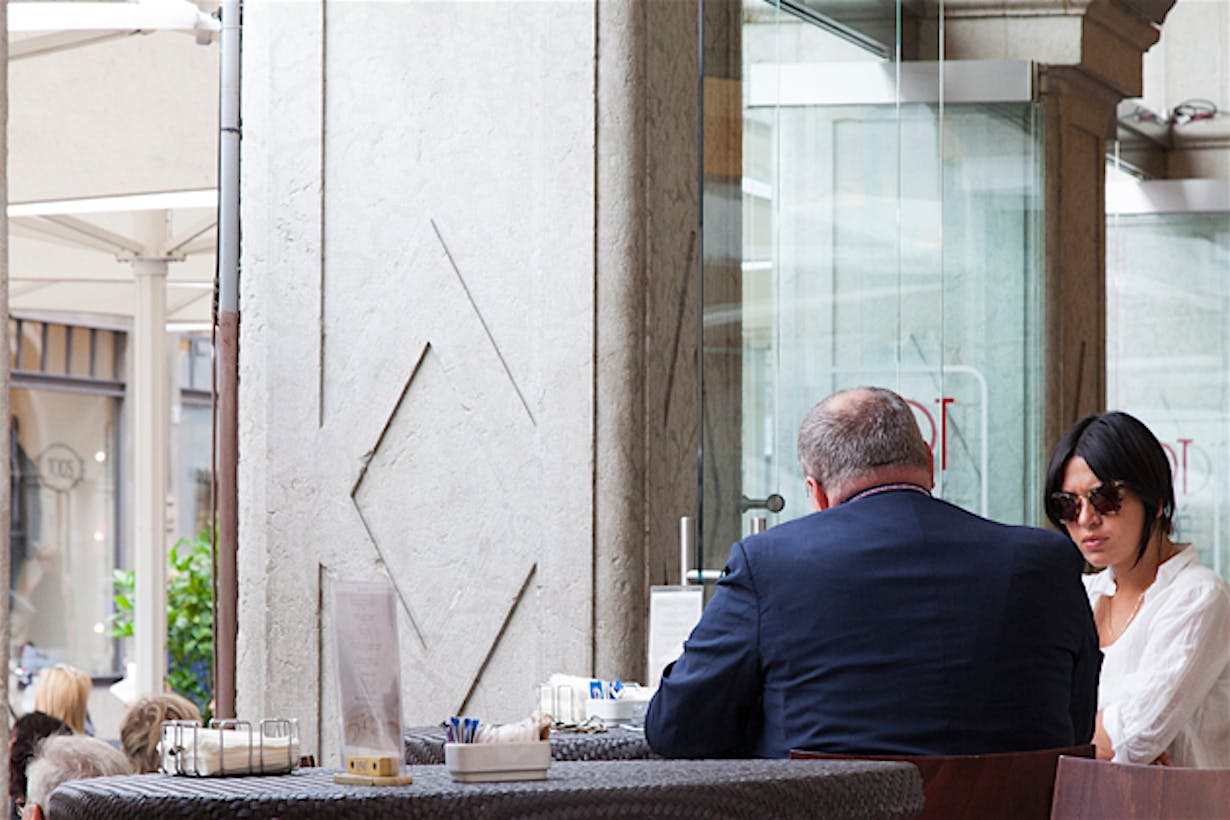
Exterior Capabilities
CSW75 can be used in exterior applications as a windbreak. Please note that at this time, CSW75 is not rated for air and water infiltration or acoustical performance.
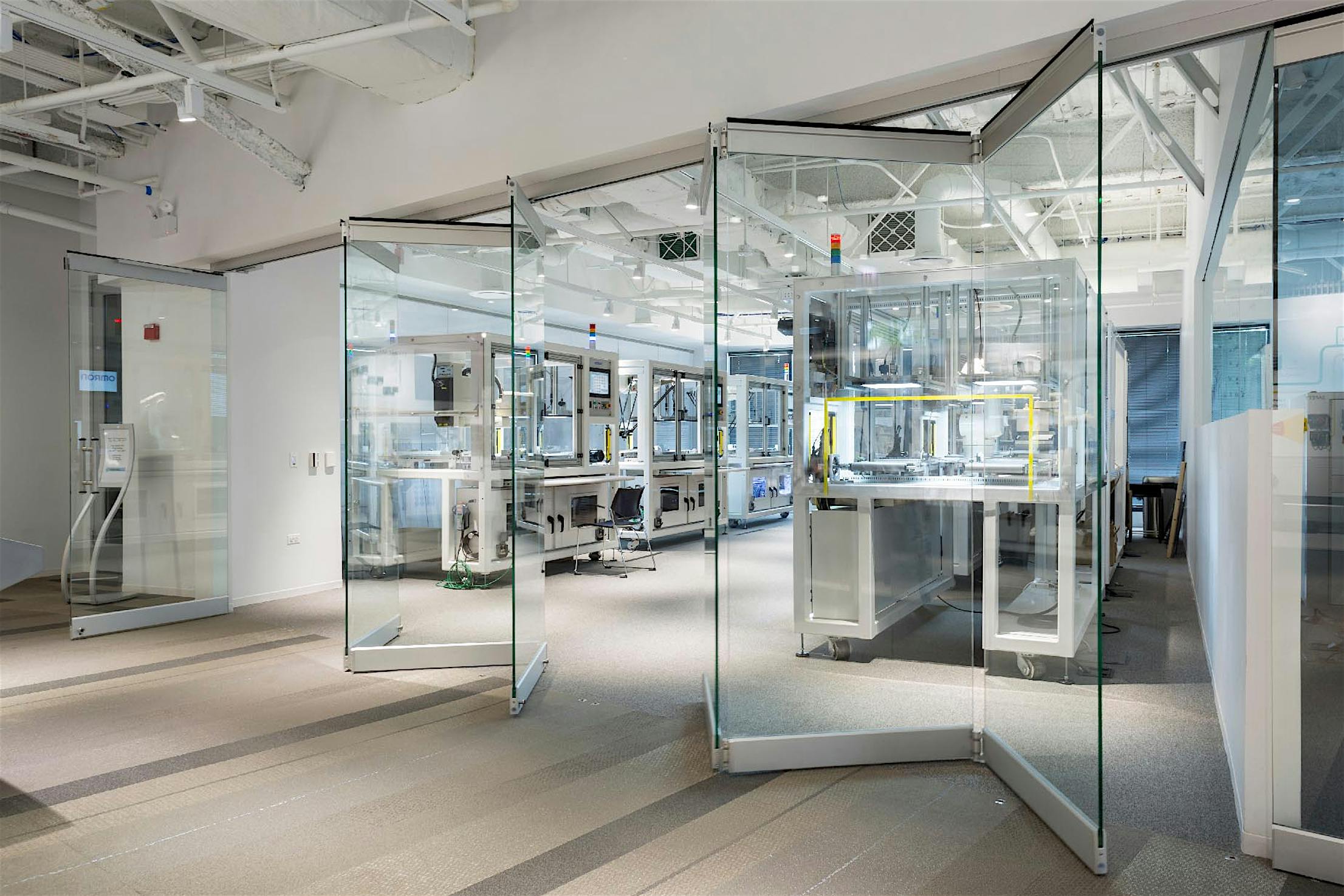
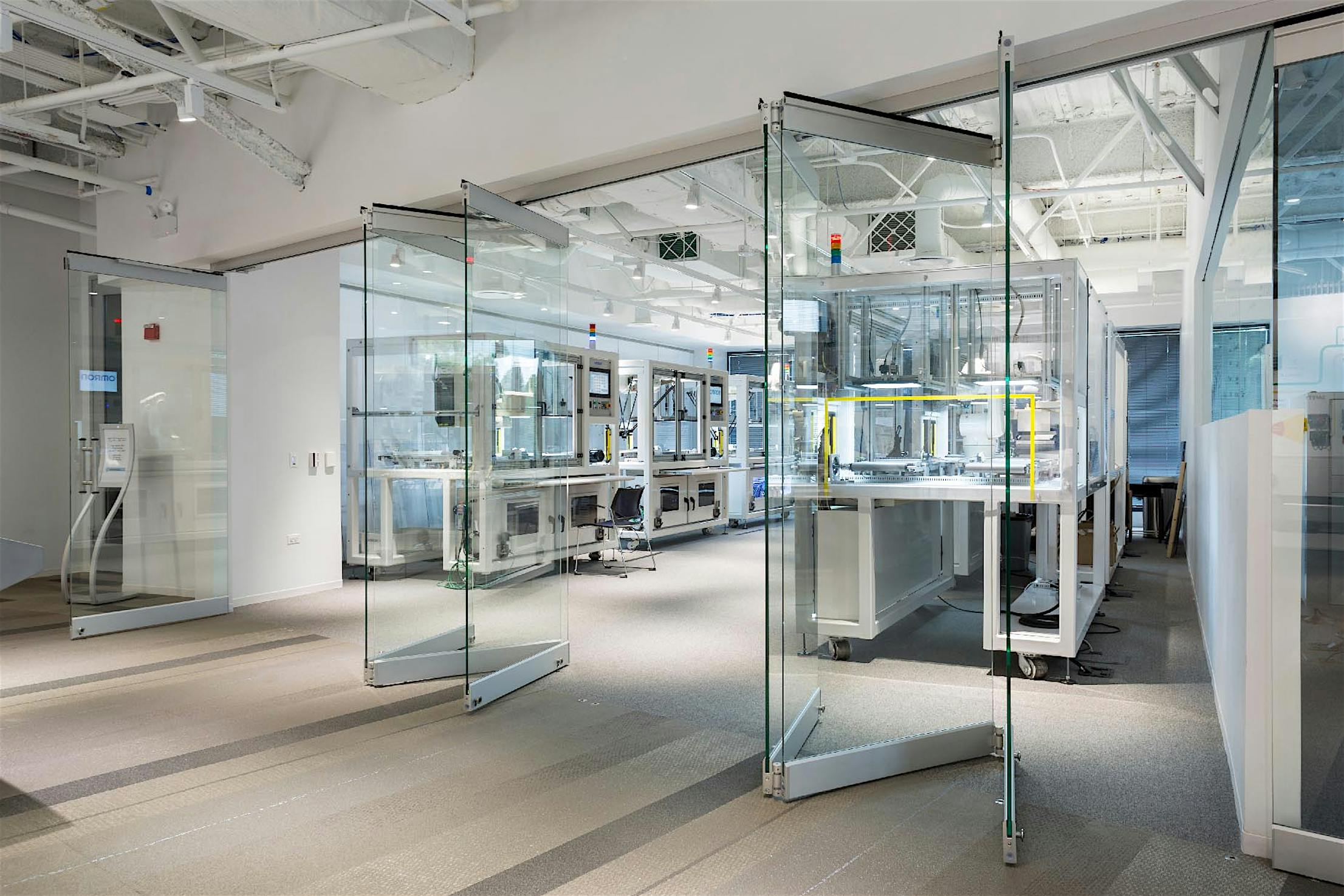
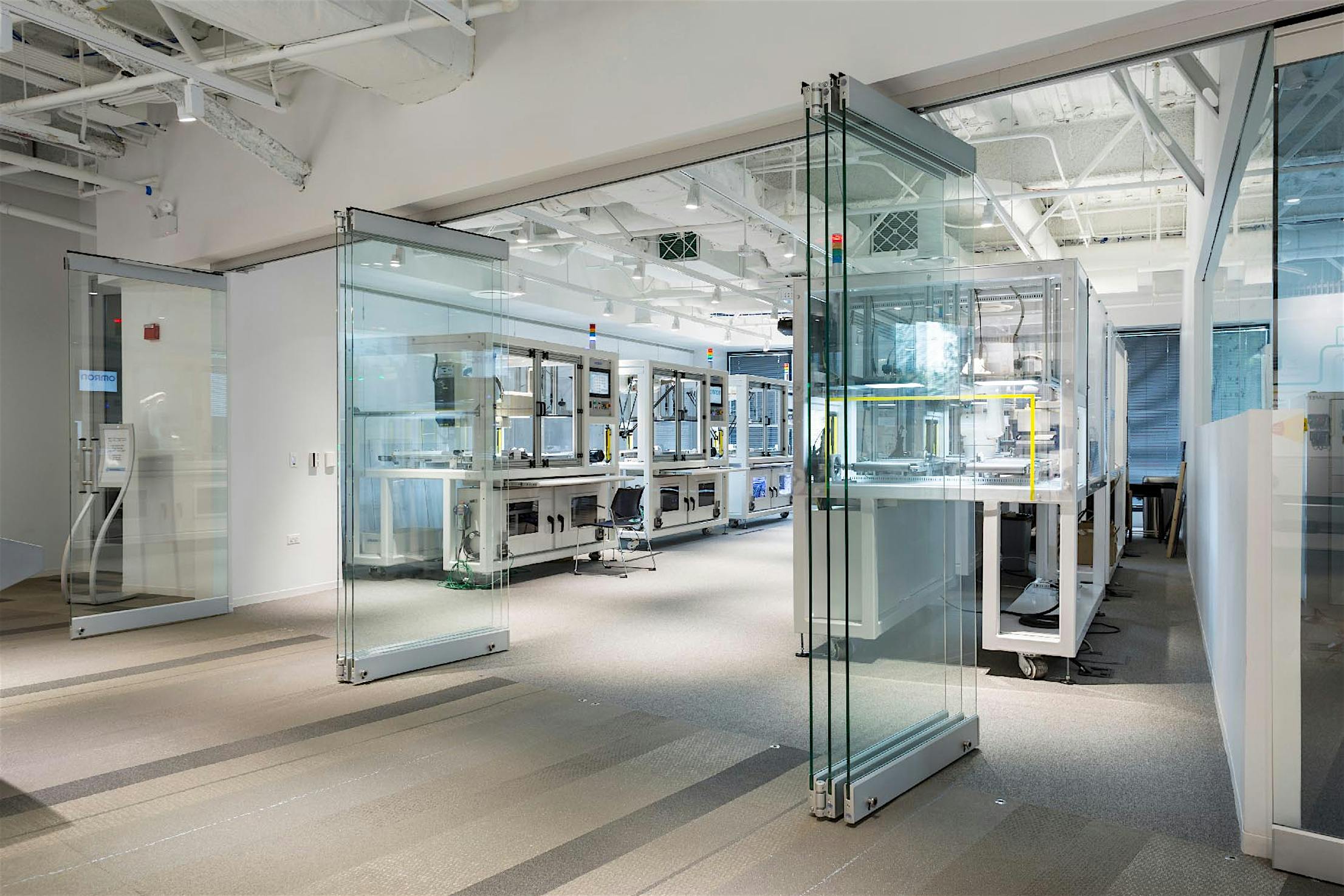
CSW75, FSW75, AND HSW75 combinations are possible. All three frameless systems utilize the same head track and share the same 3 15/16 (100mm) continuous top and bottom horizontal rails. Solve unique design challenges with three different systems that maintain the same continuous look.
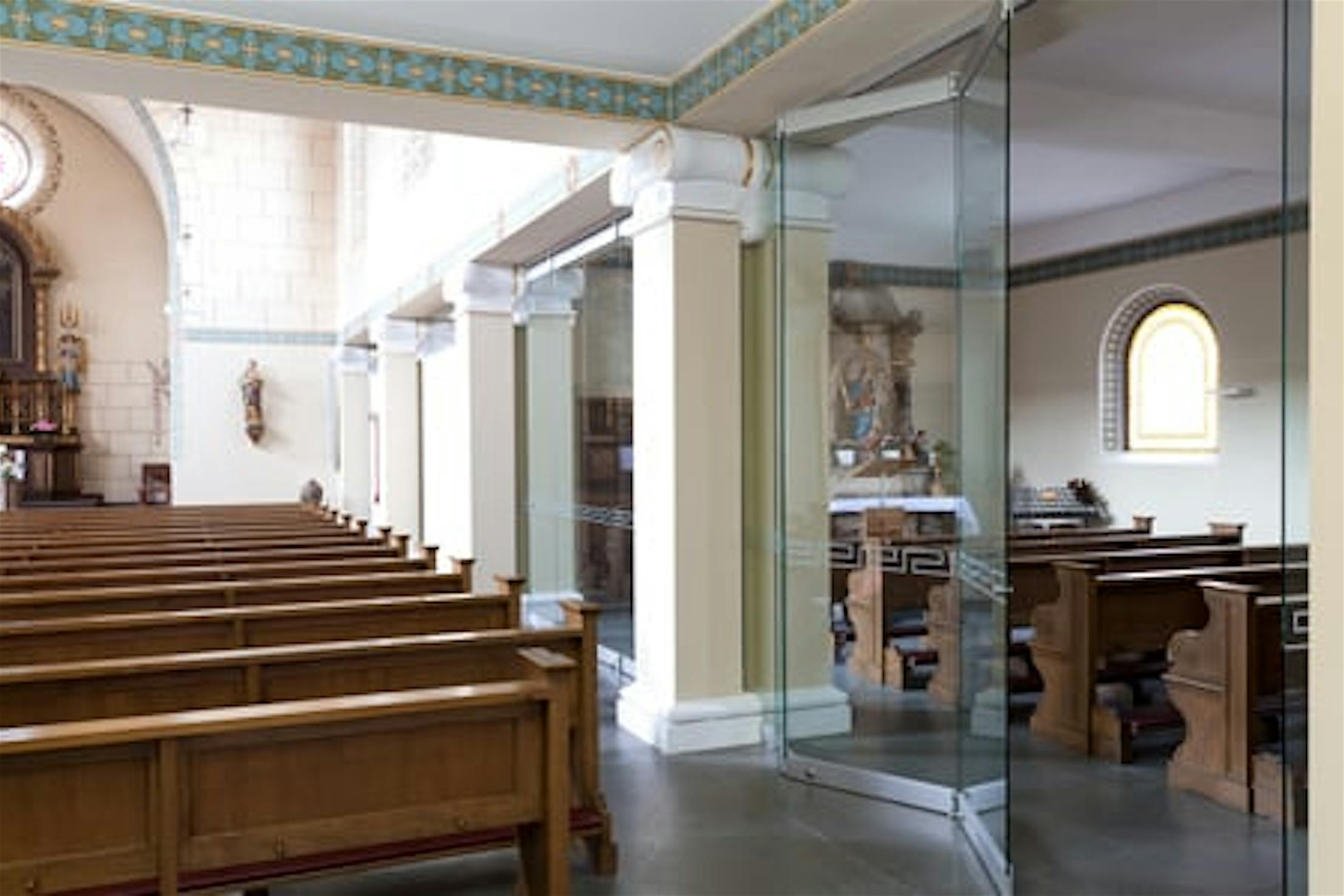
The rollers are designed using hardened steel ball bearings with glass fiber reinforced polyamide wheels with memory effect for quiet and smooth operation. Polyamide bumpers are added to each end of the roller to avoid metal to metal contact of the rollers inside the track.
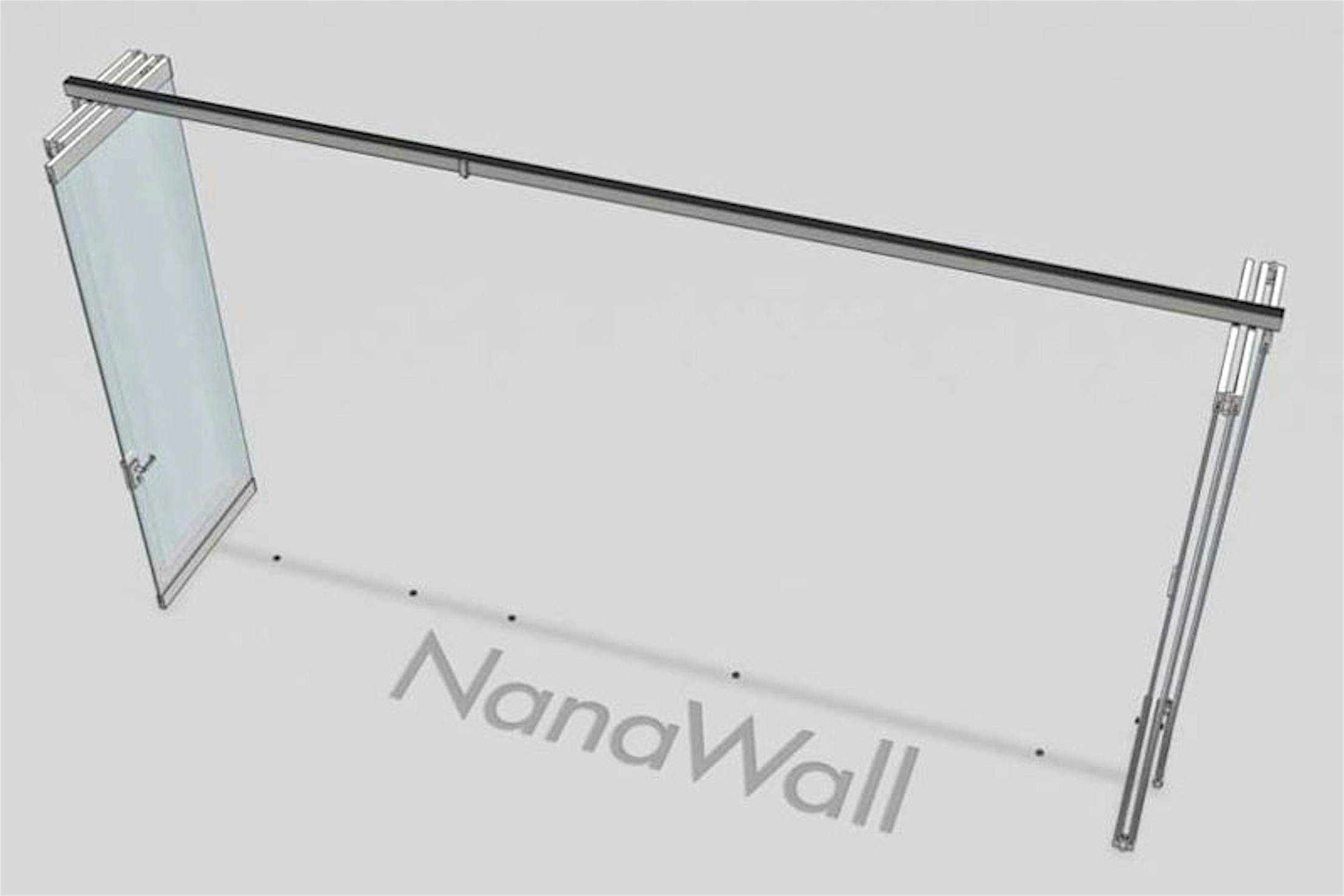
A single action swing panel is available attached to the end of a chain of panels that fold away along with the rest of the system. For additional traffic pattern requirements, a pair of single action swing panels can be added to function similarly to French doors.
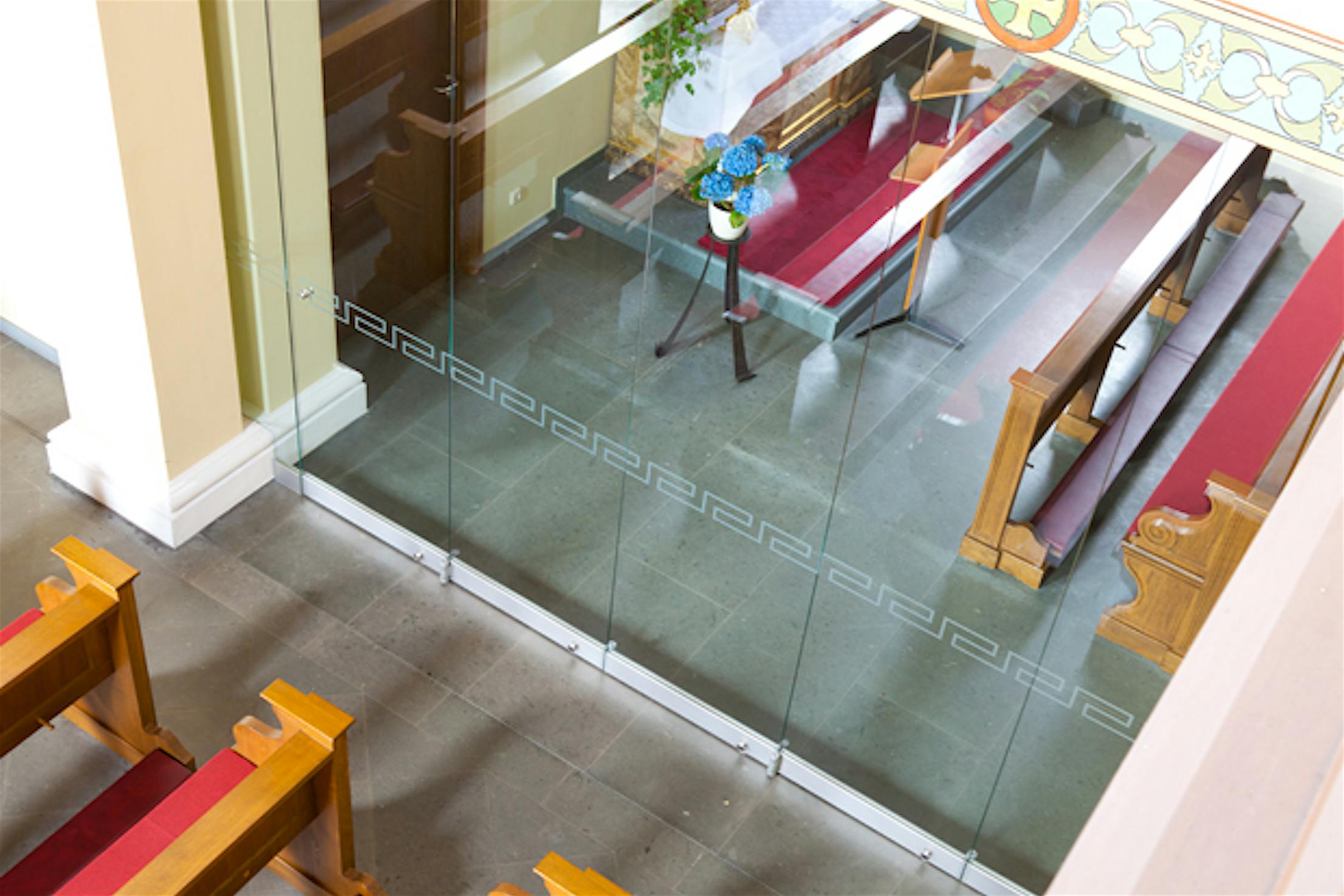
- Unit heights up to 10′ 6″ (3200 mm) are possible.
- Folding panels are available up to 3′ 3″ (1000 mm) in width.
- Single action panels hinged off bi-folding panels are available up to 3′ 3″ (1000 mm) in width.
- Non-sliding end single/double action panels are available up to 3′ 7″ (1100 mm) in width.
- End folding panel will be half the width of a folding panel.
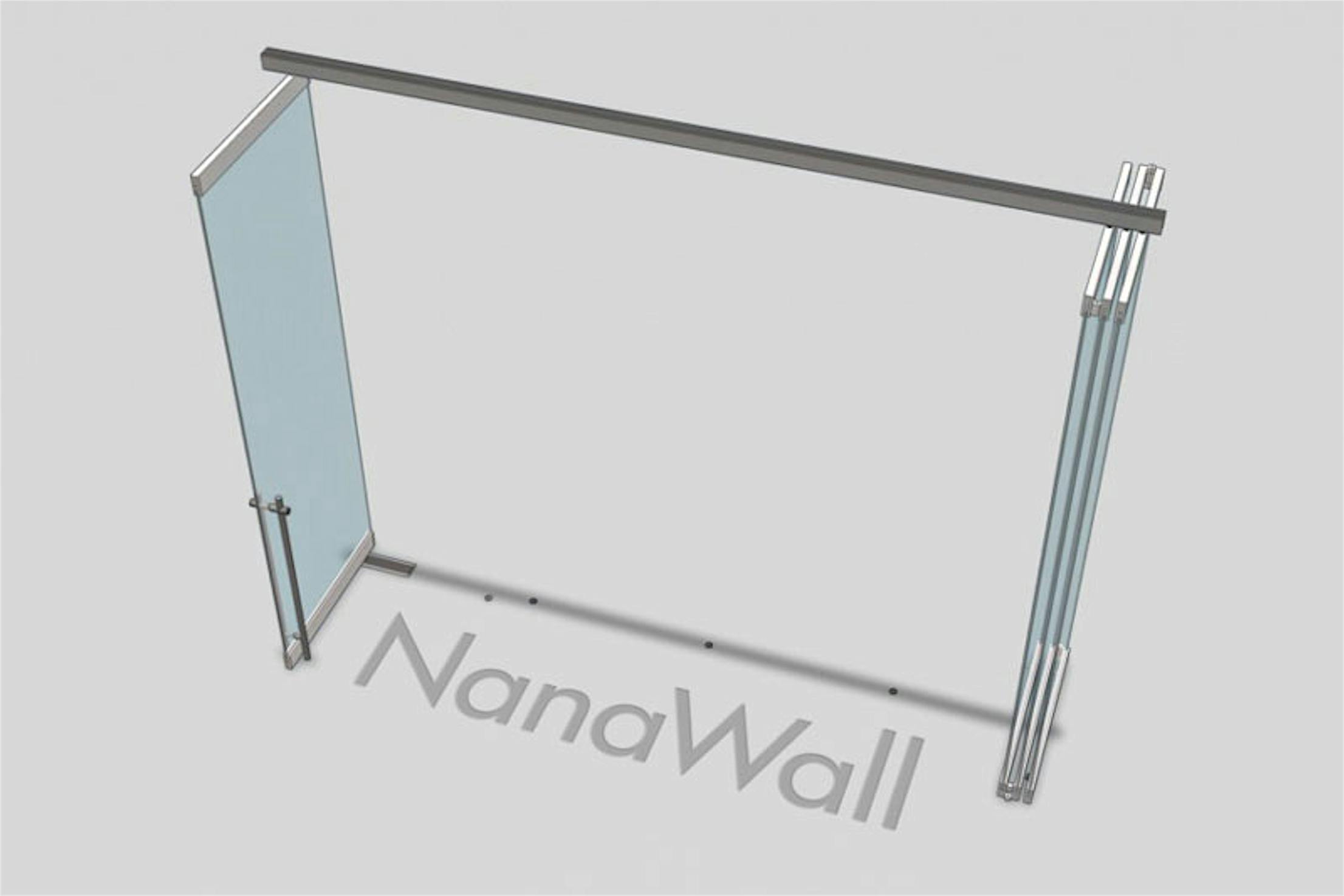
End panels can be single/double action panels with pivot points or single/double action panels with offset hinges that are capable of opening 180°. Single/double action panels with pivot points have passed 500,000 cycle testing.
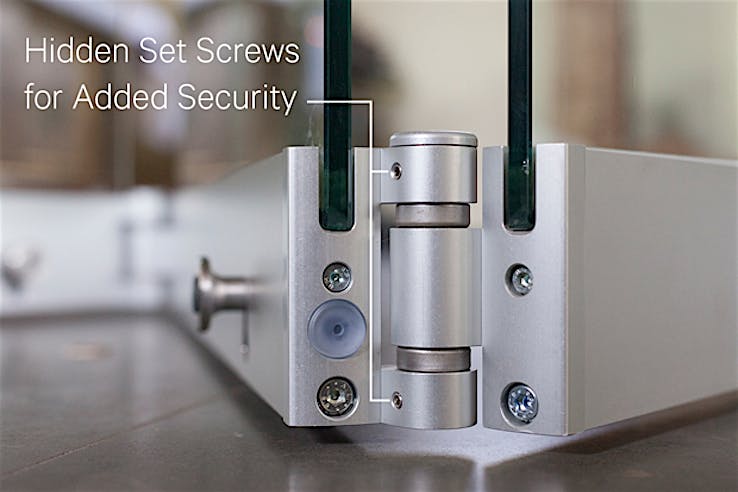
Added Security and Acoustical Buffering in an All Glass System
As a standard security measure, two hidden set screws per hinge are accessible only when the unit is in the open position. For projects requiring higher levels of security, or an increased acoustical barrier, NanaWall CSW75 can be configured with laminated glass.
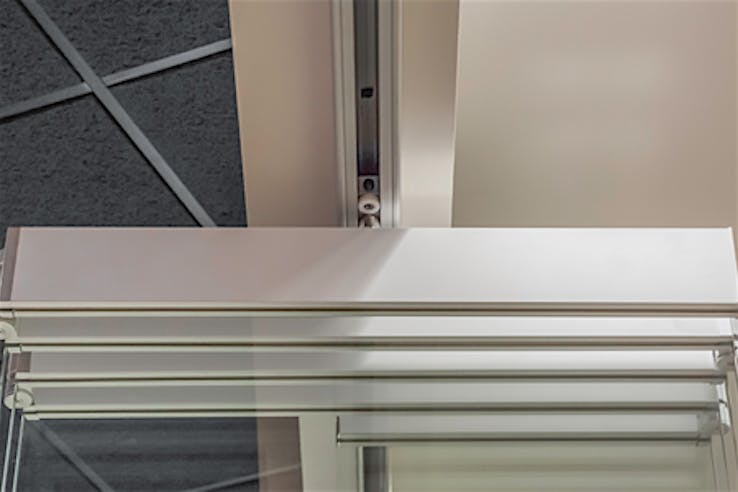
No Need for Additional Structural Support
With the CSW75 there is no need for additional structural support for the parking of the panels since parking remains within the plane of the opening.
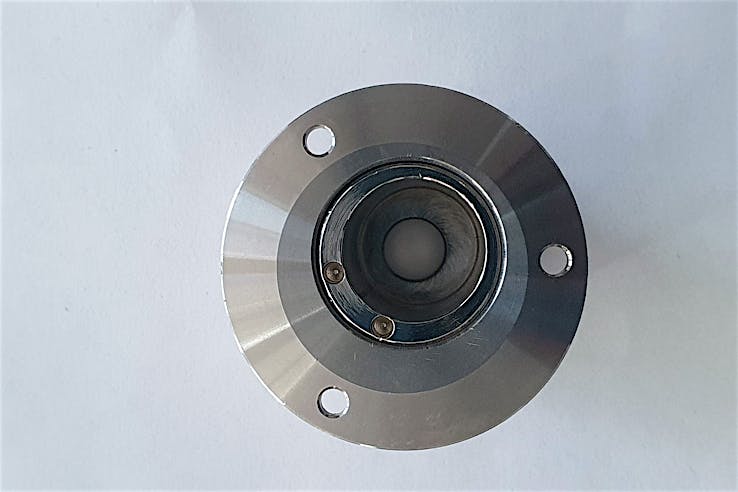
Adjustable Floor Sockets
Standard to the CSW75 are eccentric floor sockets. The built-in adjustability helps to deal with tolerances and building settlements.
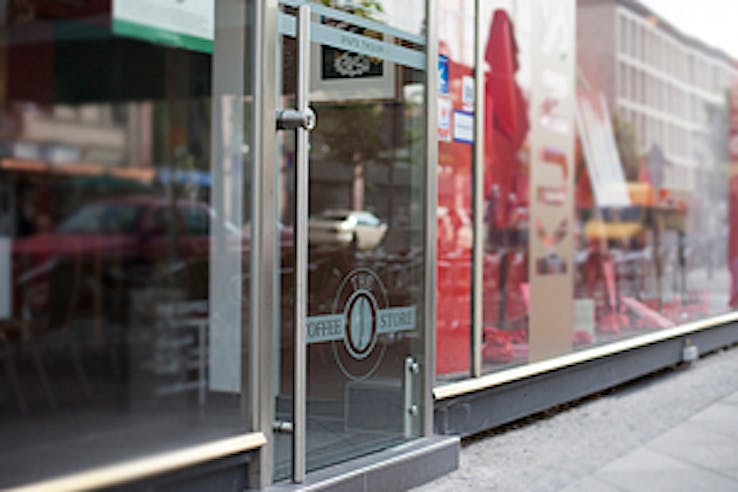
Convenient Handle Height Locking
An optional locking ladder pull integrates a locking mechanism with a profile cylinder at hand height into the tubular designed handle eliminating the need to kneel to lock the door at the bottom rail. Locking ladder pulls come in a brushed stainless steel finish.
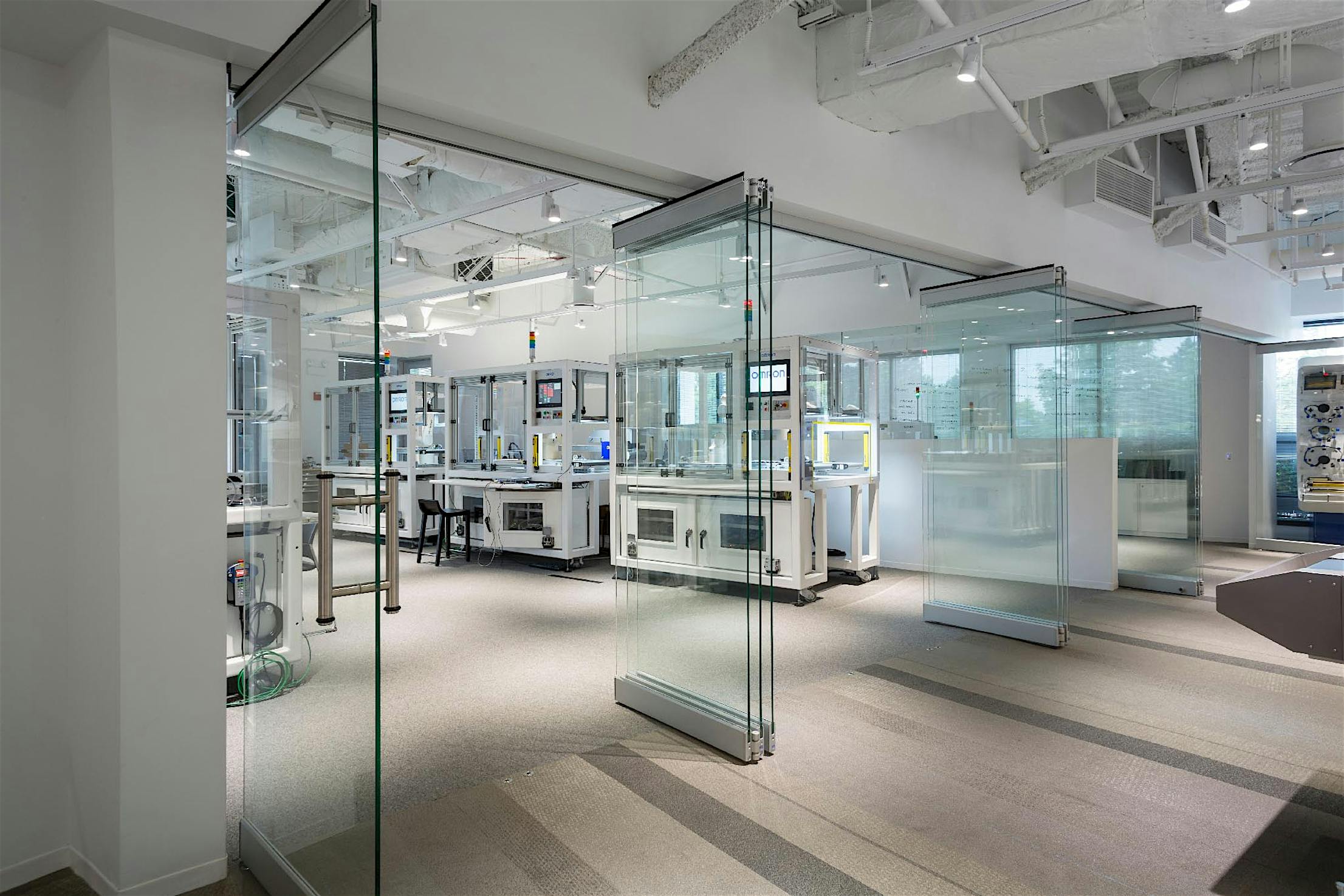
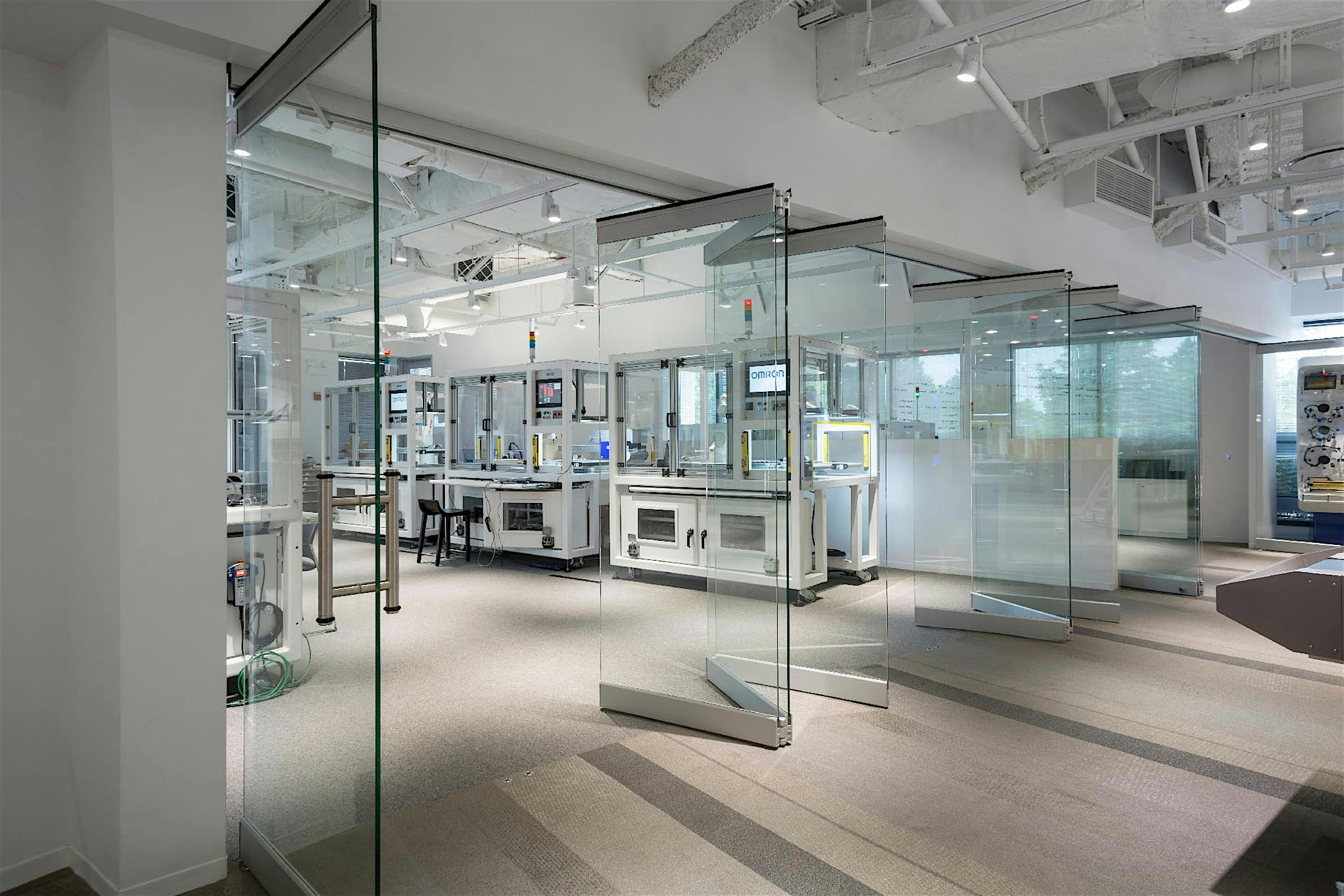
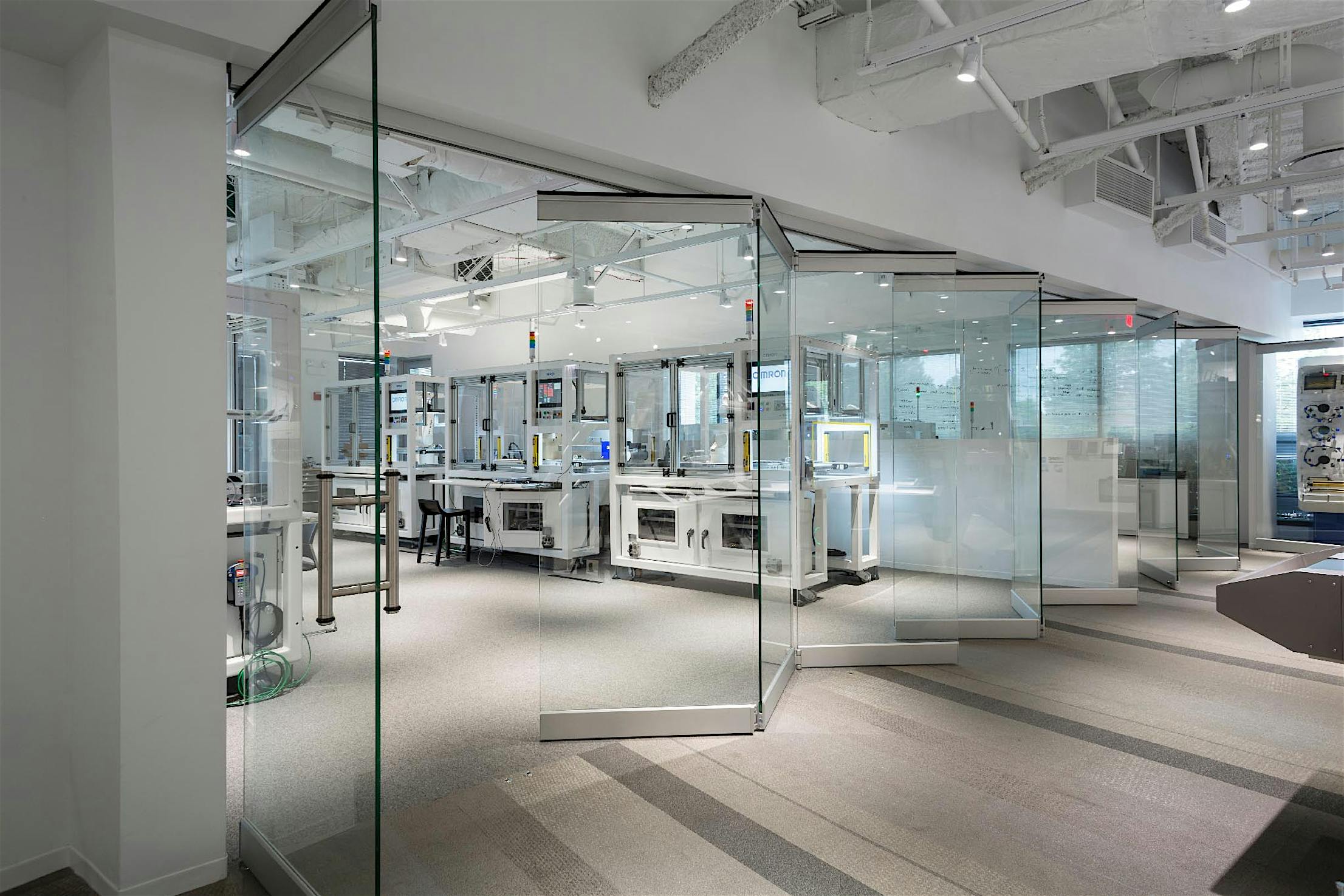

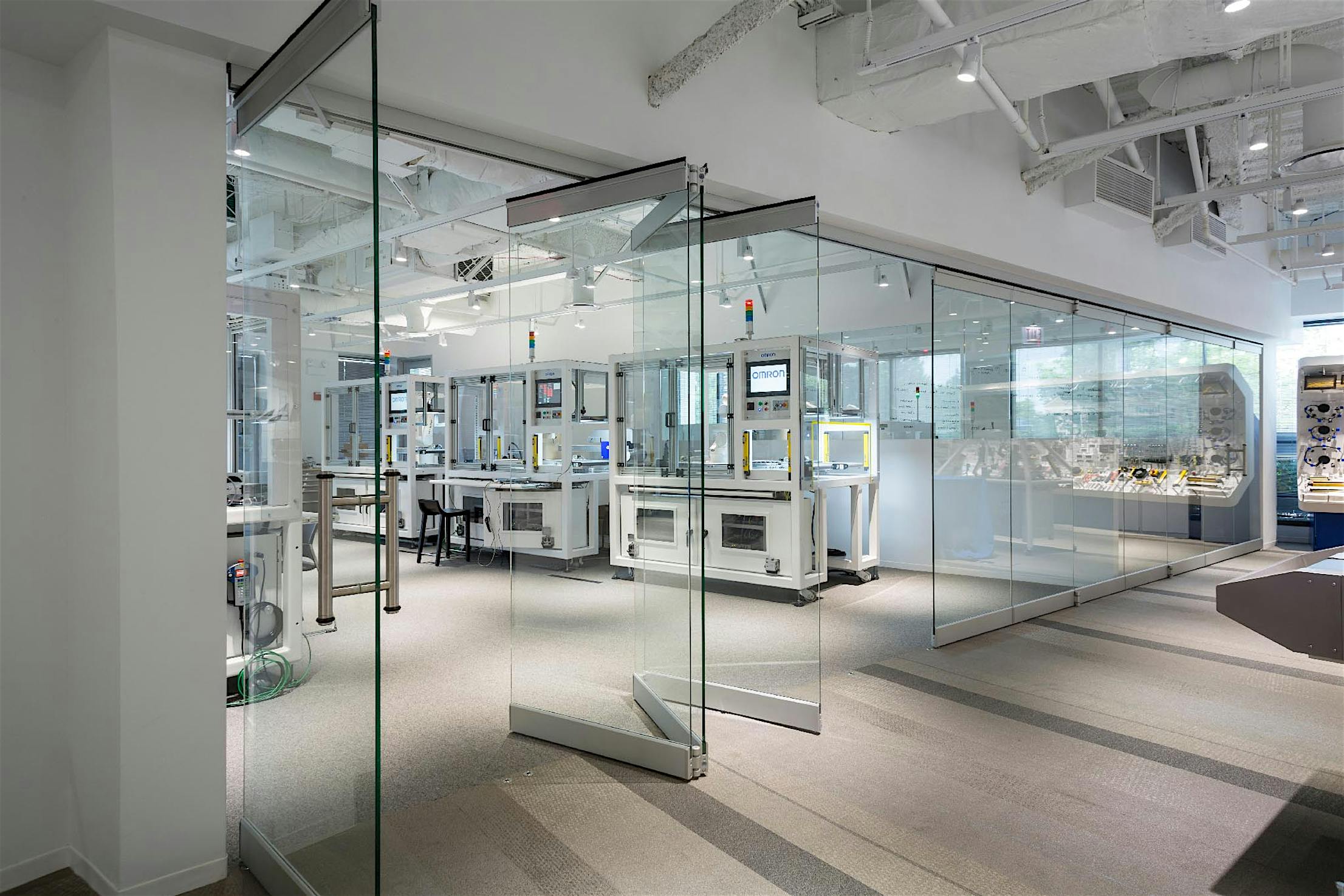
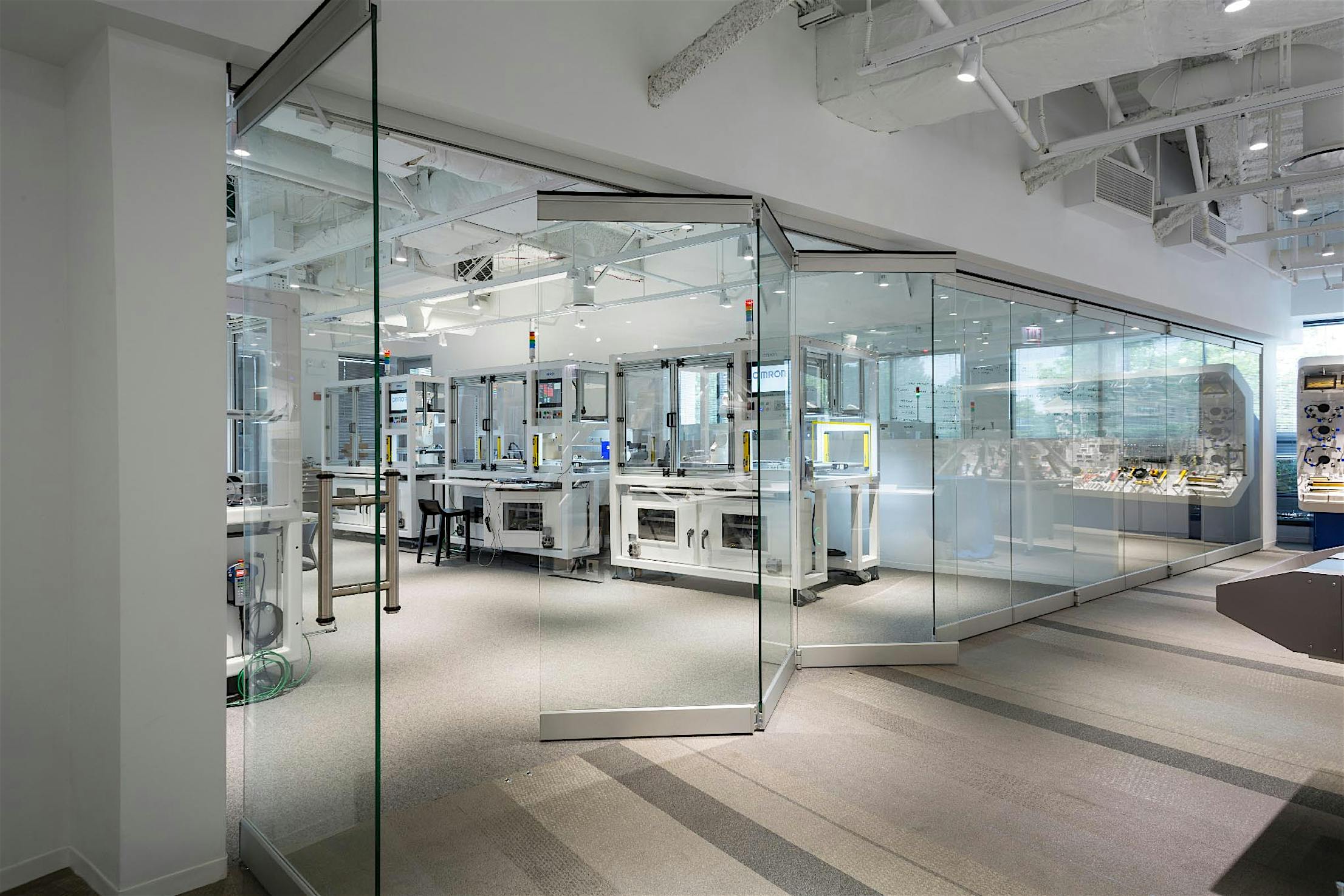
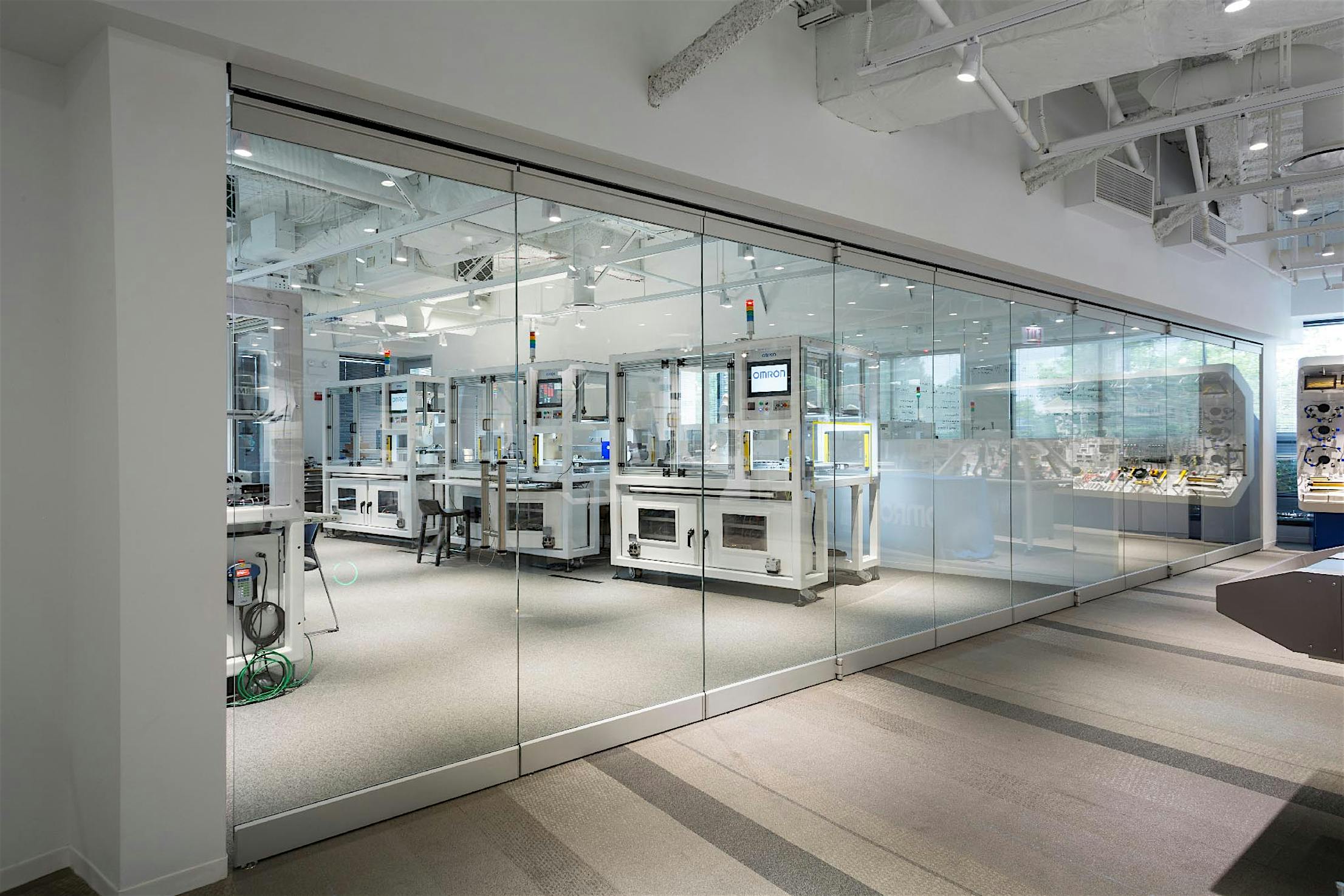
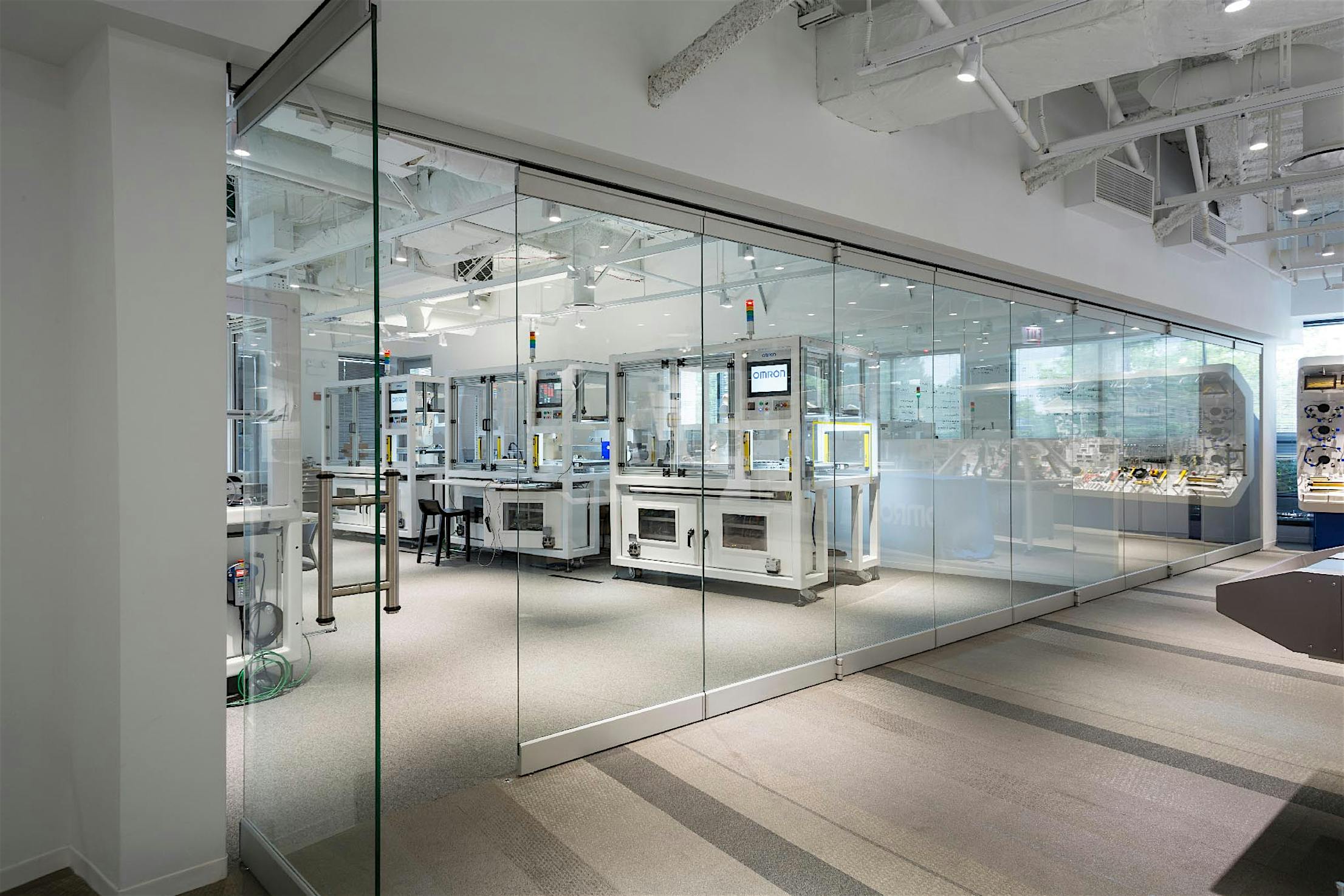
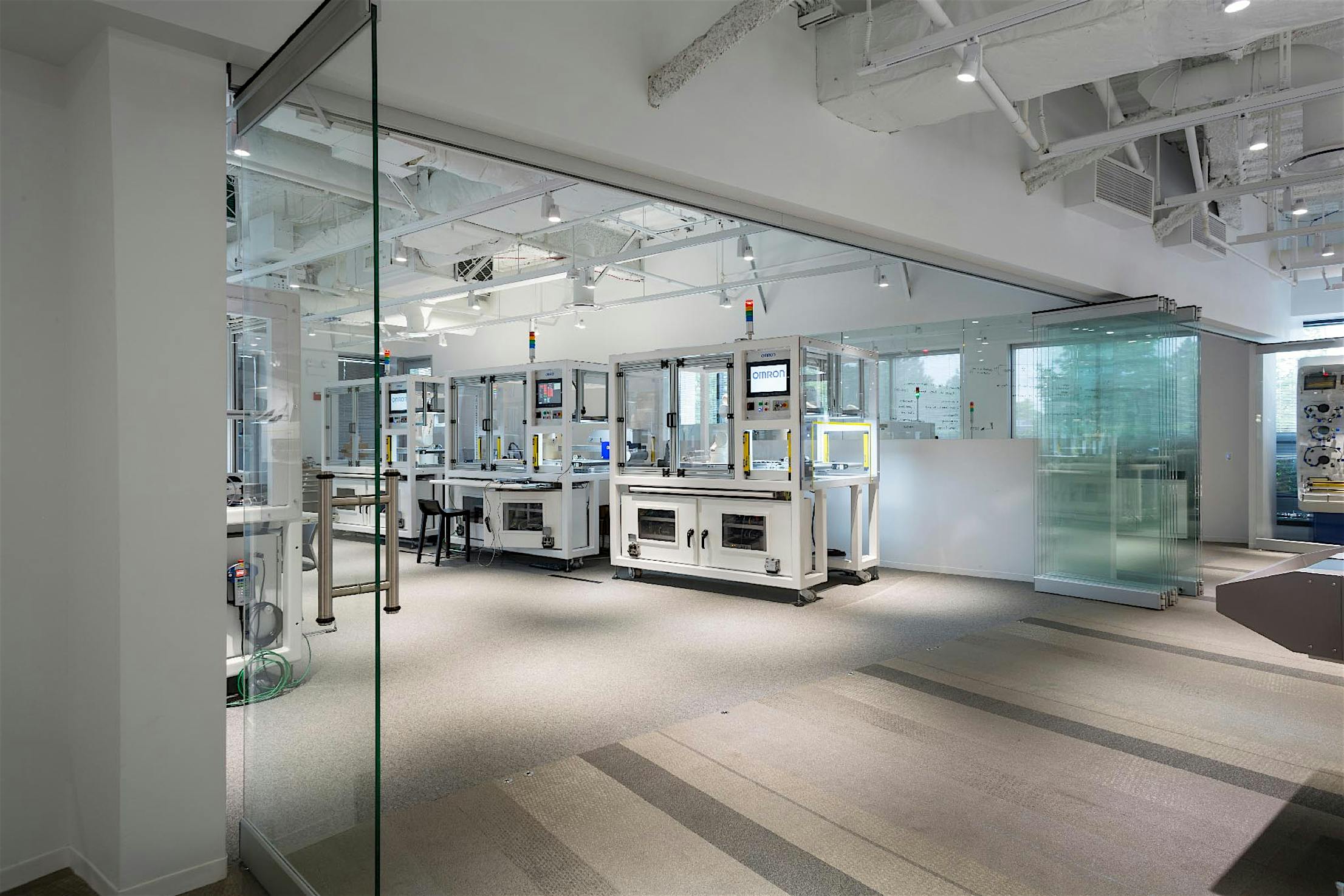
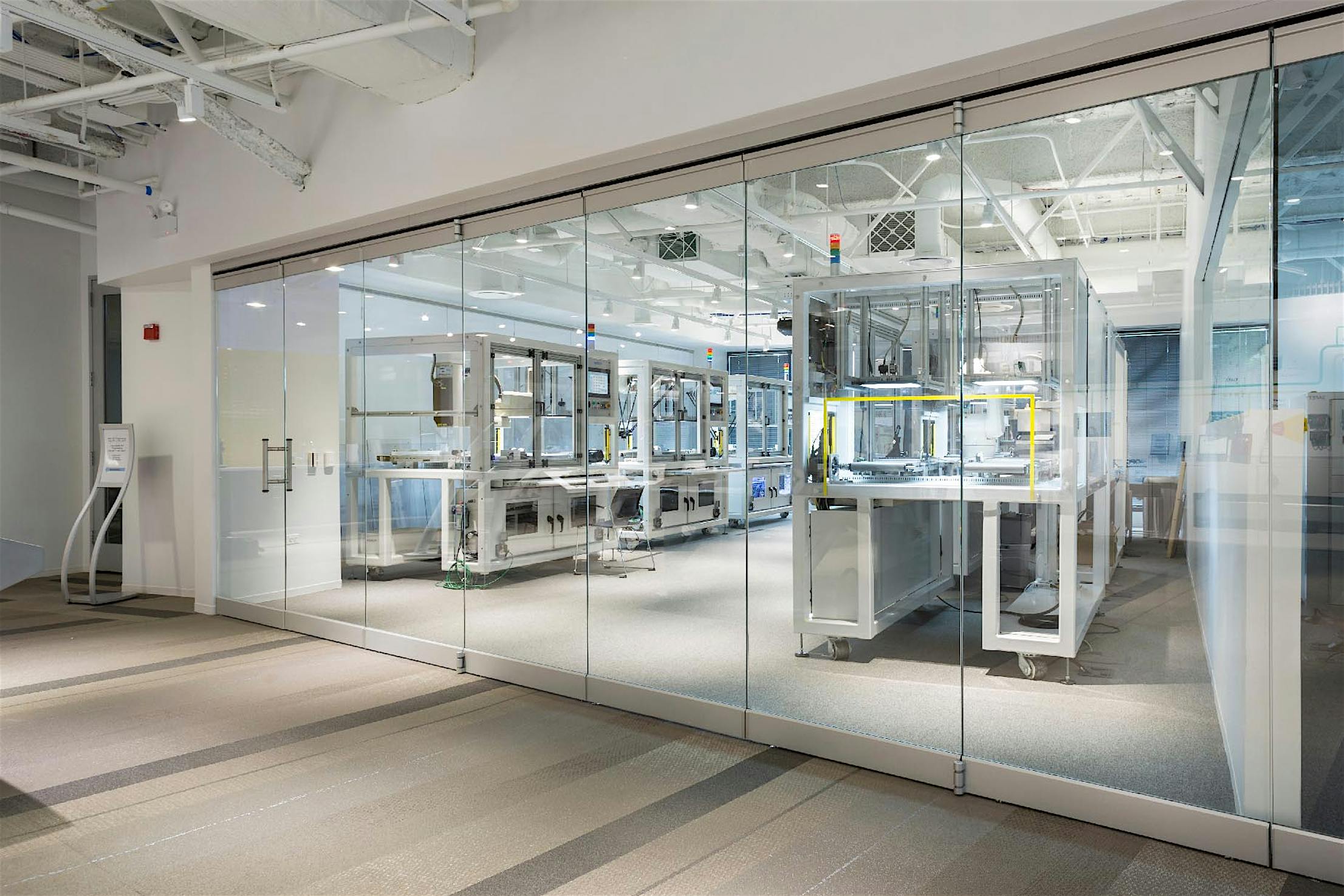
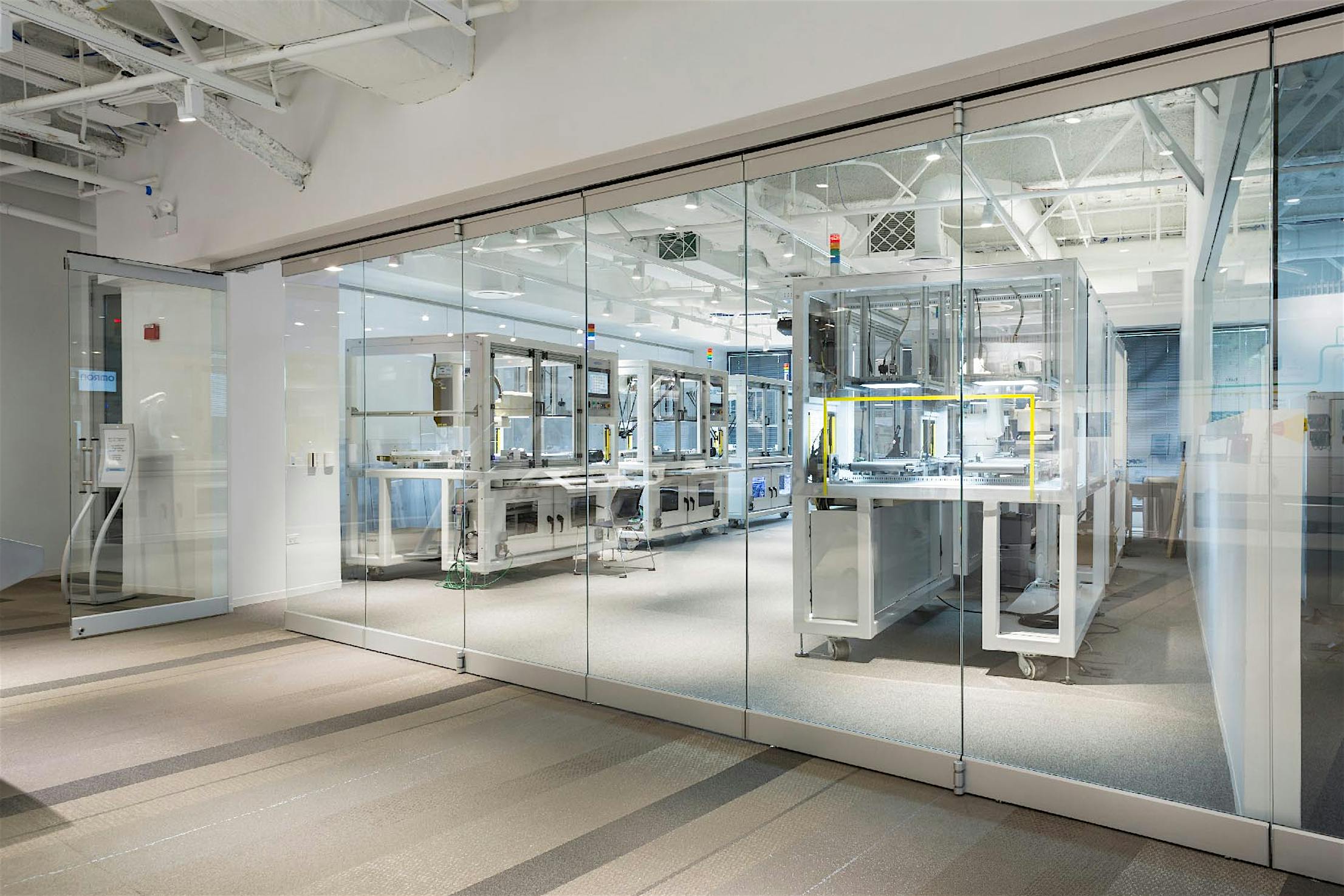
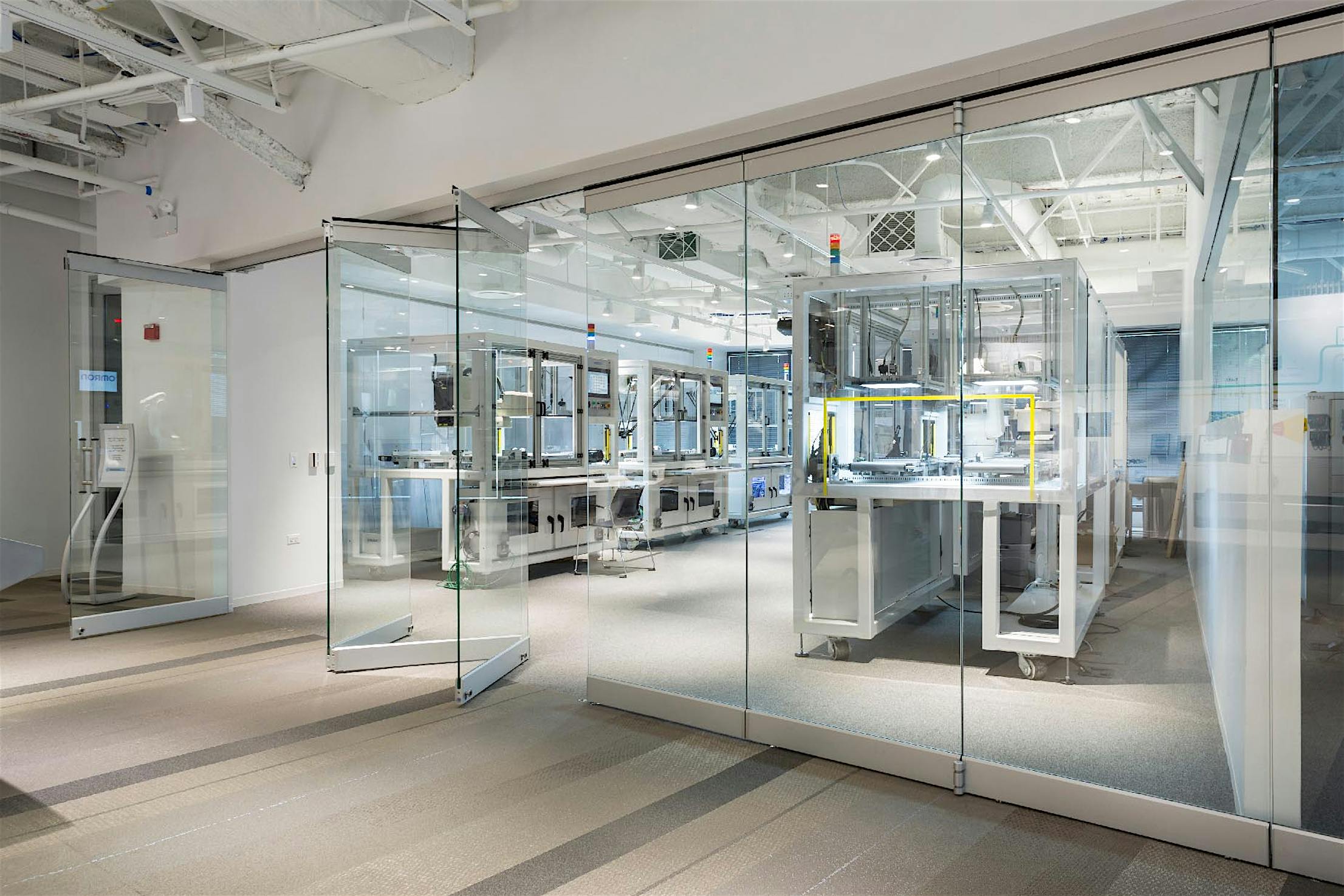
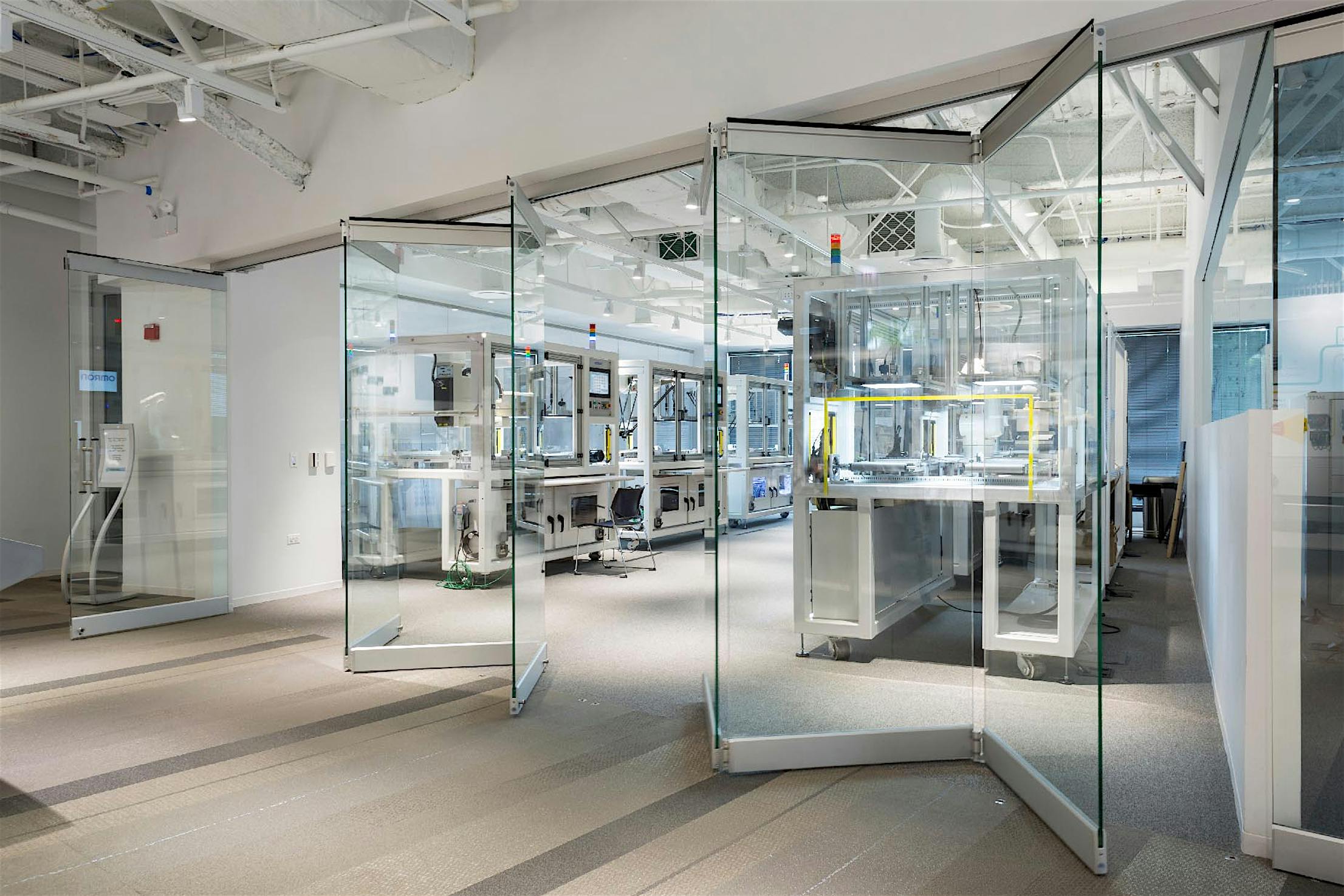
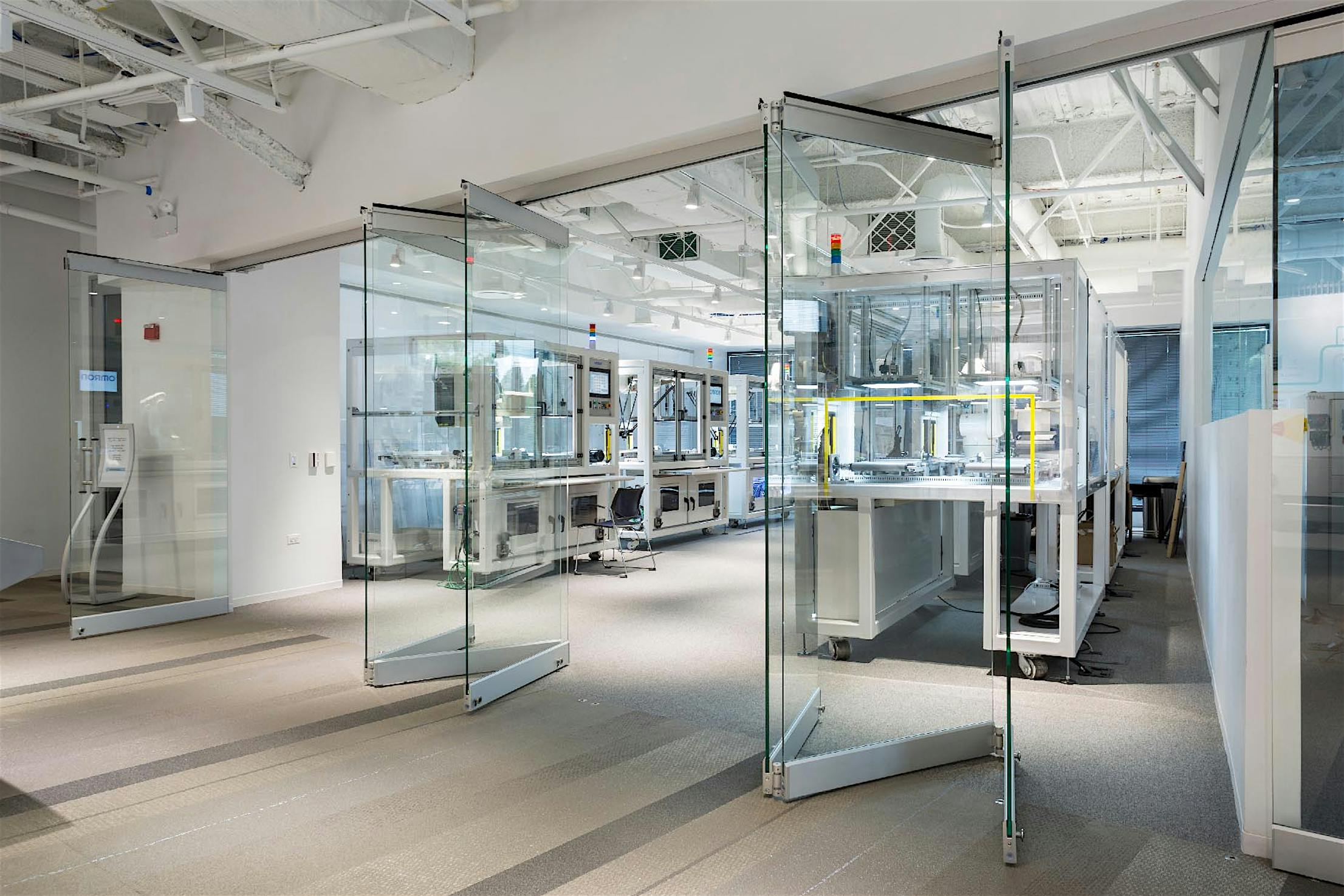
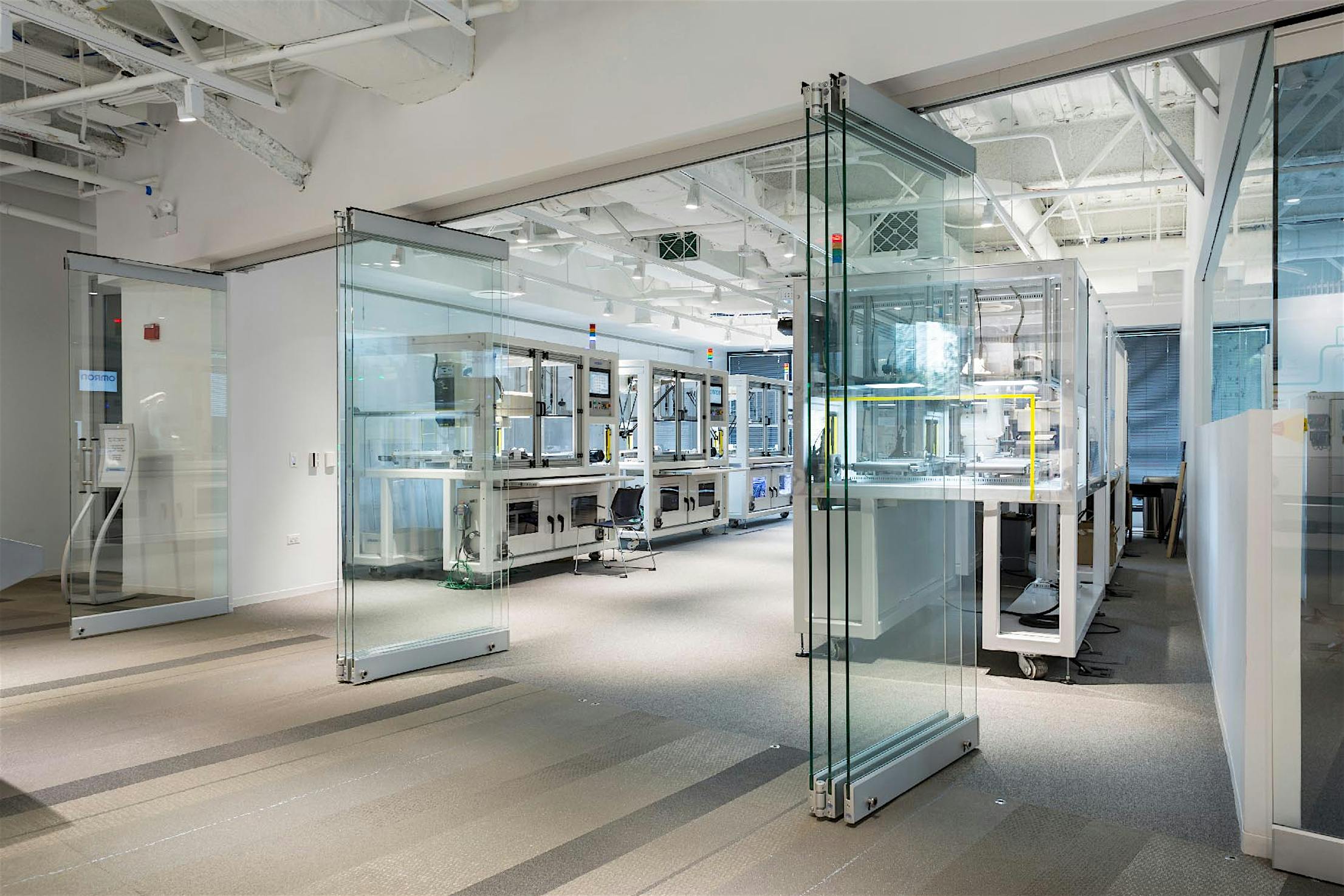
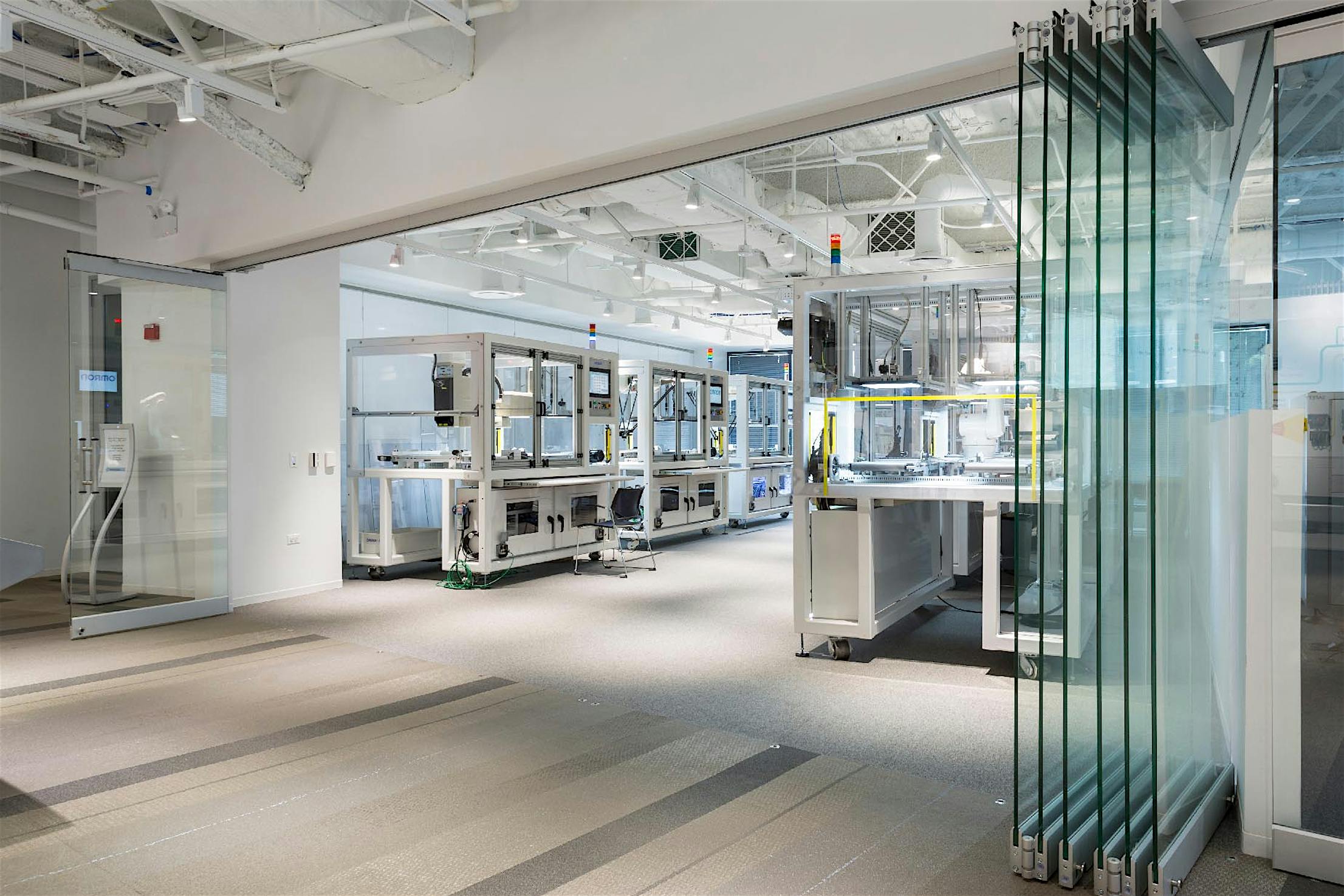
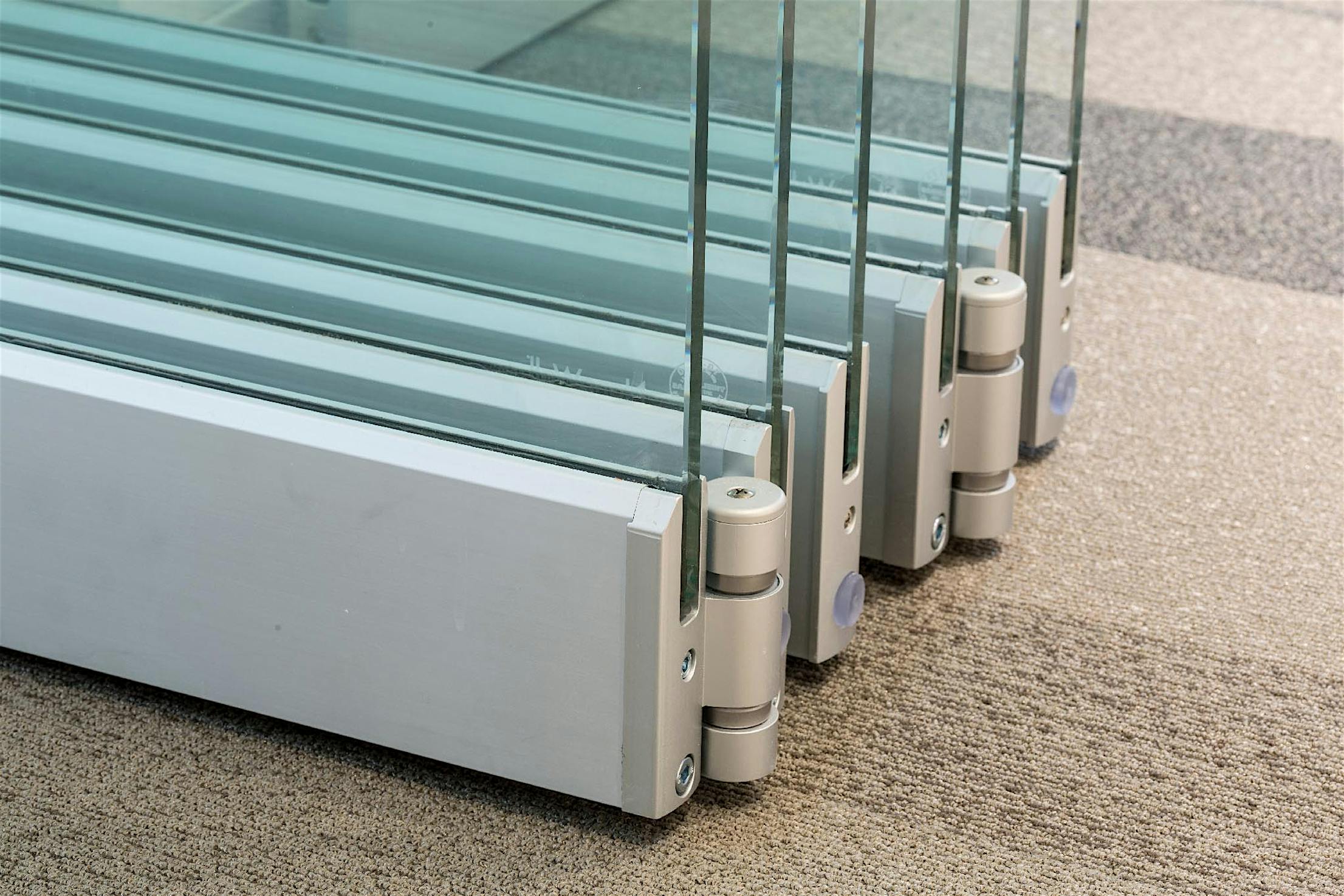
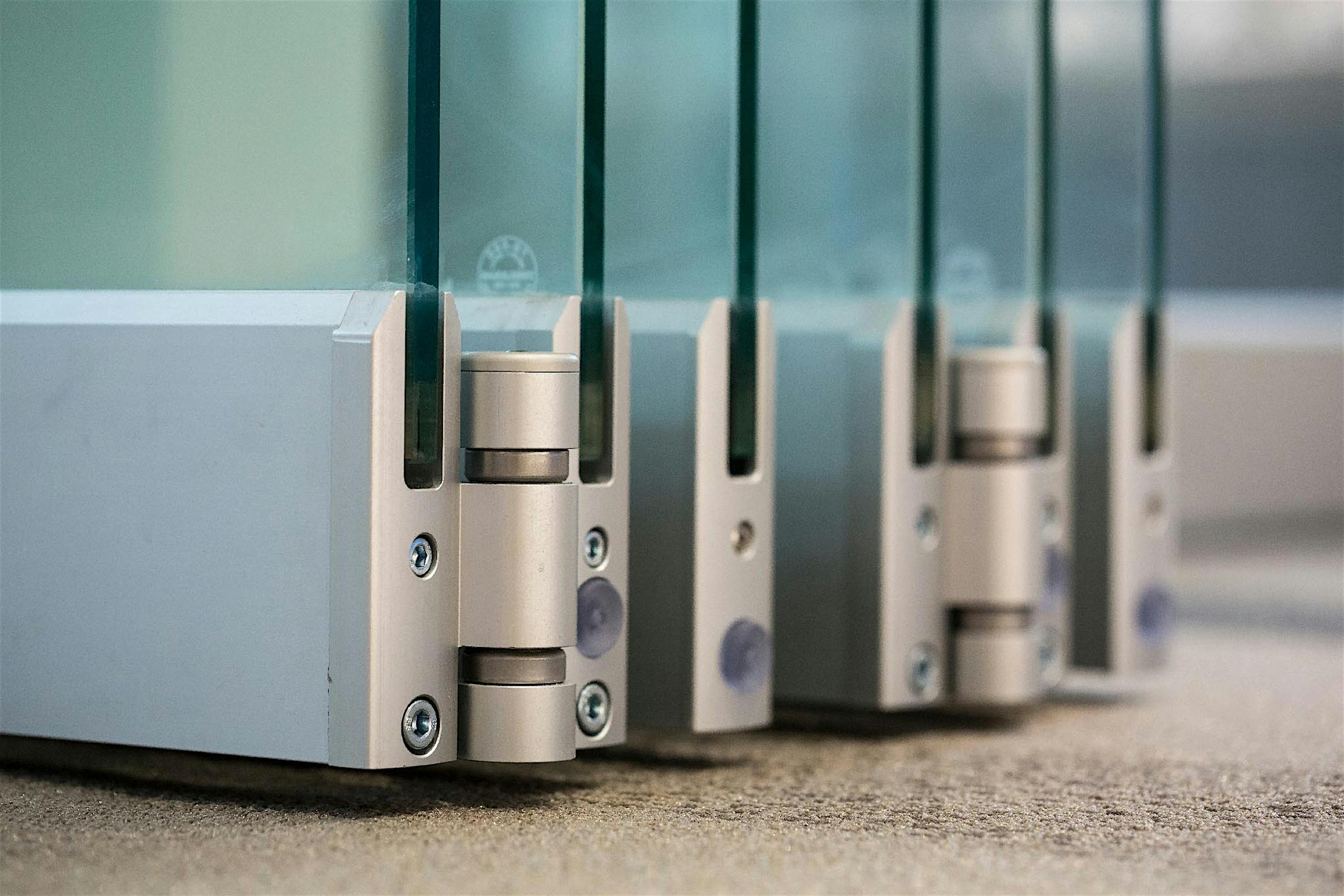
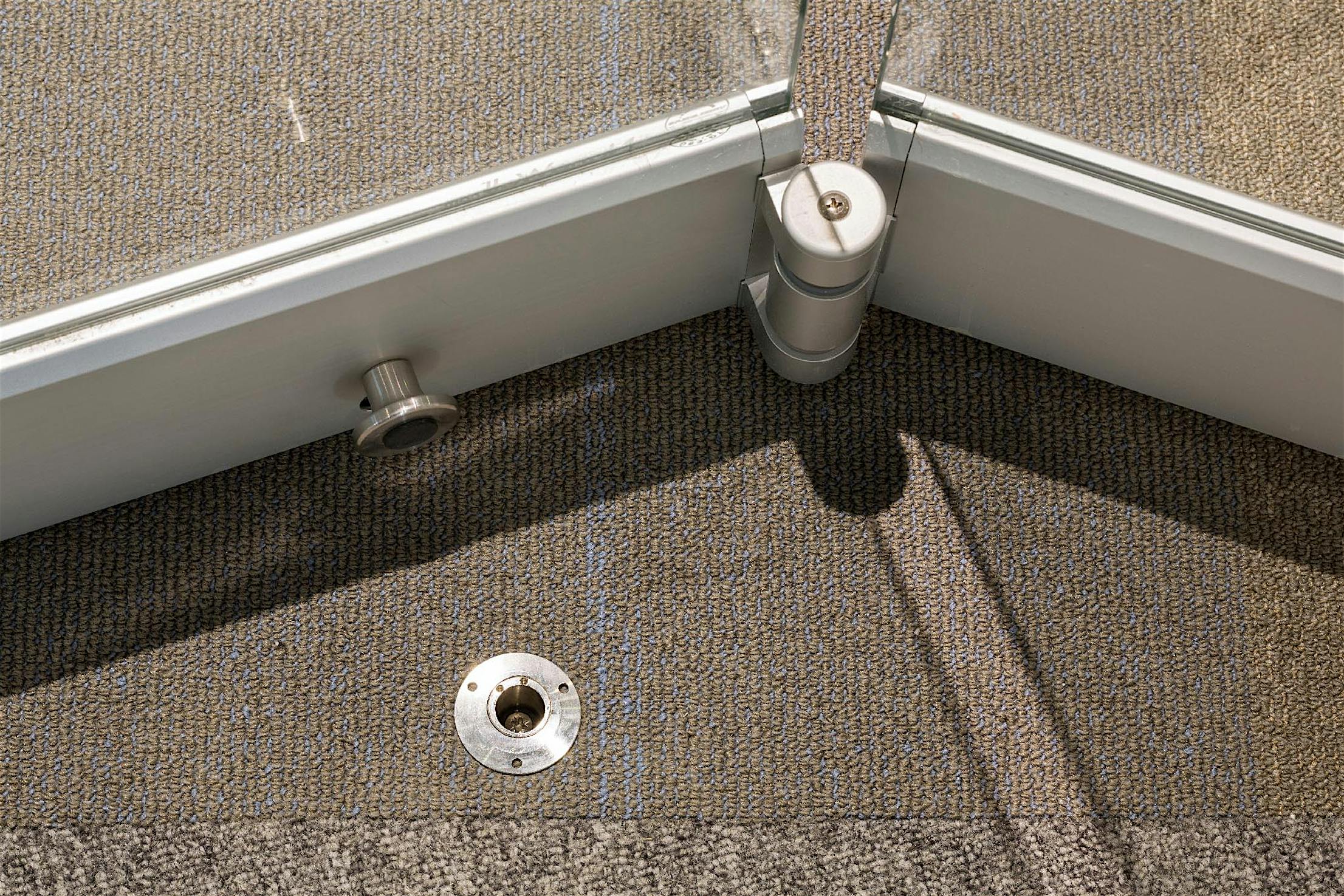
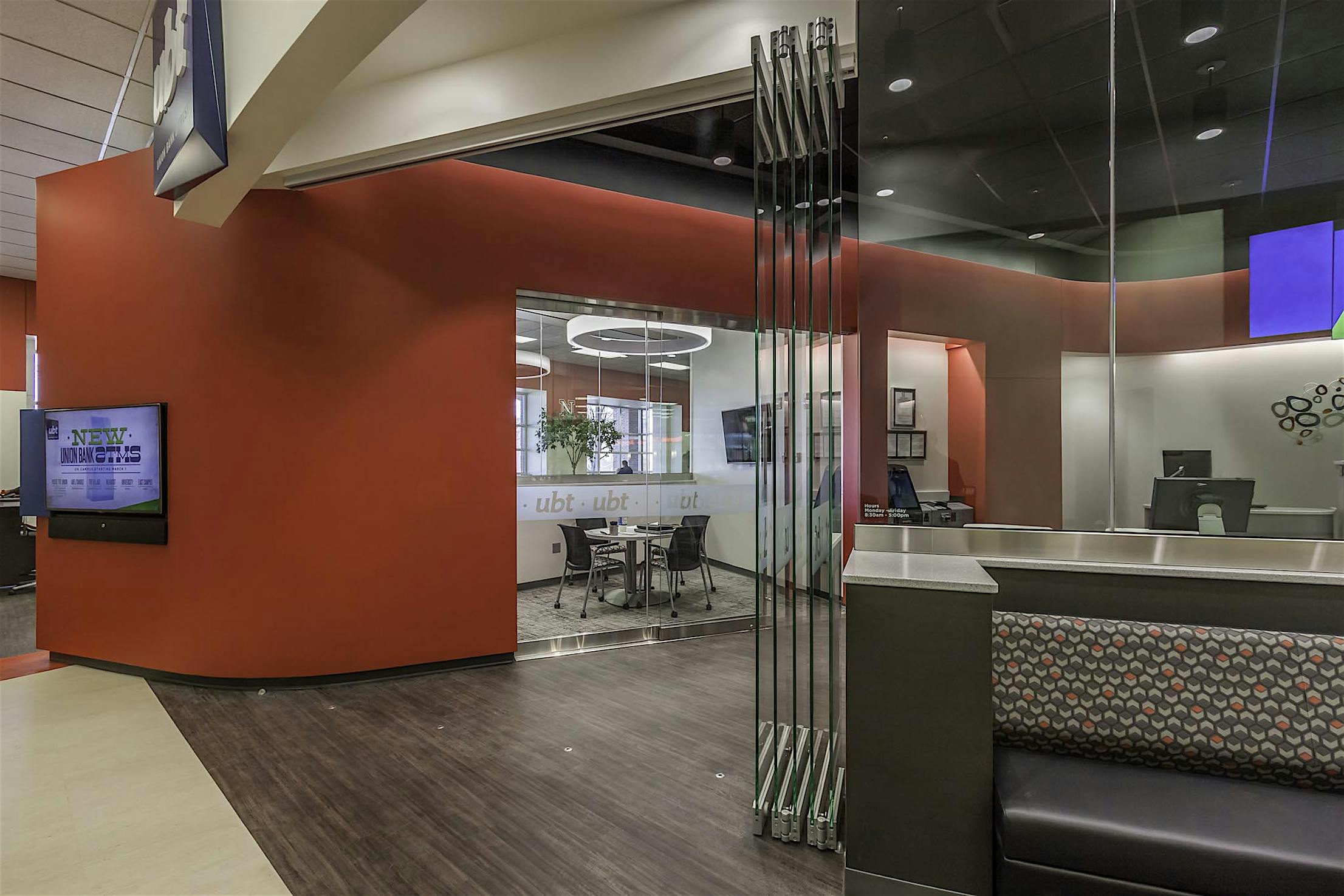
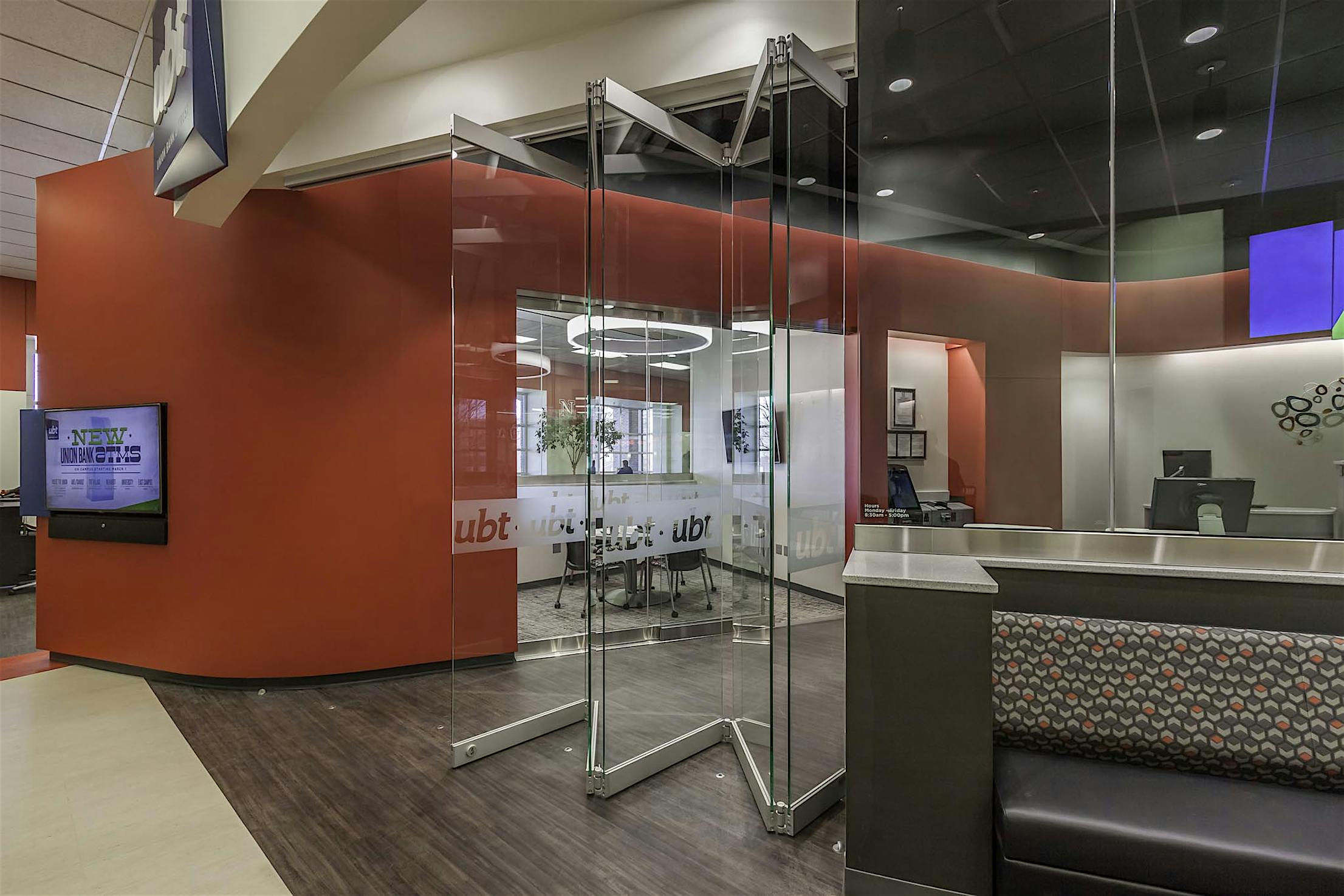
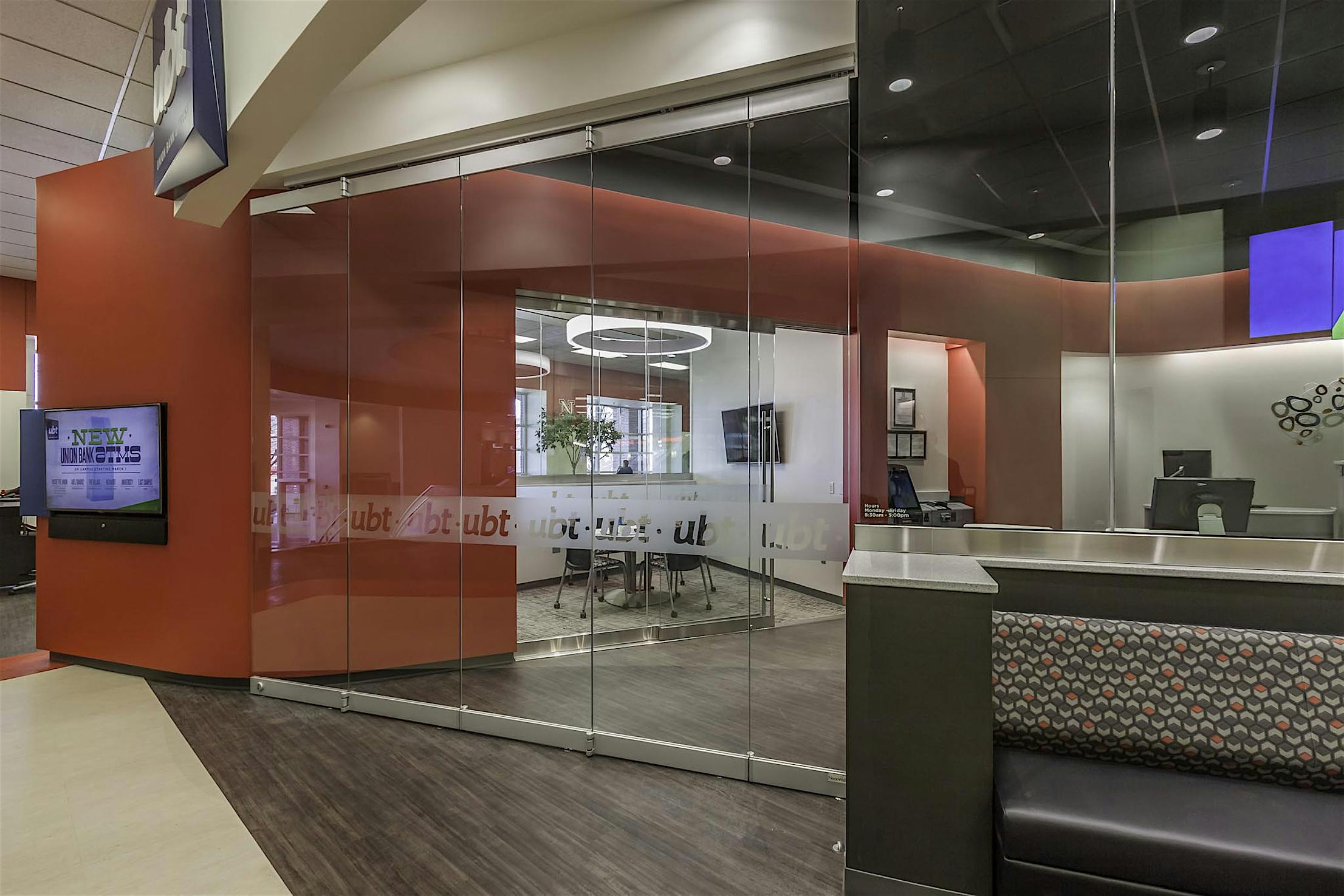
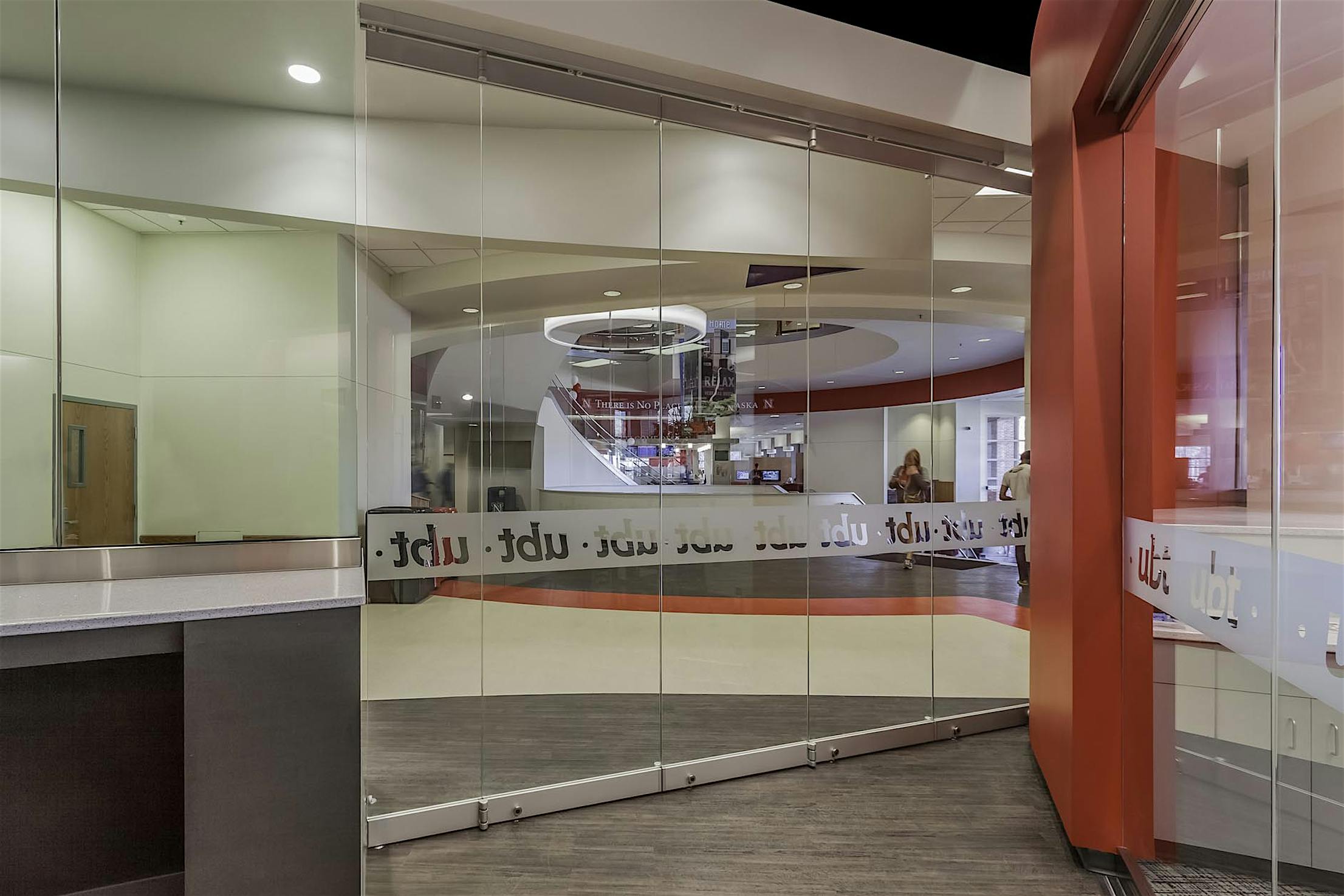
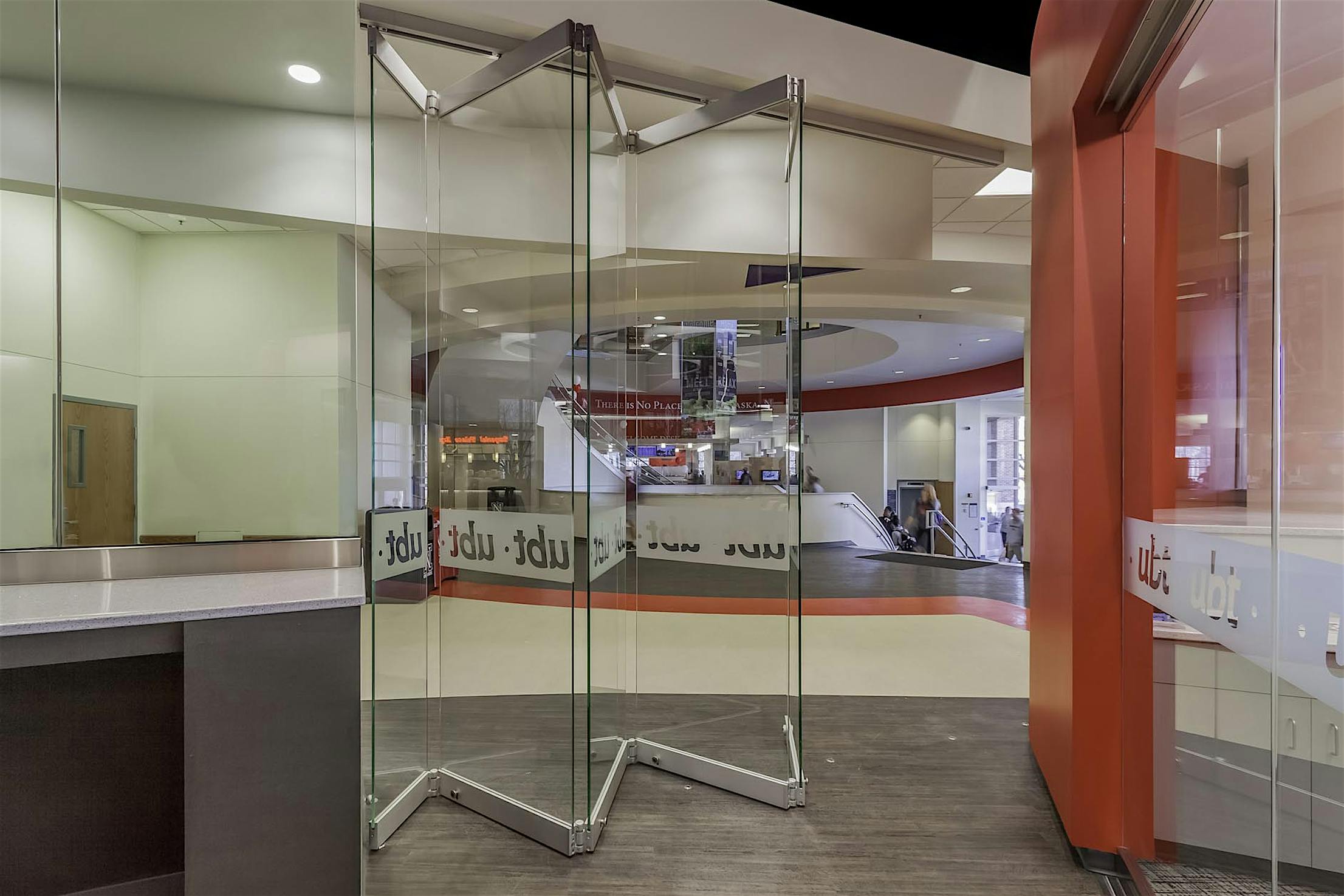
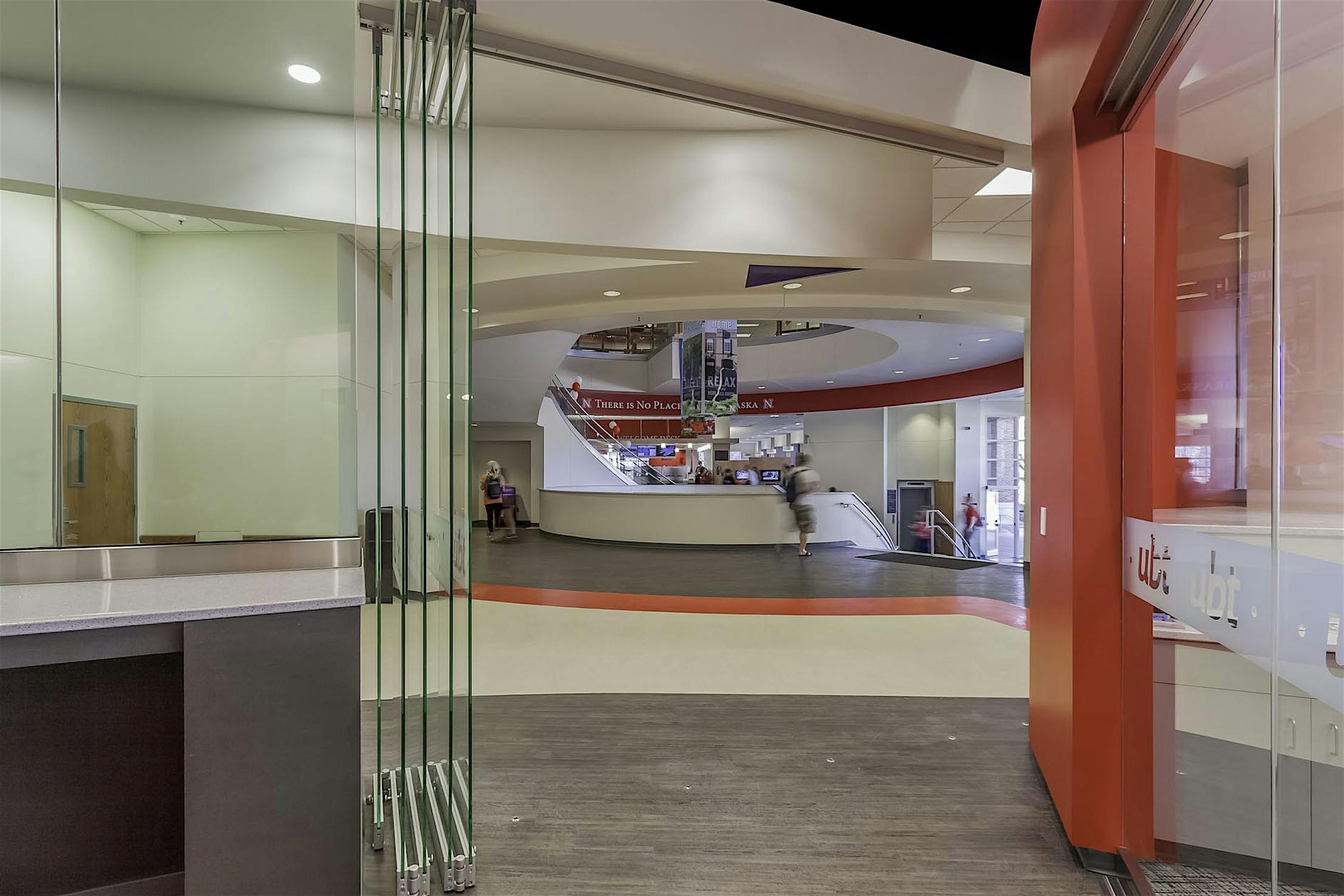
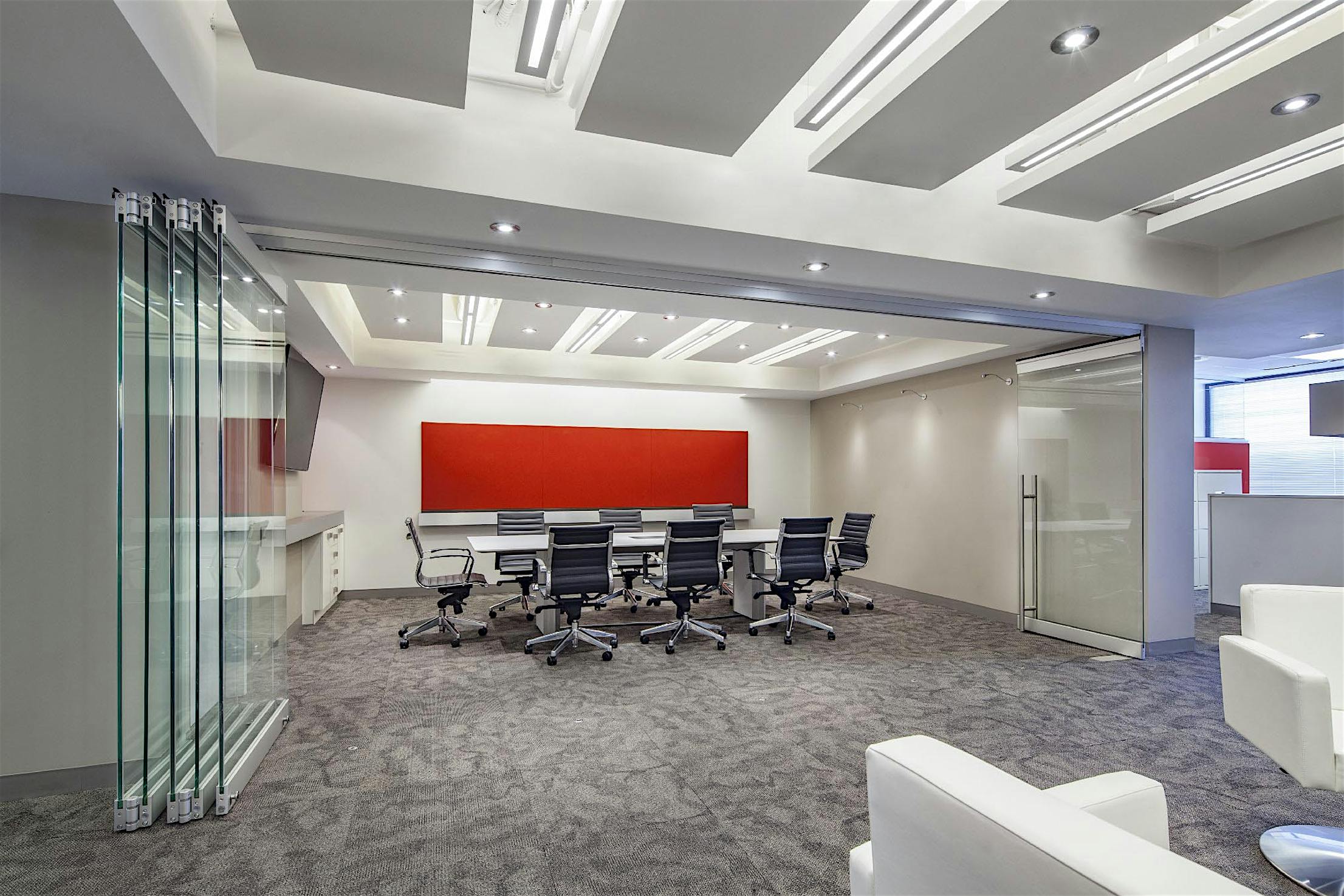
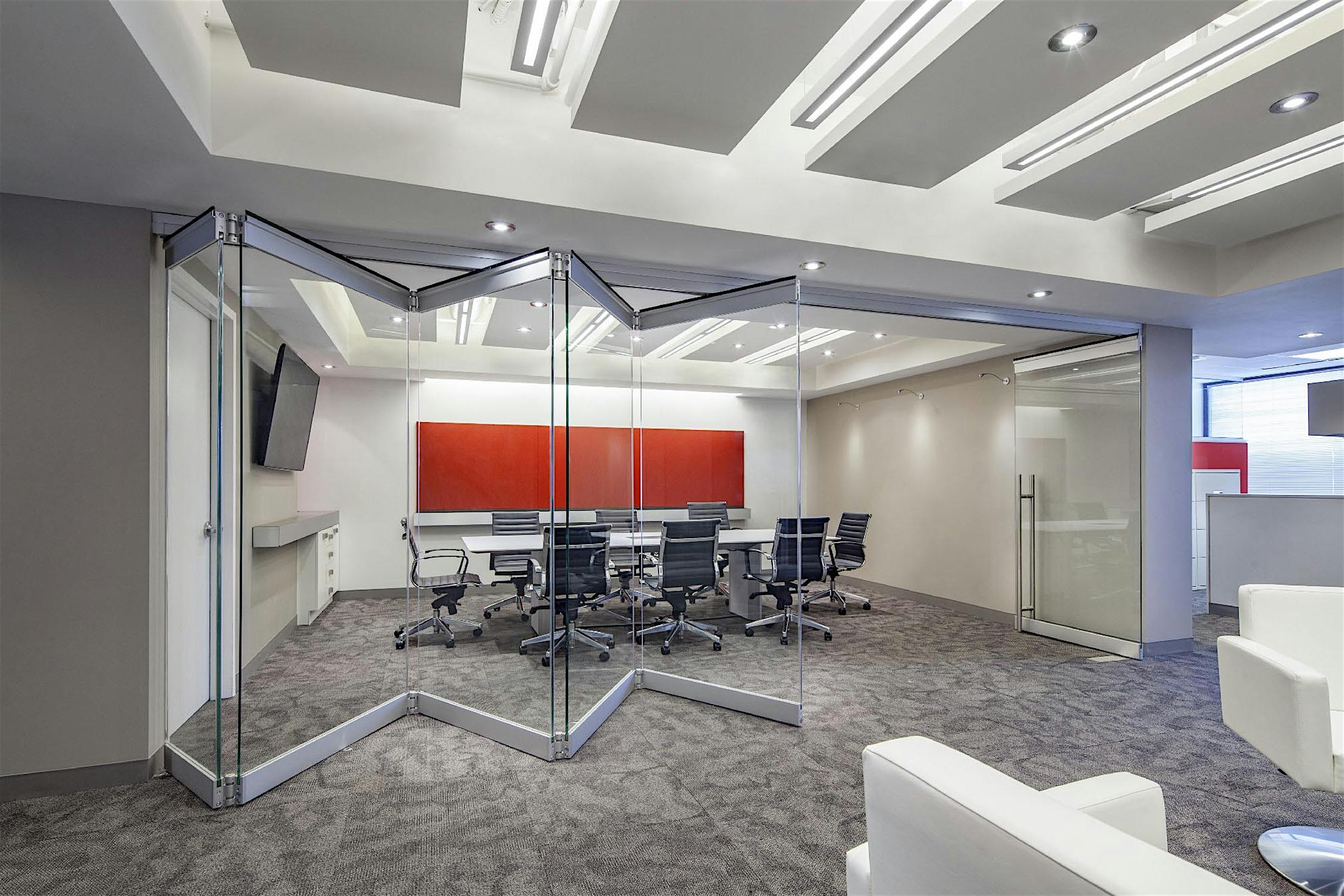
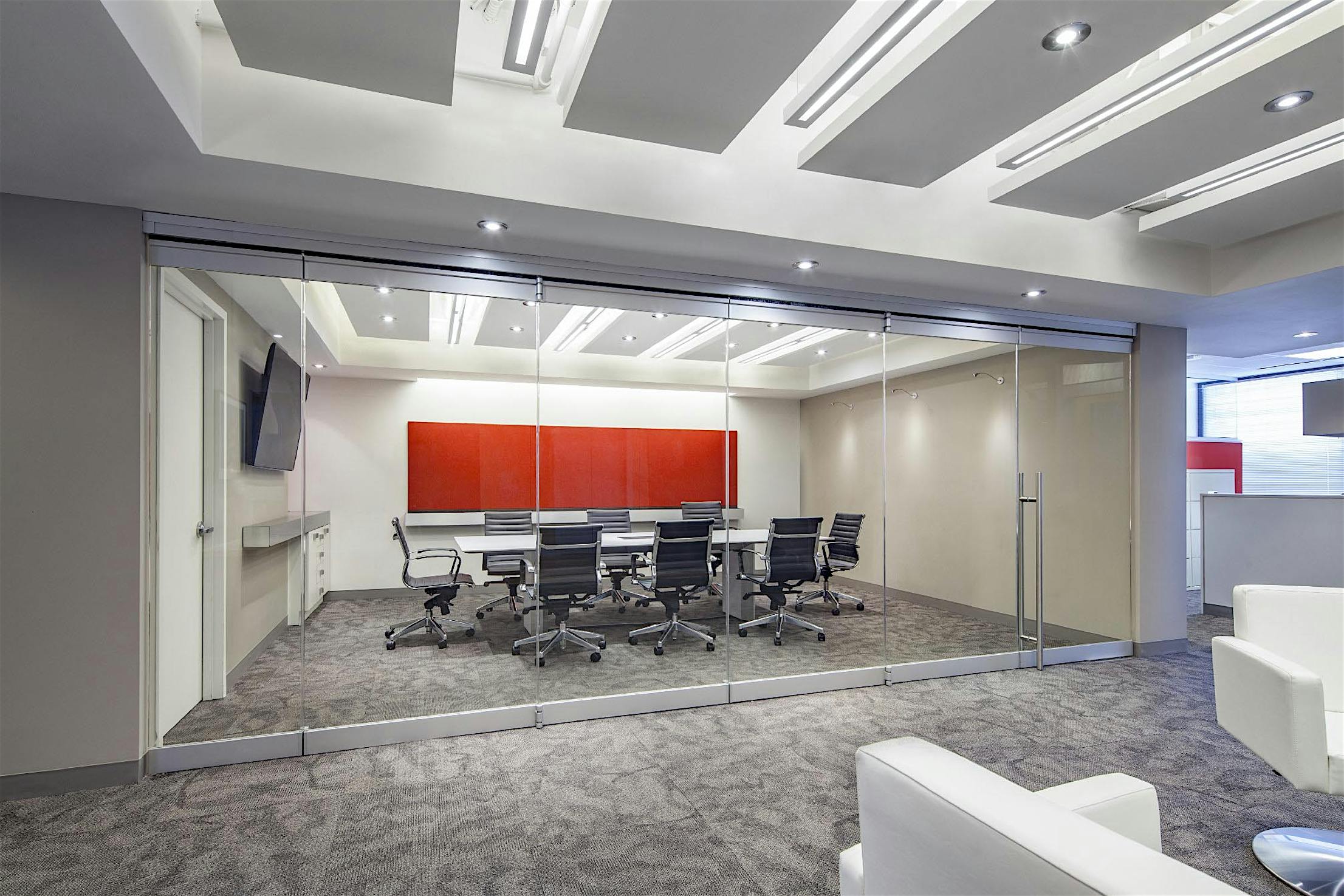
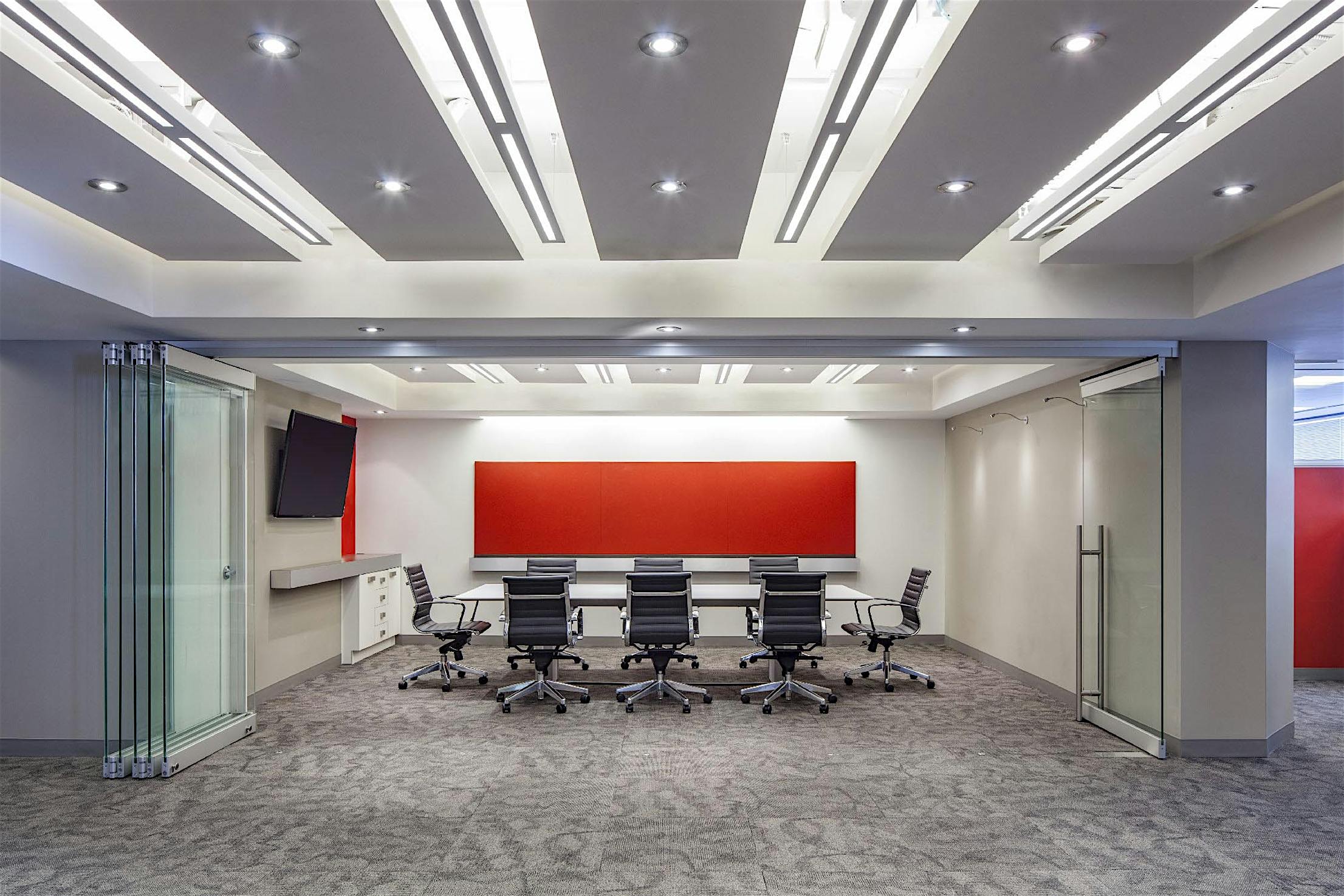
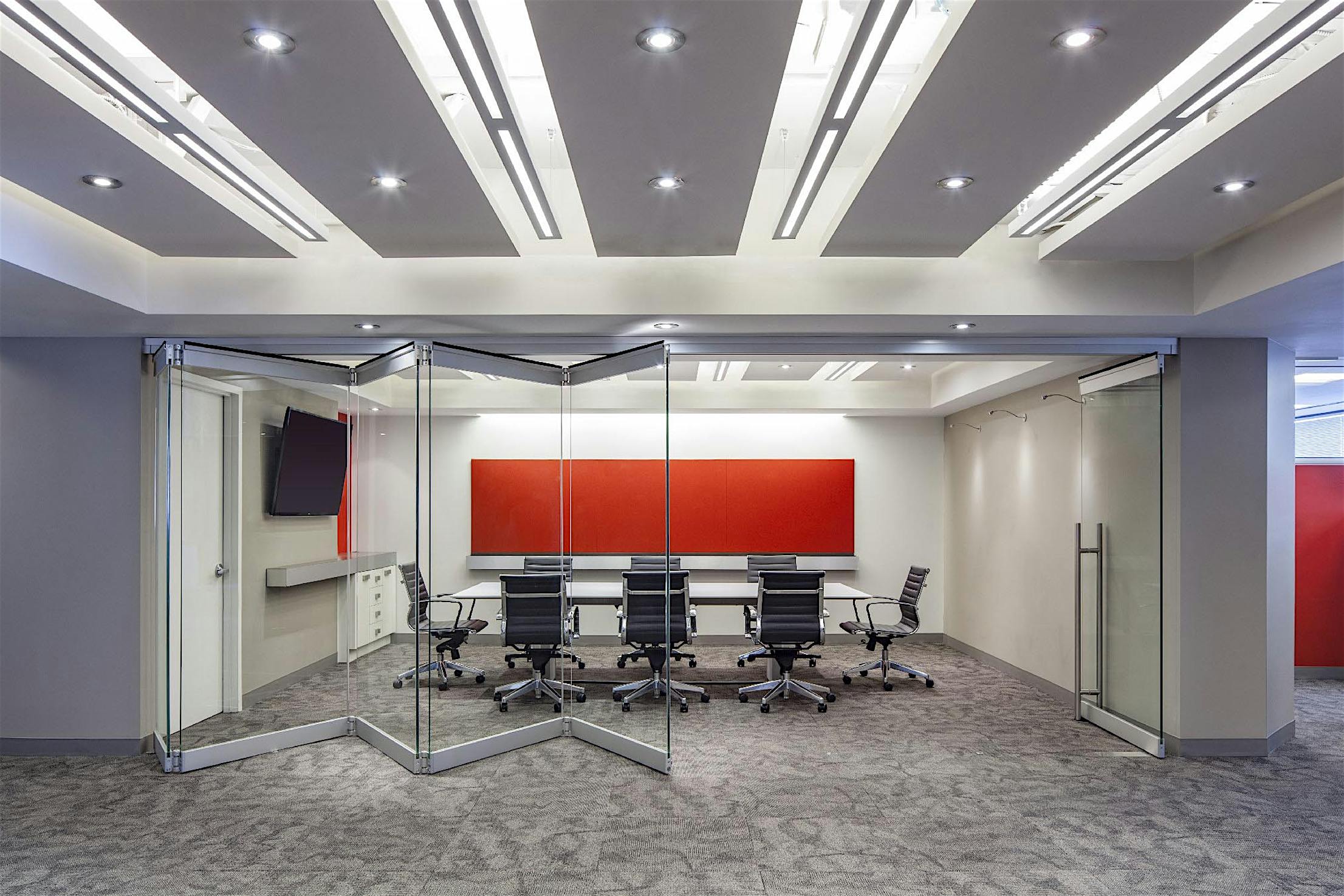
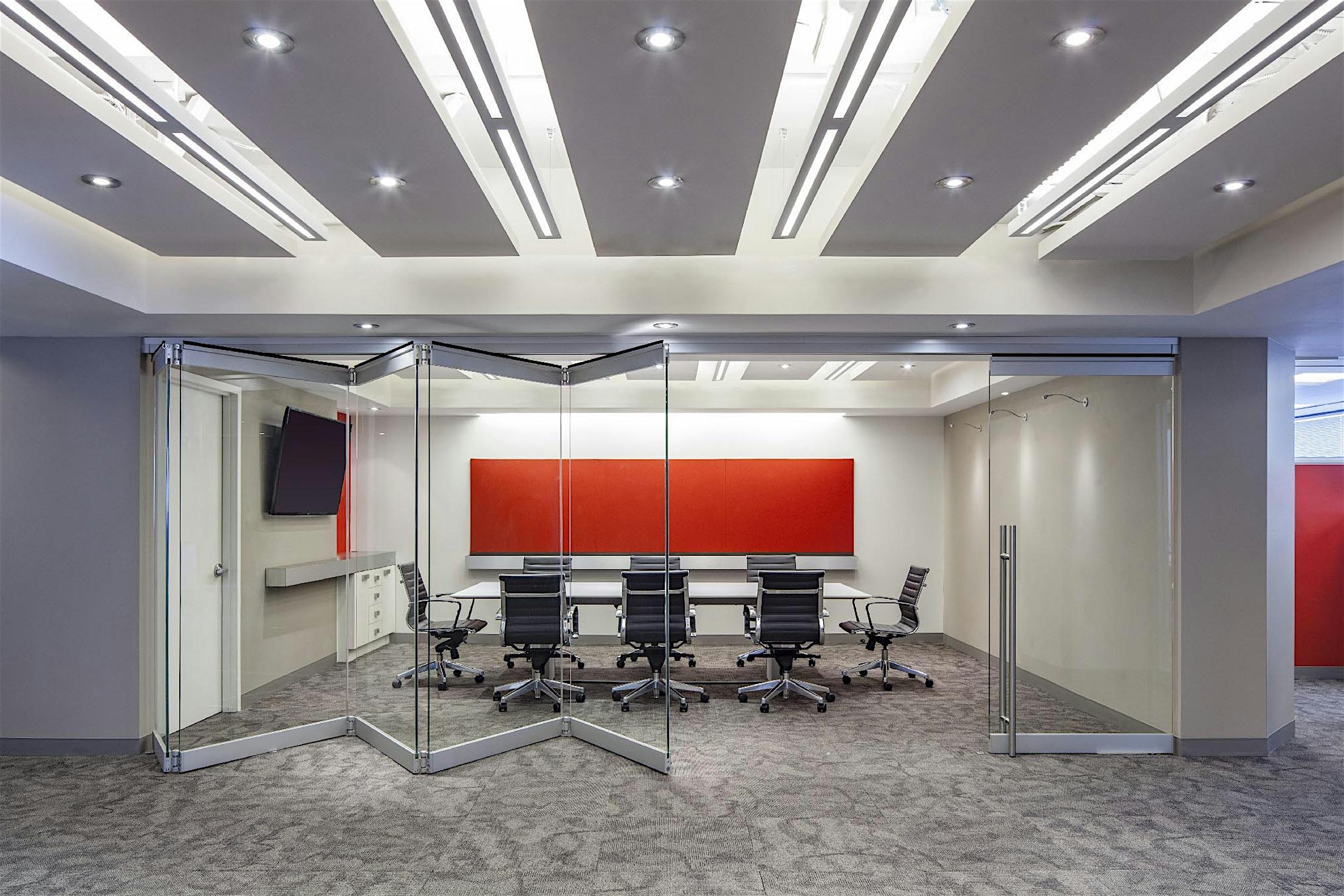
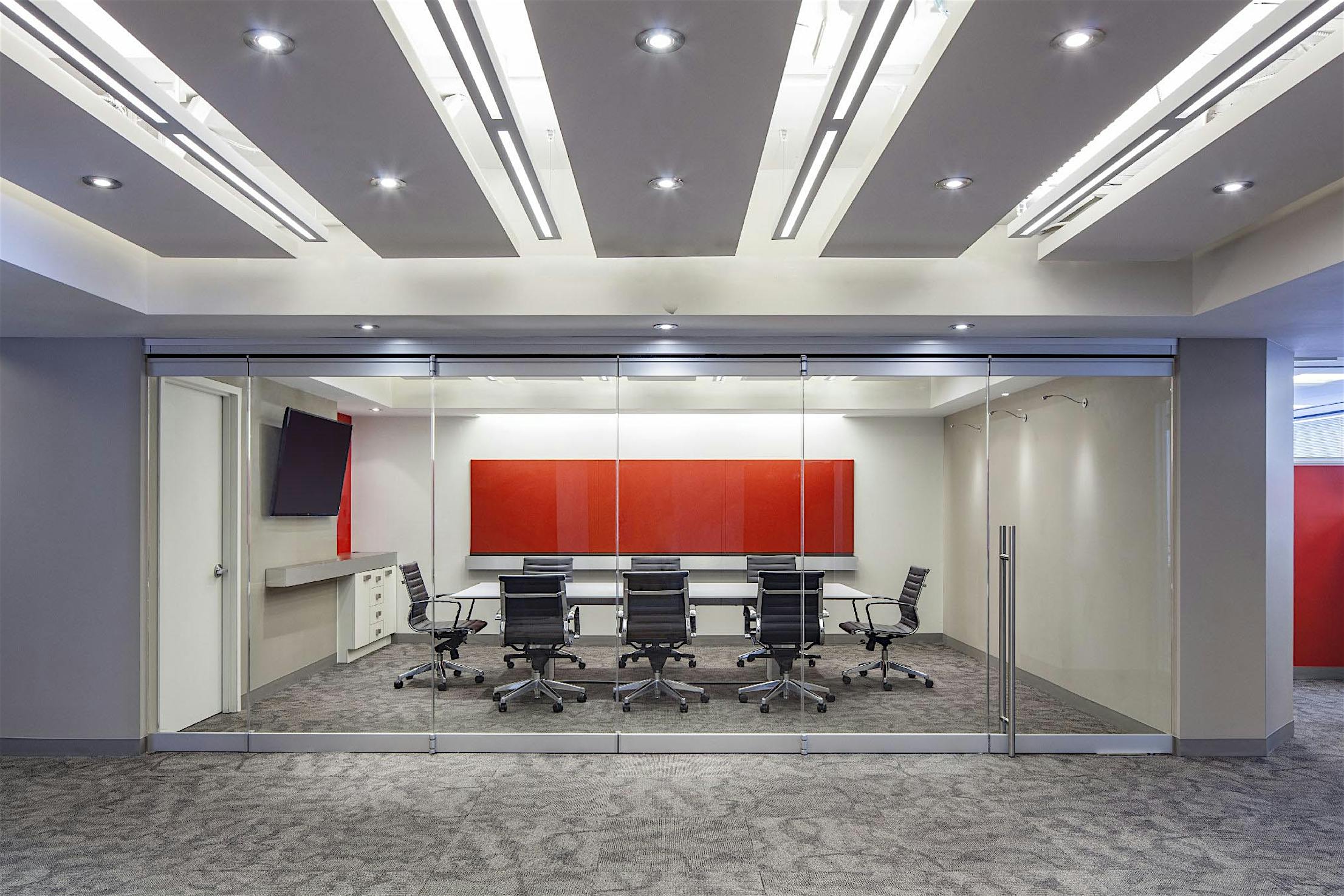
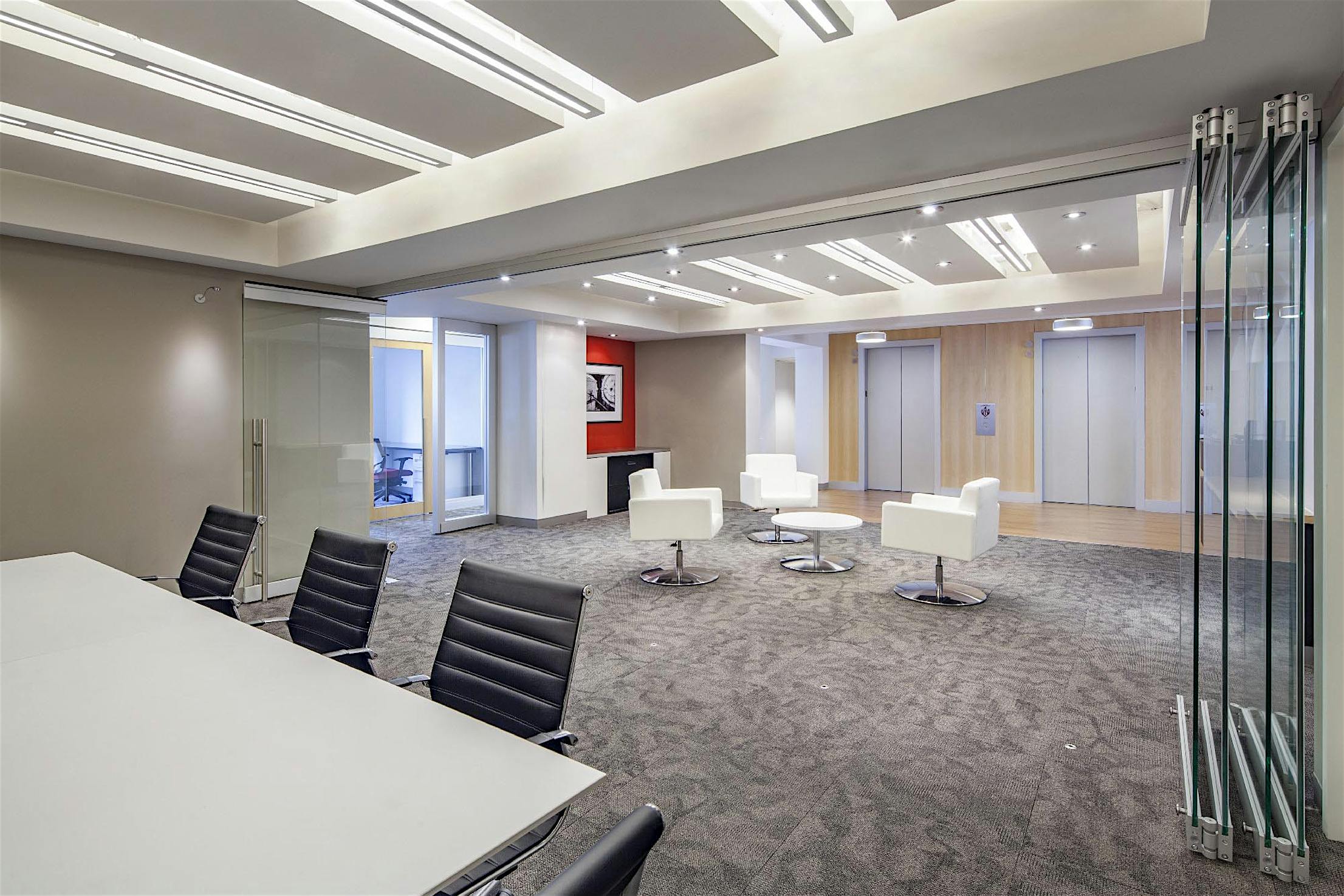
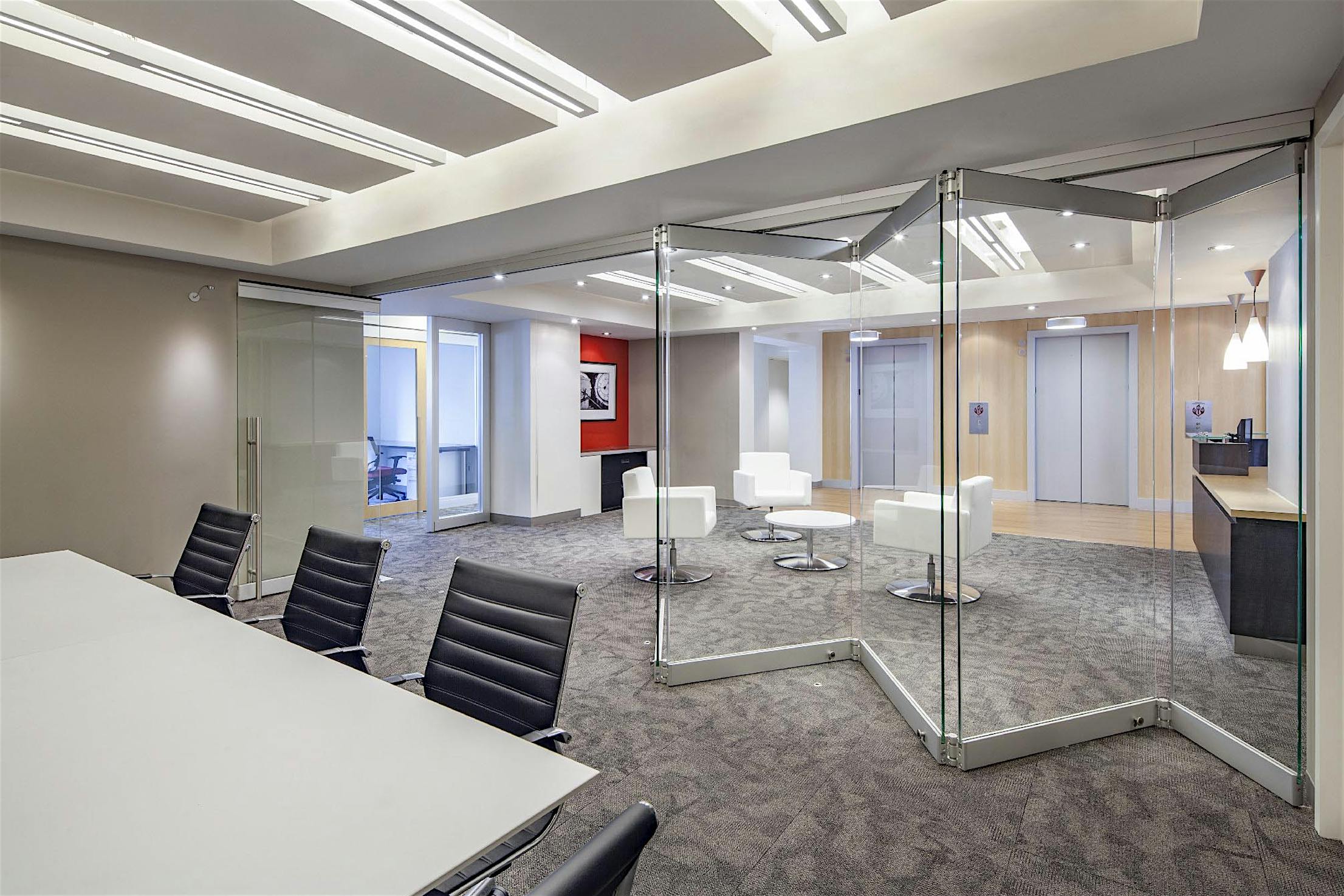
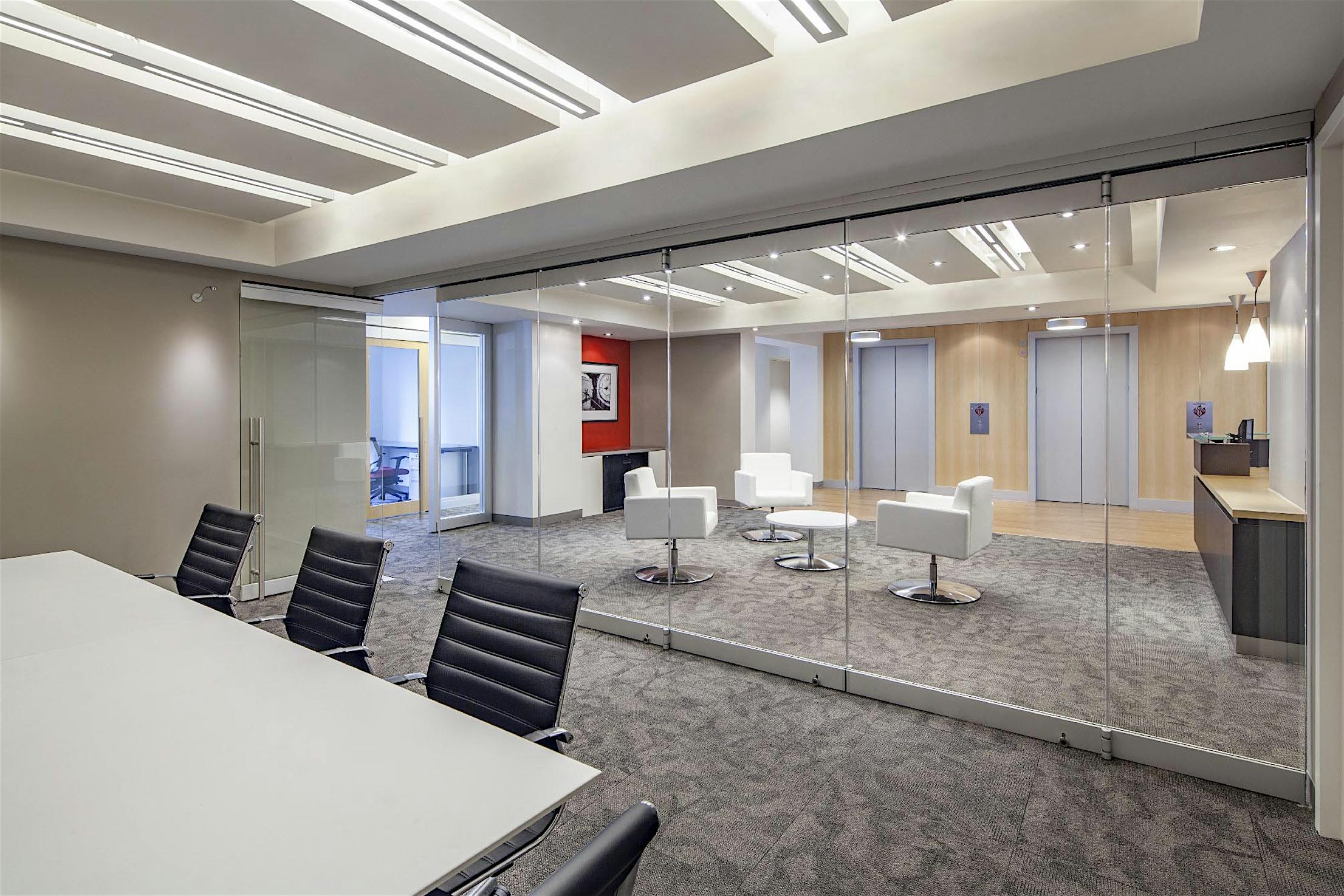
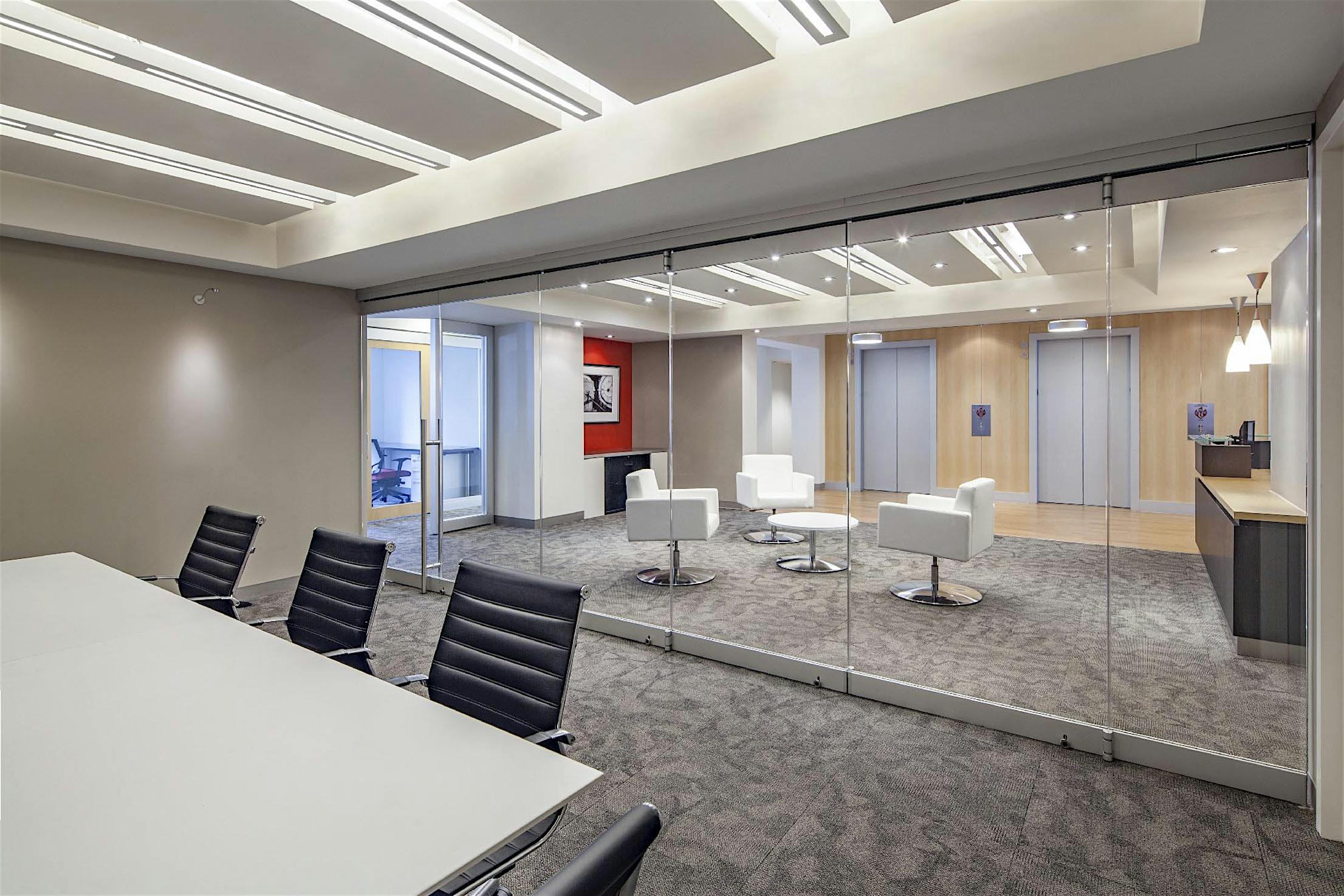
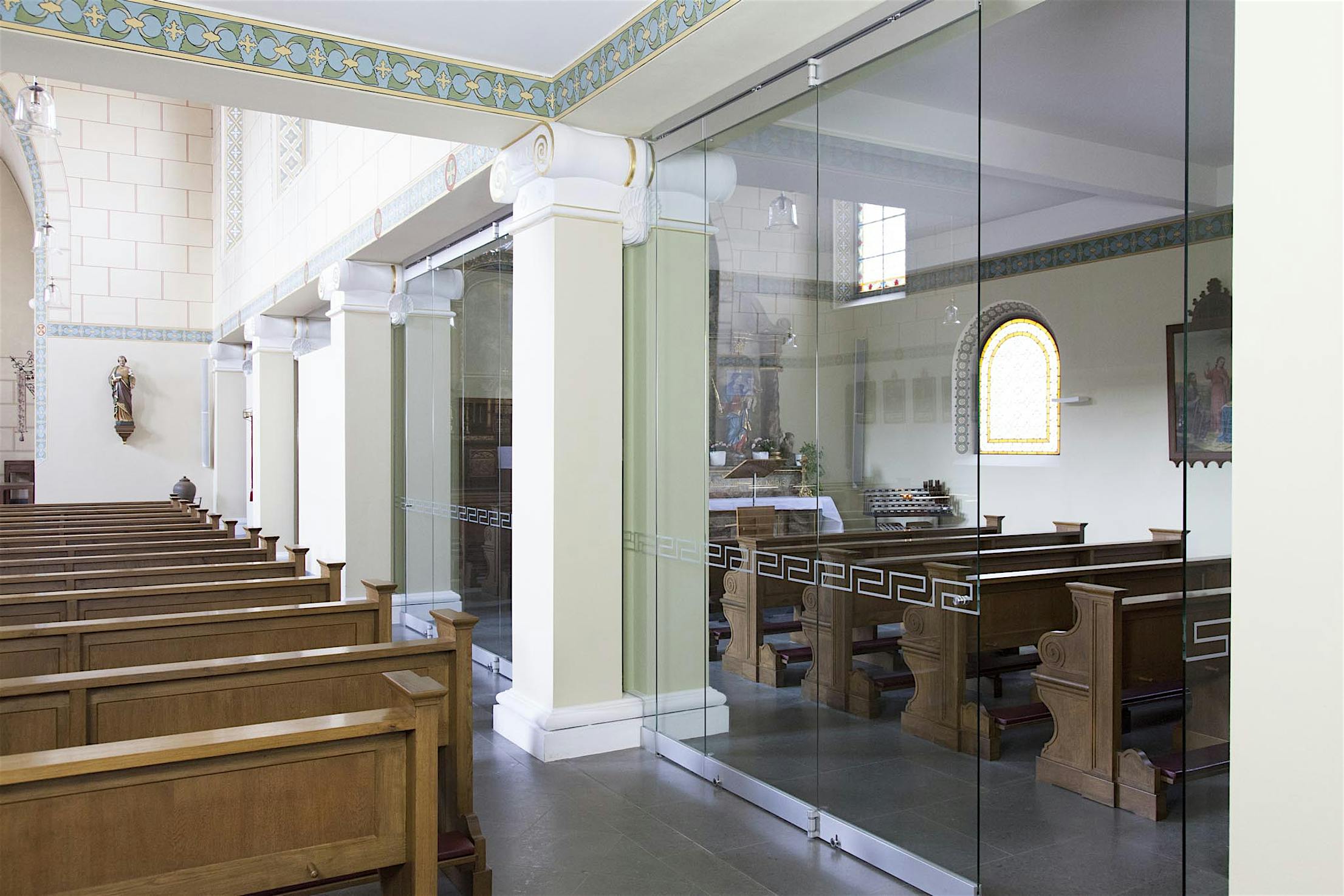
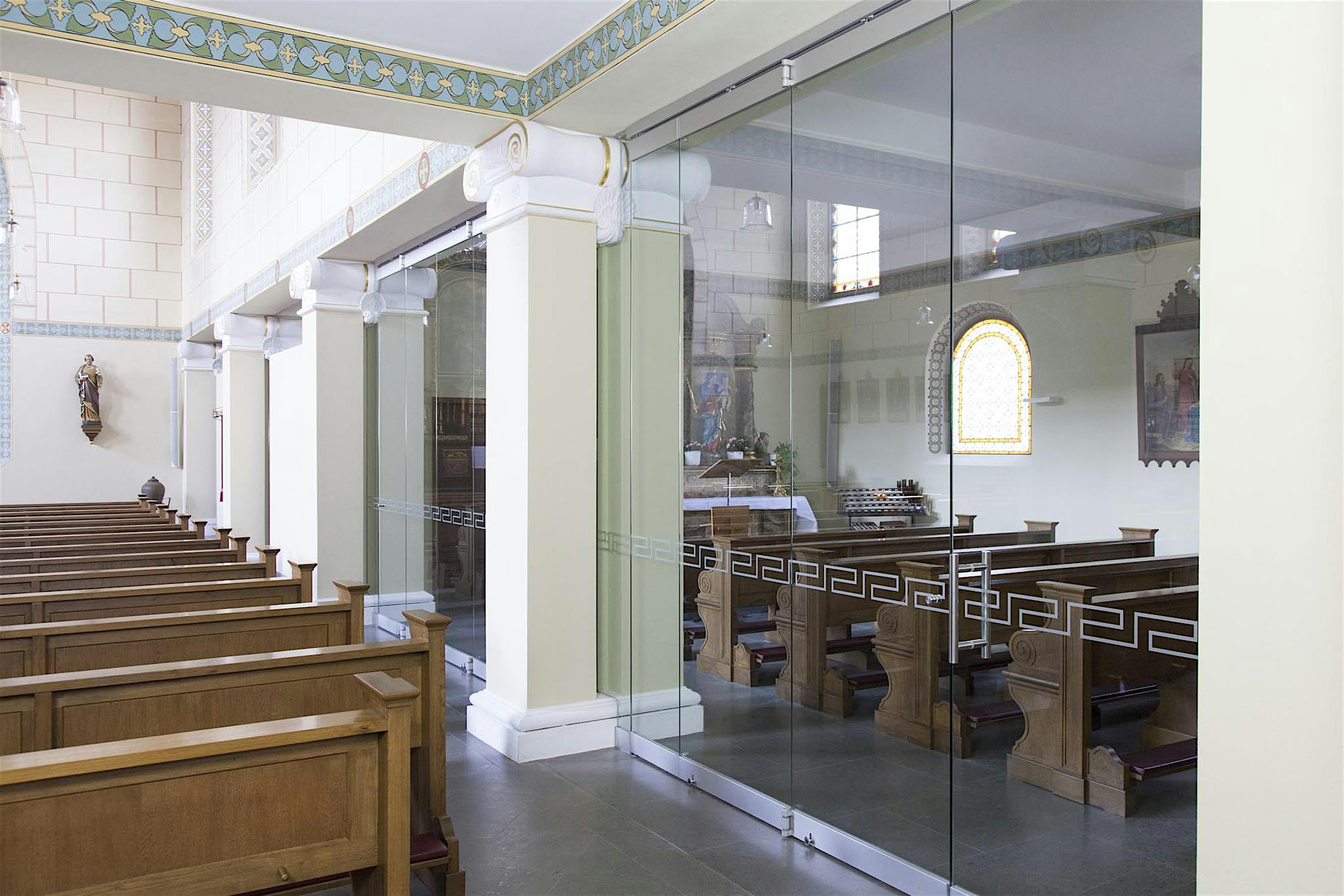
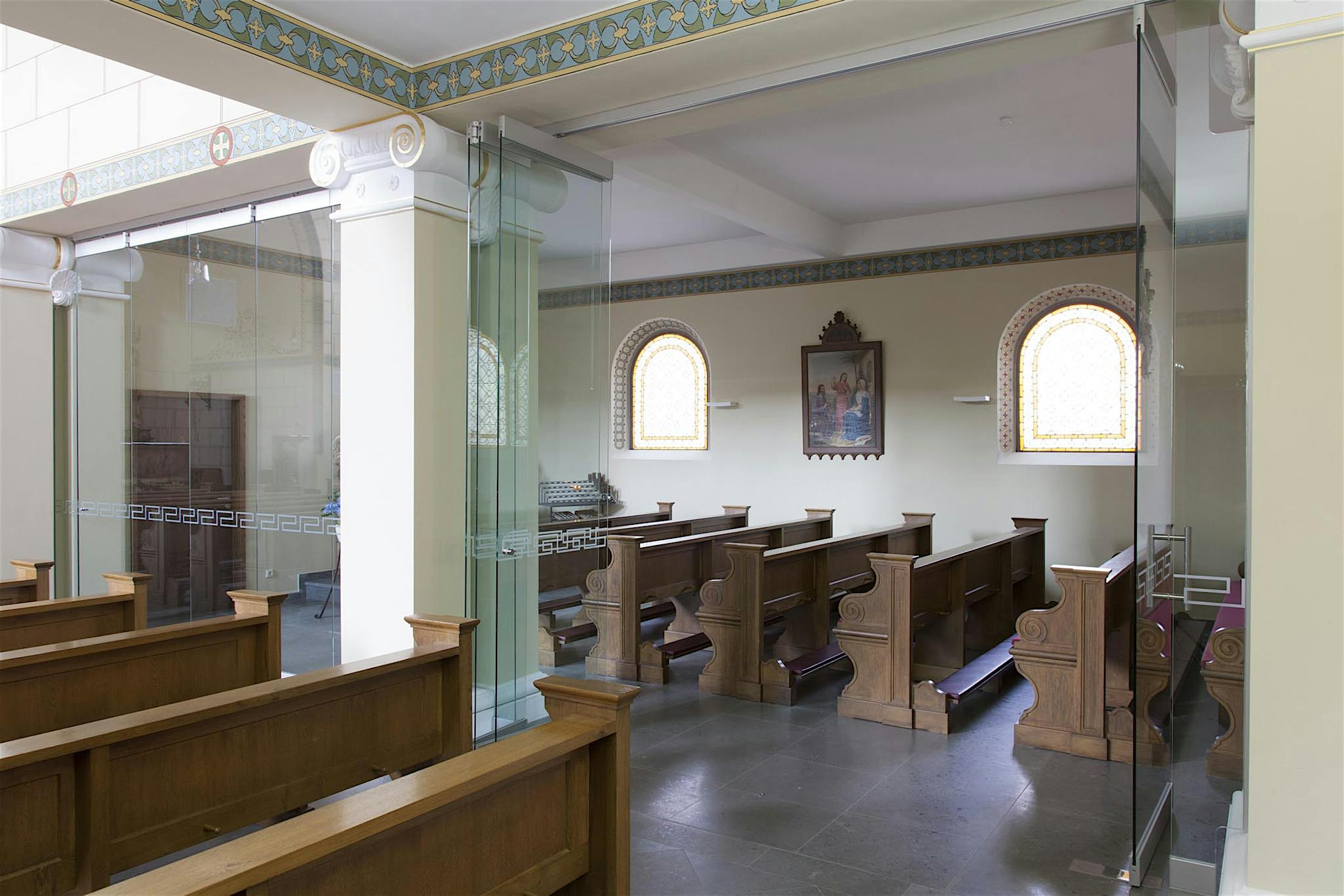
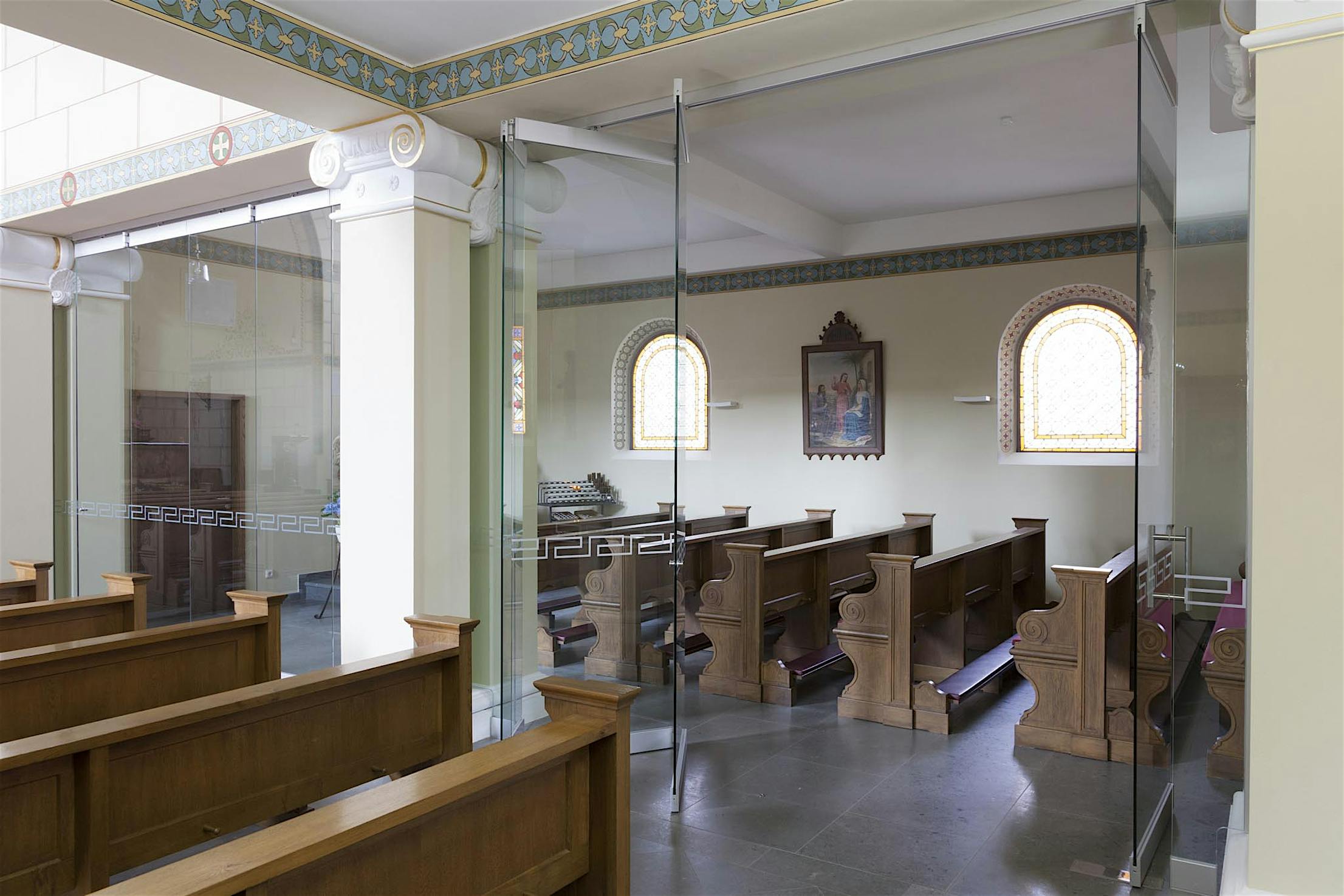
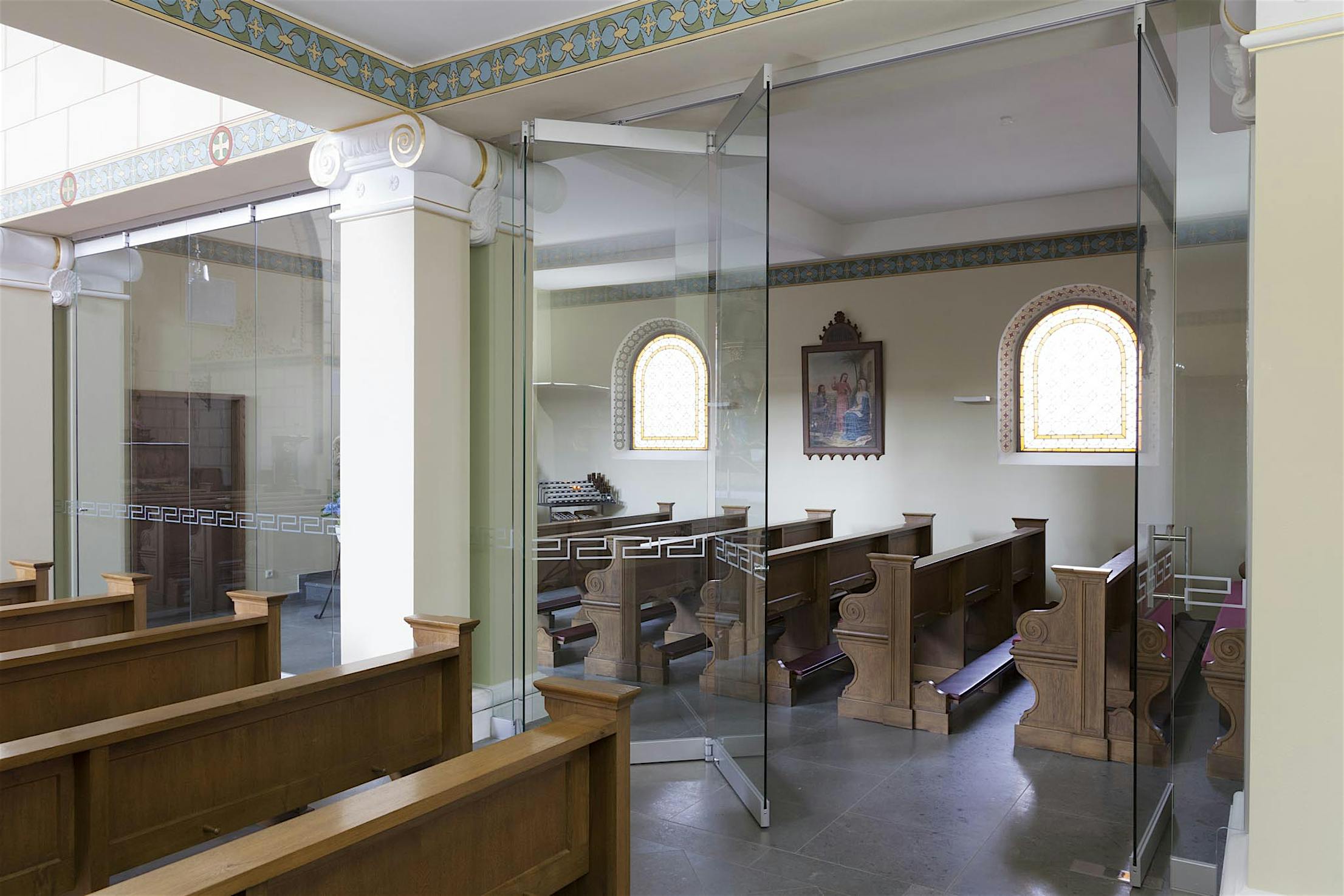
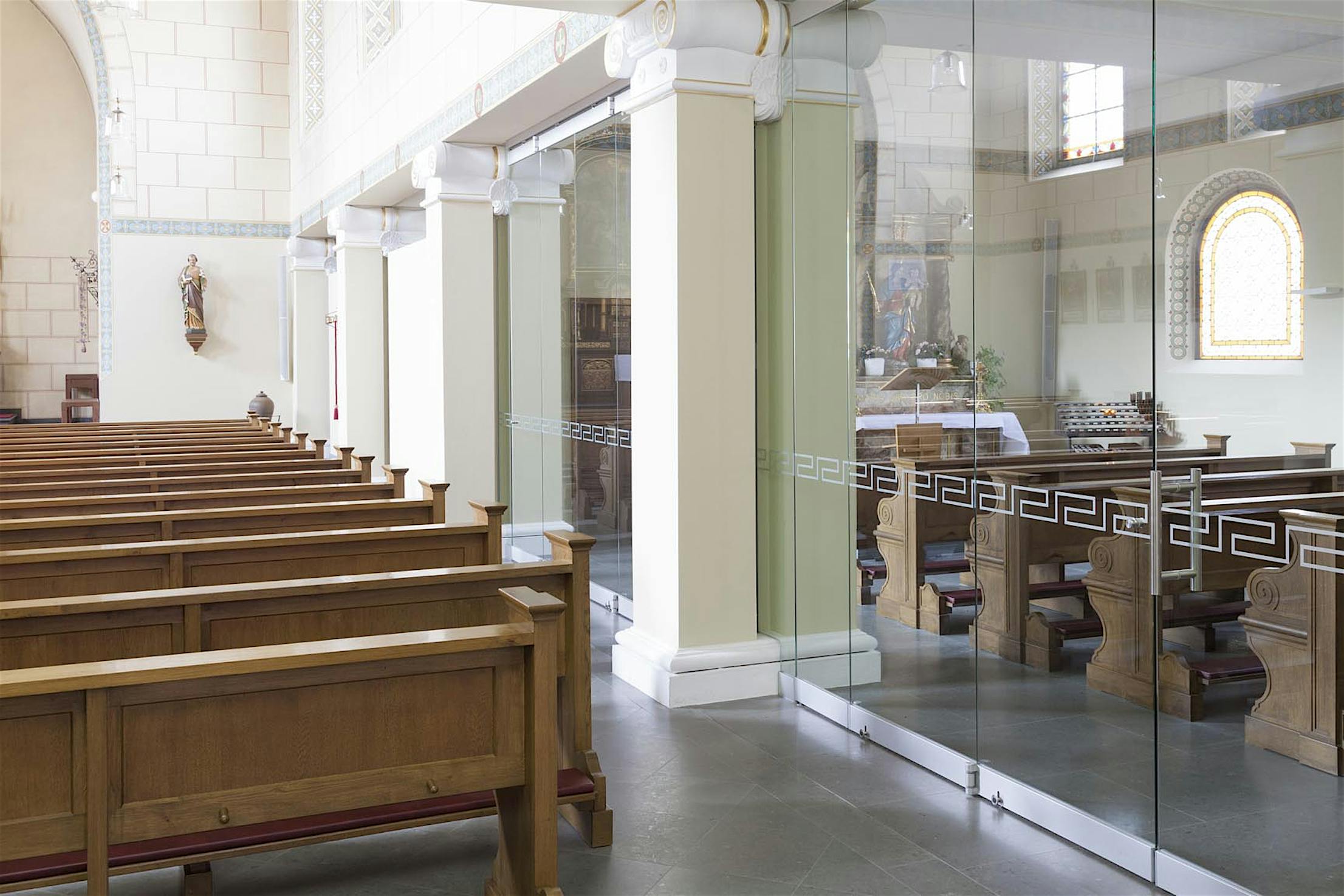
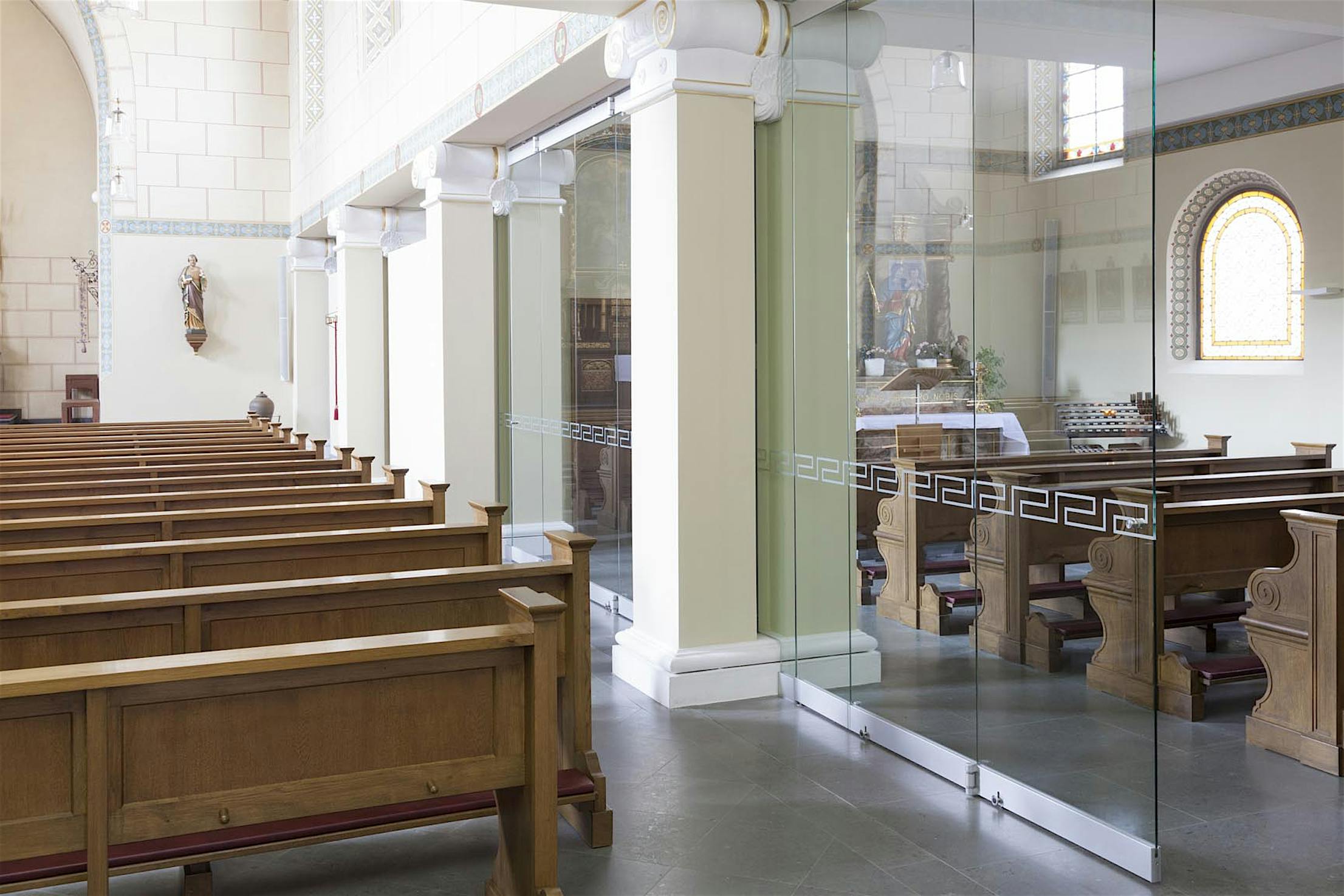
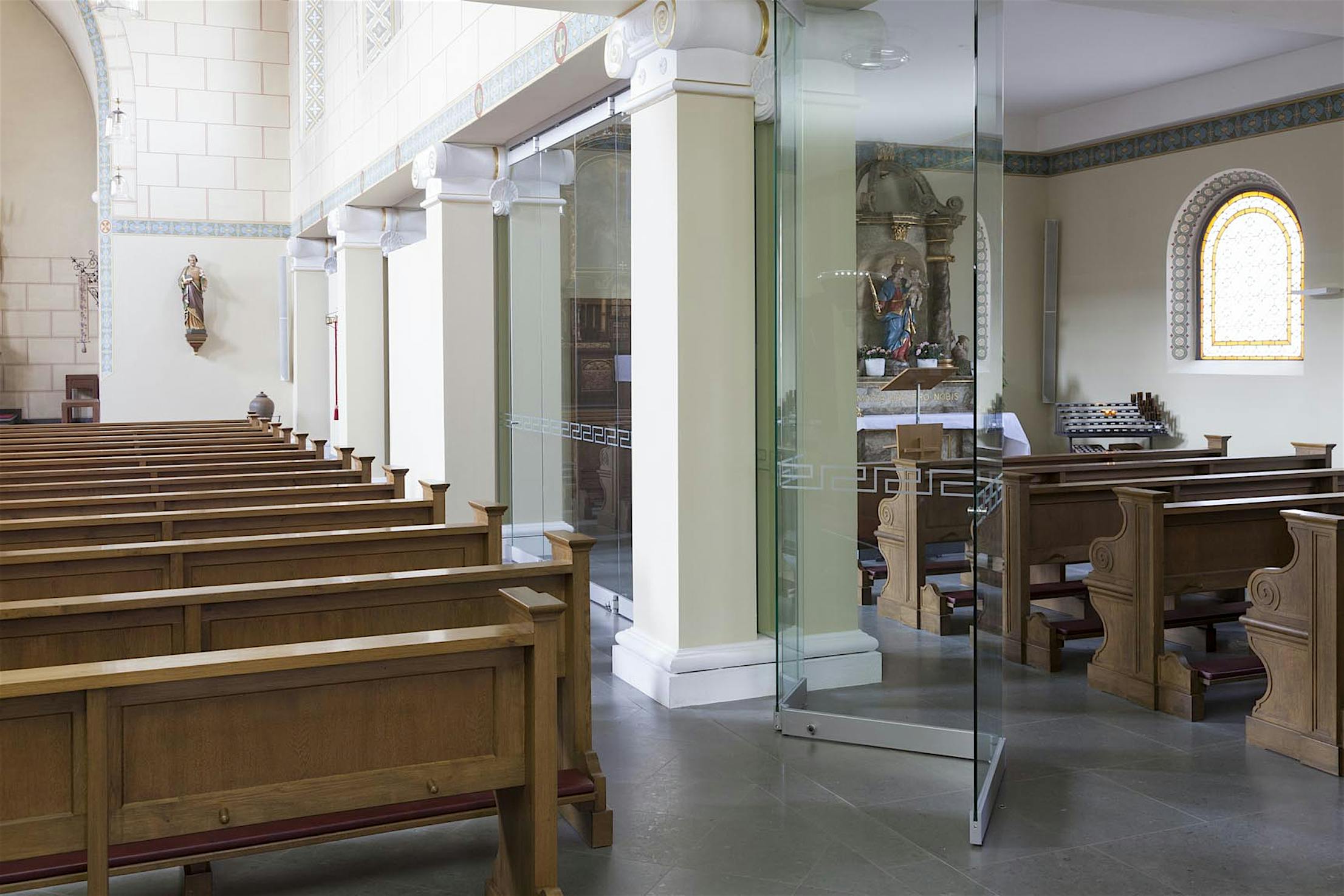
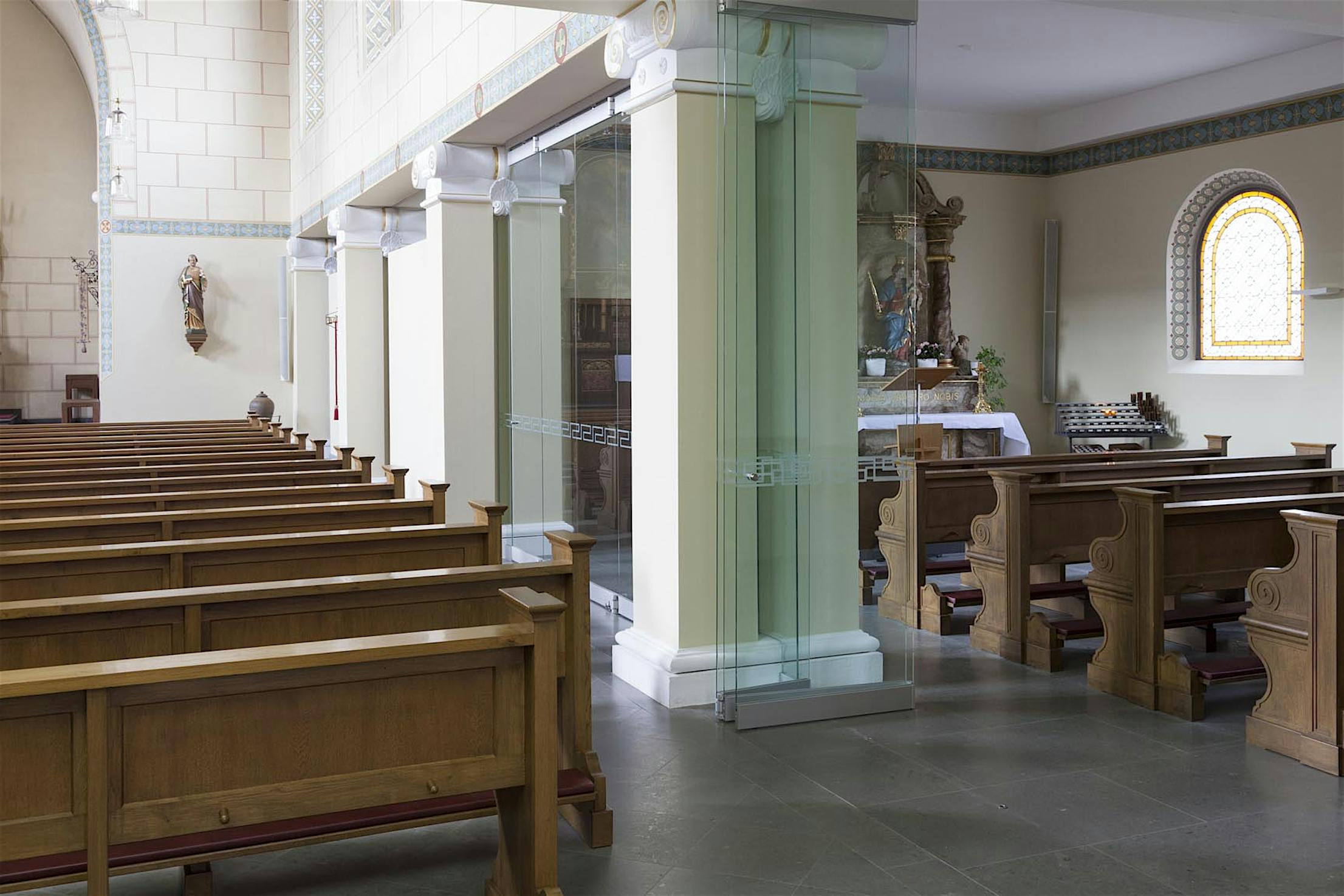
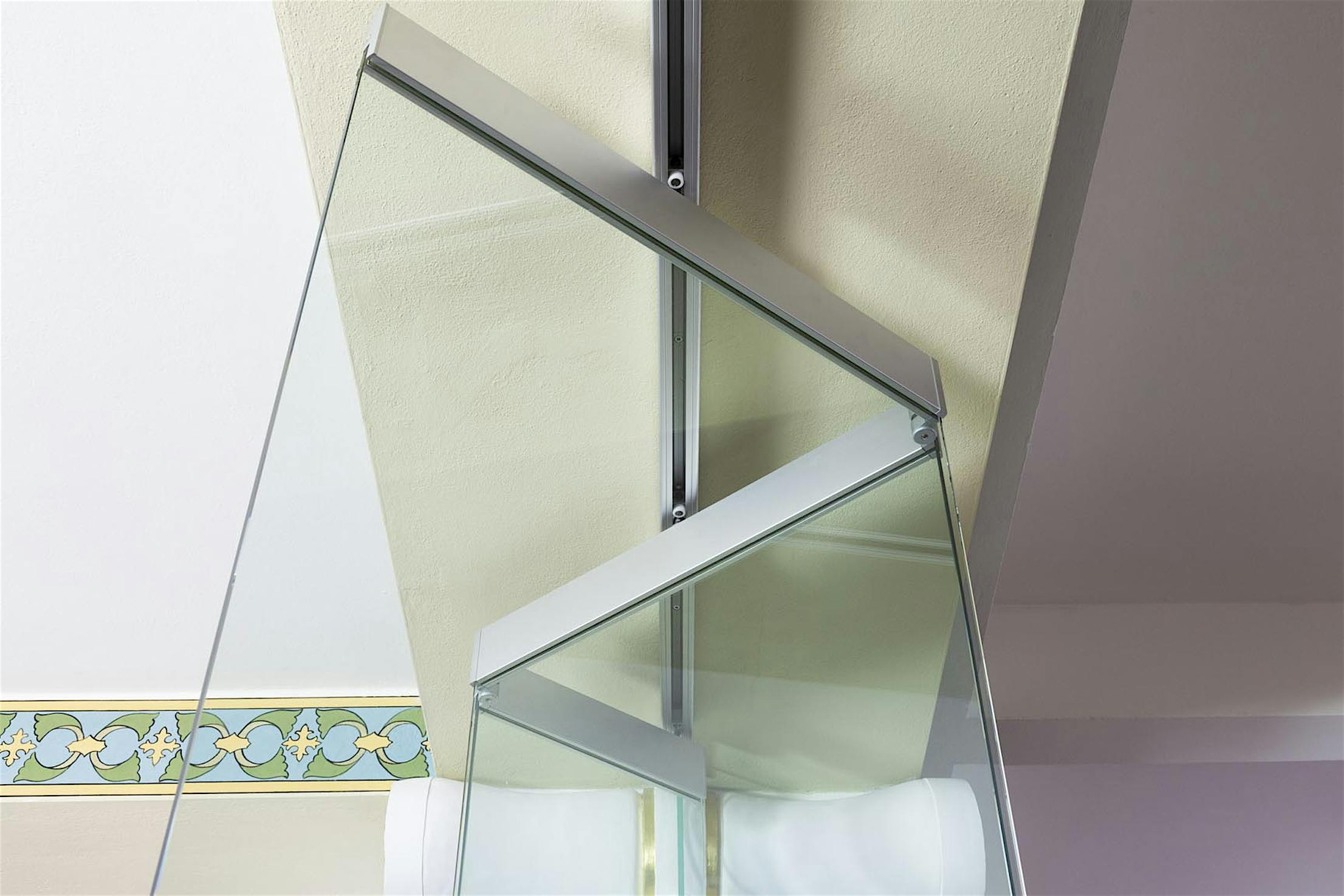
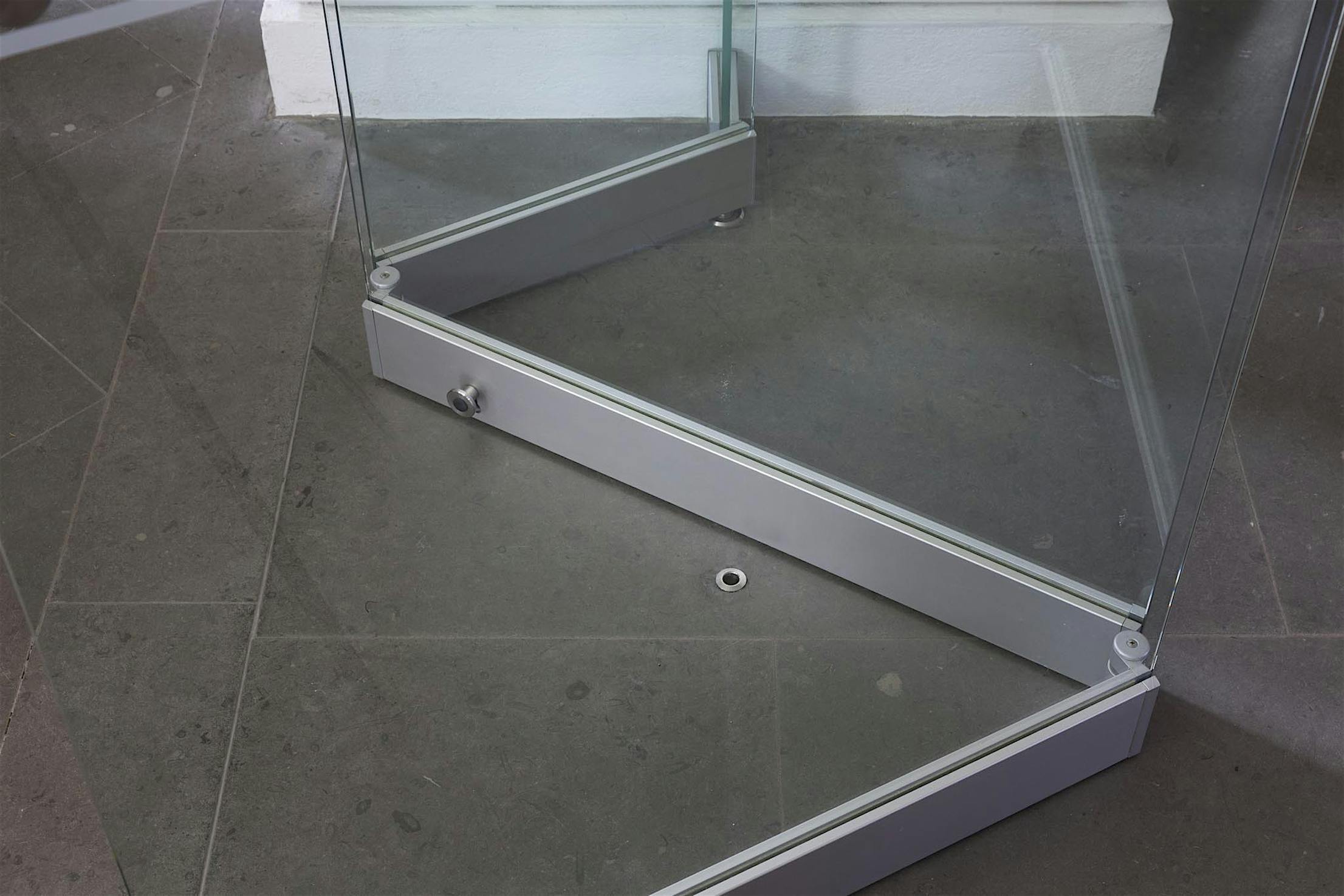
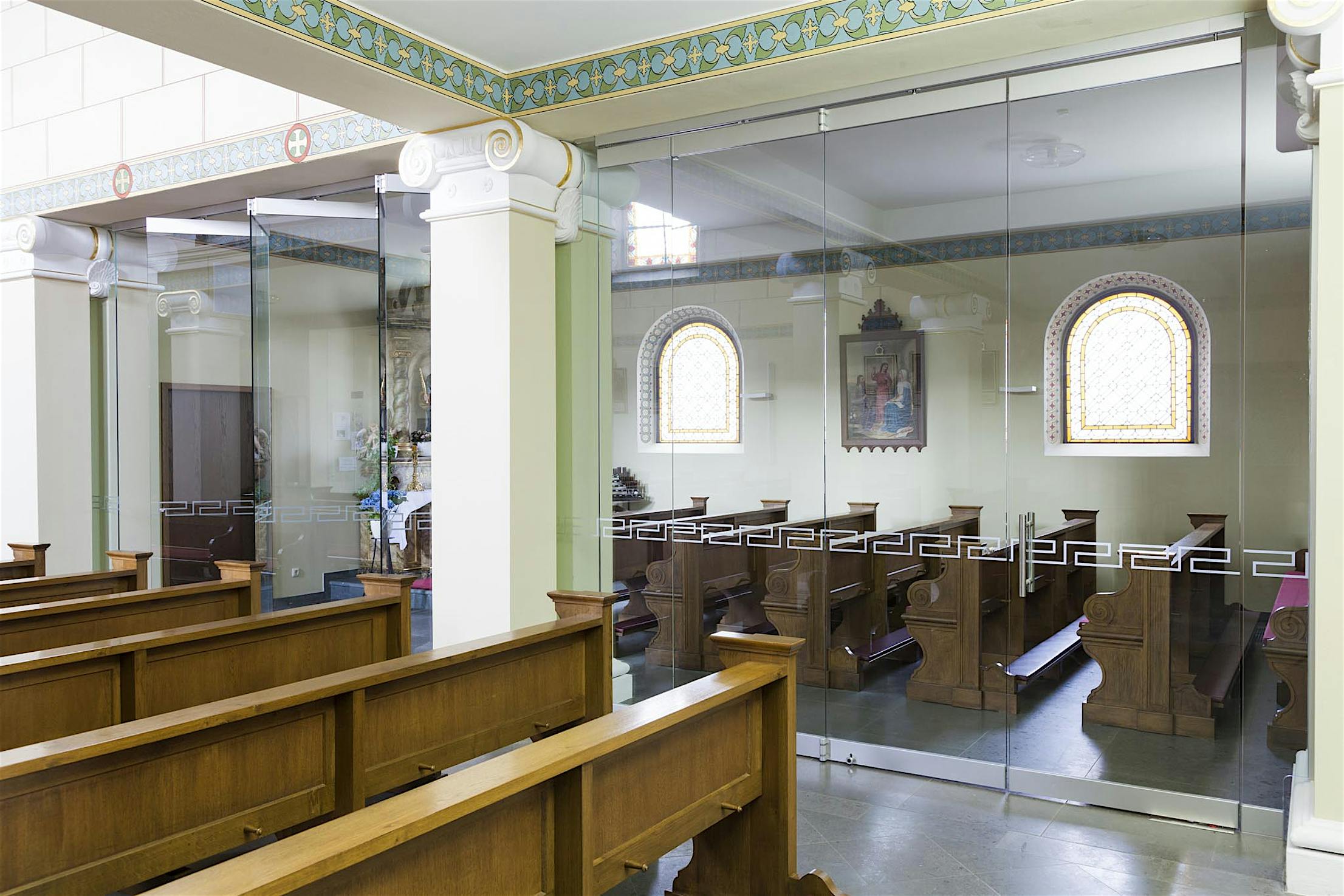
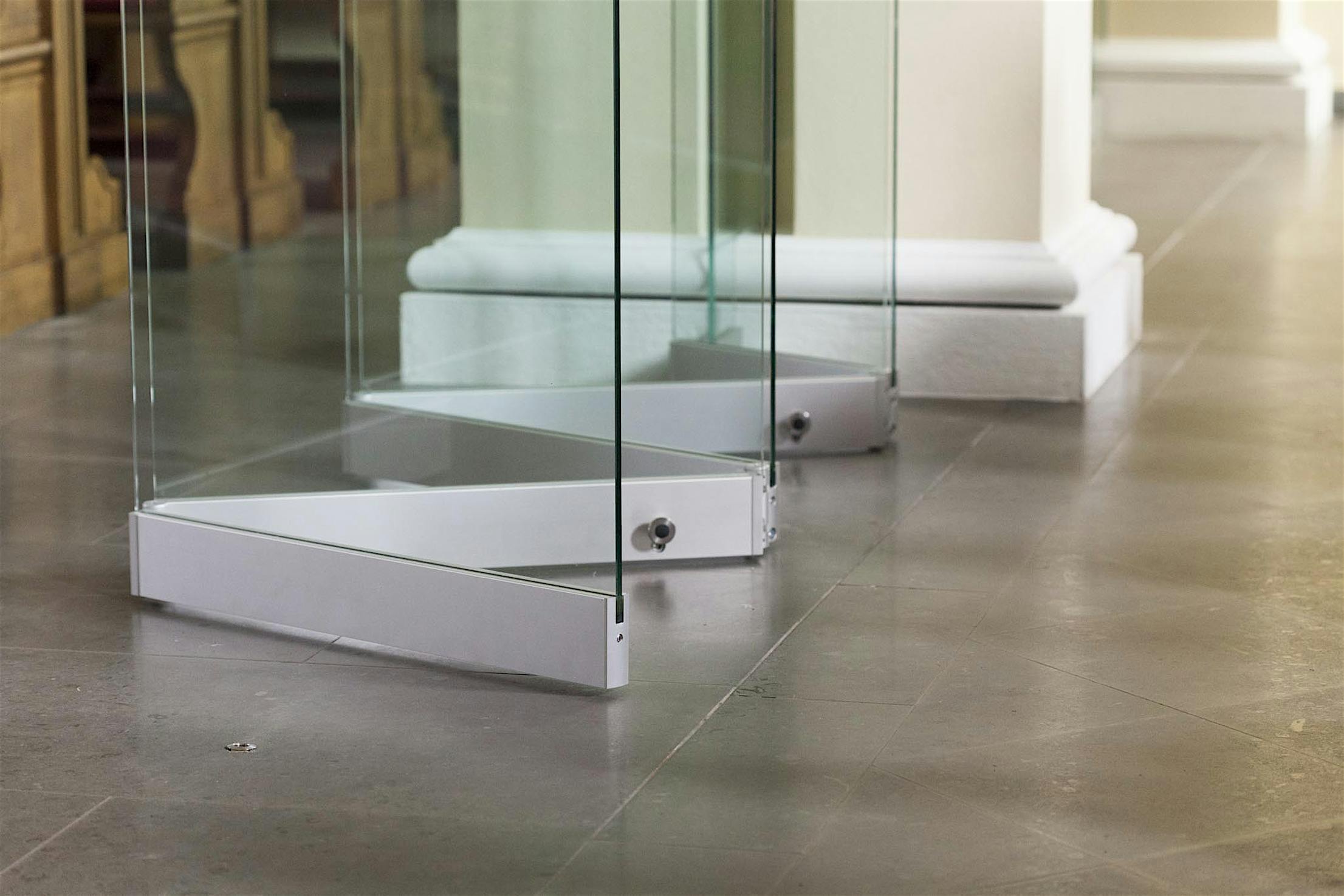
Ease of Operation
NanaWall systems offer single-handed operation and move smoothly with little effort
Flexible Configurations
Design with no limits – our glass walls can be tailored to your imagination.
Interior Ready
Sill options designed specifically for interior applications.
Sustainable Design
NanaWall products contribute to multiple LEED rating systems and potentially several credit categories.
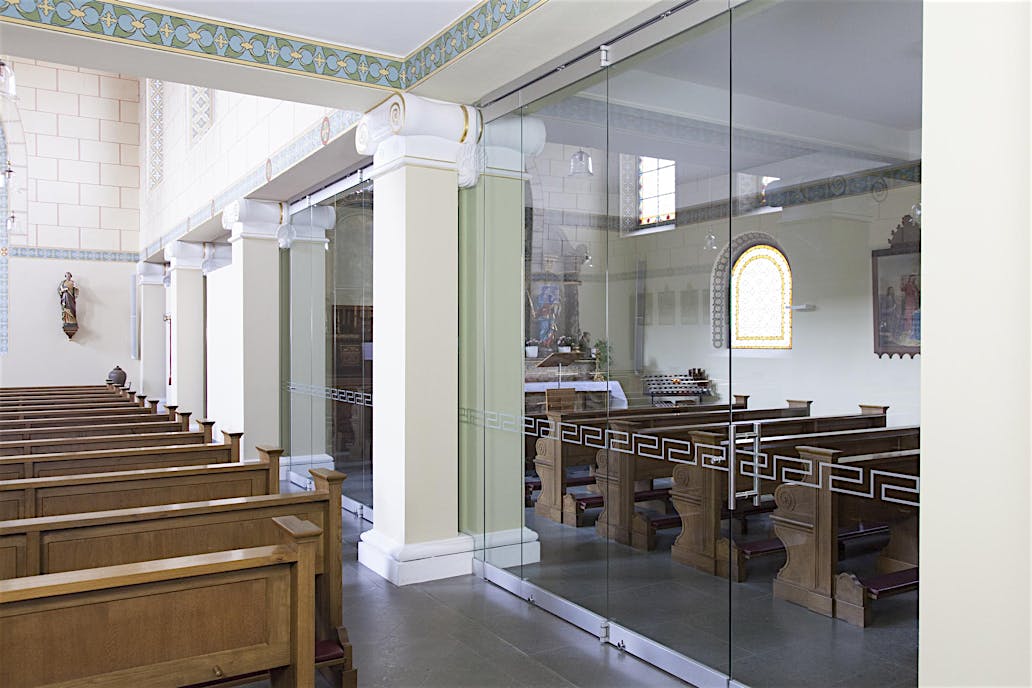
100,000 Cycle Testing
Single/double action panels with pivot points have passed 100,000 cycle testing.
Cycle testing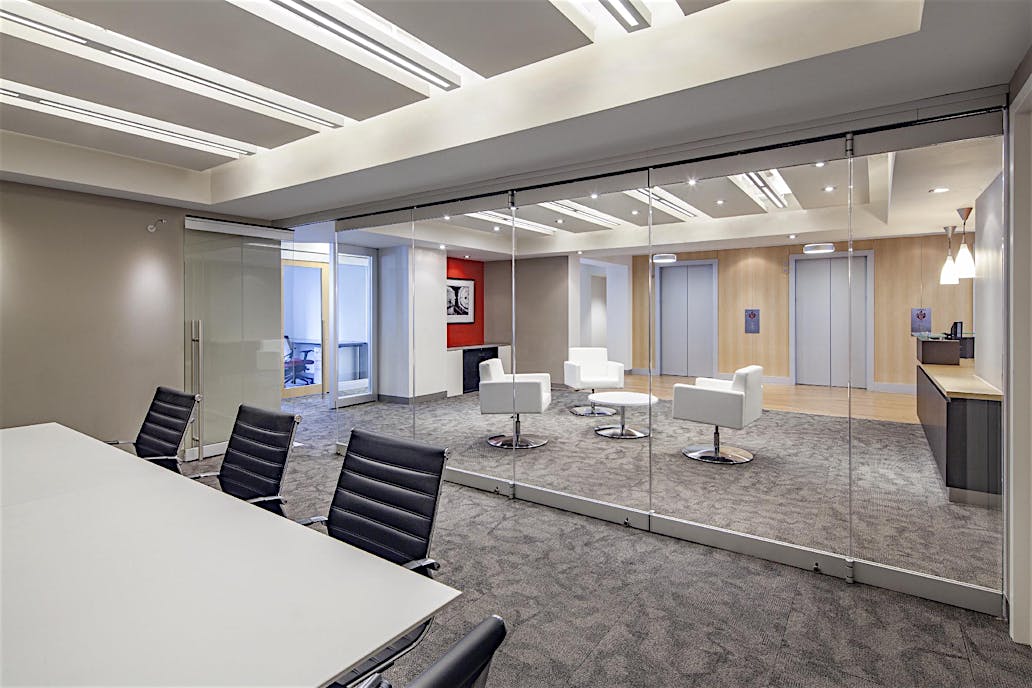
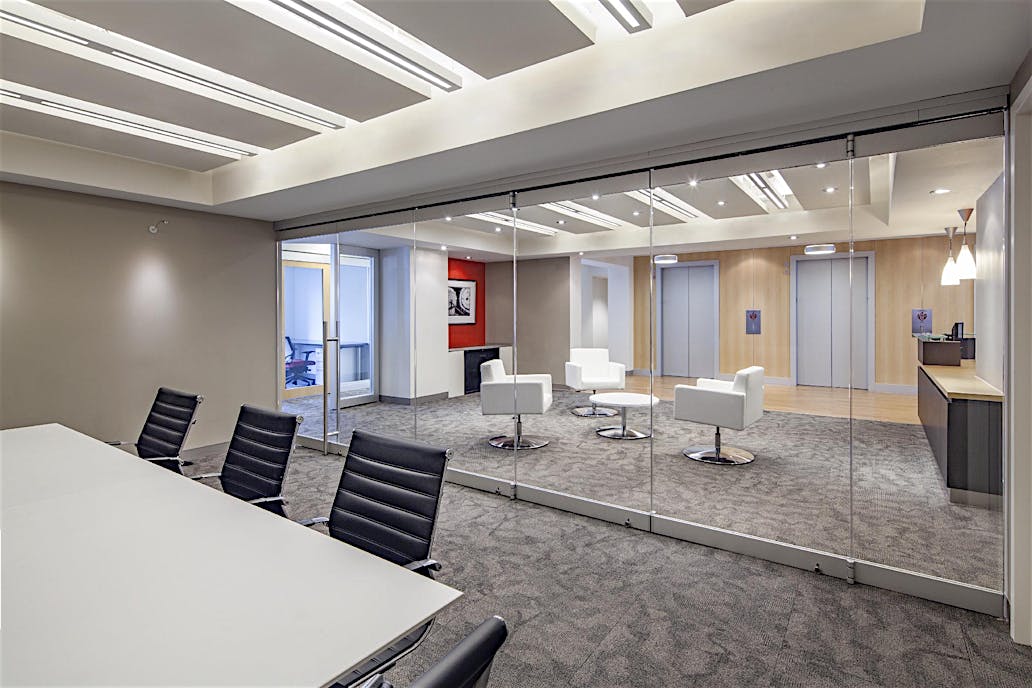
Performance When Closed Matters Most
Large openings are easy to design and there are many options to choose from. When deciding on a product that best for your project, performance when closed needs to be considered
What Our Customers Have to Say
Helios
In a tenant improvement, available space is finite, and at a premium. See how to transform space, on demand, into different-sized rooms with different functionalities.
Dairy Farmers of America
By designing the conference room with PrivaSEE, this office achieved a space with a high degree of acoustic privacy, while maintaining a sense of openness.
"The nicest meeting room we have in this building is the [PrivaSEE] boardroom."
— Architect
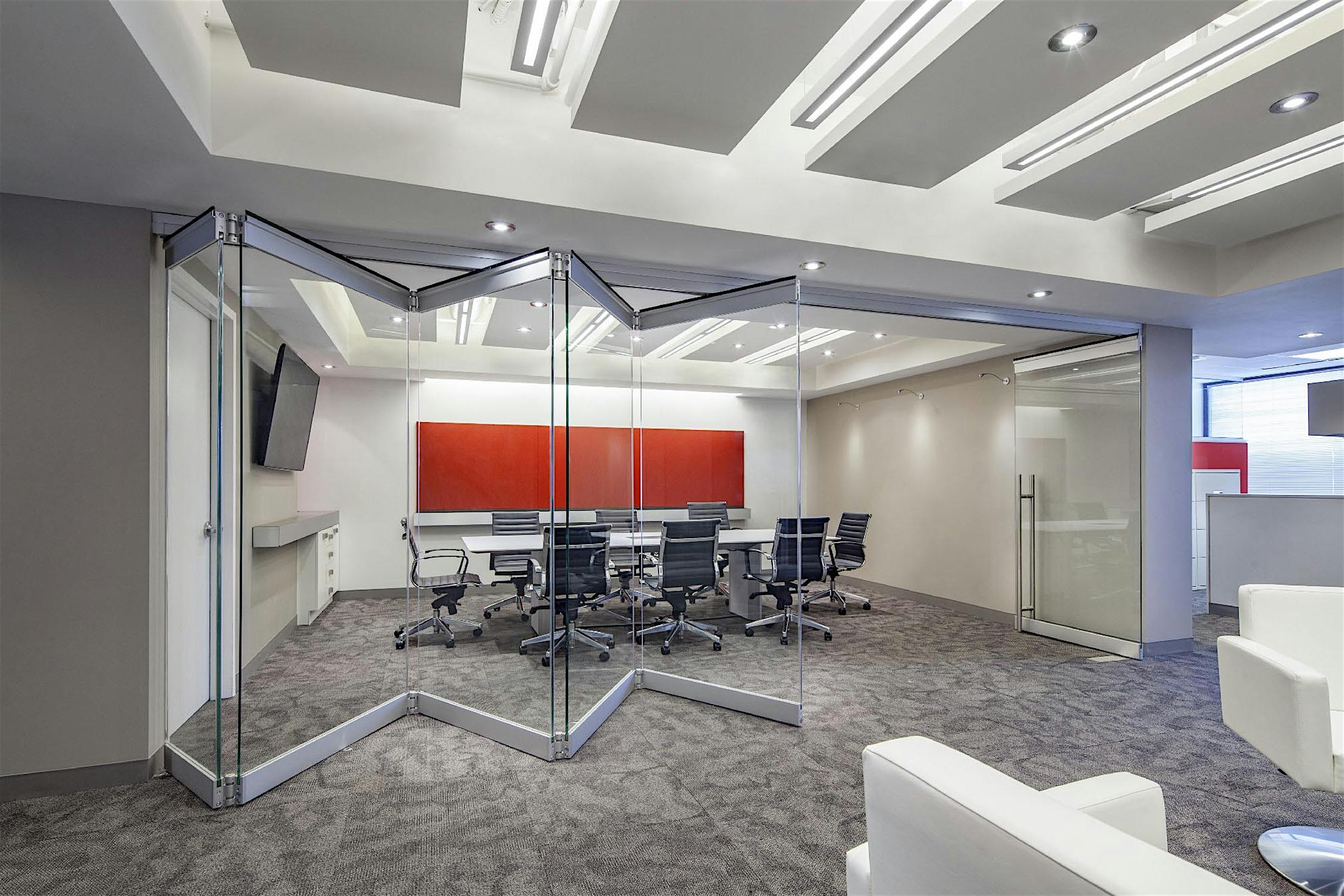
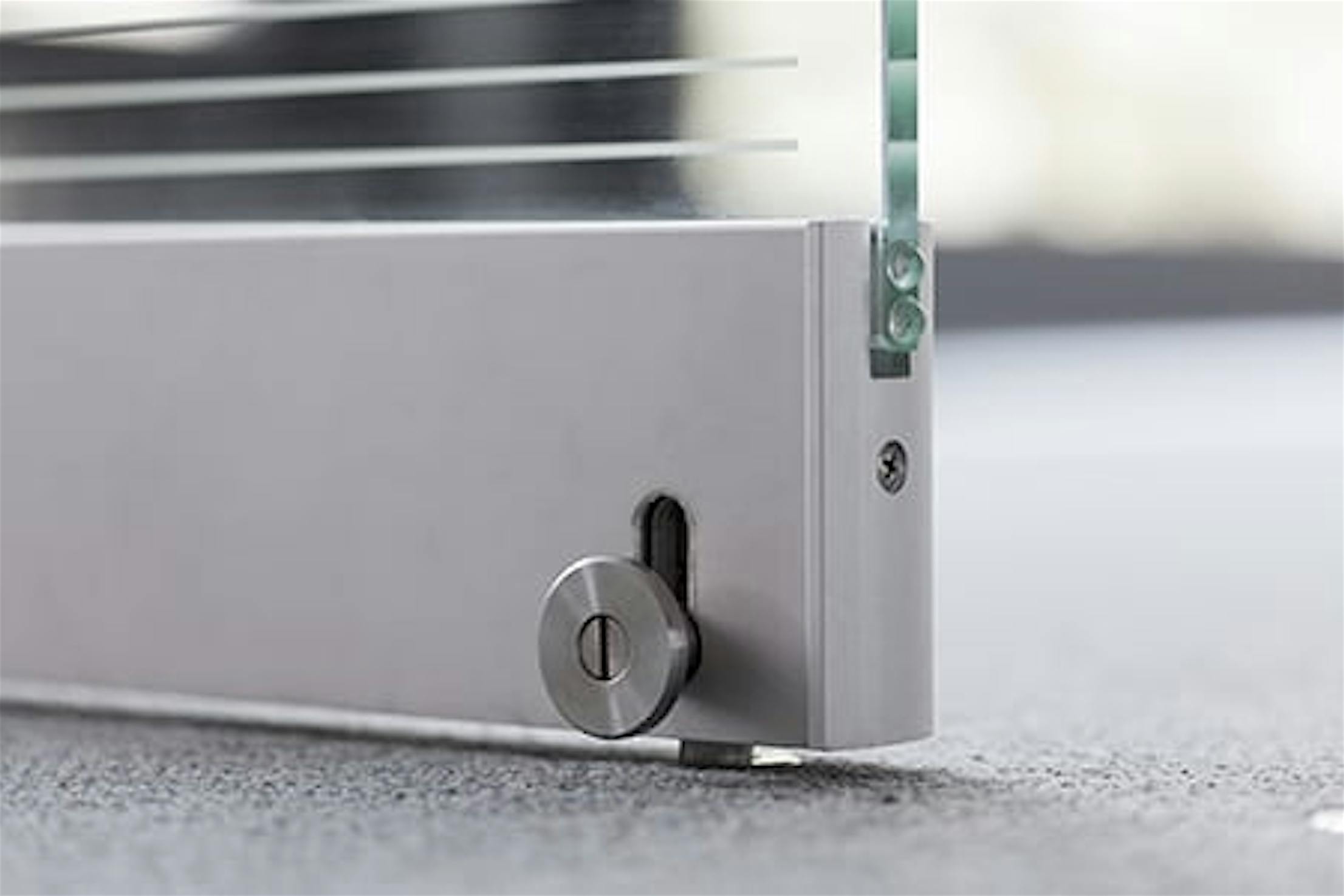
Quick release floor bolt with spring loaded security feature, floor bolt with profile cylinder, TUBO 100.
See Locking OptionsStainless Steel Lever Handles
See Handles Options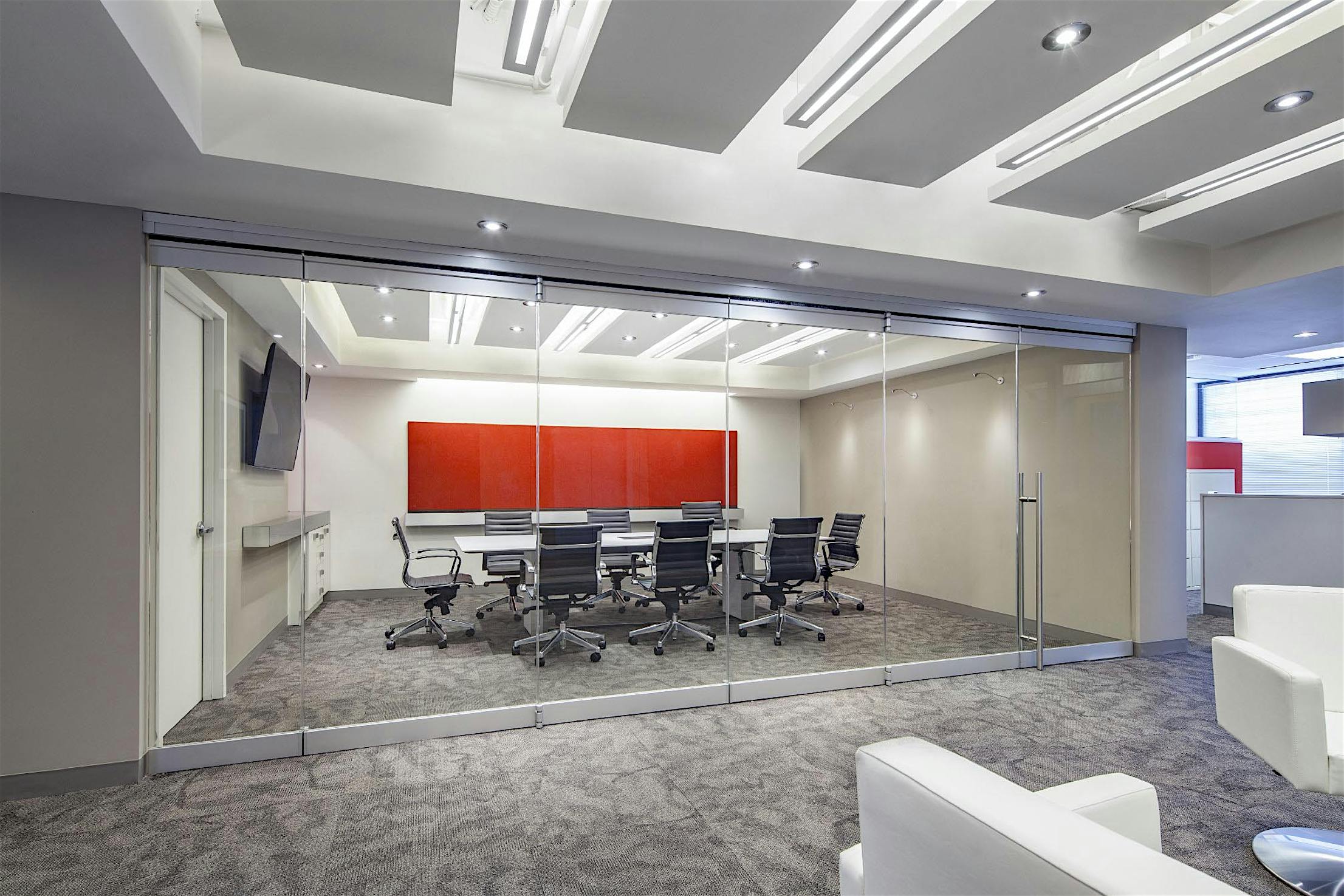
Standard glass thickness supplied is 1/2" (12 mm) tempered or (12.52 mm) laminated. To reduce glass stress, glass is clamp installed for equal distribution of weight.
An optional white interlayer can be added for the closed panels to be used similarly to a white board. Additional glazing options include low iron or decorative glass. All glazing is reduced iron. Please contact NanaWall Systems for more details.
See Glazing Options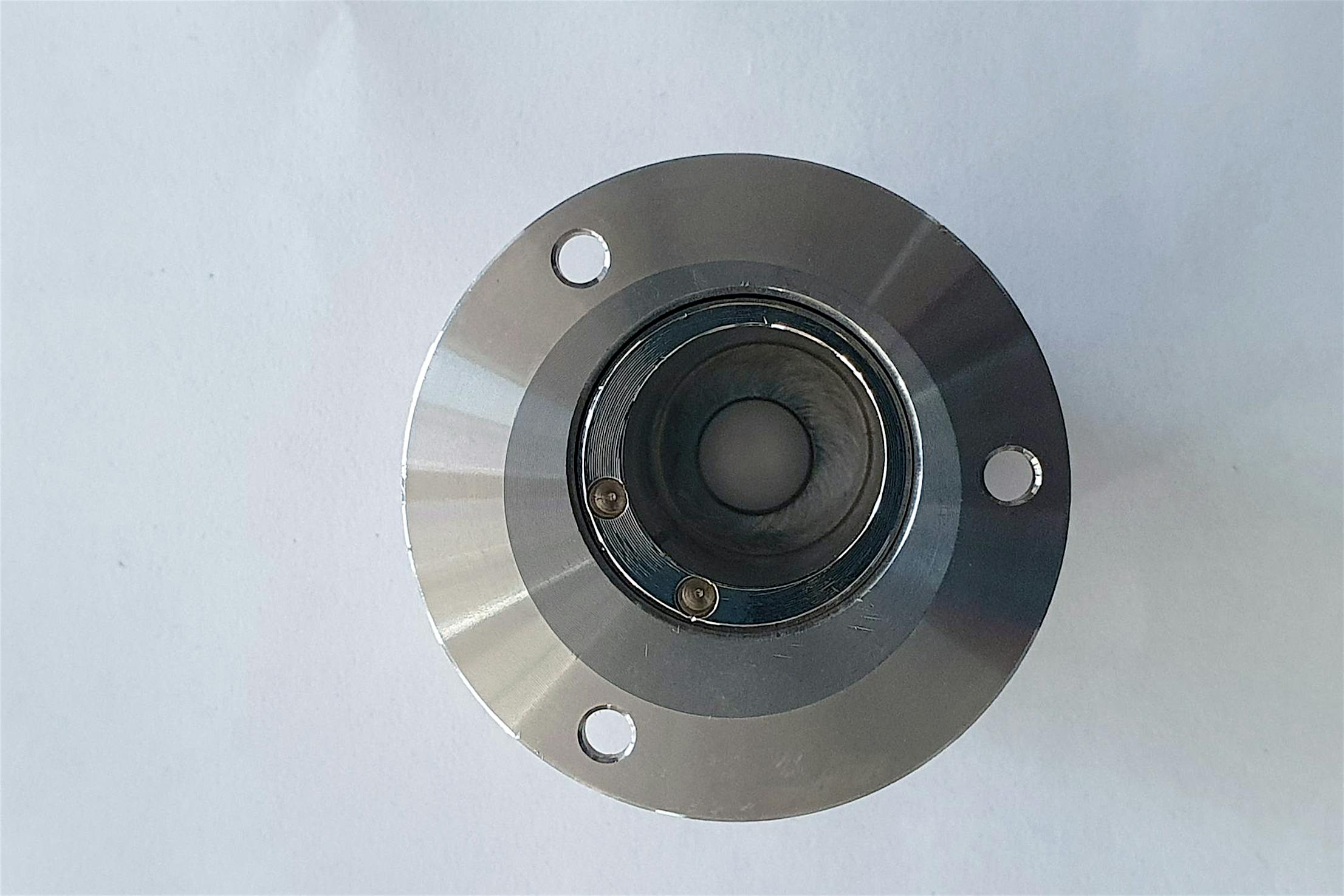
CSW75 options : Adjustable Floor Sockets.
See Sill OptionsAll standard configurations.
Explore limitless possibilities with our systems. Design and customize systems using our 3D CAD/Revit/Spec Configurators or contact our dedicated design team for more possibilities.
More Configurations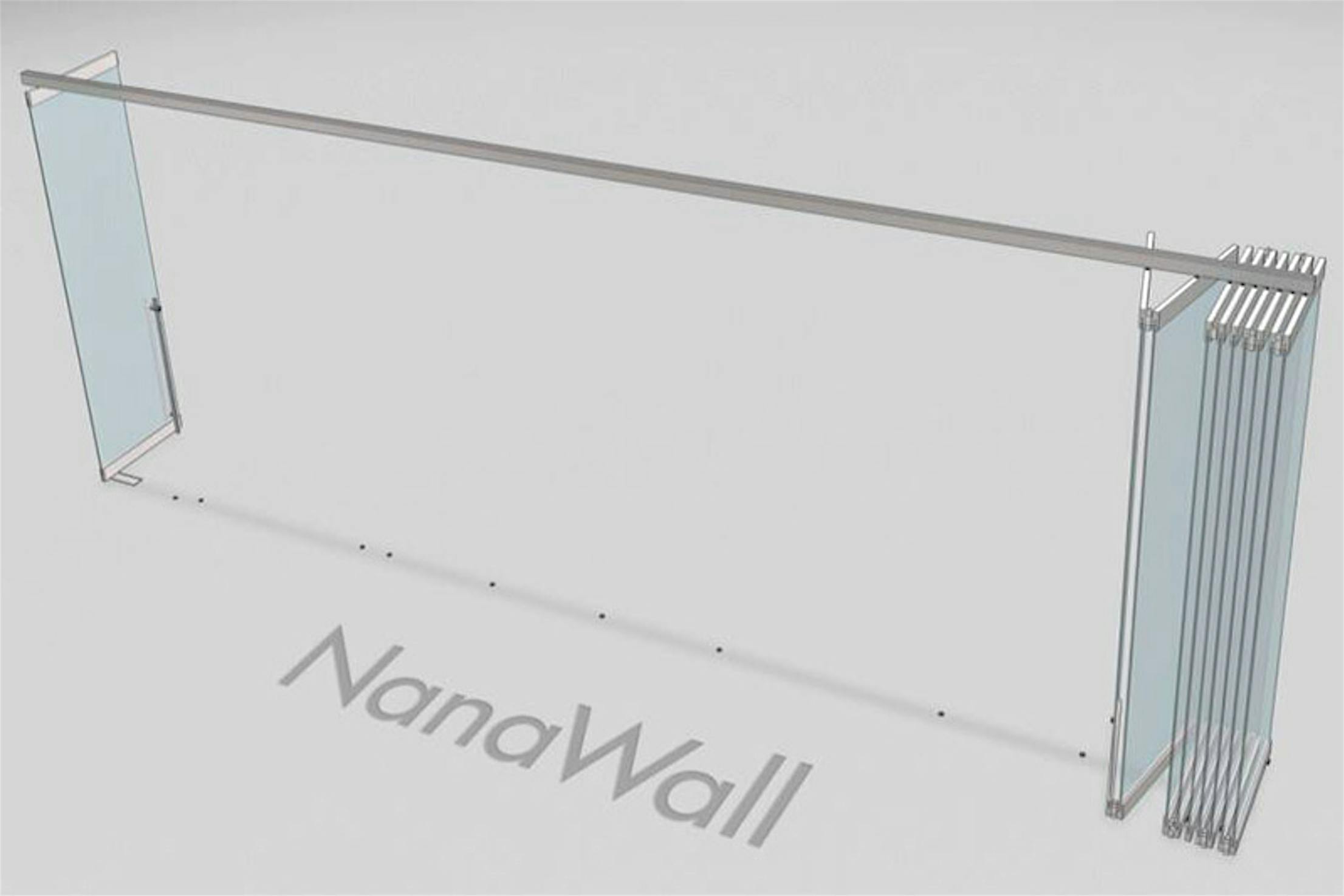
Explore limitless possibilities with our systems. Design and customize systems using our 3D CAD/Revit/Spec Configurators or contact our dedicated design team for more possibilities.
More ConfigurationsWe consider ourselves your partners from day one. Connect immediately with a NanaWall expert to answer your questions and explore how we can support your project.
(866) 210-4285
Monday - Friday: 7 AM - 5 PM PST
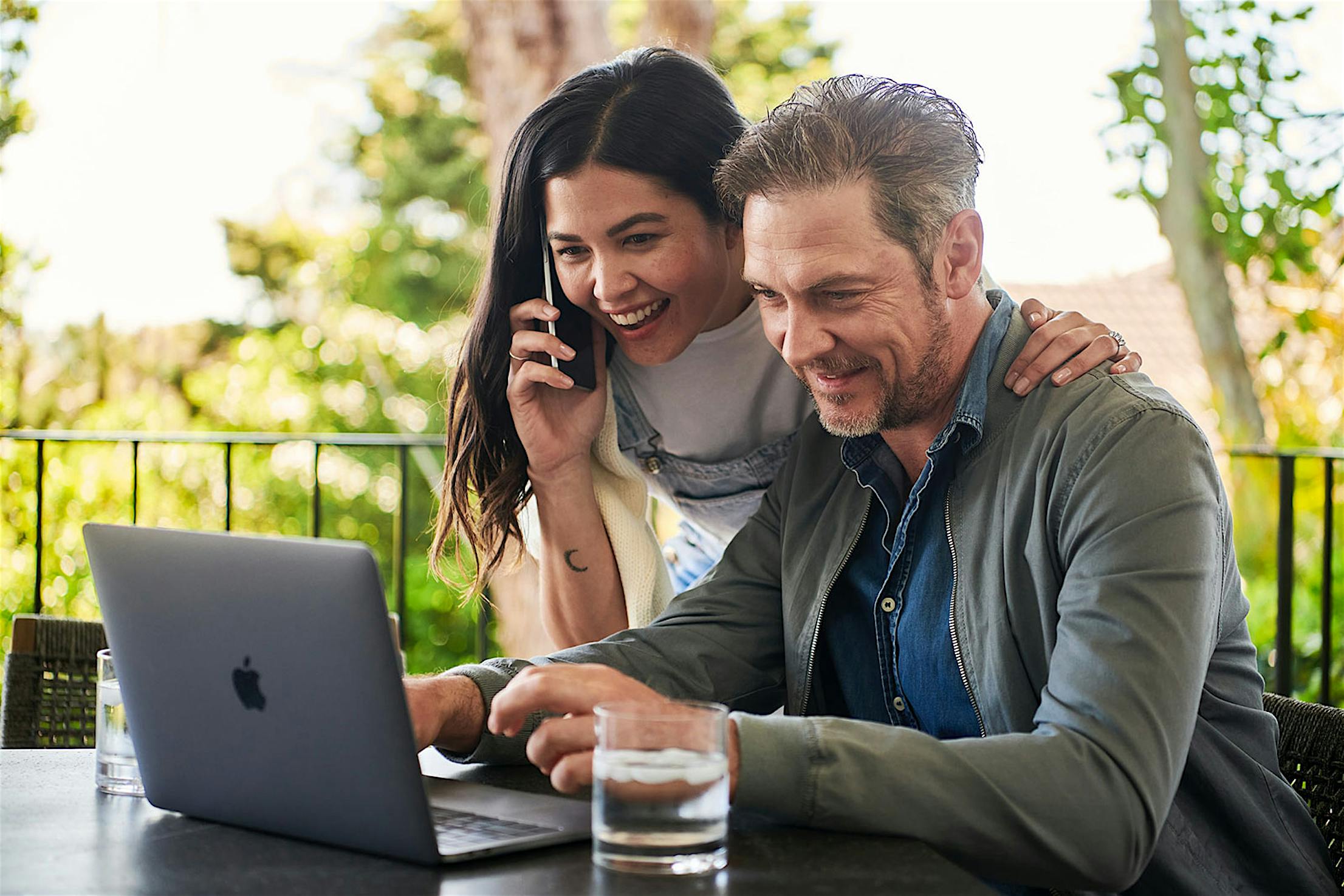
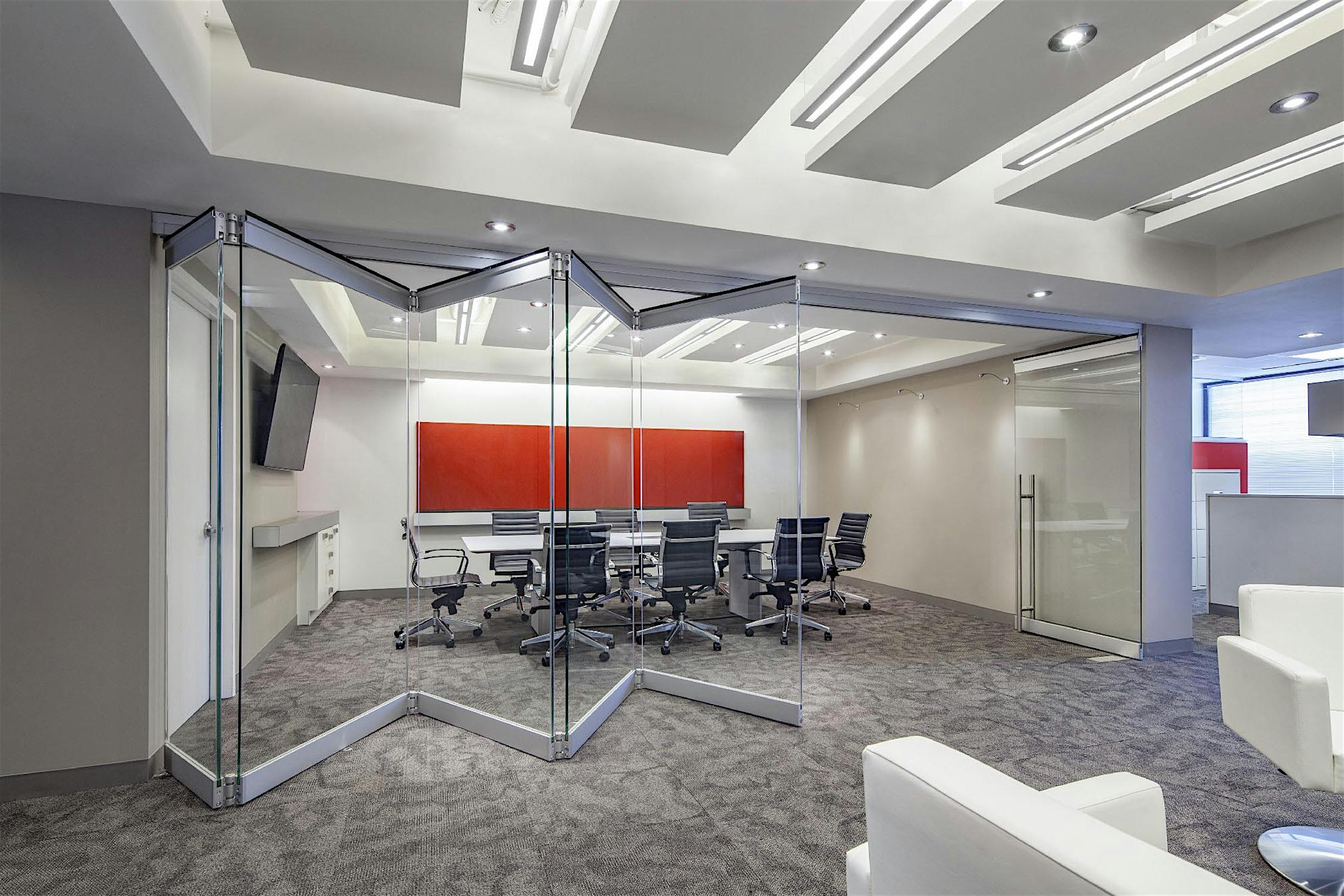
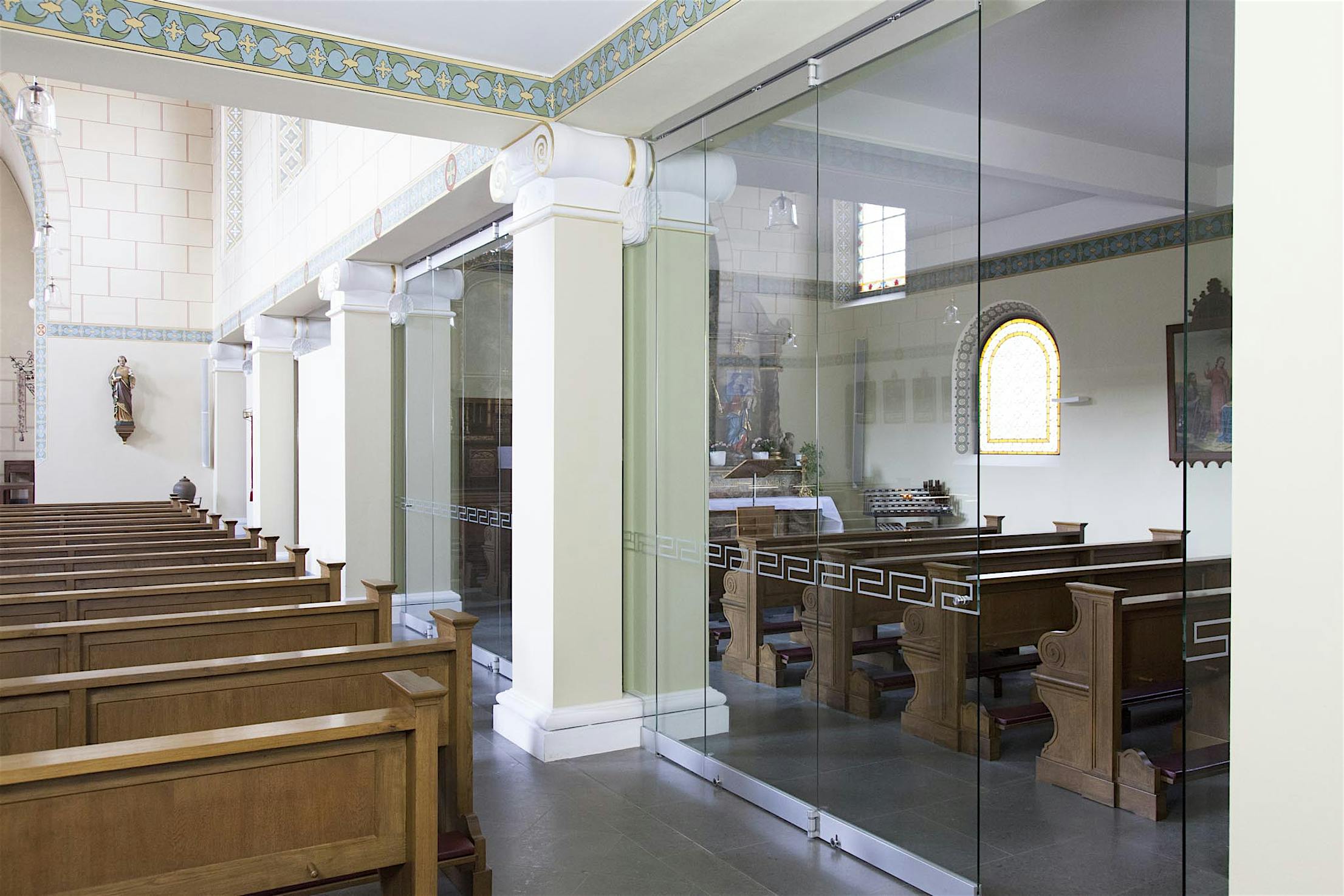
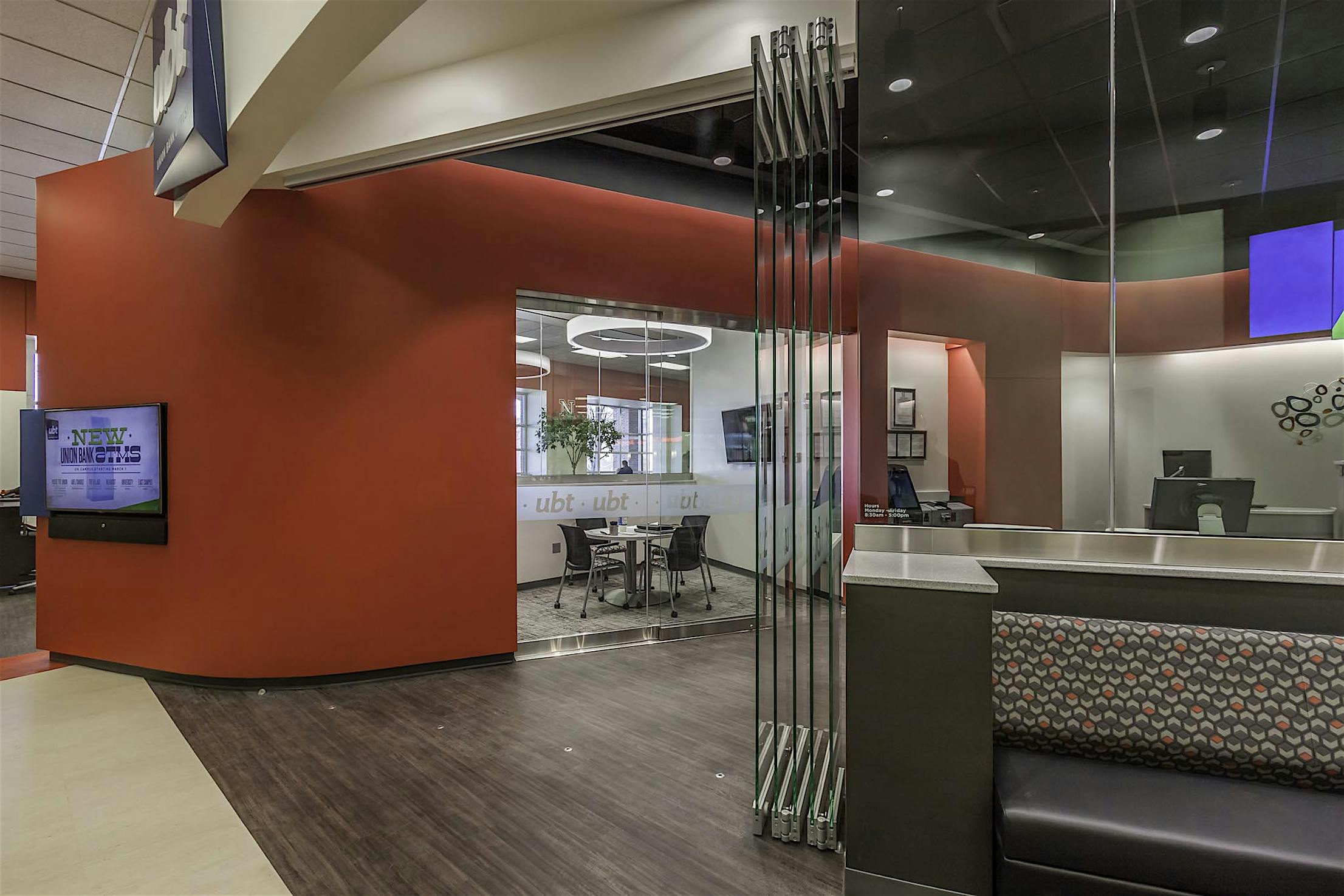