cero
Large Panel Minimal Sliding Glass Walls
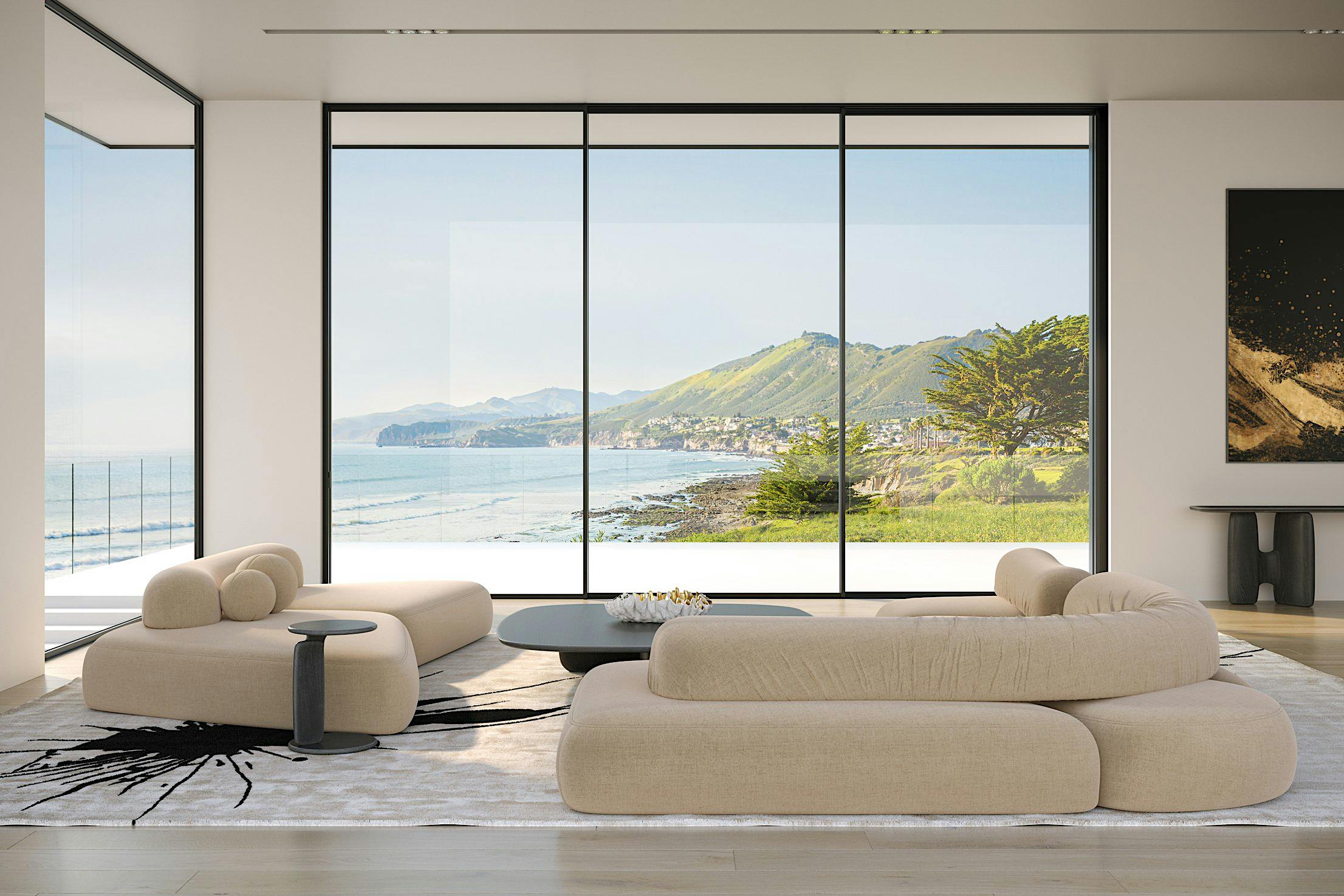
- With the largest panels available in the NanaWall product line, cero sliding panels reach sizes as large as 9′ 10″ (W) x 15' (H) (3000 mm x 4550 mm) for cero III
- cero by NanaWall is architectural minimalism at its finest
- Aluminum framed panels are a mere 1 5/16″ (34 mm) producing clean, uniform, and ultra-thin lines
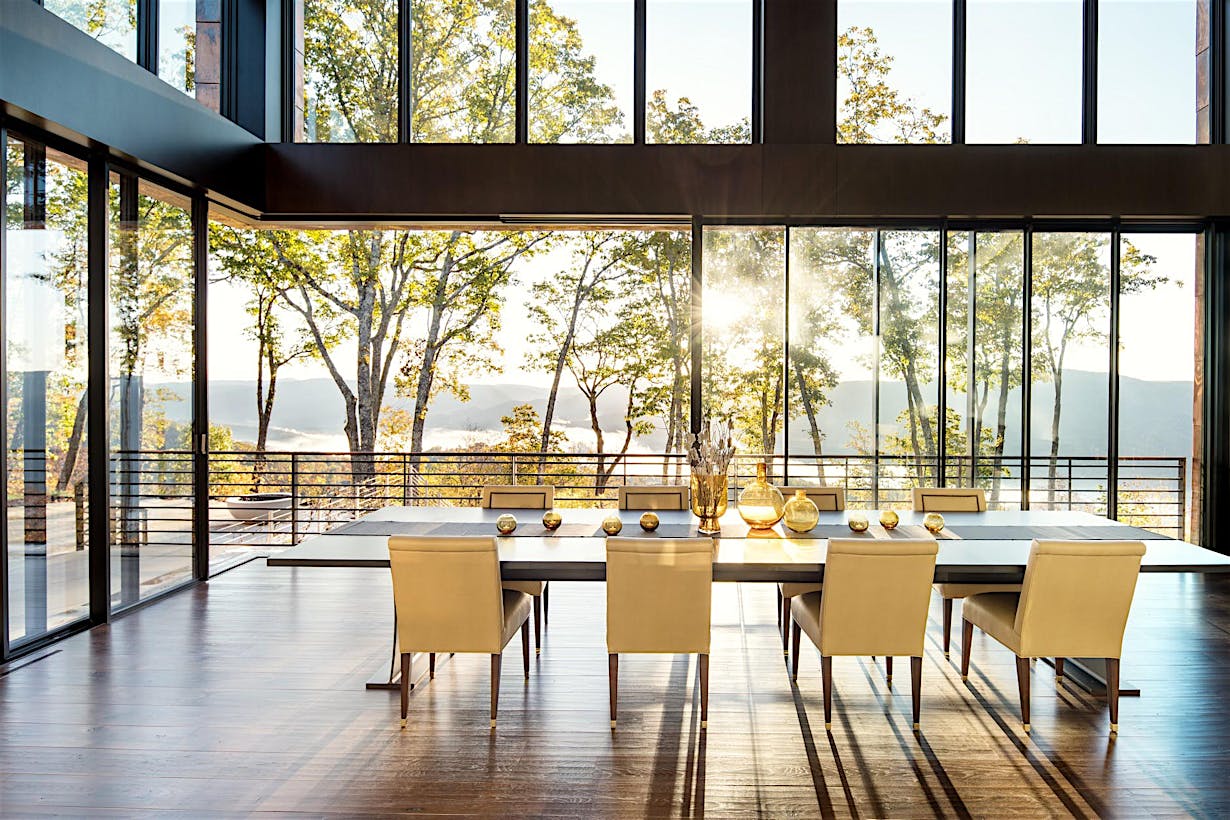
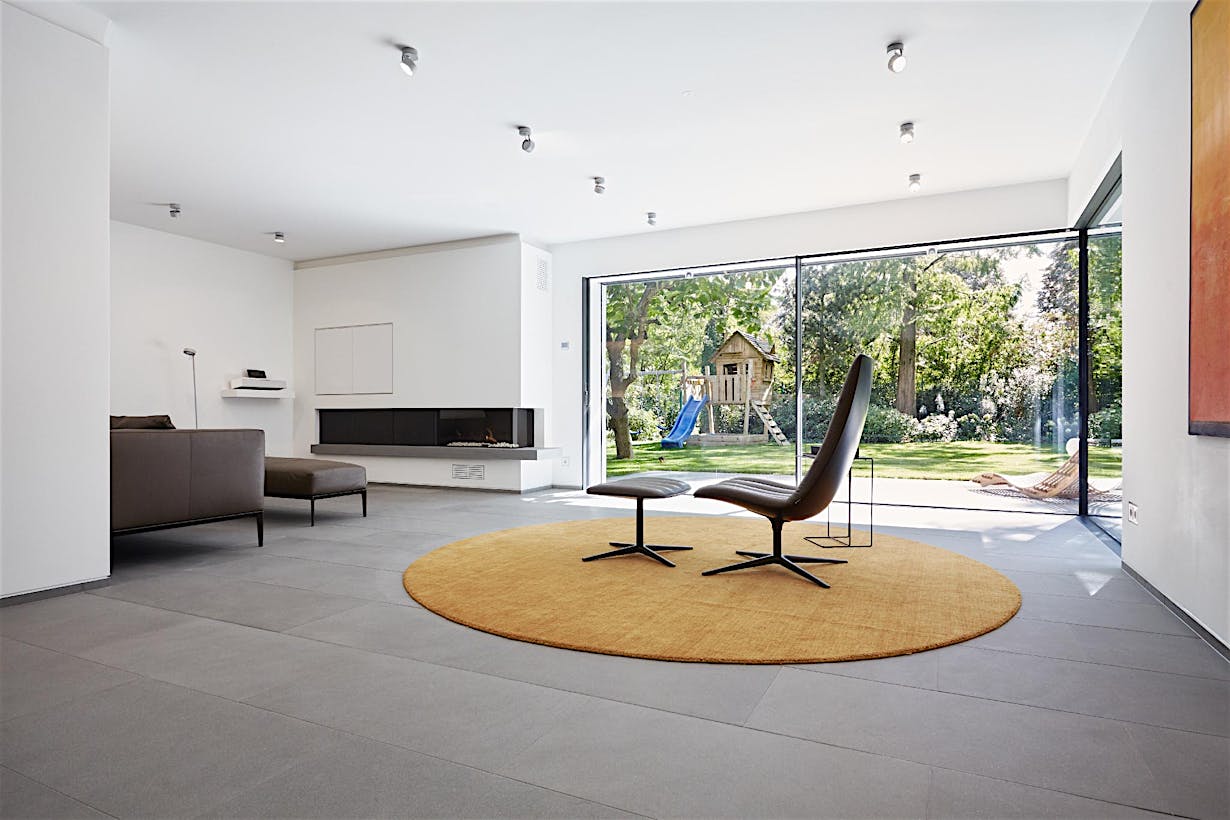
ce•ro (ˈsirō)
noun
The minimal framed large panel sliding glass wall by NanaWall—simple in form yet engineered to perfection. Producing clean, uniform, and ultra-thin lines for maximum light filled spaces that connect the interior to the exterior.
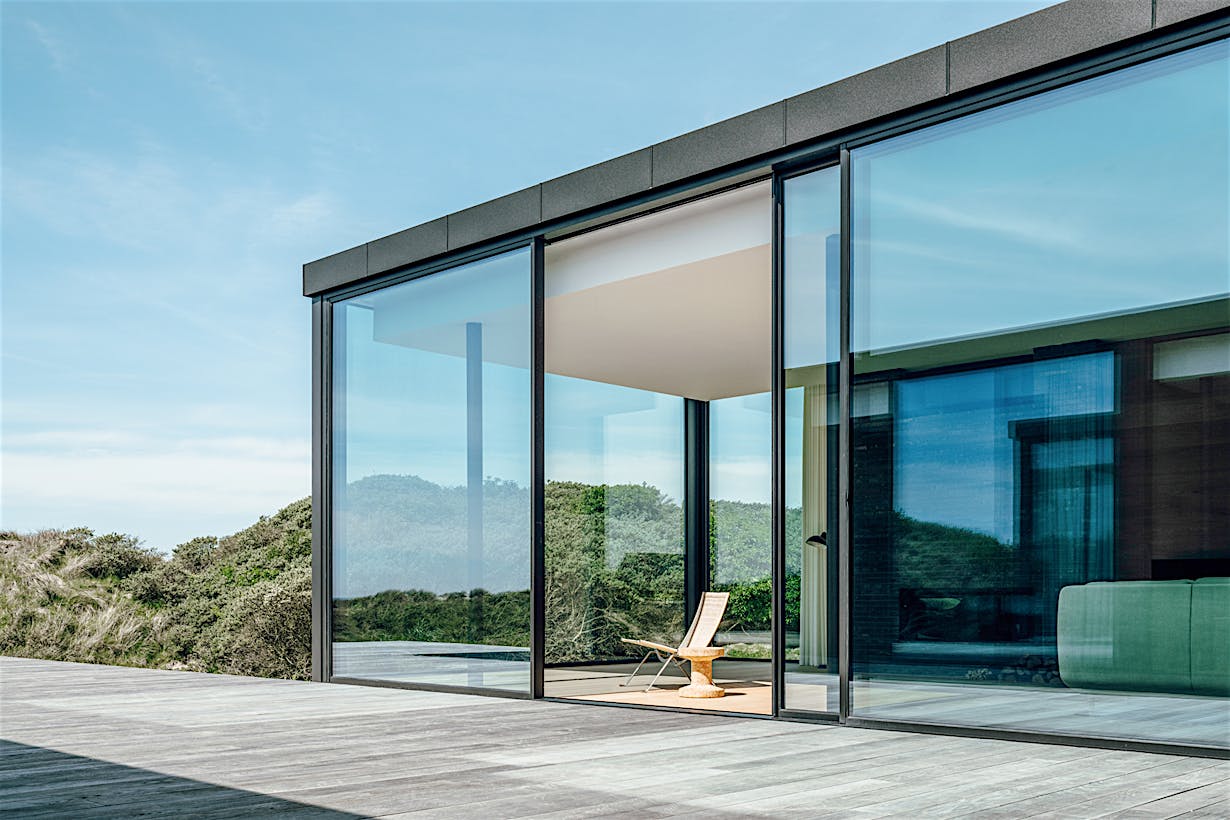
A Floor-to-Ceiling Lens to the Outside
The award-winning cero offers full floor-to-ceiling sliding glass panels with recessed top and bottom tracks. Produced through time-tested premium German engineering, cero allows for maximum transparency with the largest panes of glass and the most minimal frames offered by NanaWall.
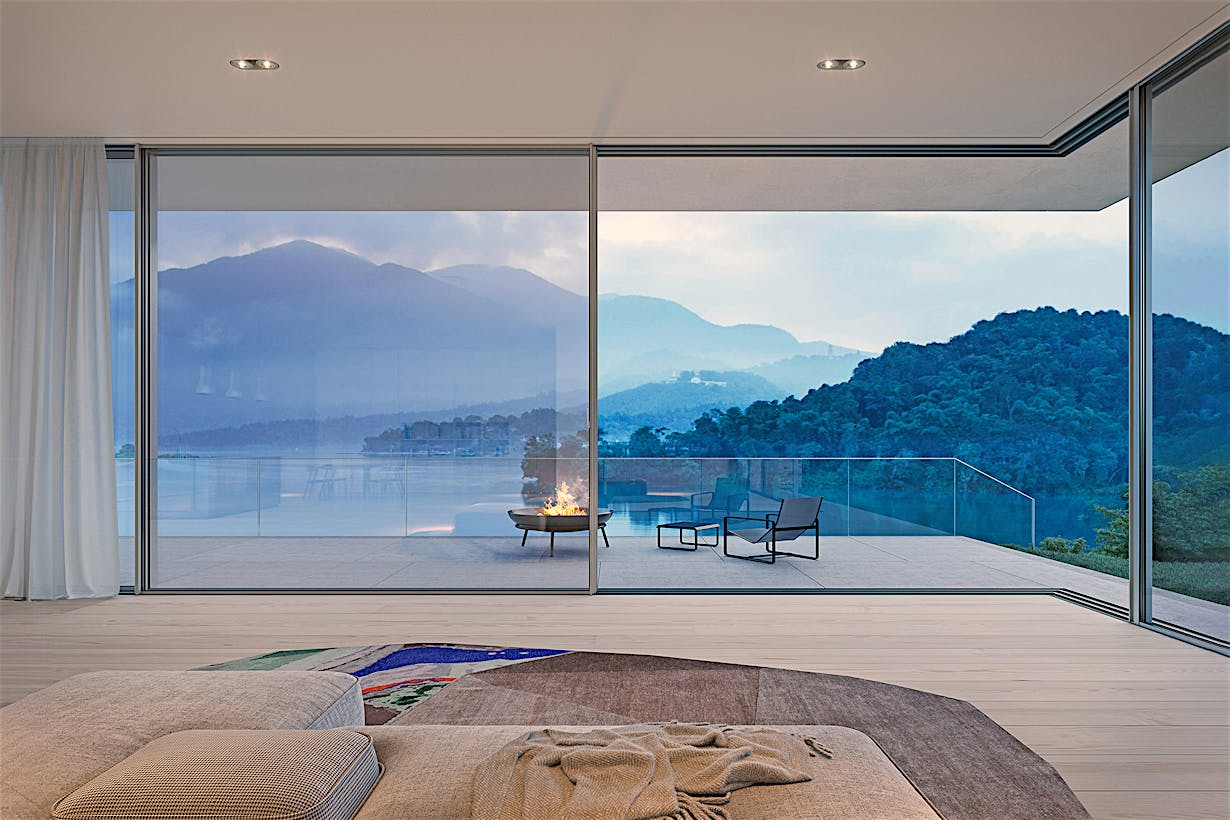
Creative Design Freedom
cero®―absolute architectural minimalism at its finest―questions conventional boundaries. With cero, architectural design is distilled to its most essential elements allowing for light, form, material, space, and nature to speak for itself. Outside and inside become one.
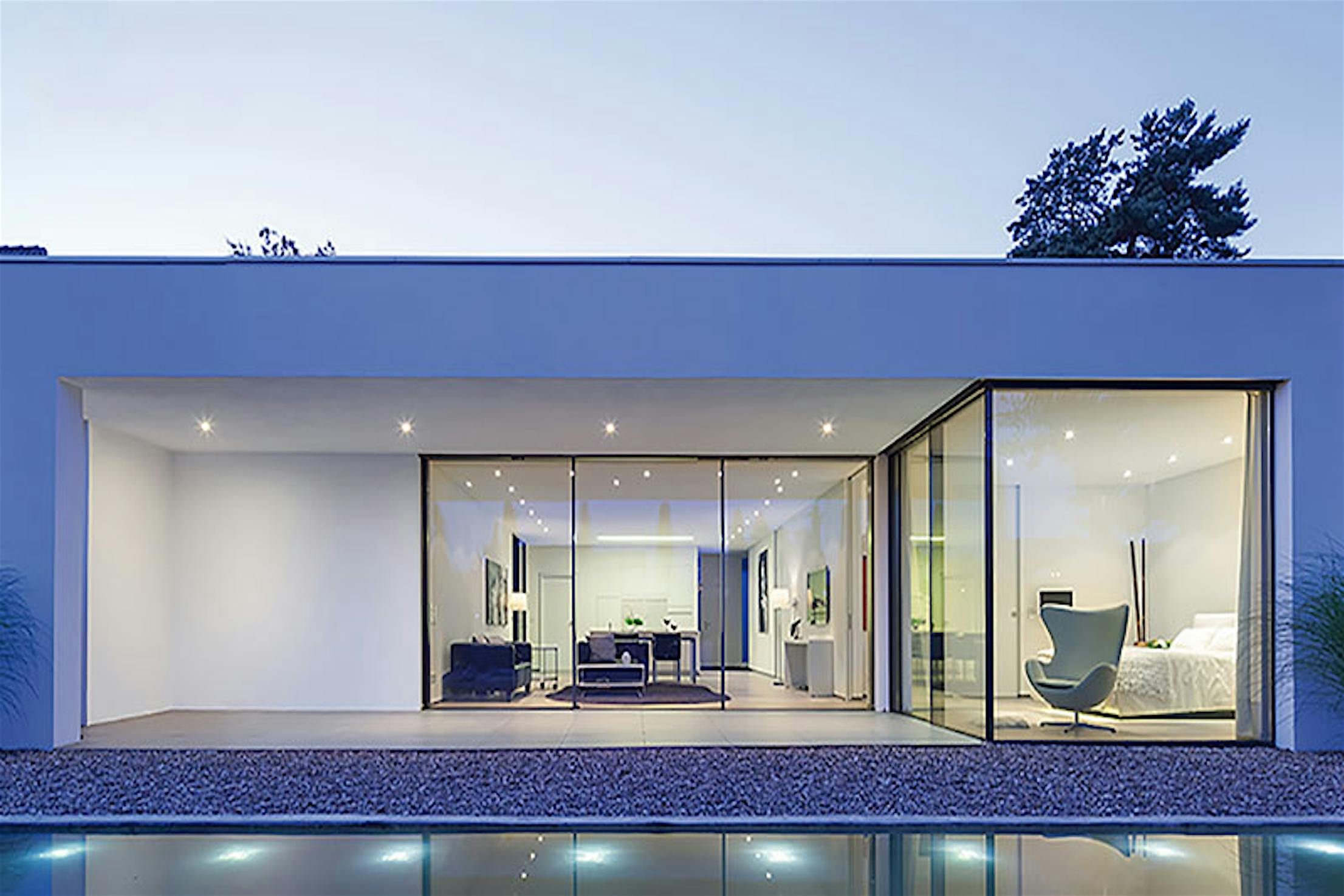
With cero, the panel’s rails and stiles are uniform with a consistent 1 5/16″ (34 mm) top to bottom, side to side, achieving a symmetrical and minimalist design. The result is beautiful sightlines and a 98% glass-to-frame ratio.
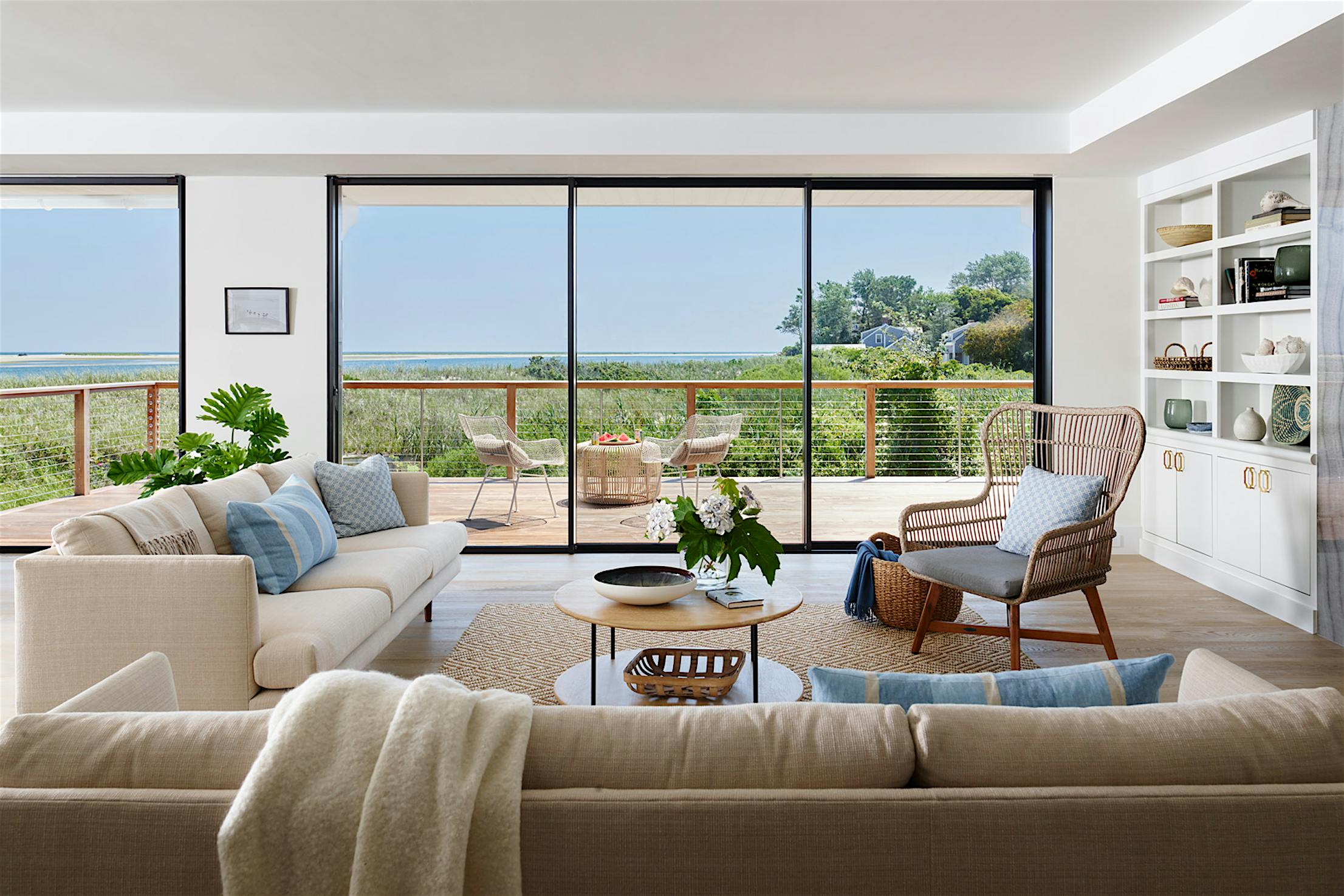
NanaWall's intelligent approach and innovative use of materials reflects a creative integration of design and technology. Within each system component is the NanaWall DNA—meticulously designed and engineered to offer unparalleled quality and durability ensuring systems stand the test of time.
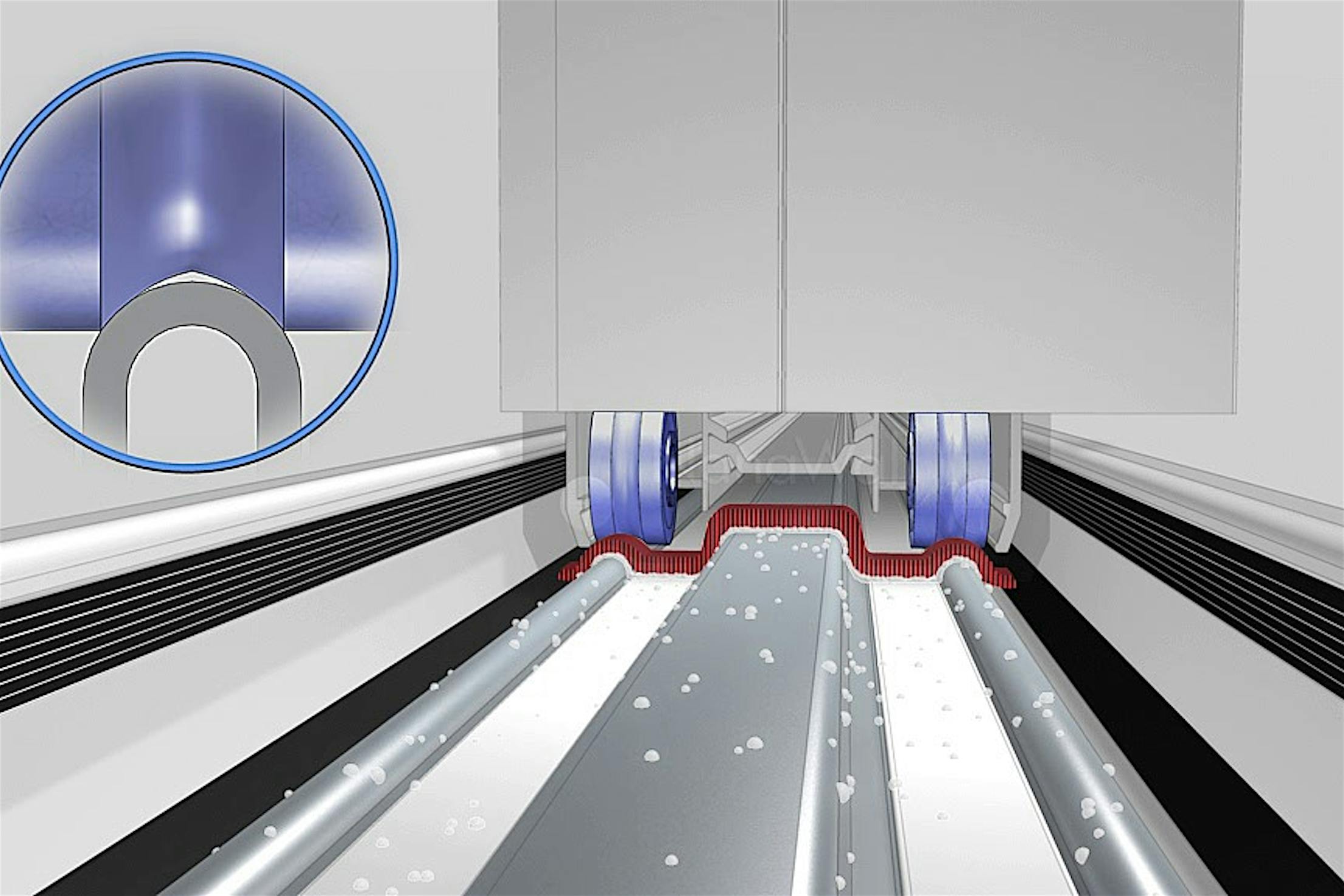
NanaWall Floor Supported Technology assures that the rollers run above the water table, ensuring long-term operational excellence. cero has been rigorous testing to withstand 40,000 opening and closing cycles. Double-sided brushes in front of each roller prevent debris accumulation and contribute to continuous smooth operation.
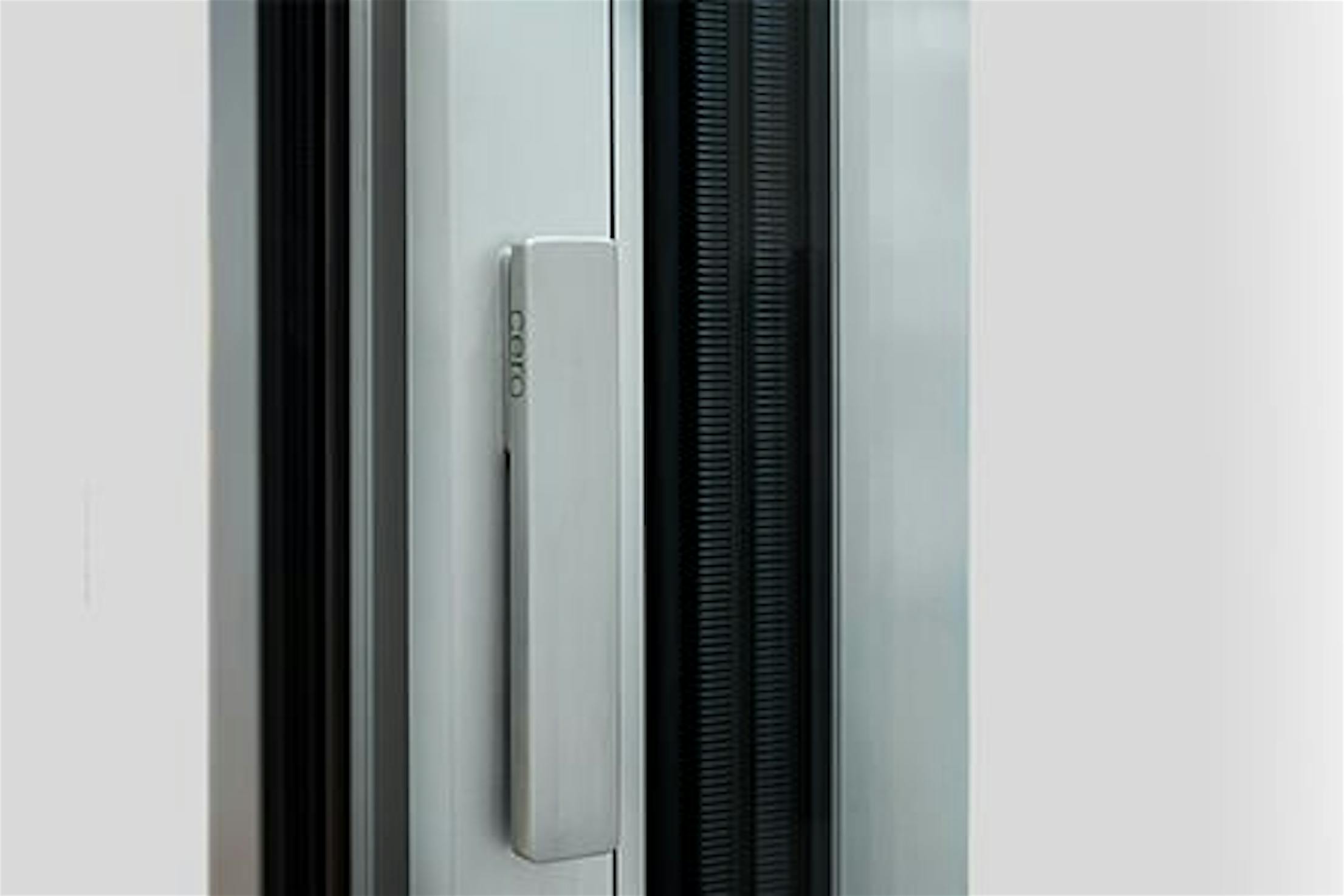
Secure multipoint locking and flat handle are integrated into the 1 5/16" (34 mm) vertical profile to maintain the clean, minimal appearance. A full 1" (25 mm) throw securely locks the panel top and bottom. For higher security concerns, optional European security standards of either RC2 or RC3 are available.
See Locking Options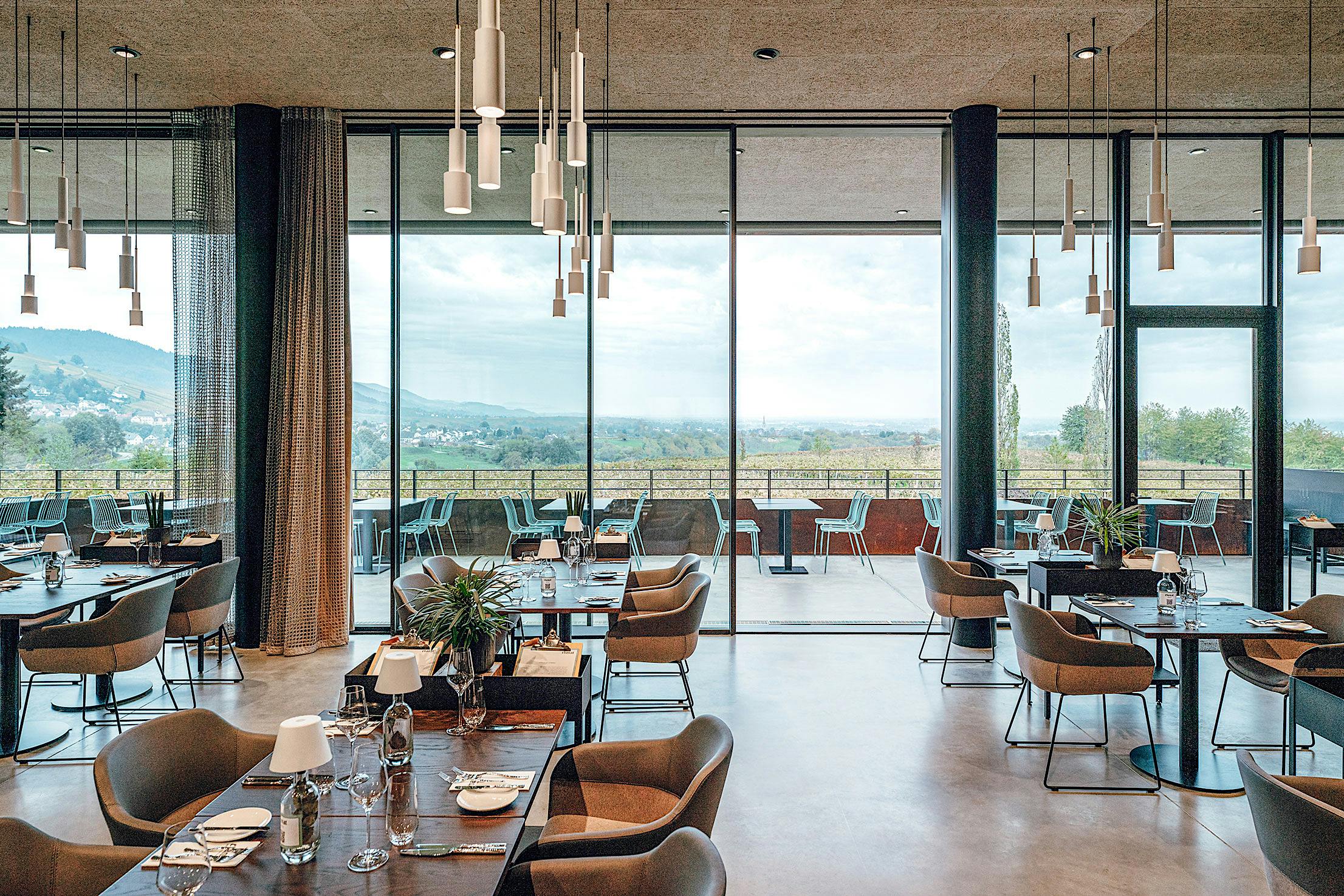
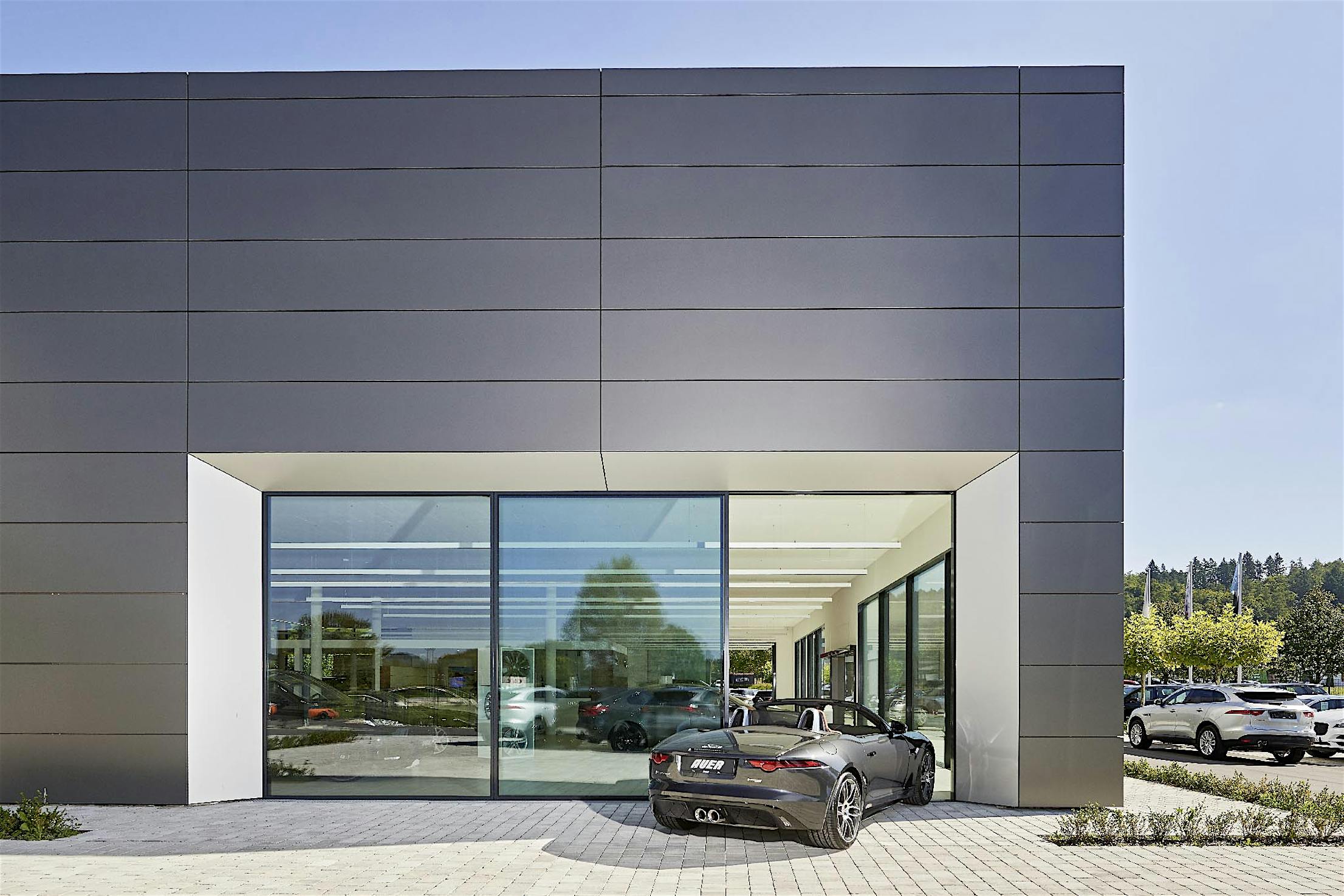
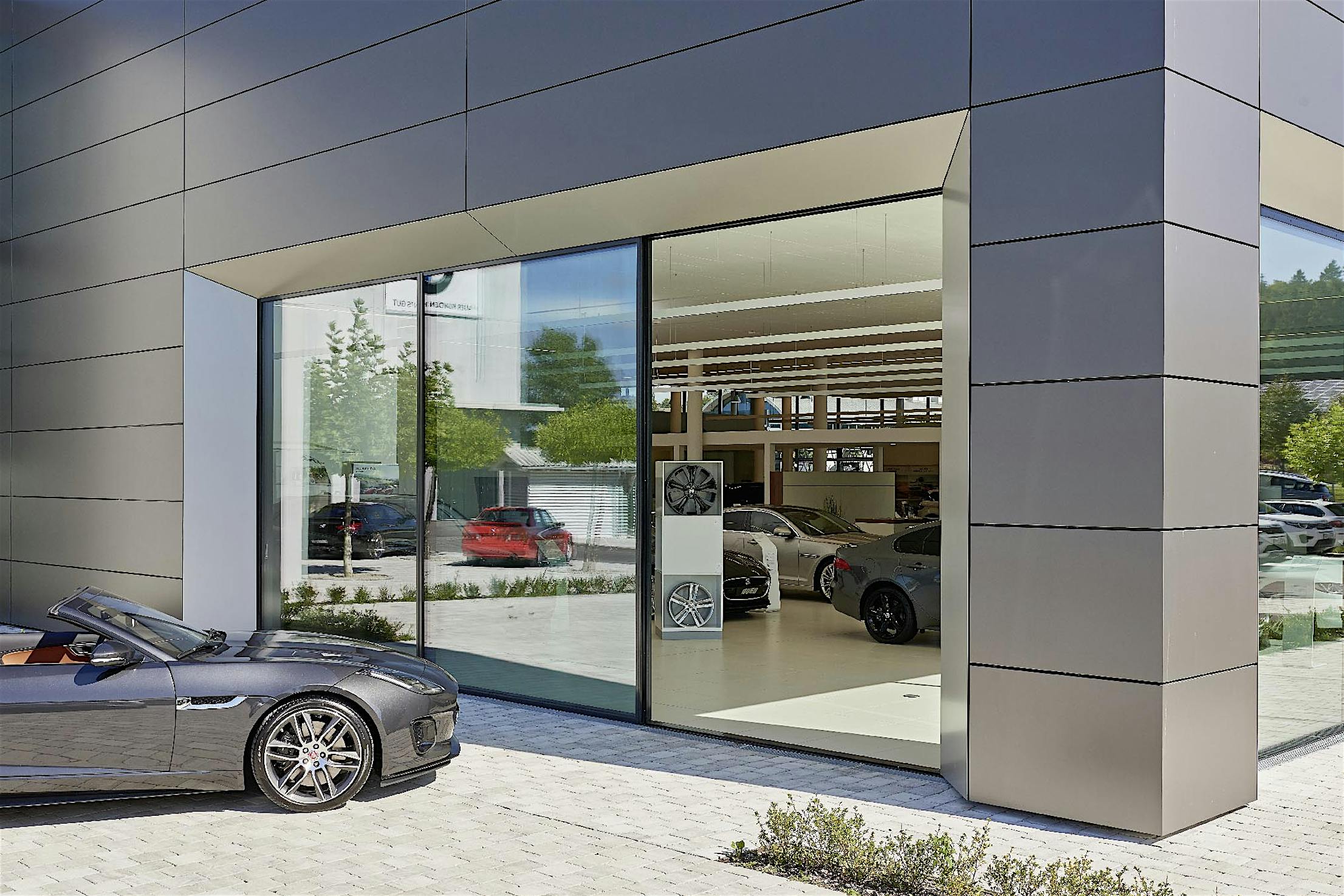
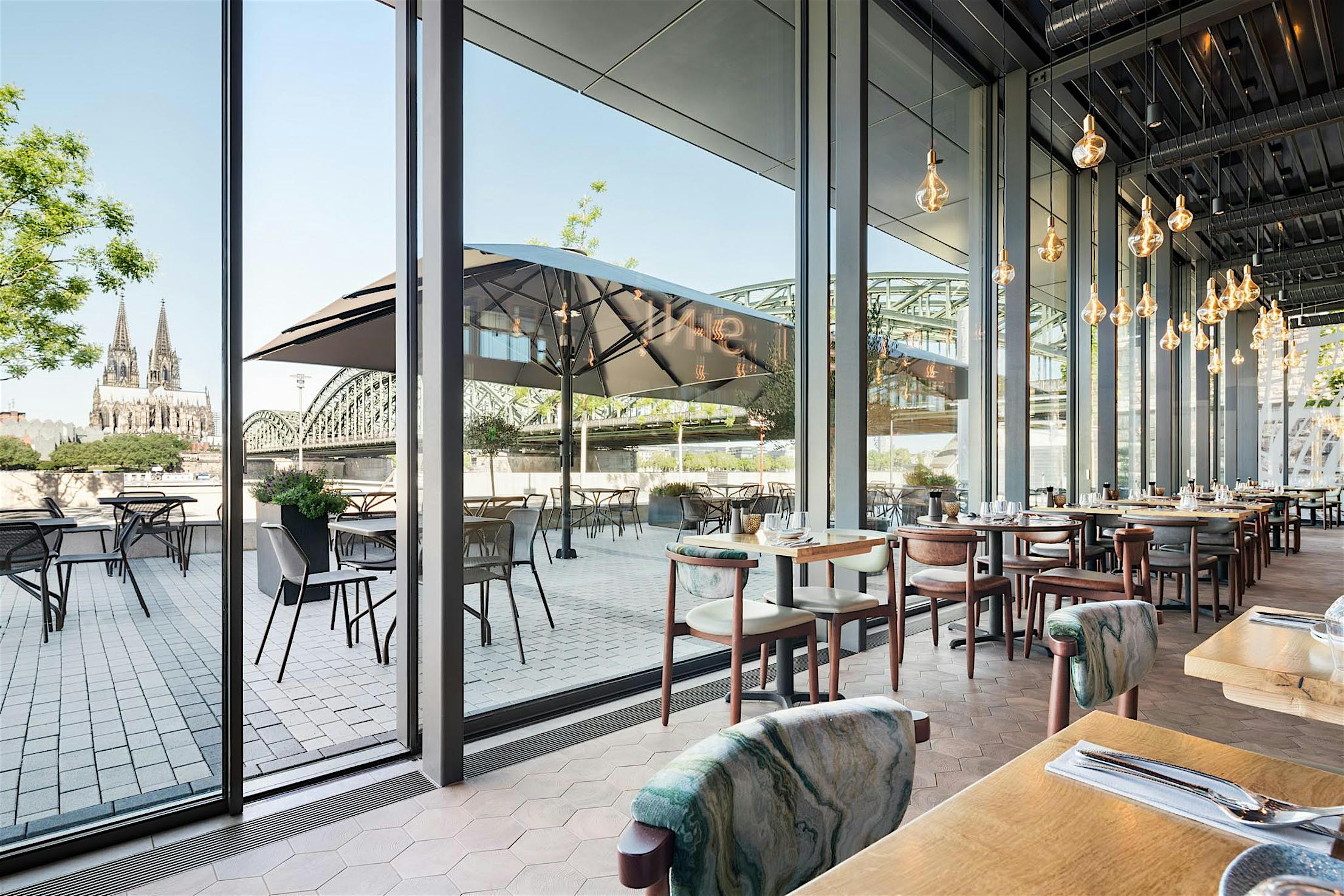
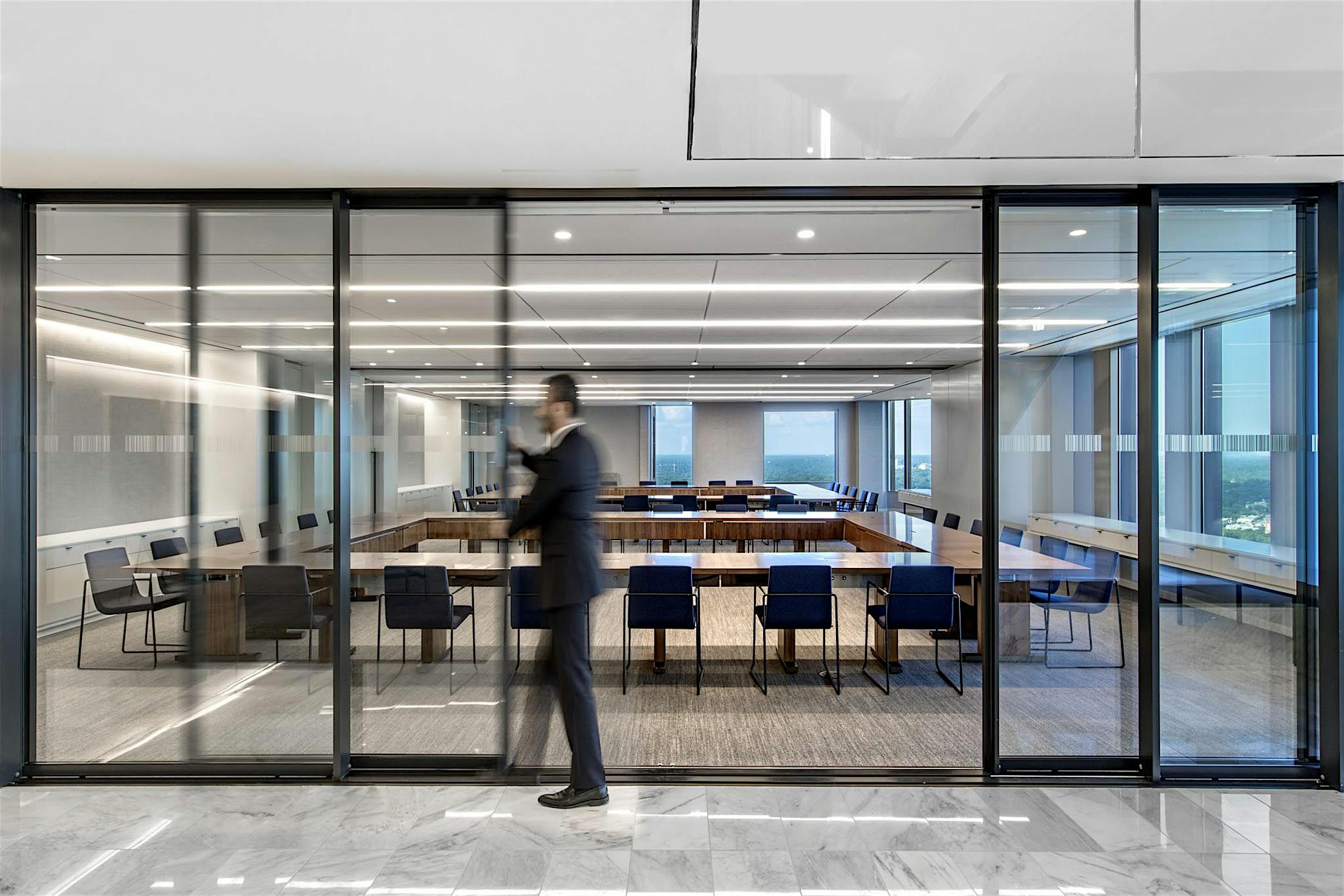
Exterior—cero transforms glazed floor-to-ceiling façades into flexible openings in commercial settings such as auto dealerships, hotels, and restaurants.
Interior—For interiors, cero is a fully tested and acoustically rated minimal sliding glass wall capable of reaching sound control up a unit STC 43.
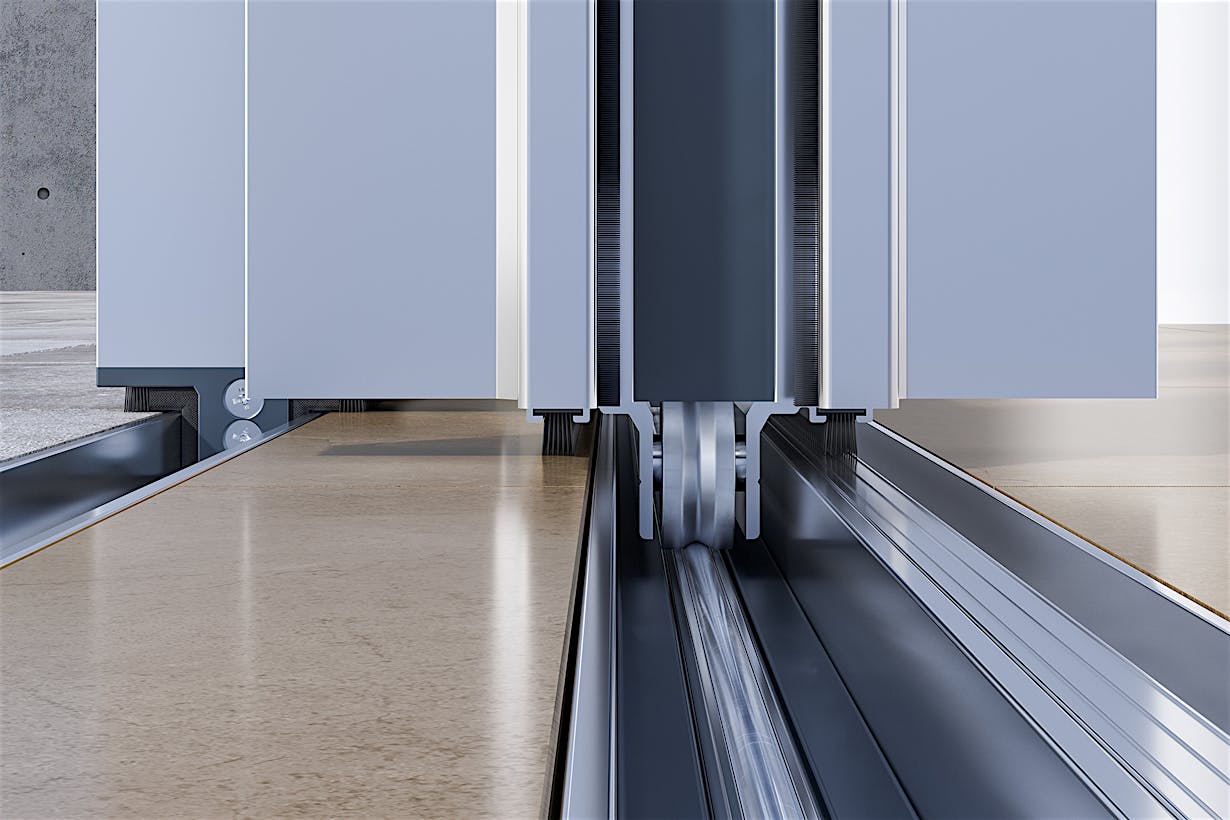
Uncompromised Roller System
Unique to cero is a Gothic arch wheel bearing design. With a 2-point contact of each stainless steel wheel to the bottom stainless steel track, the system glides with less friction. Floor supported cero panels are operated by concealed carriers containing a pair of wheels with encapsulated and self-lubricating ball bearings for smooth sliding.
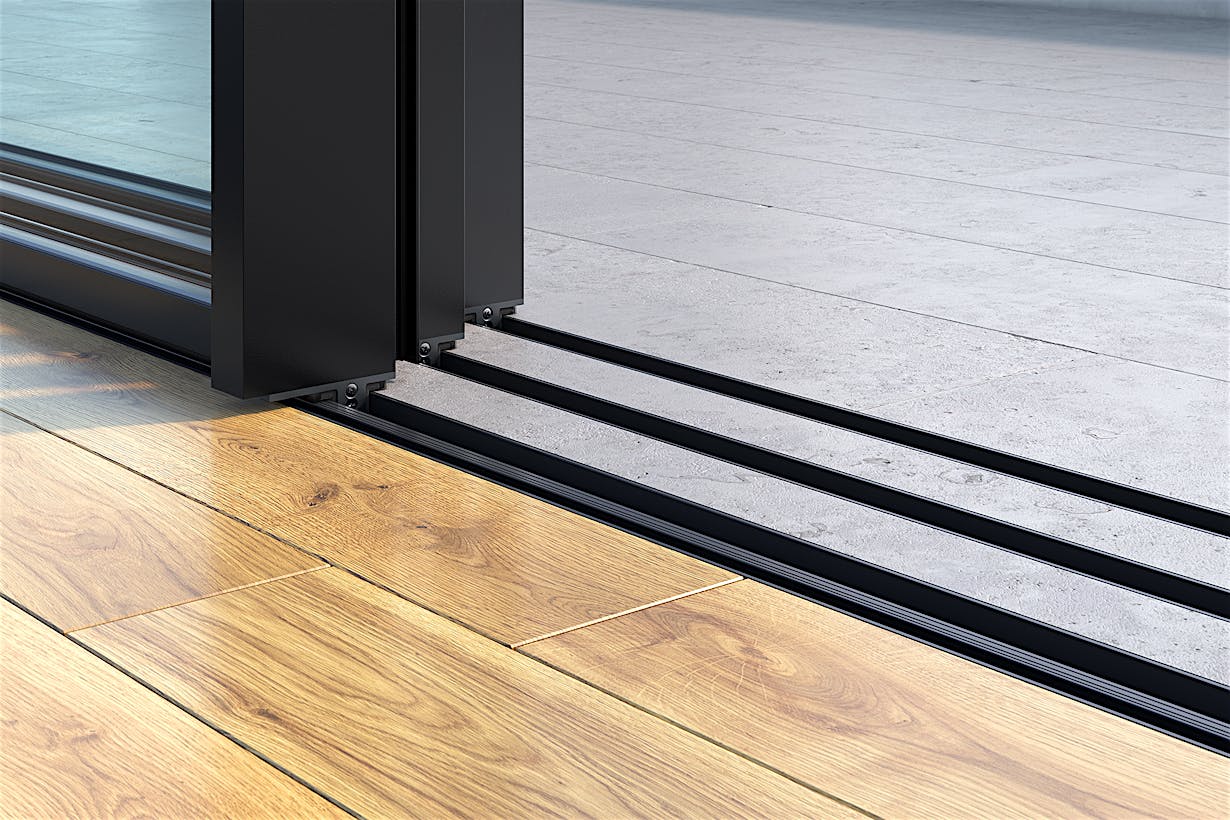
Minimal Sill for cero II
For cero II, the Minimal Sill offers a minimalistic and aesthetic transition between the interior and exterior. Finished flooring inserts can be easily installed in between the tracks making this sill virtually disappear. The Minimal Sill is shallow, provides water management, and is barefoot friendly.
Download cero® Sill Options eBook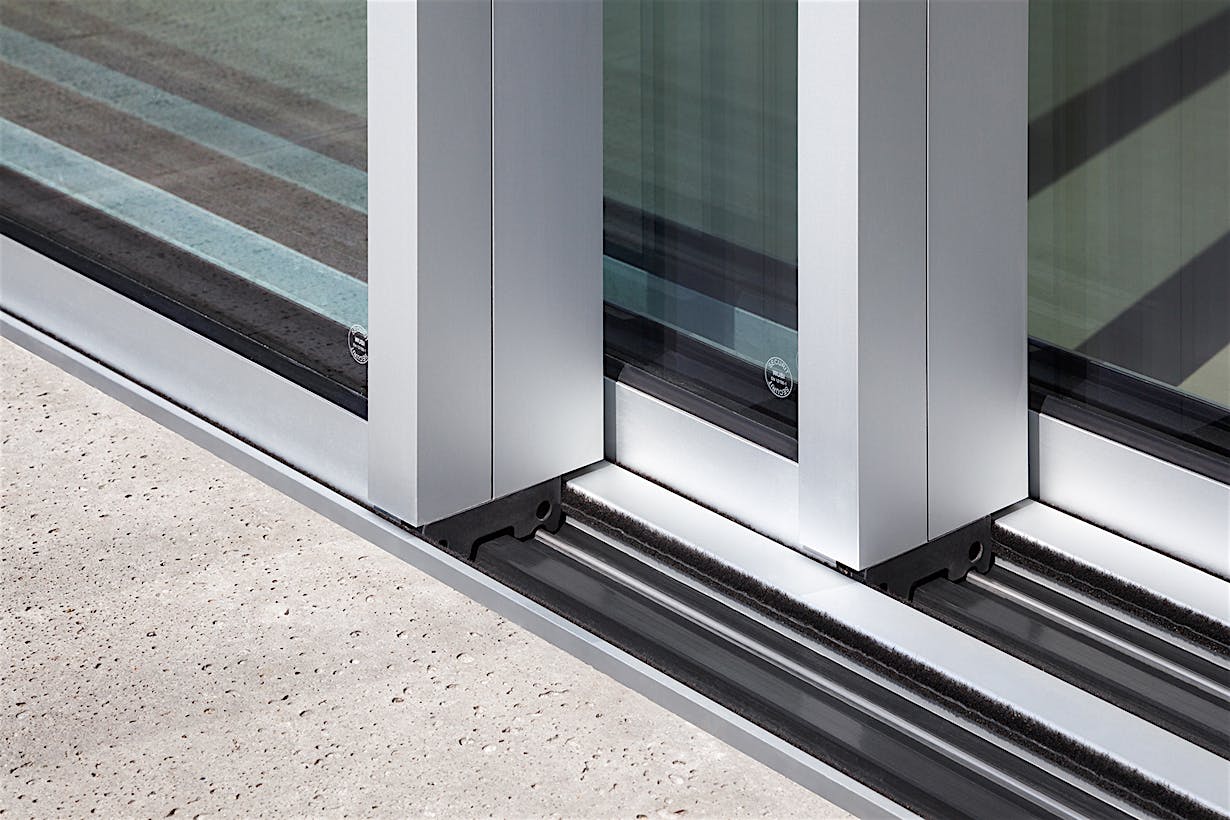
Performance Sill for cero II | cero III
cero's thermally broken Higher Weather Performance Sill offers 1/8″ (3 mm) height adjustability to accommodate potential building movement. Recessed installation seamlessly connects interior and exterior spaces, with an optional ADA-compliant track insert. The engineered drainage system ensures water management, while a French drainage option is available if required.
An Advanced Guide to cero® Sill Options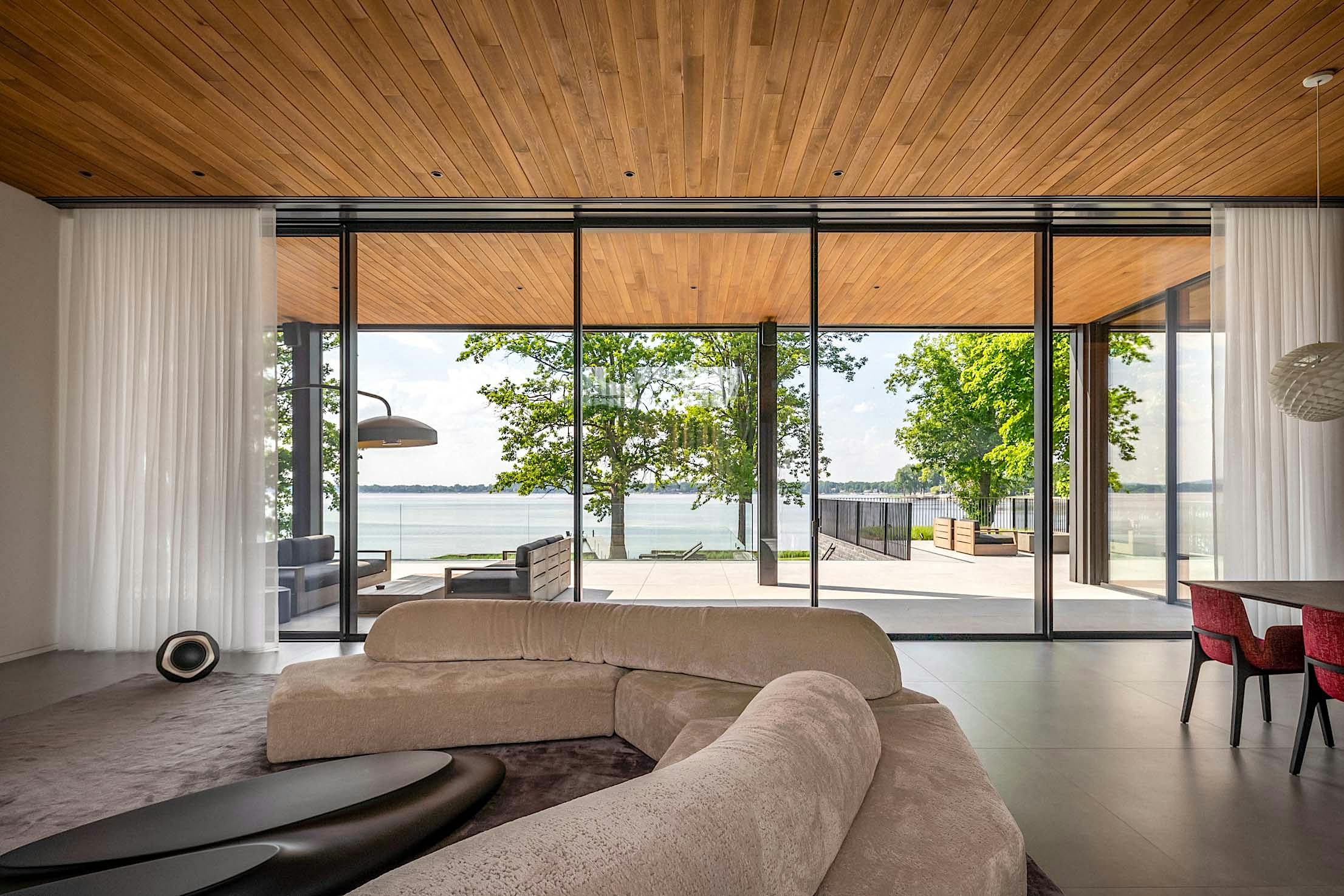
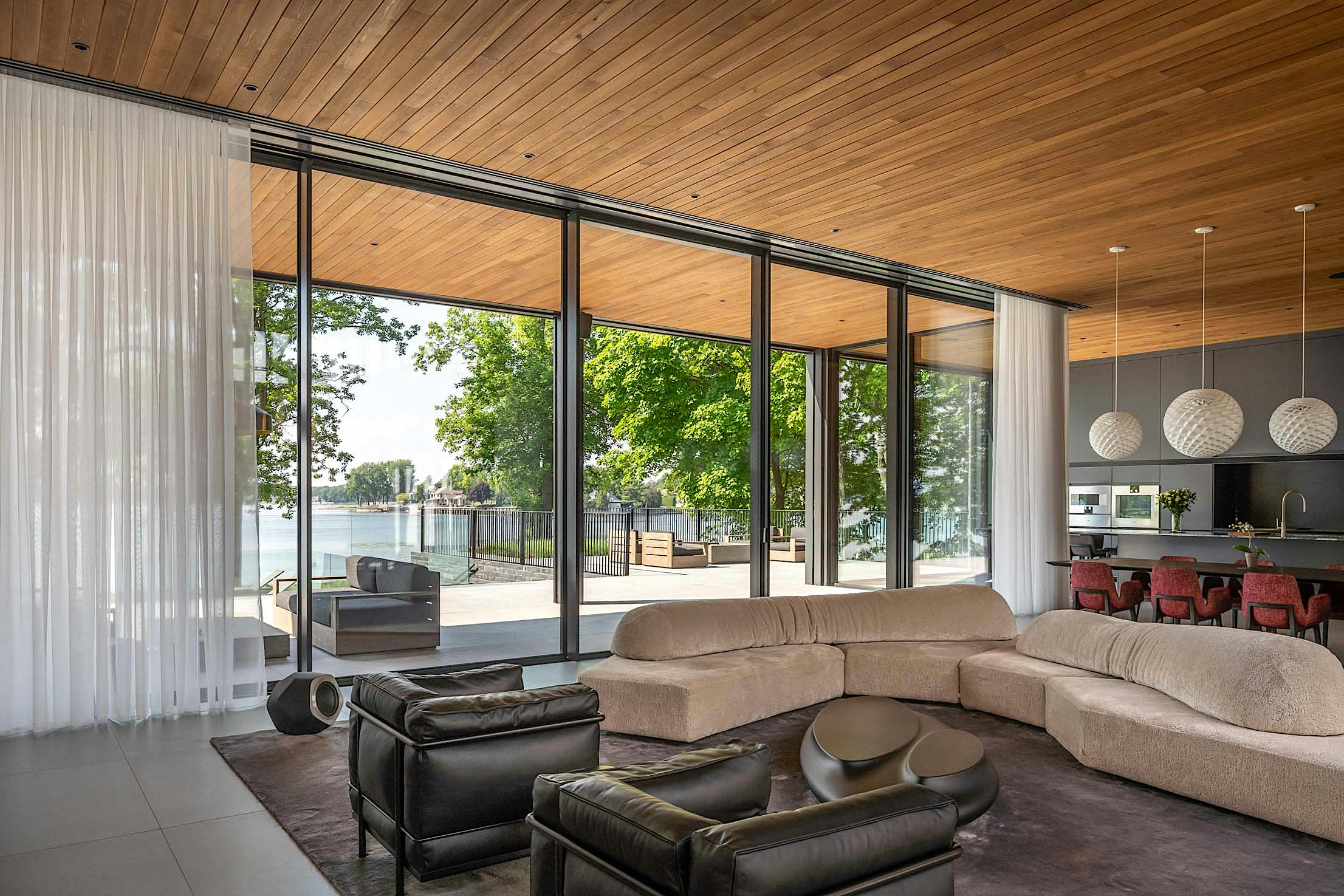
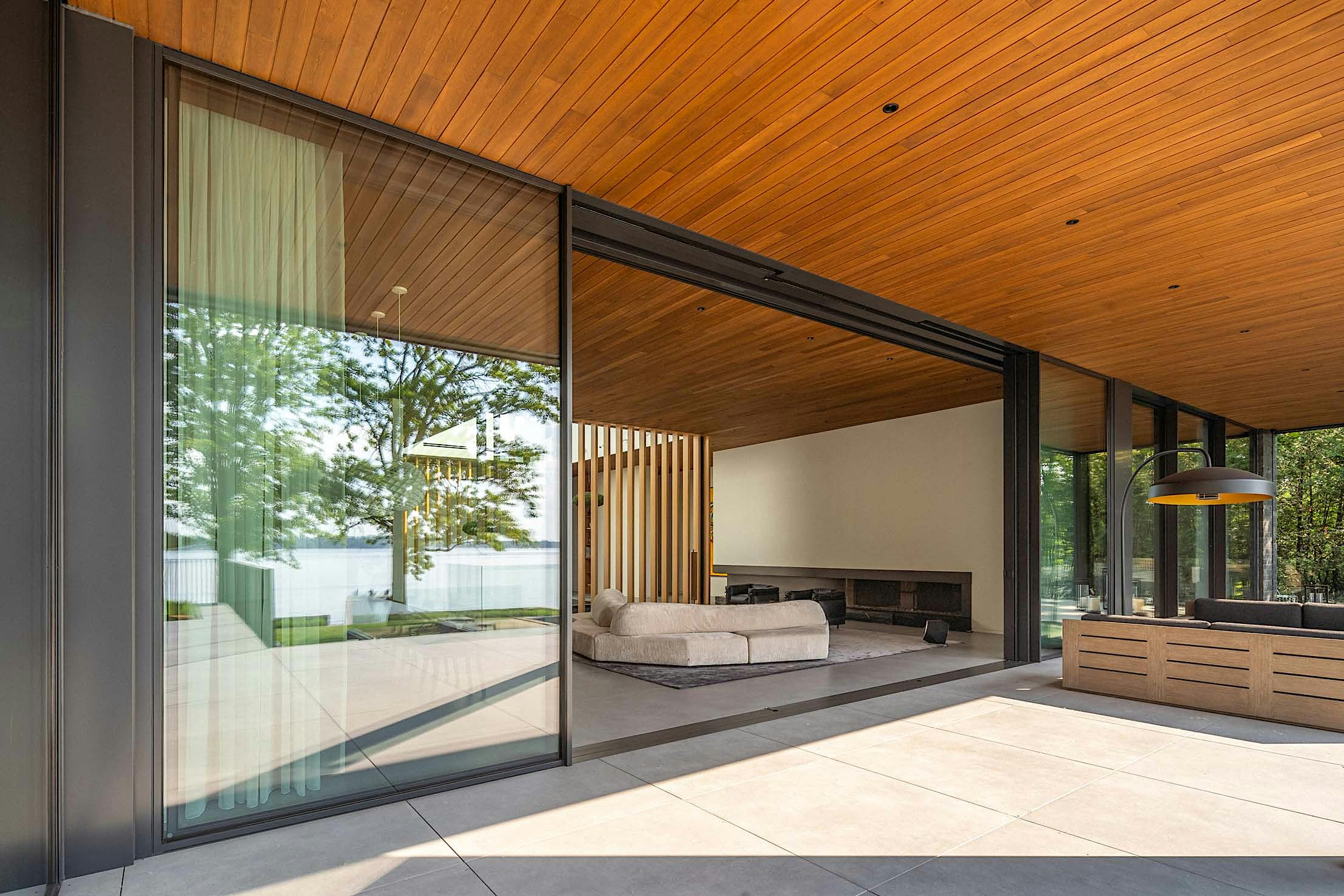
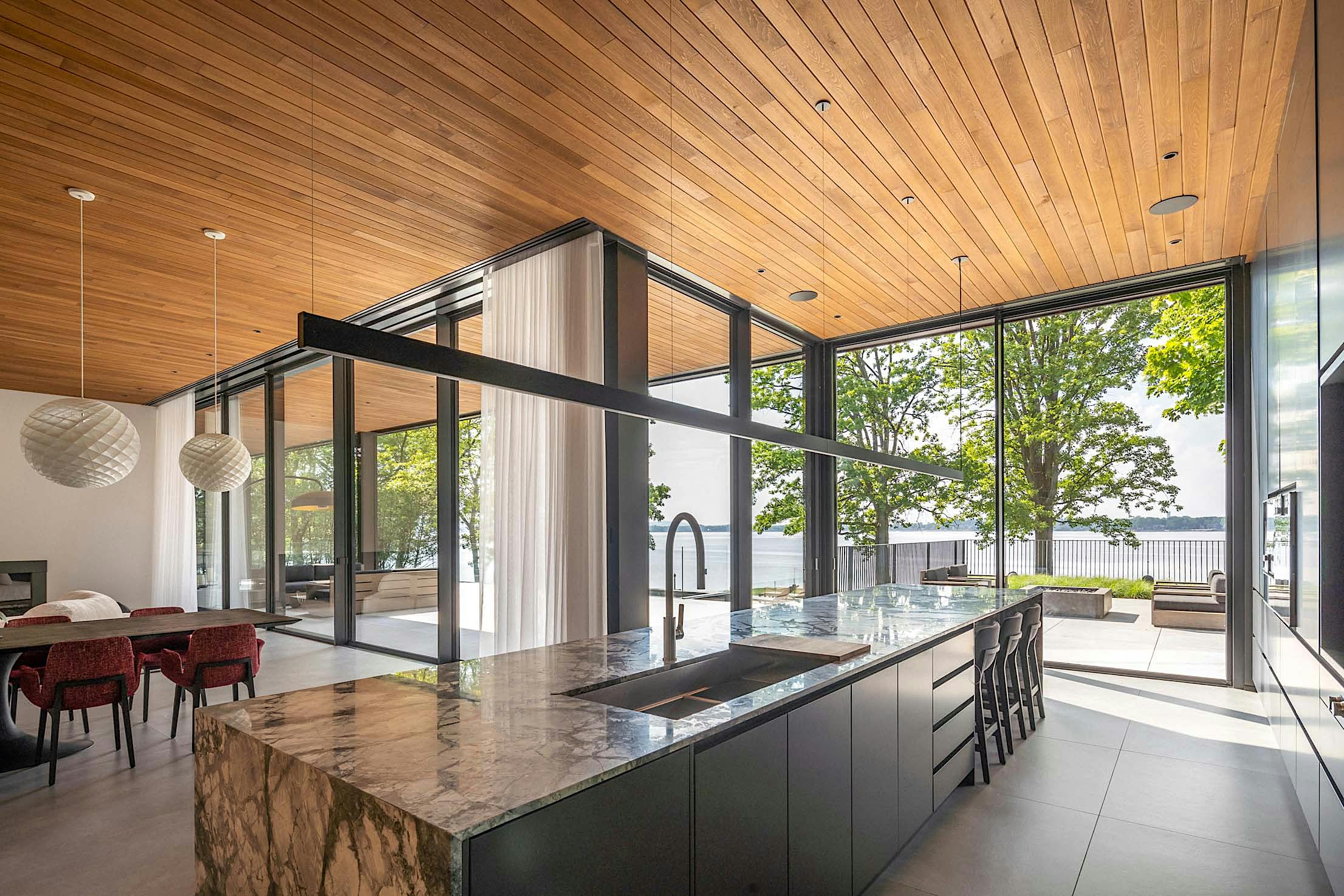
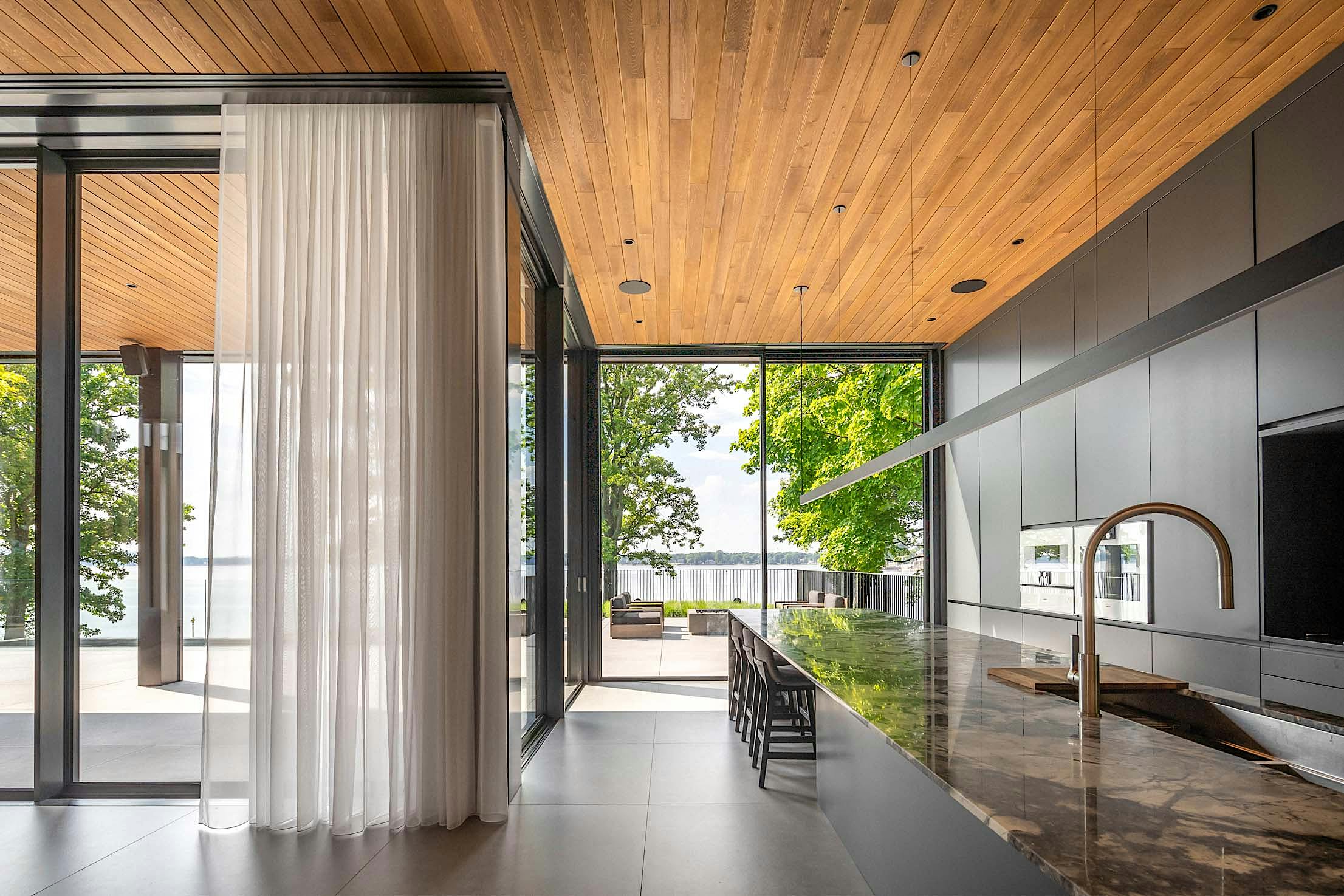
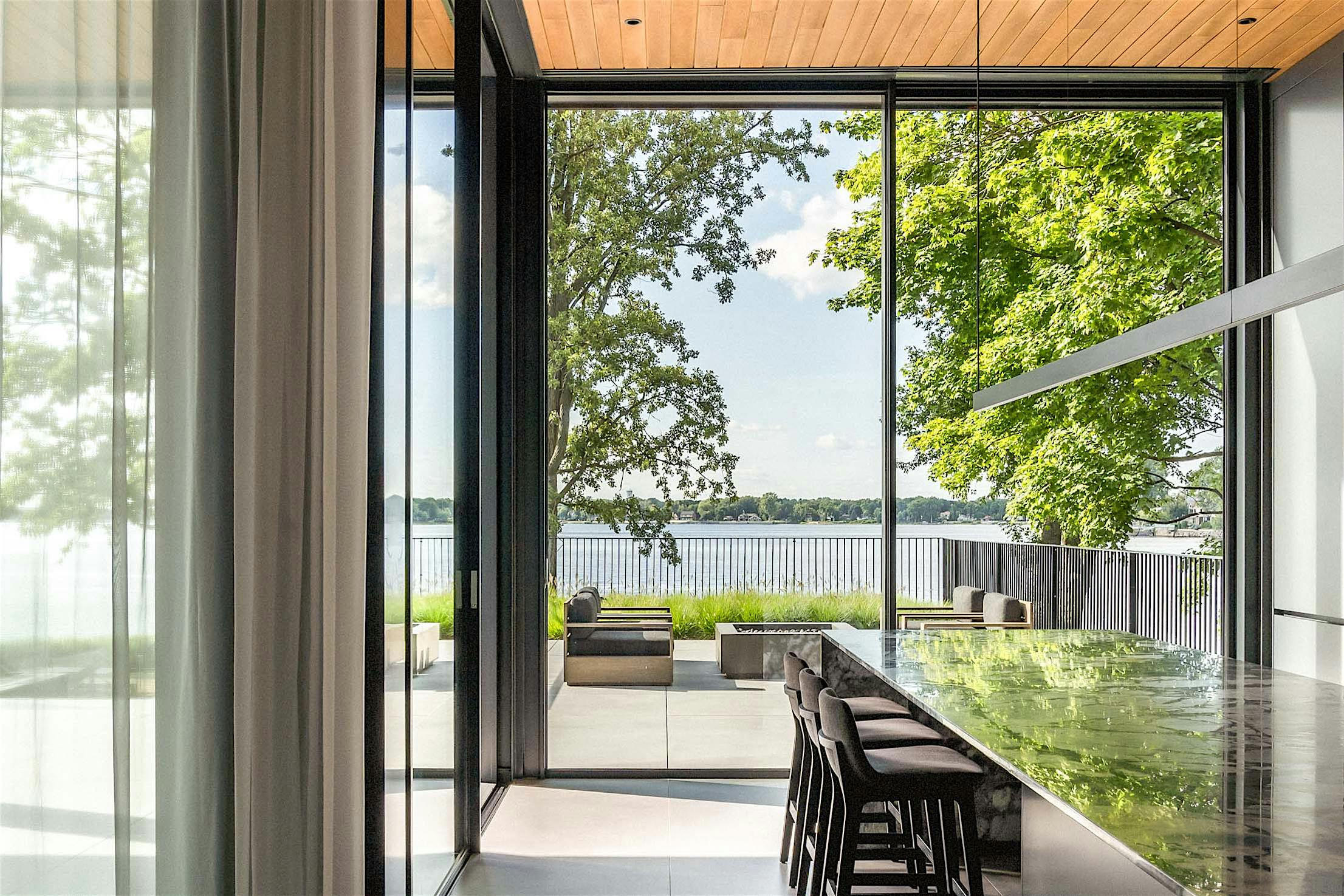
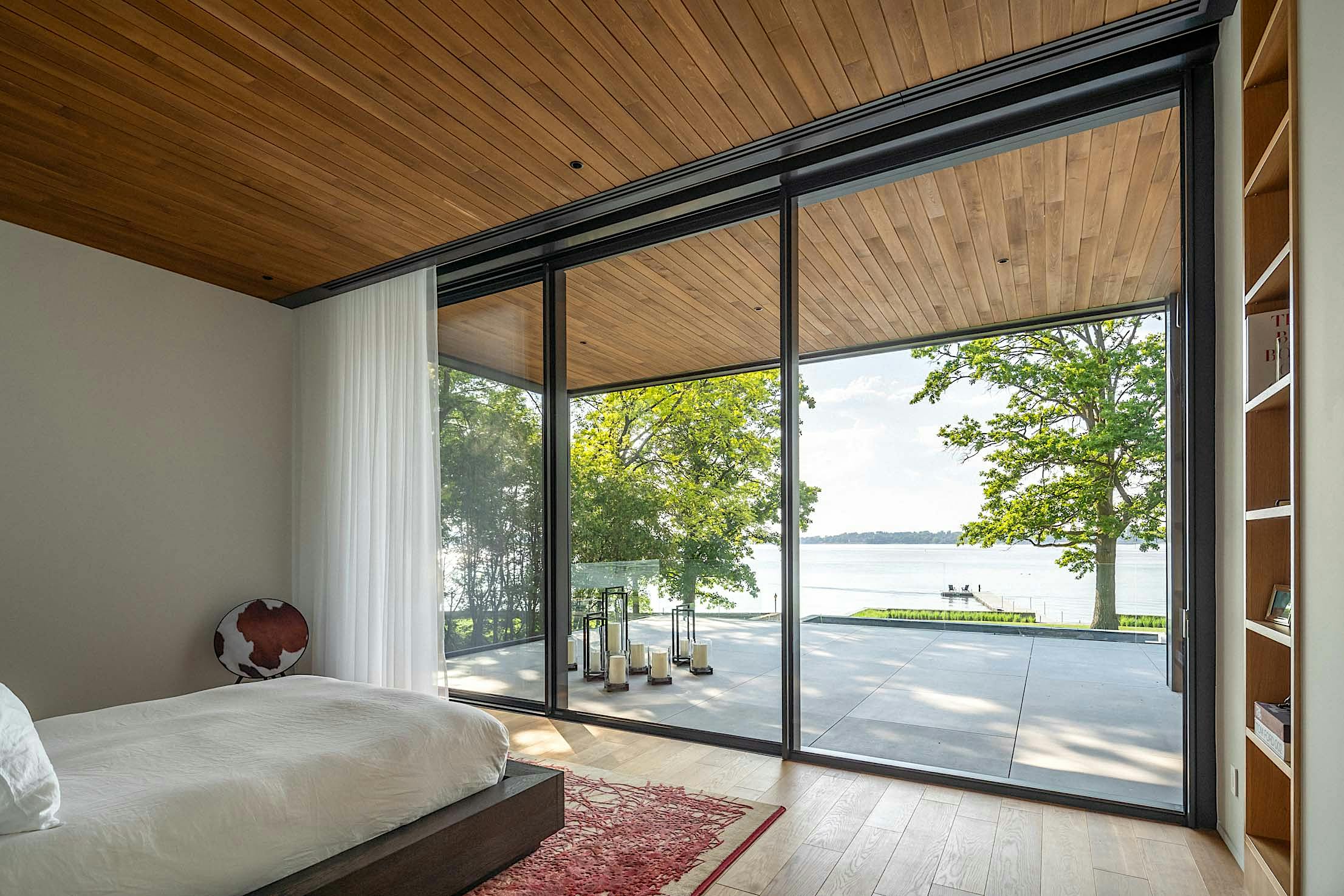
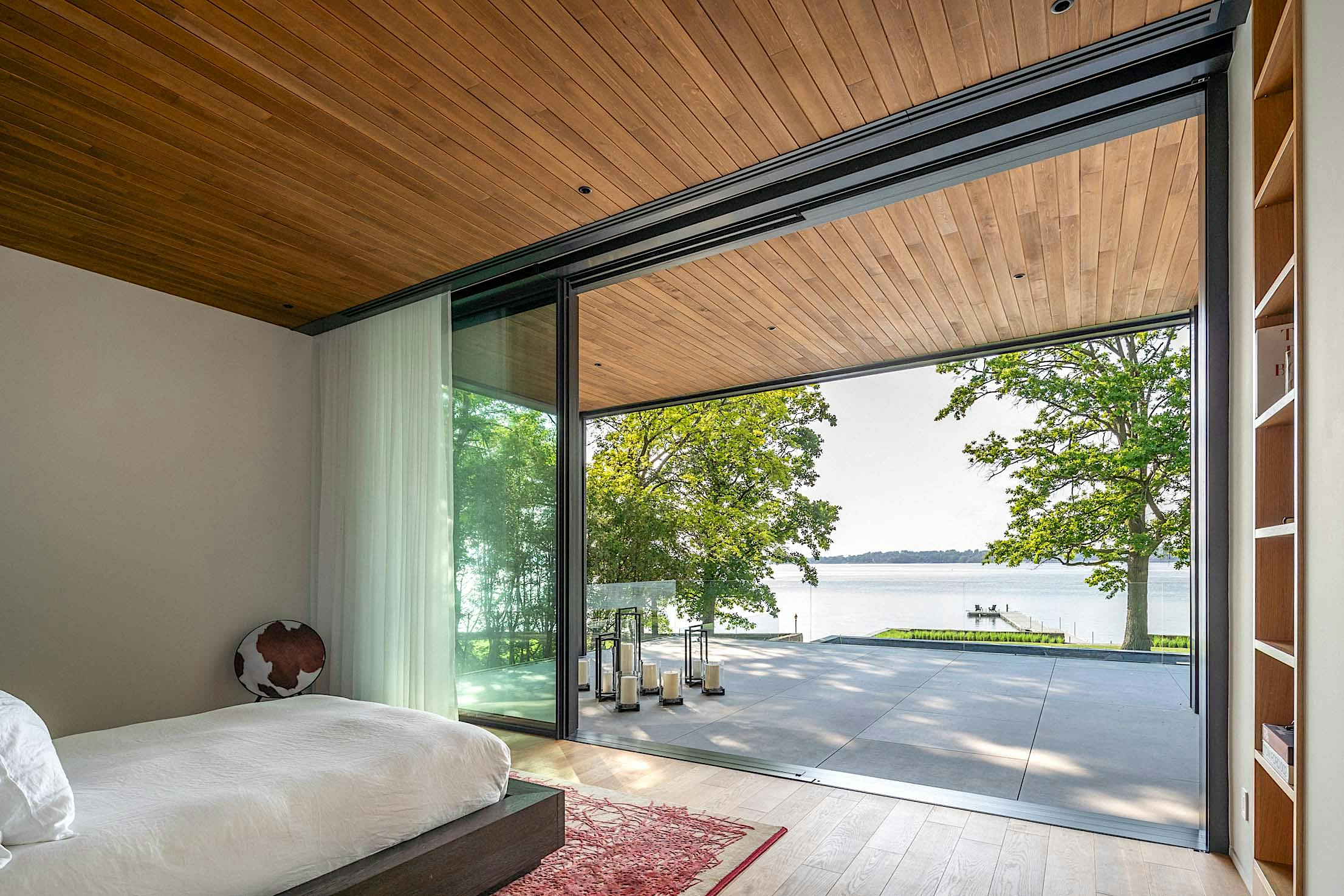
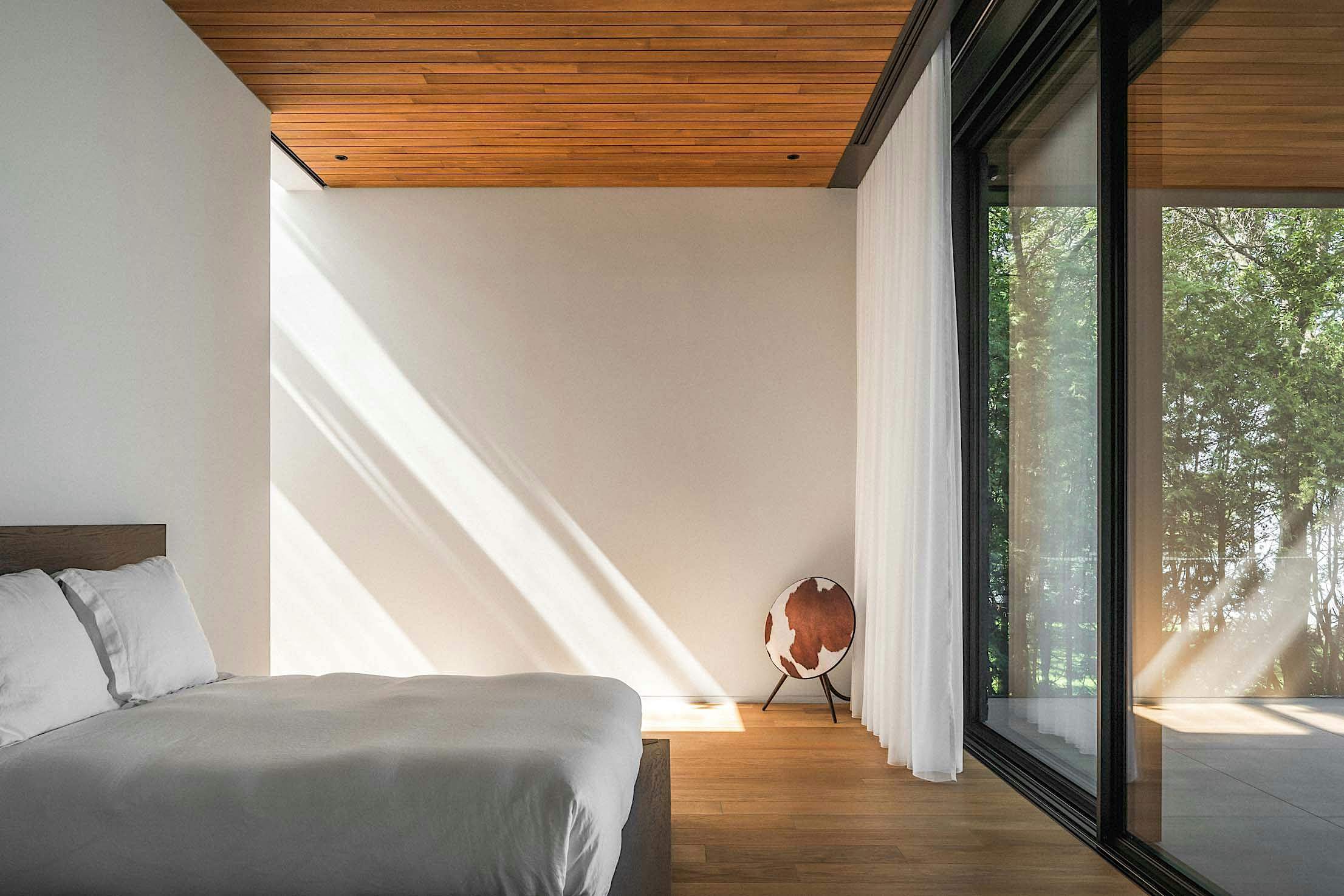
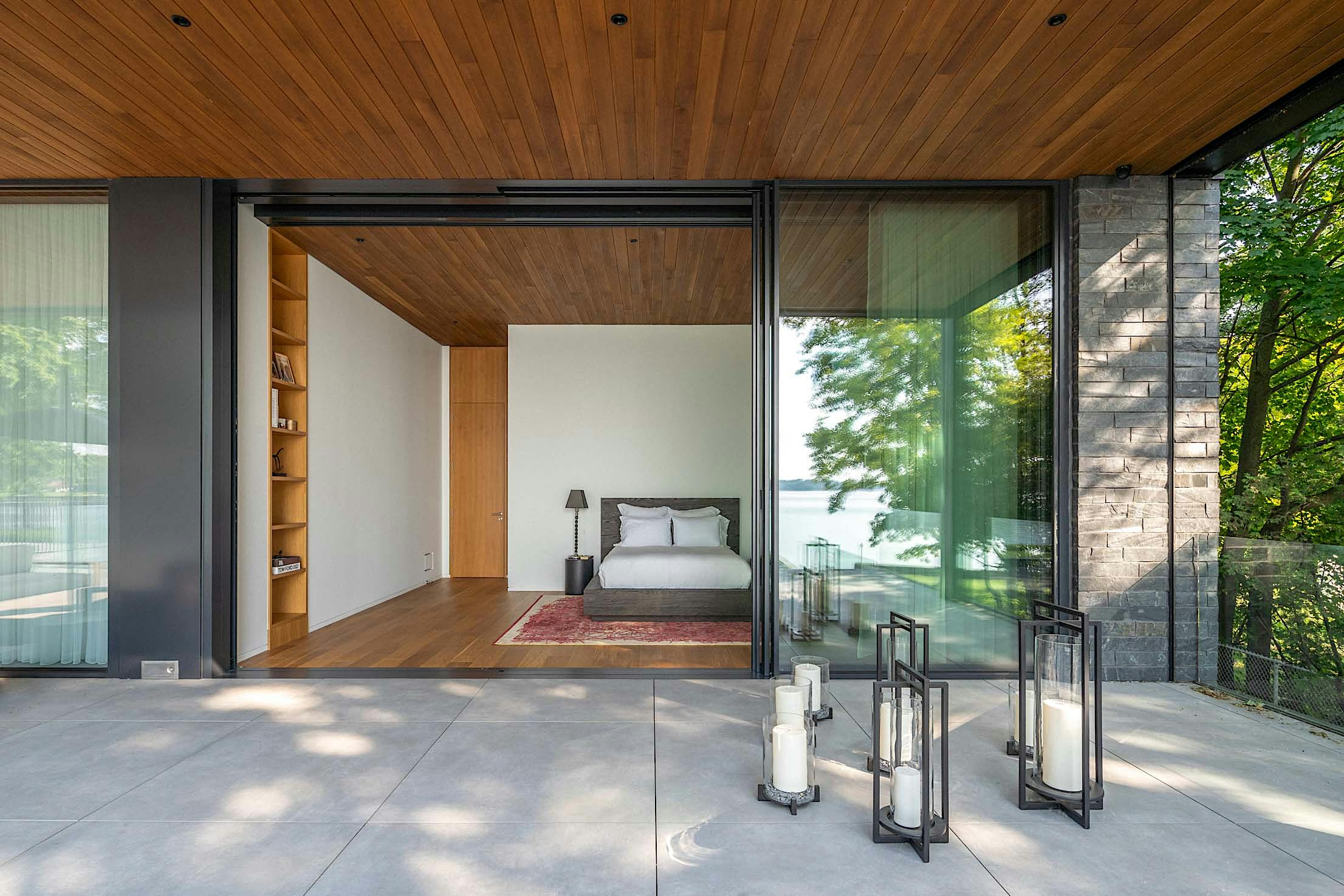
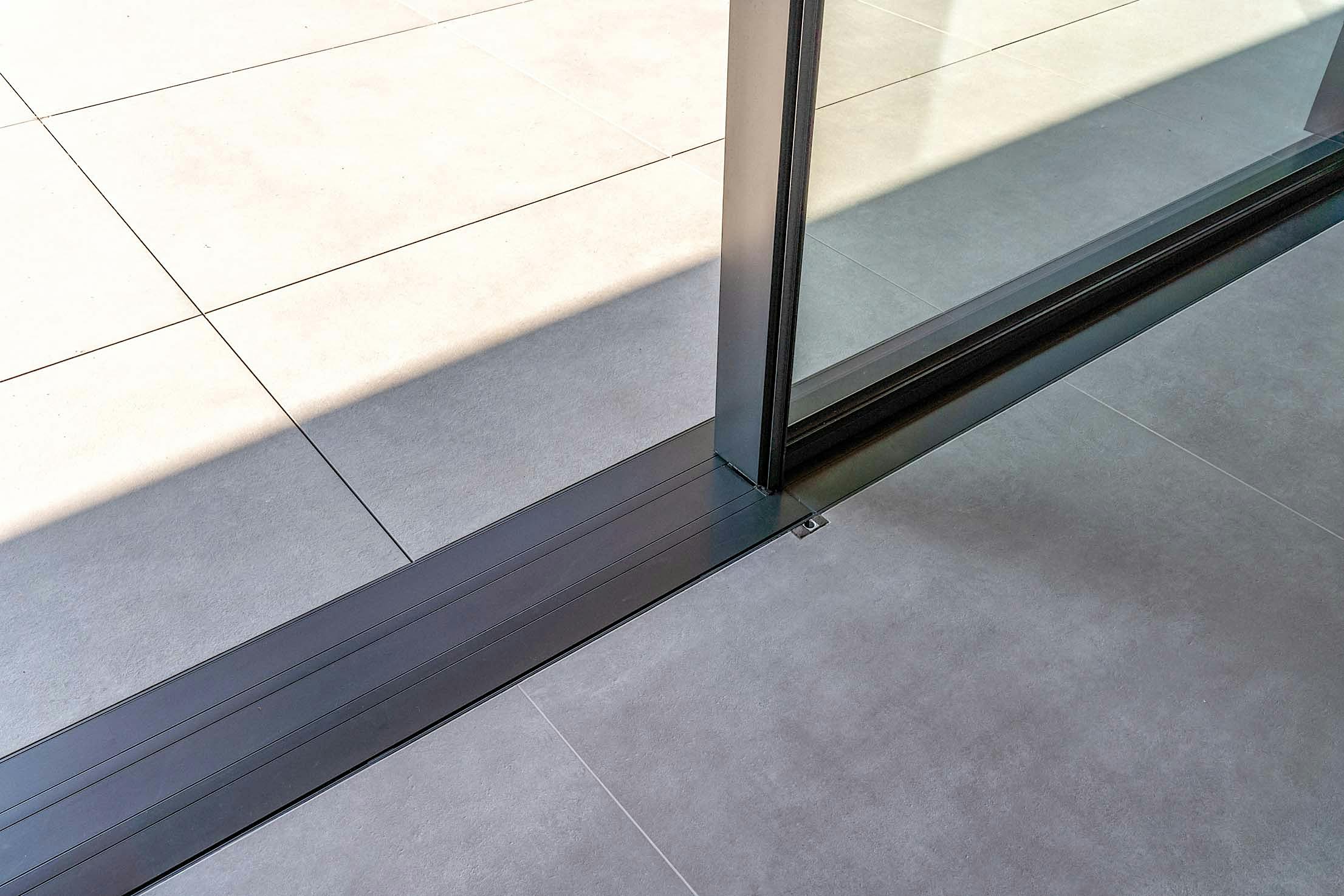
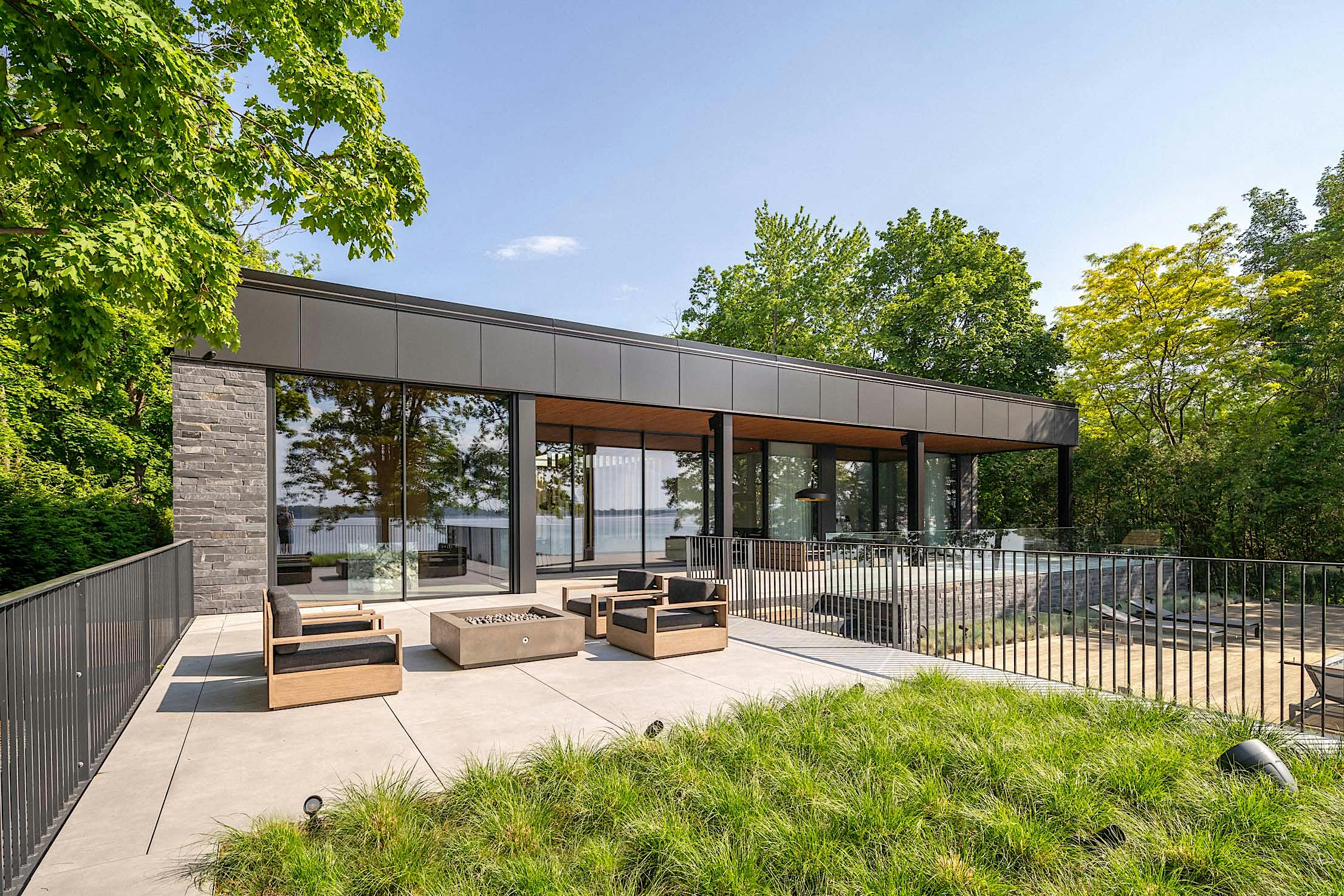
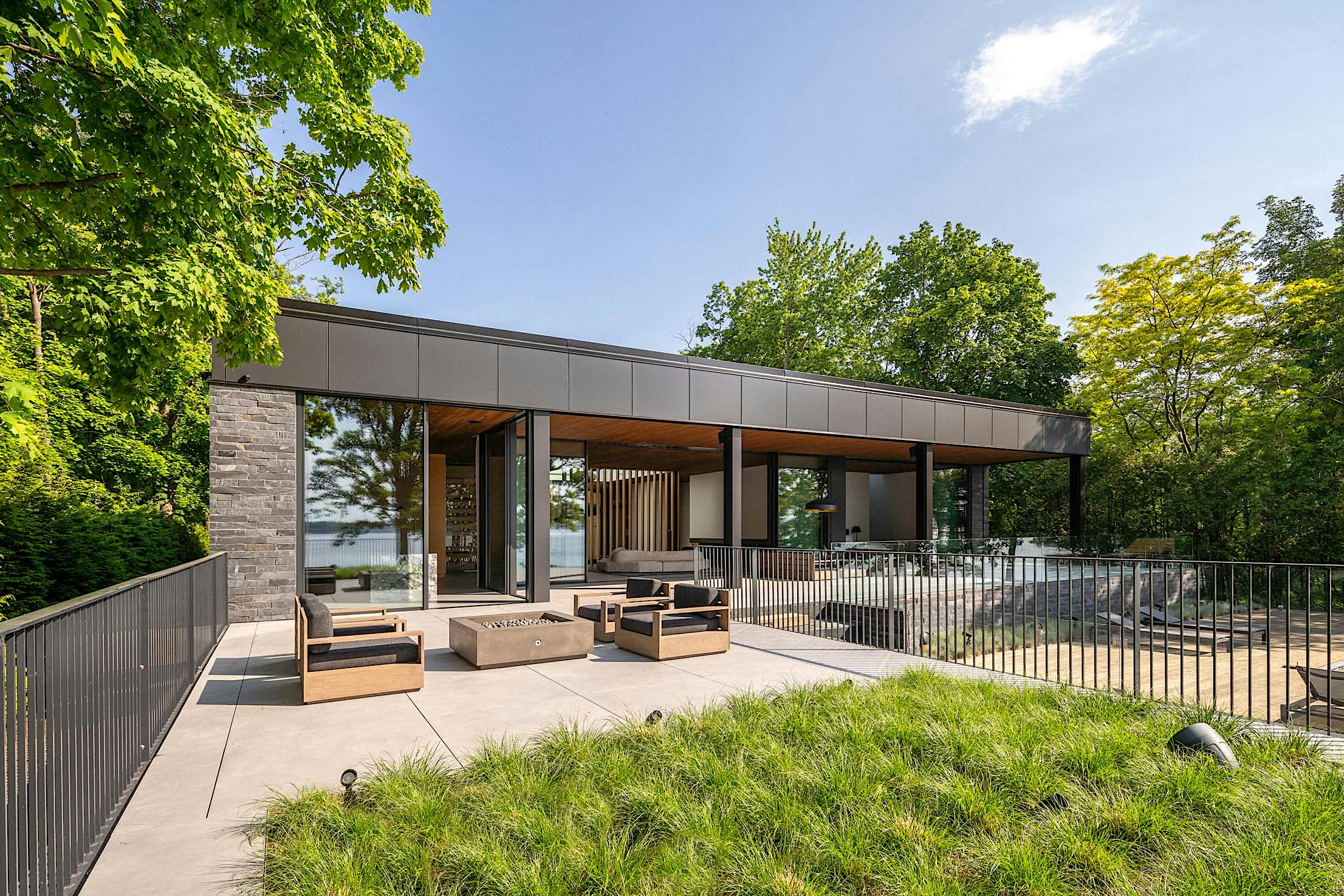
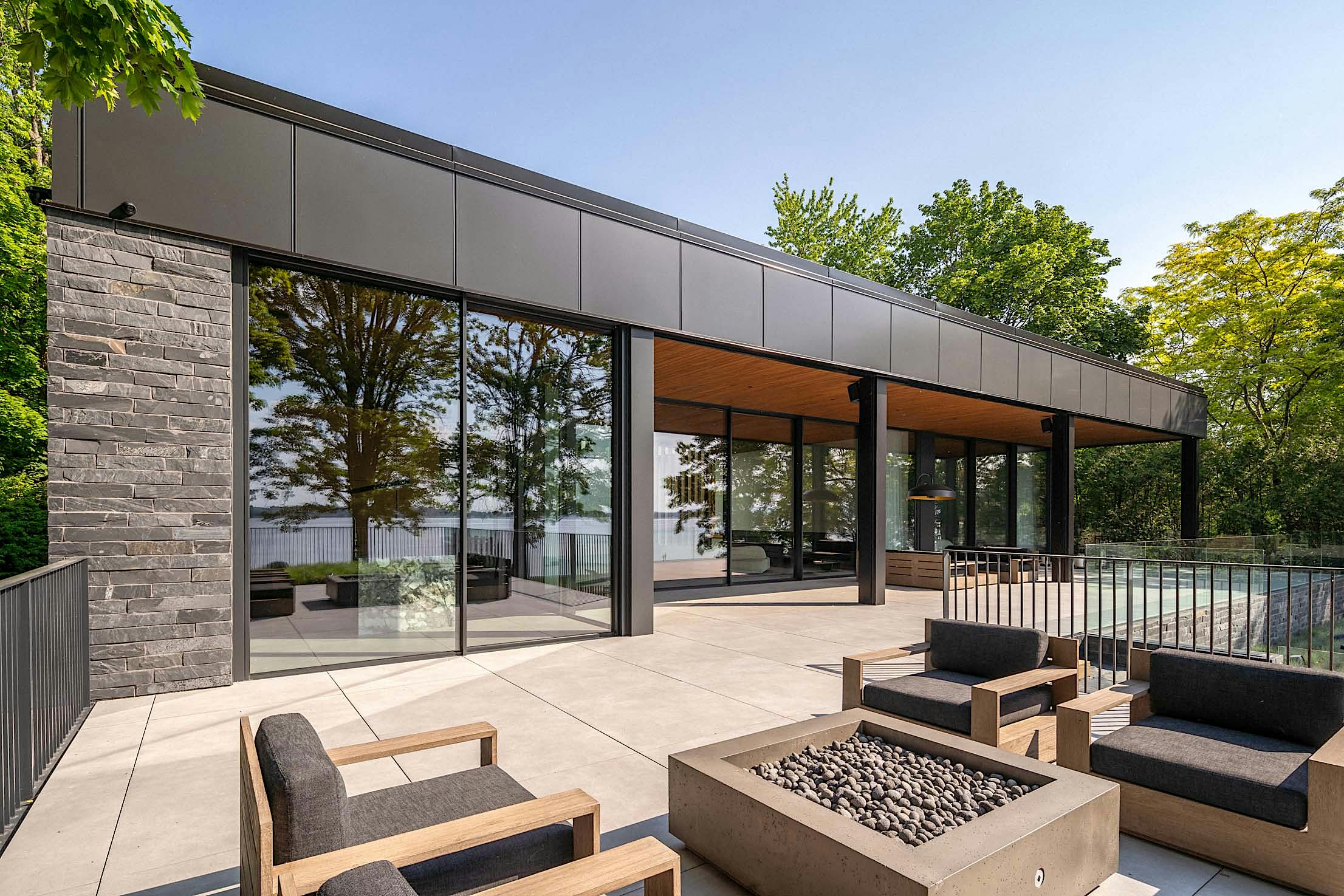
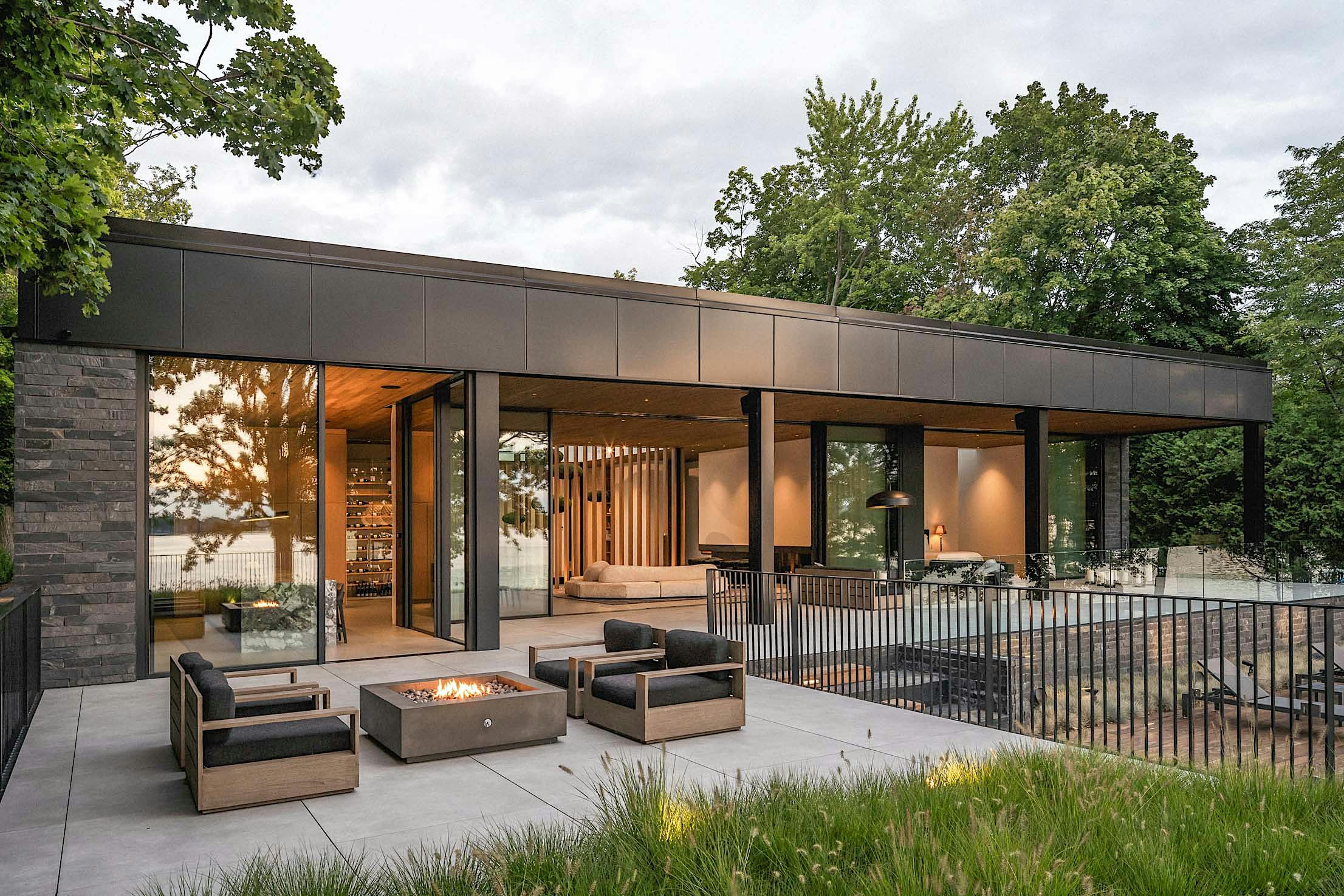
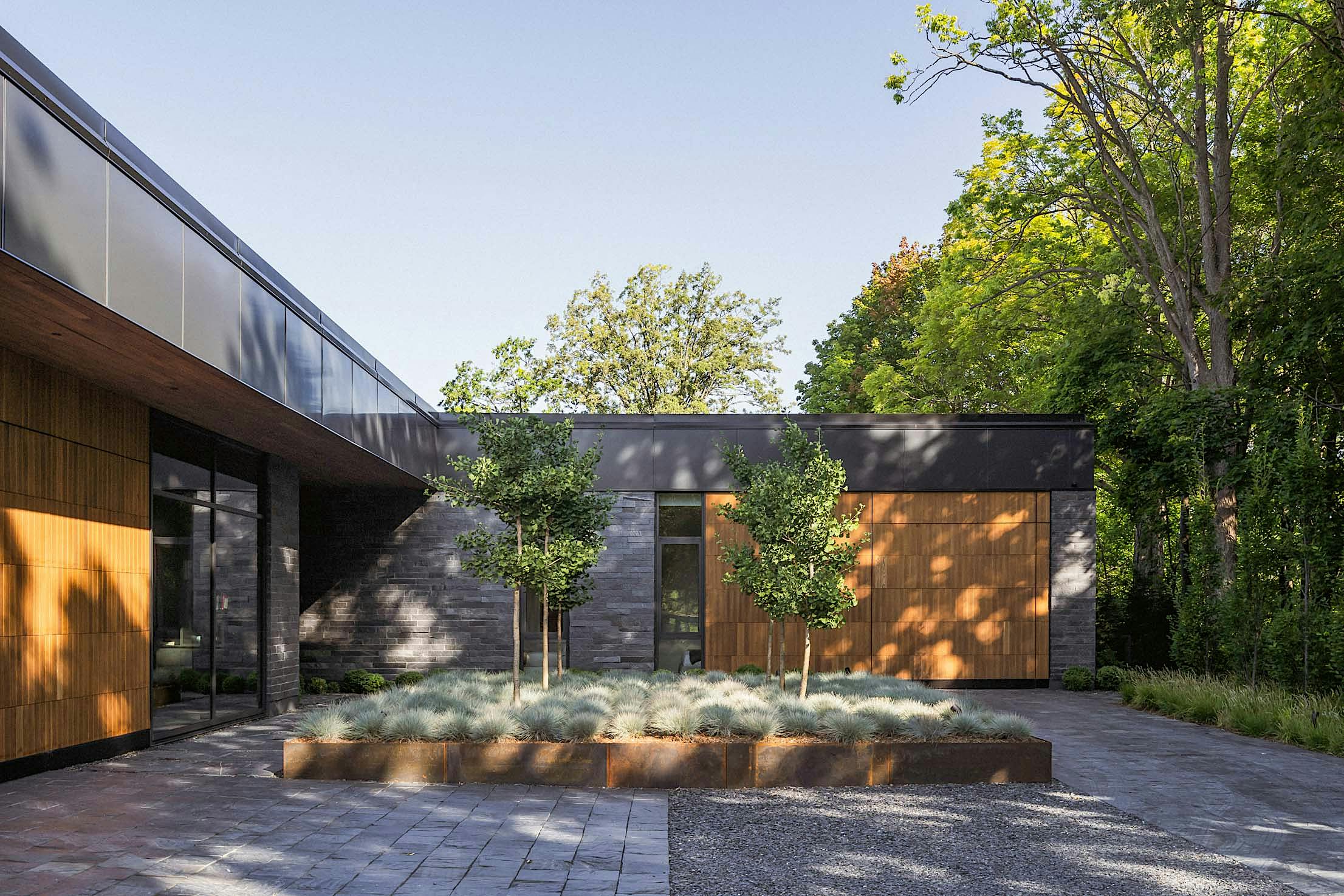
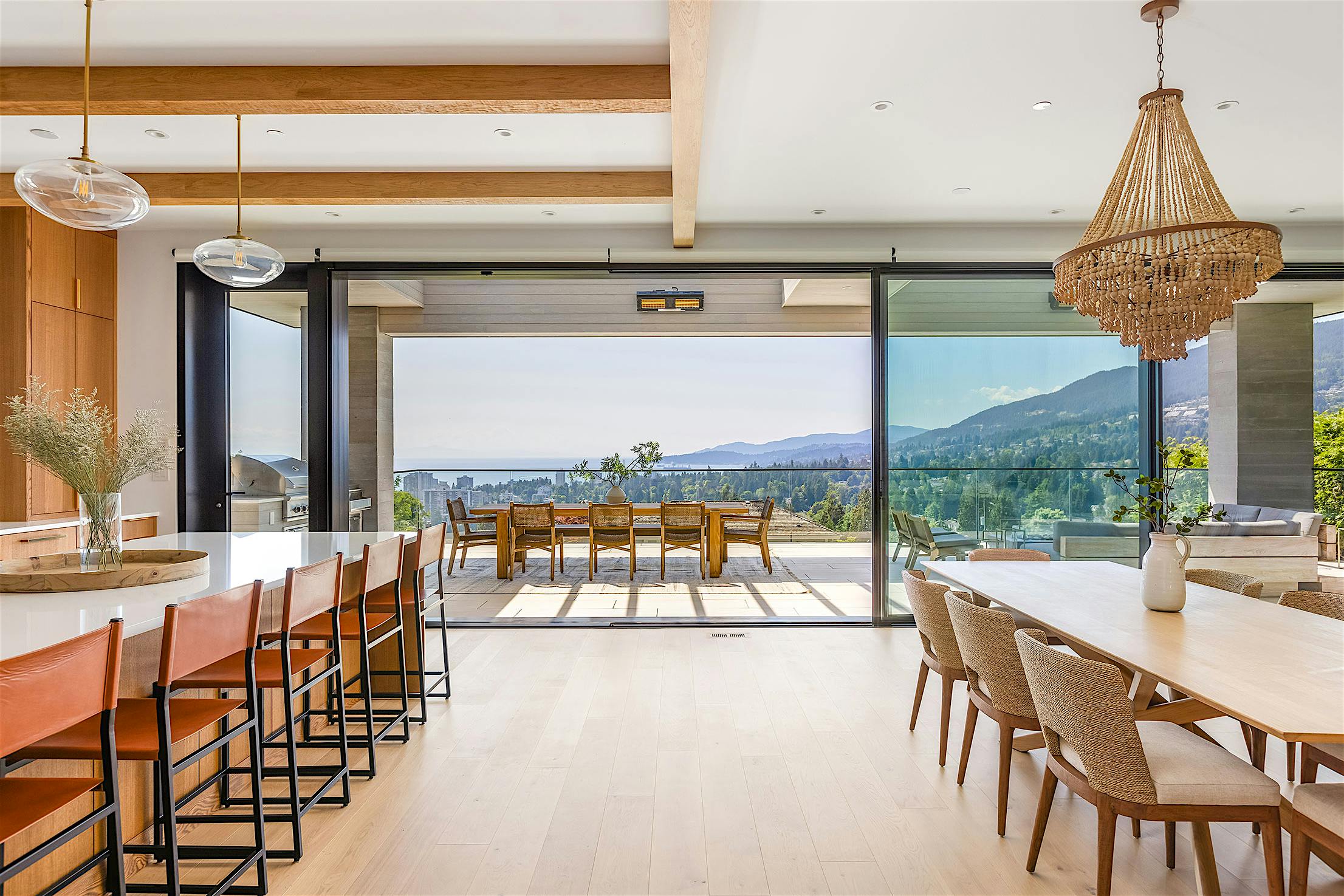
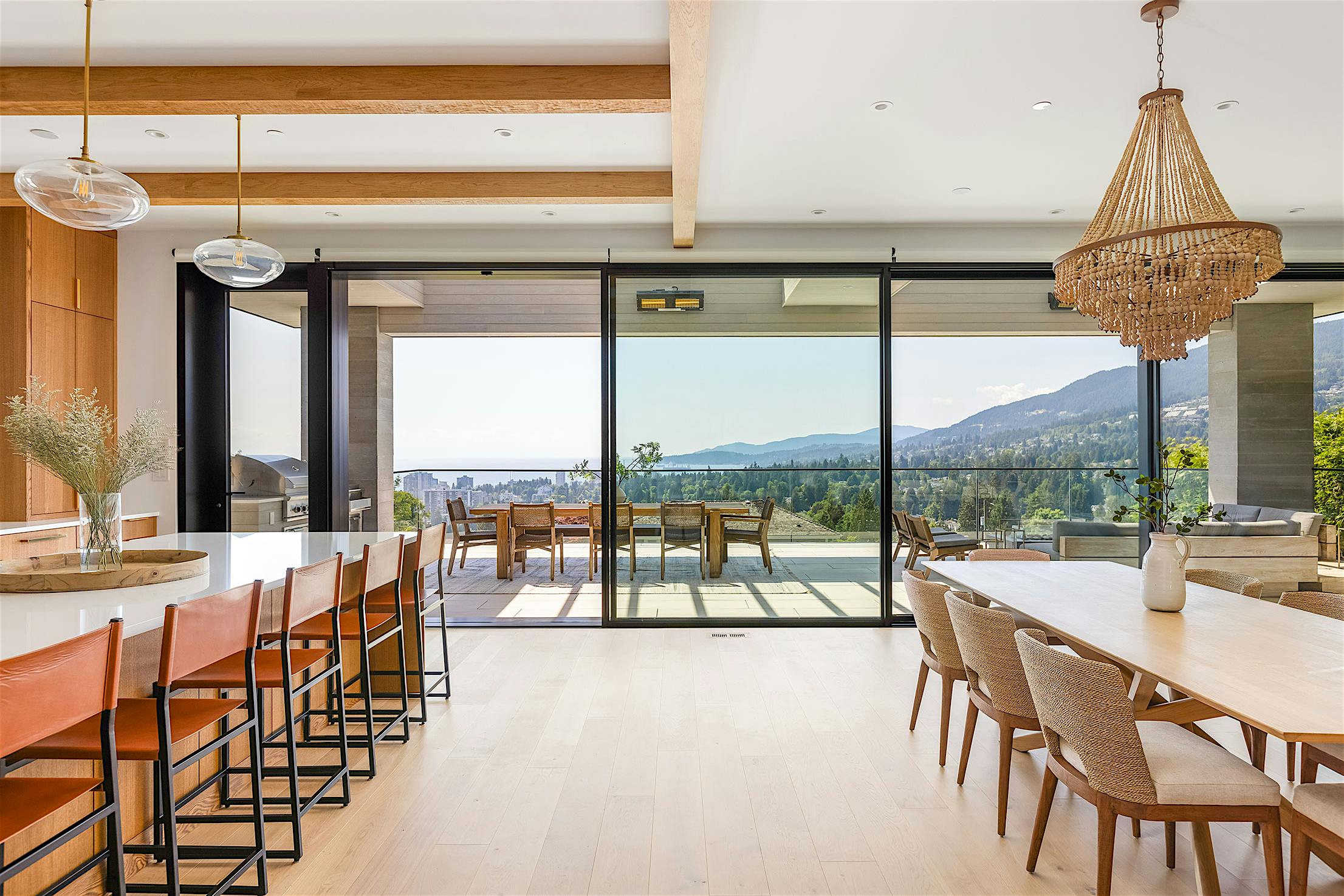
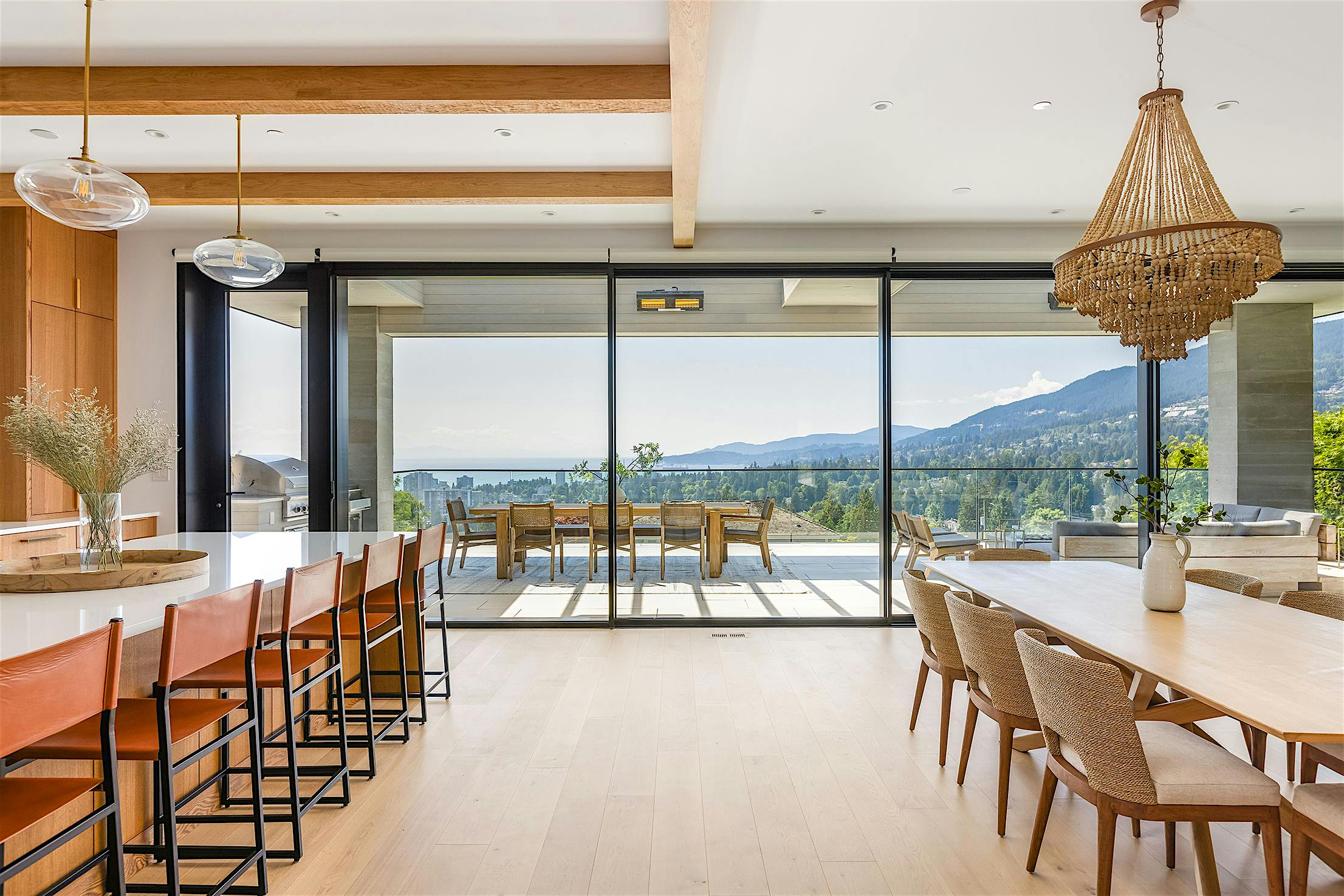
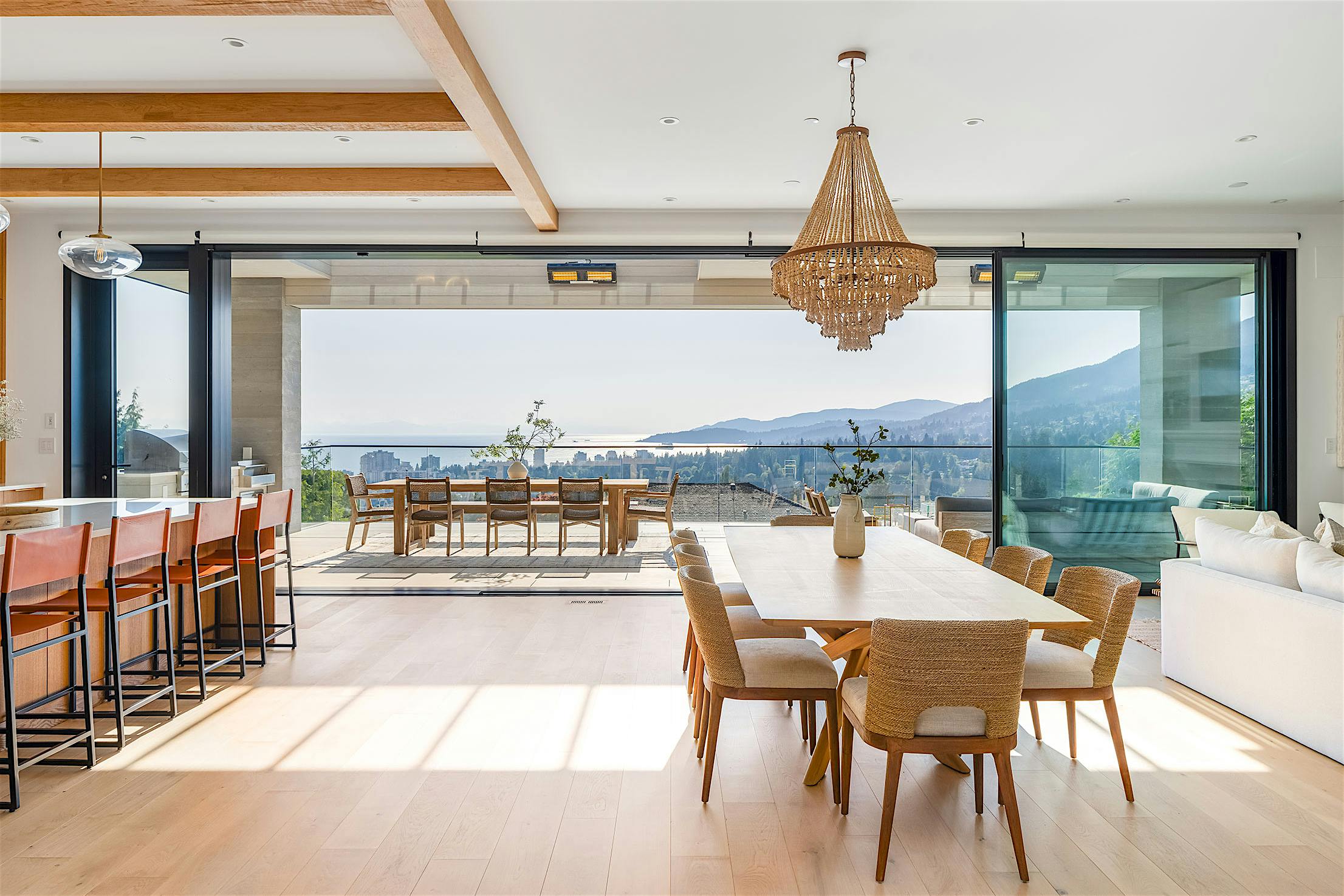
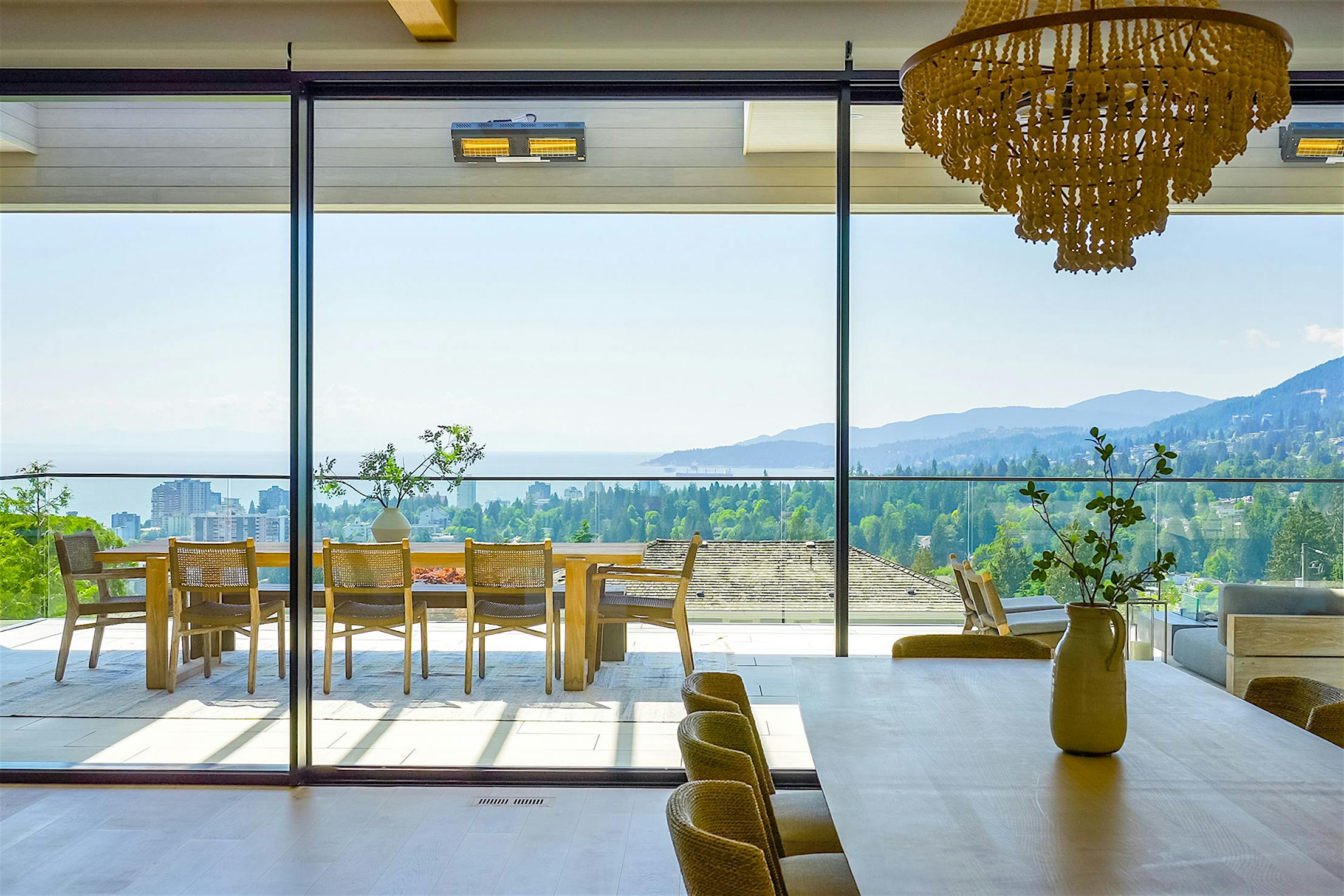
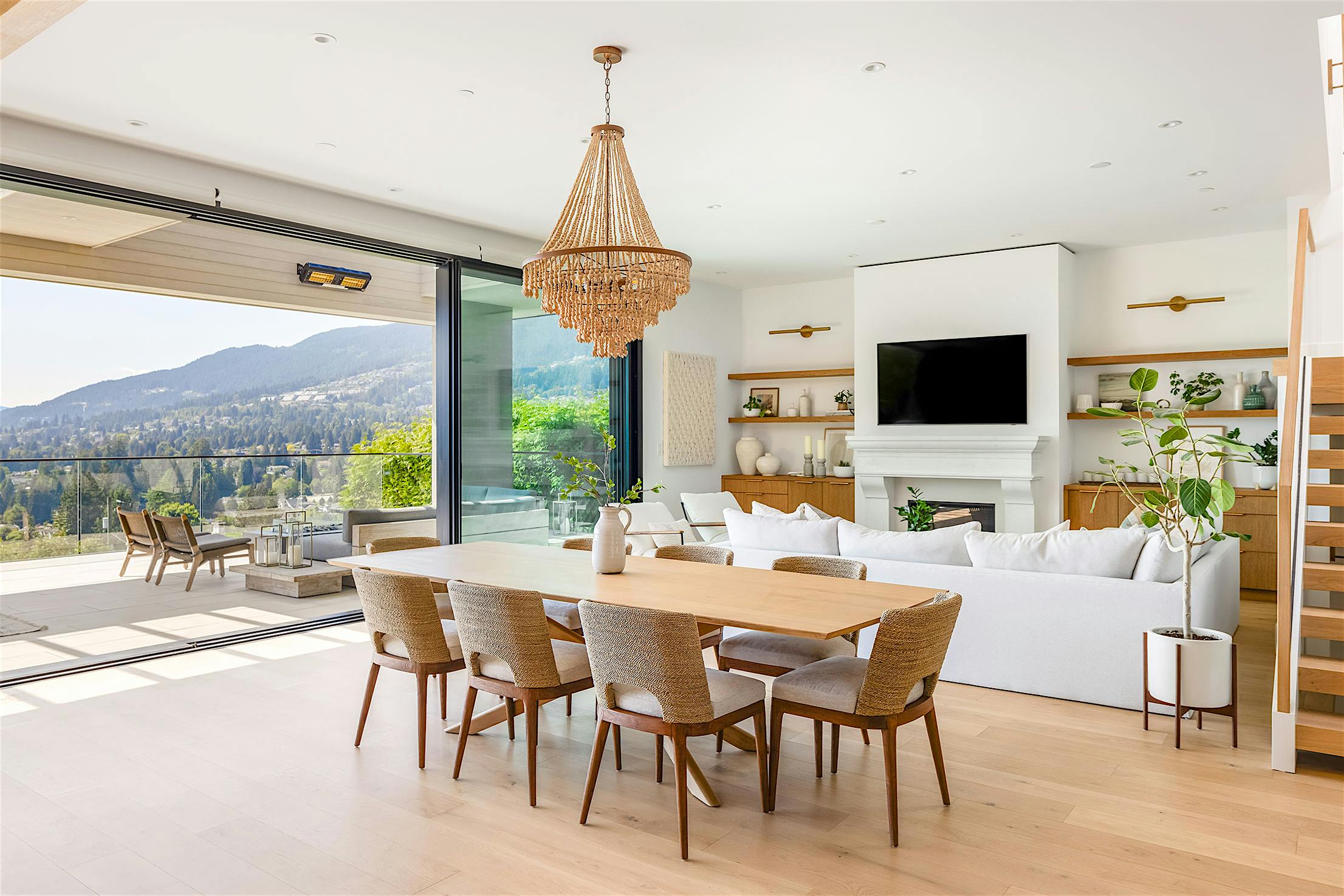
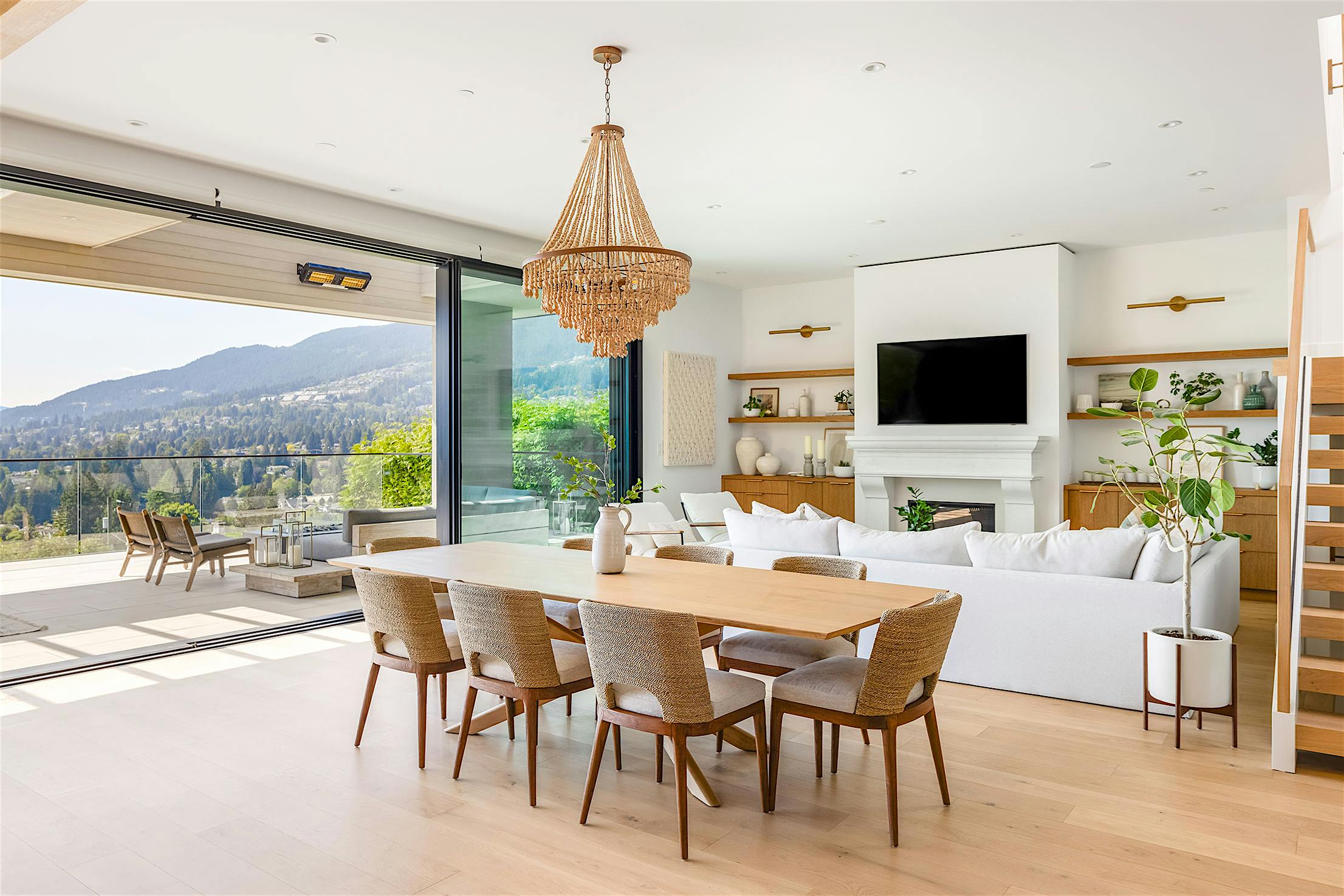
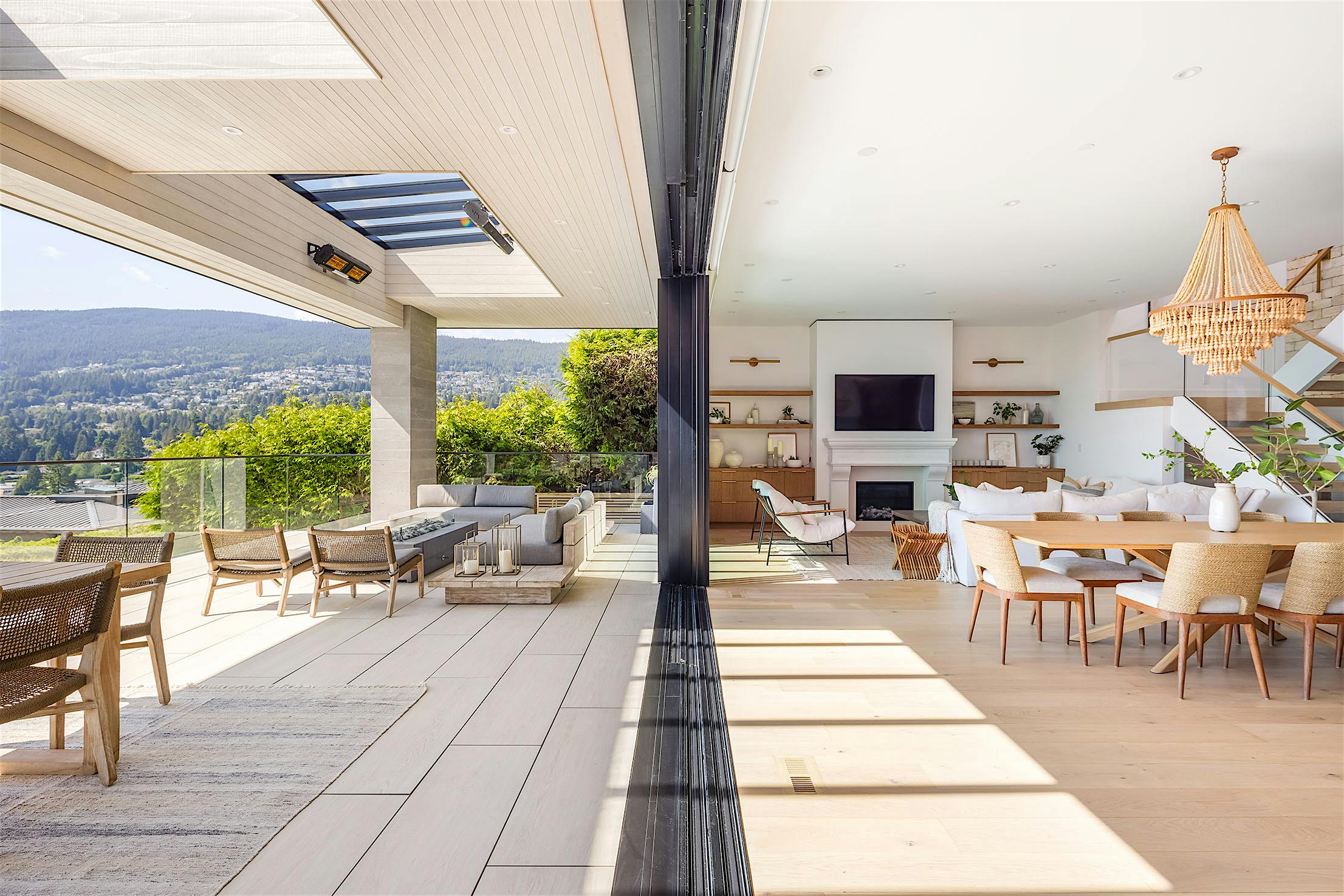
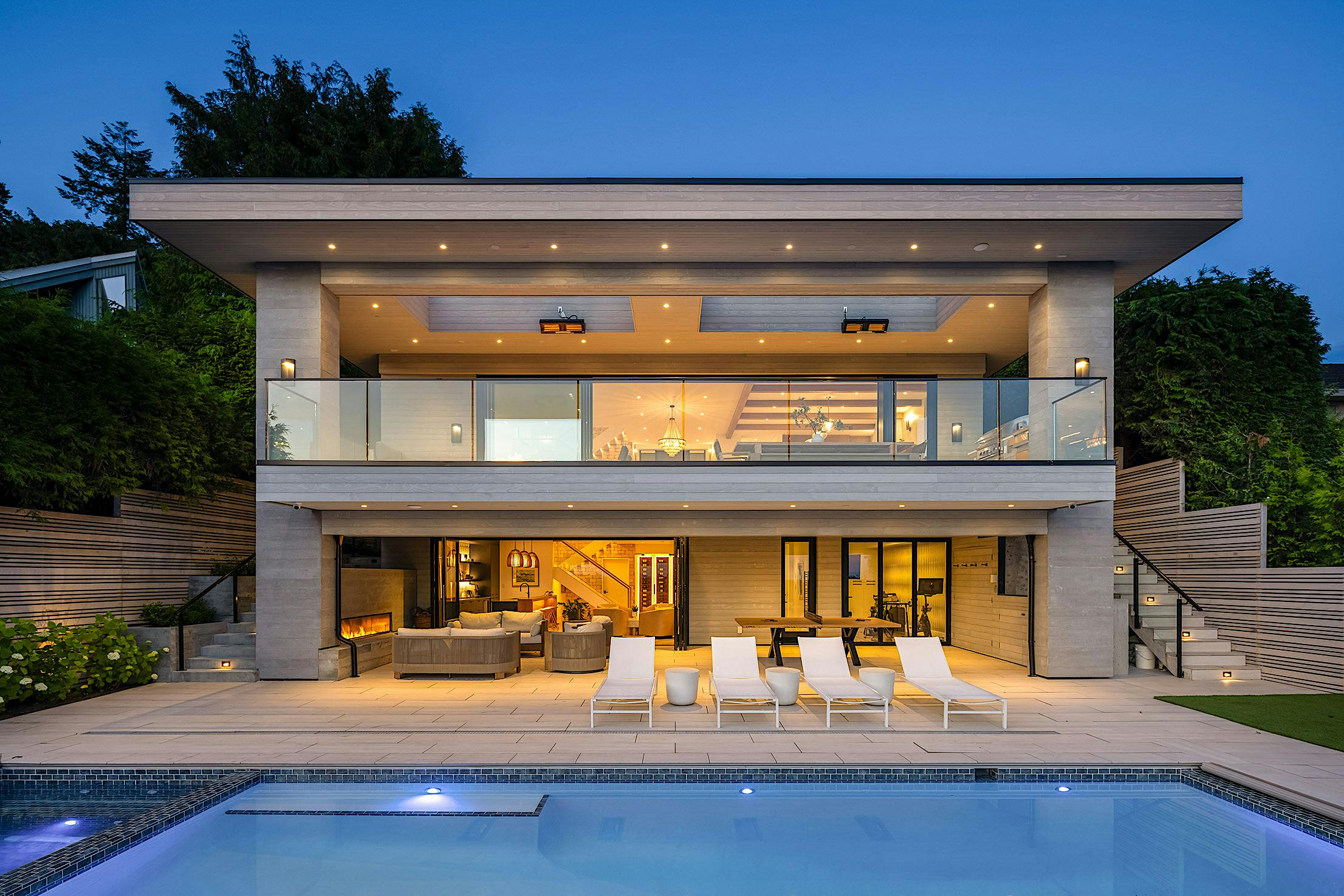
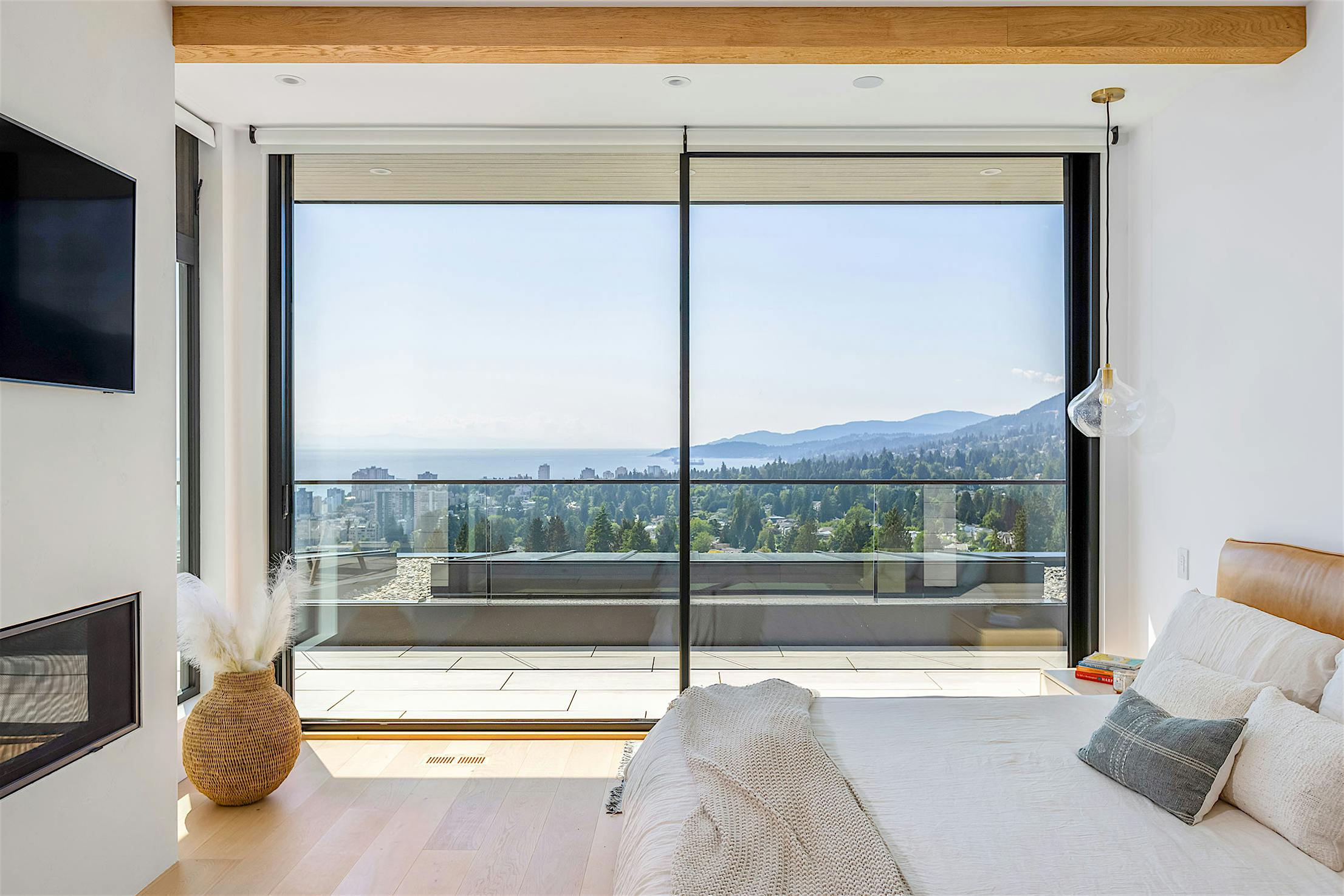
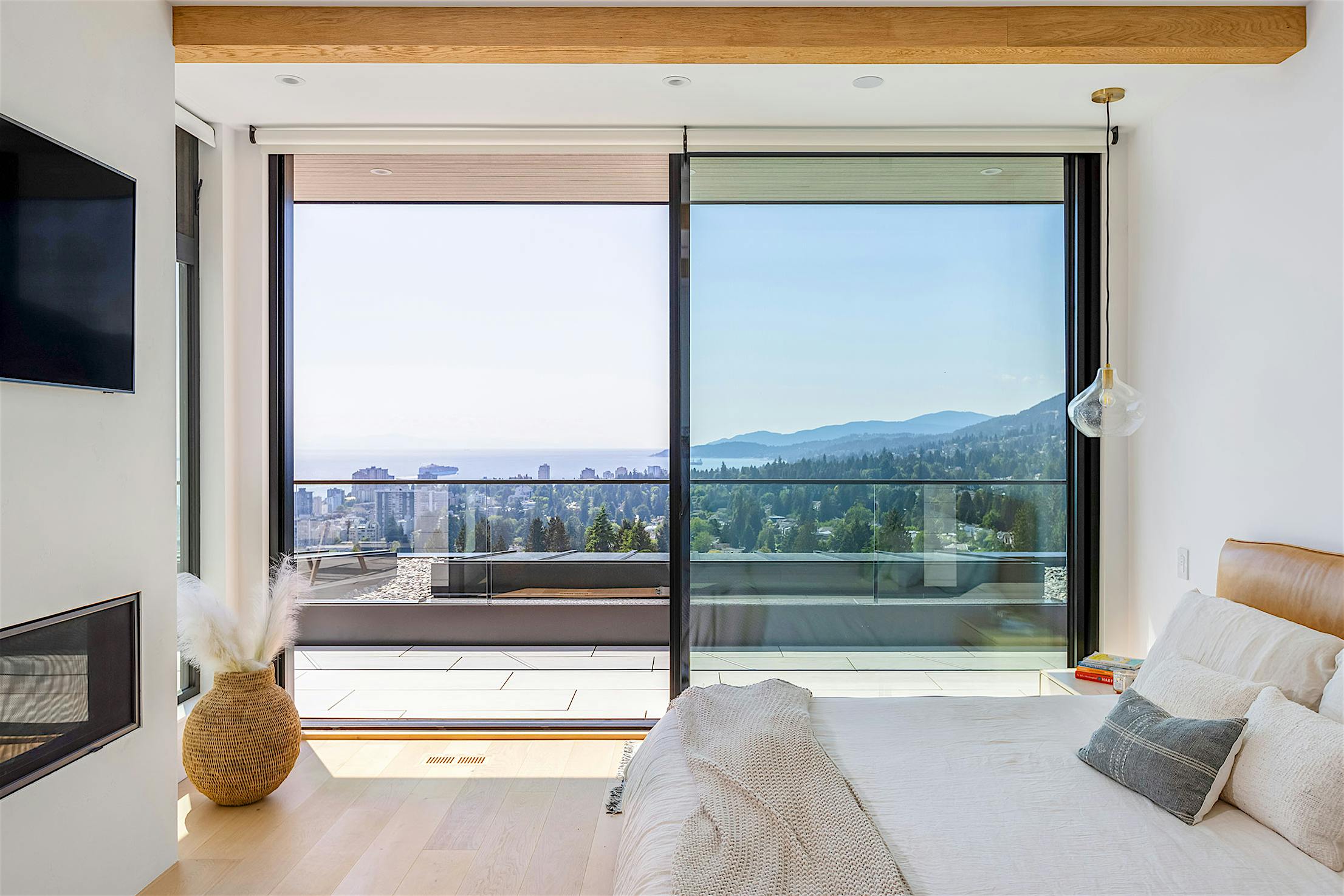
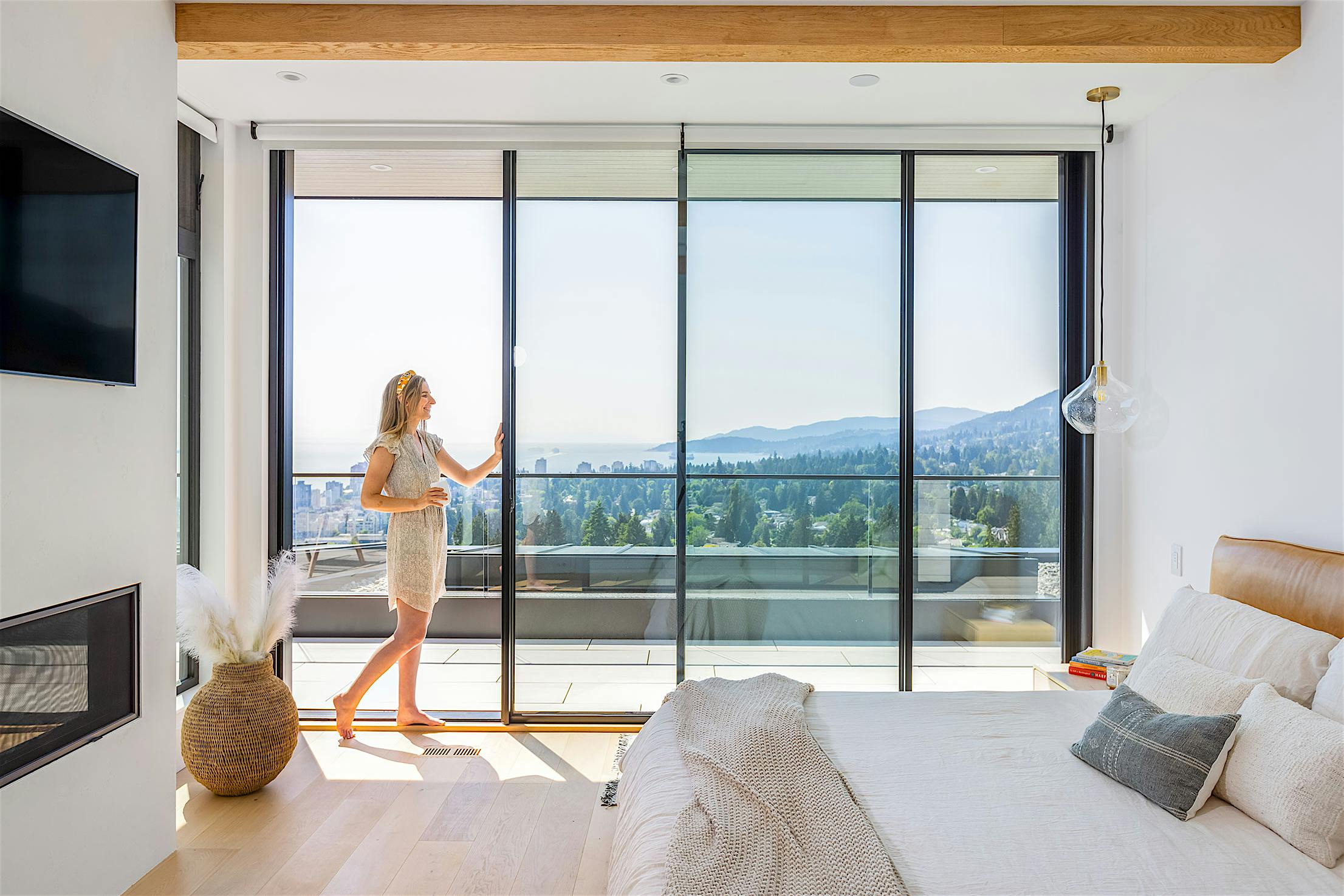
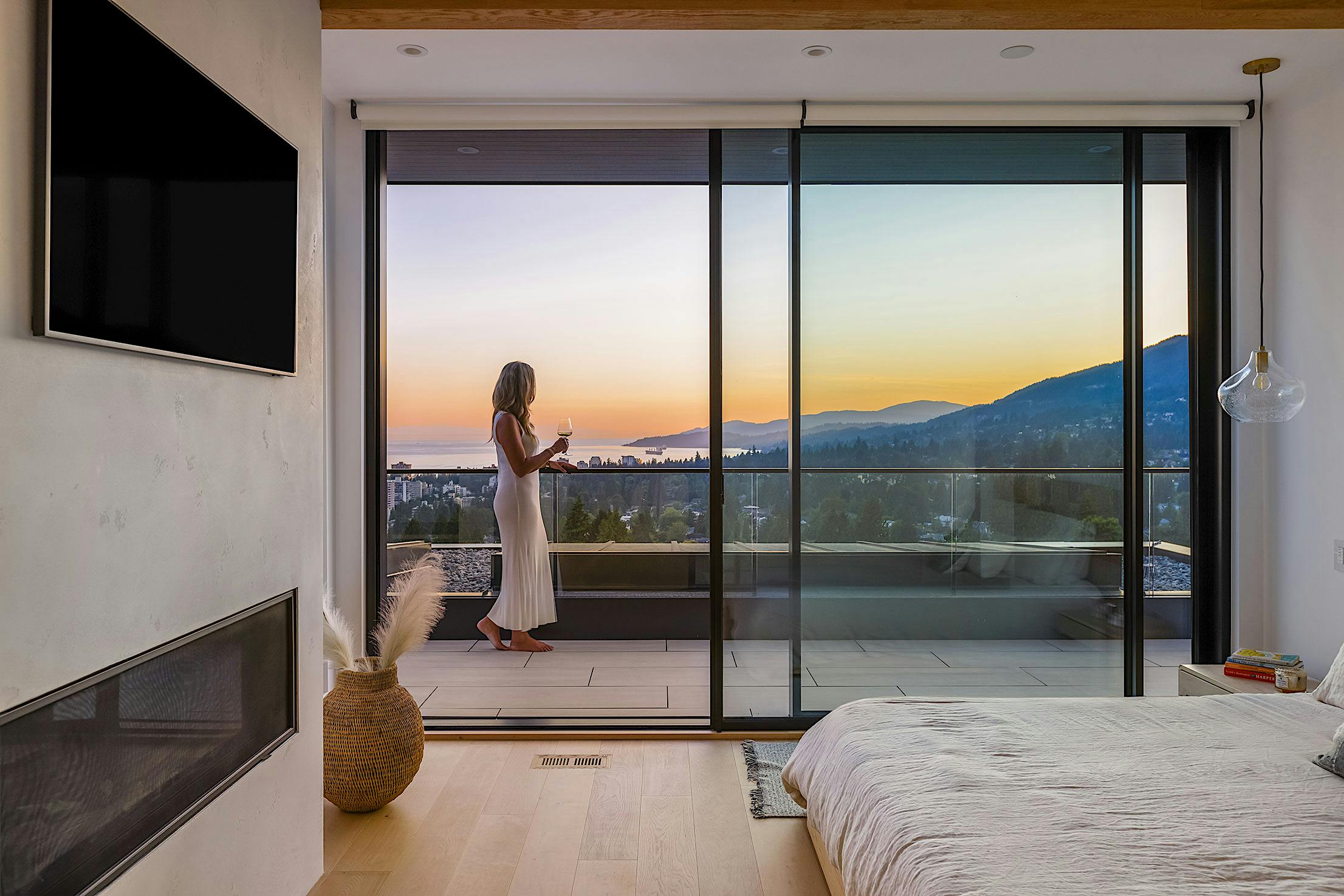
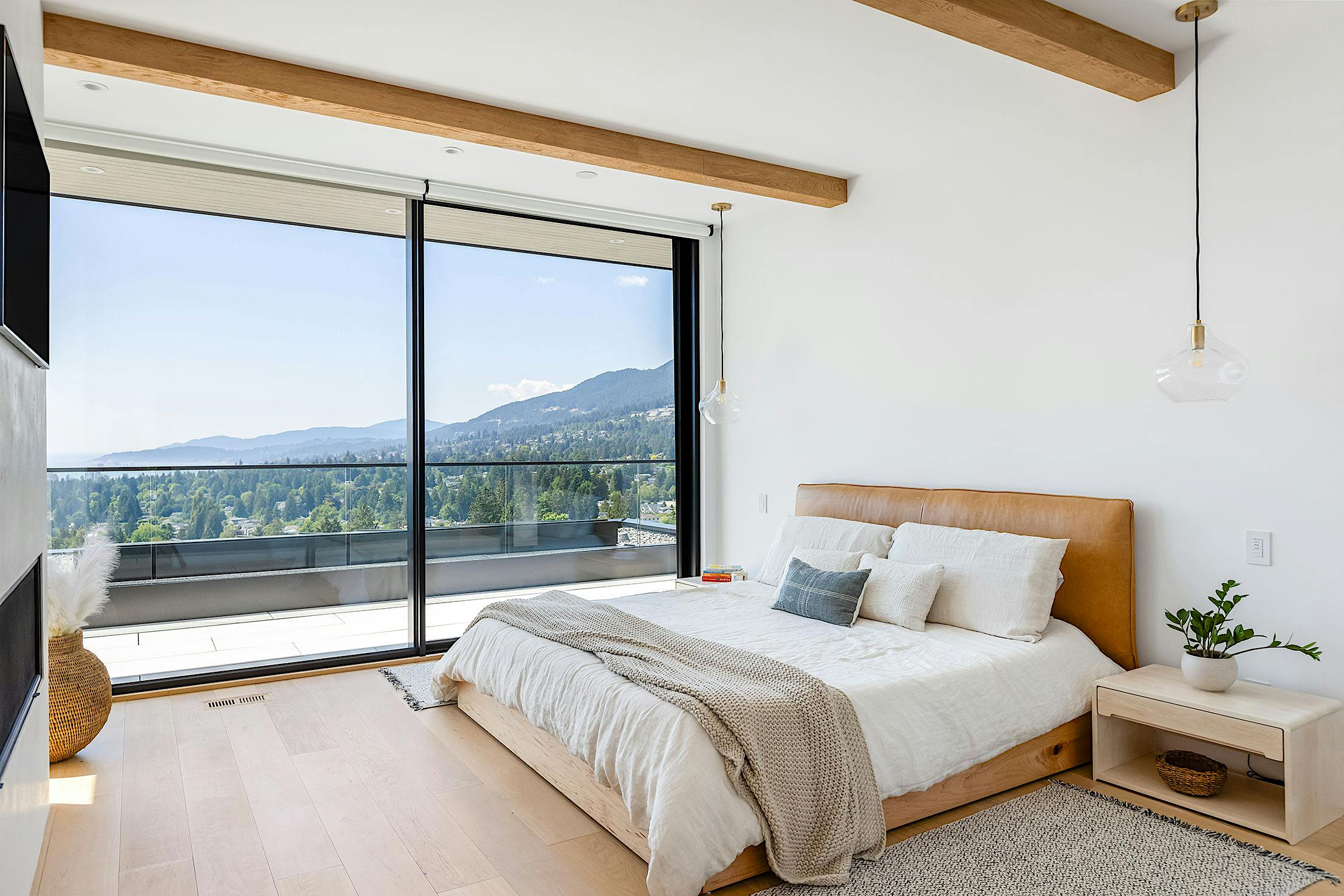
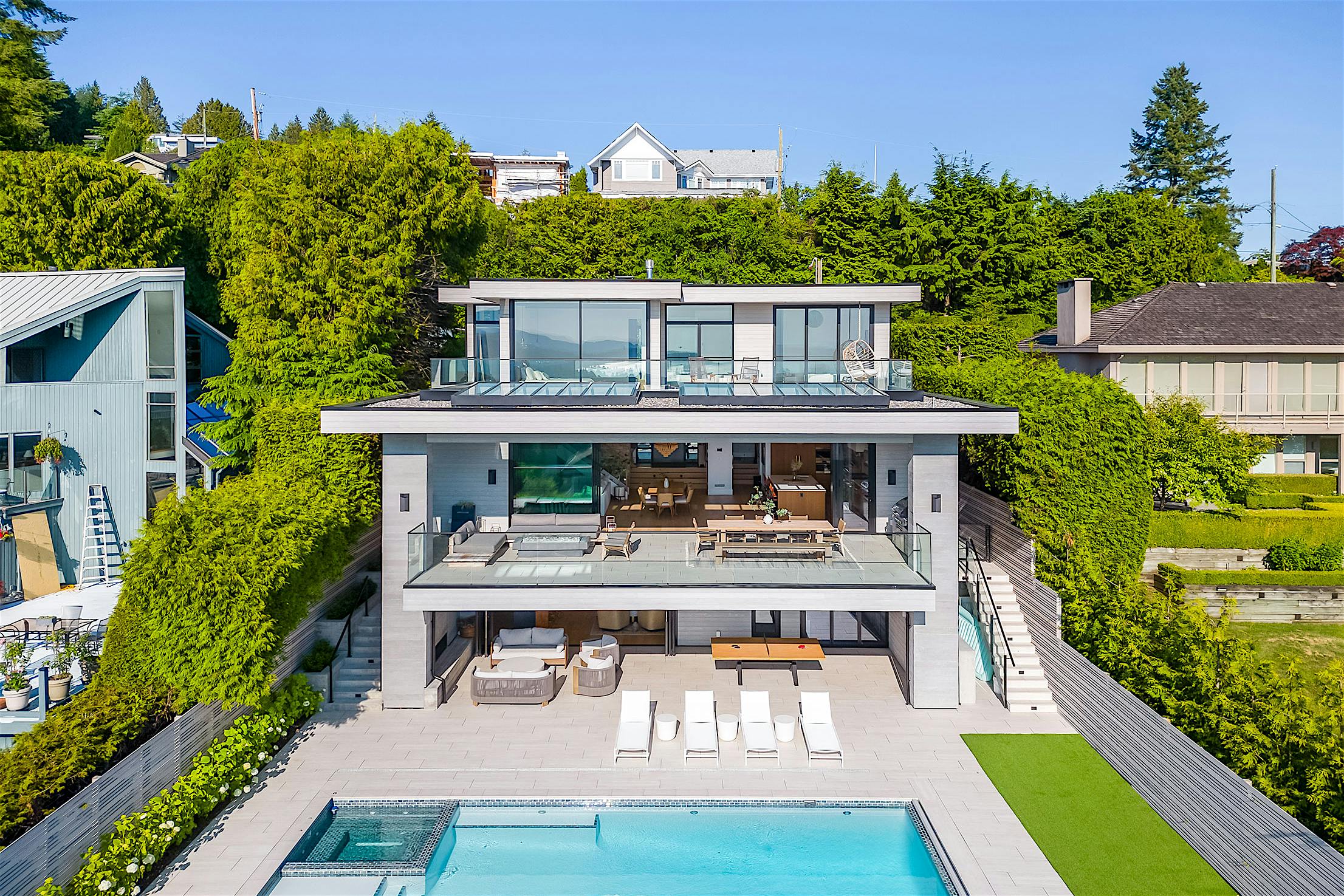
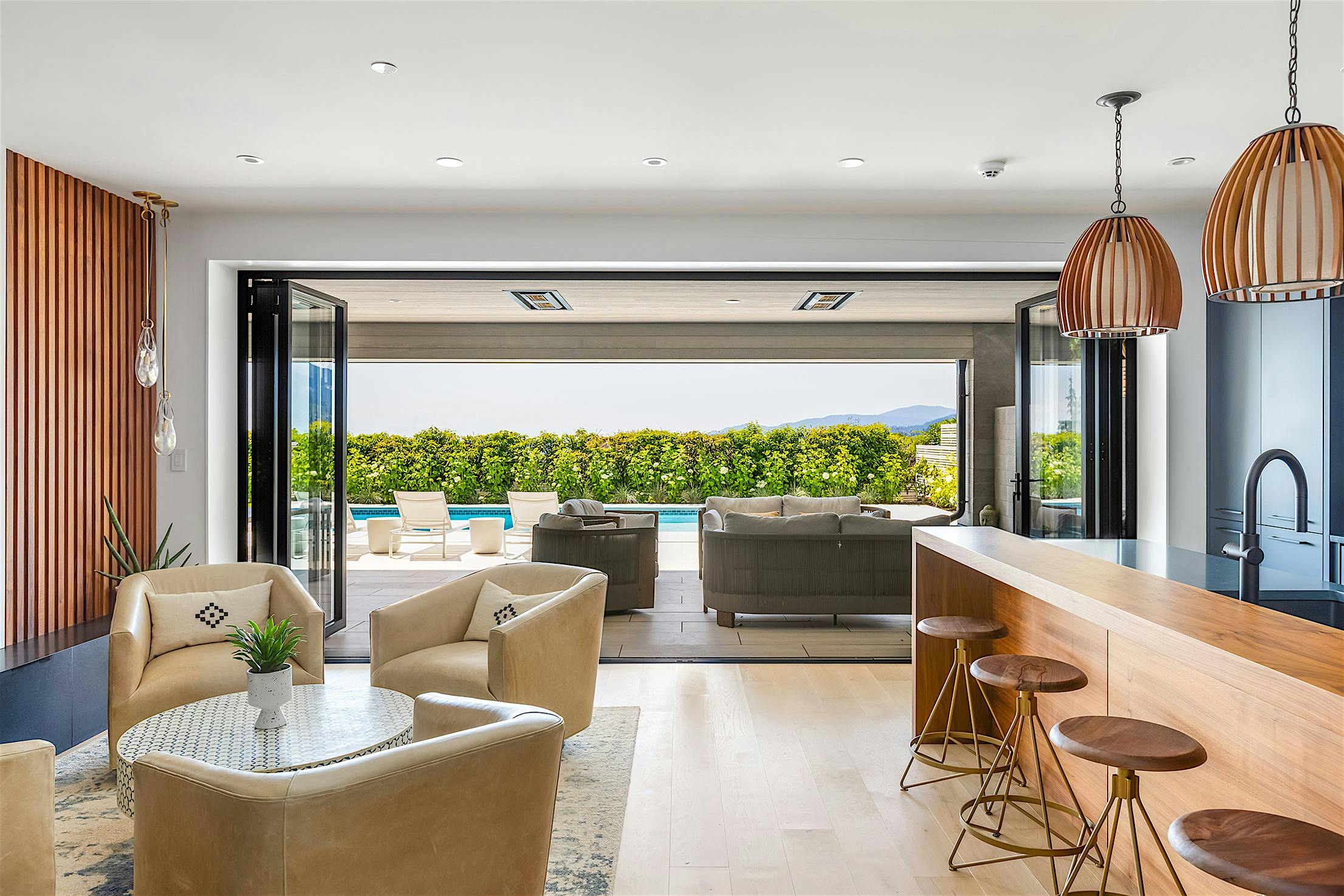
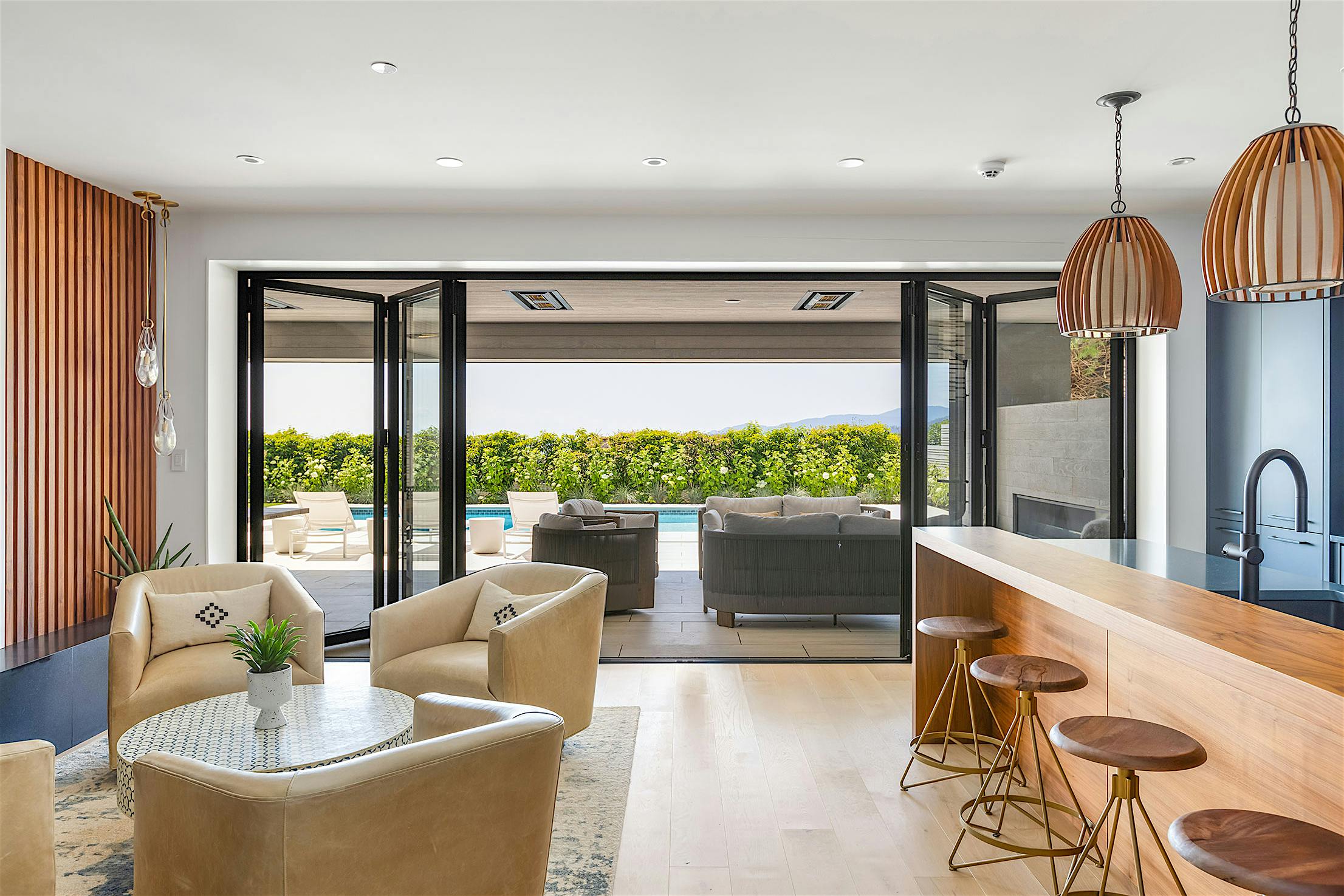
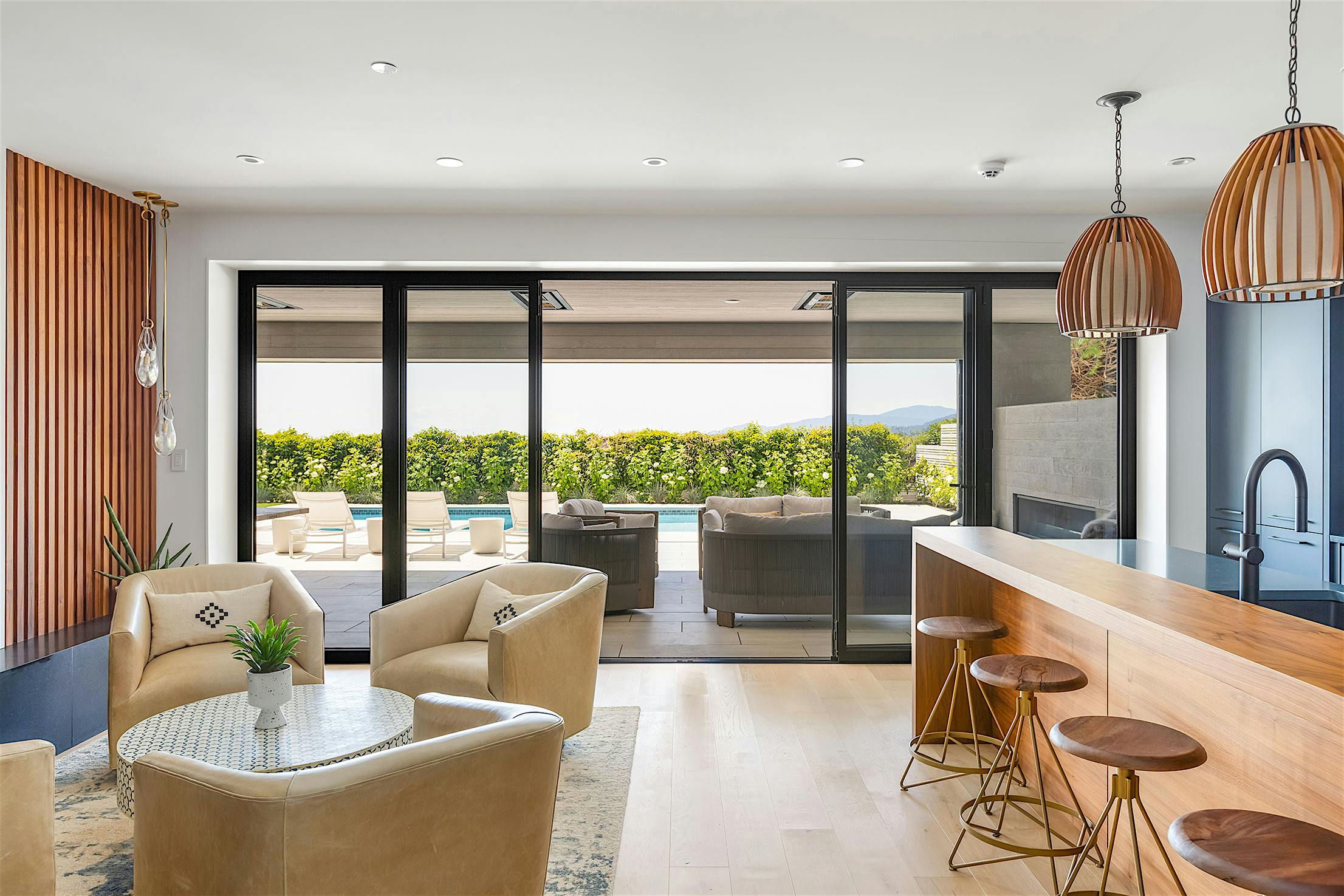
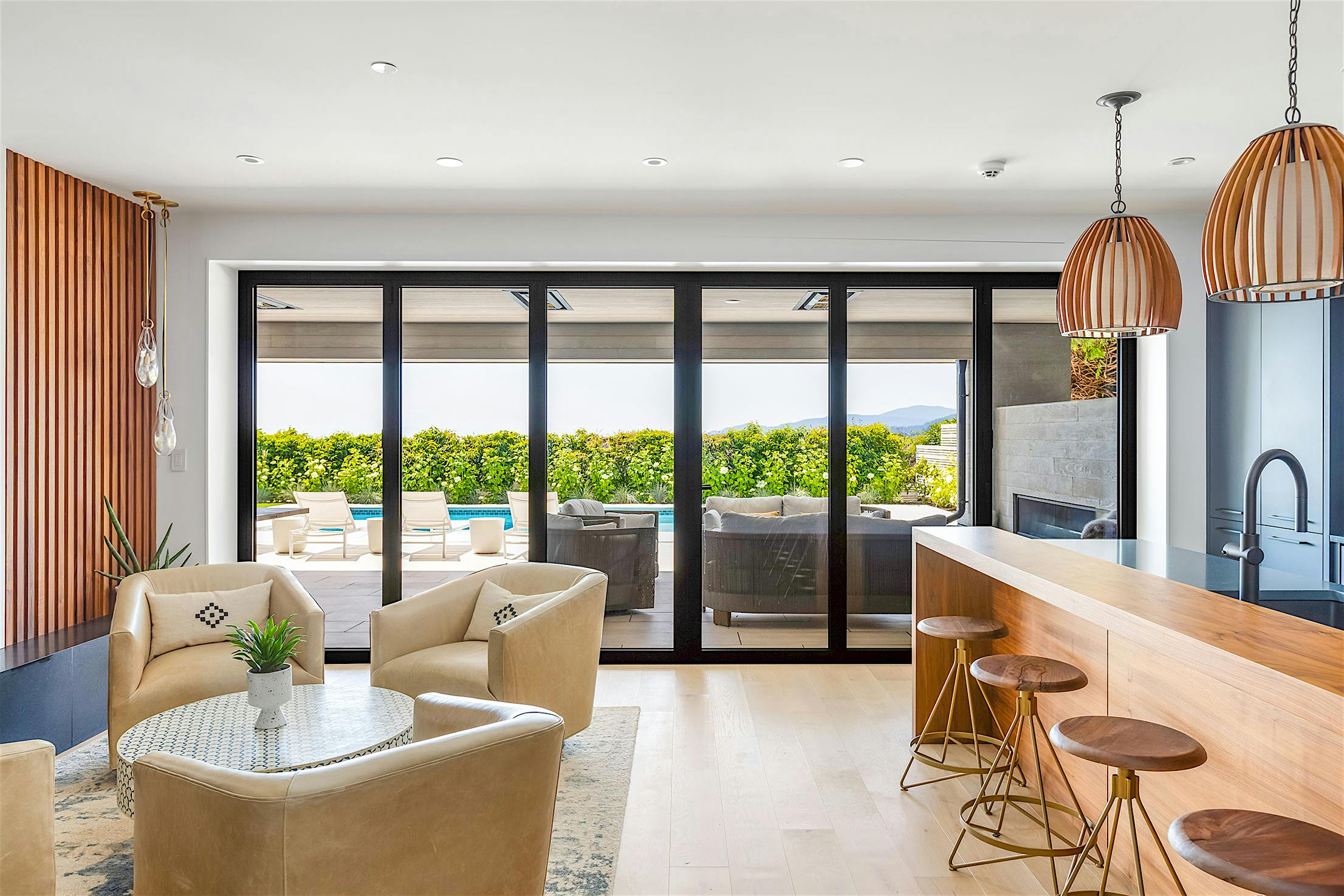
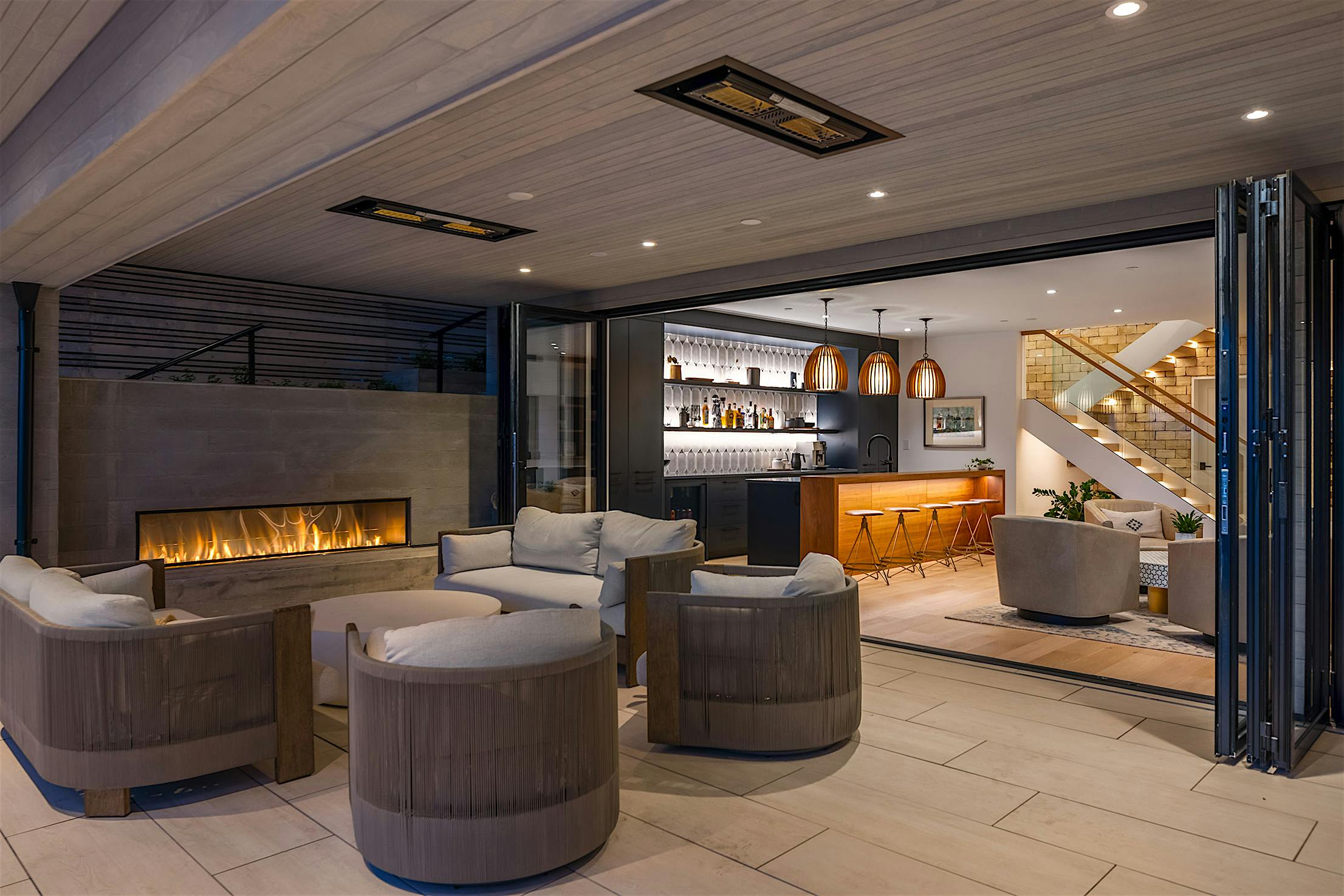
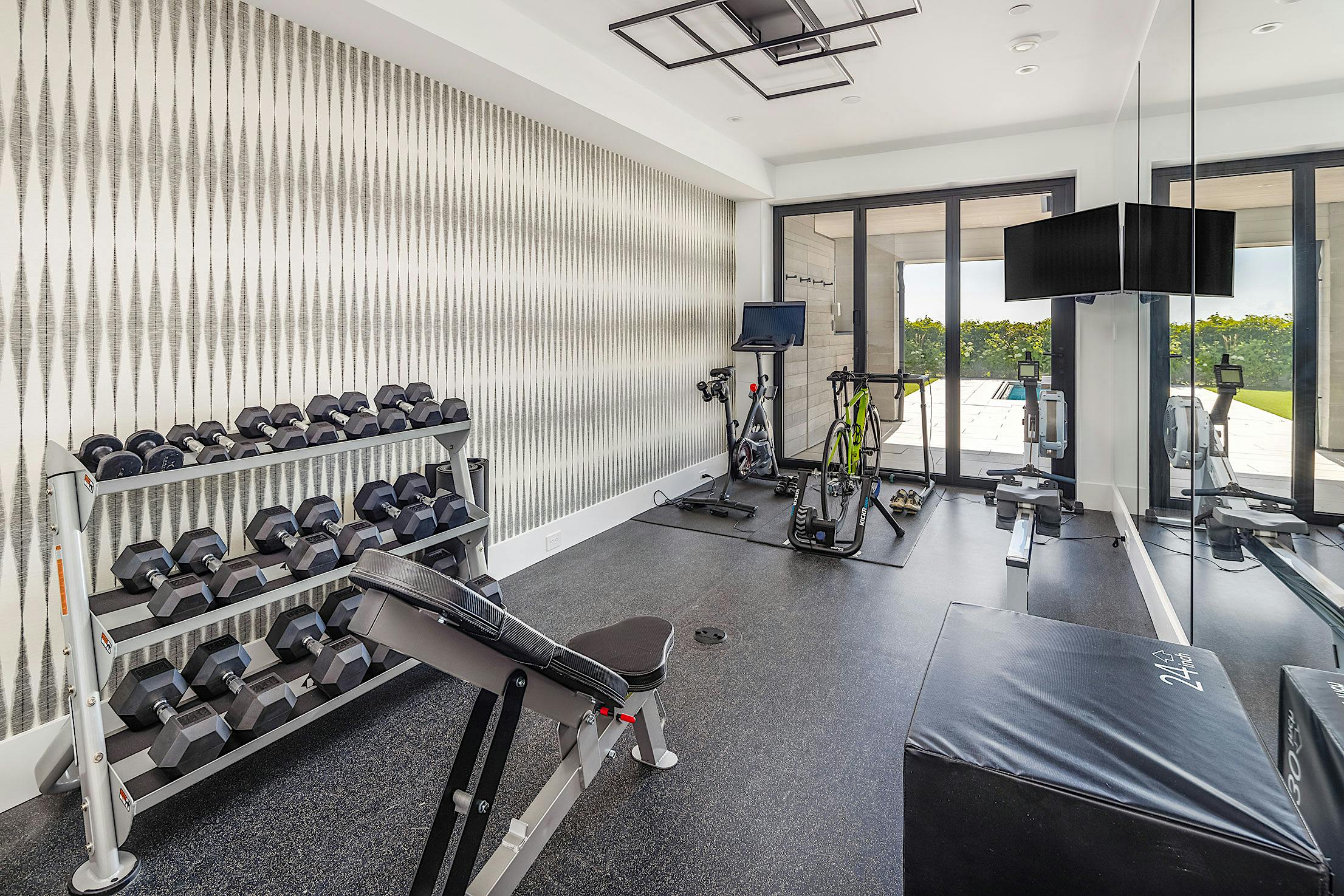
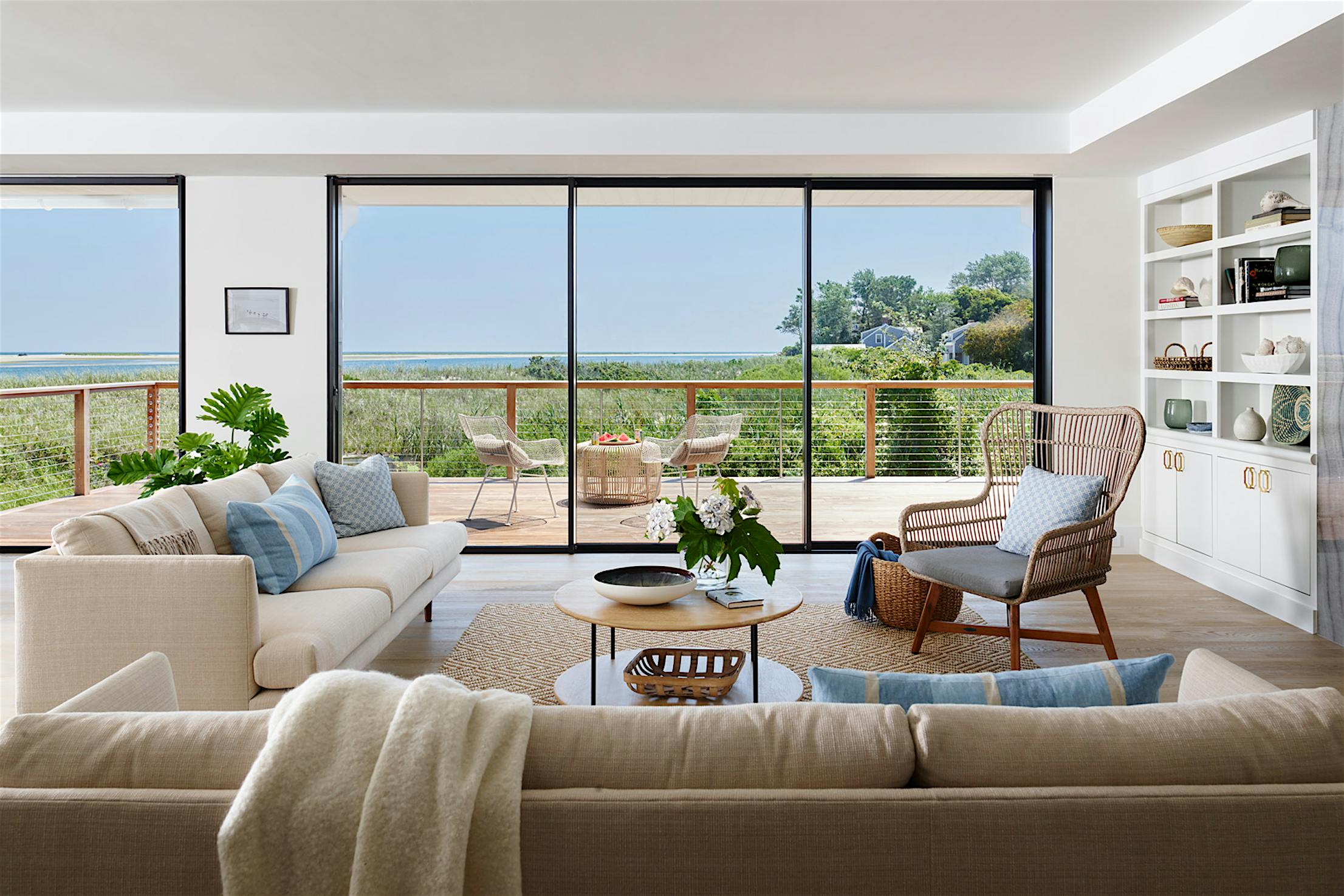
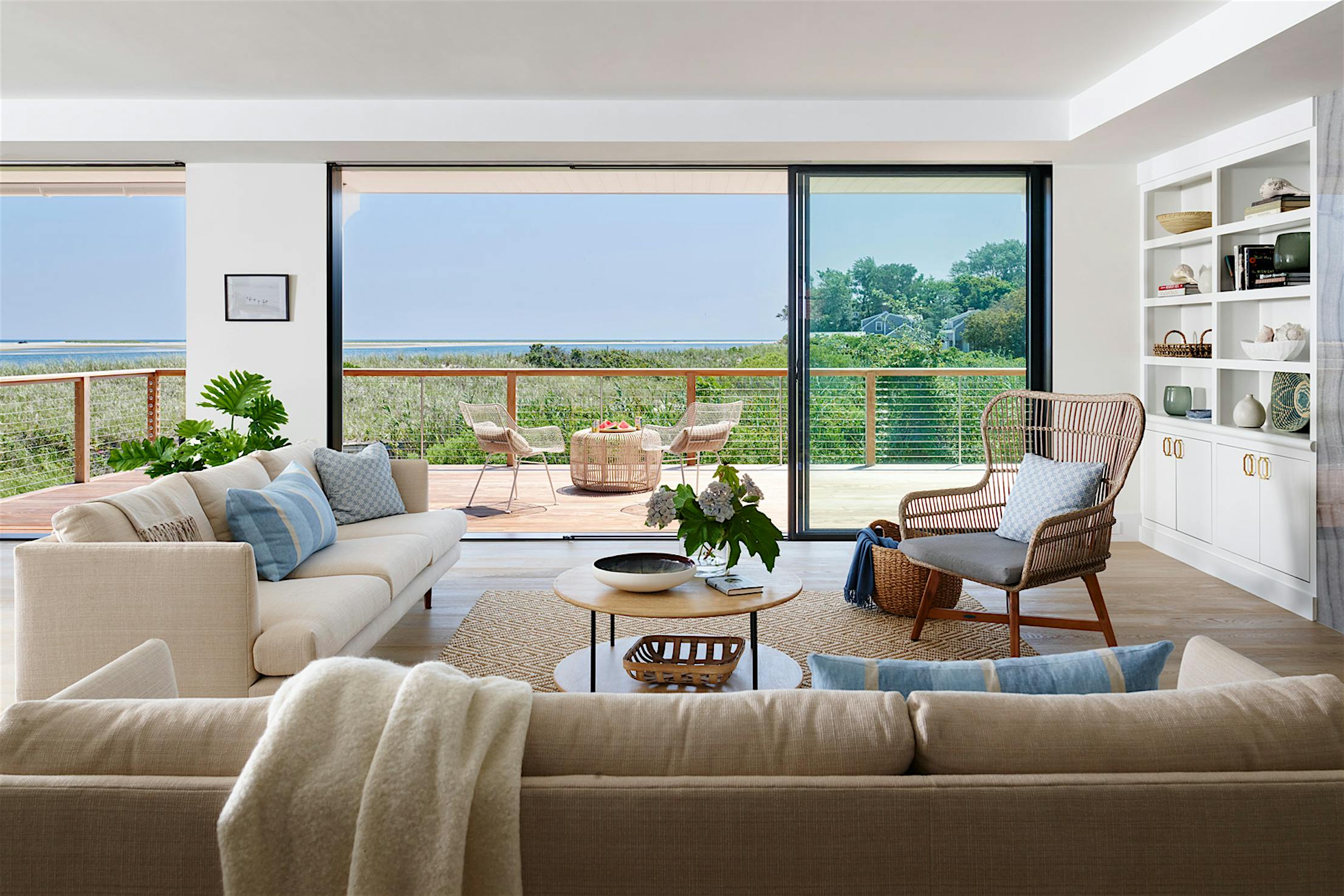
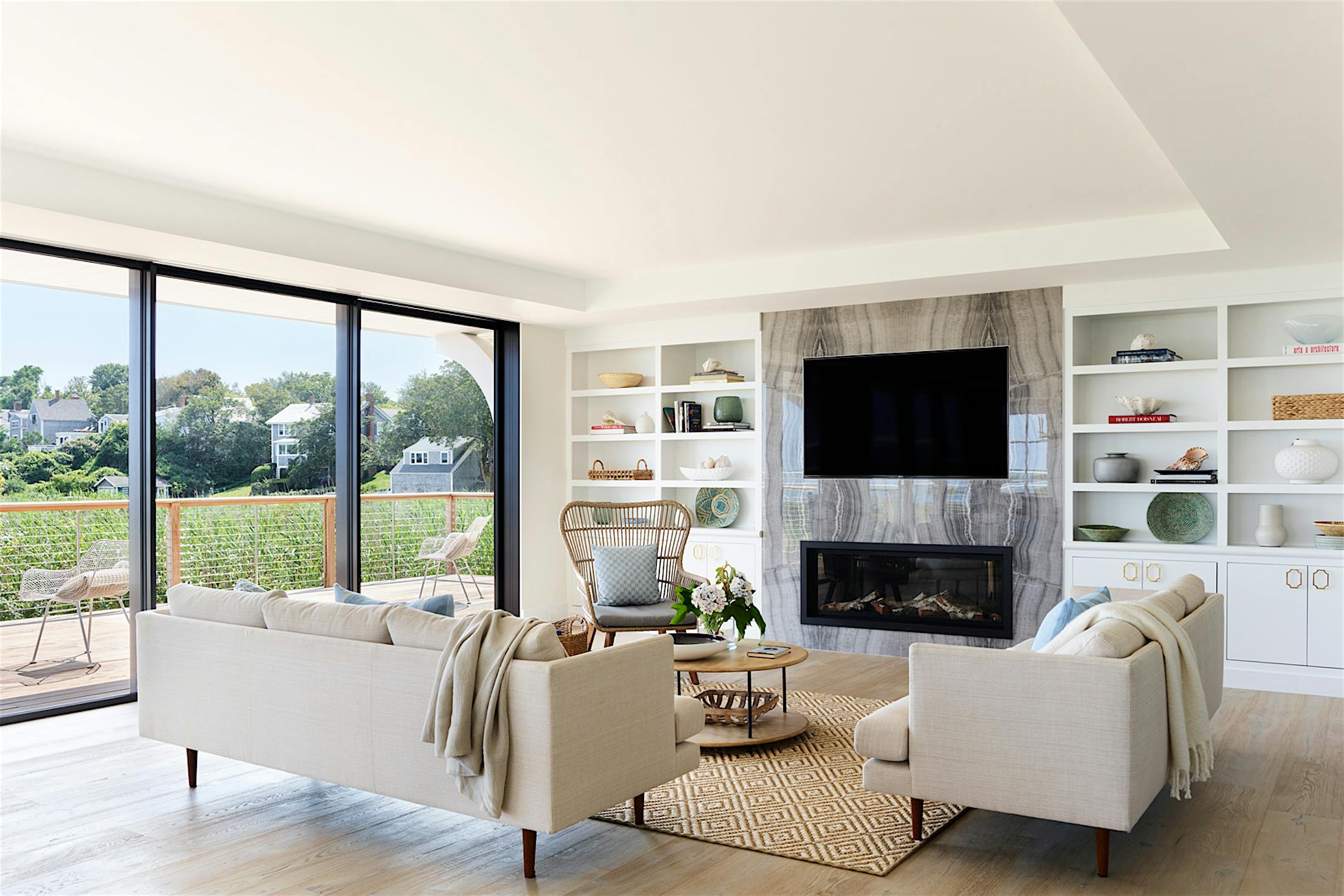
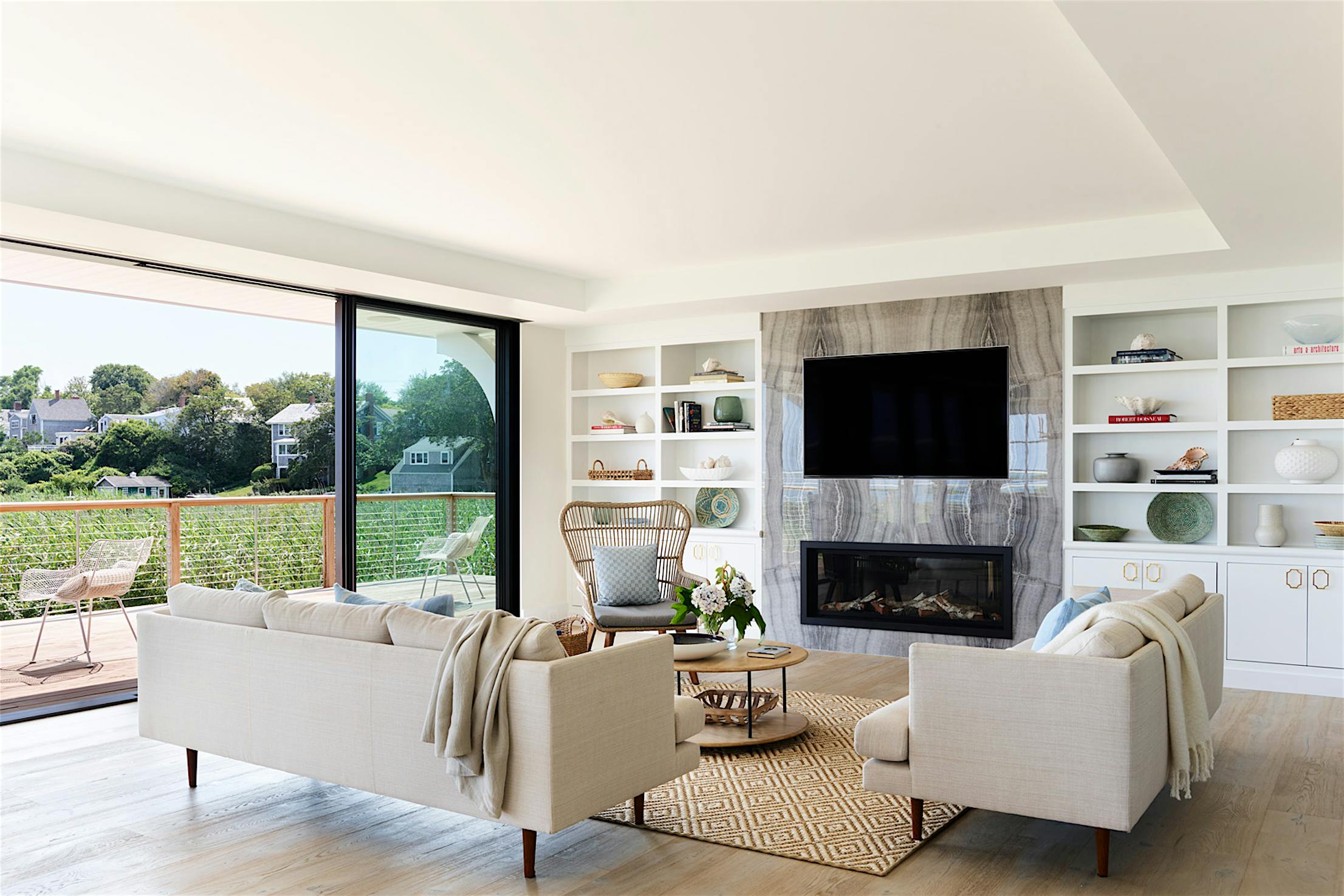
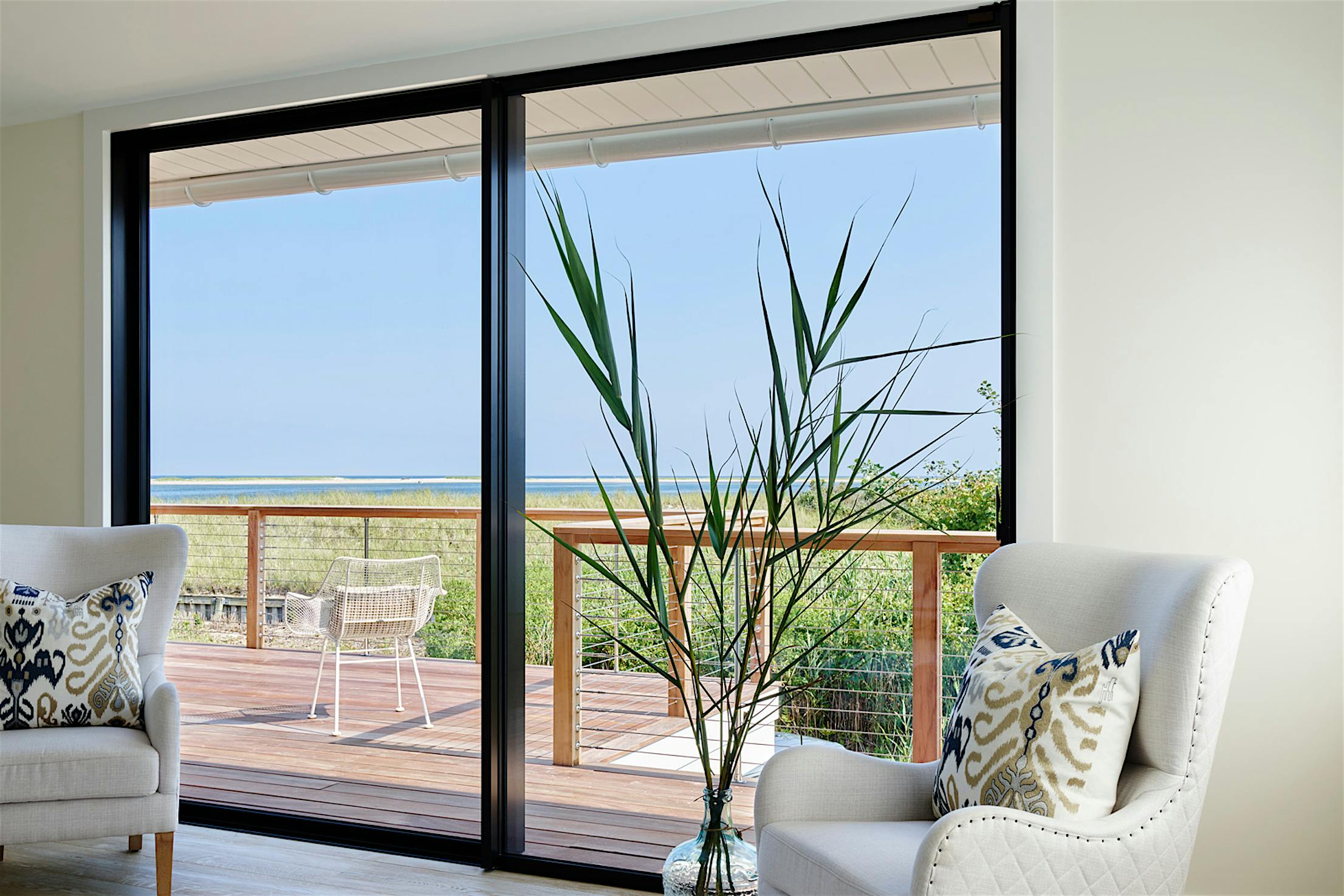
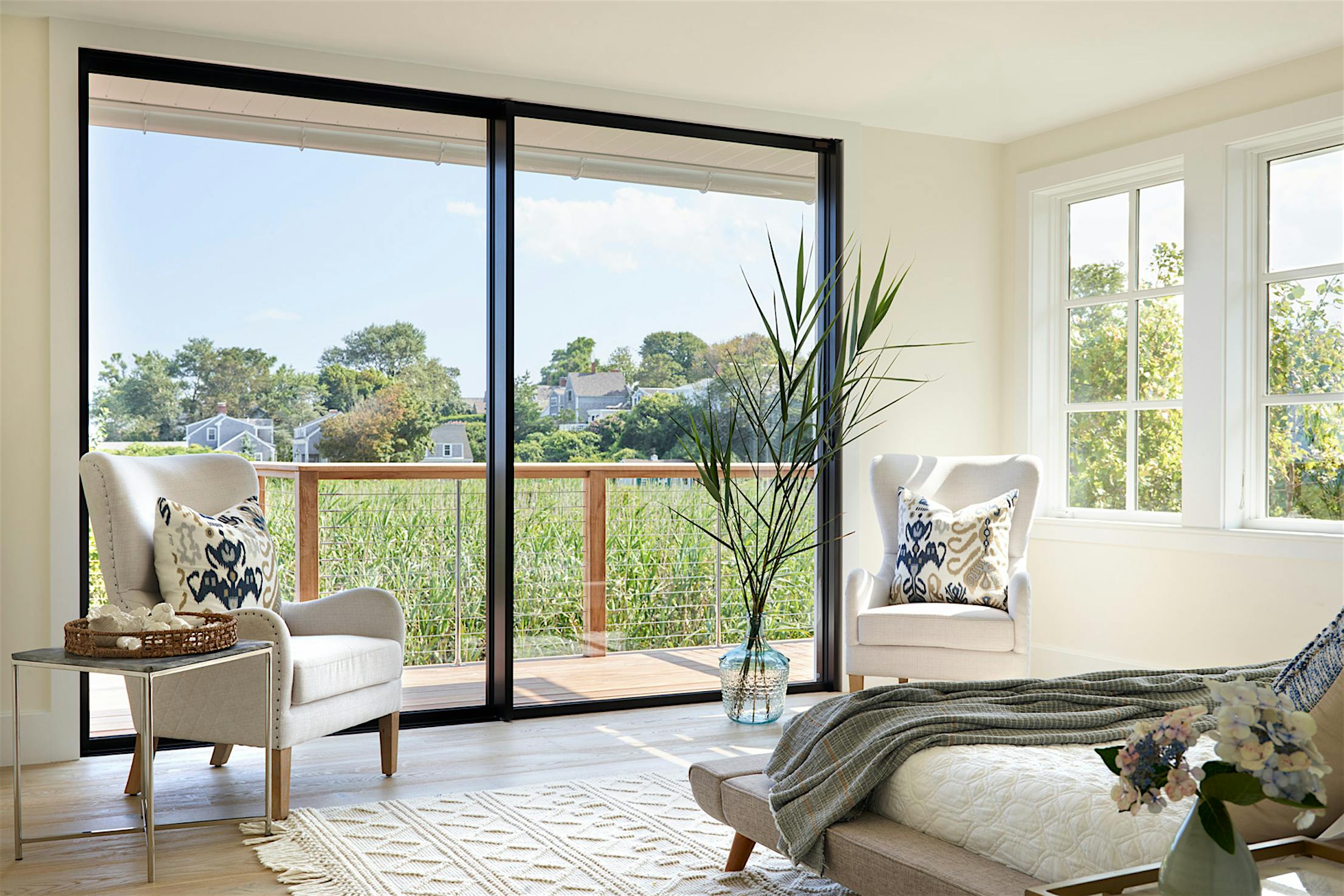
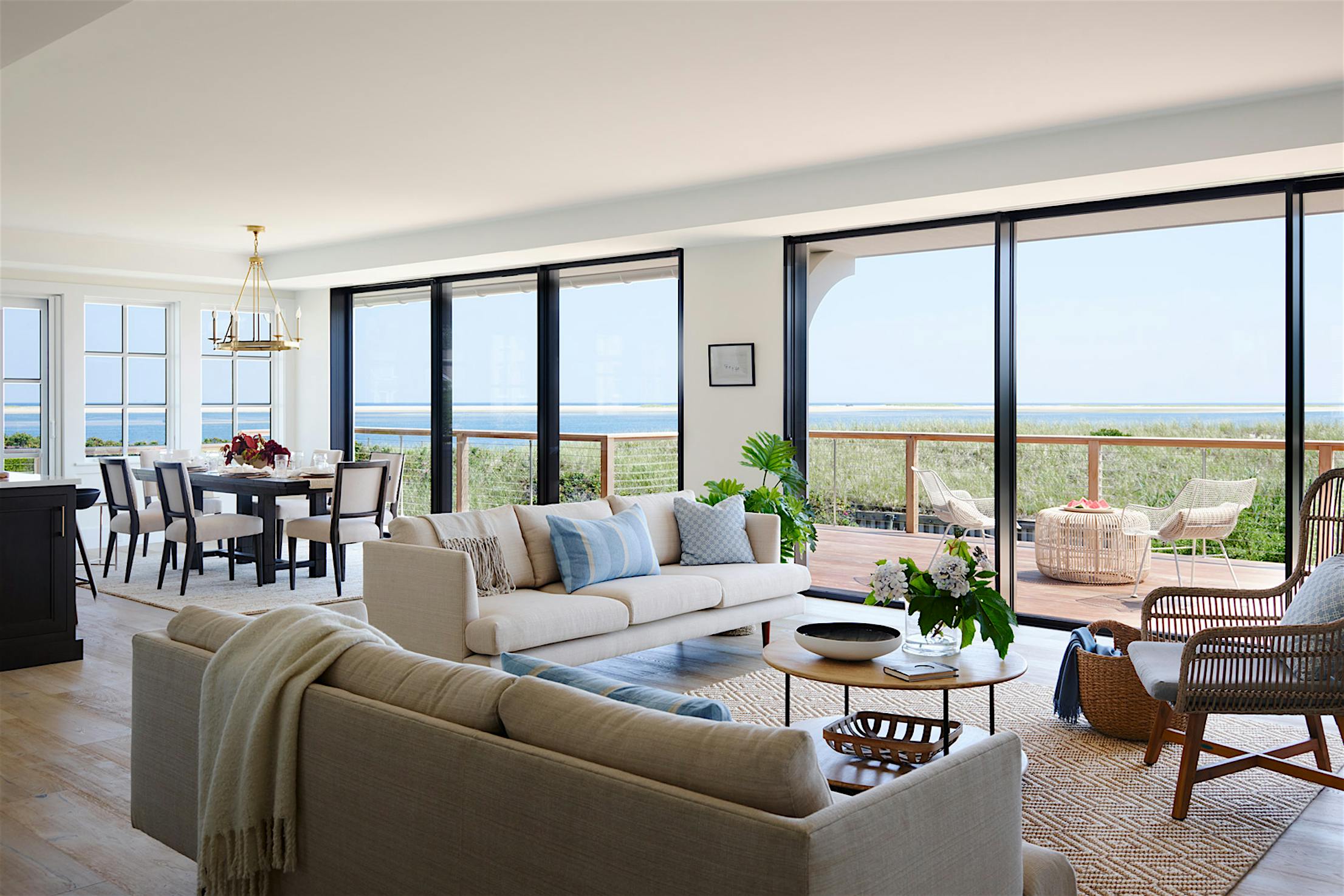

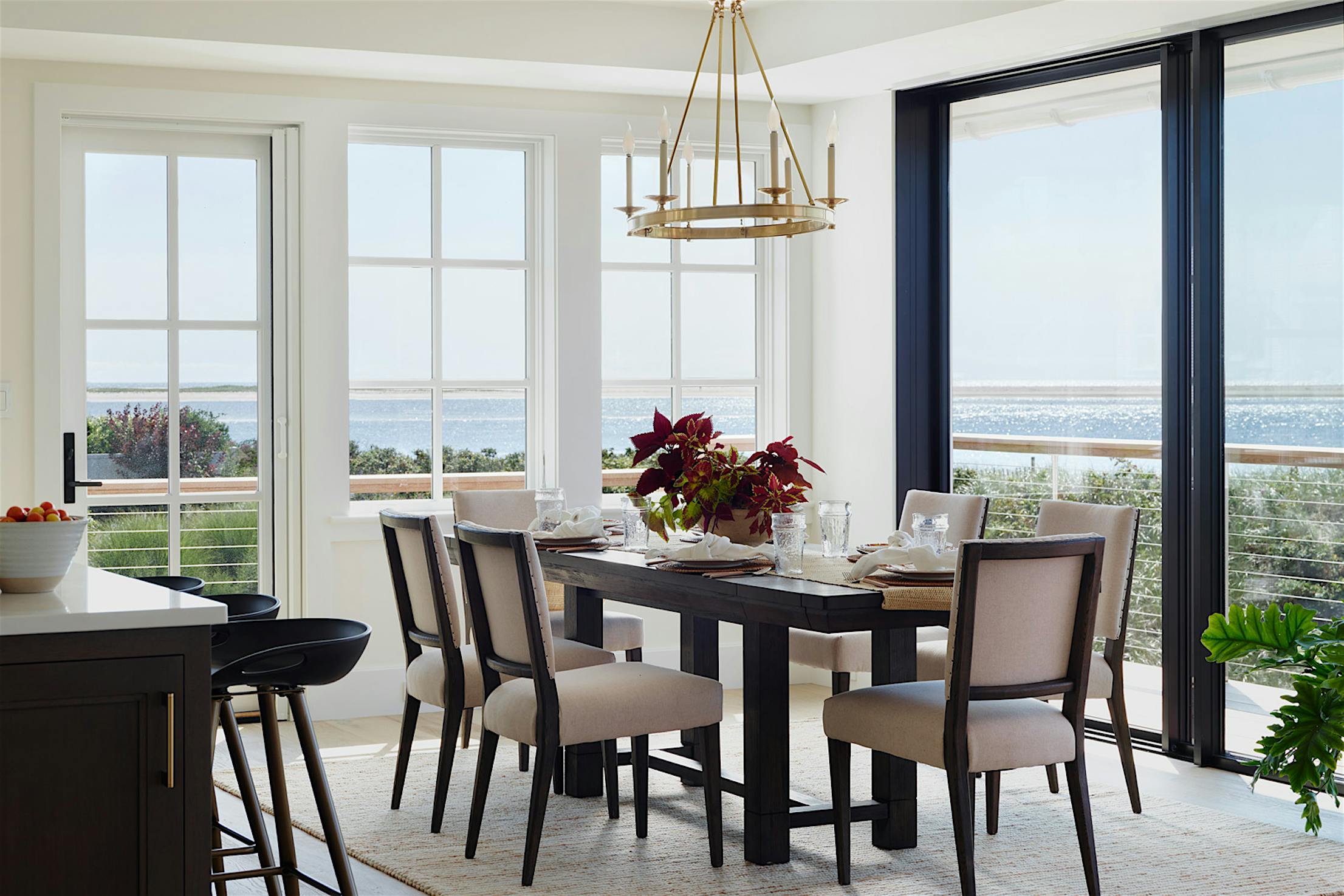
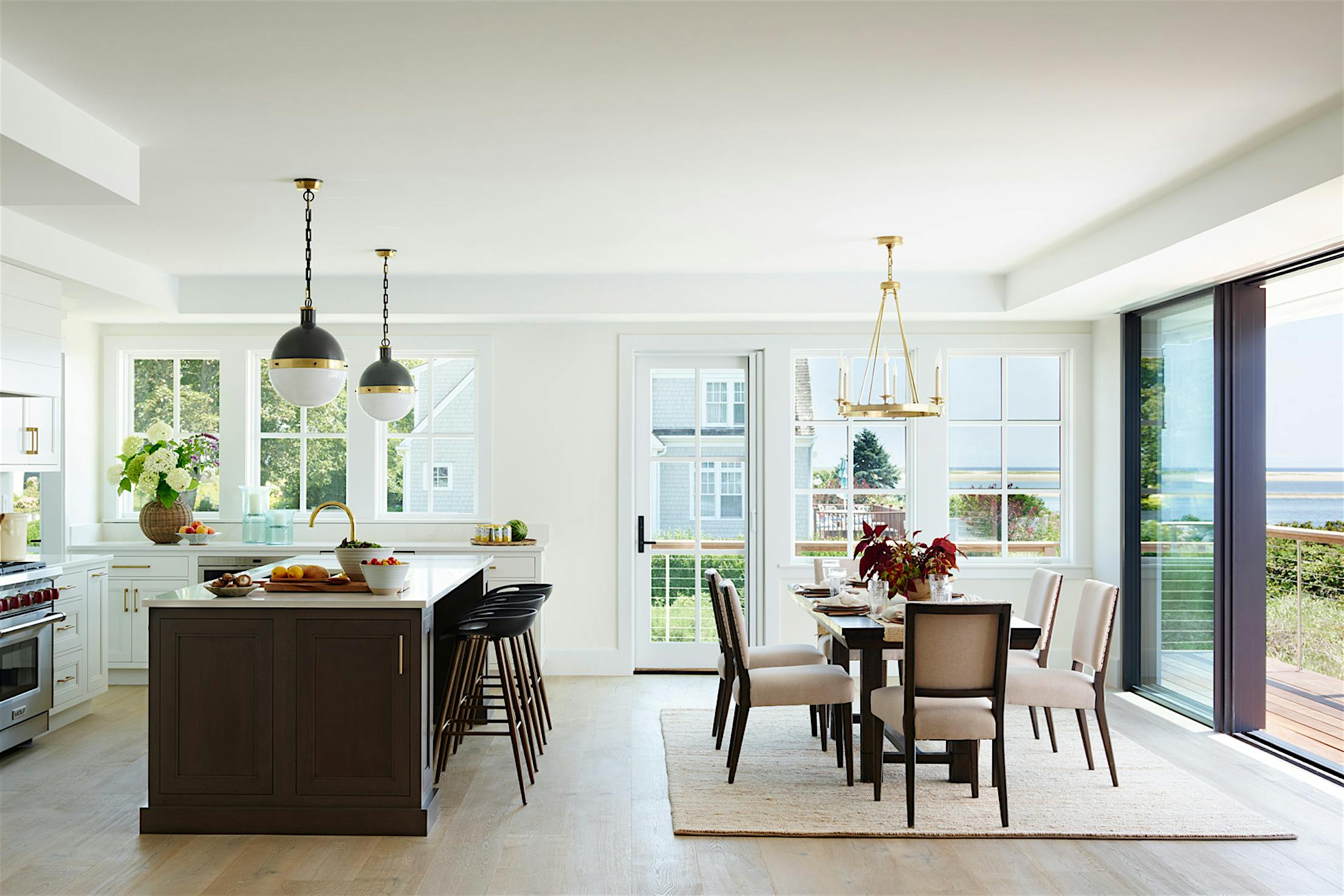

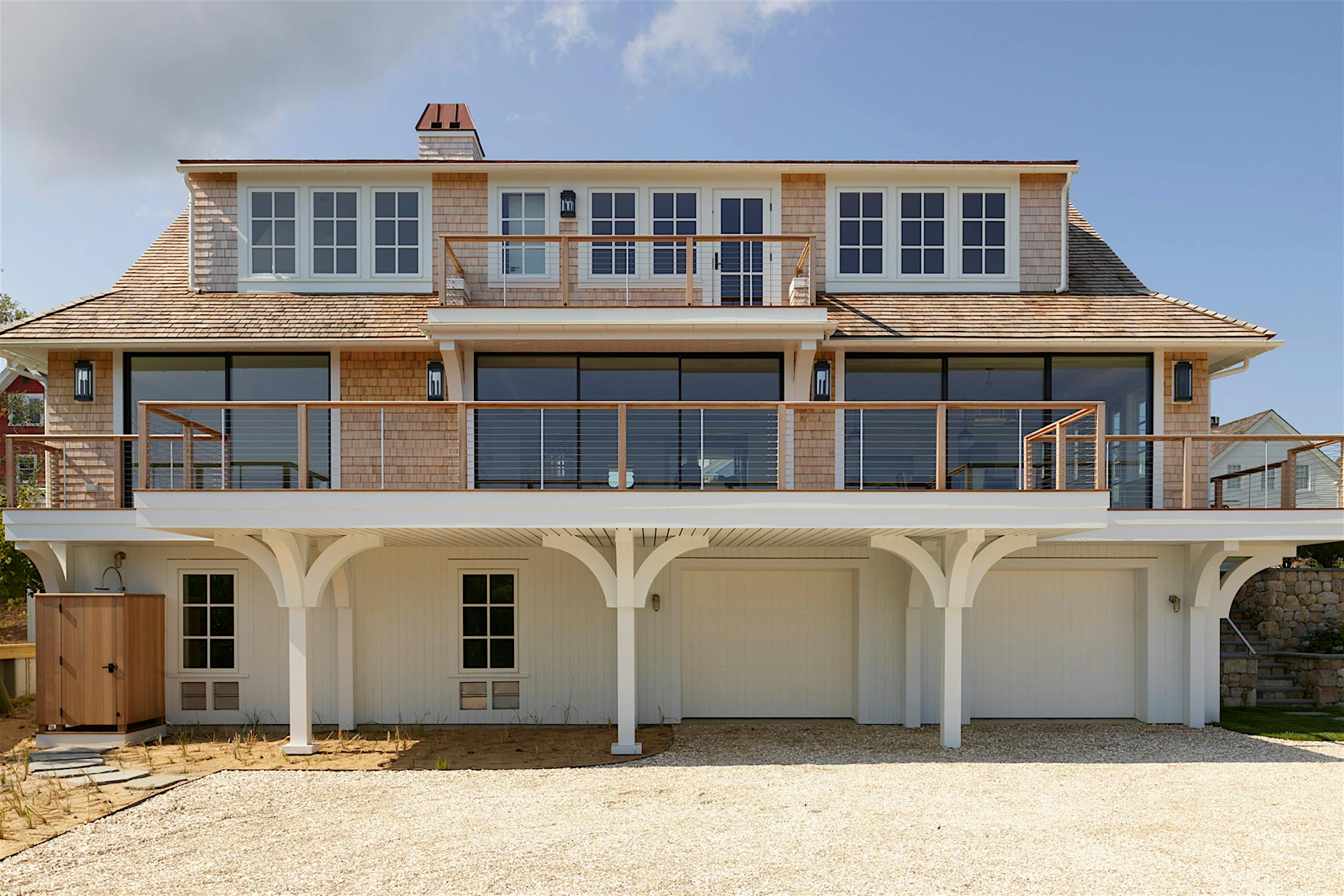
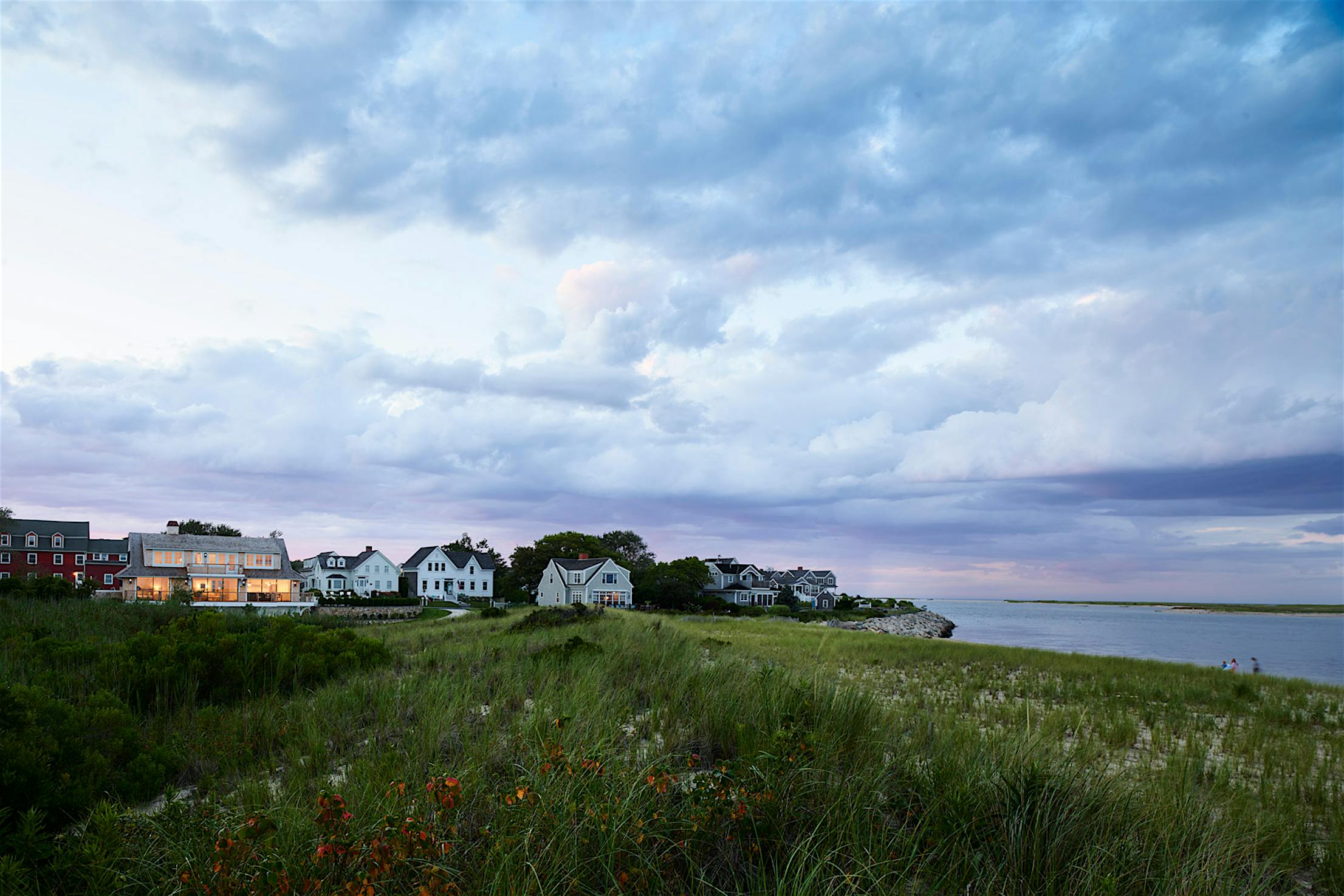
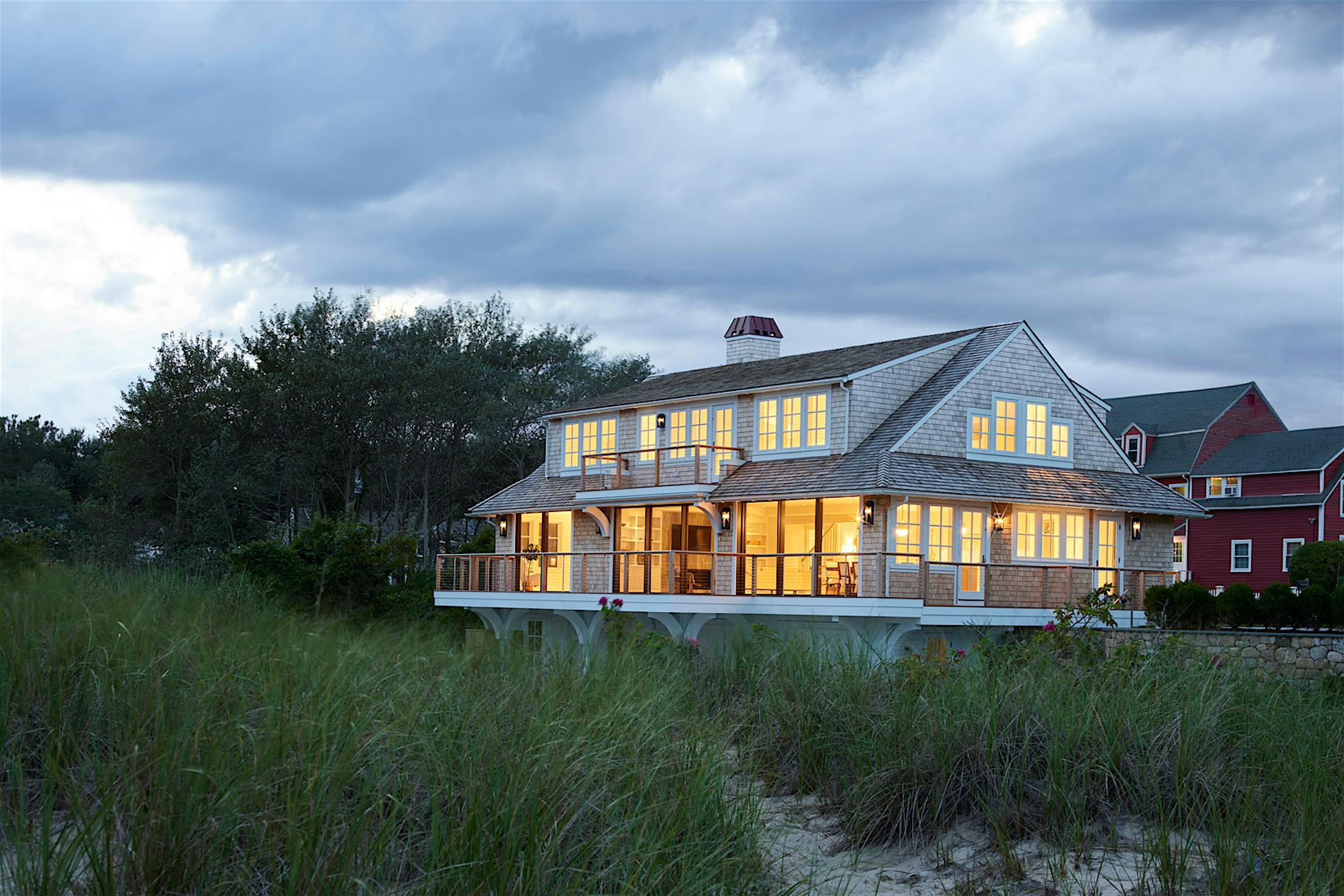
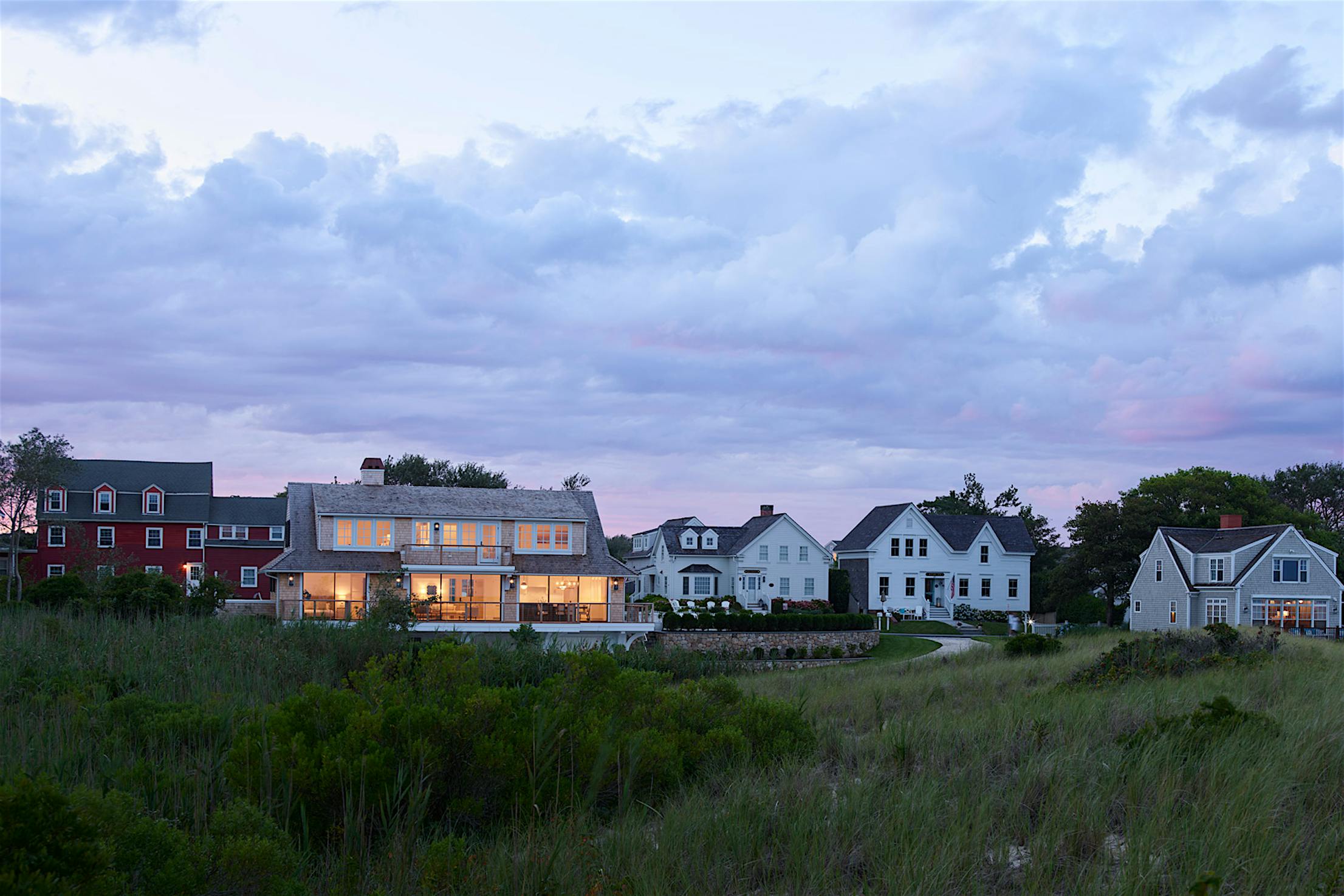
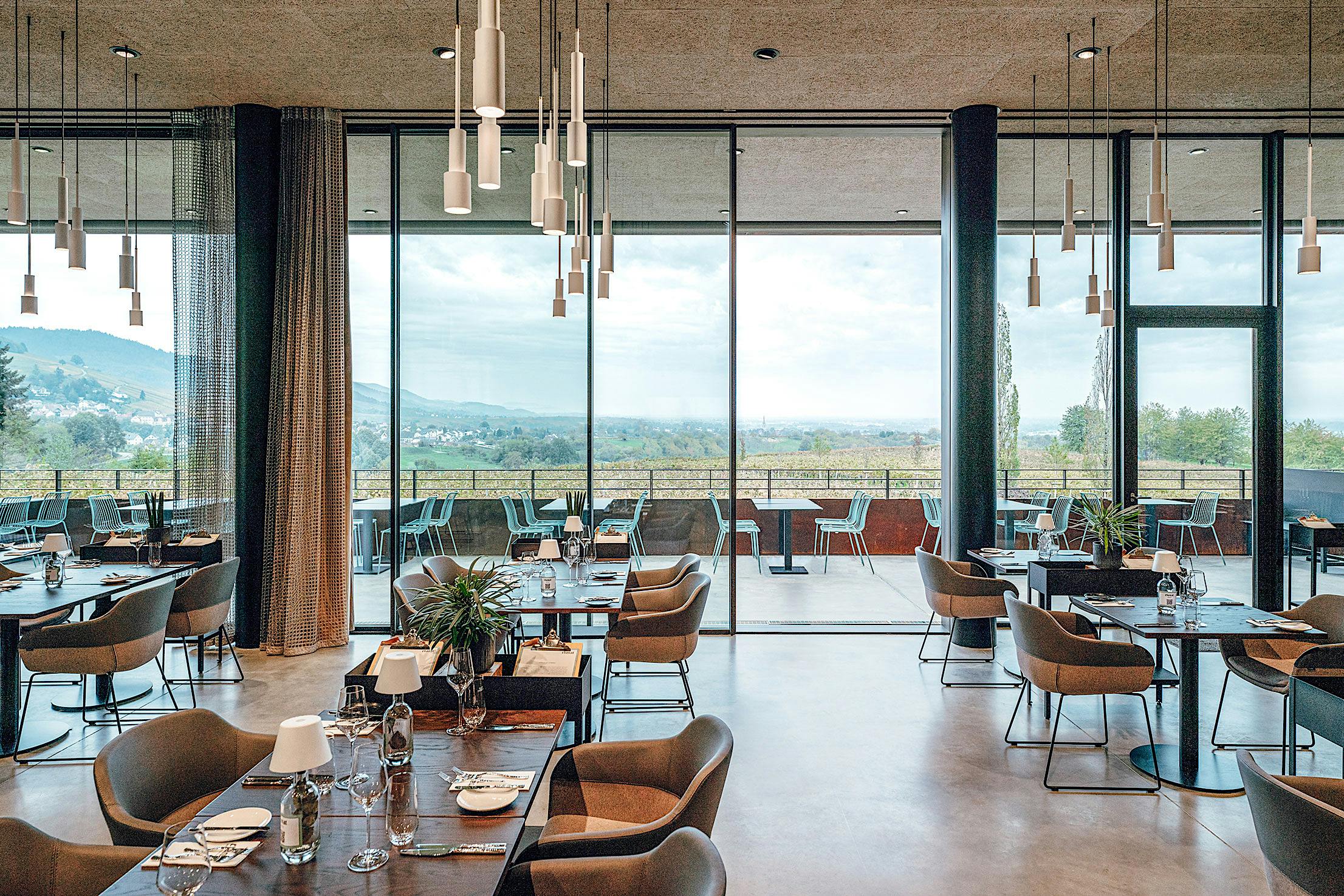
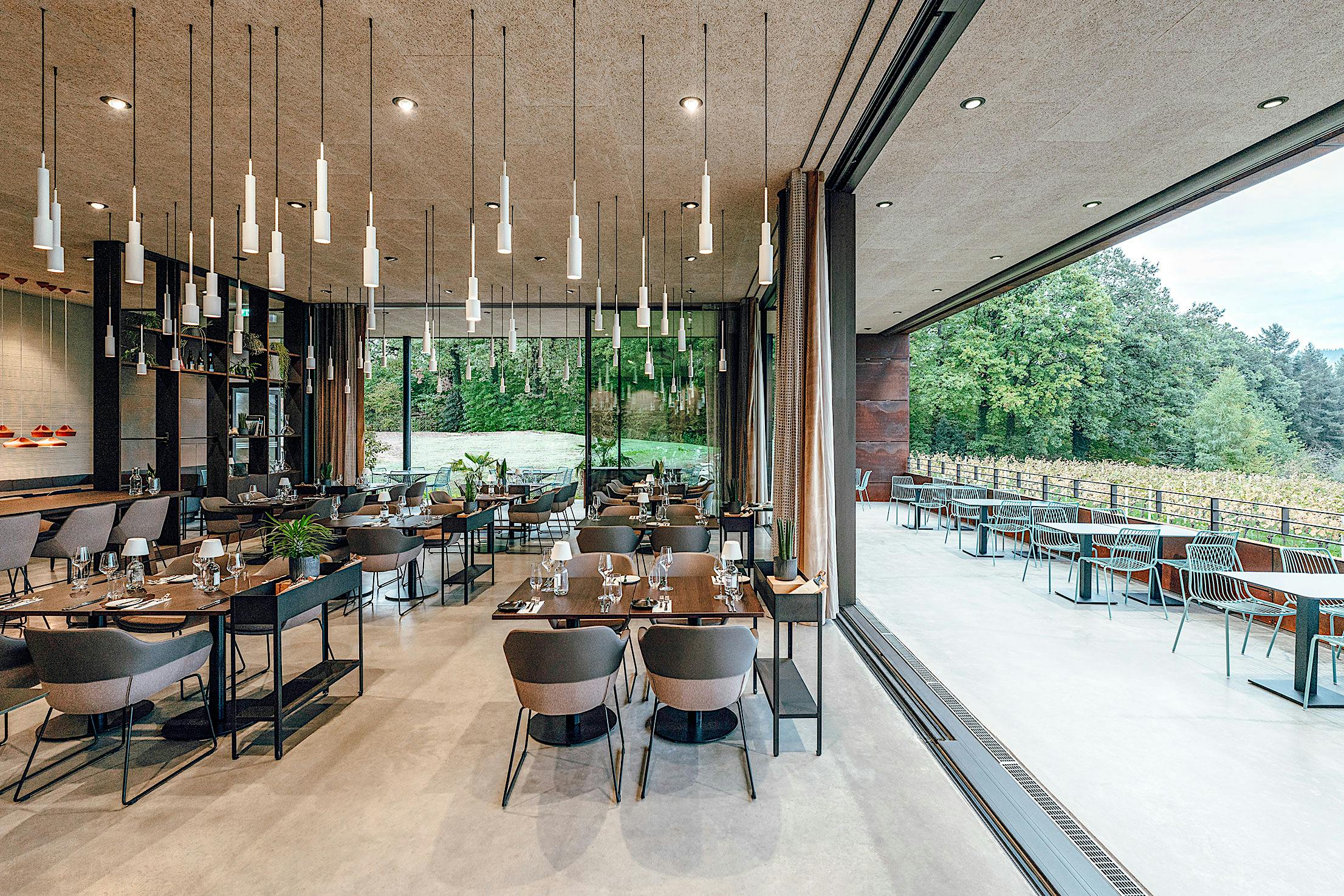
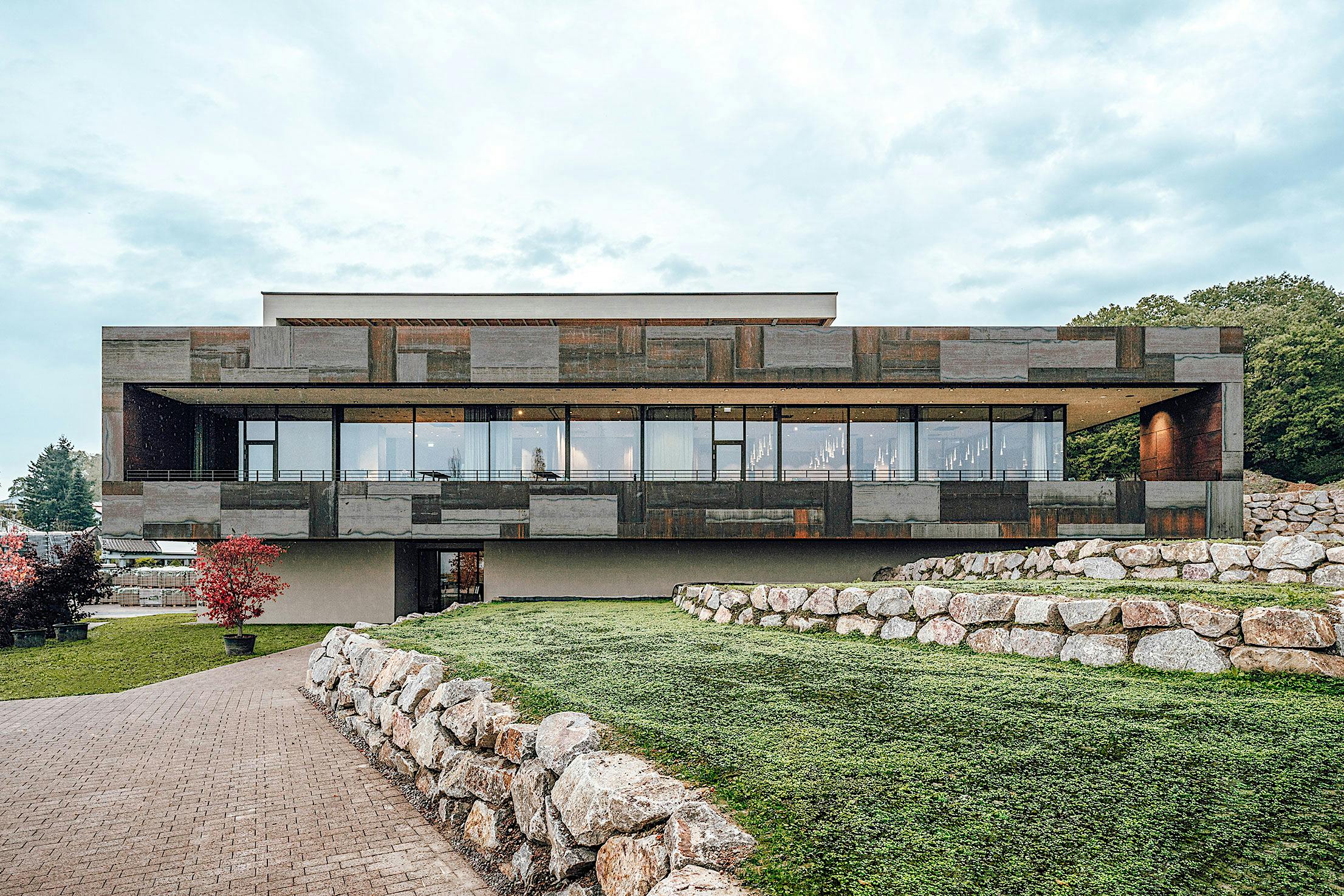
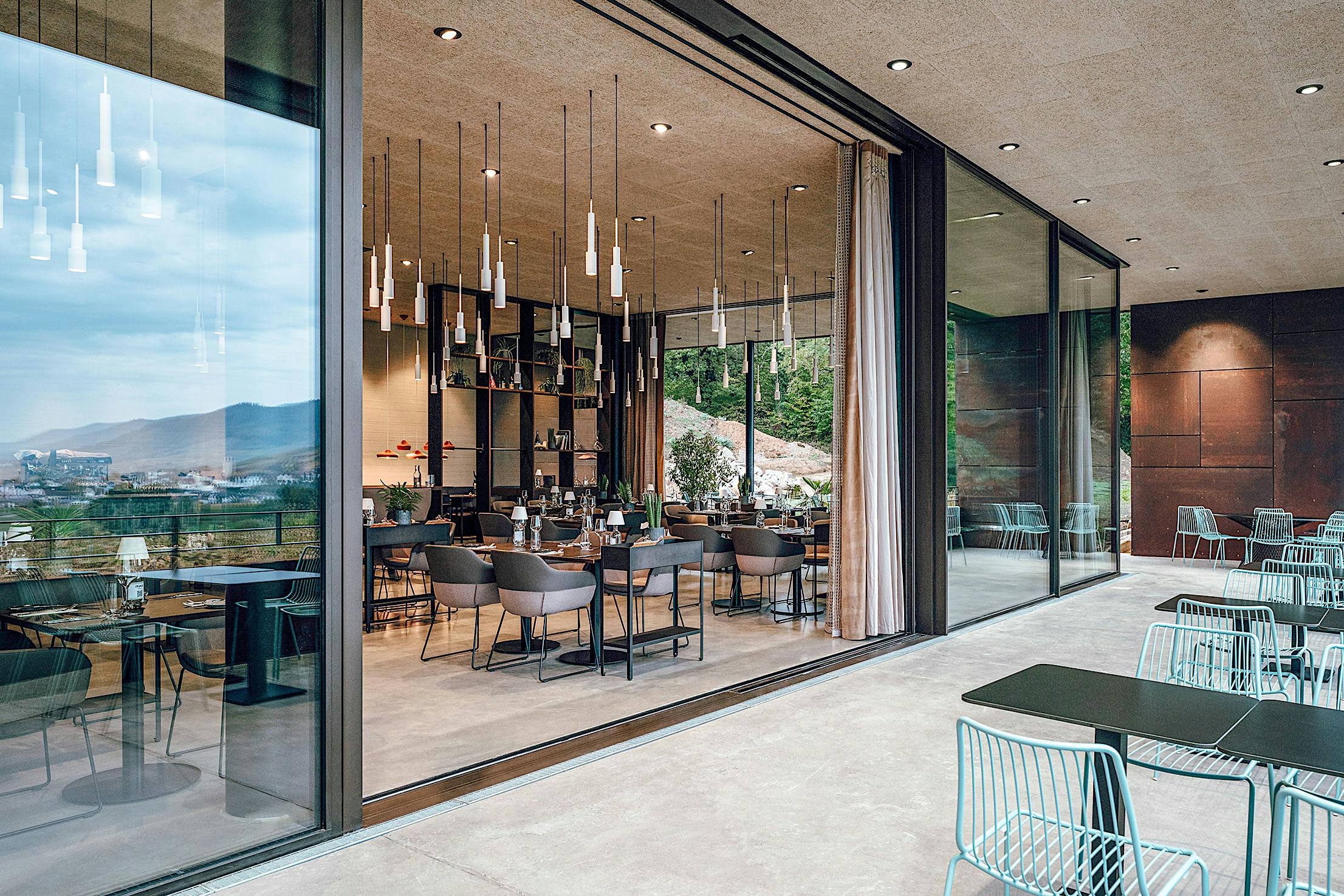
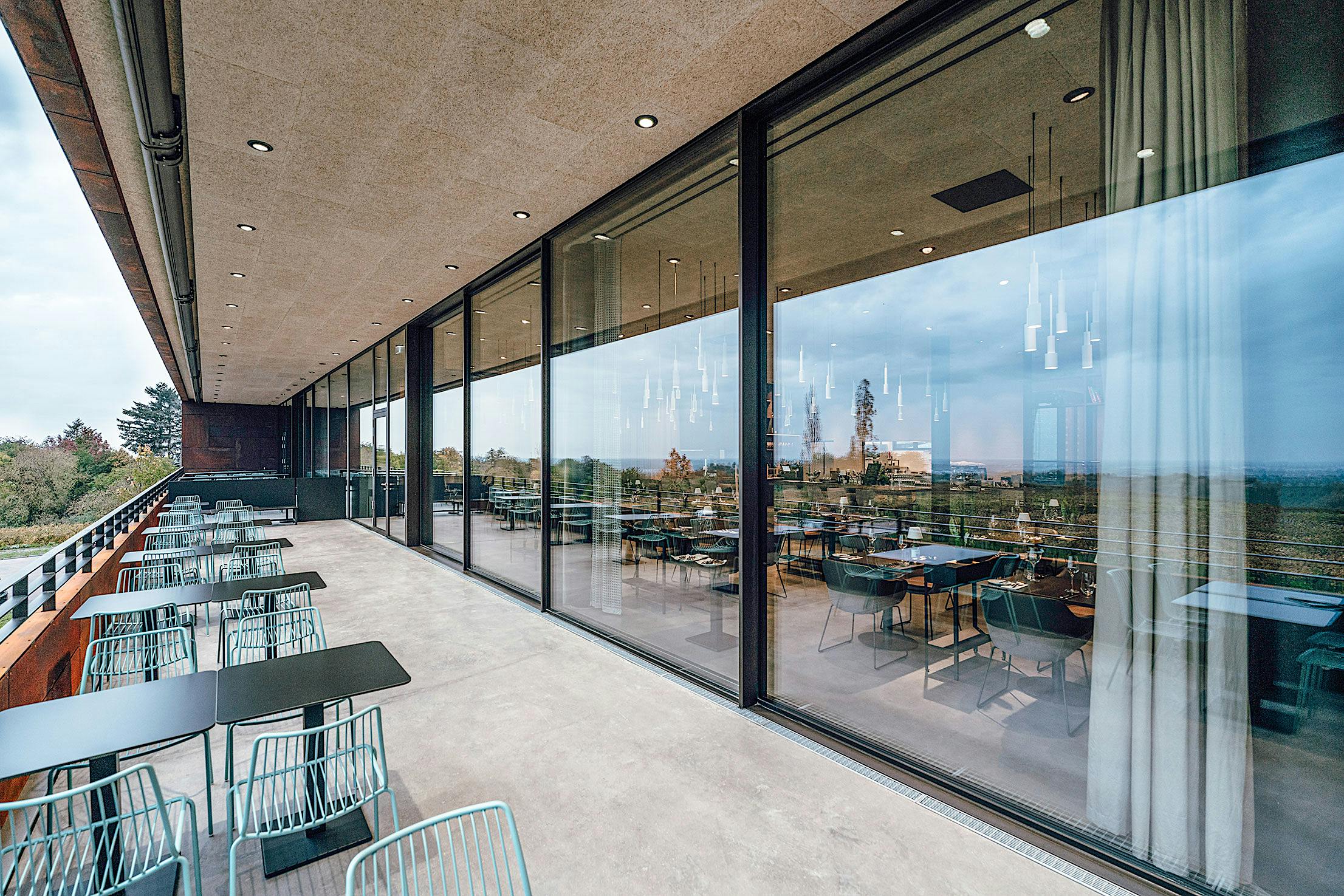
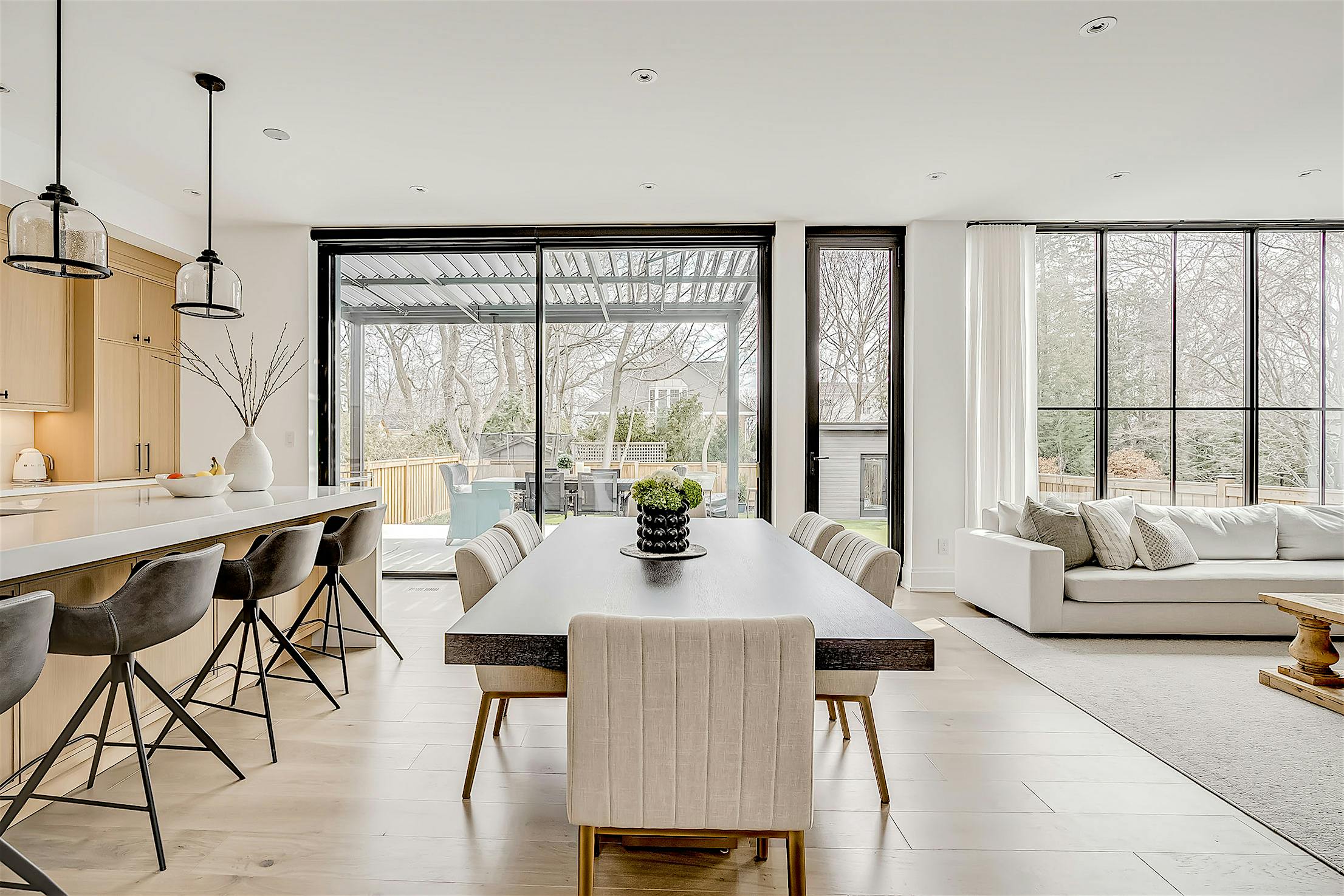
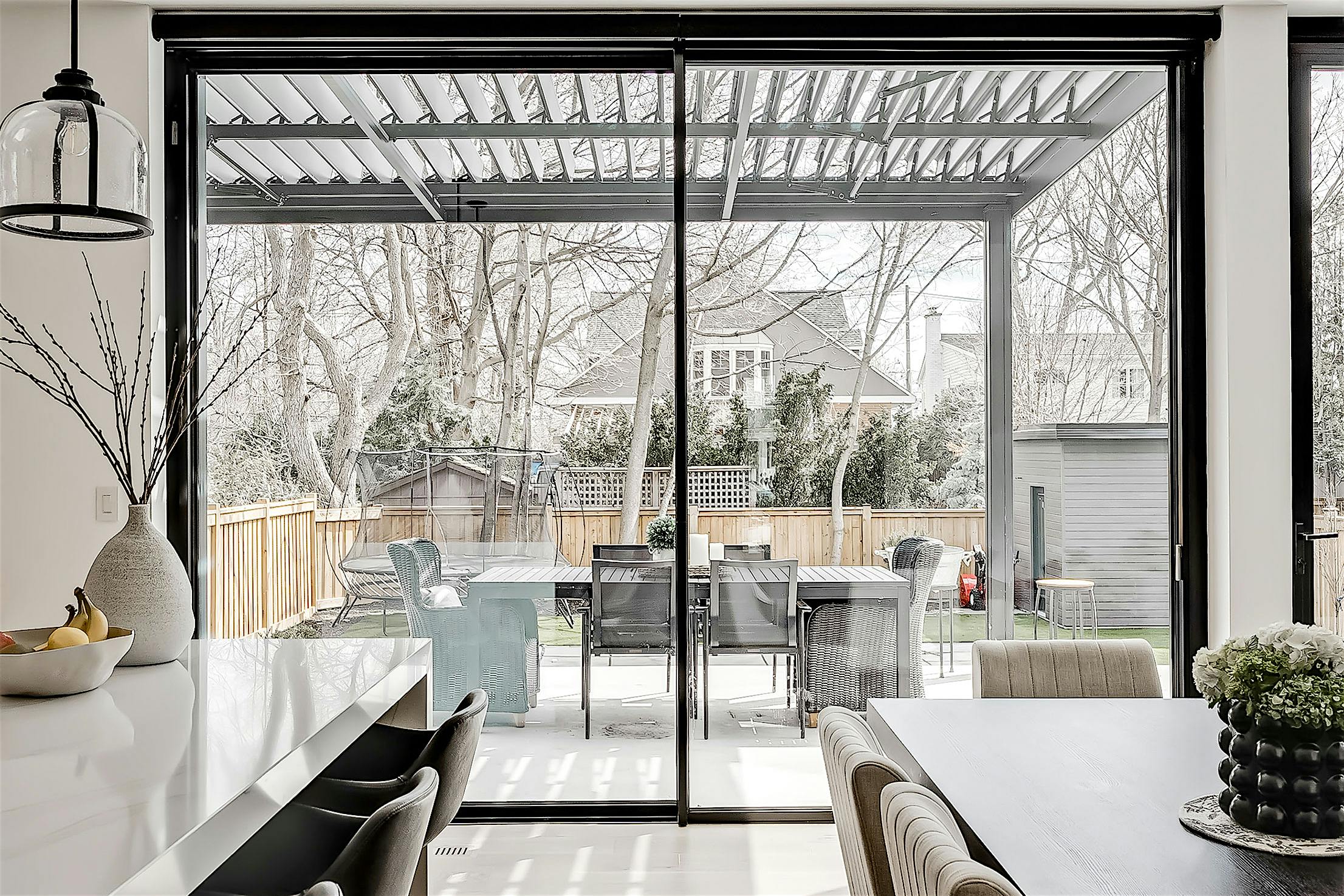
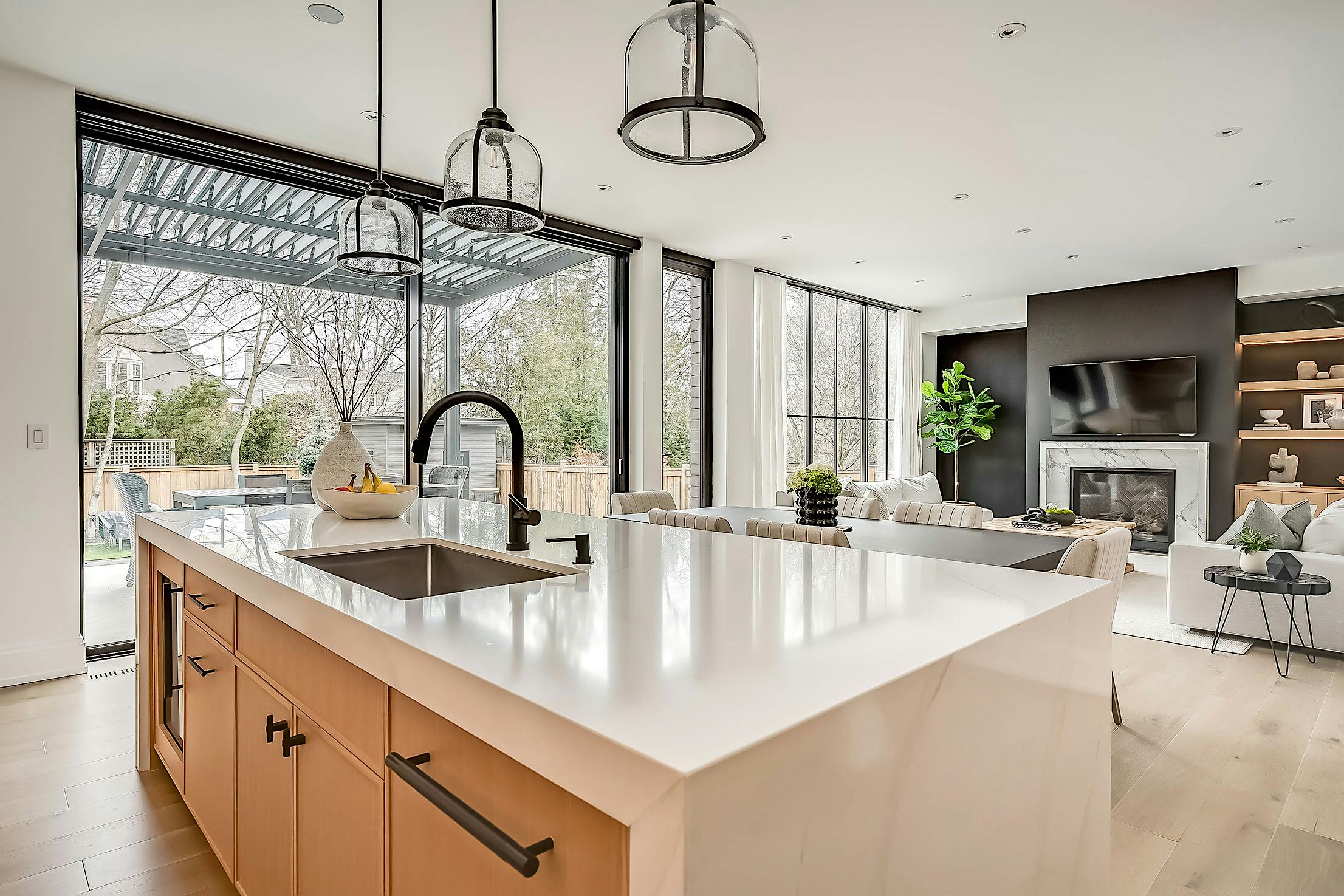
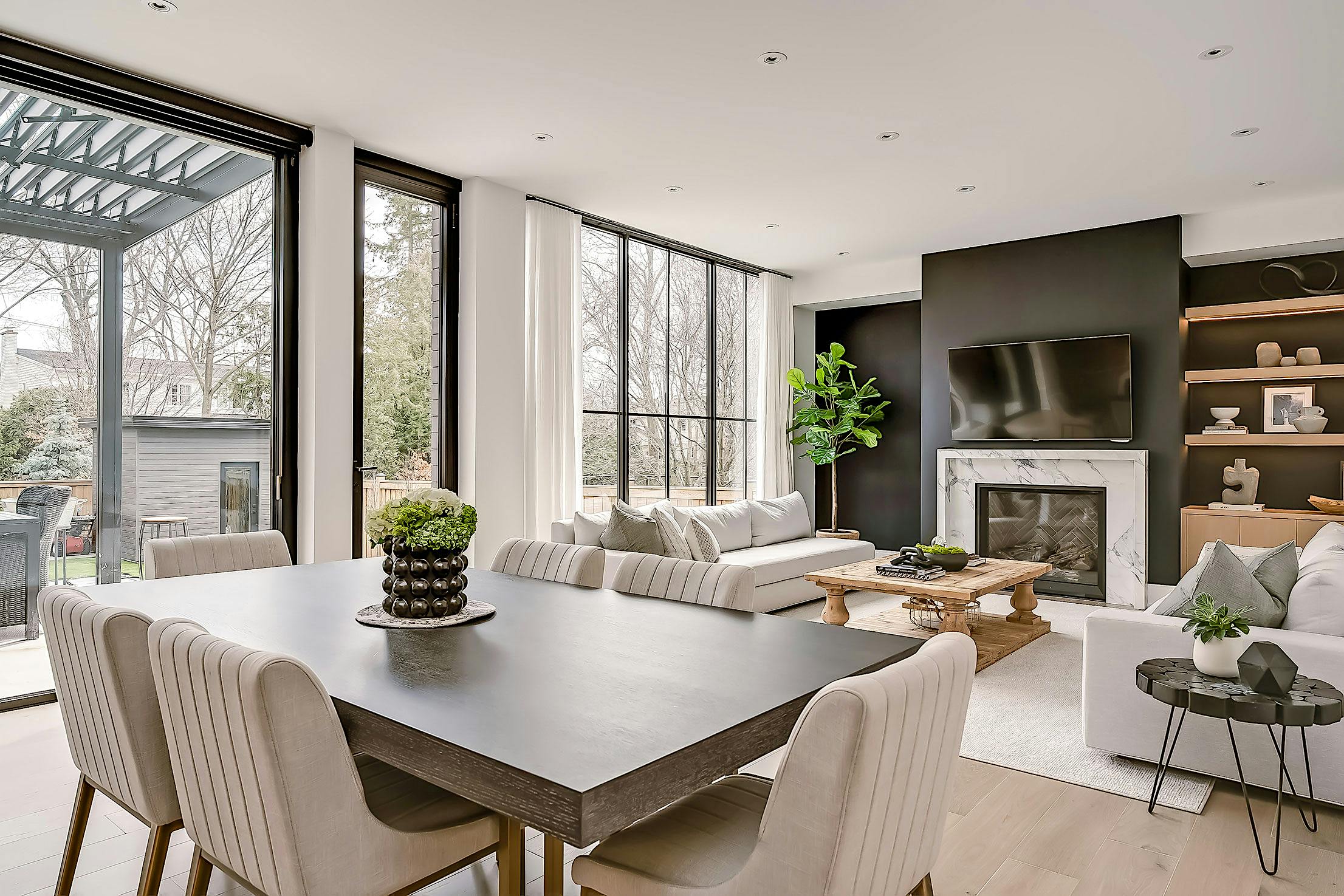
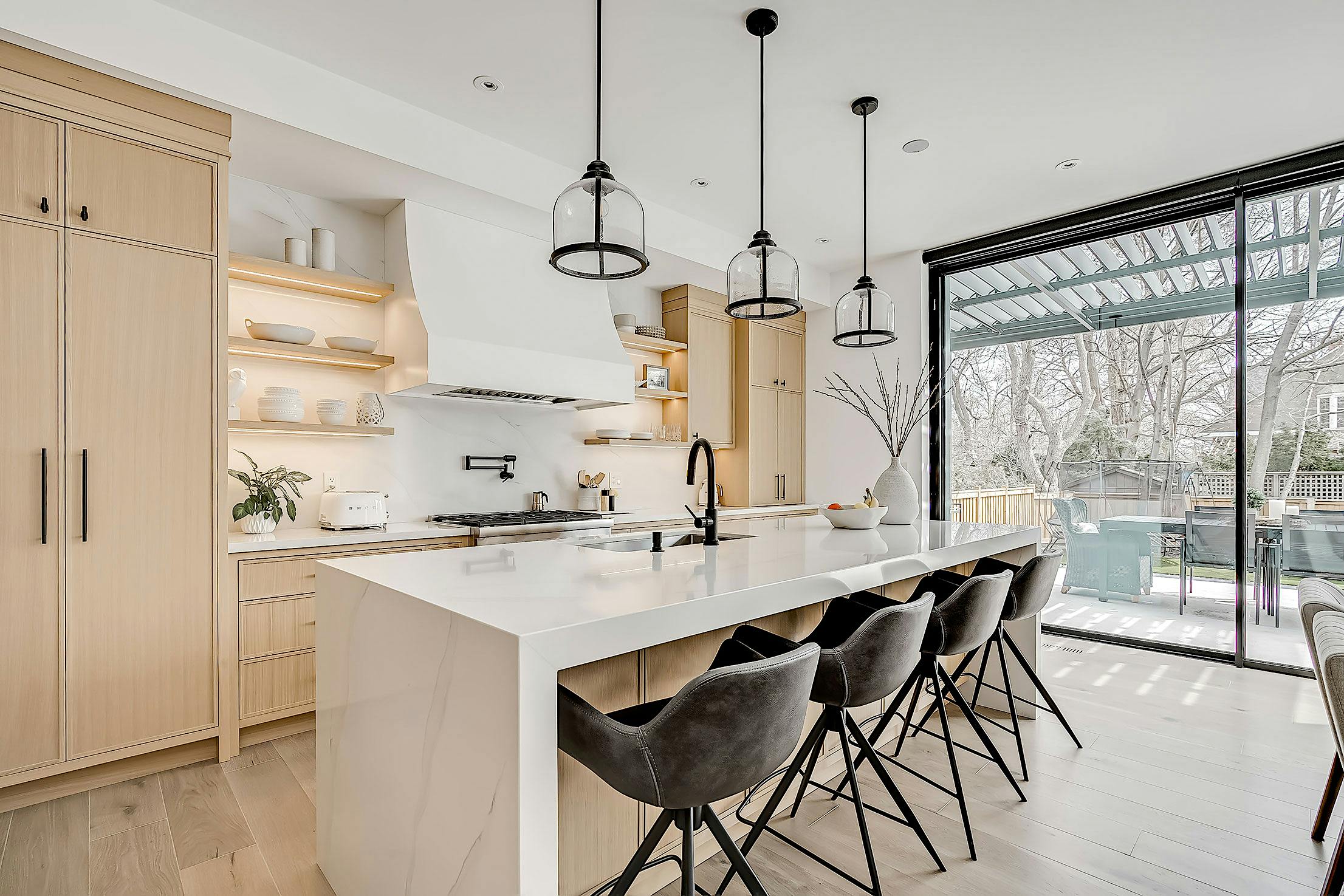
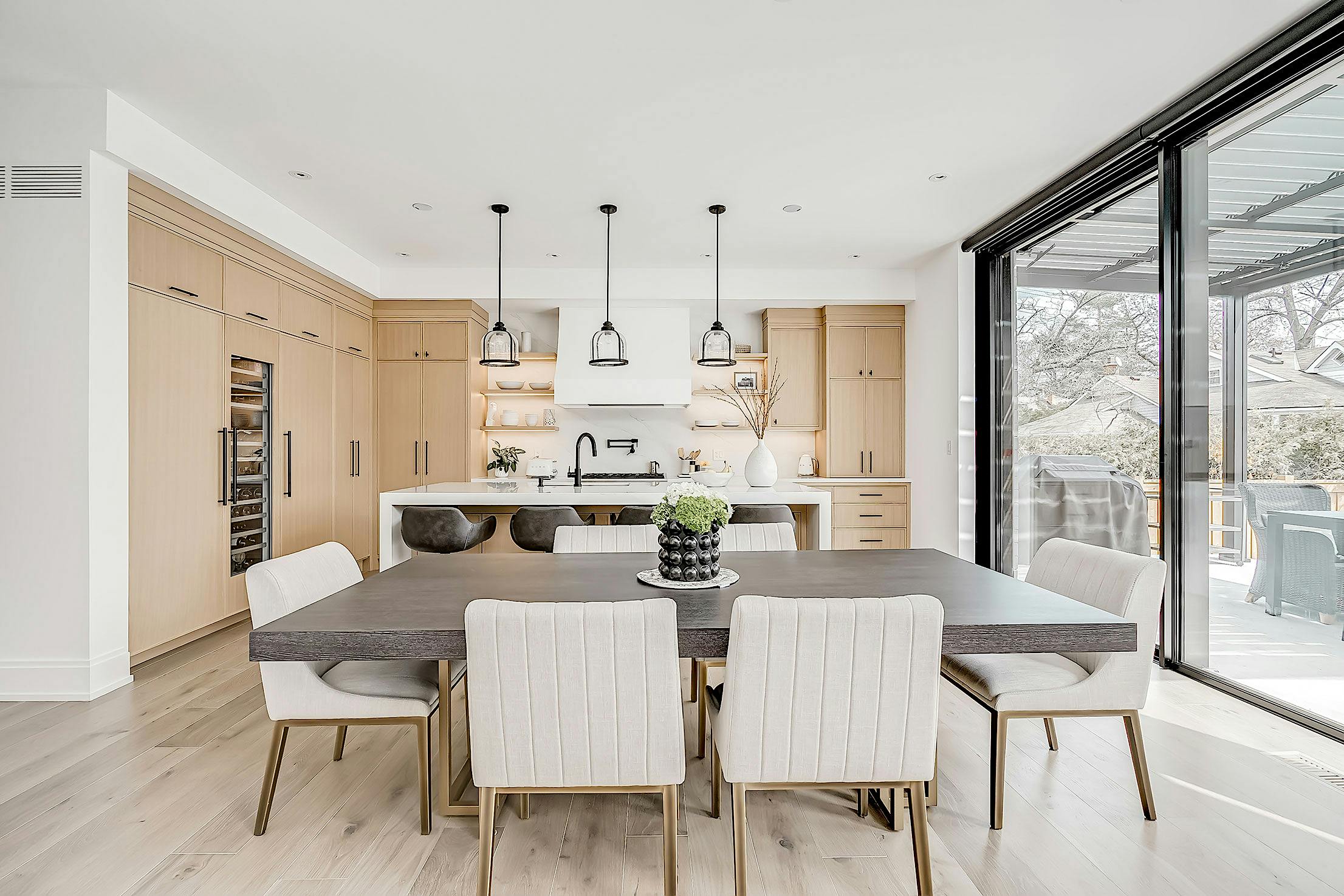
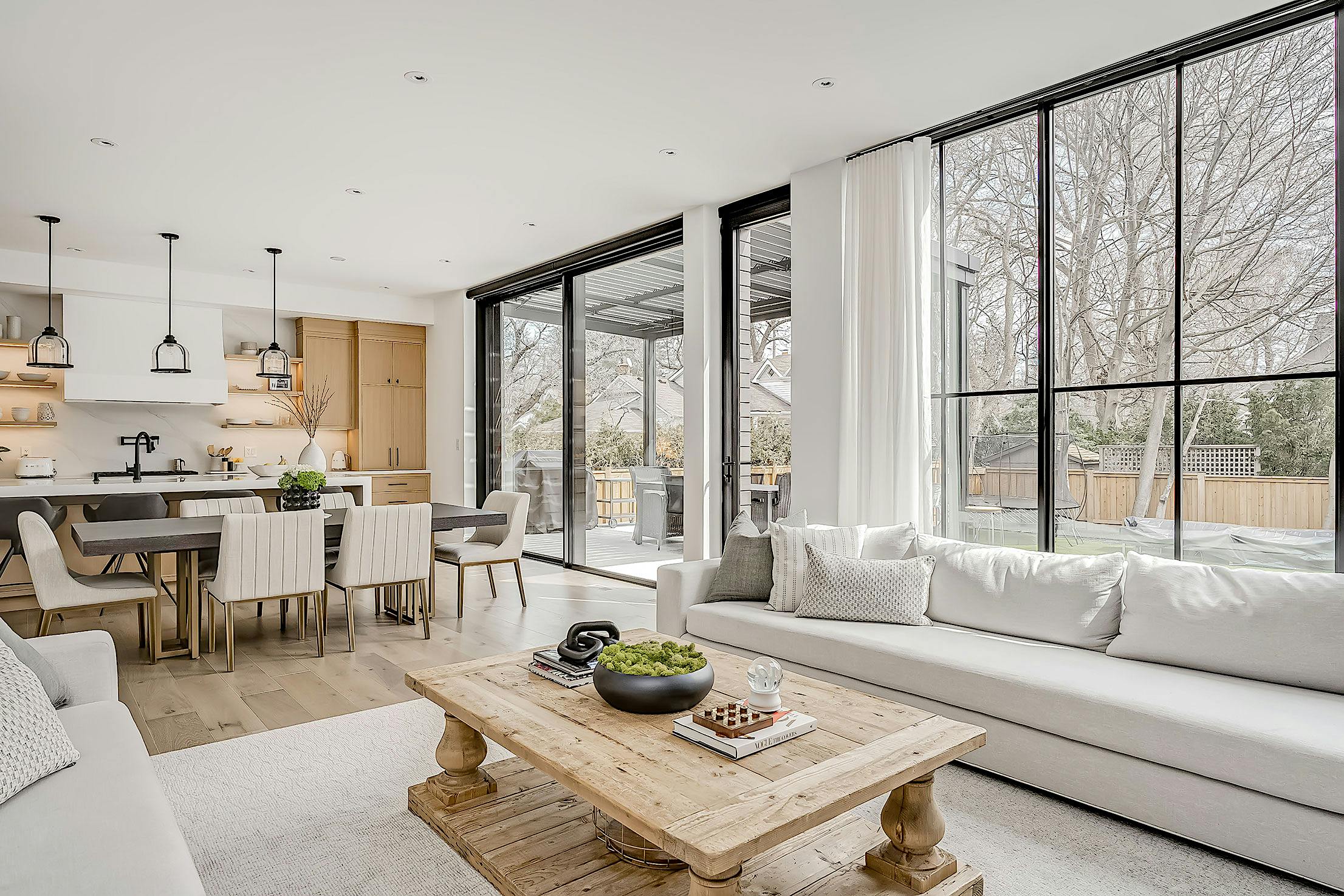
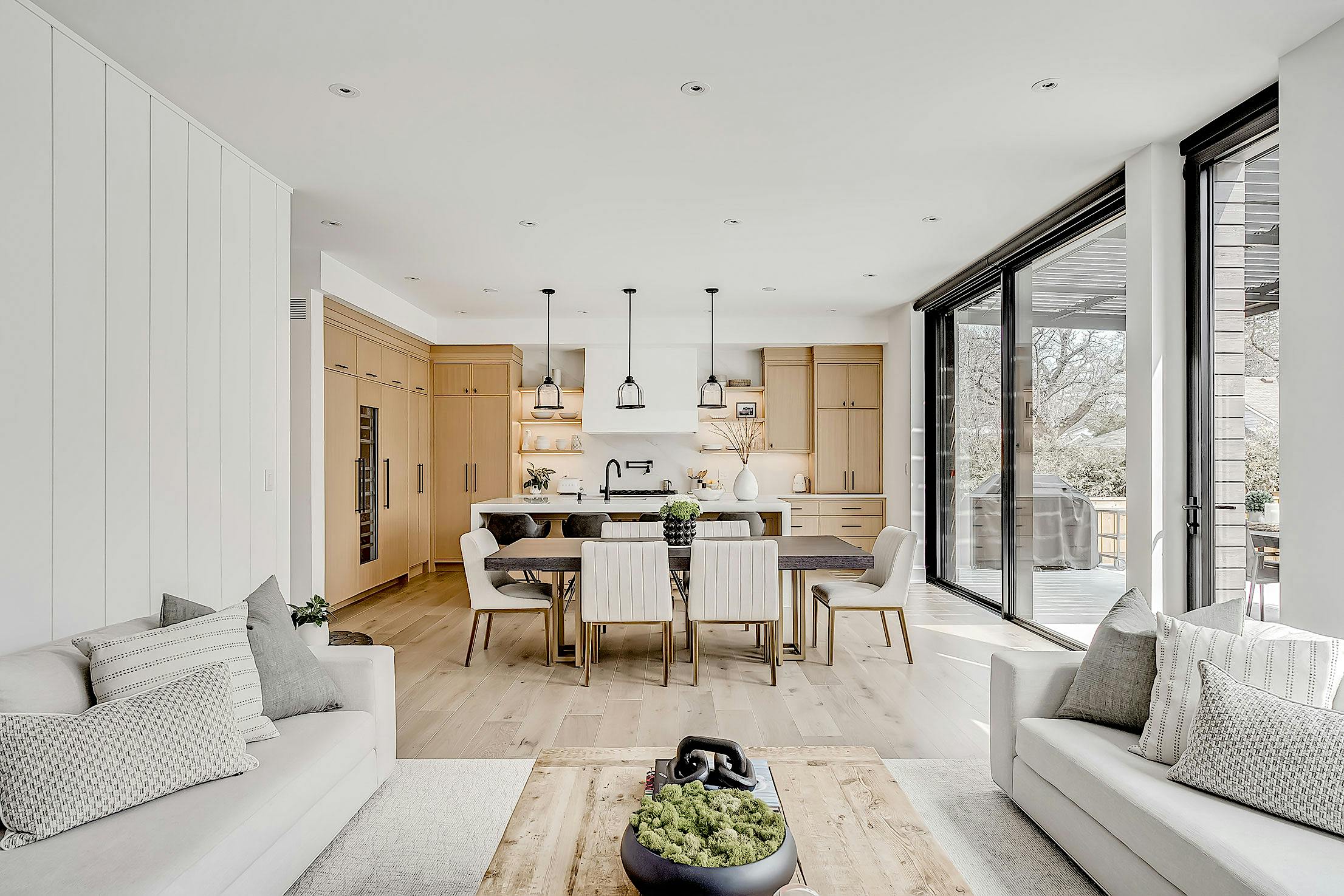
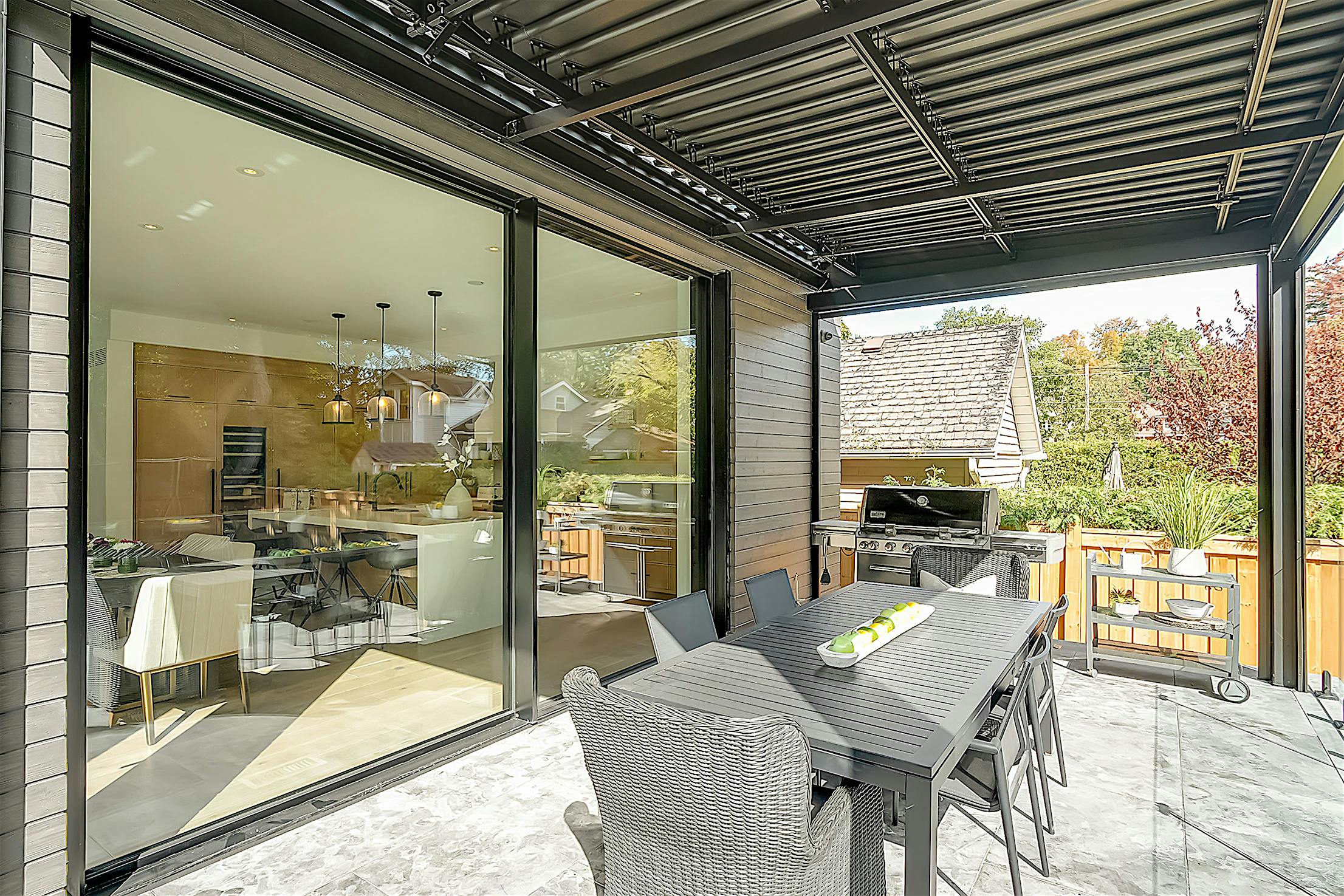
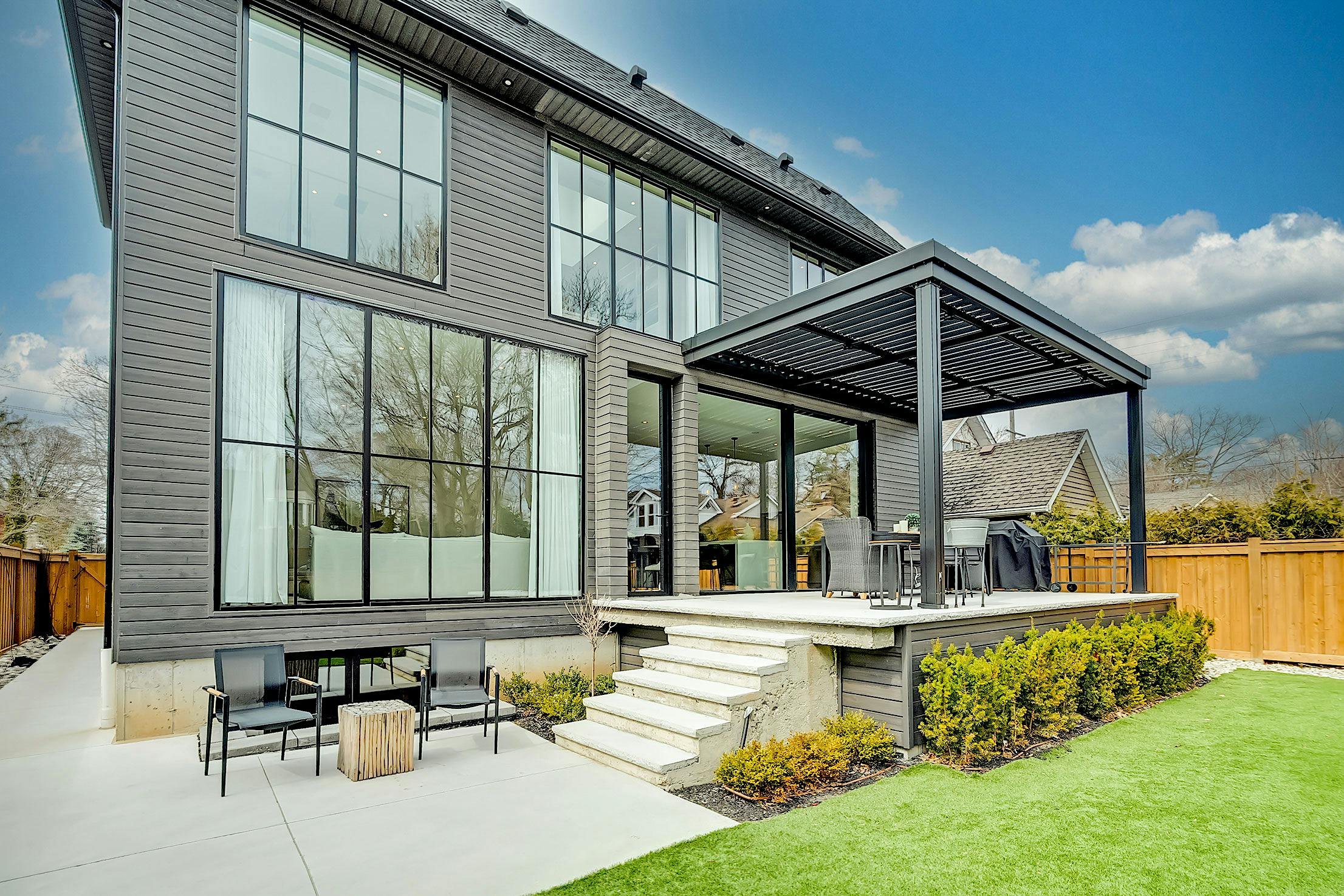
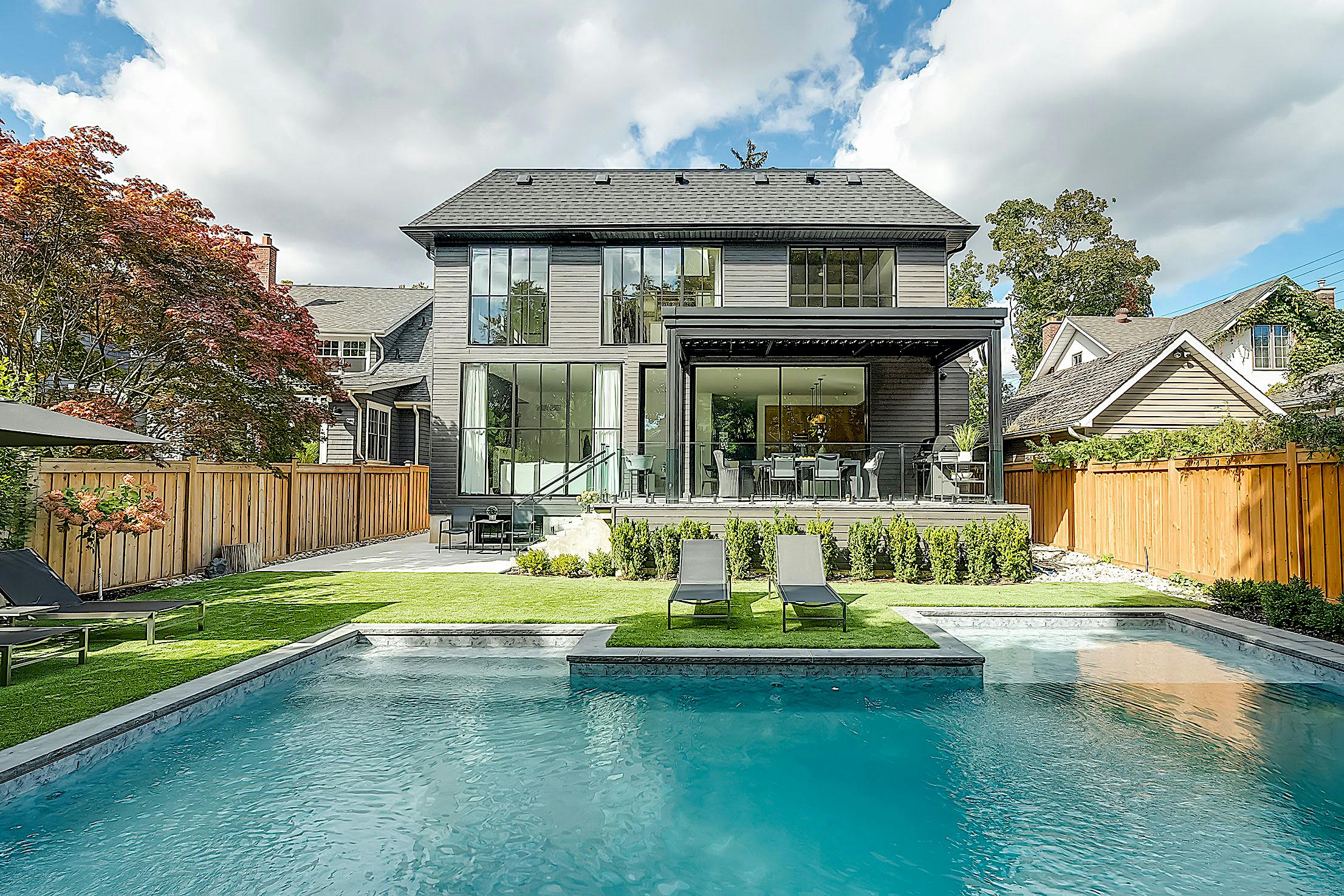
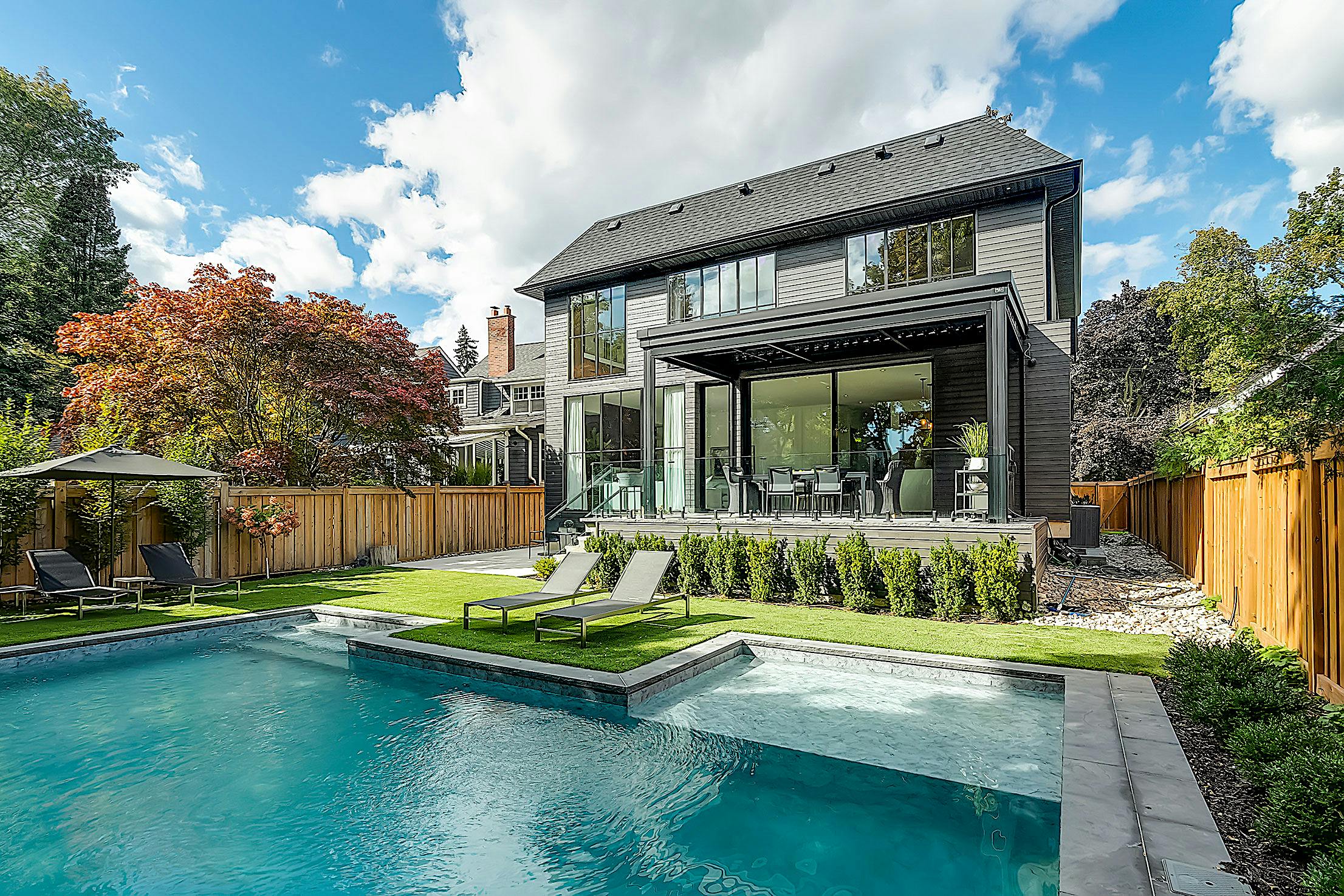
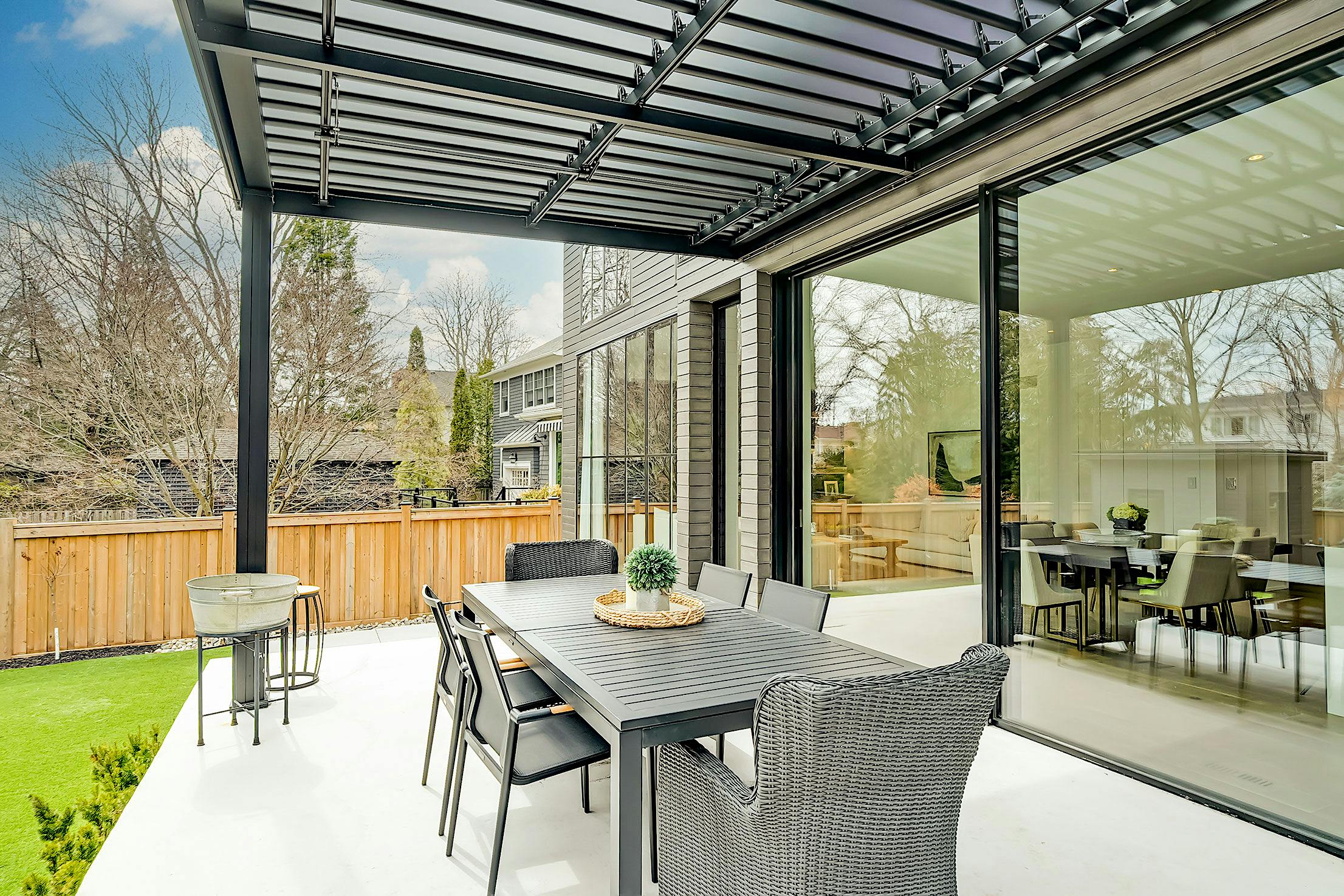
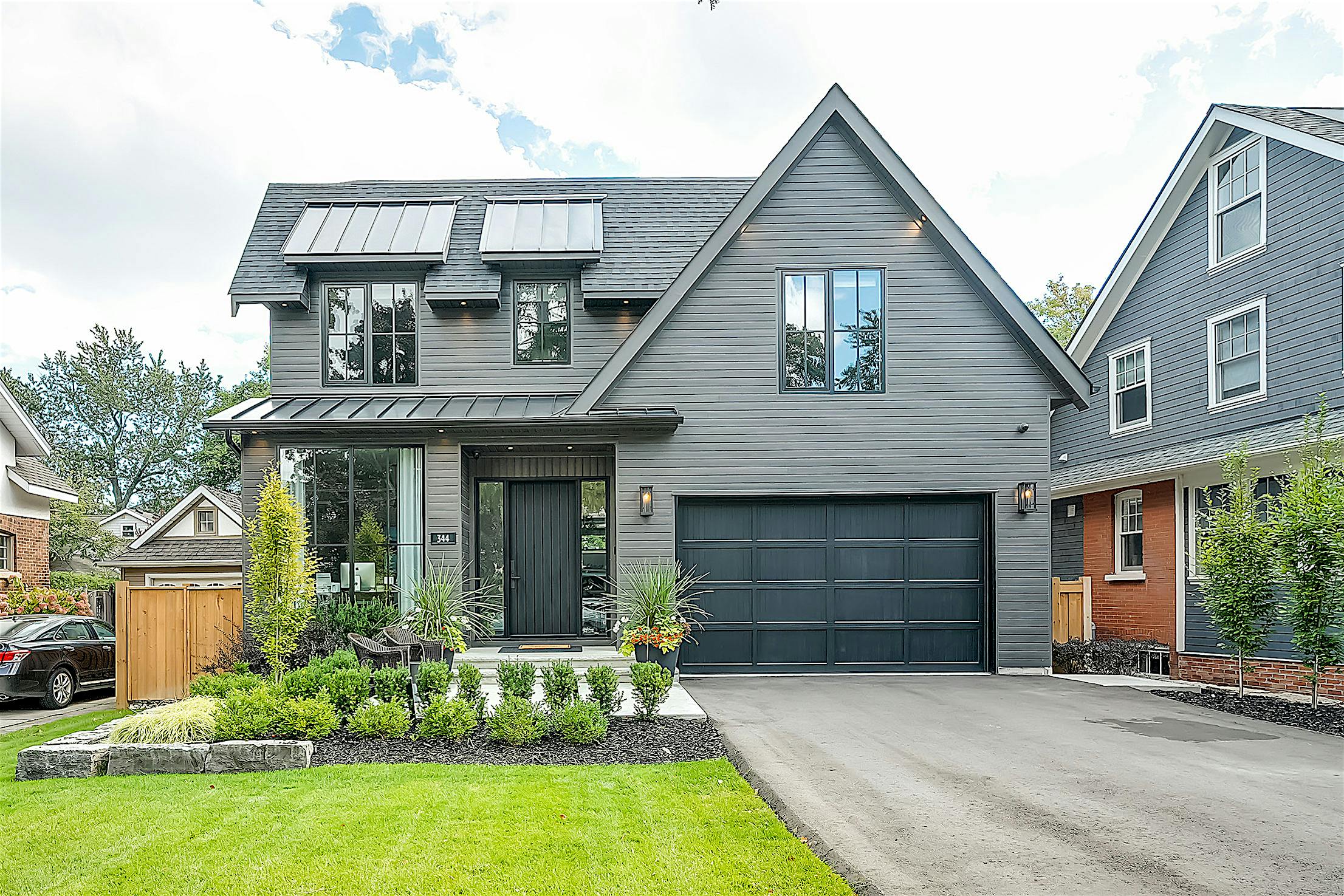
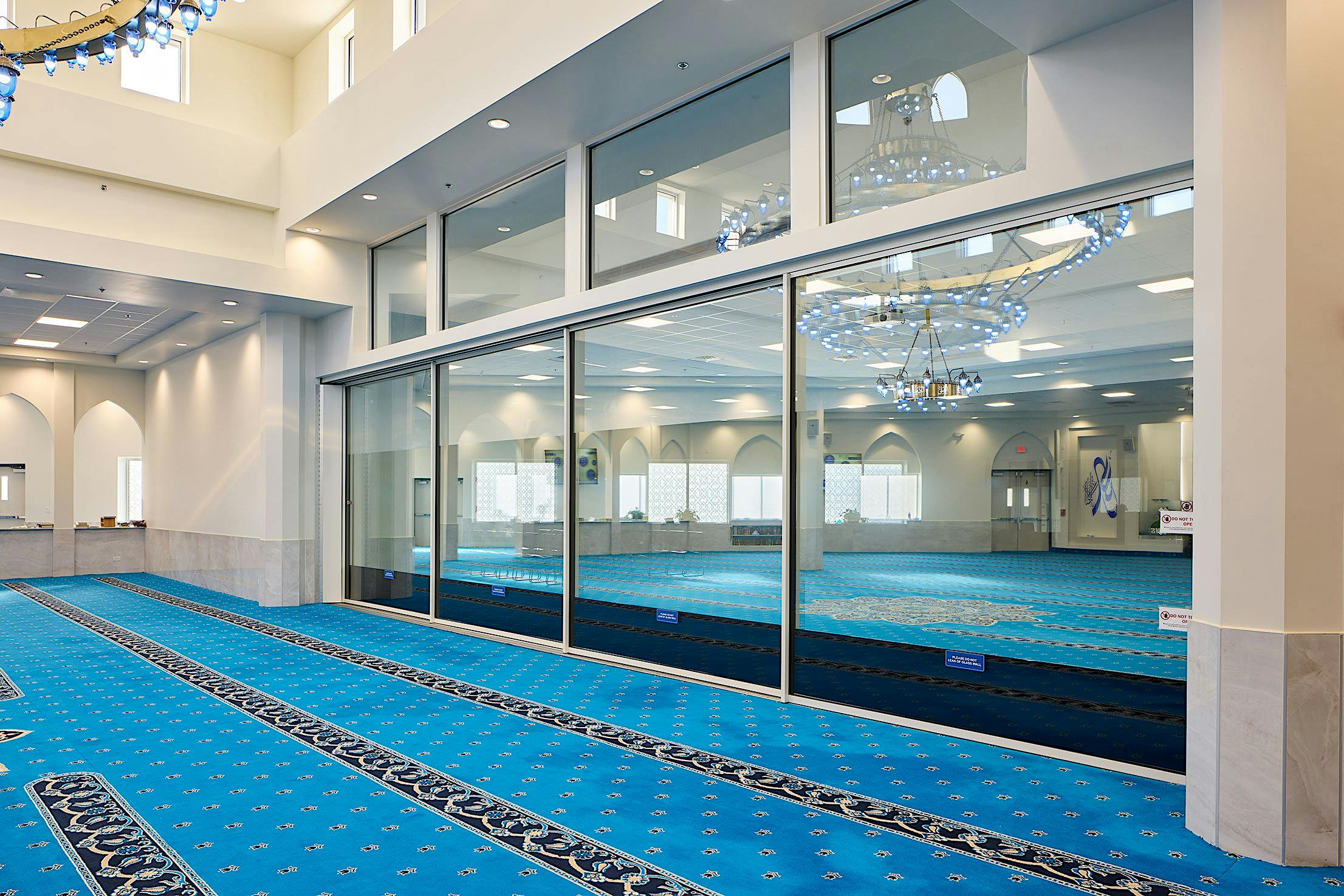
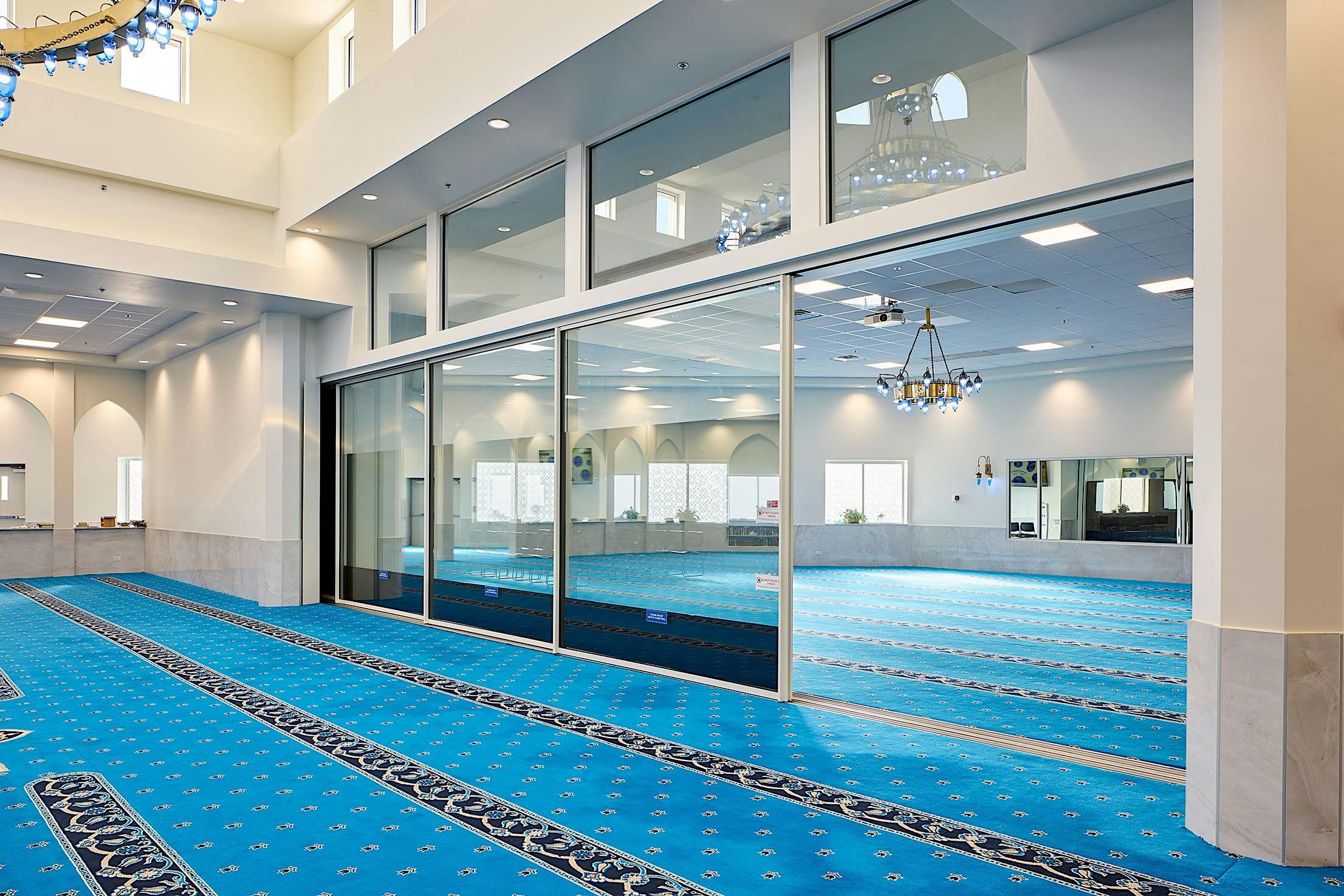
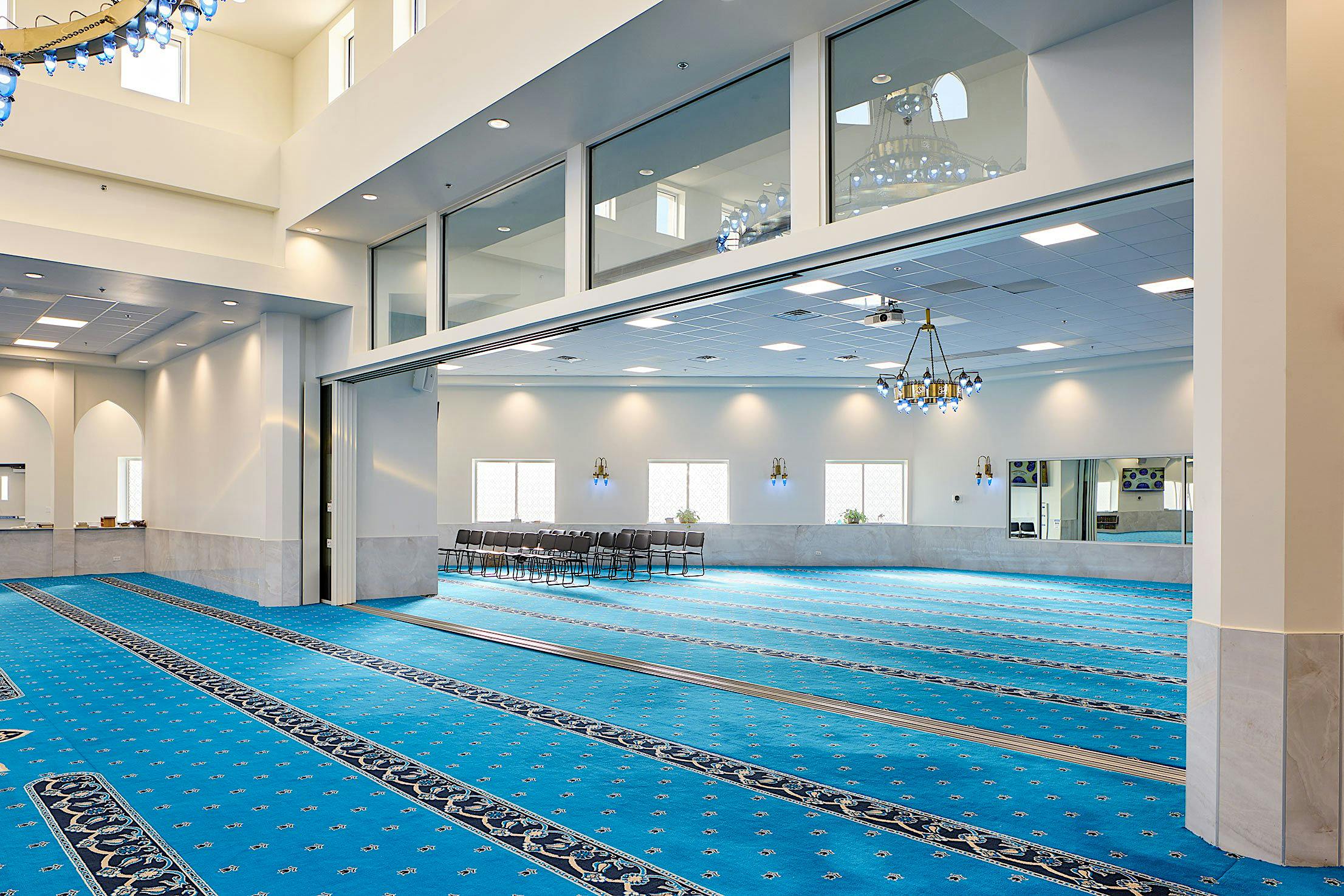
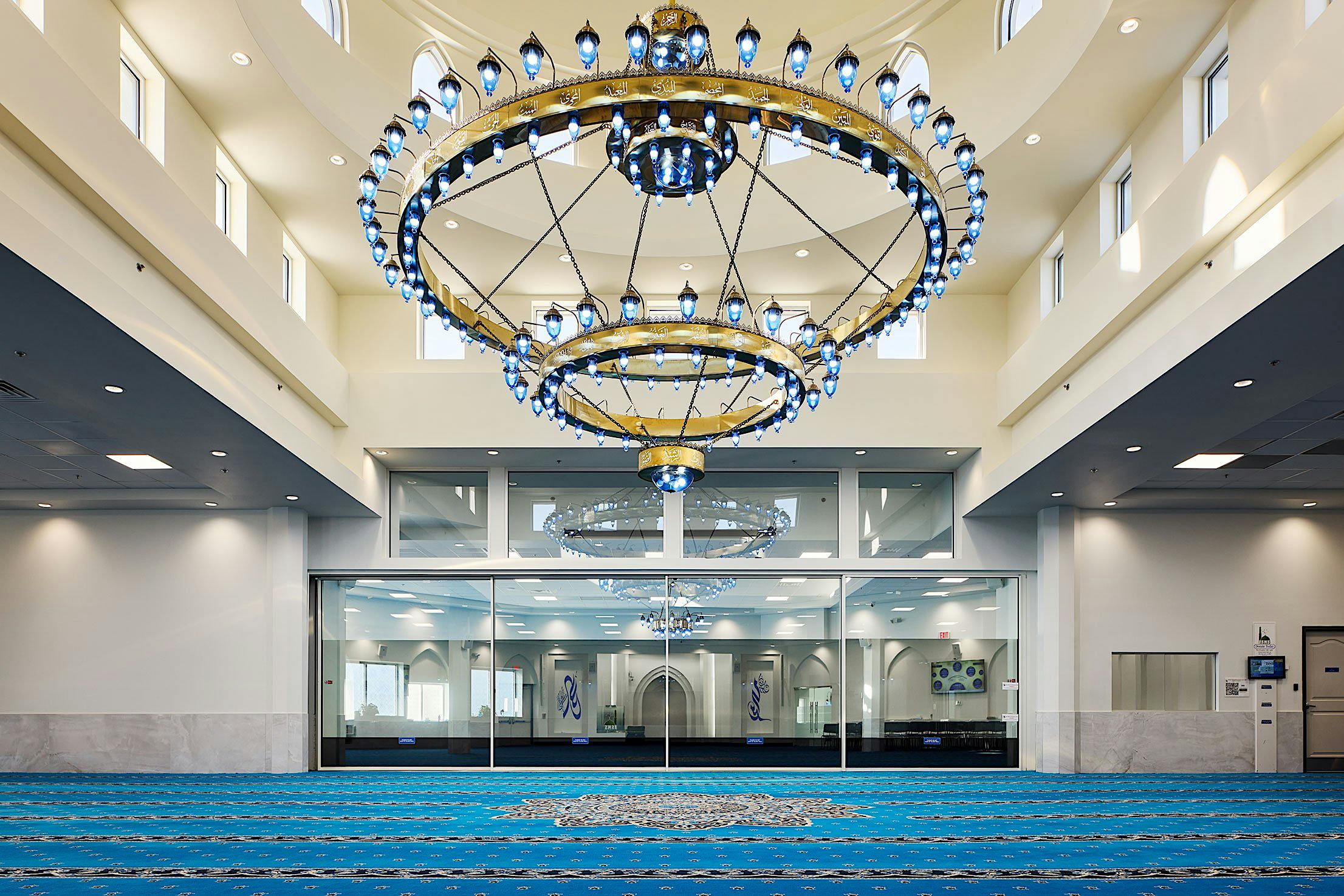
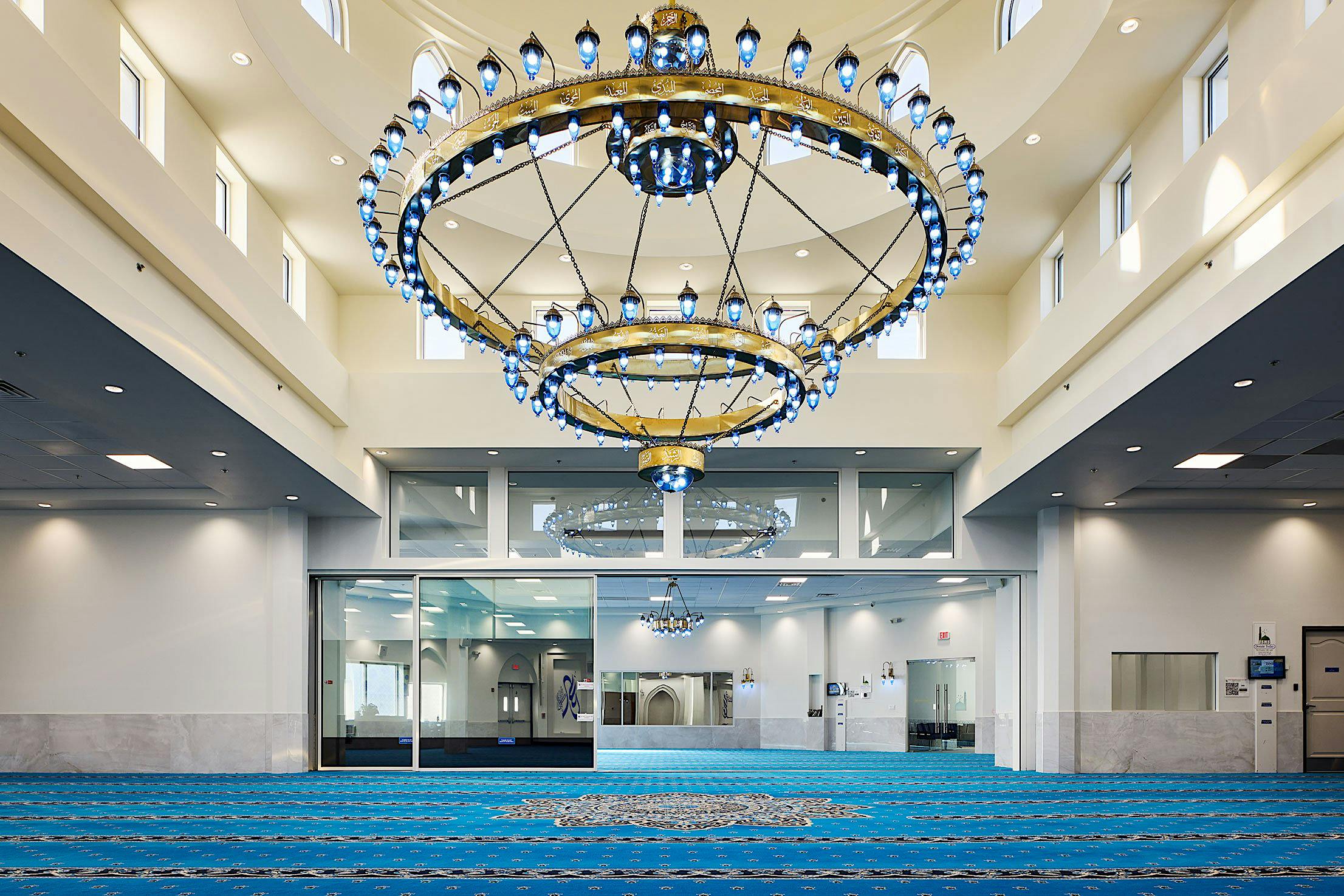
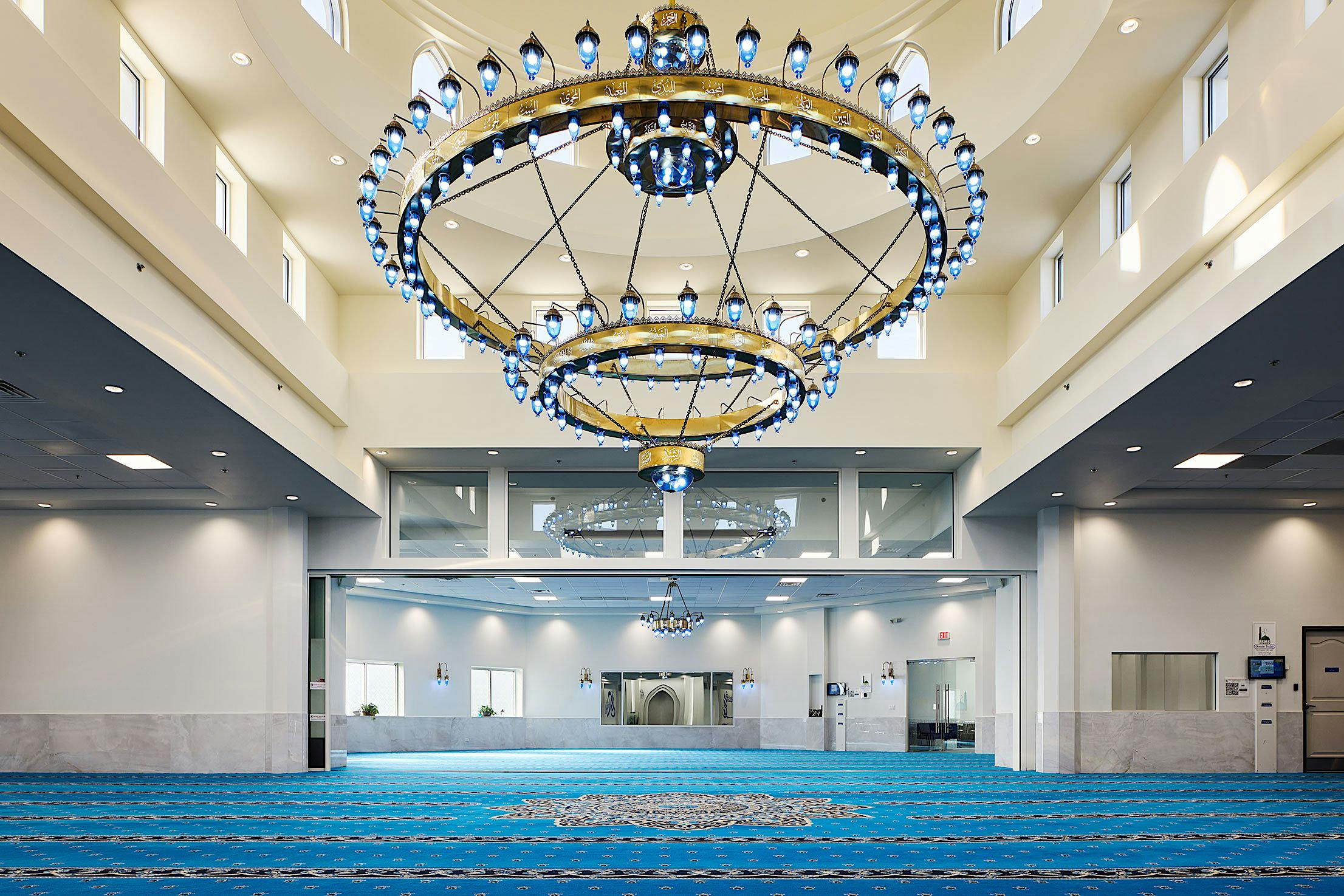
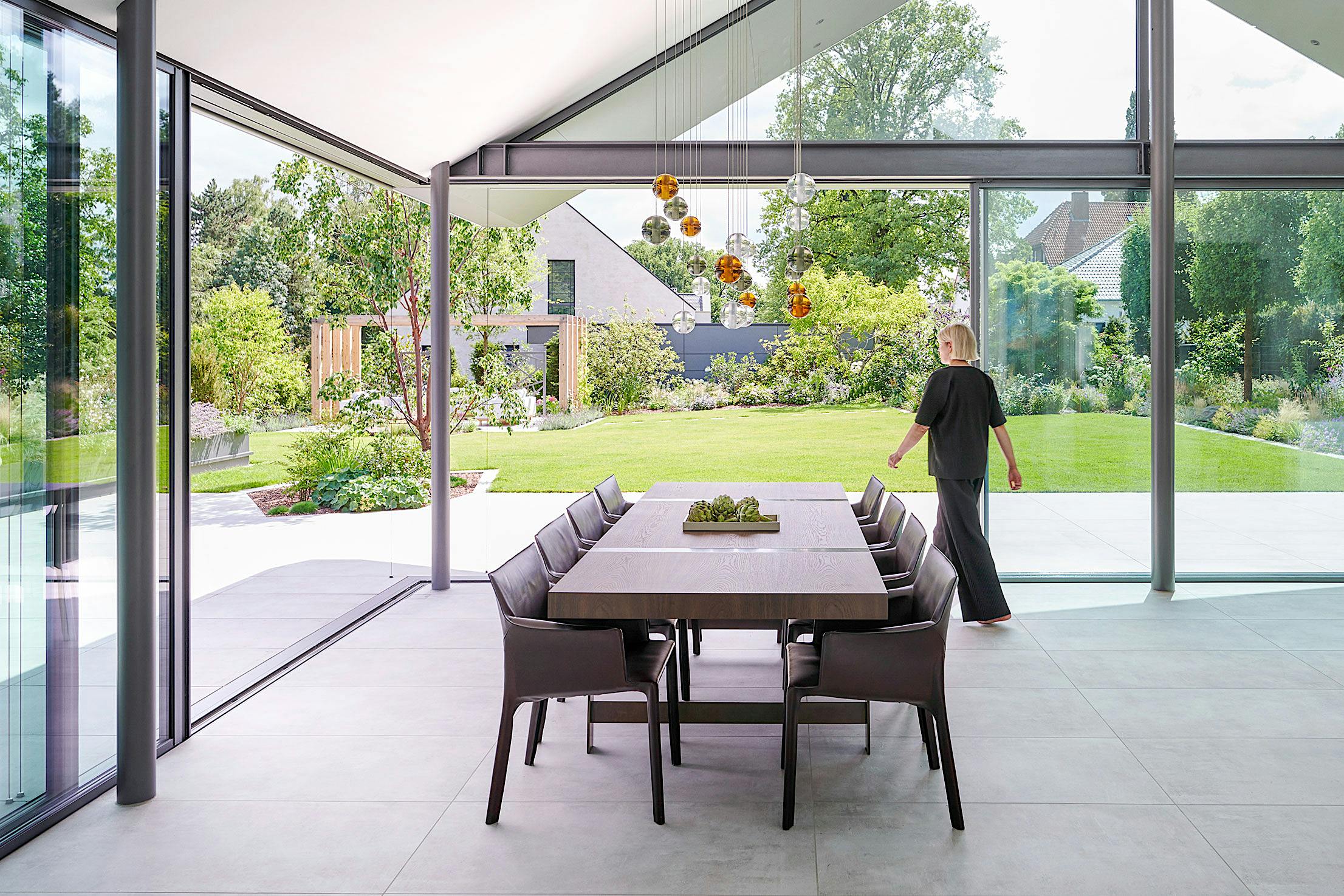
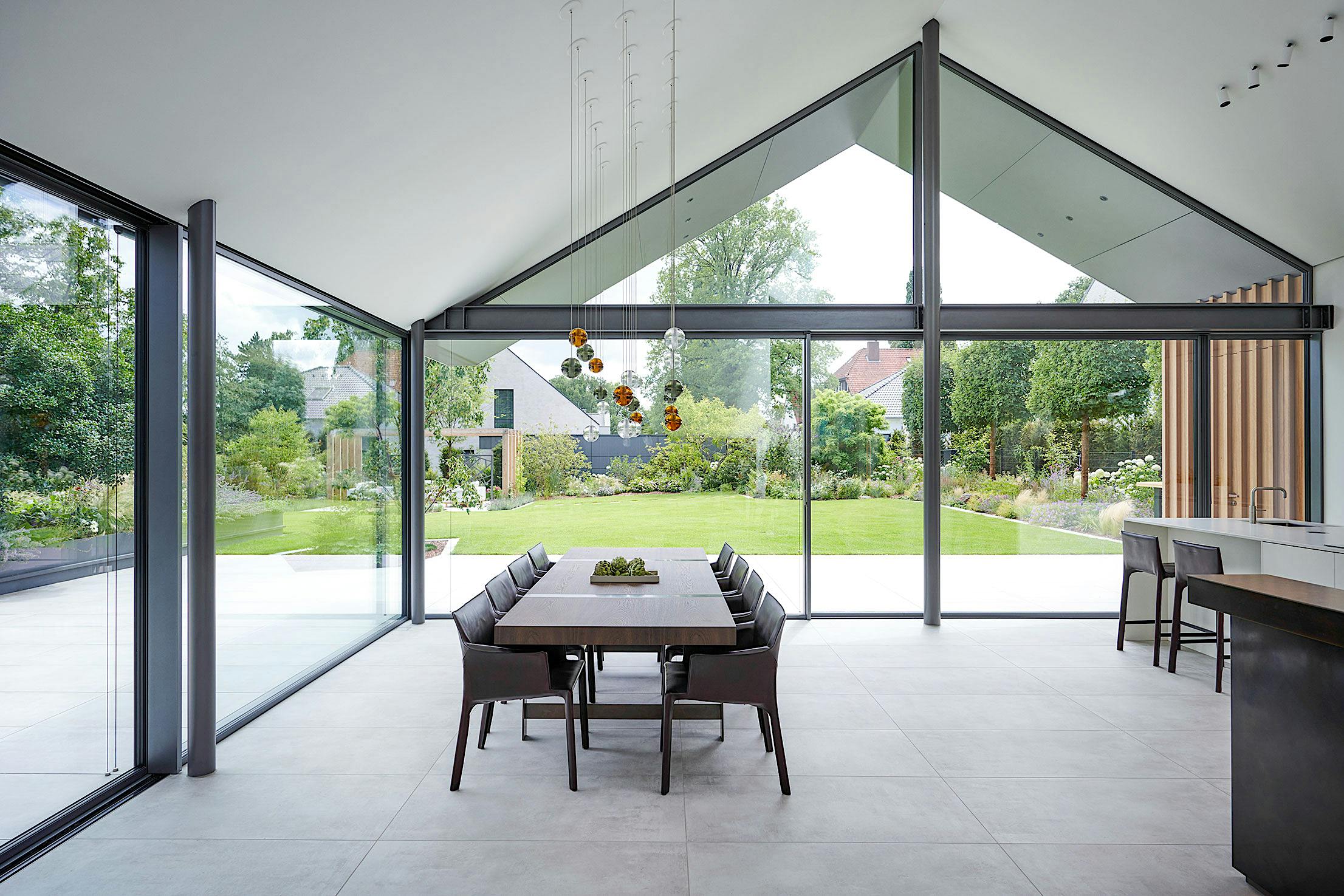
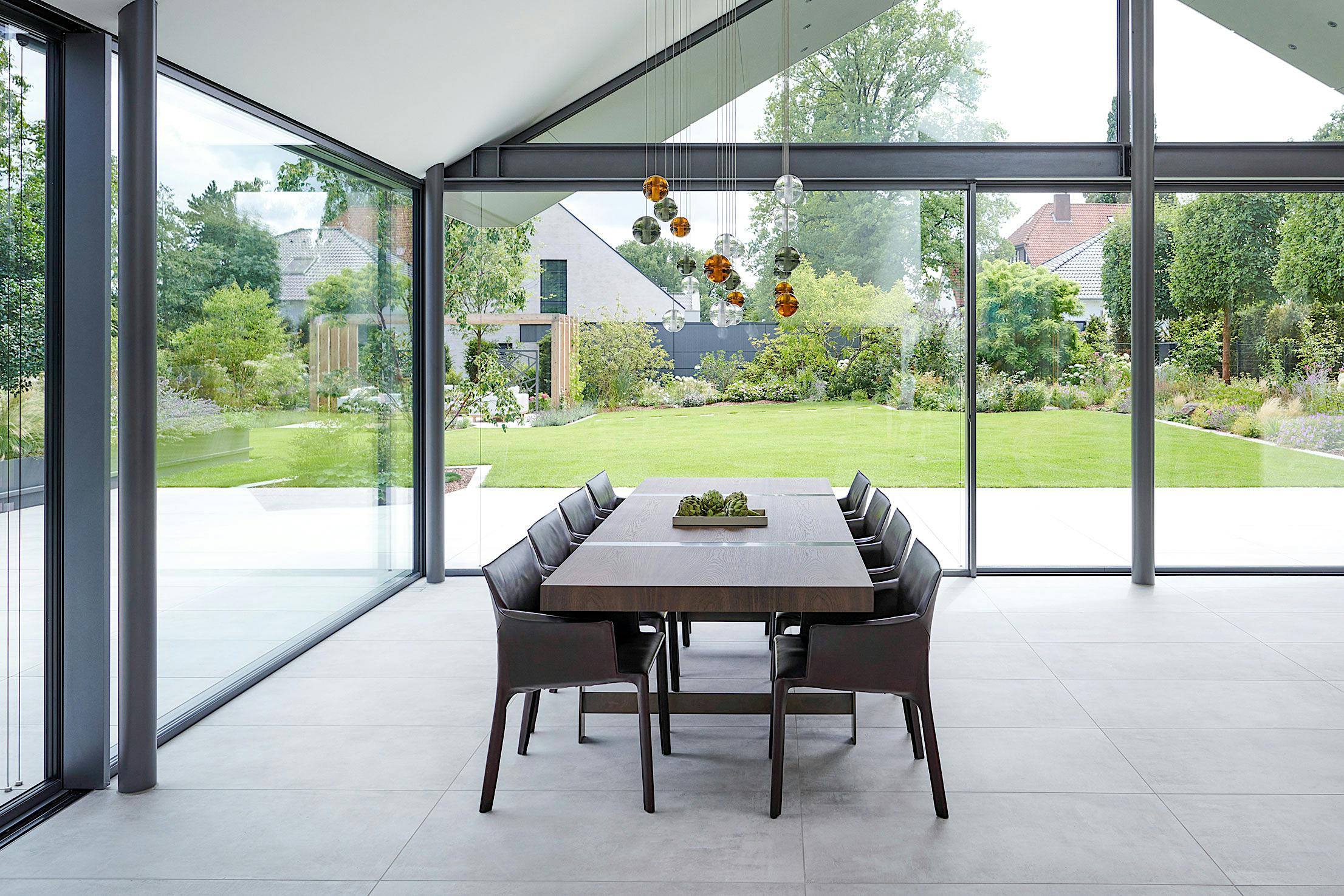
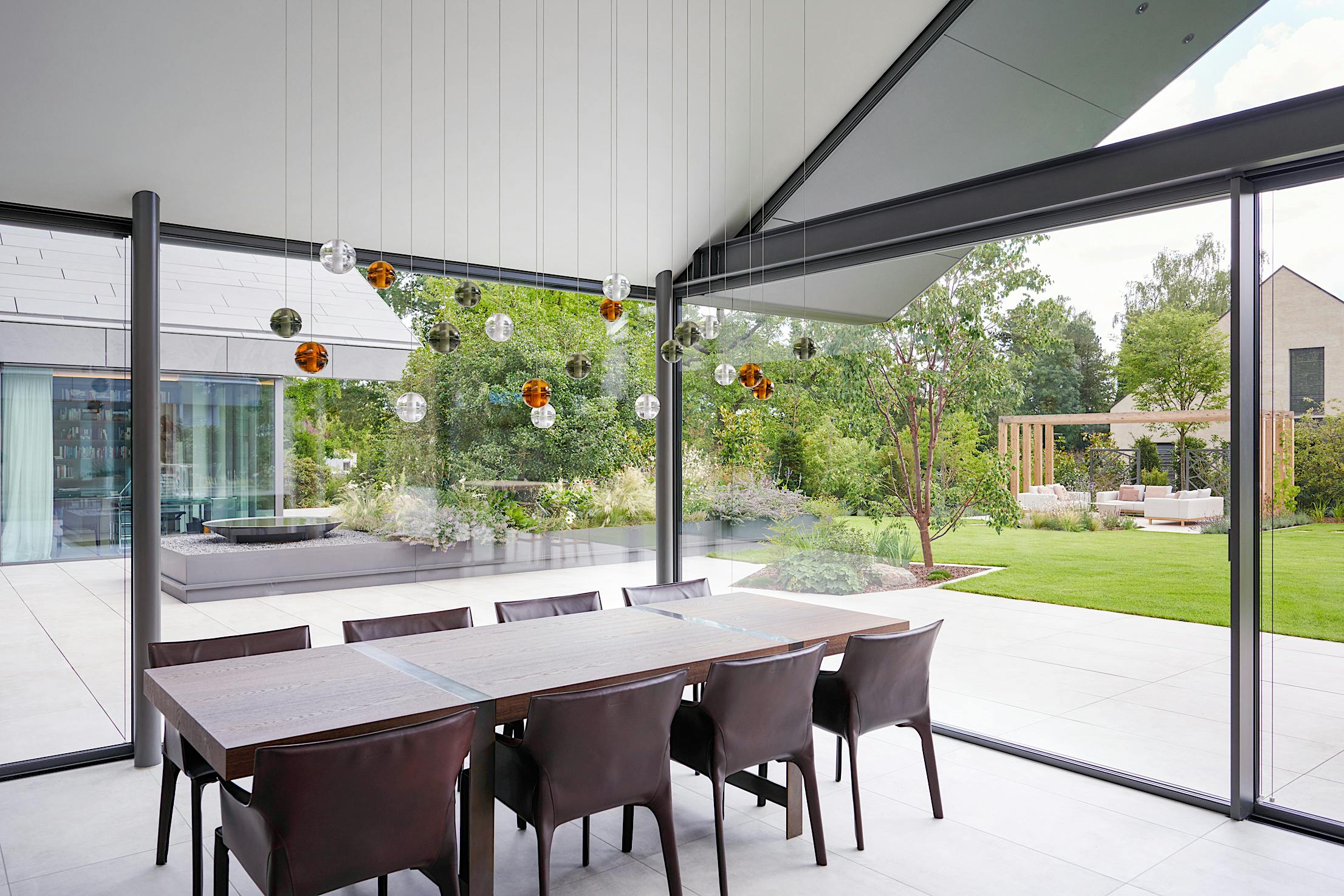
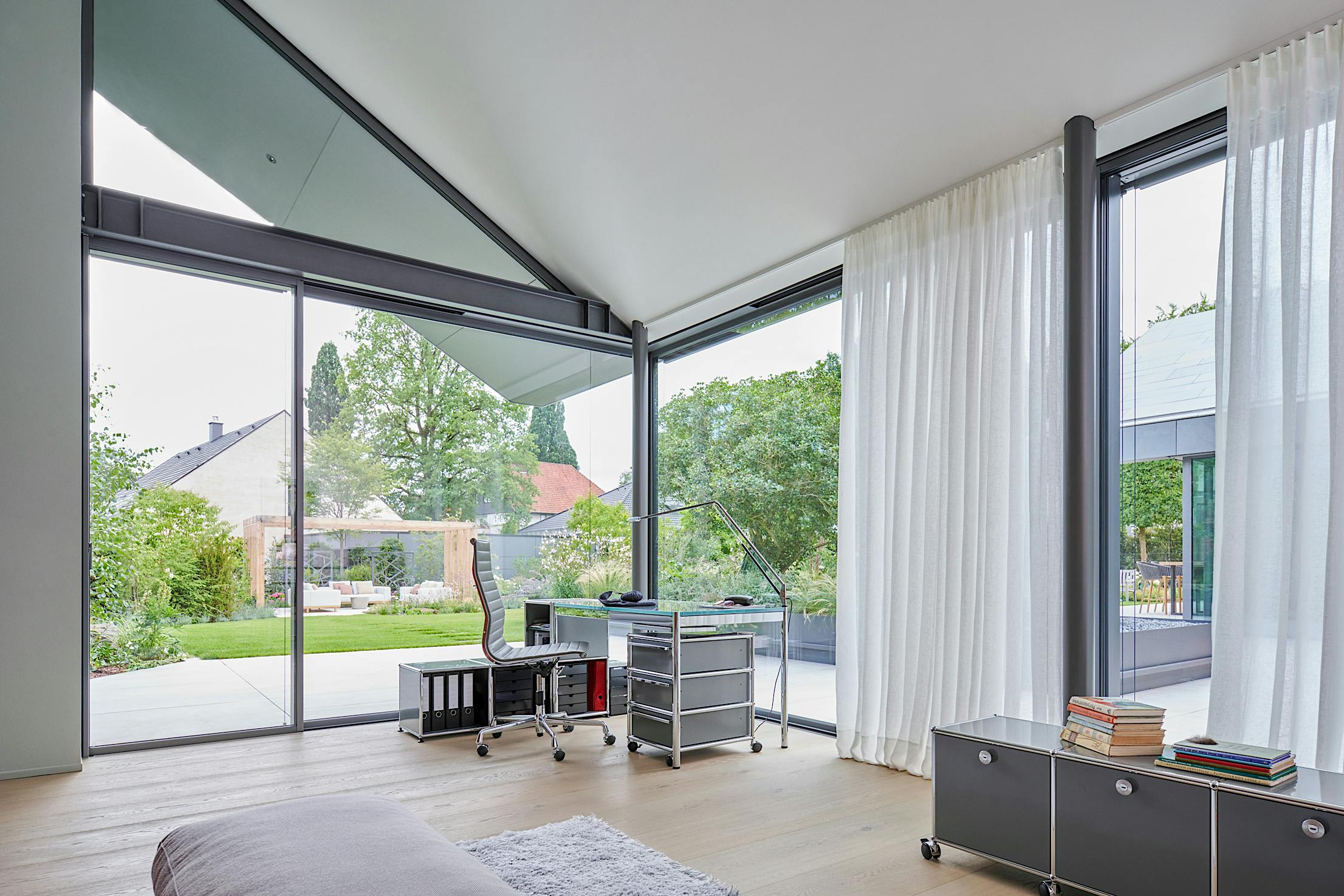
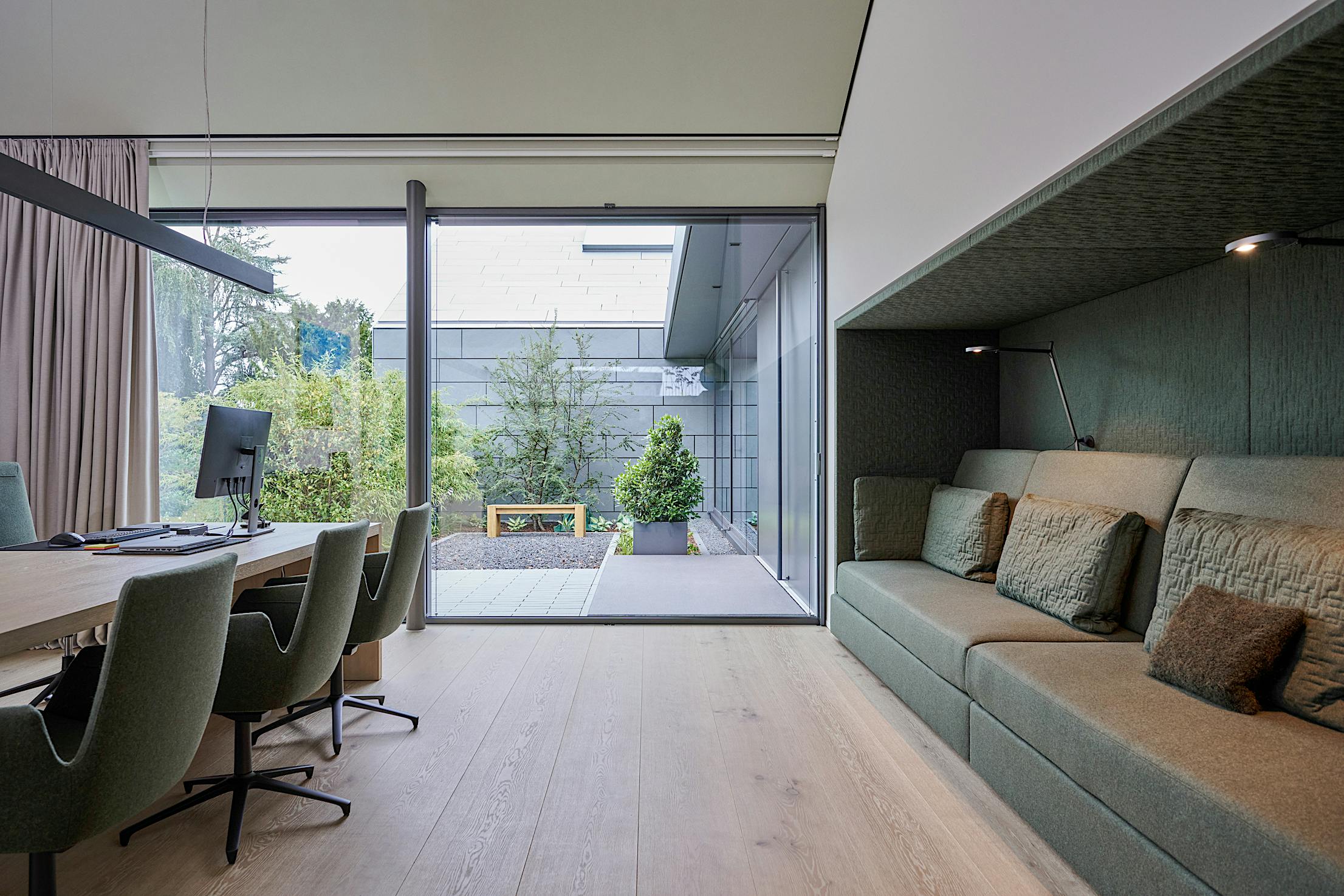
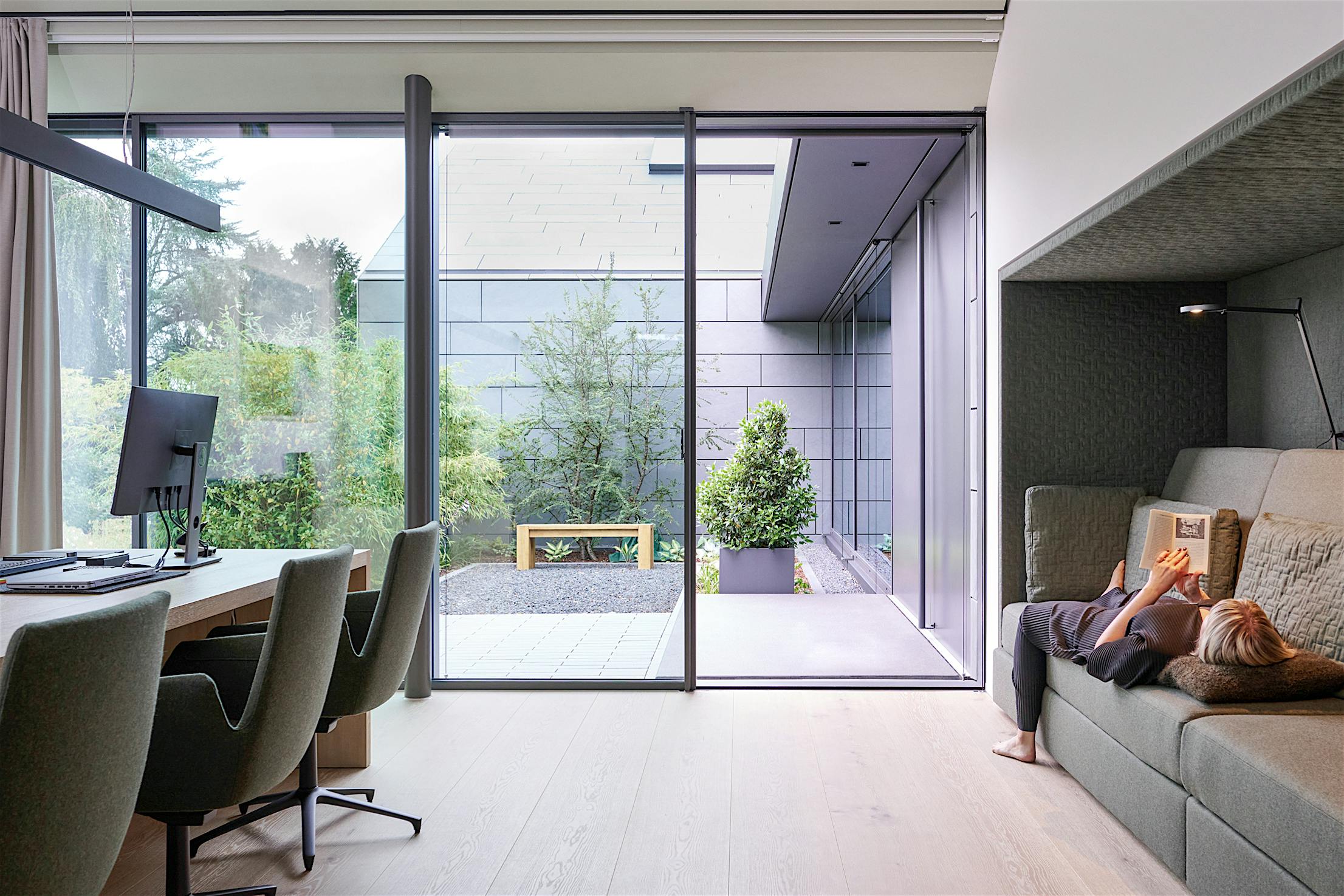
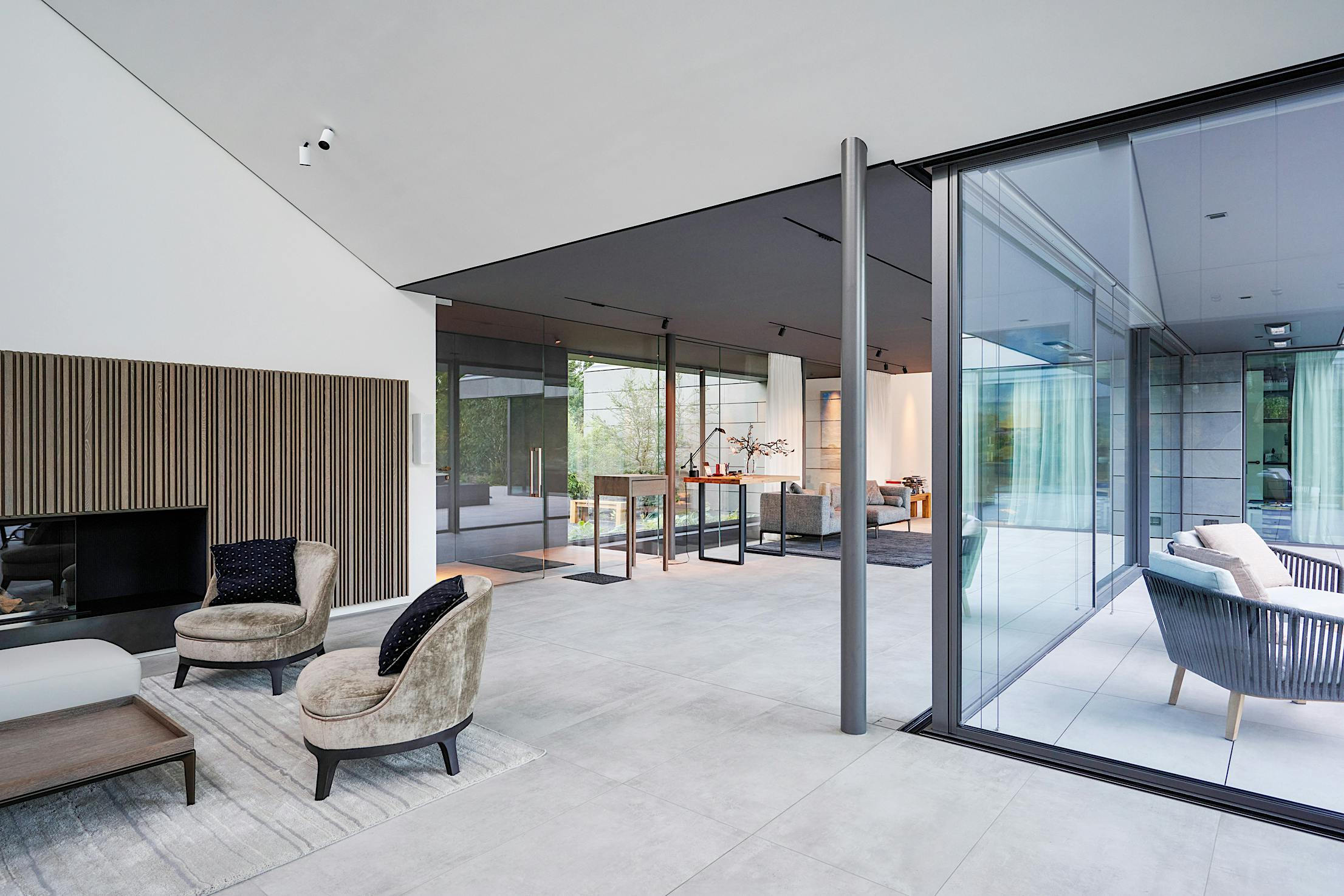
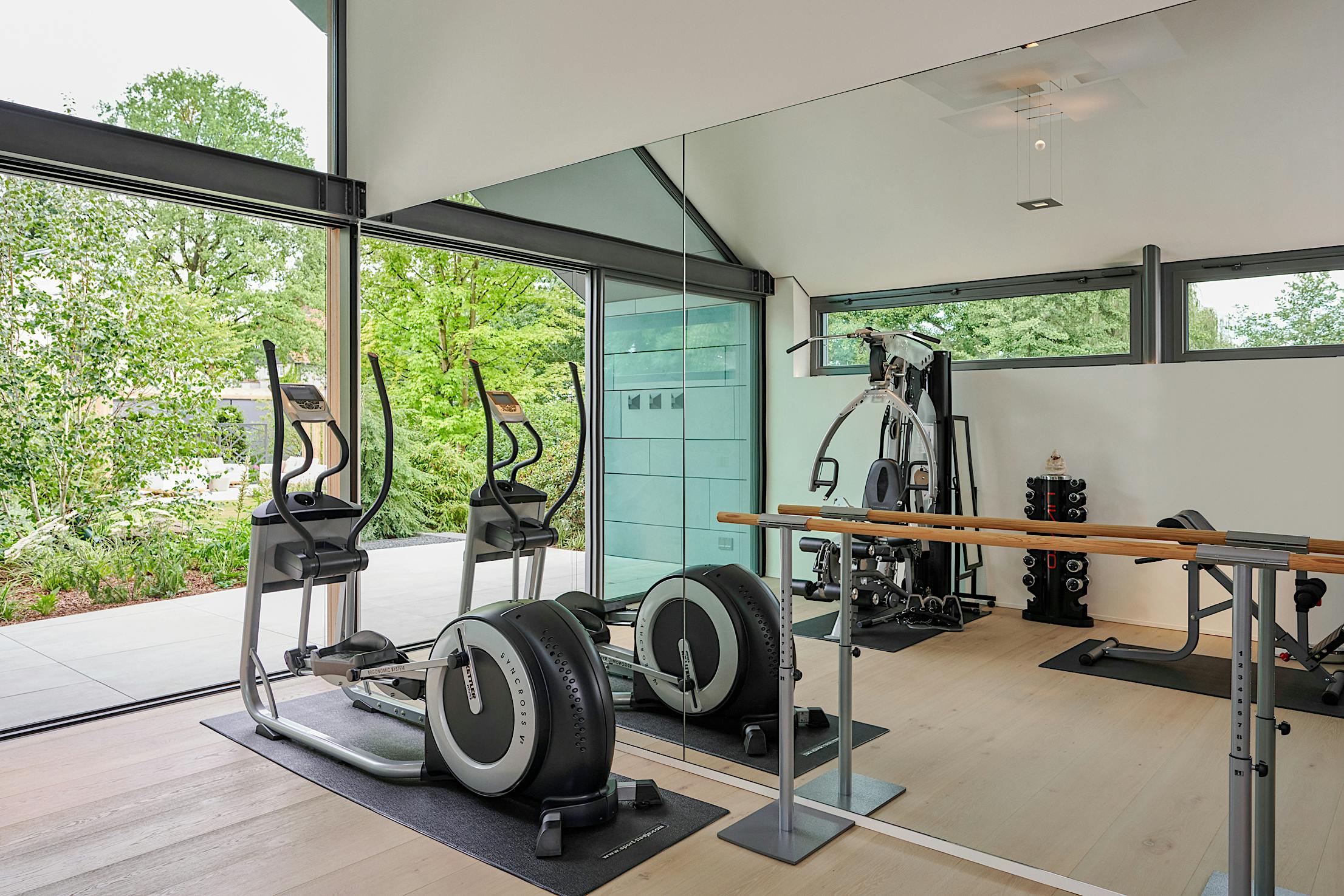

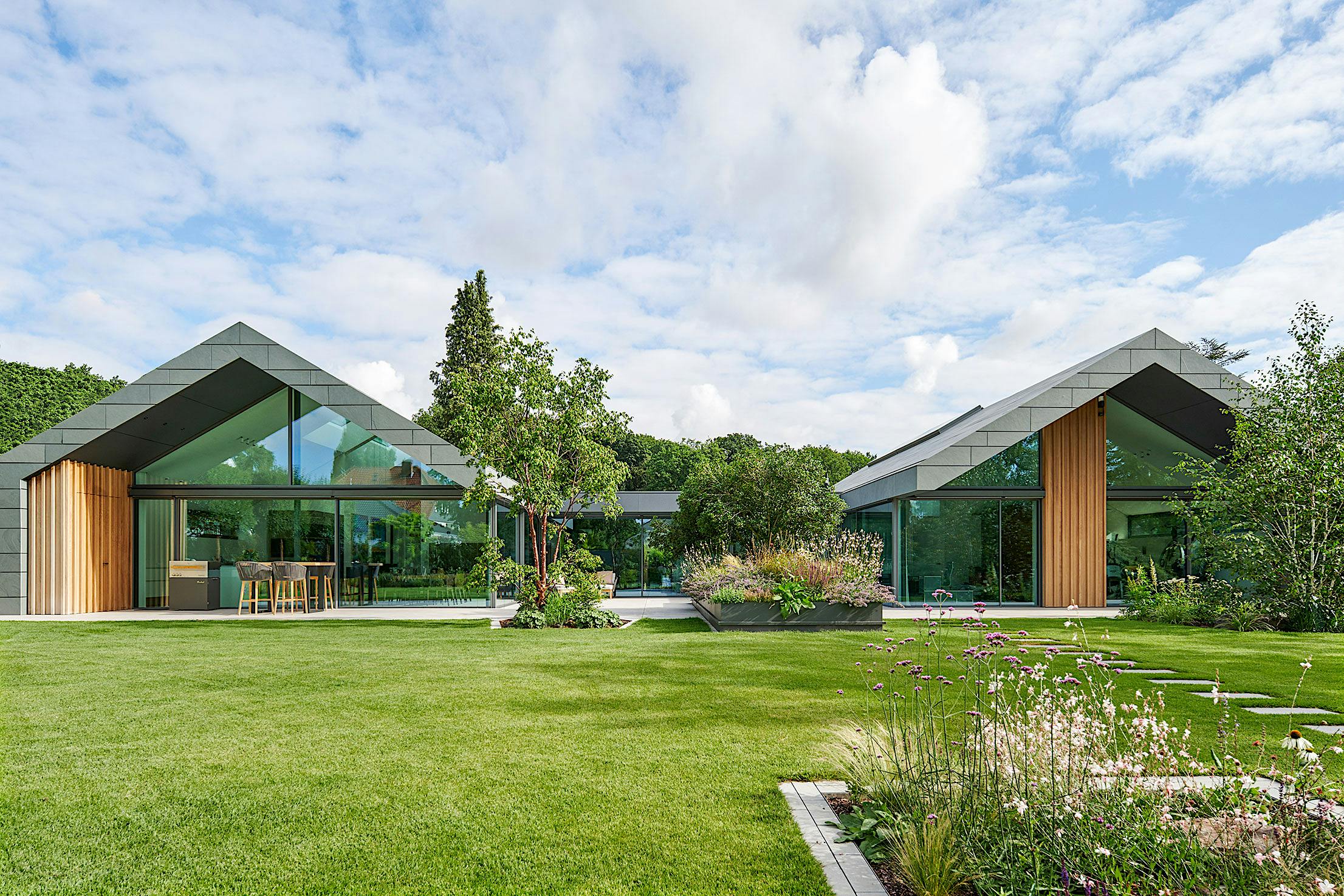
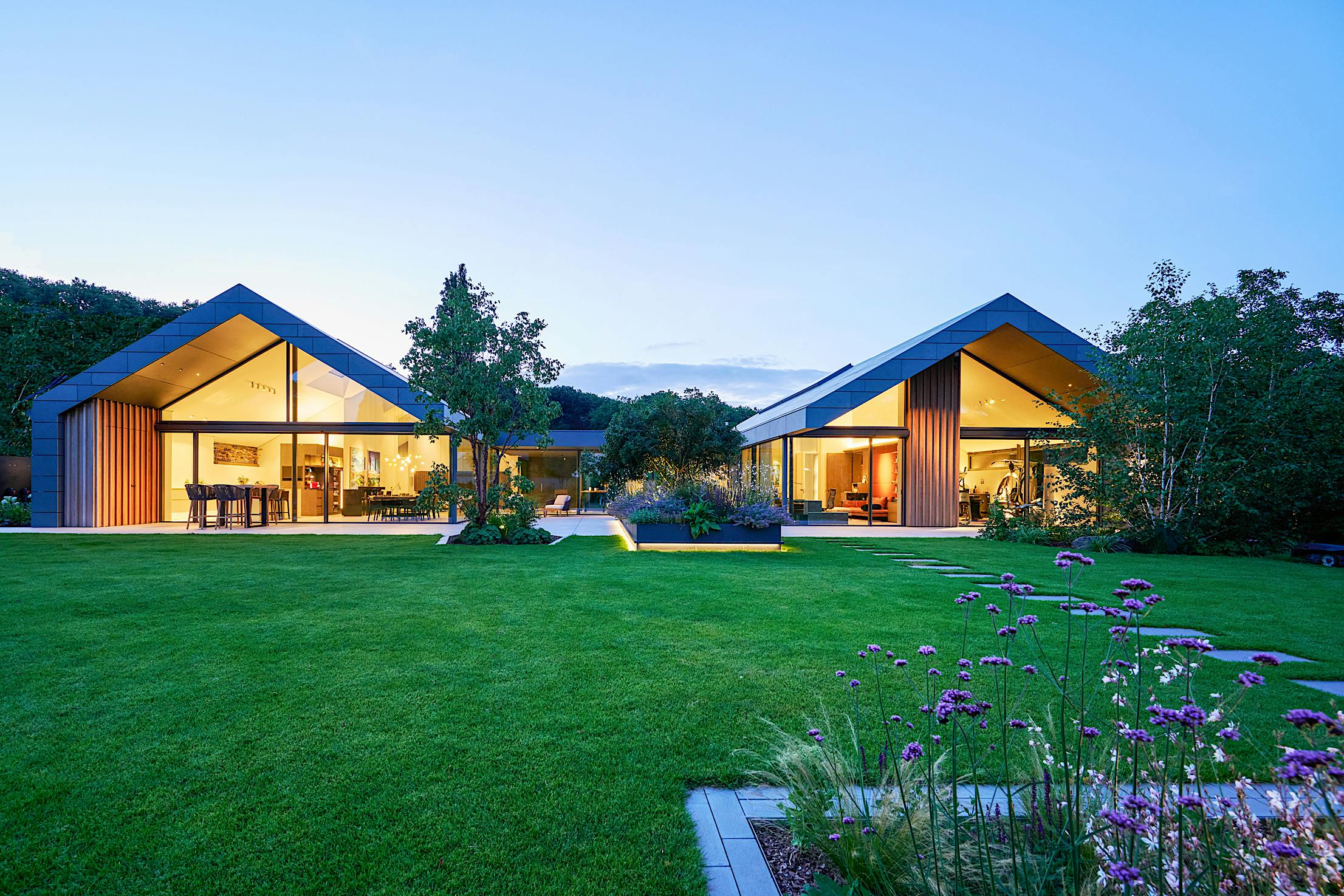
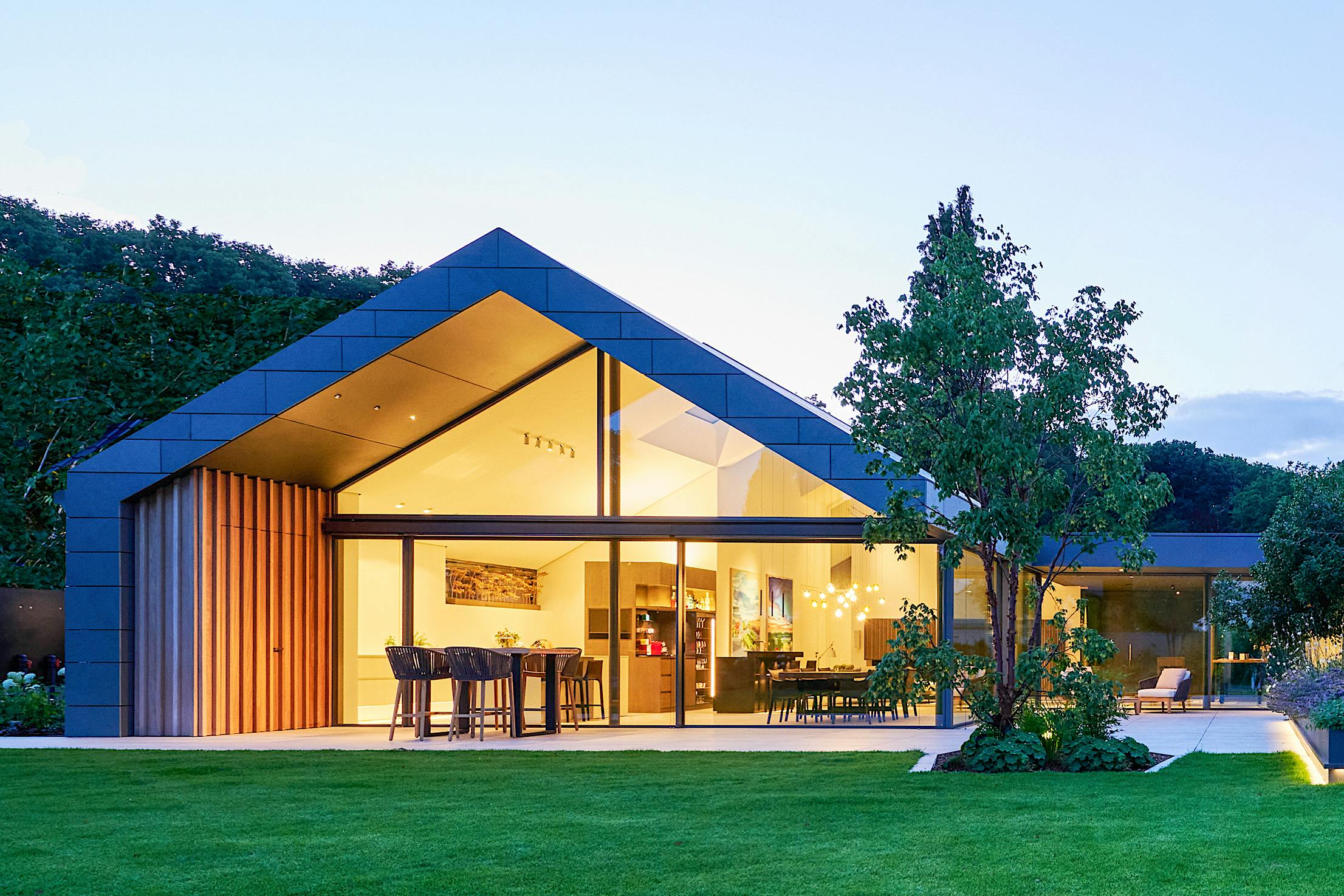
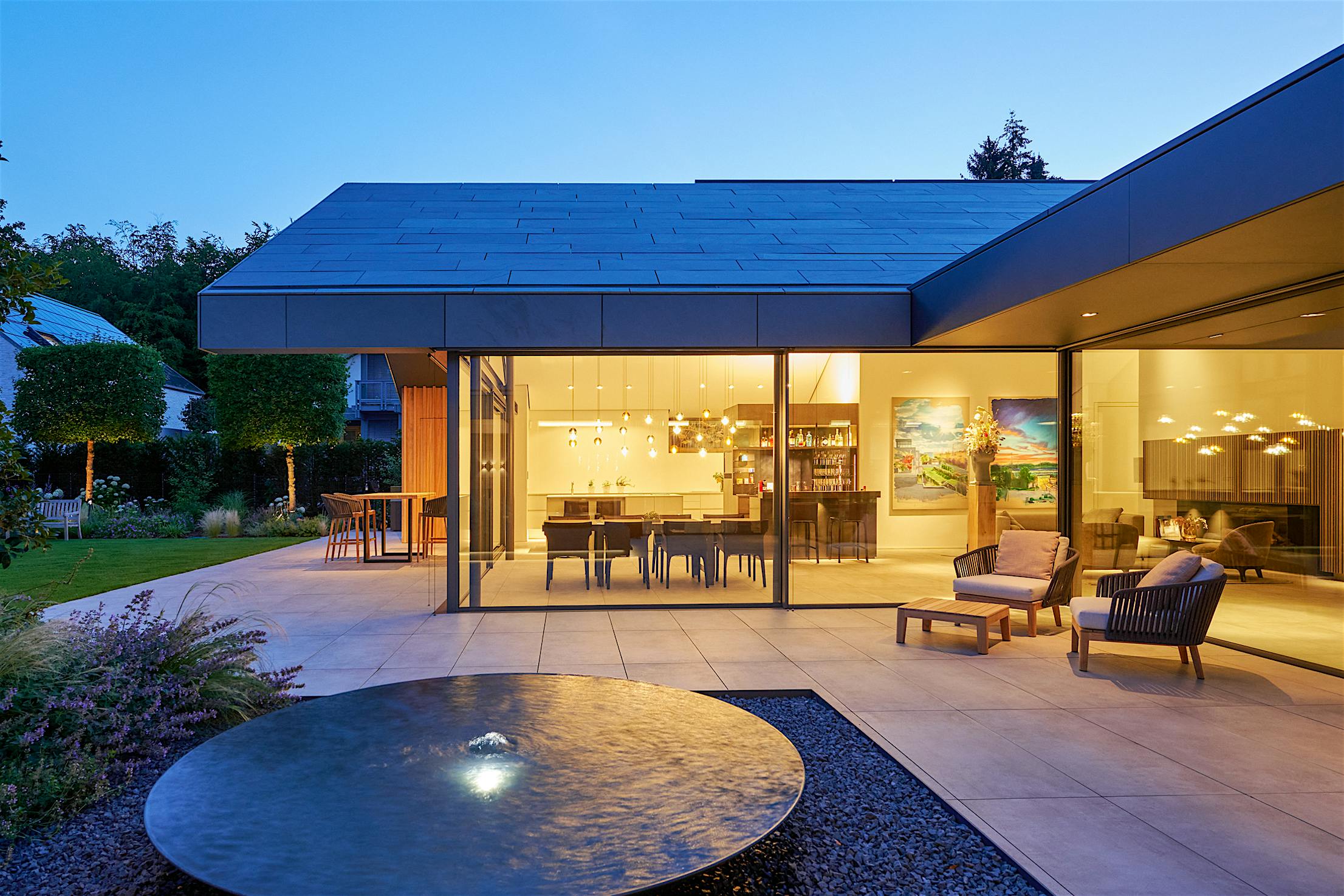
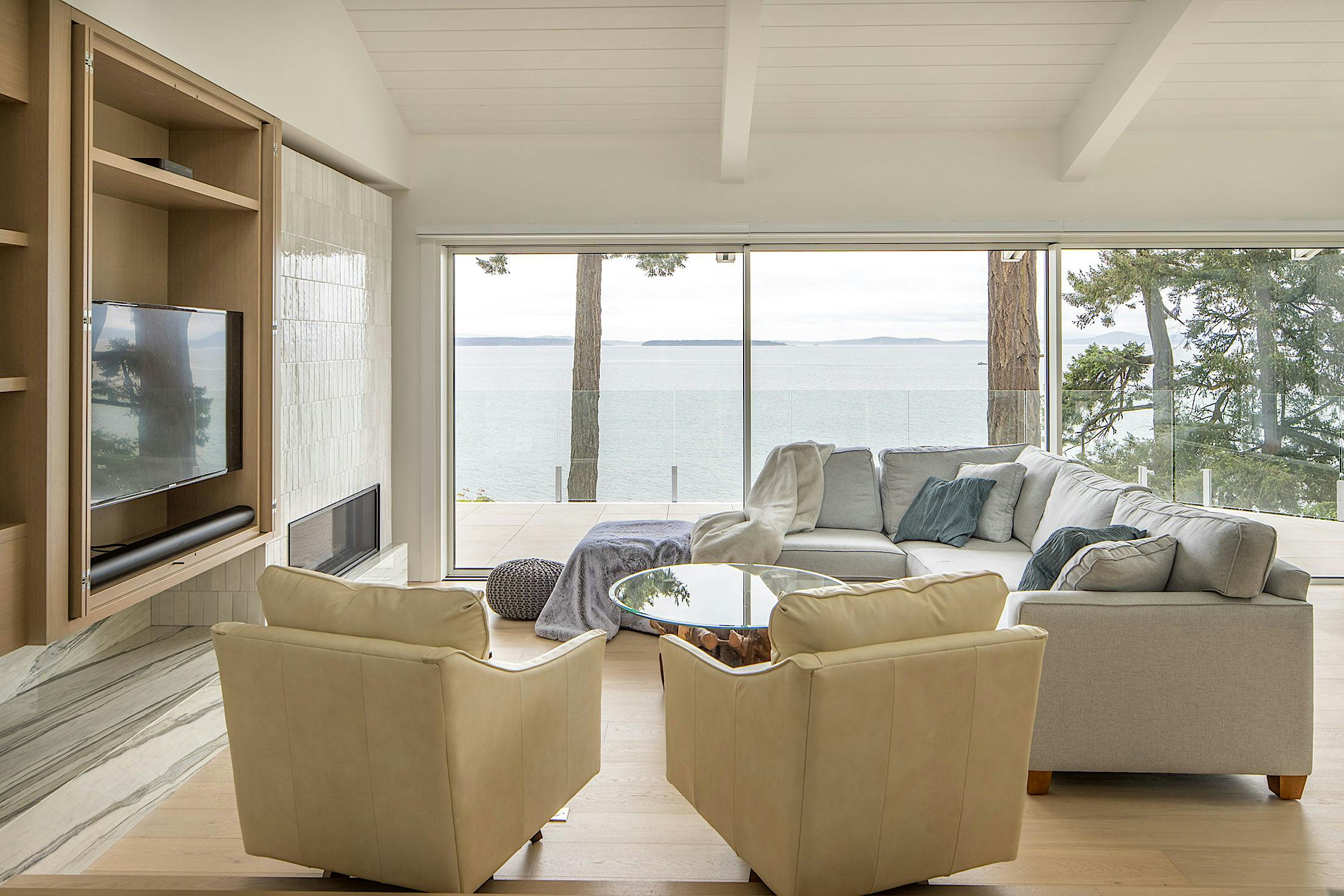
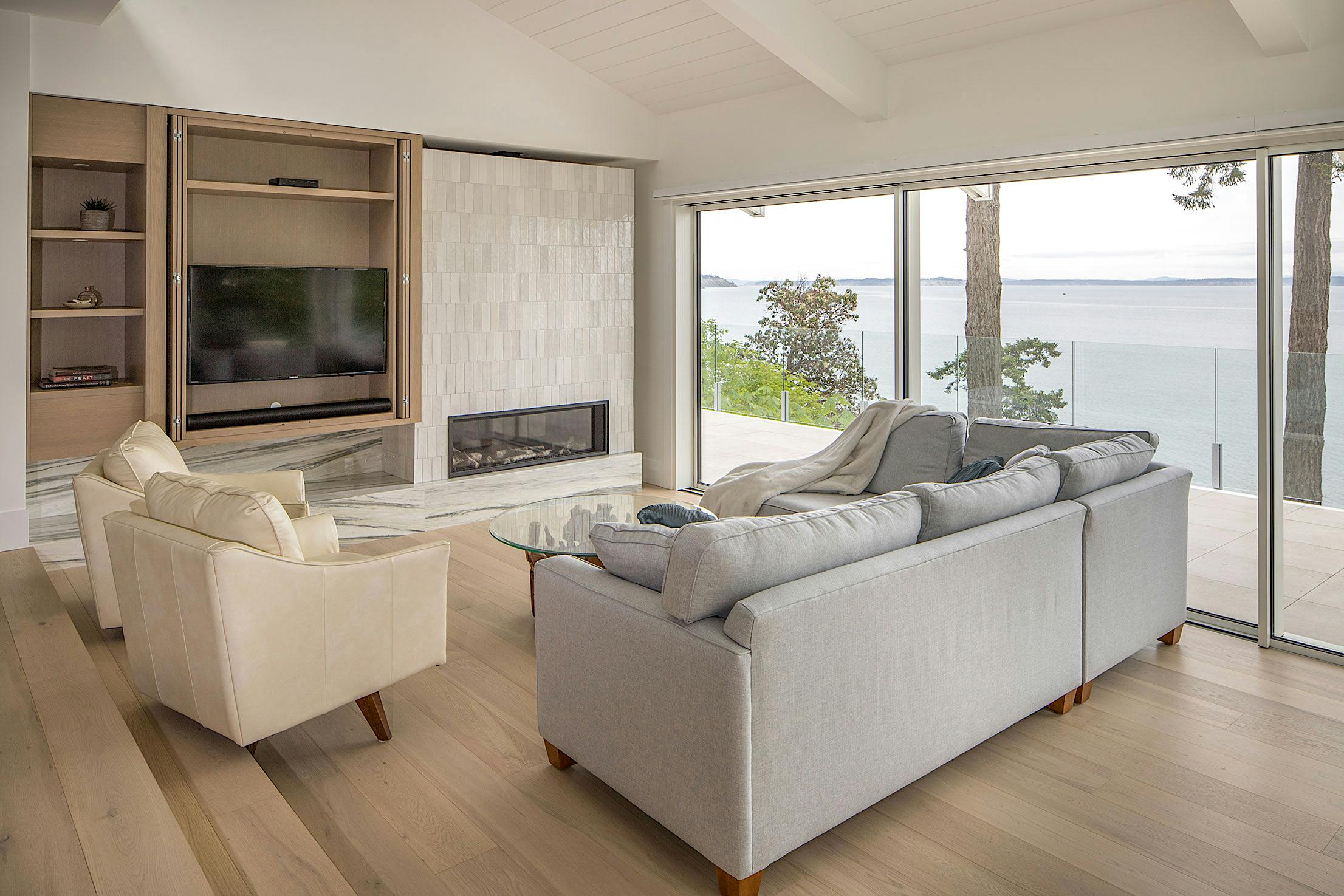
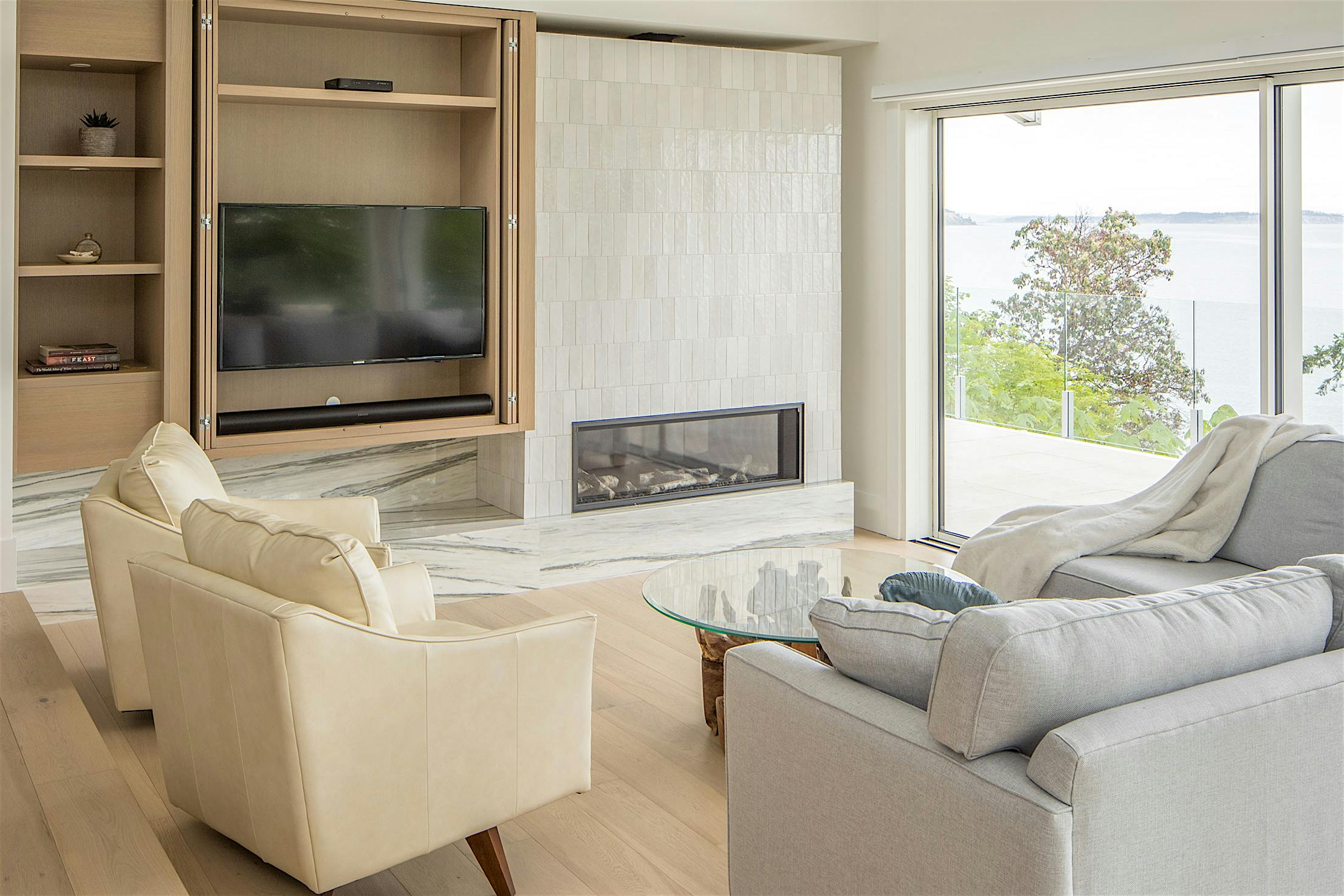
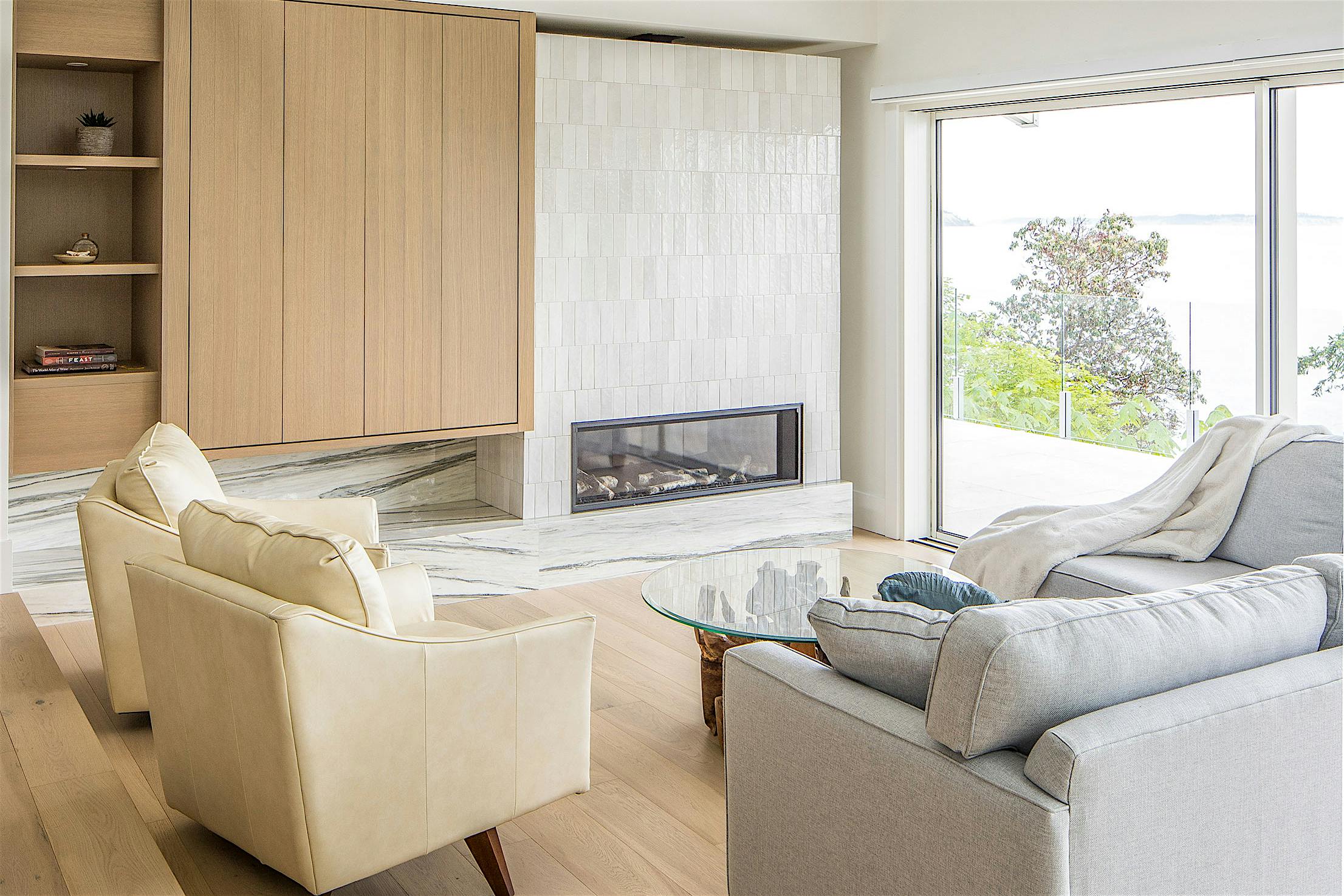
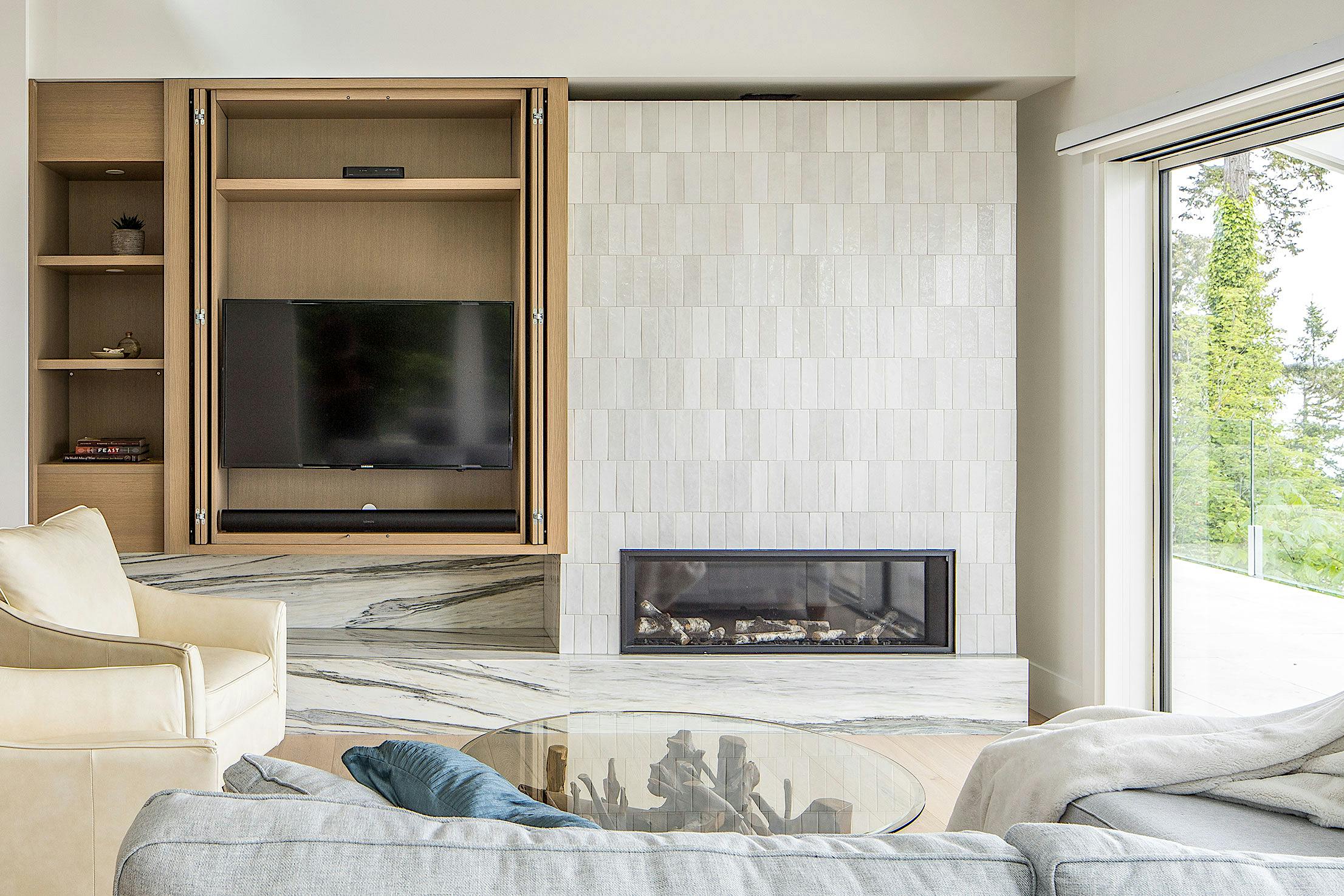

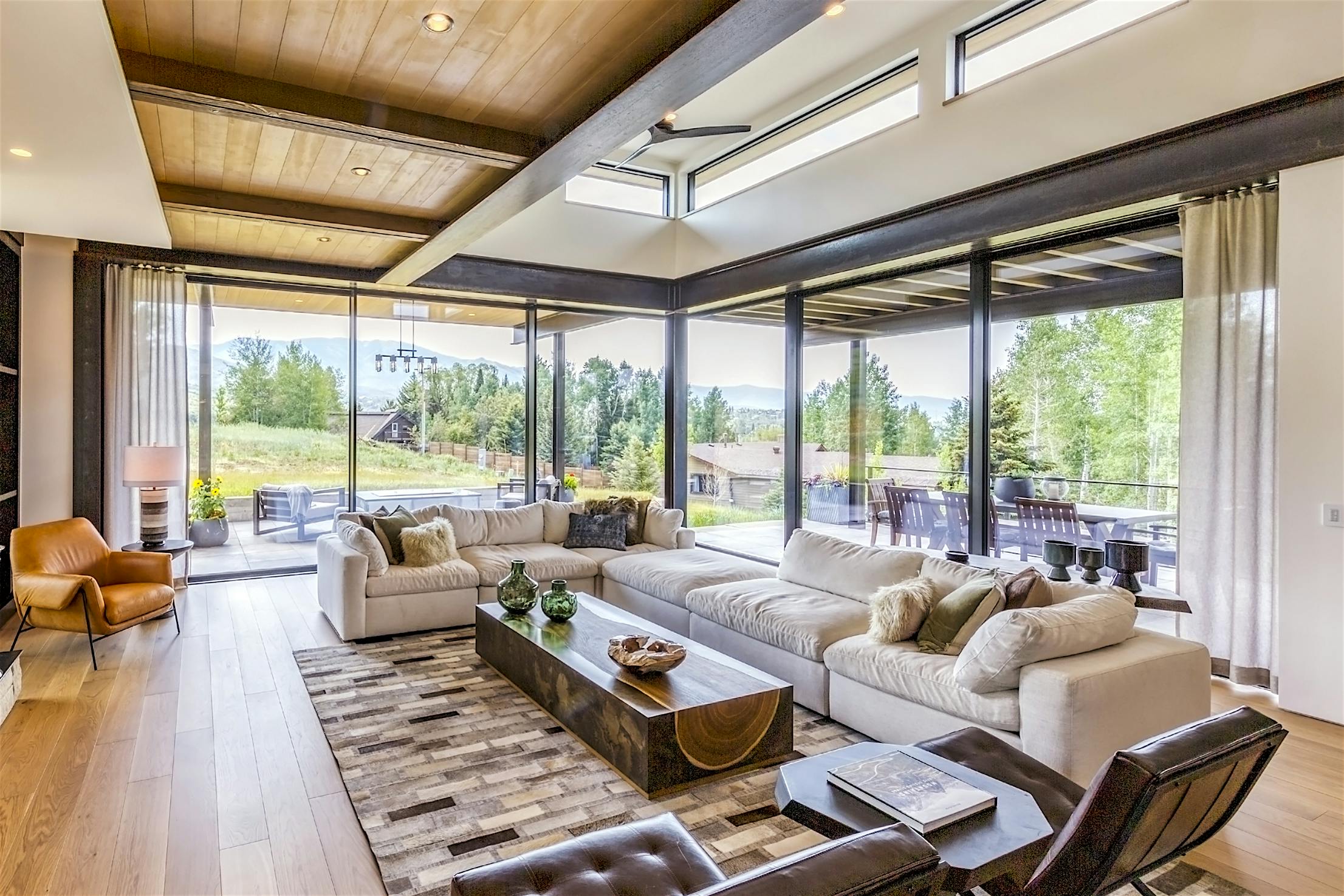
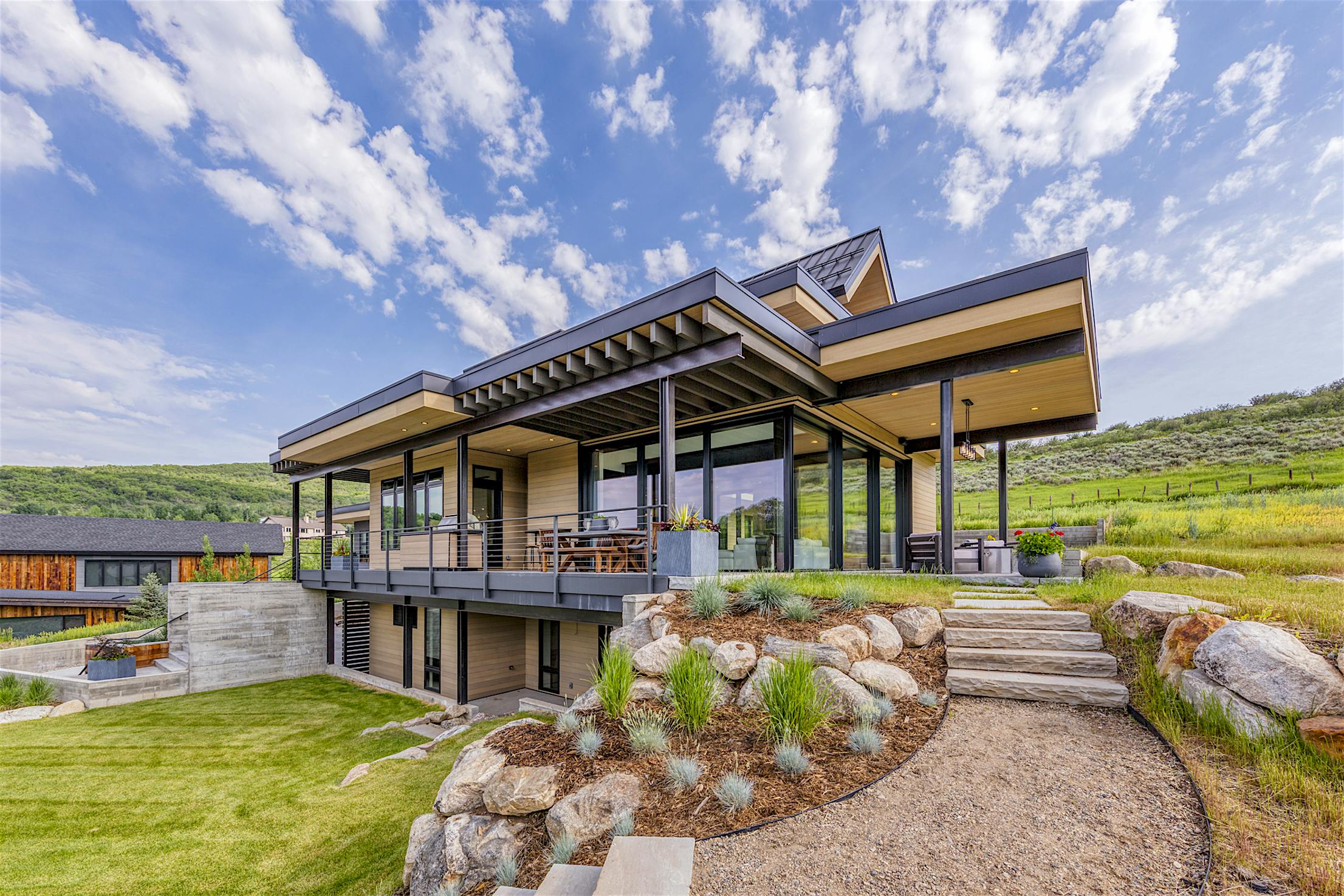
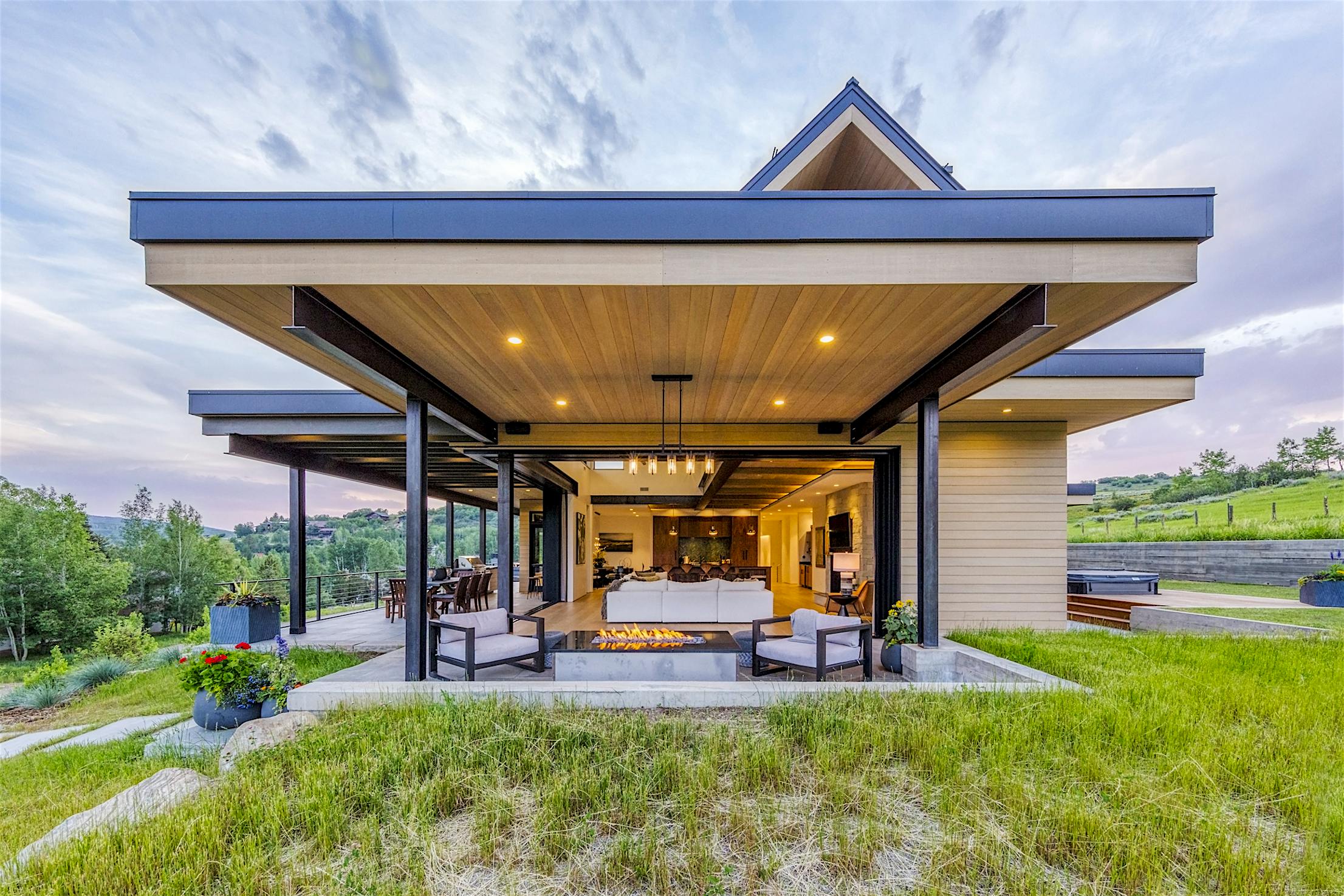
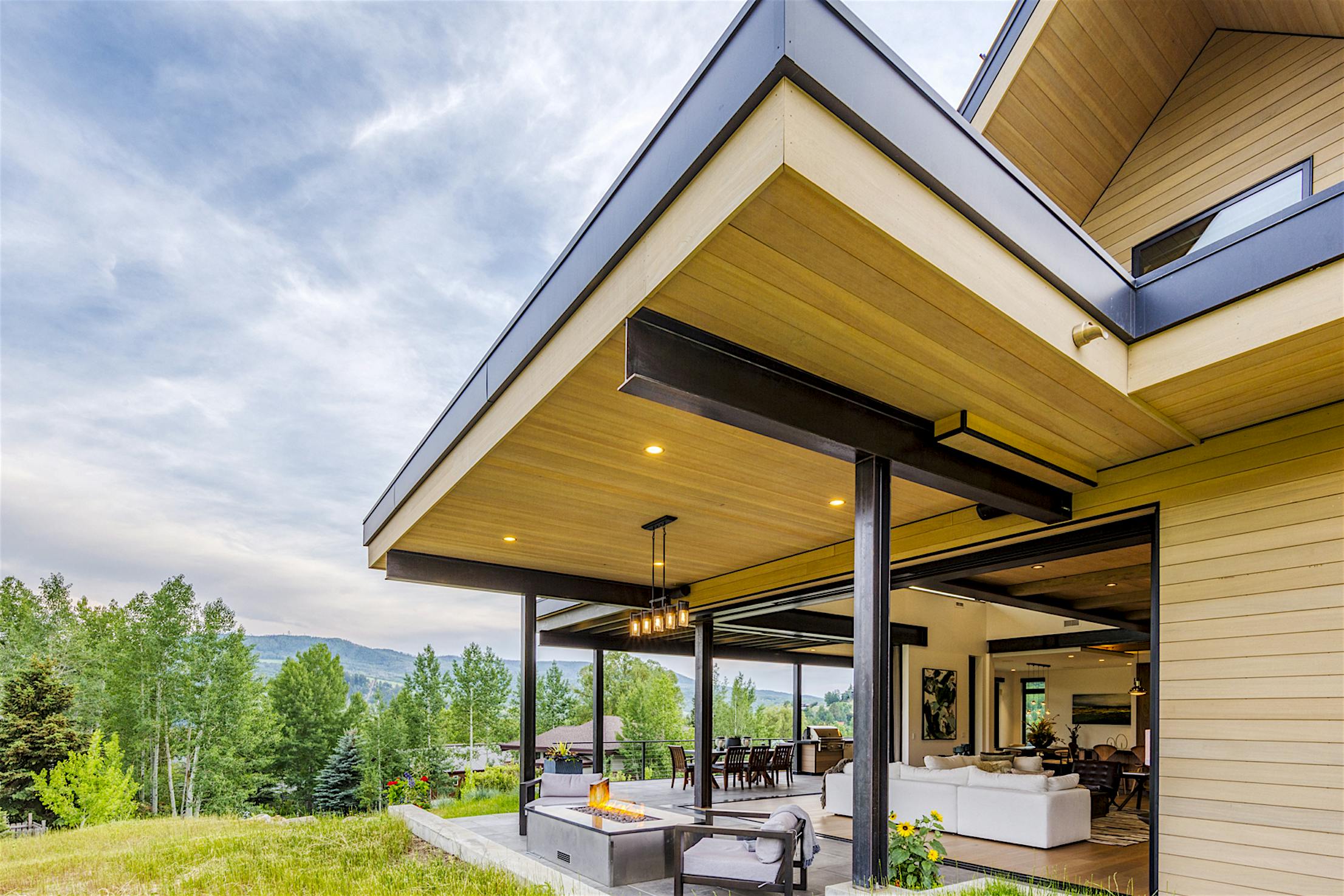
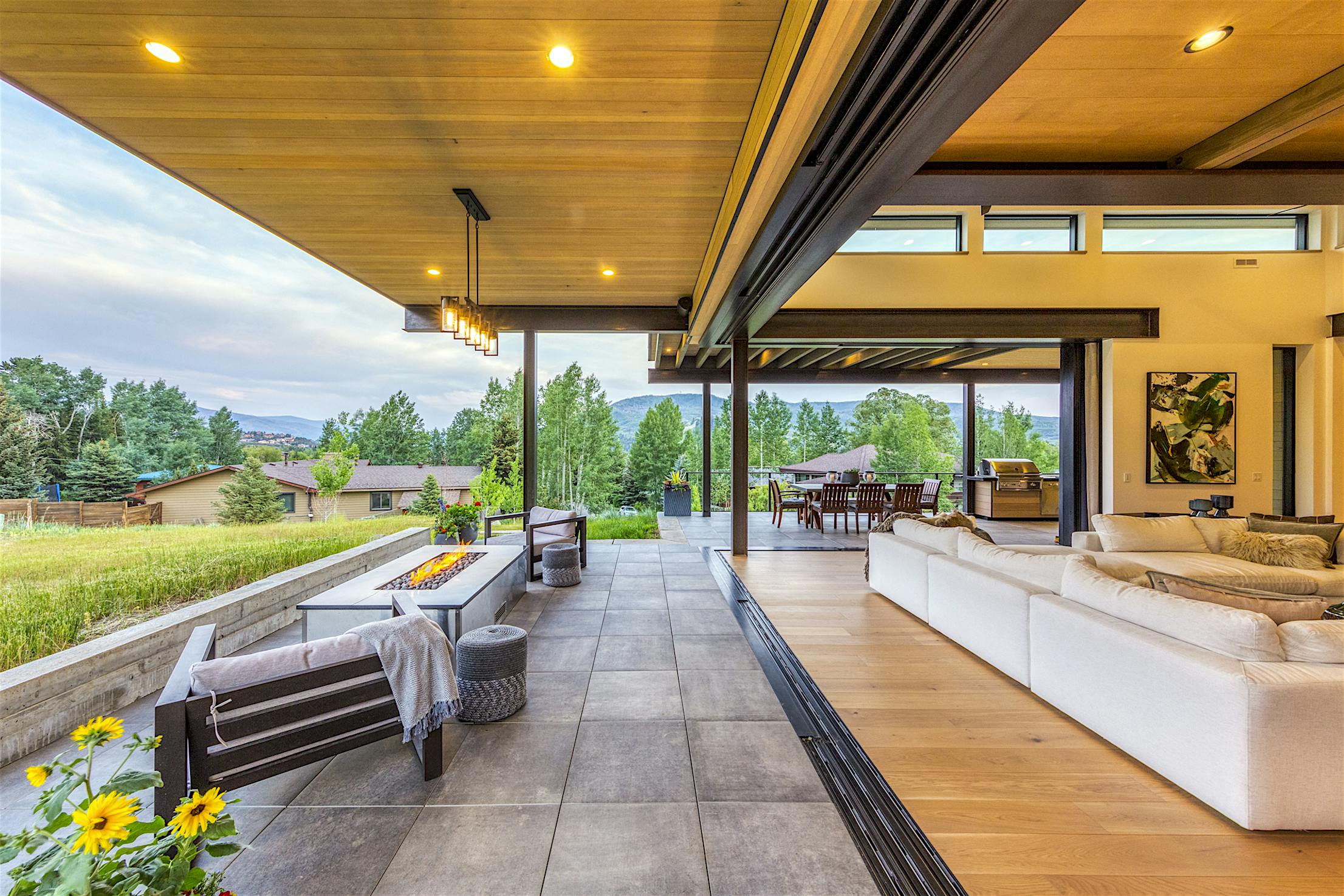
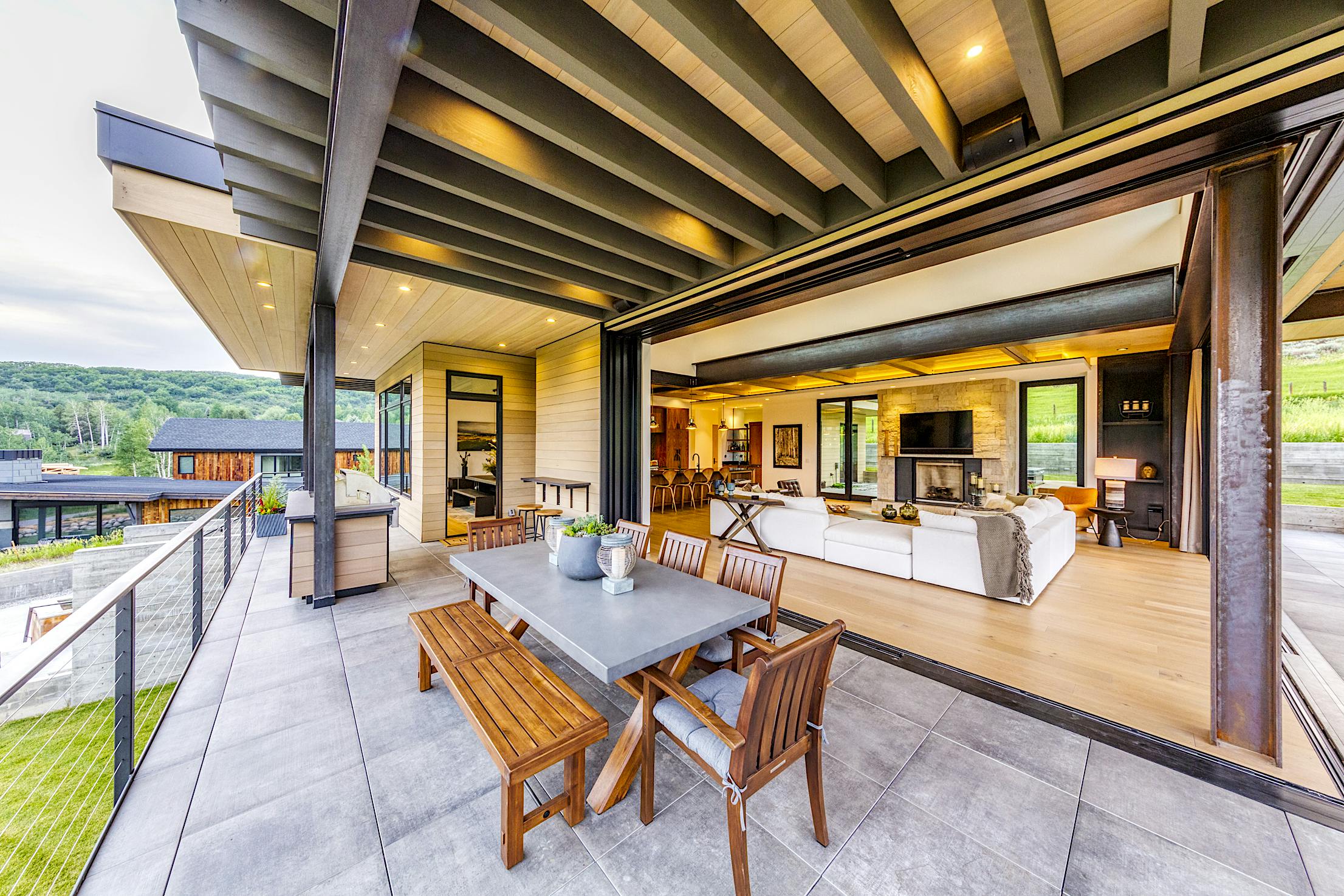
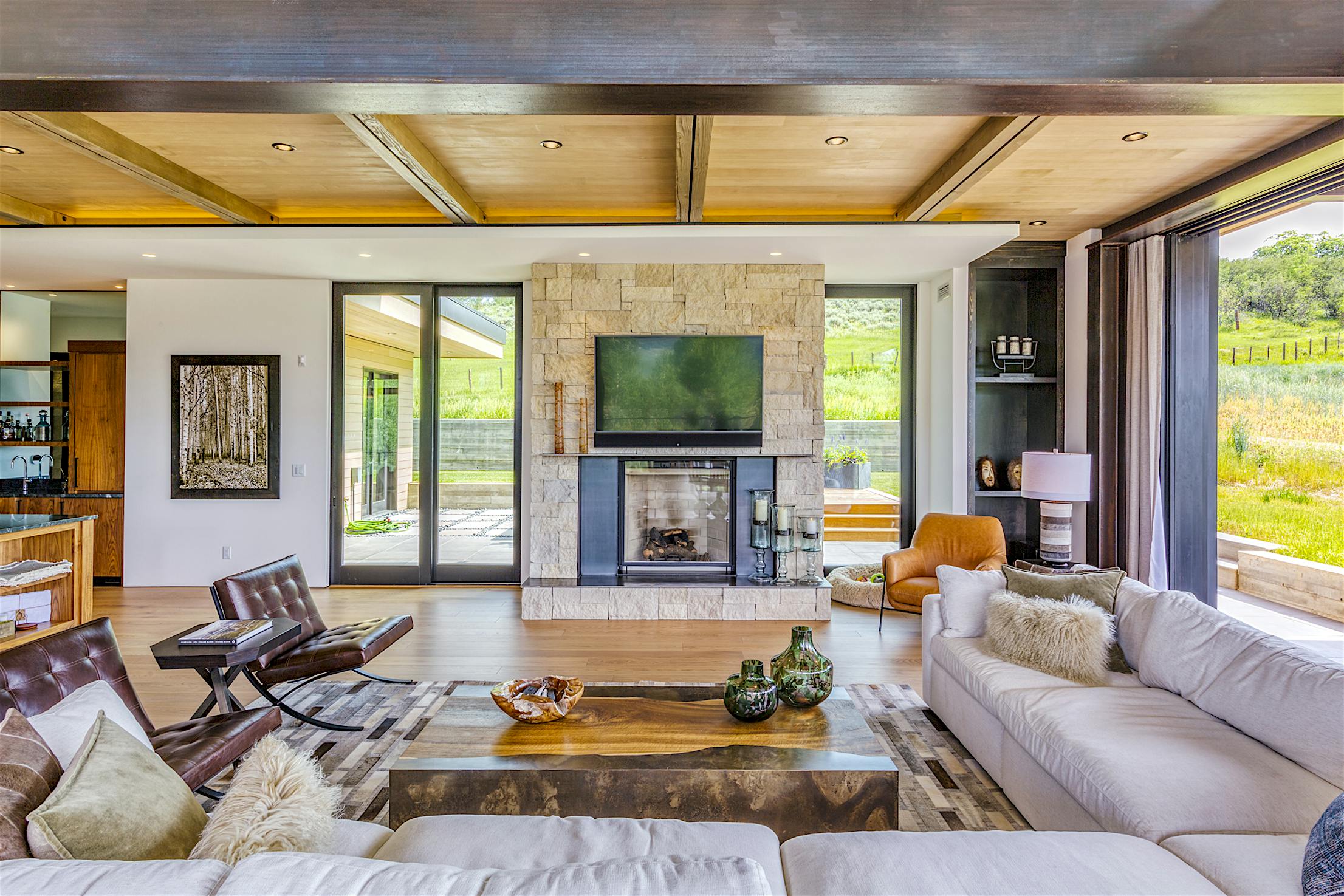
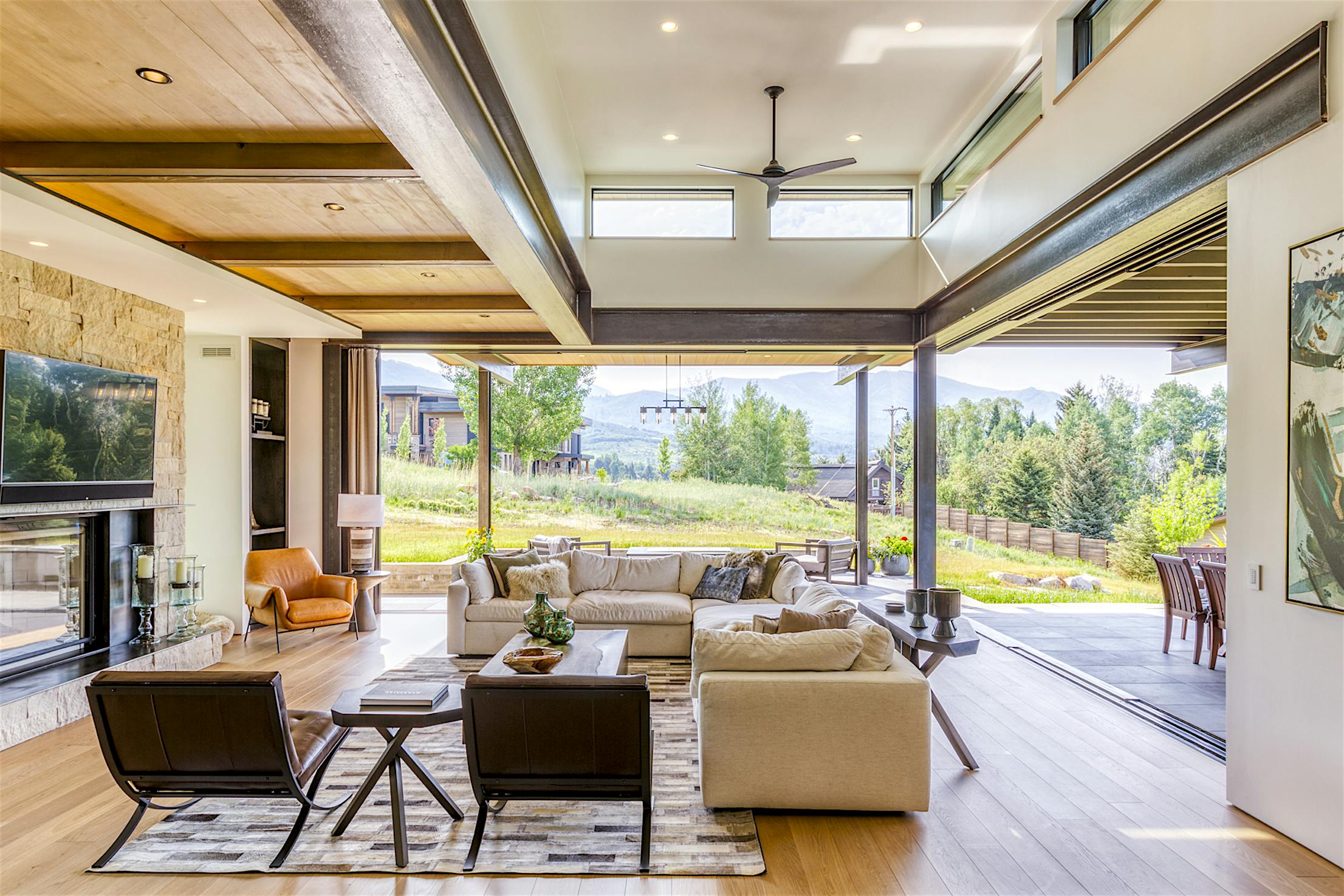
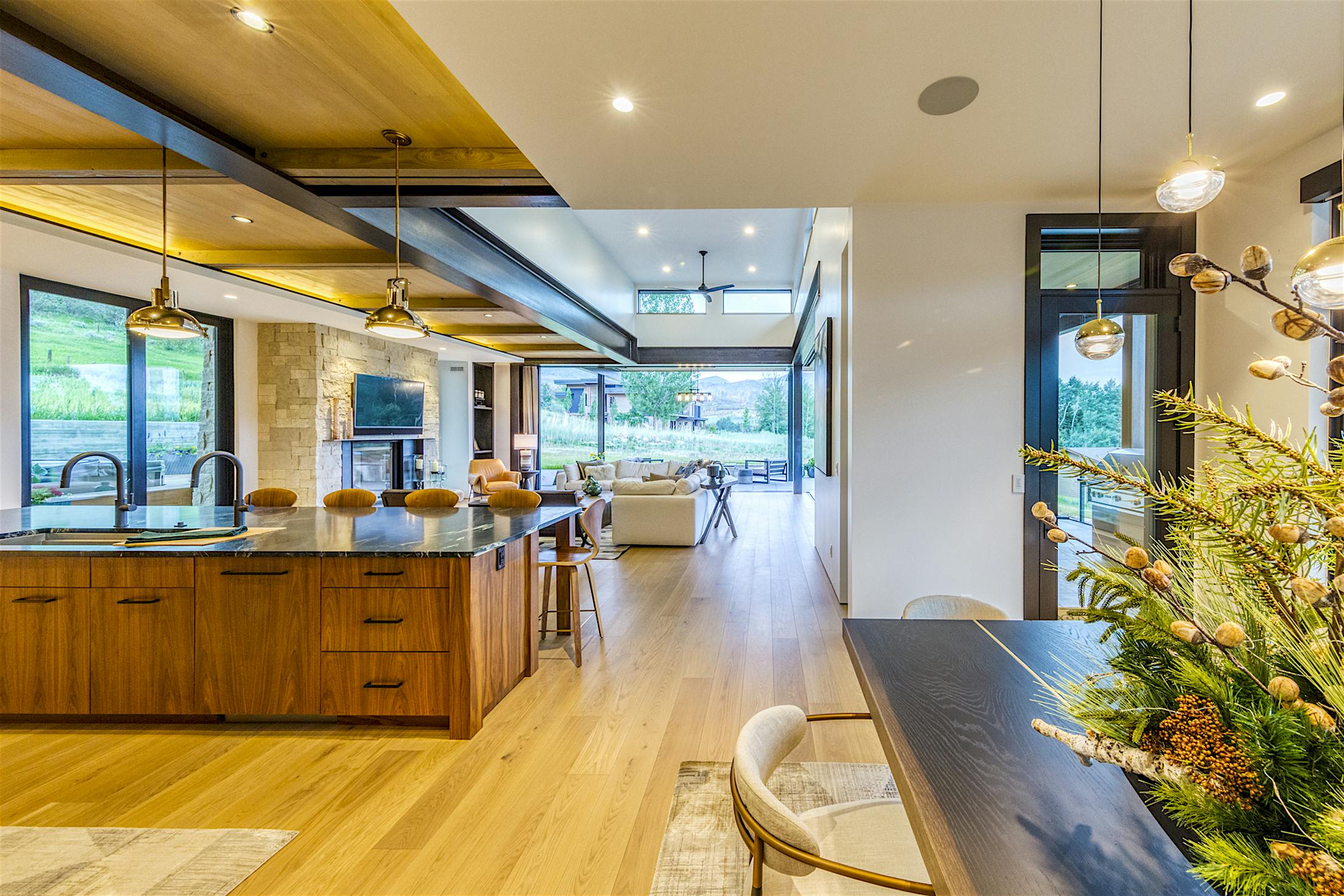
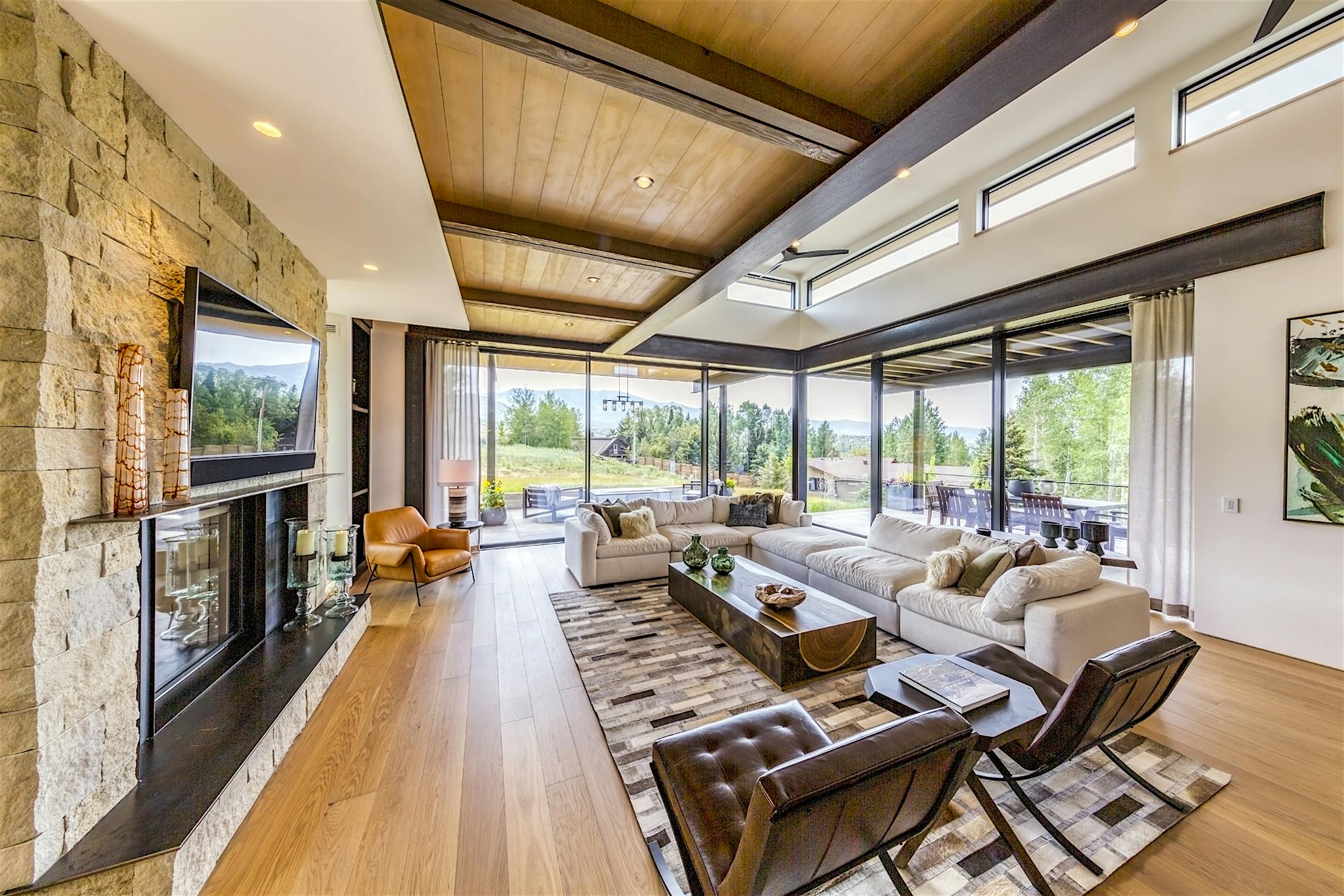
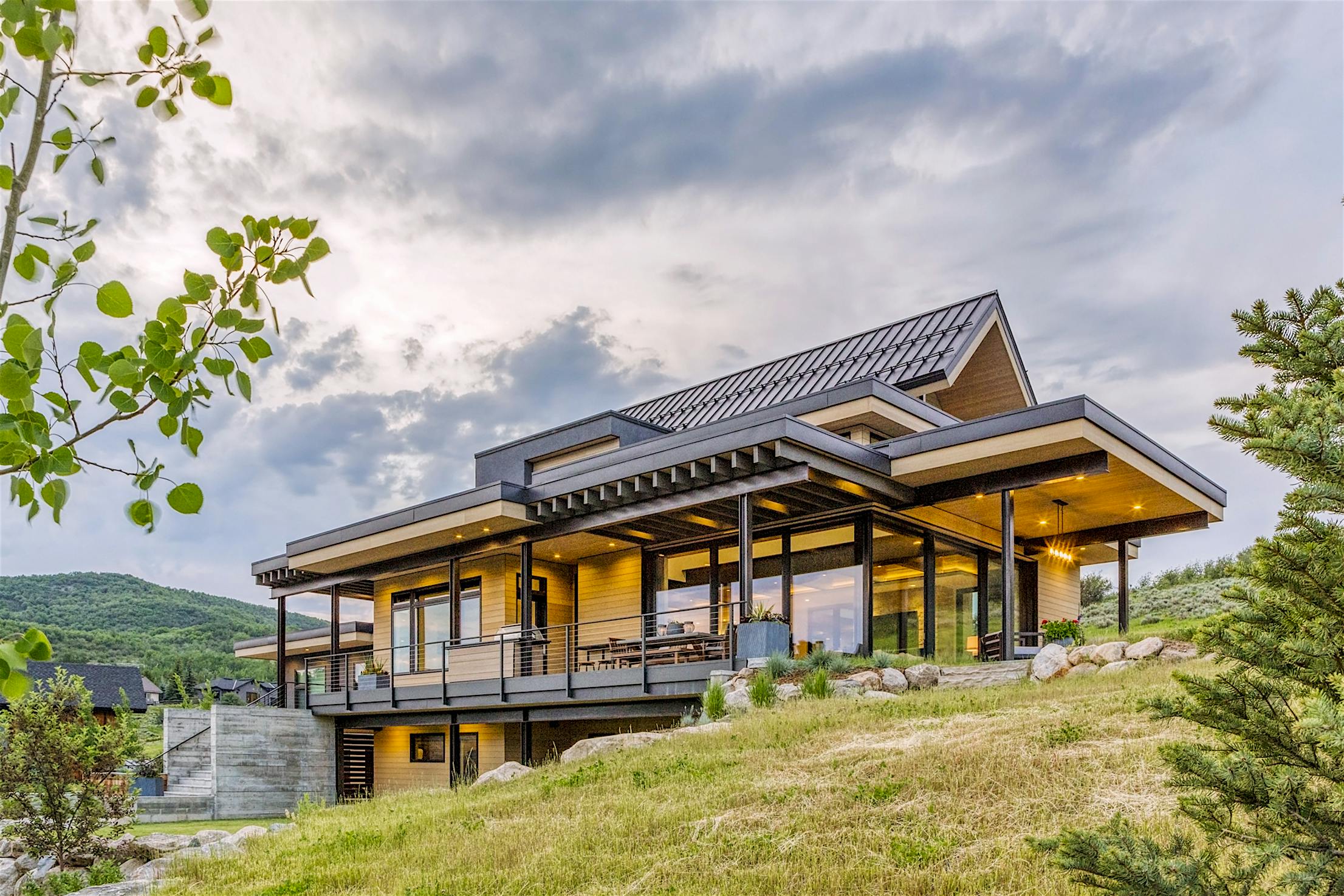
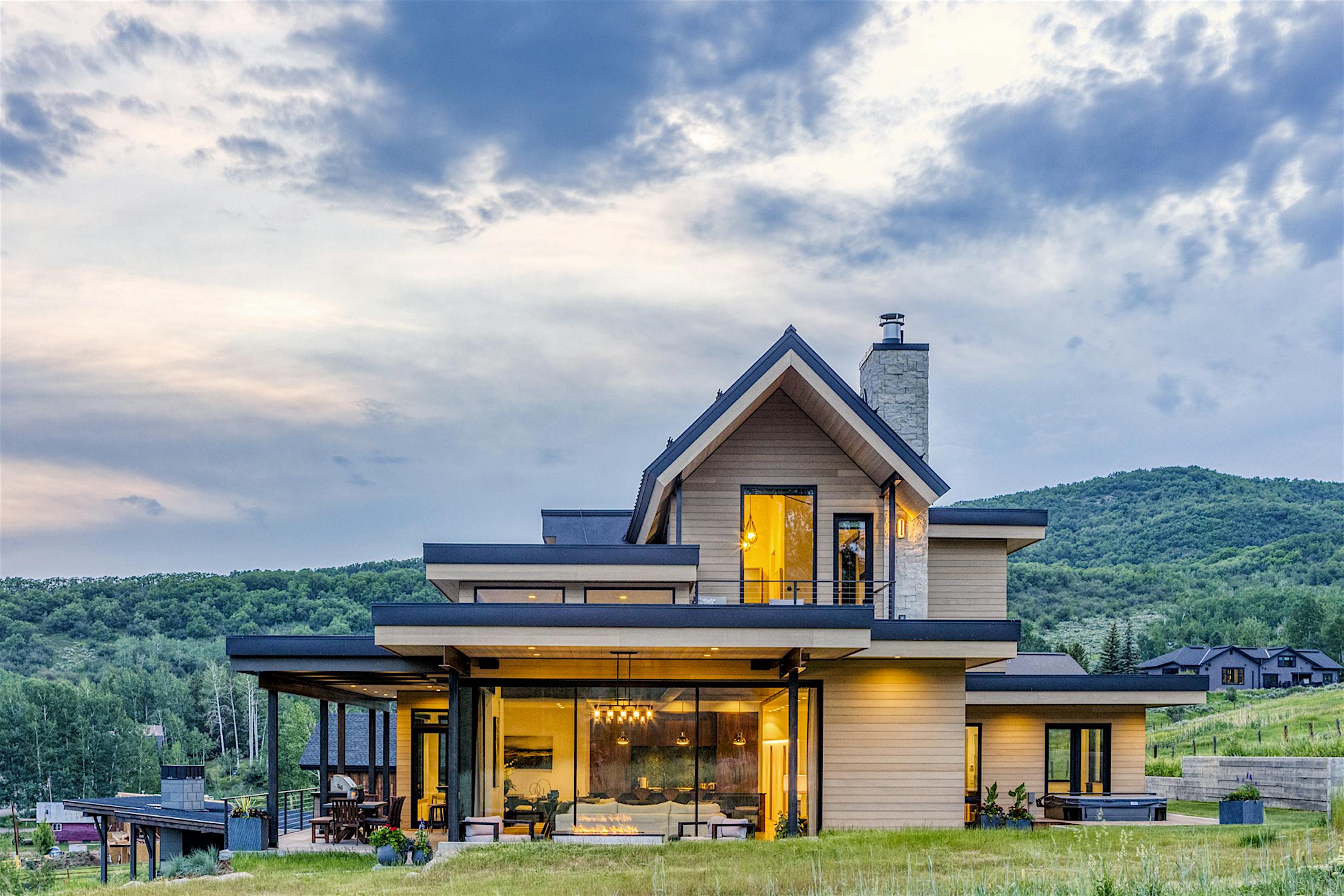
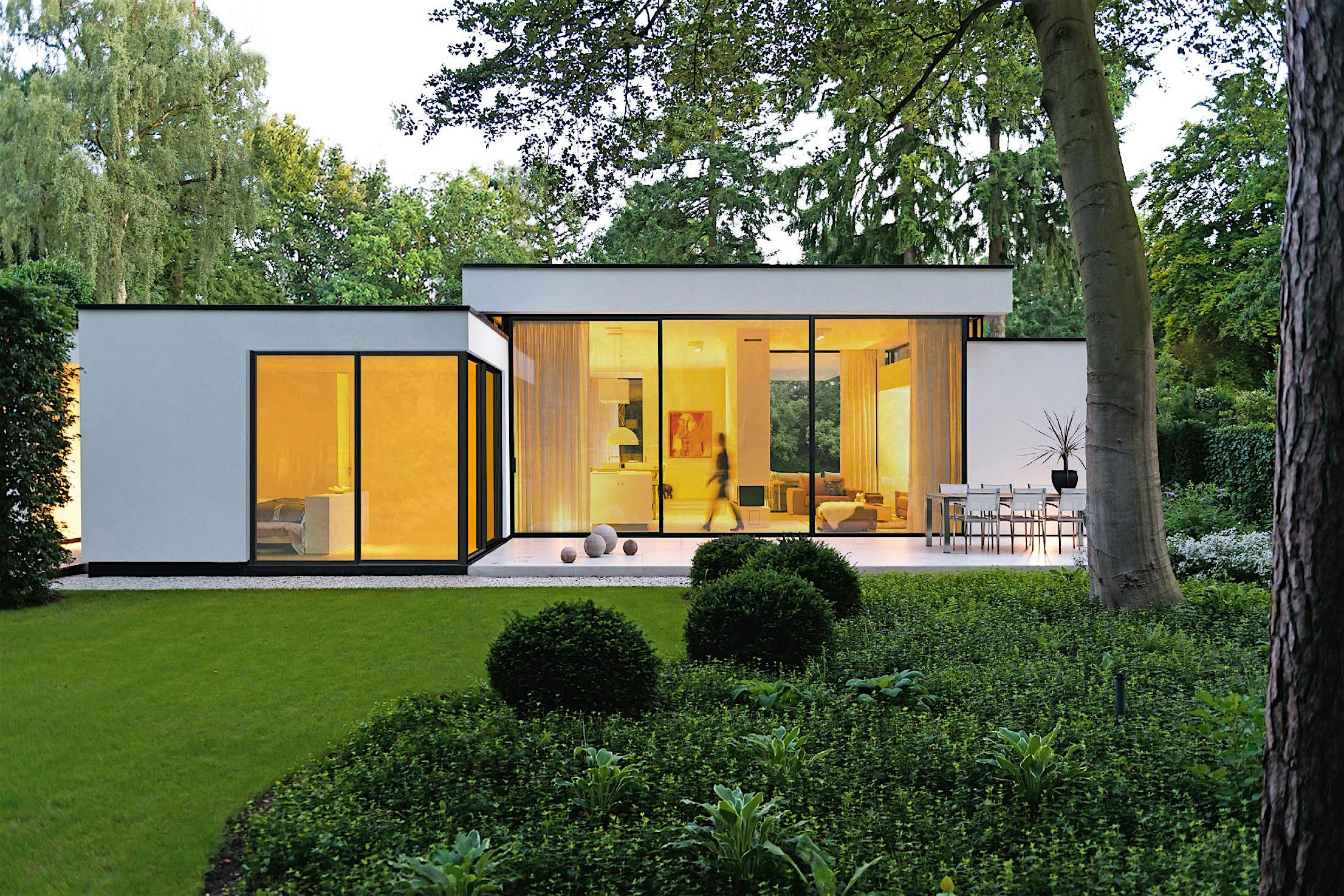
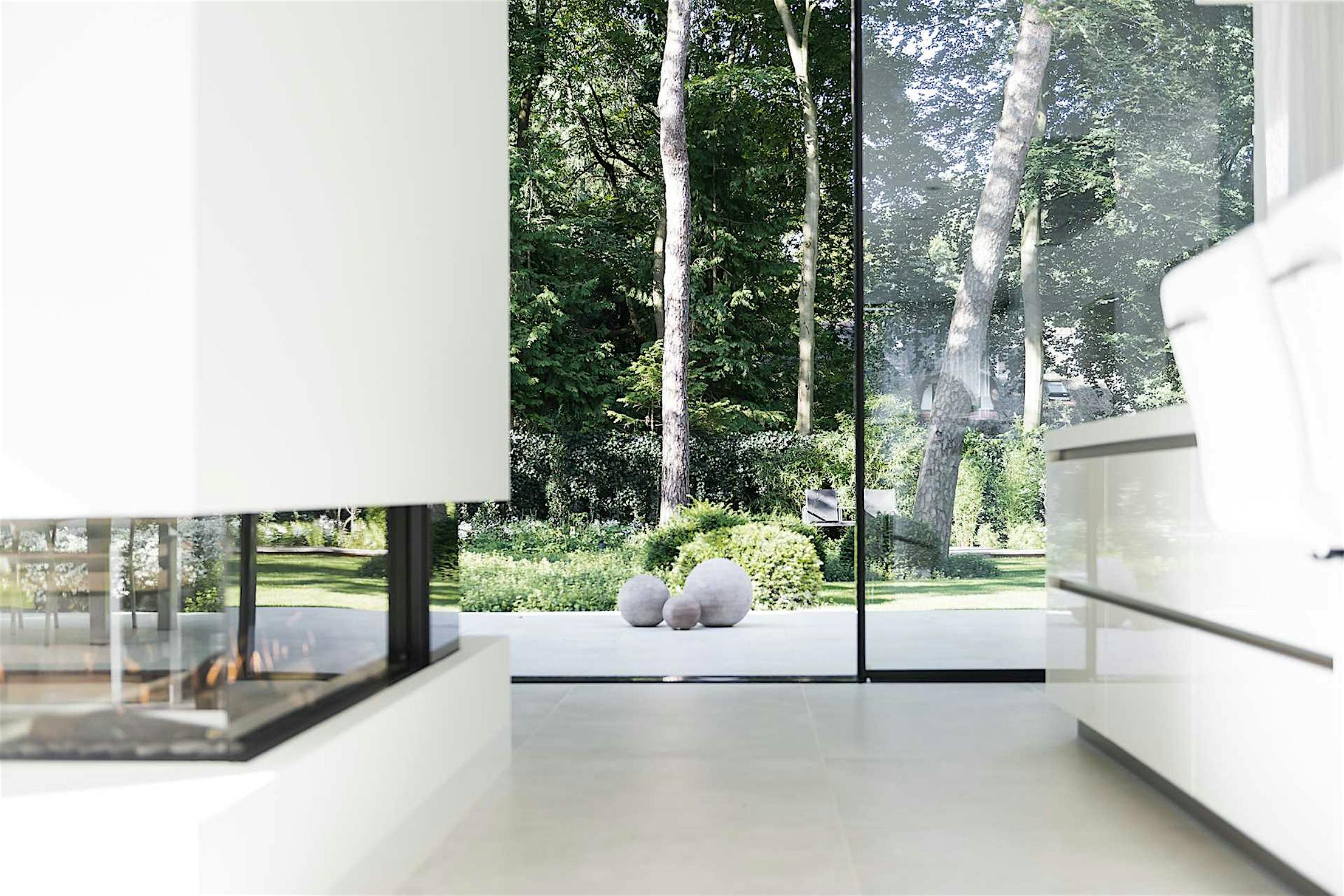
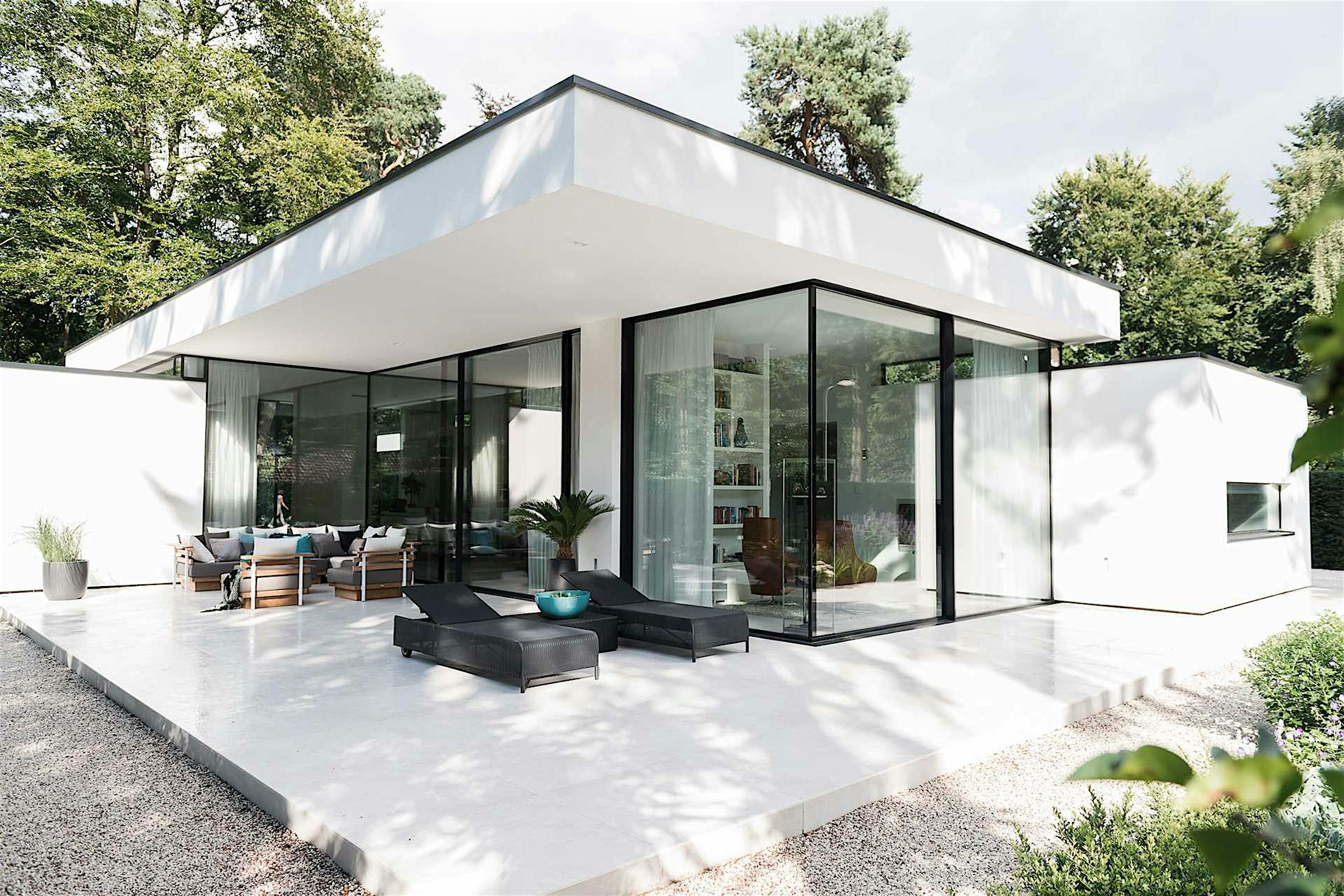
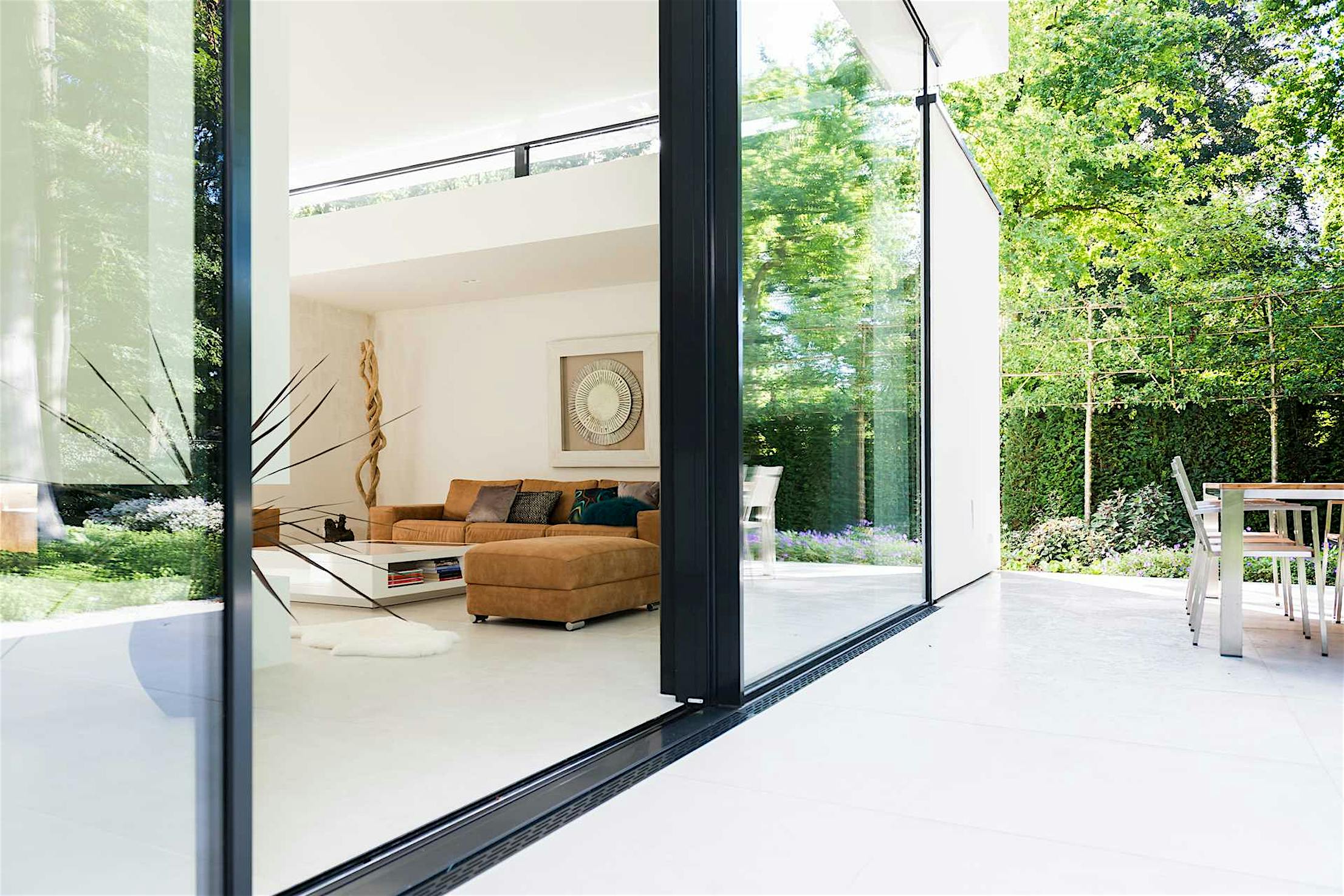
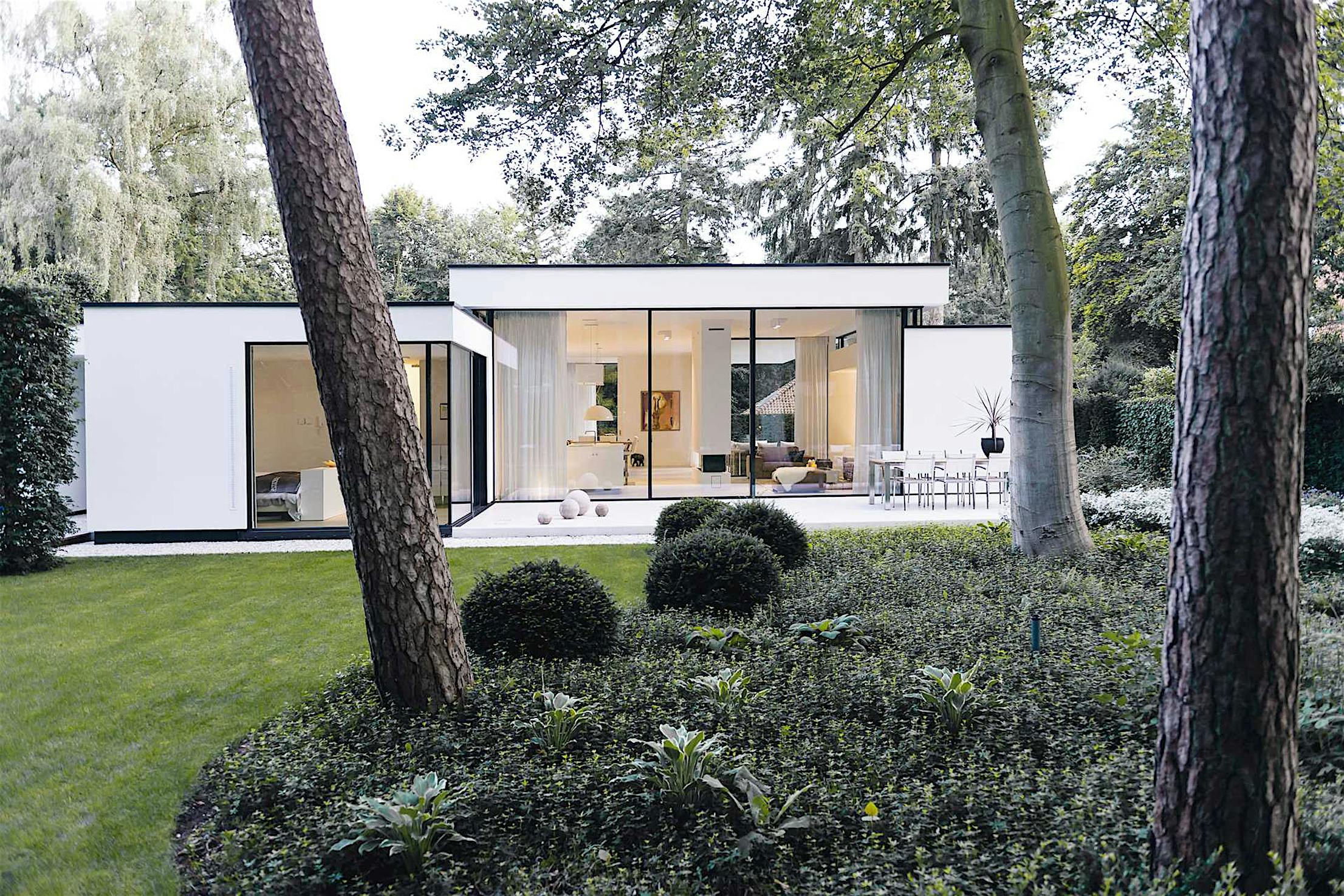
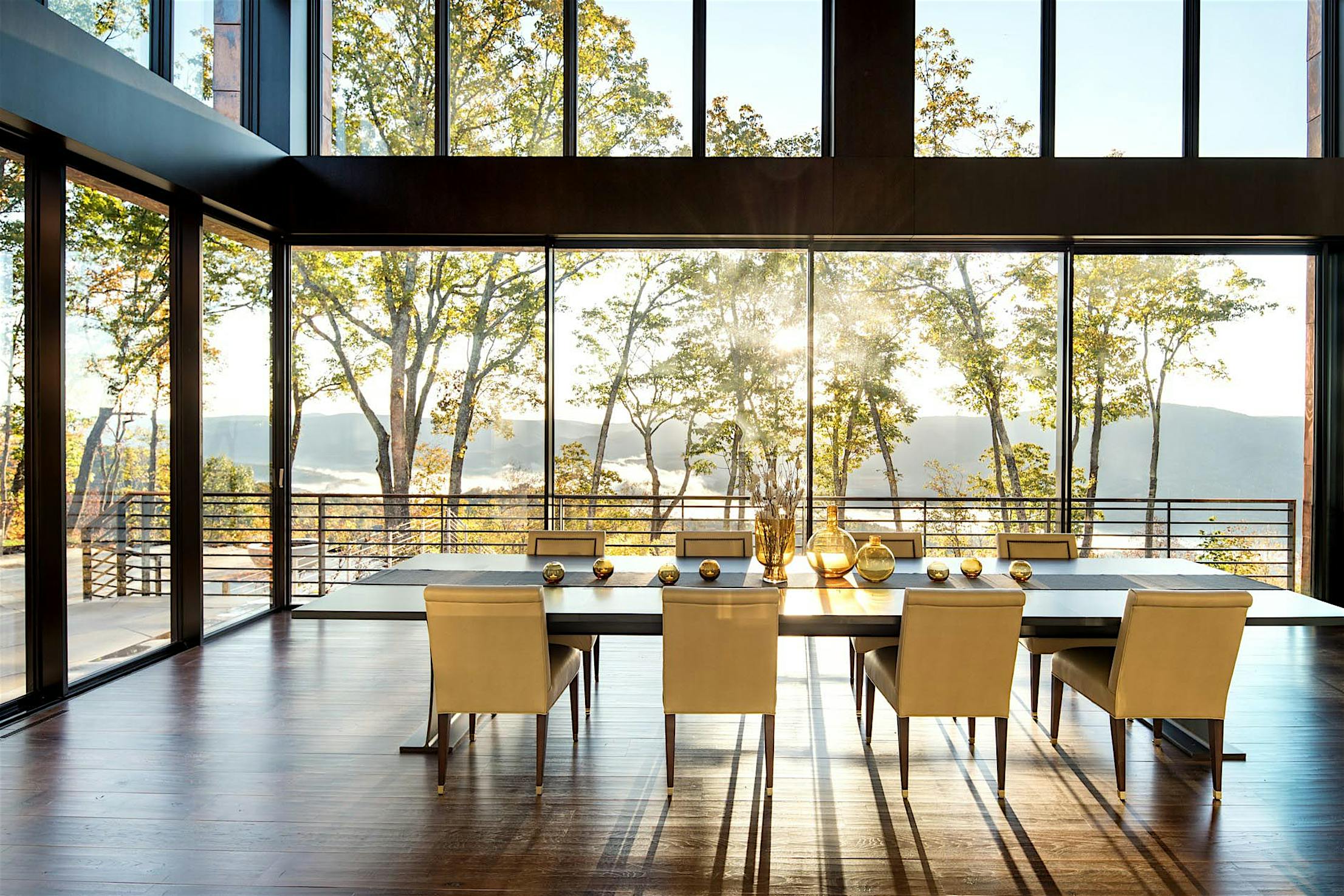
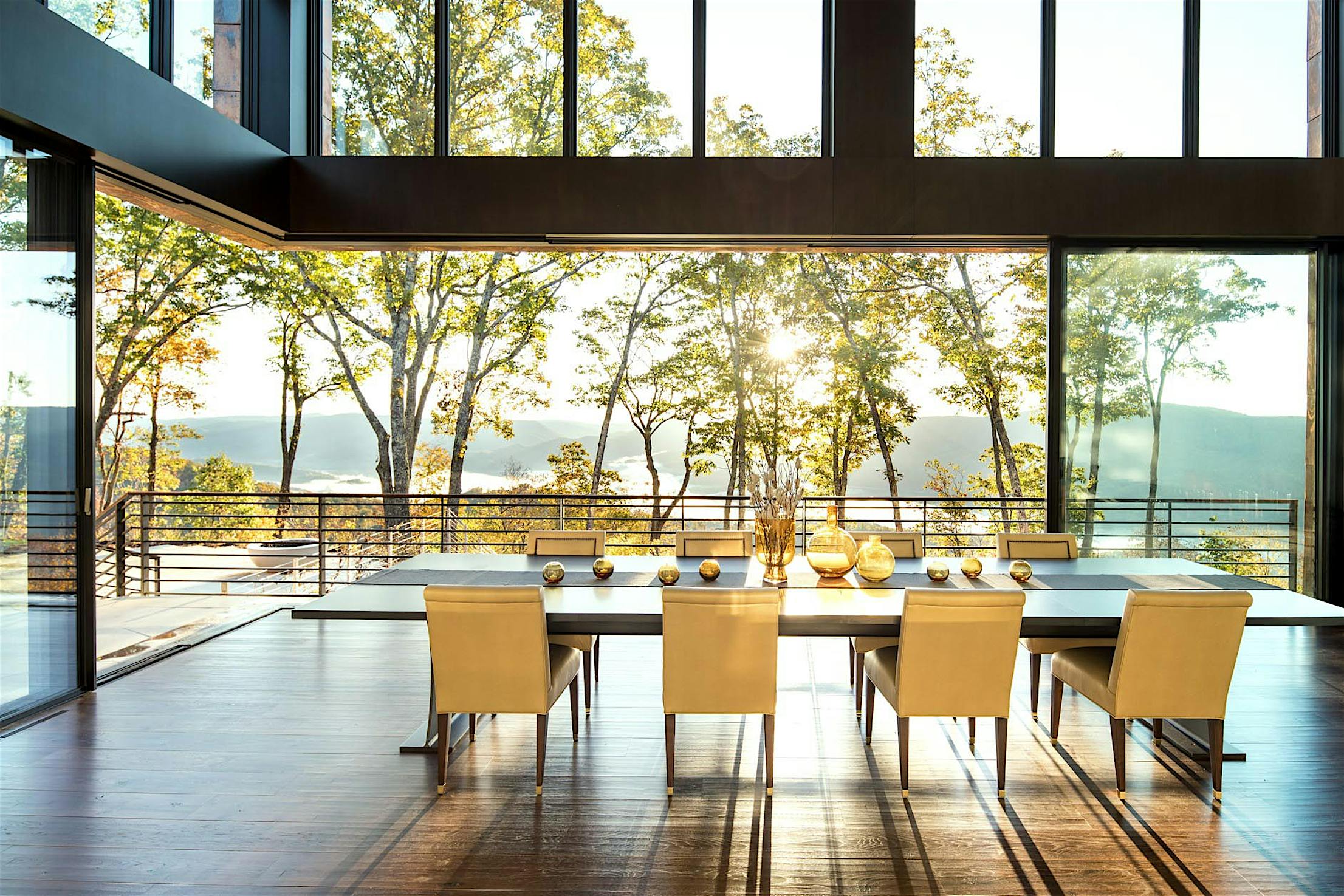
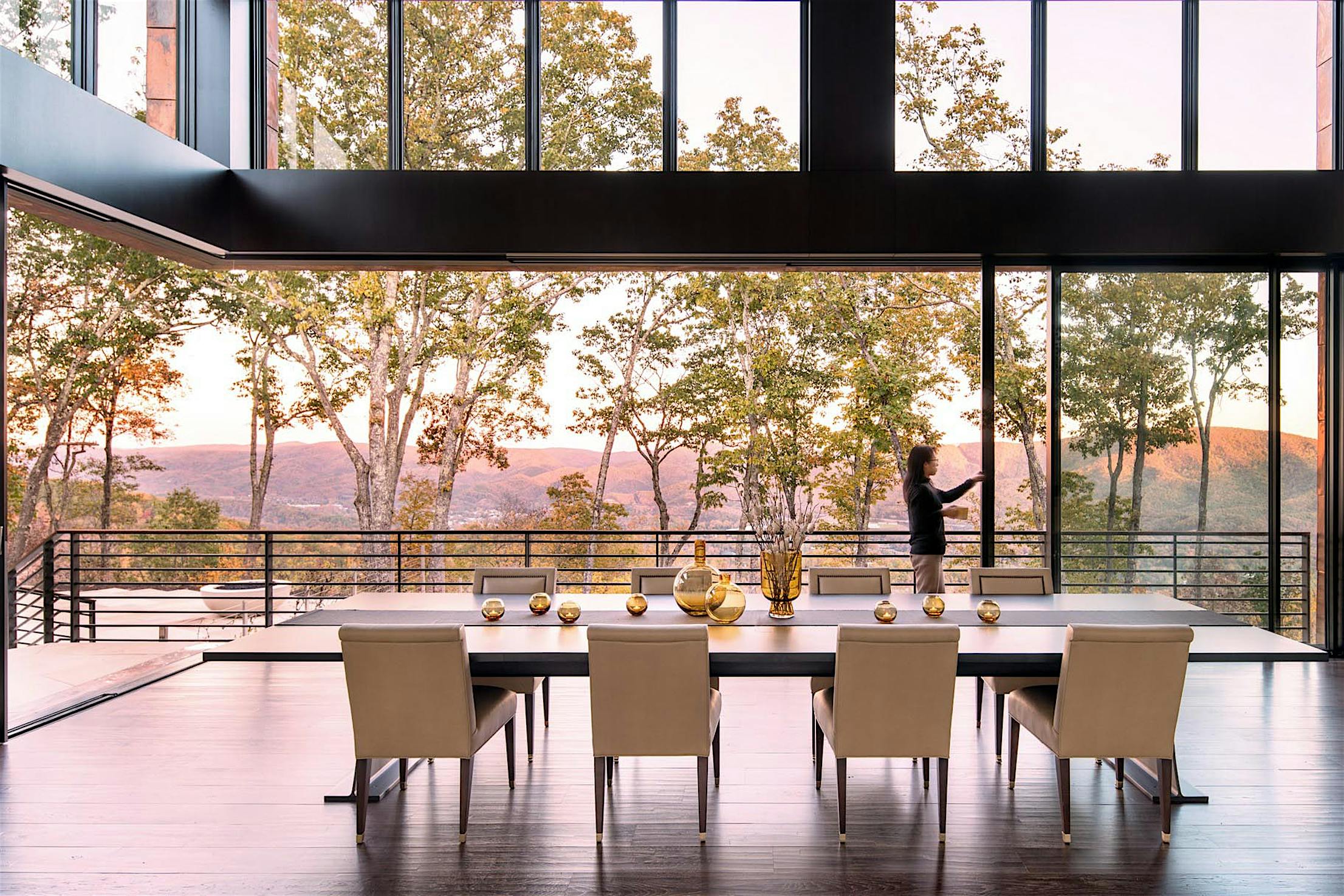
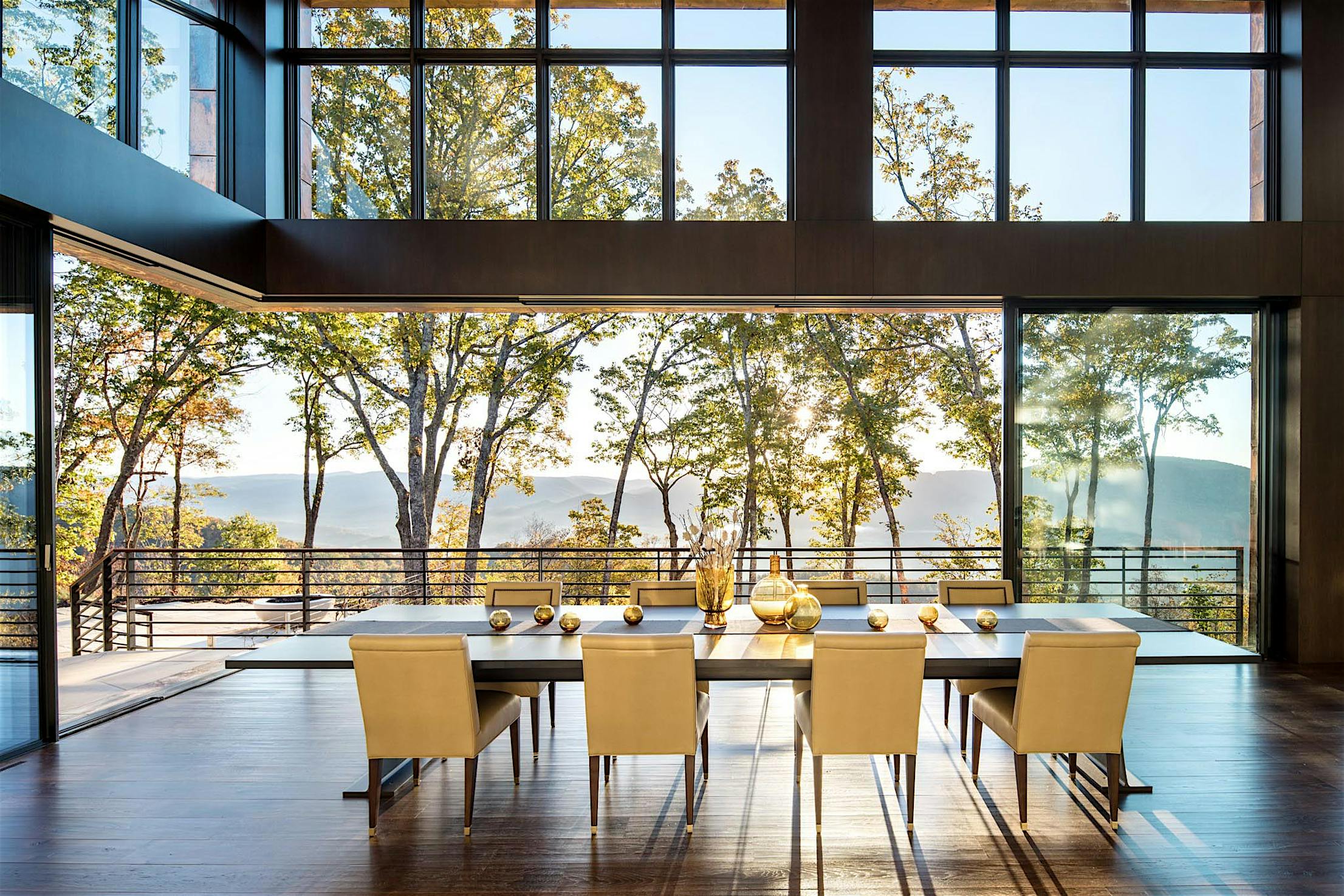
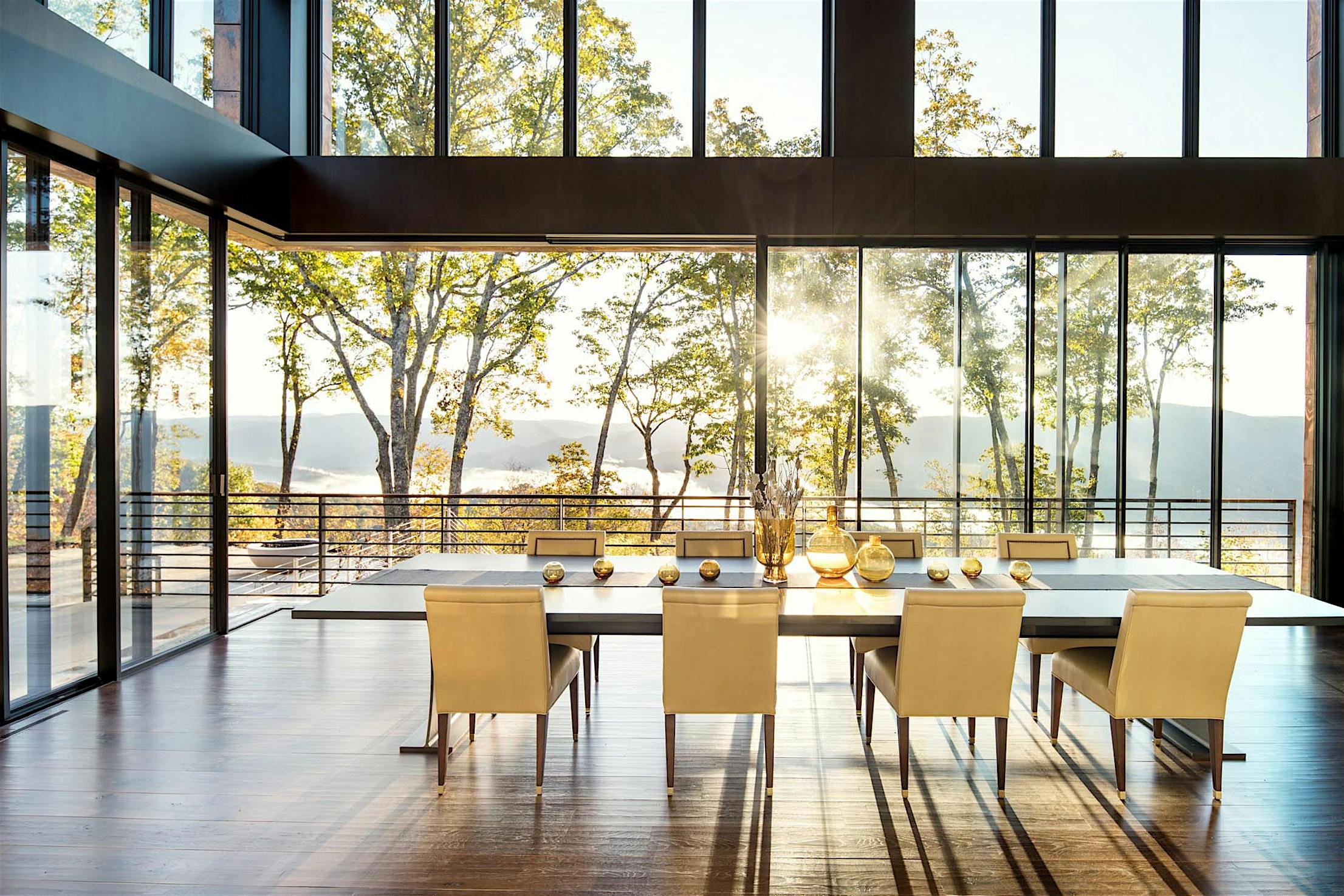
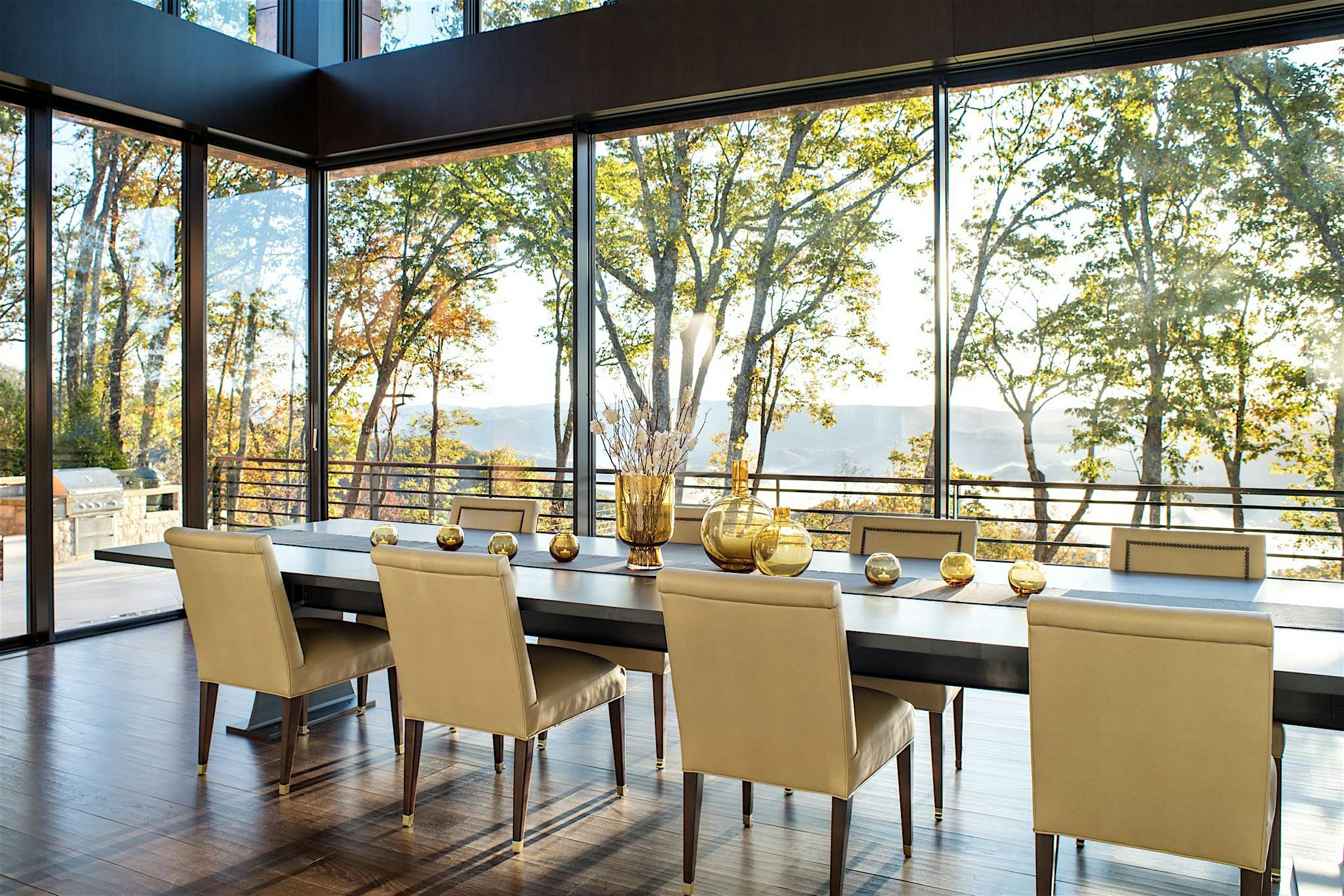
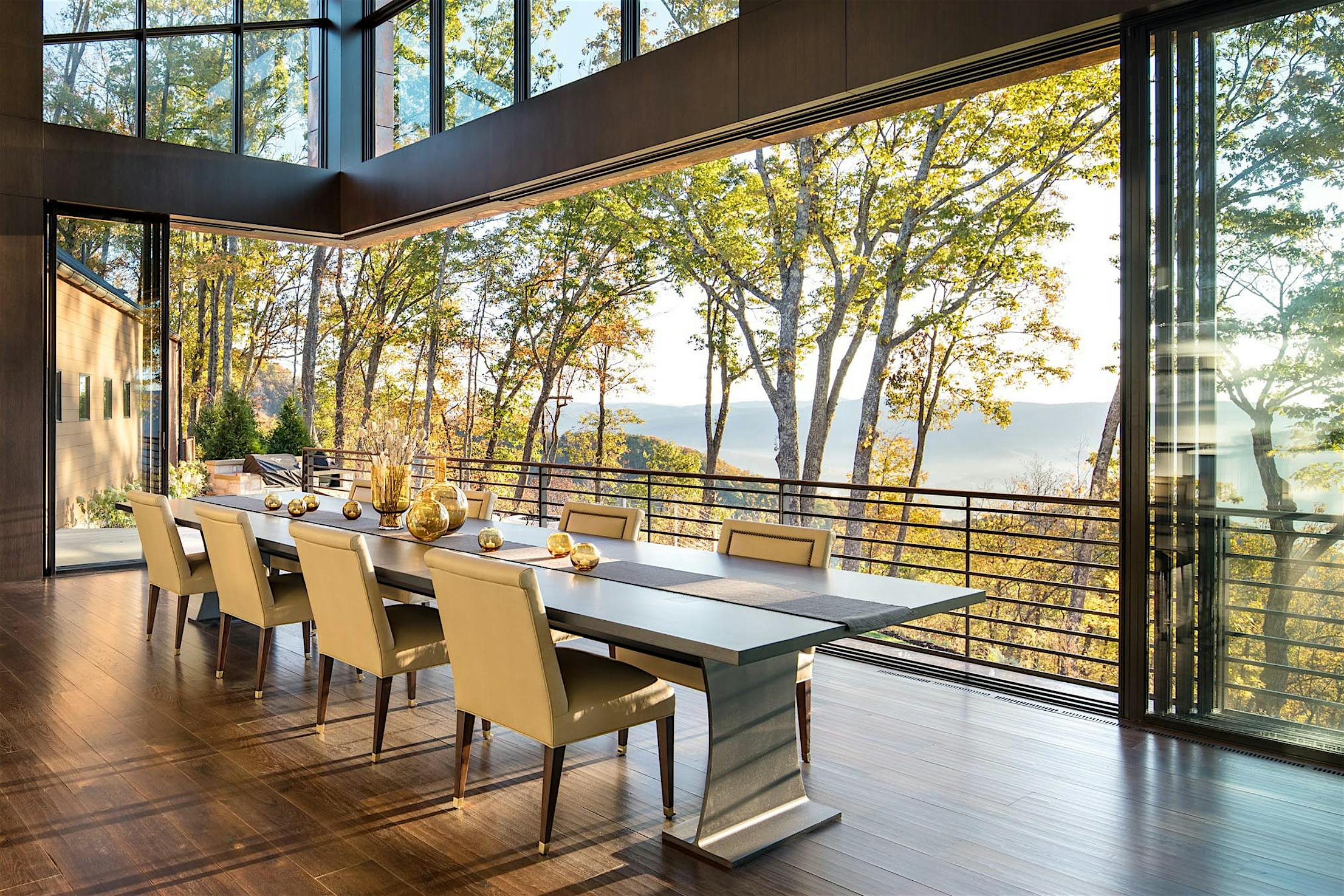
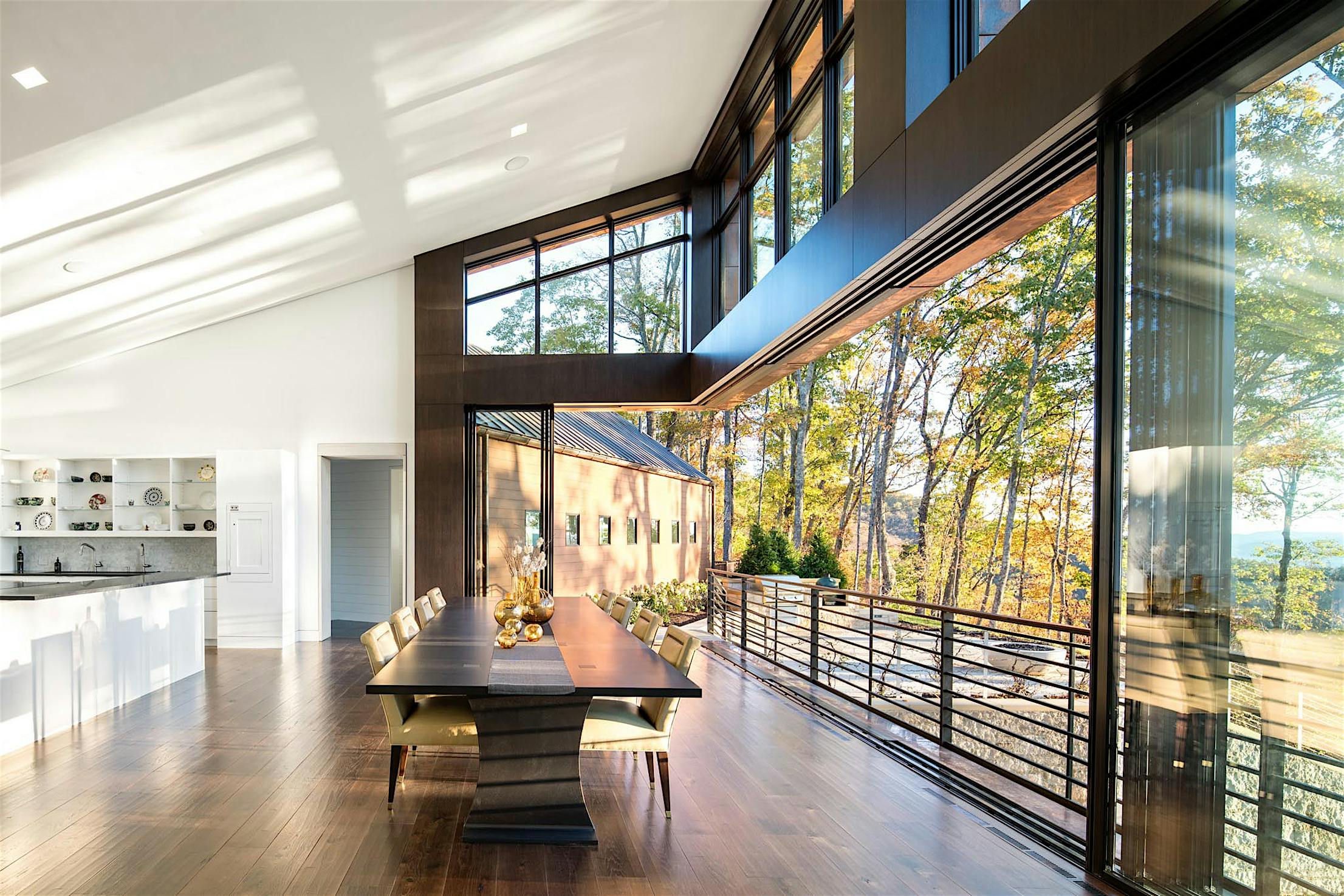
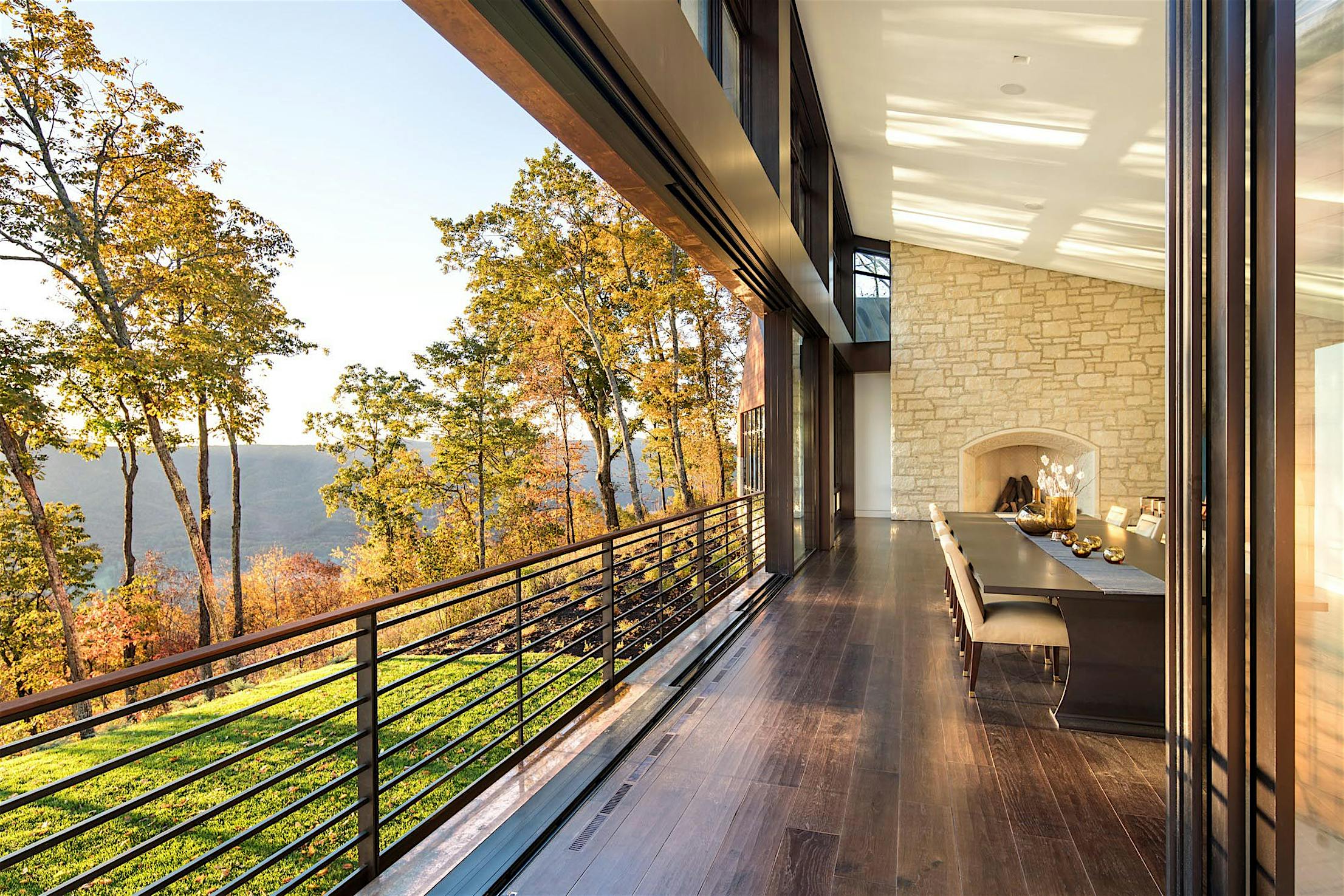
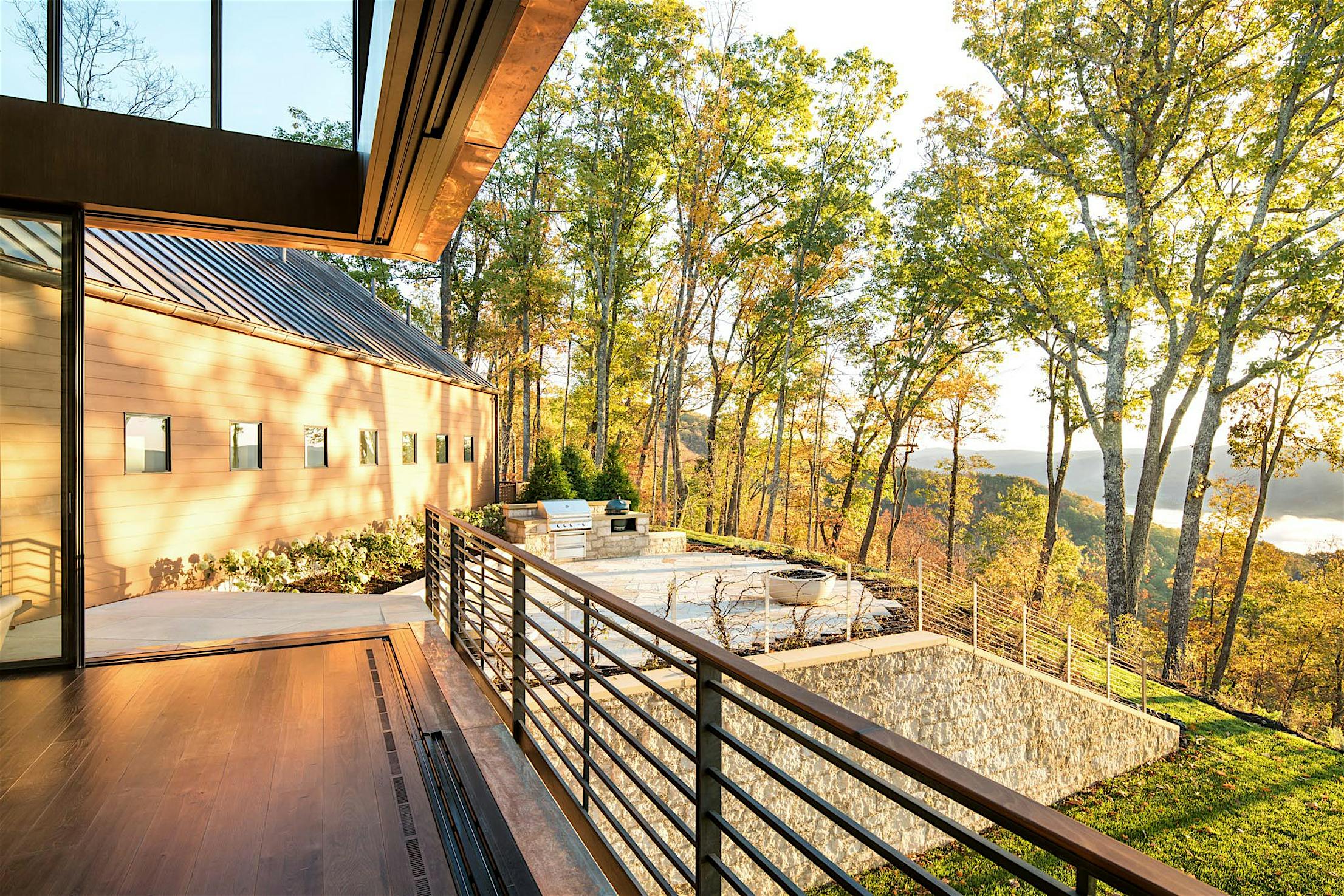
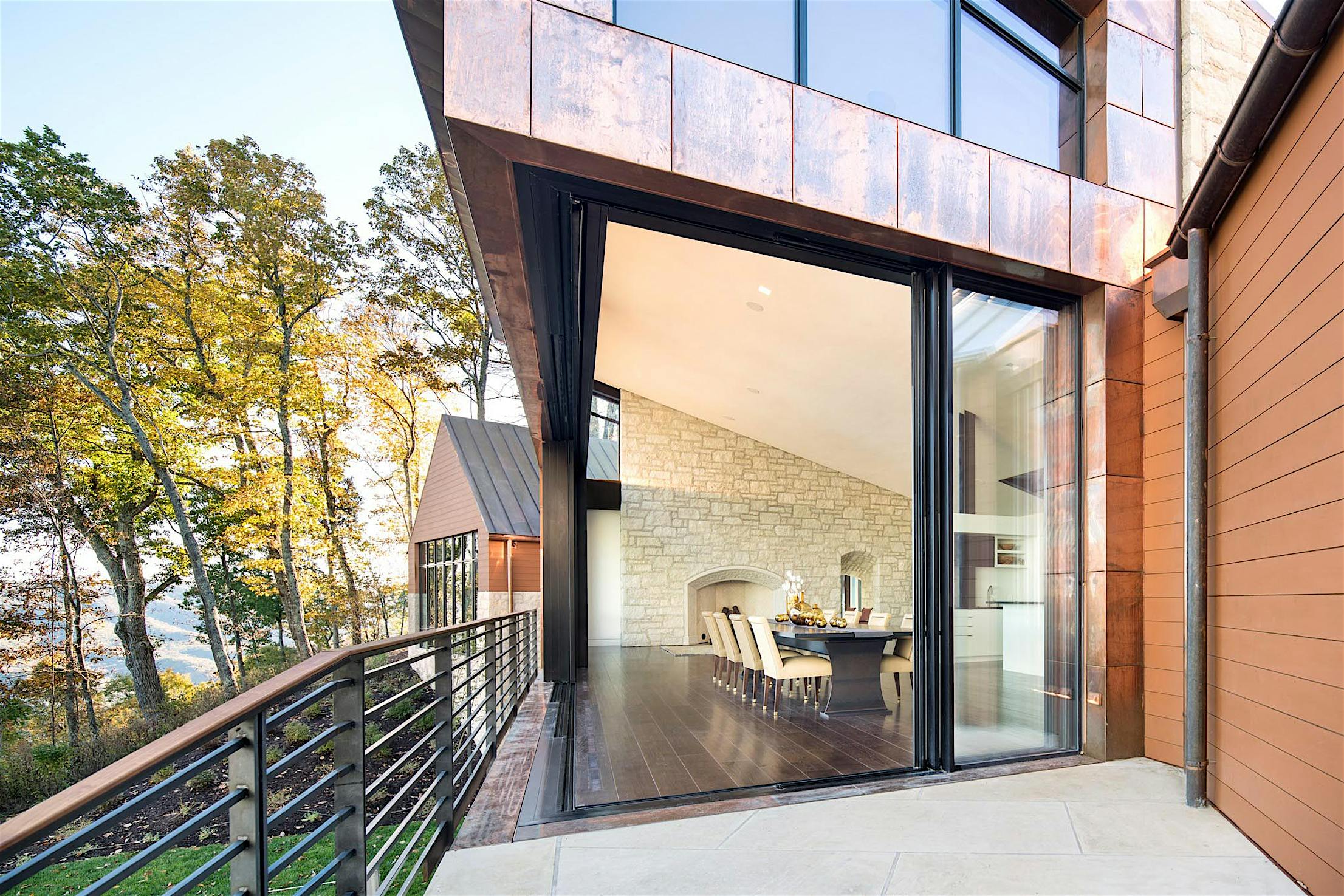
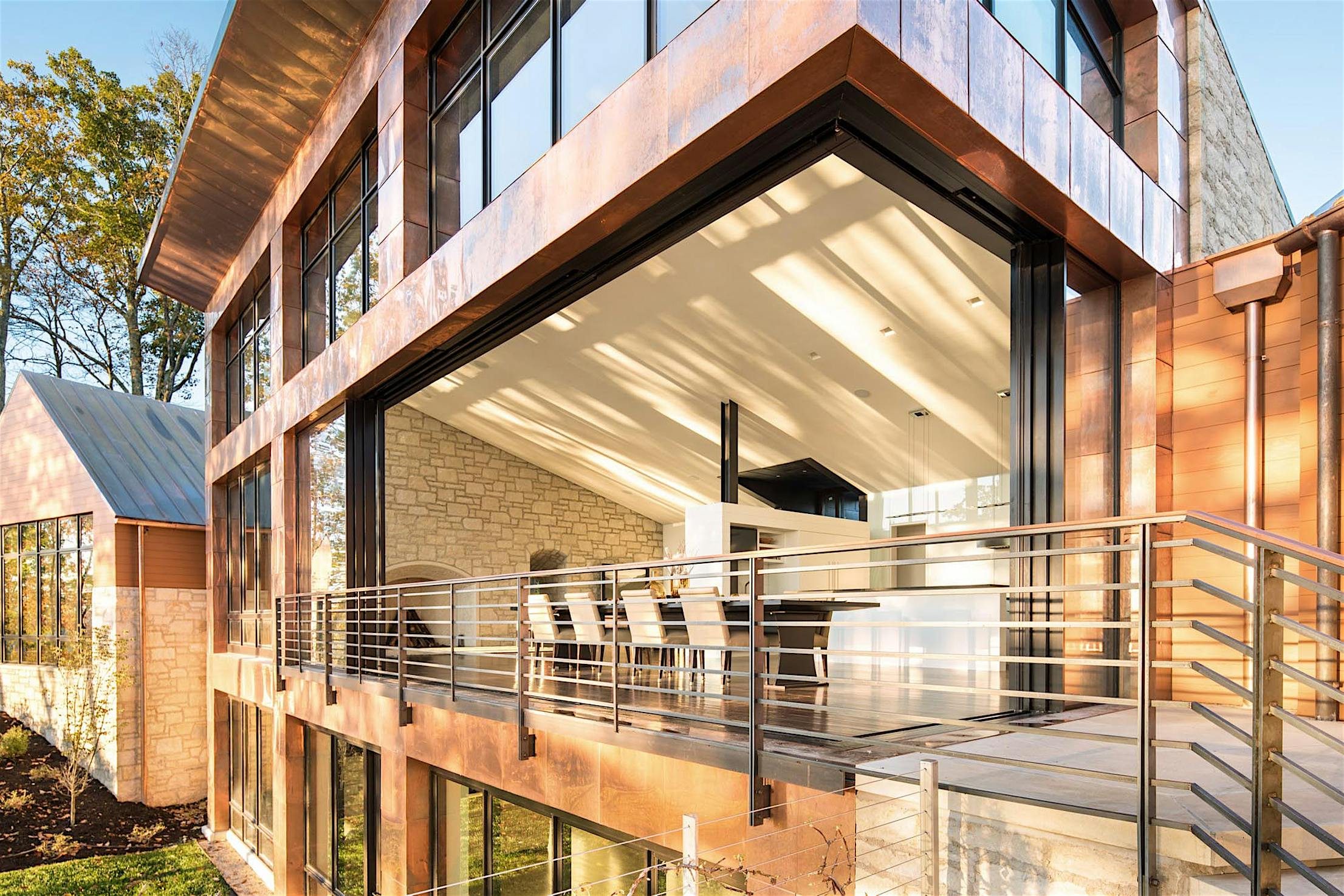
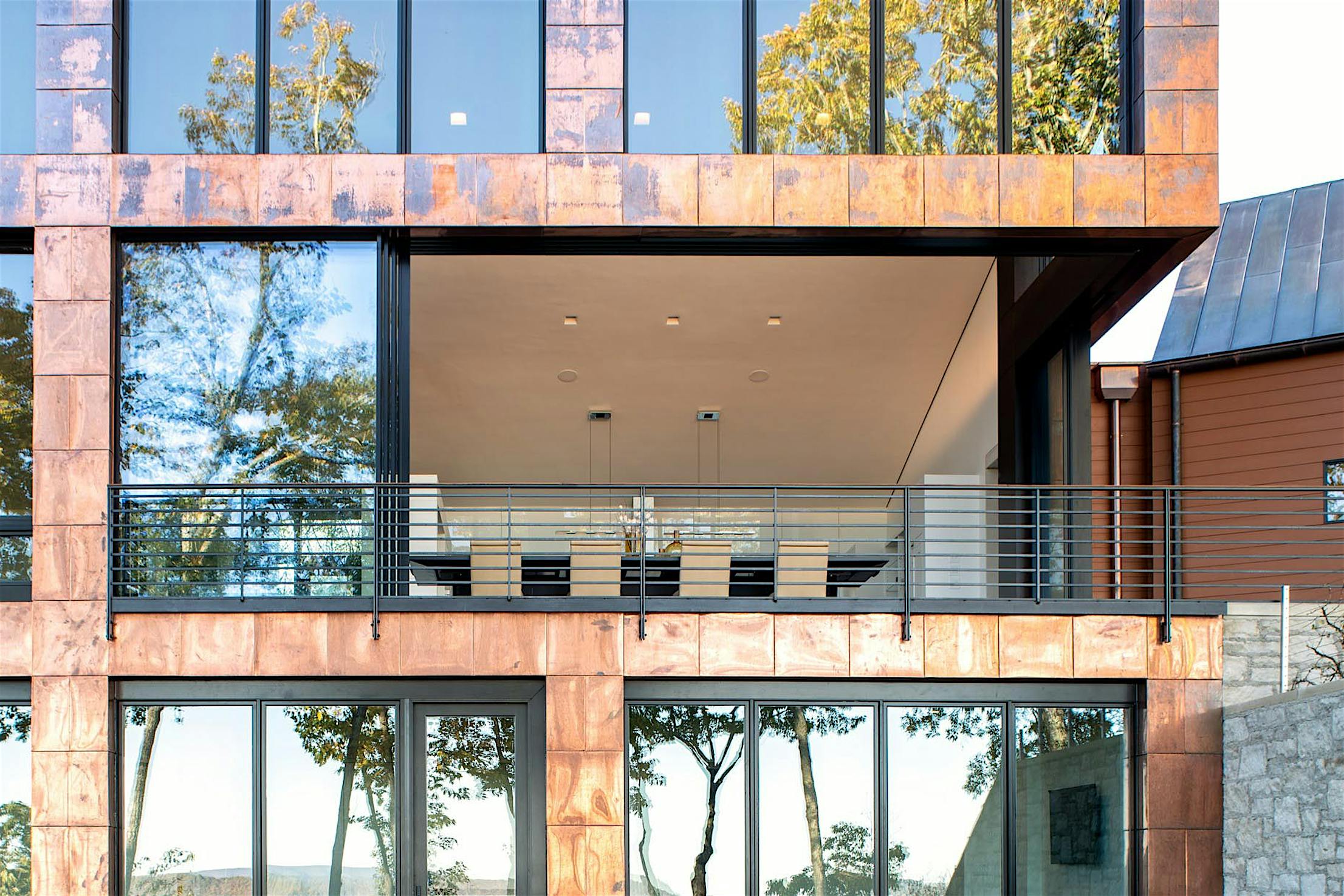
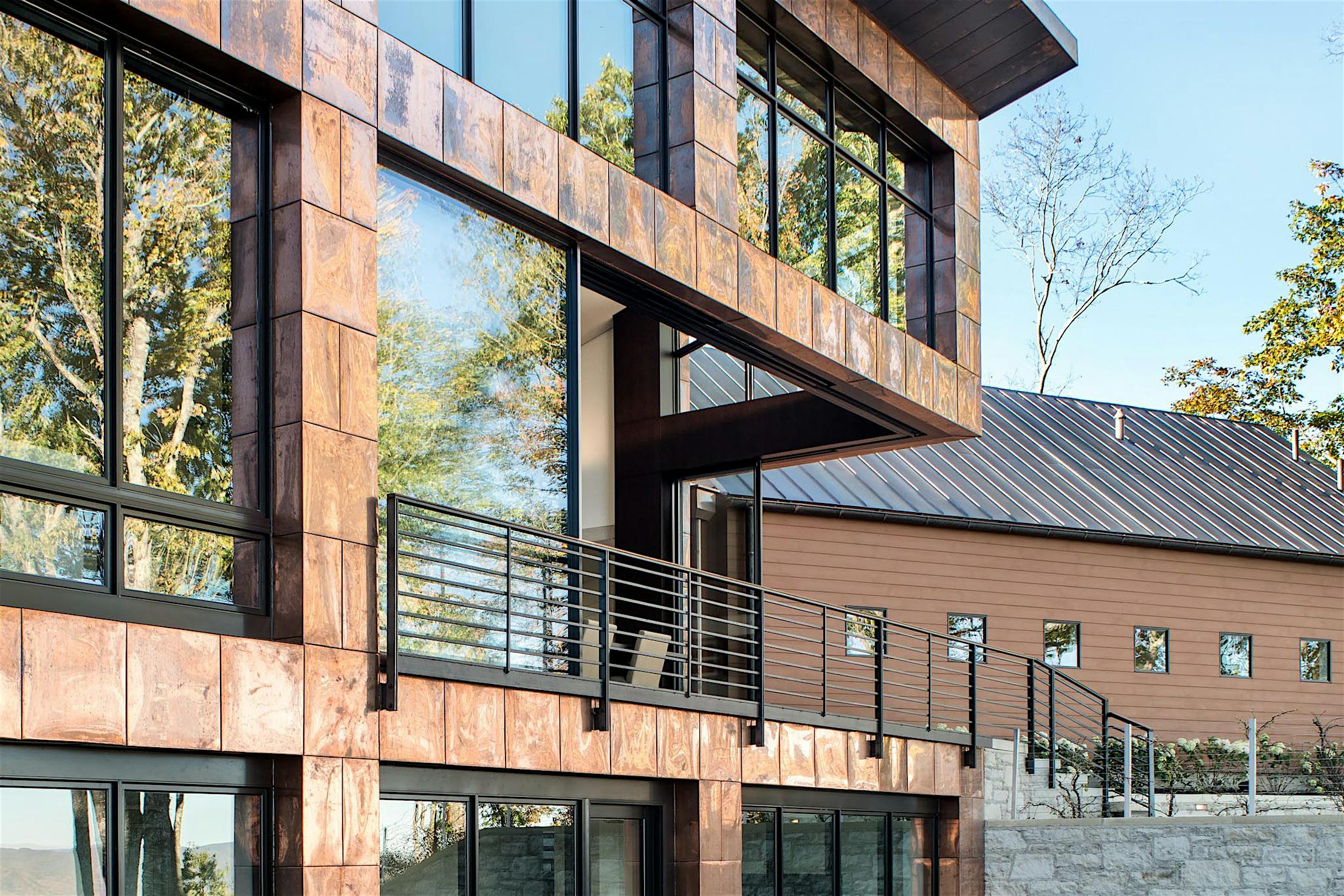
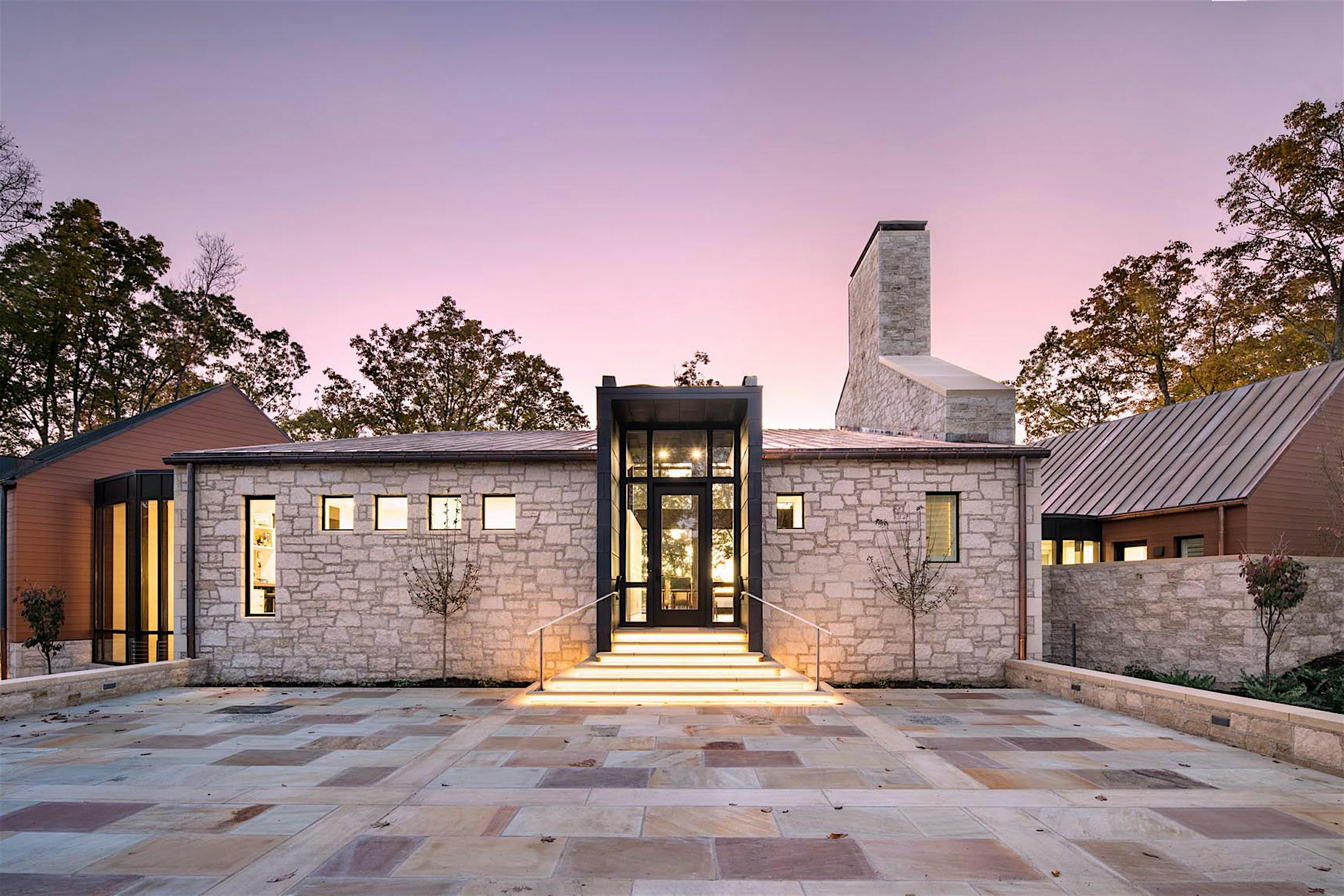
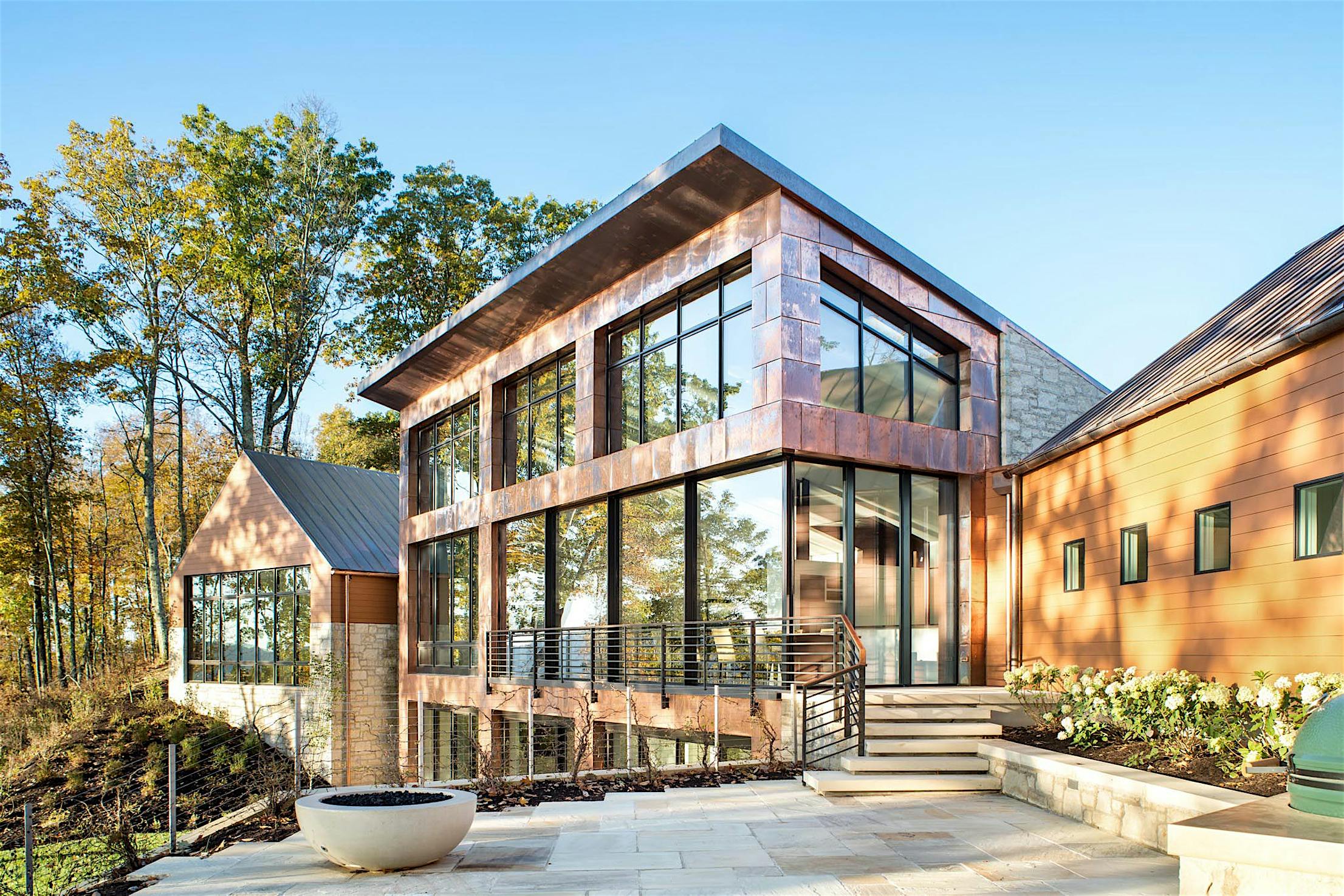
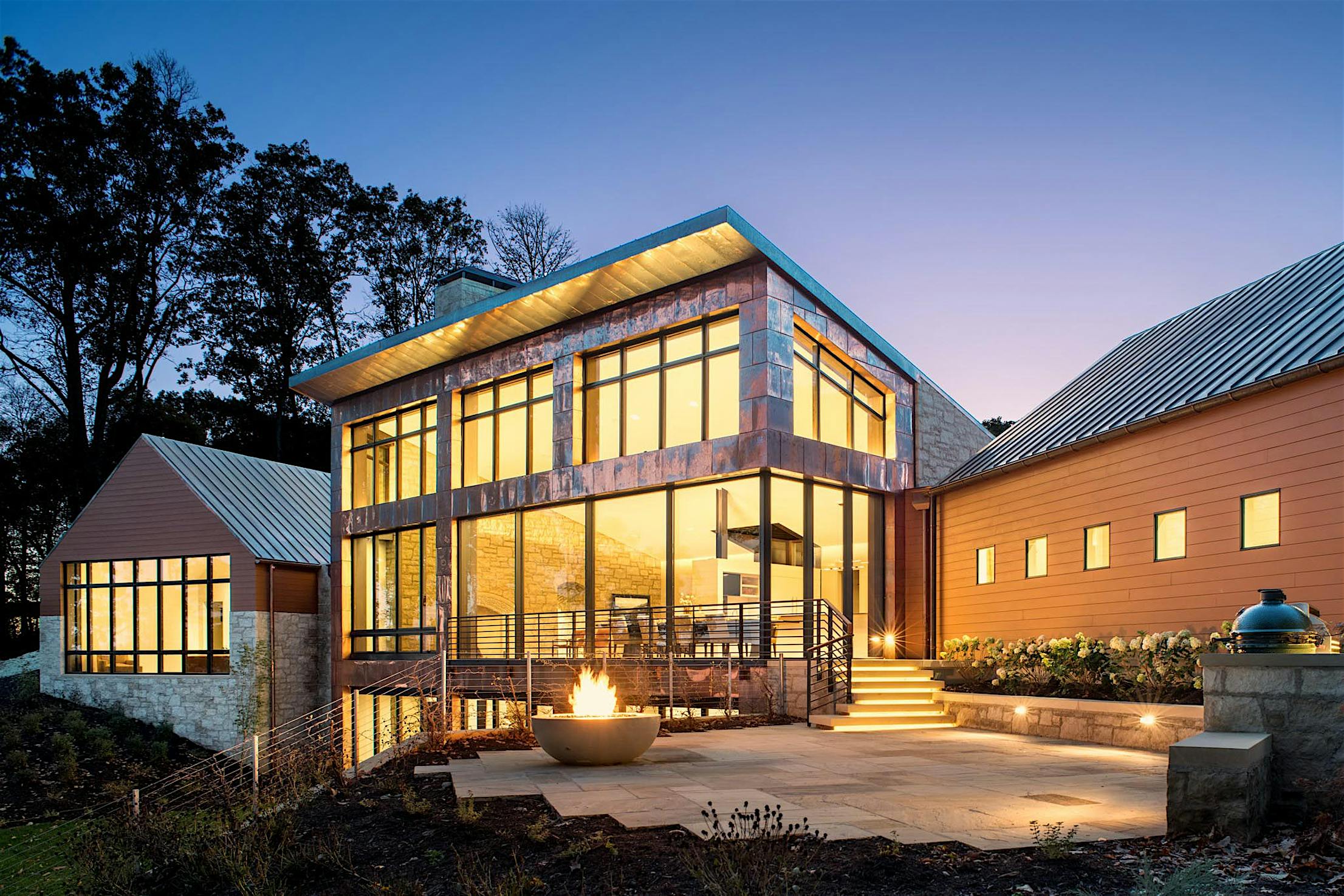
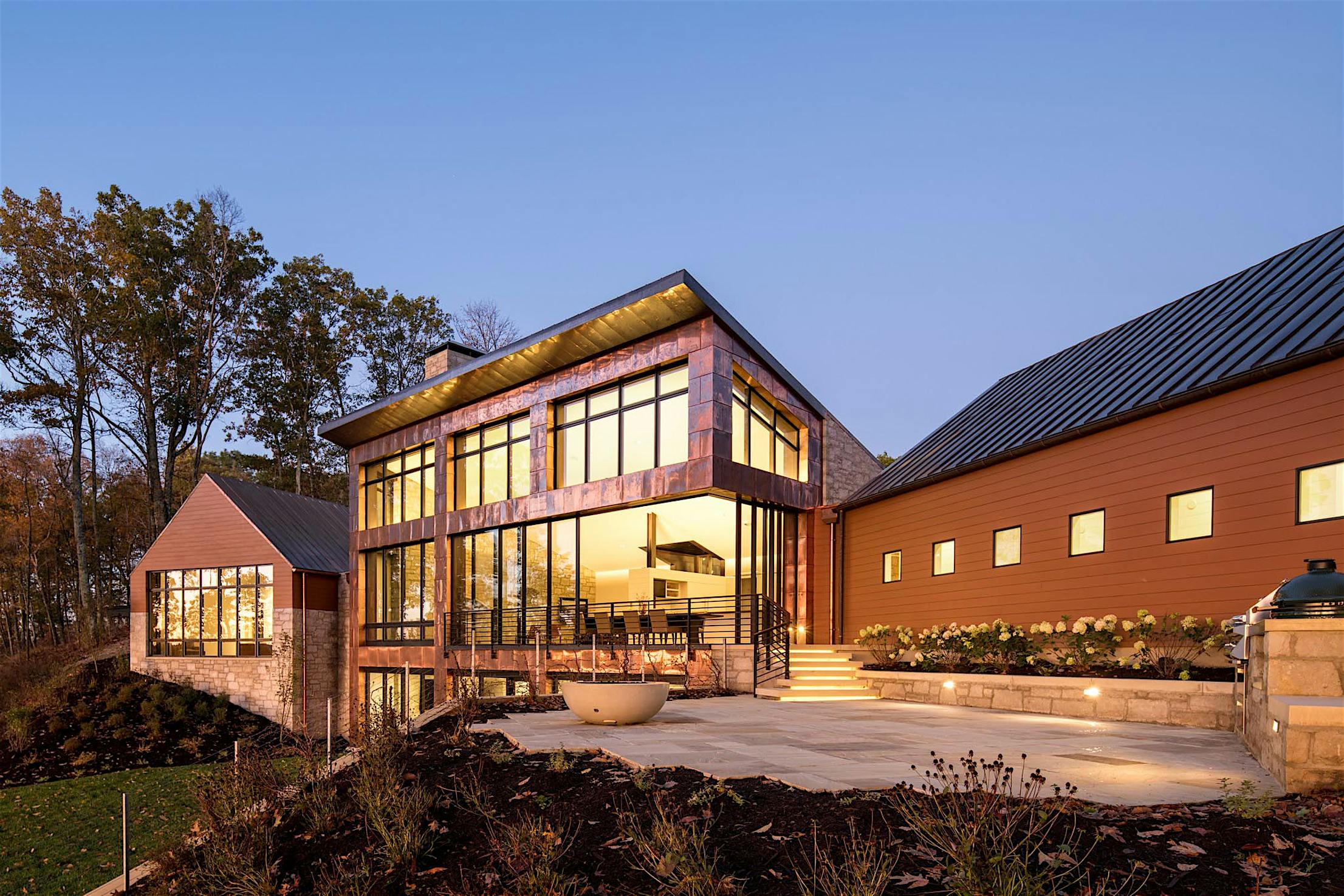
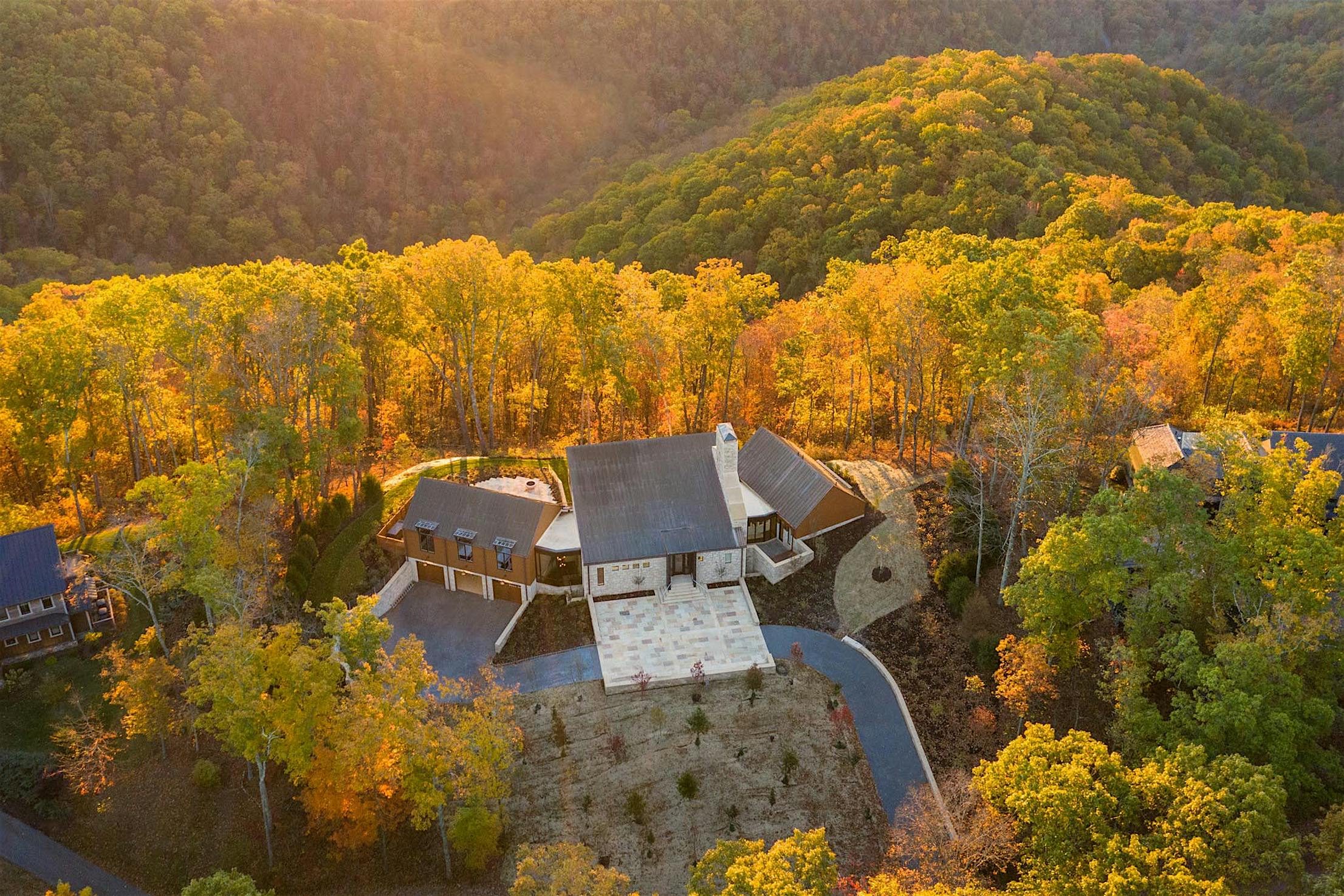
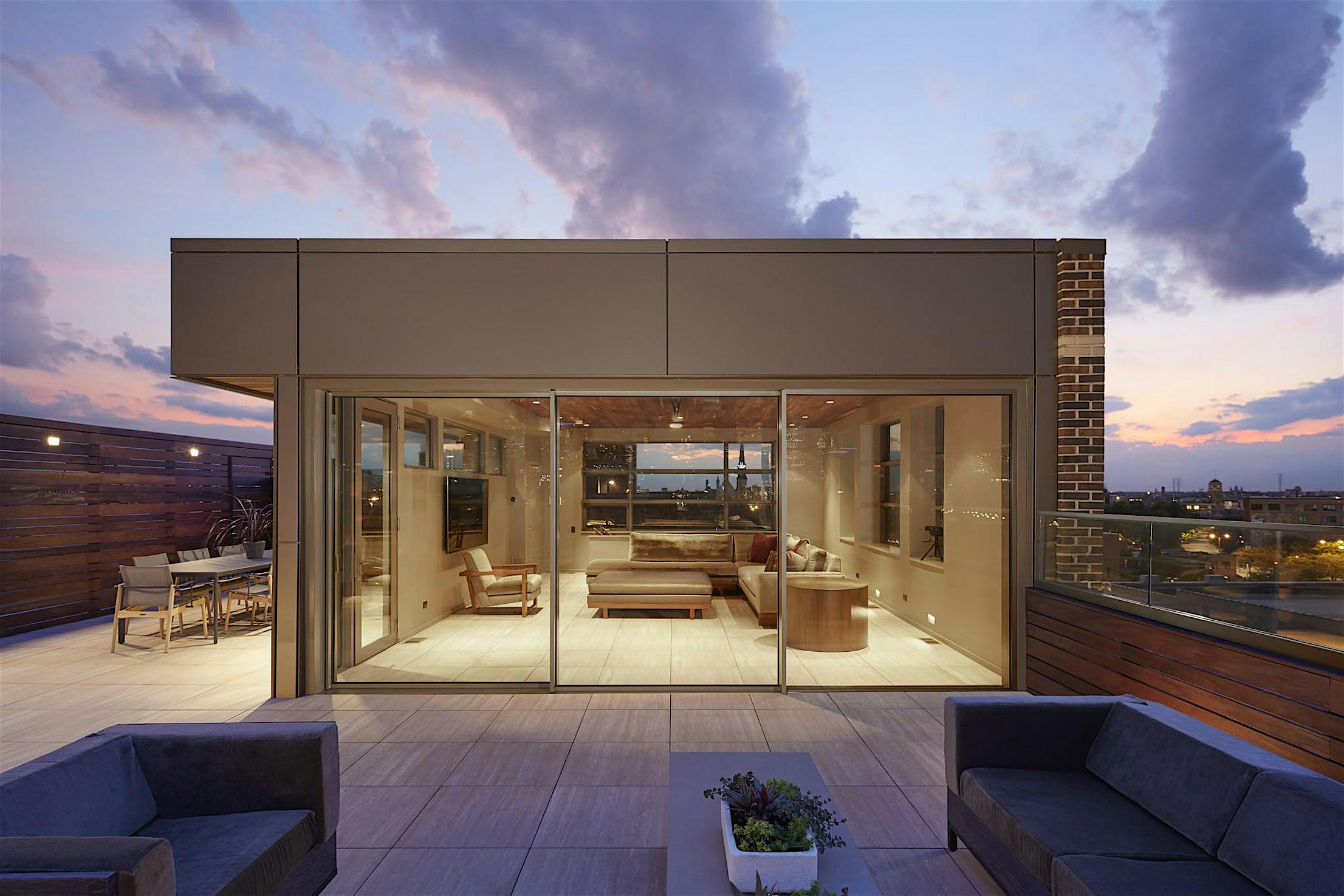
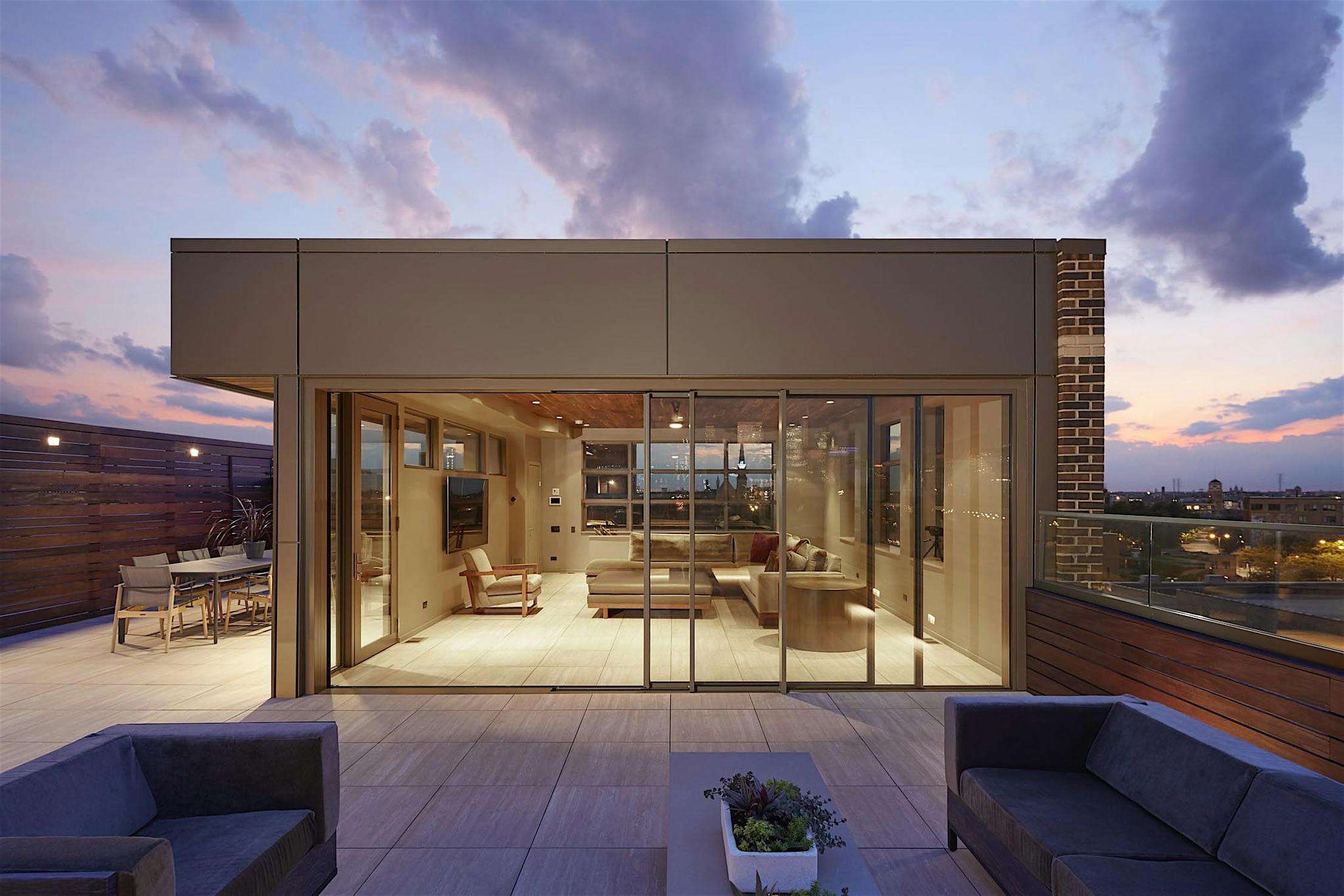
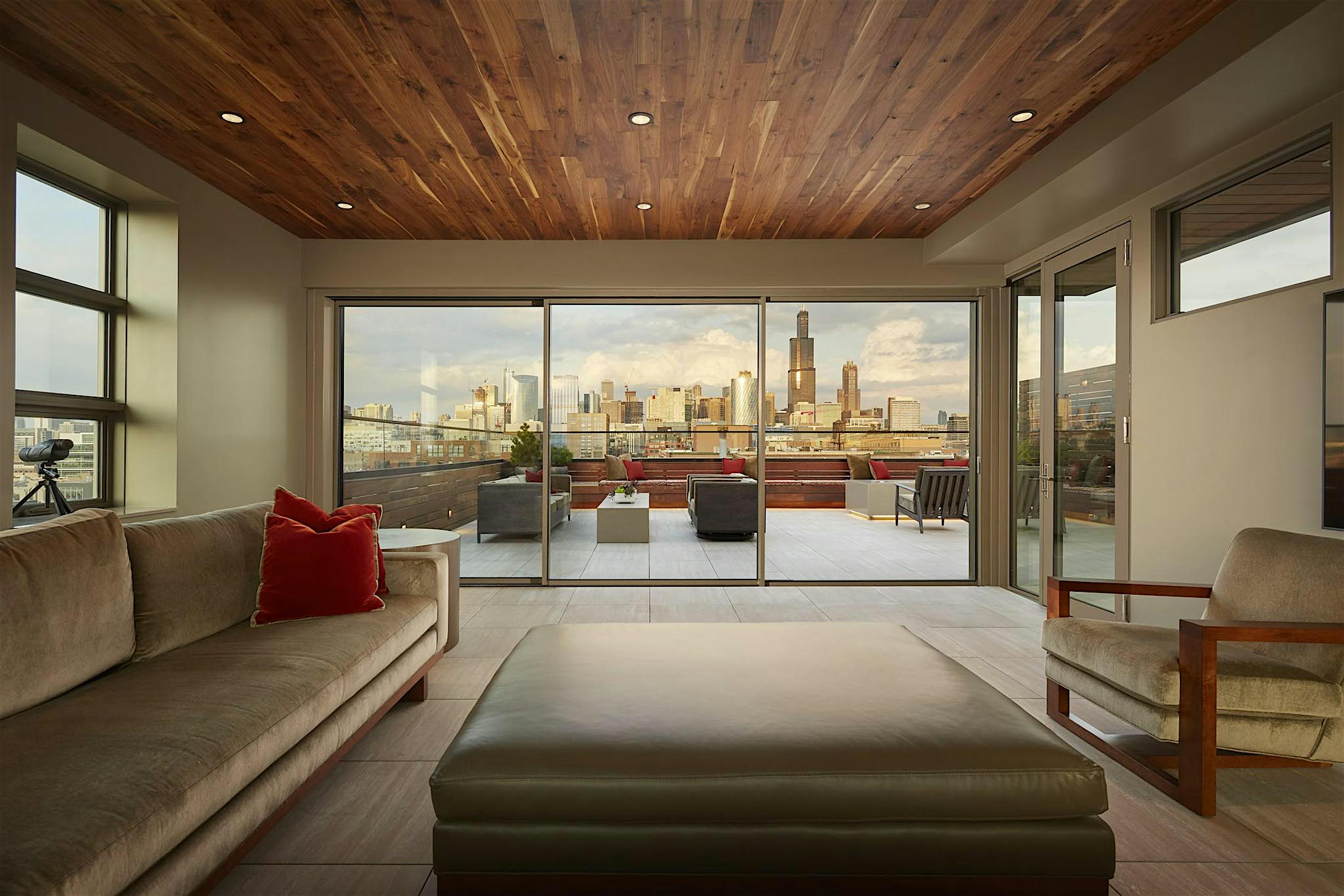
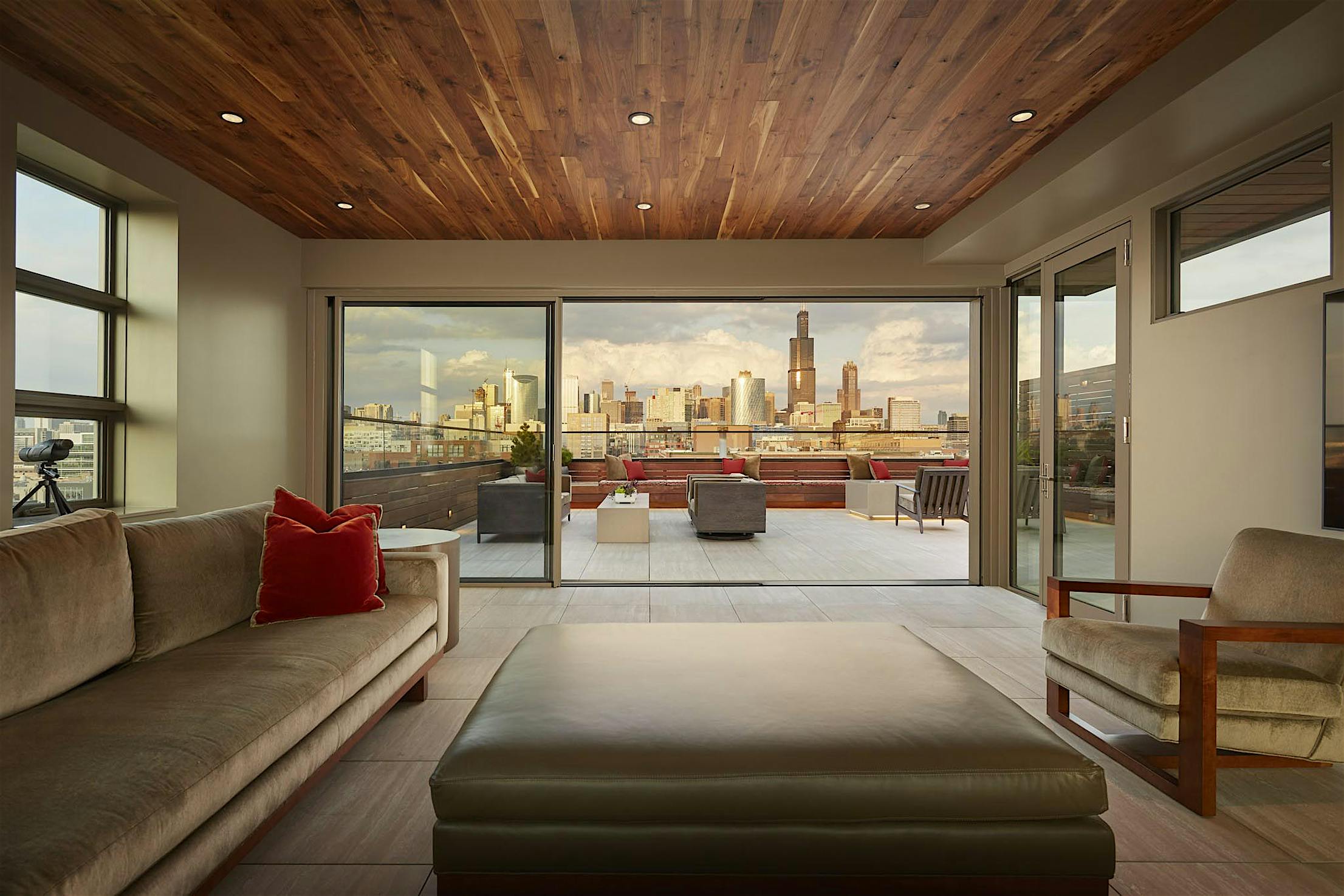
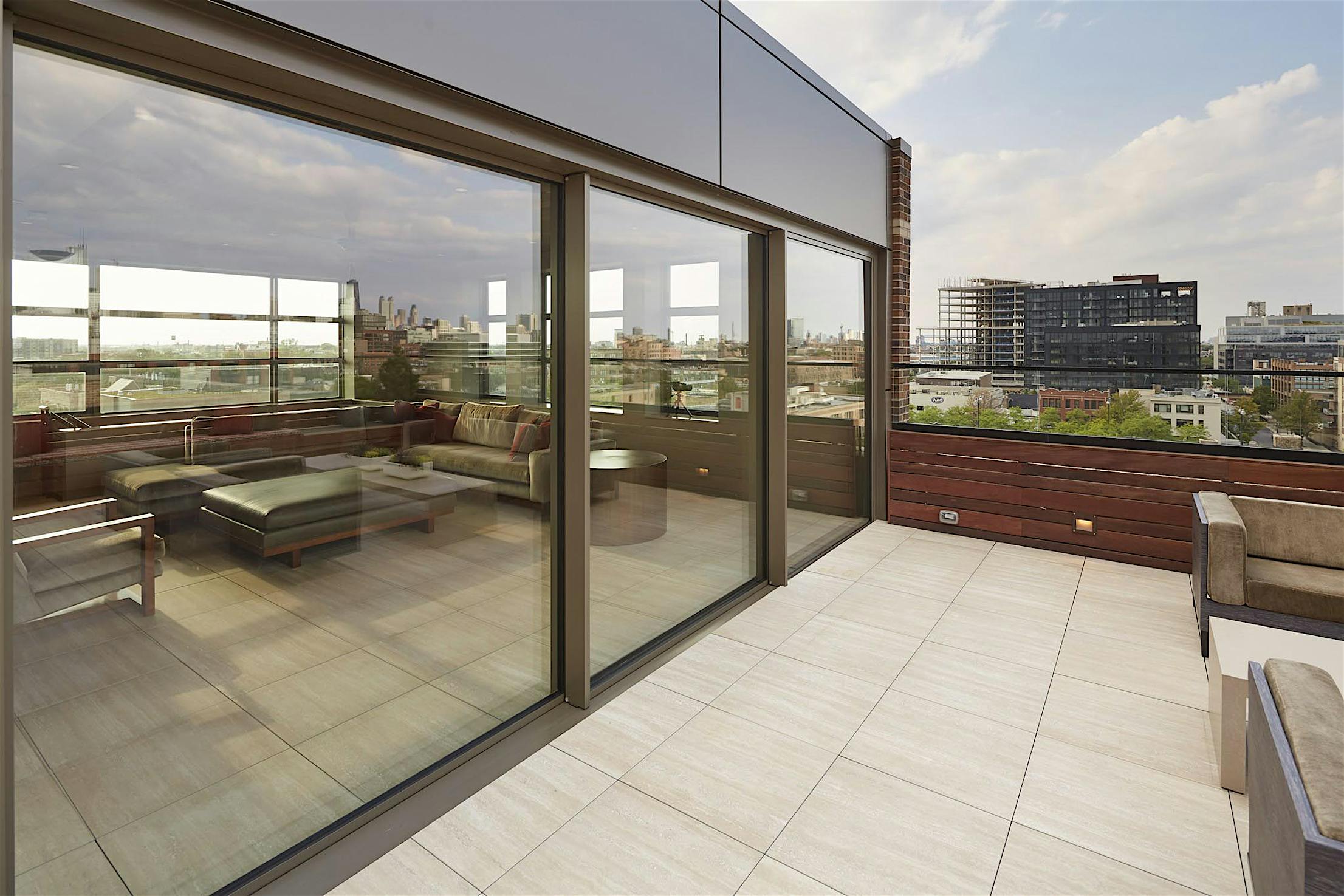
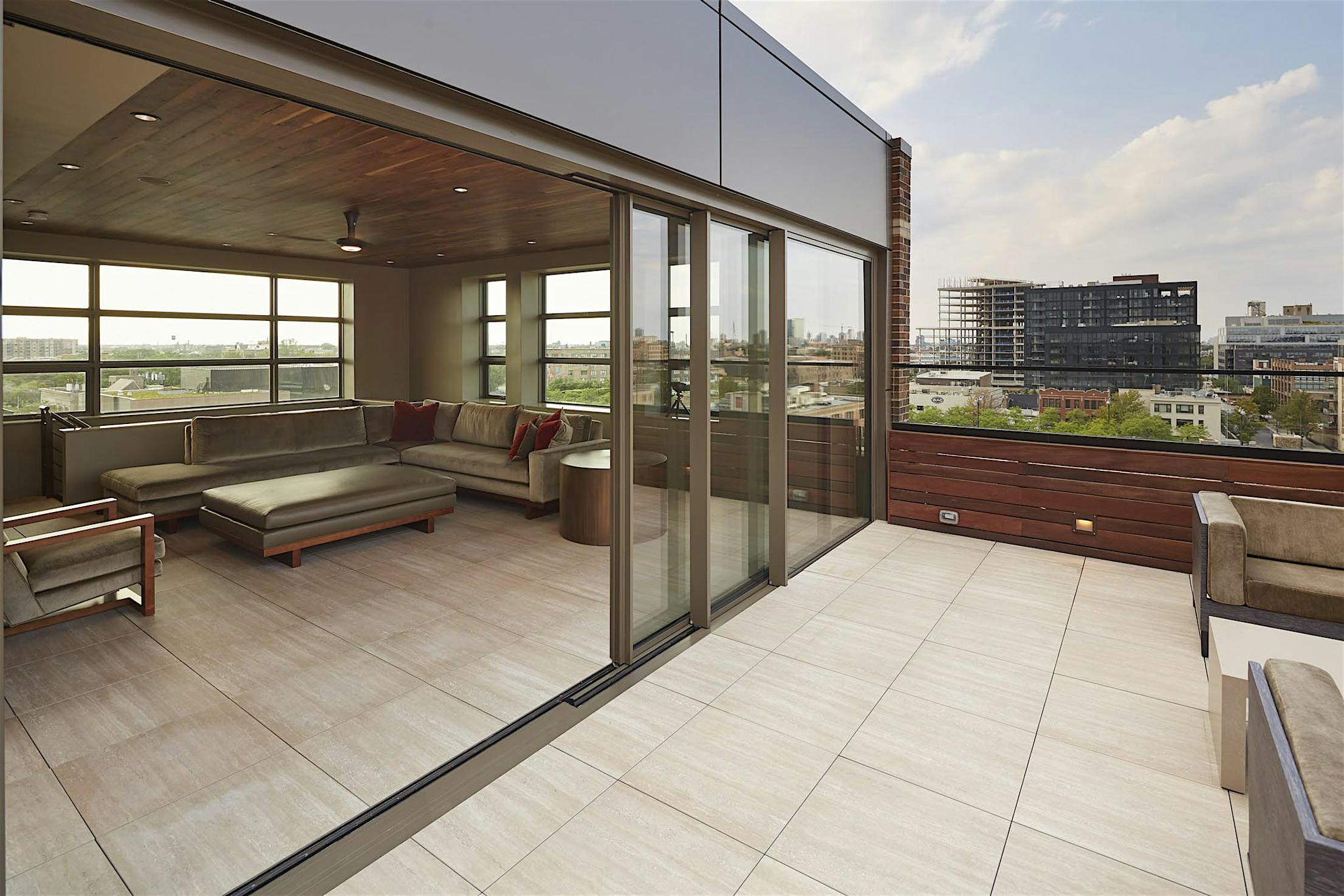
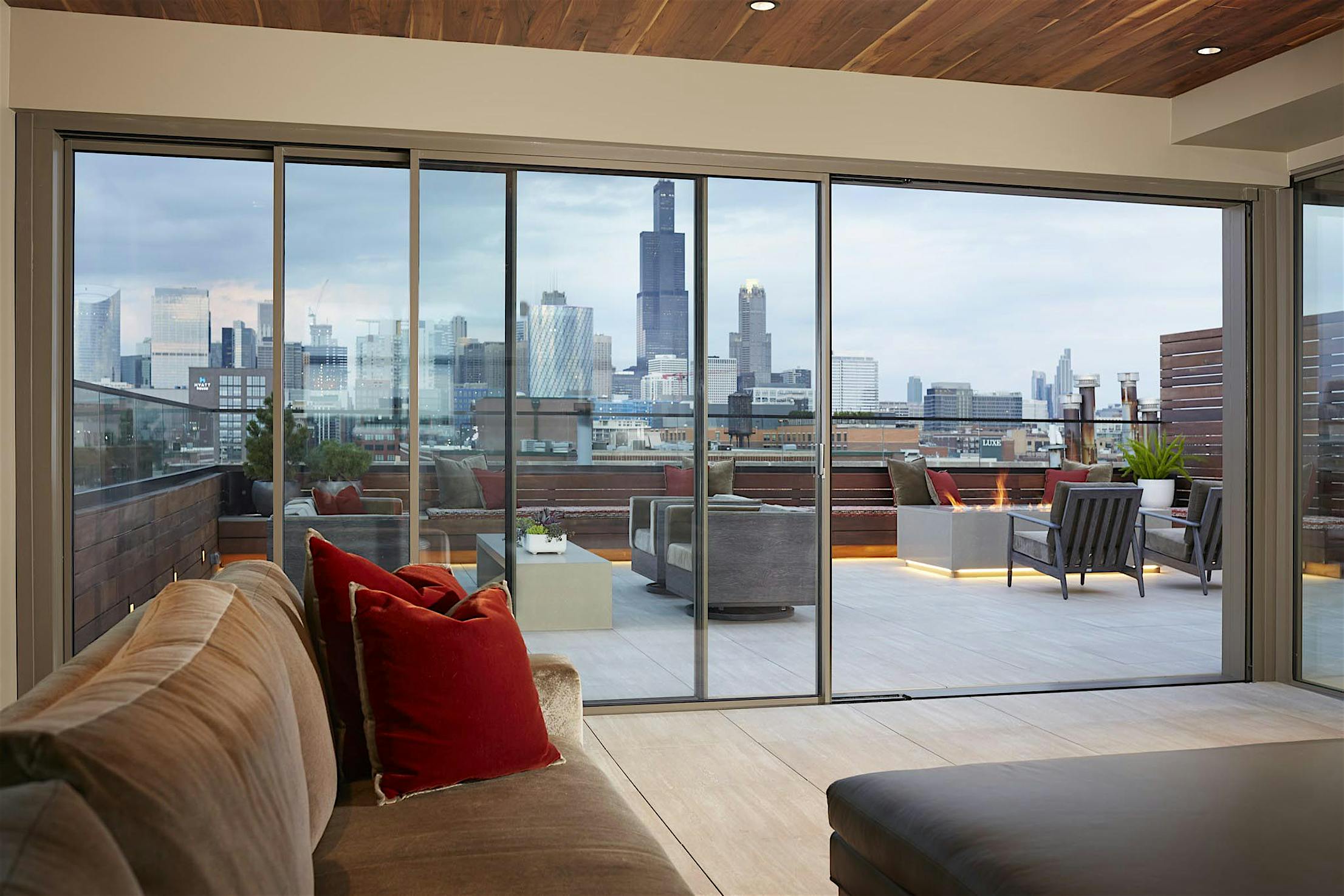
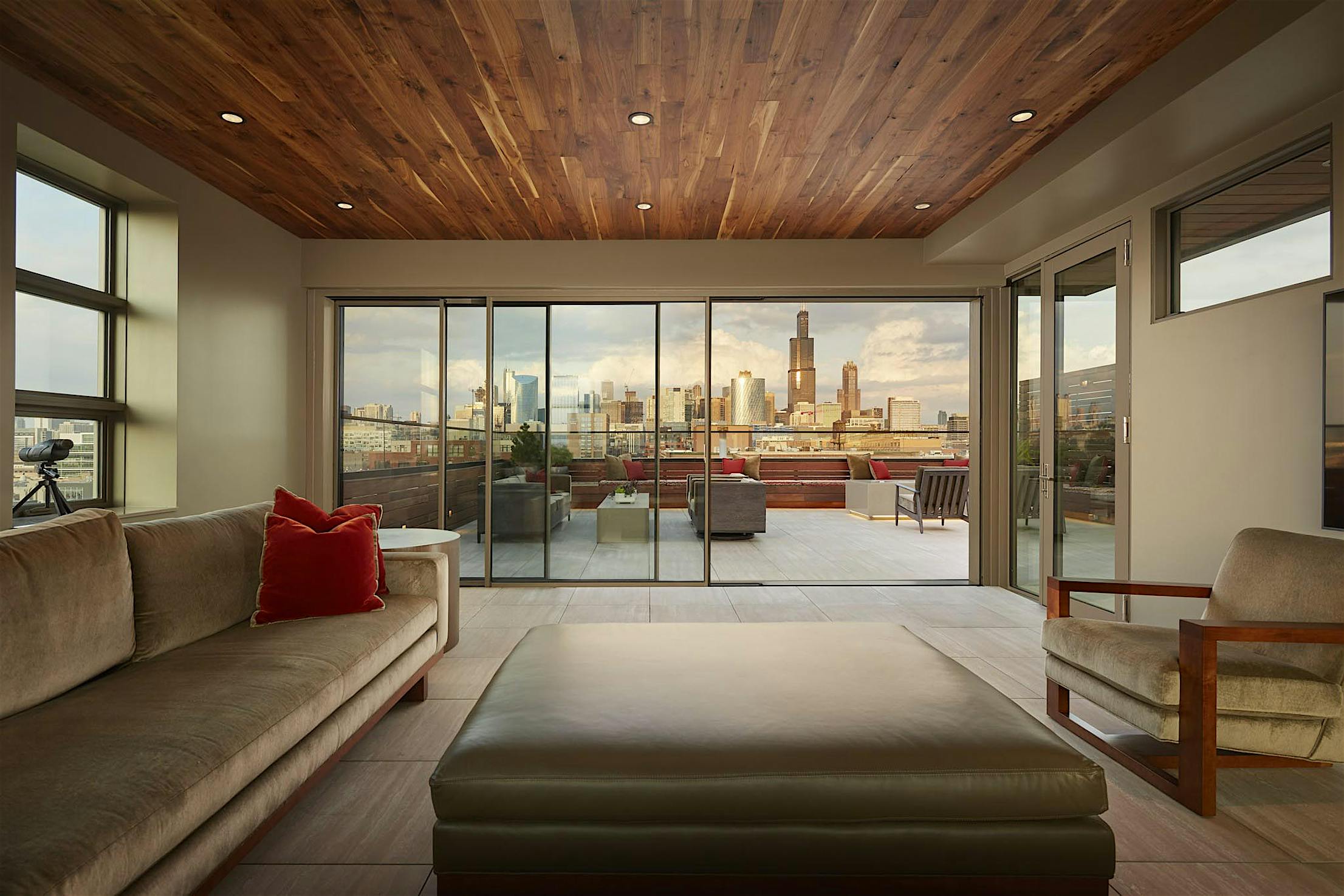
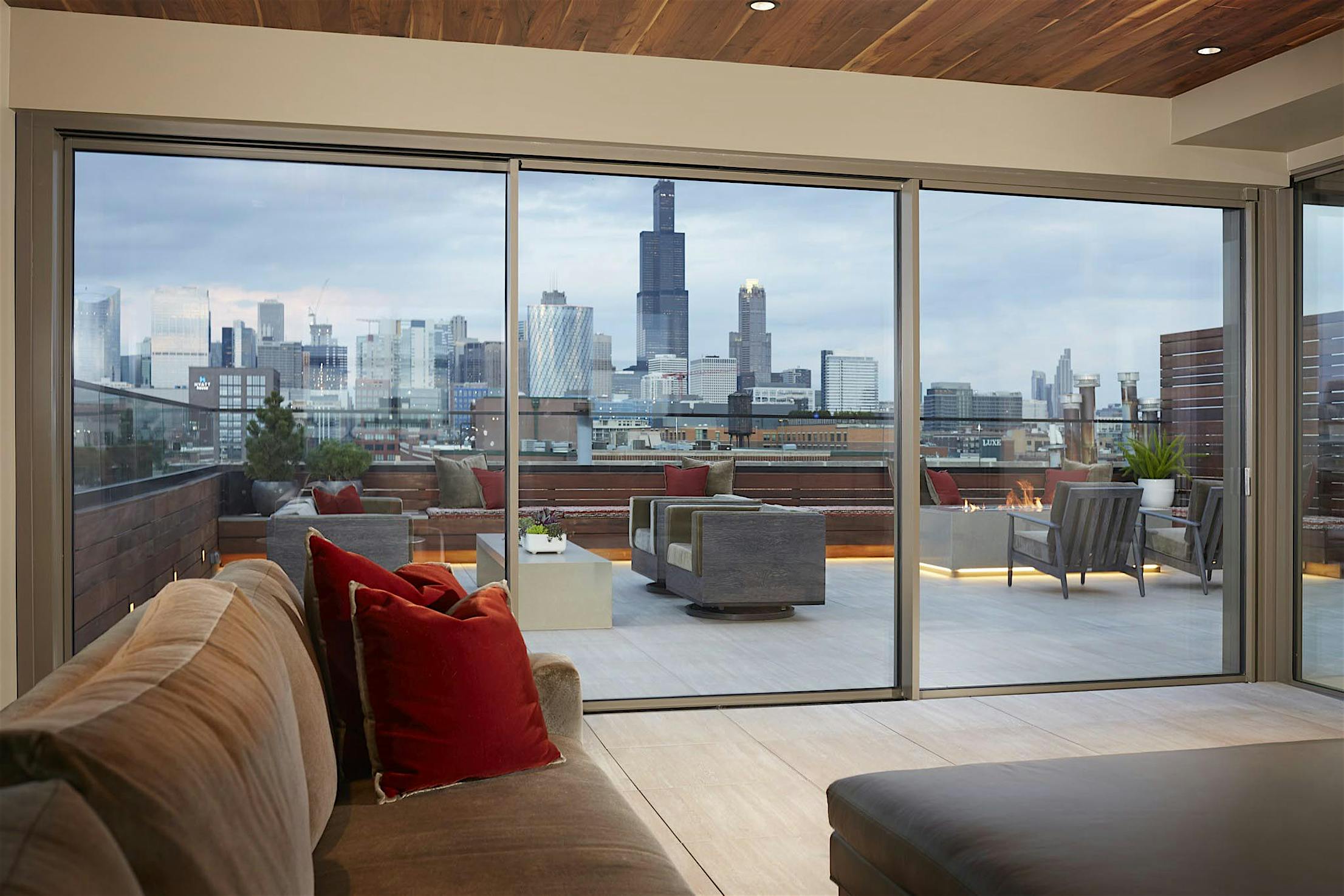
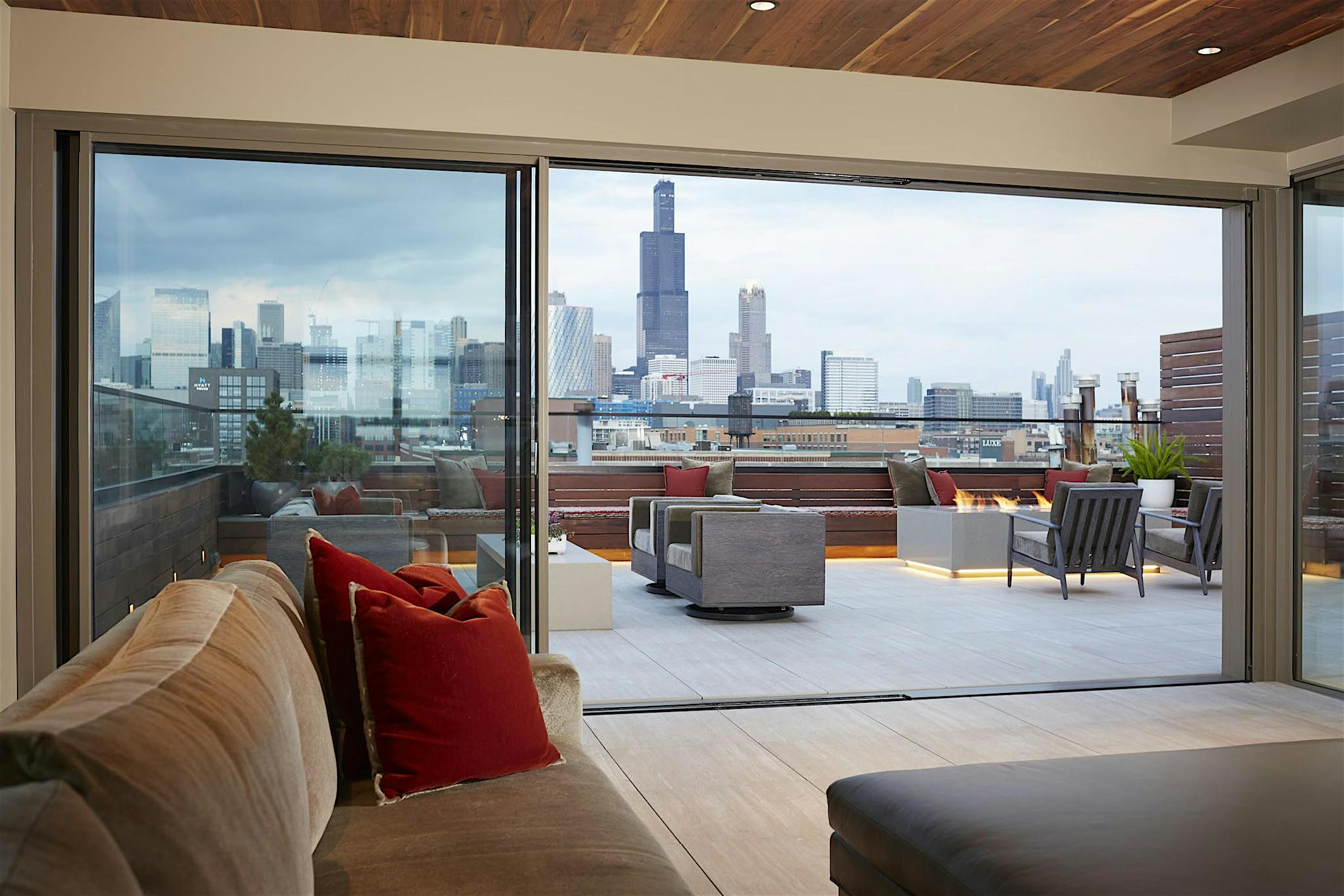
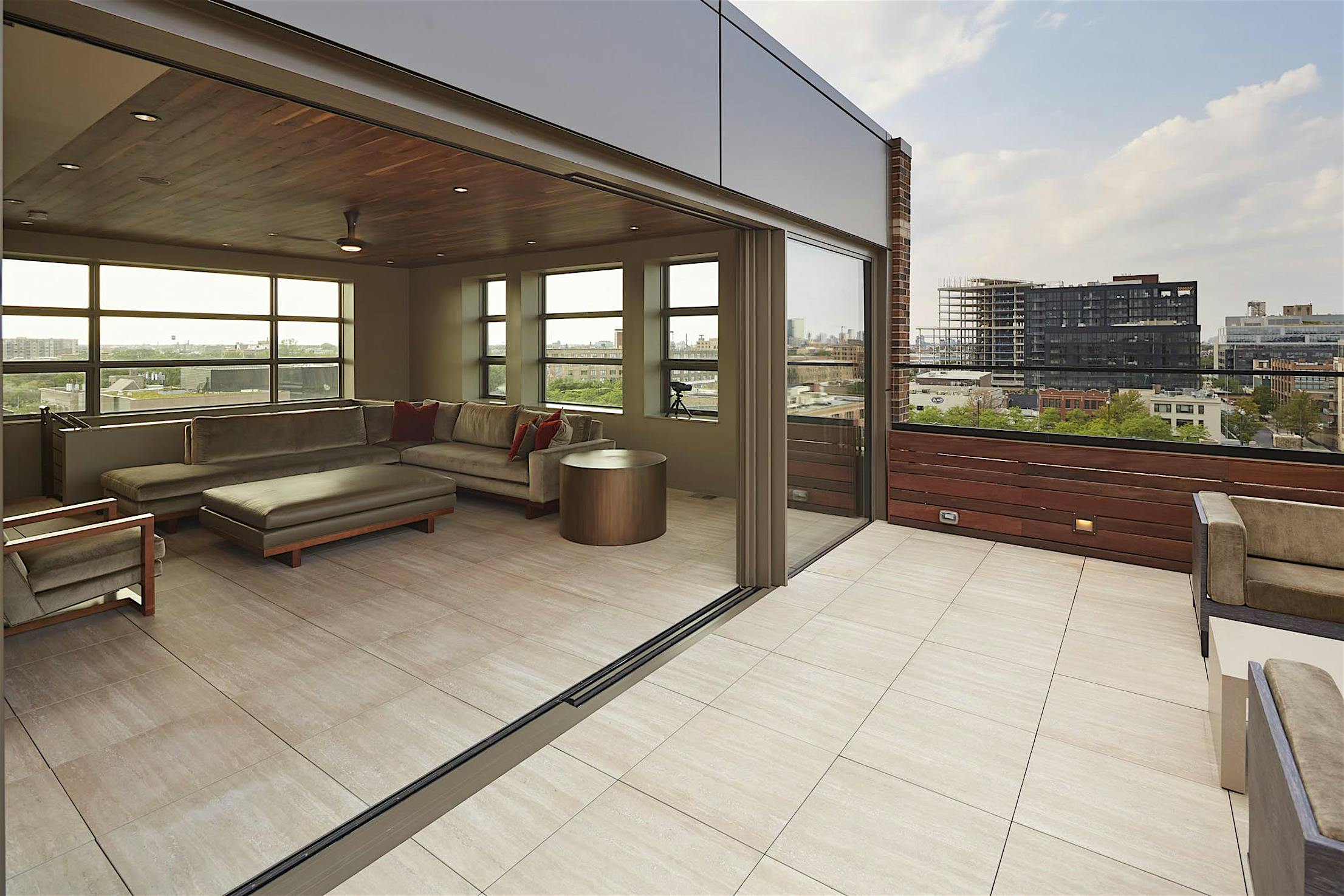

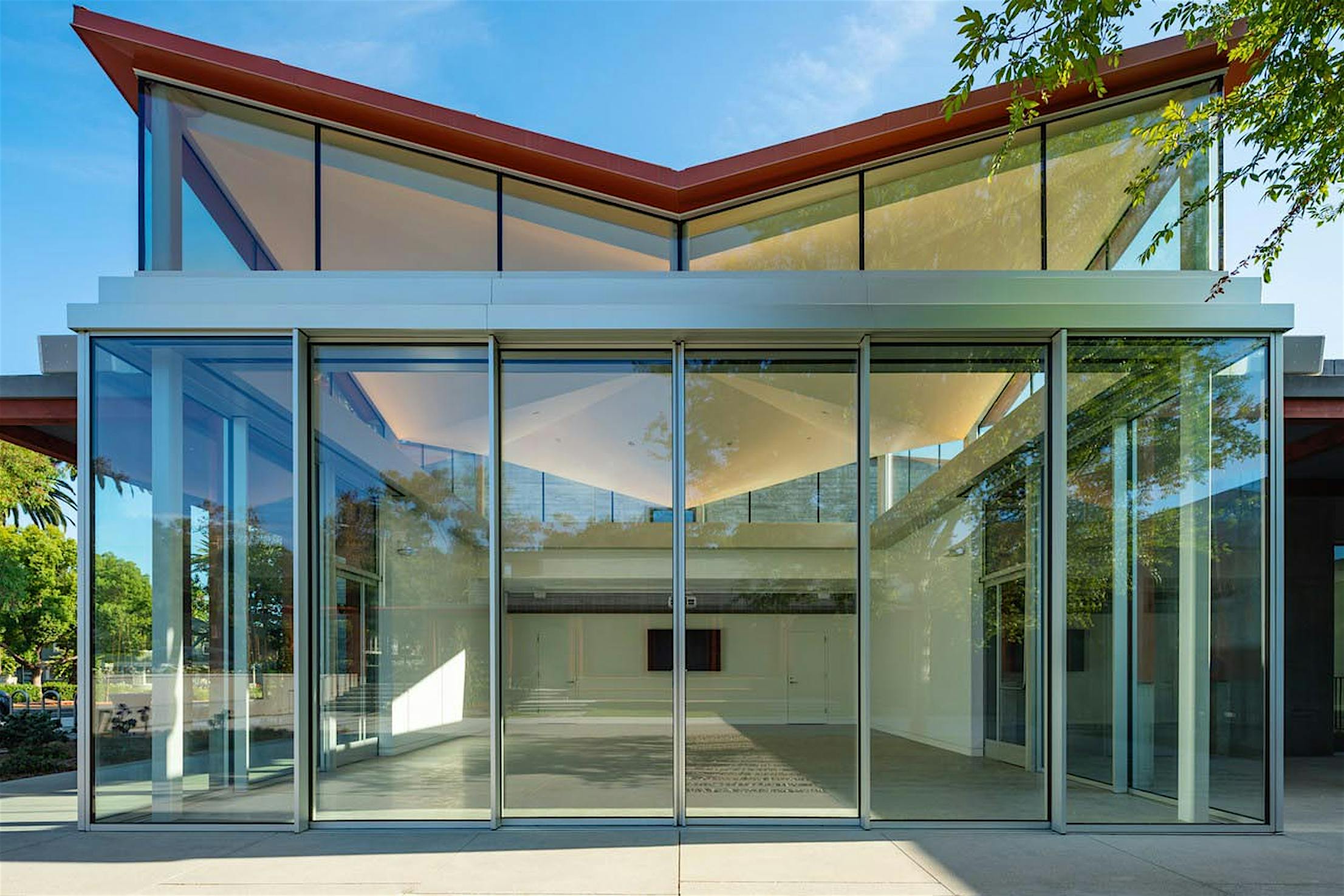
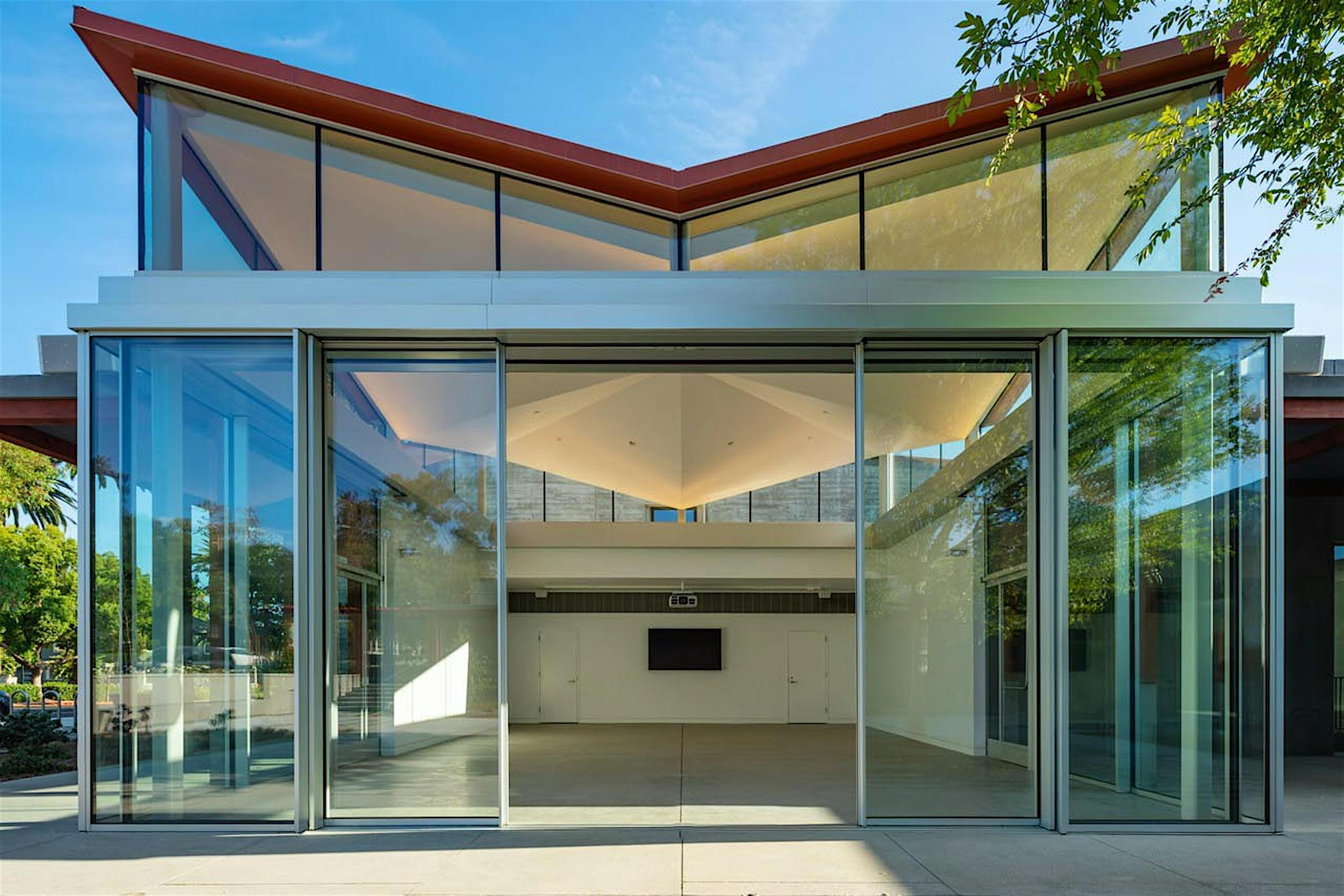
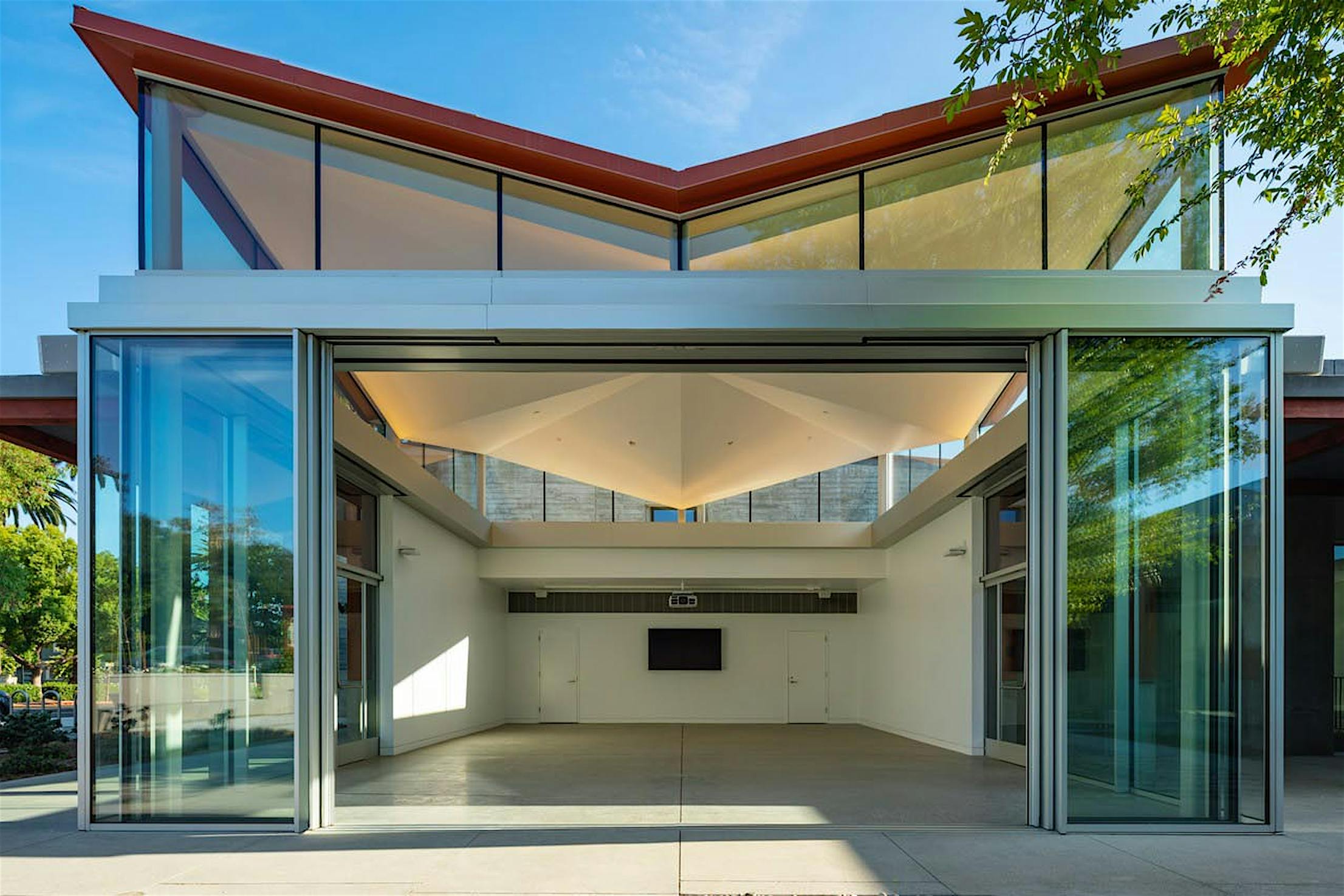
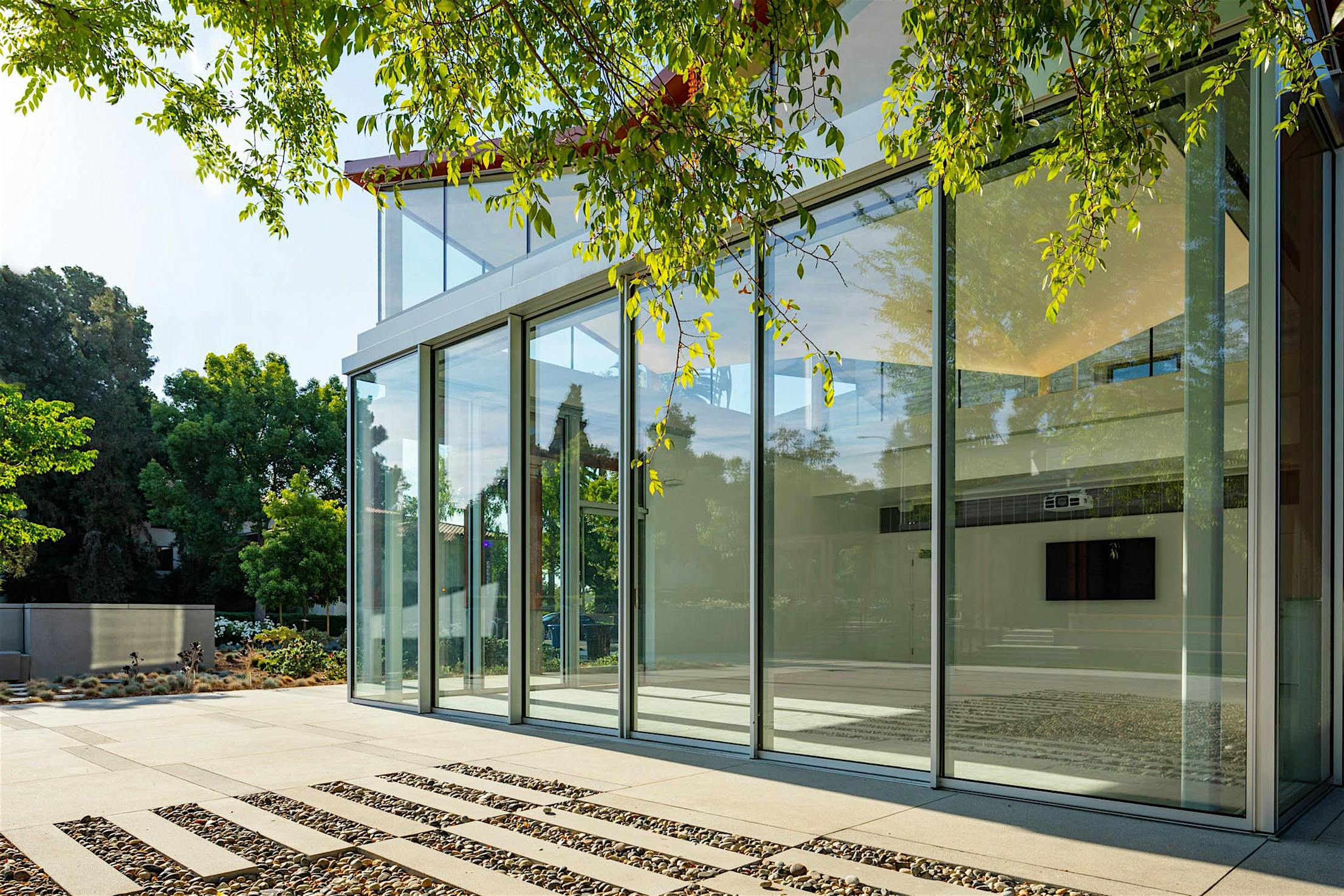
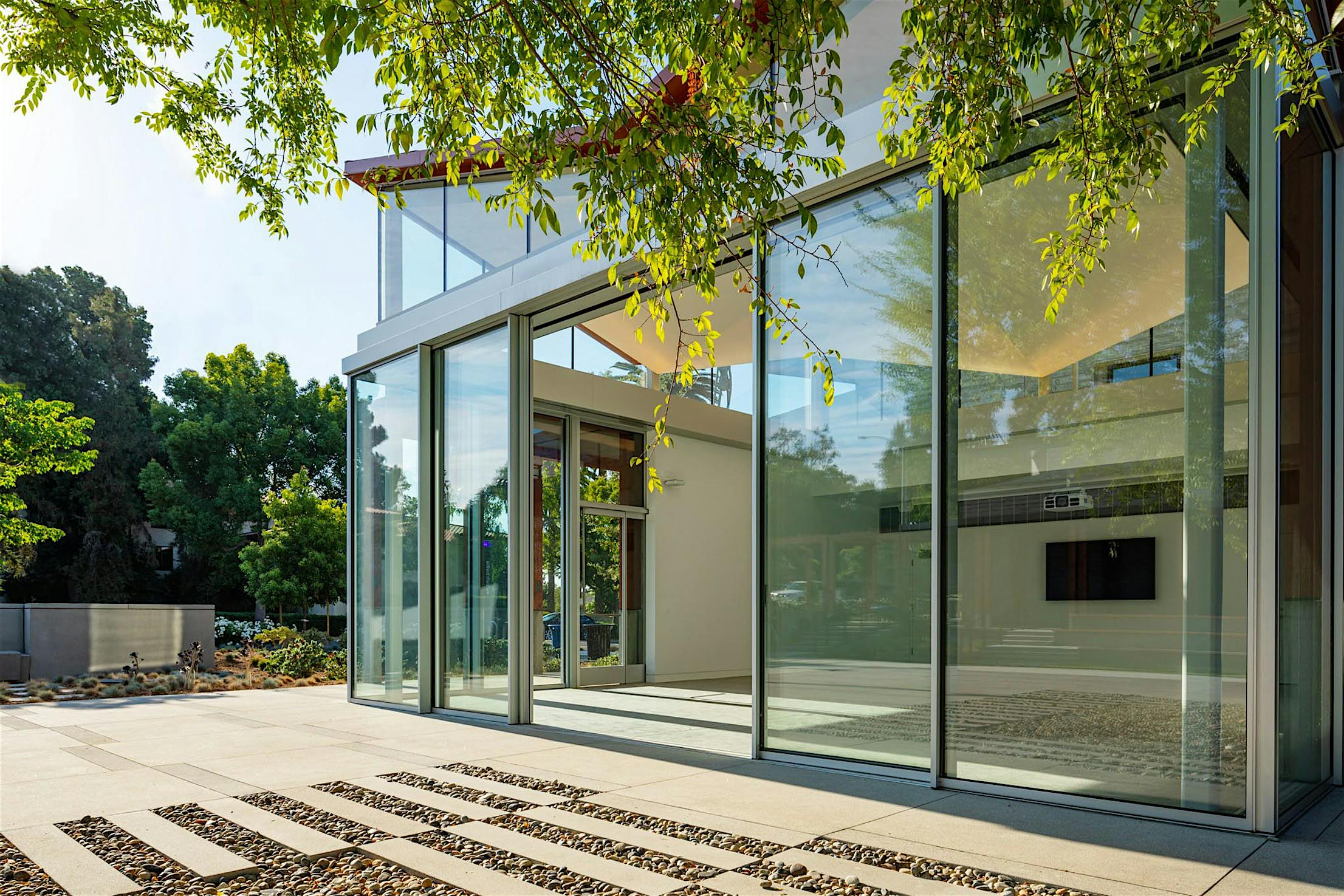
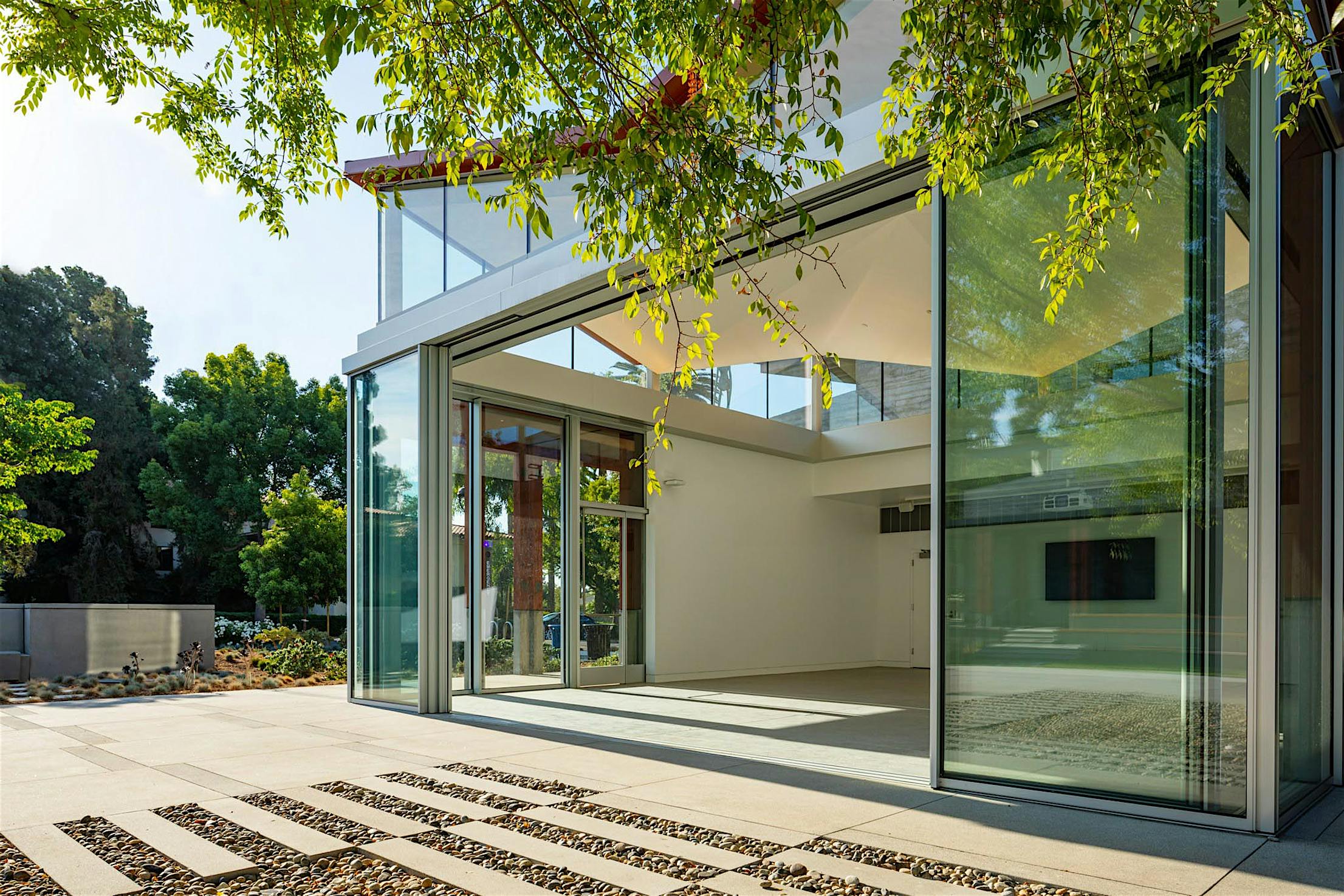
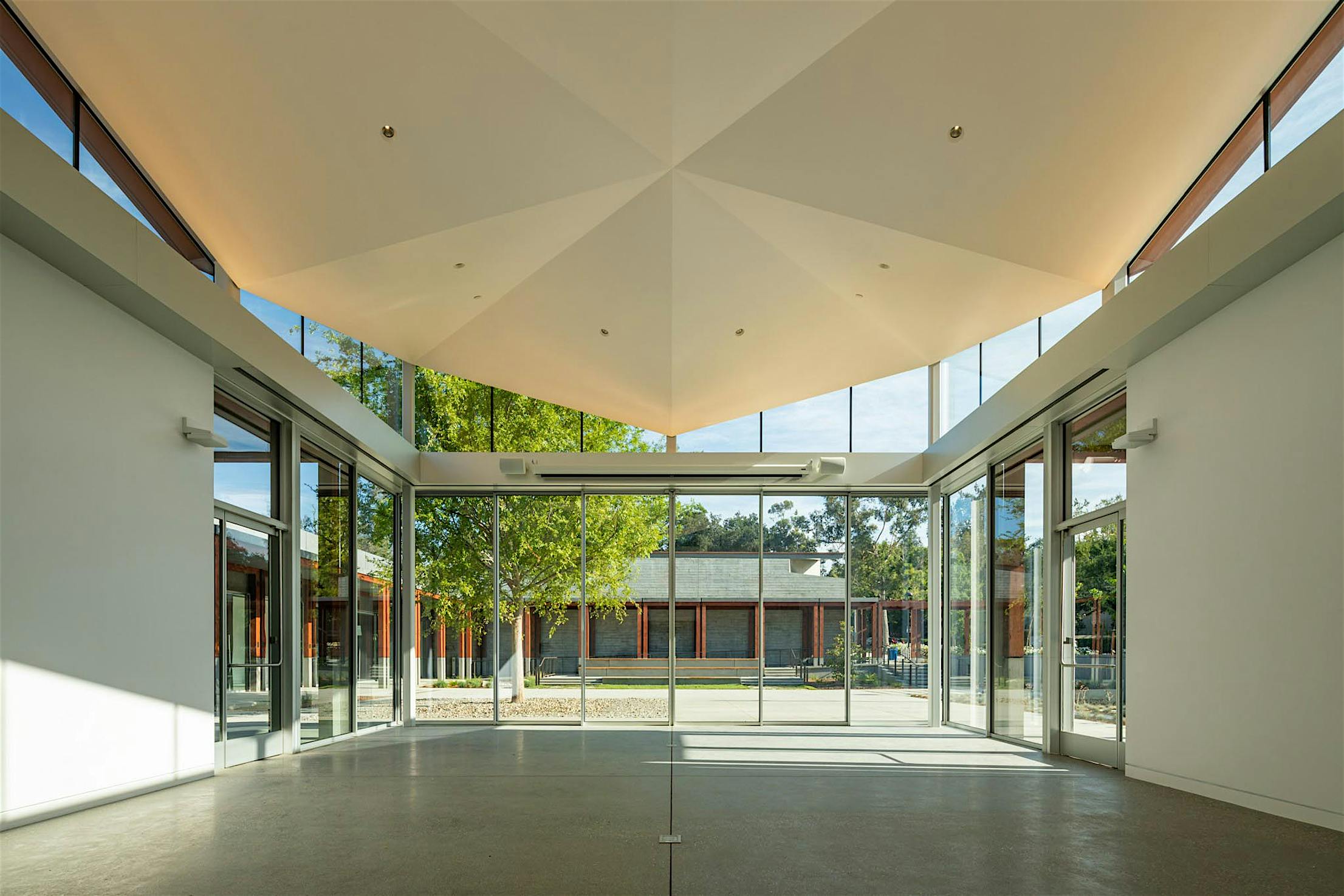
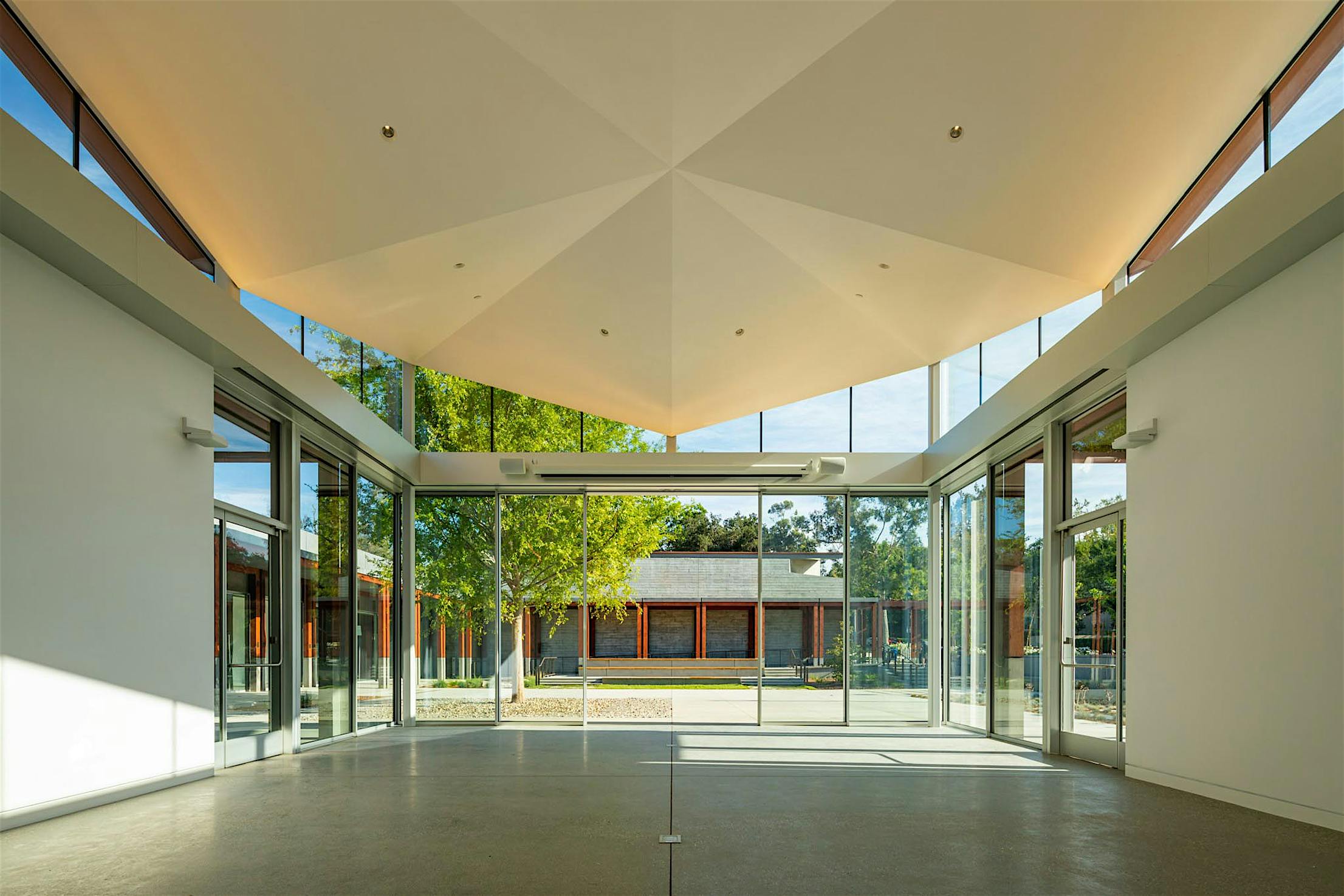
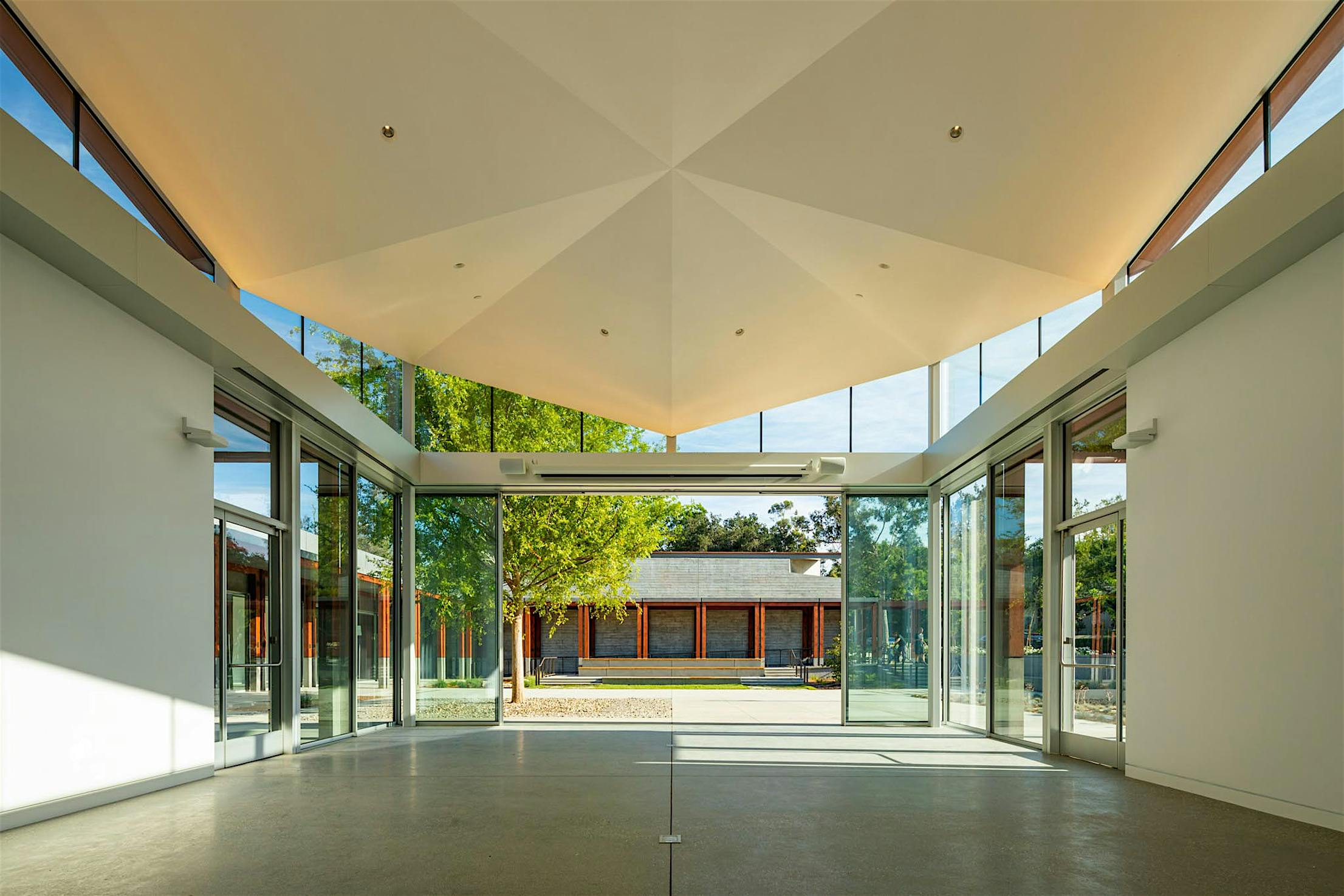
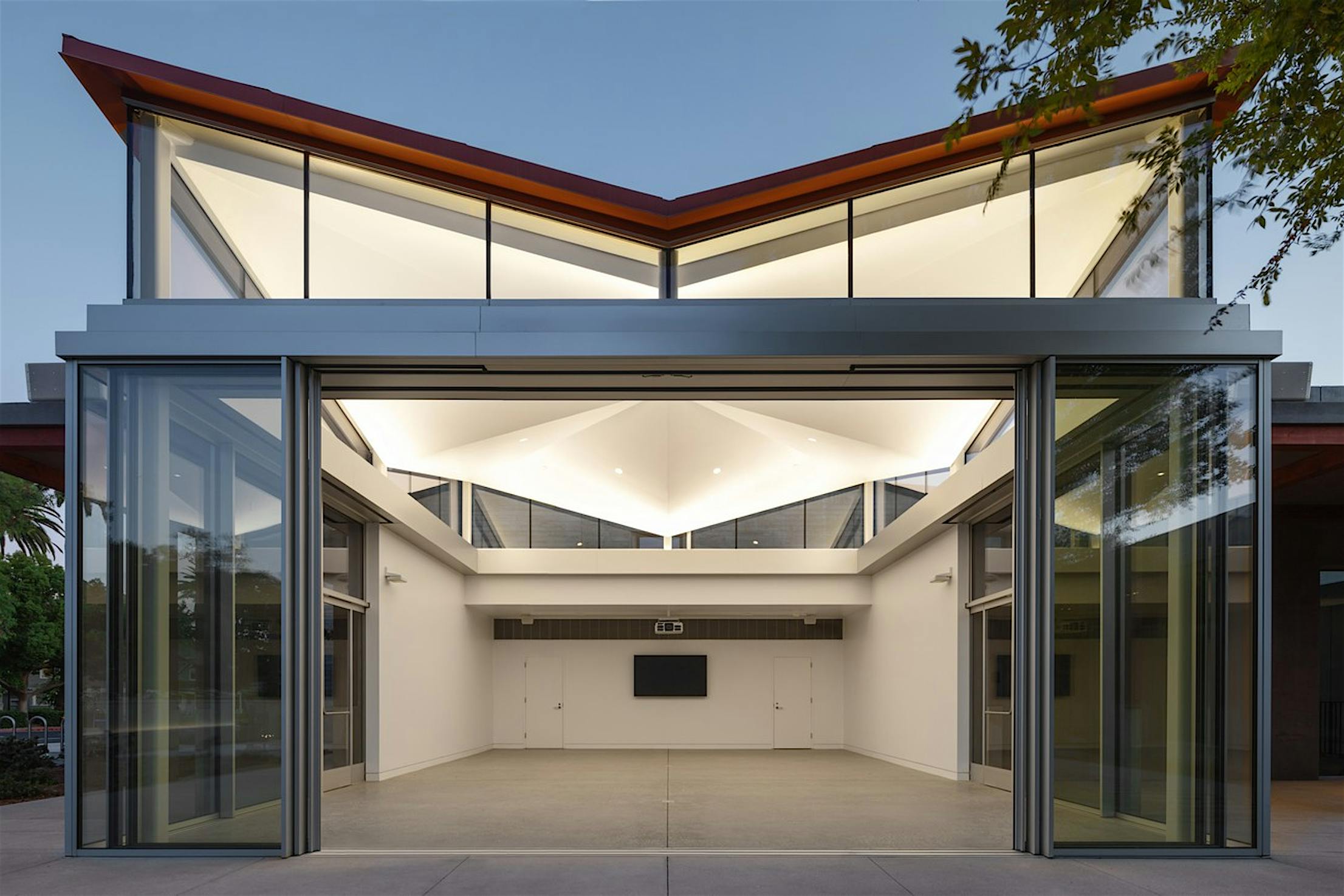
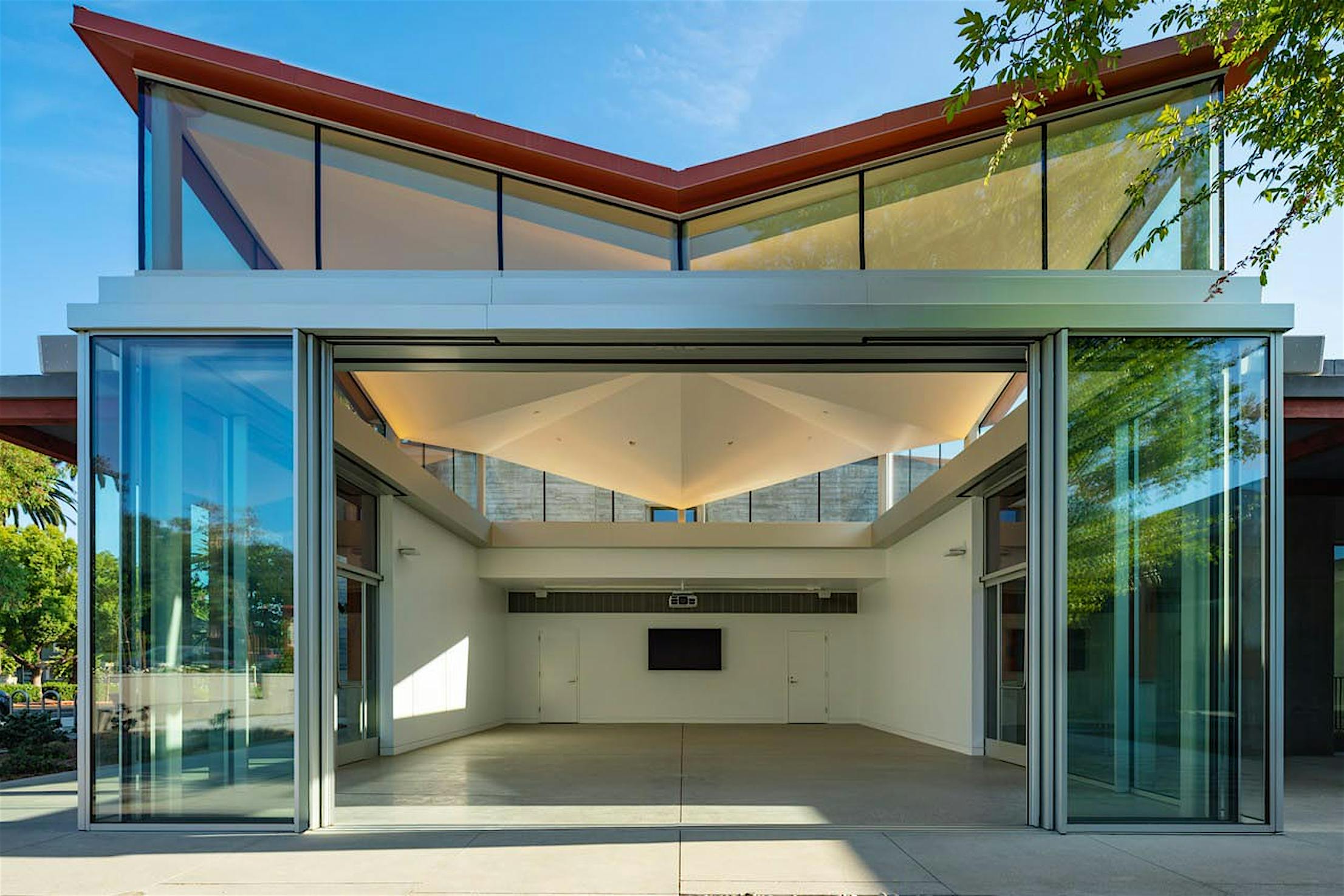
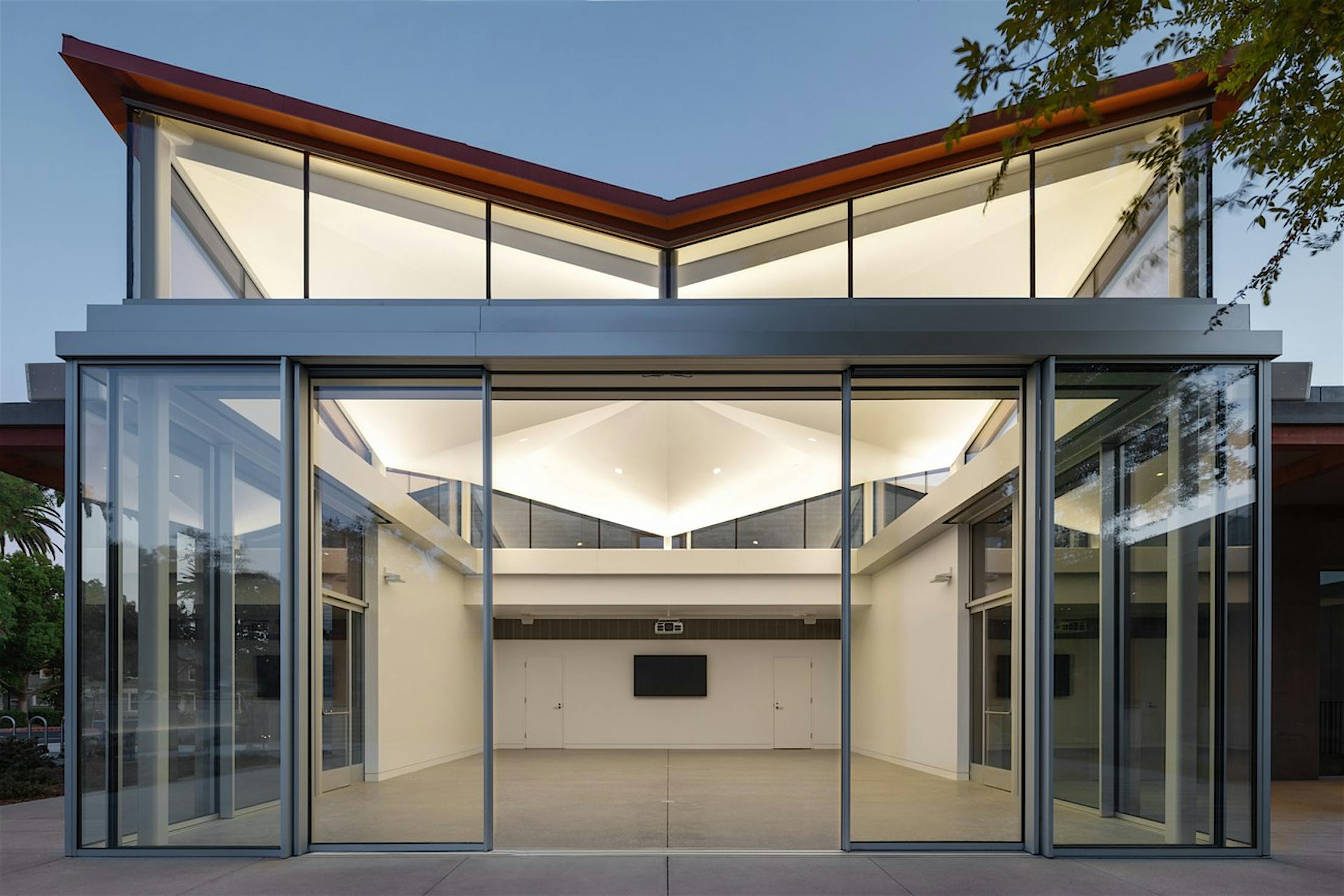

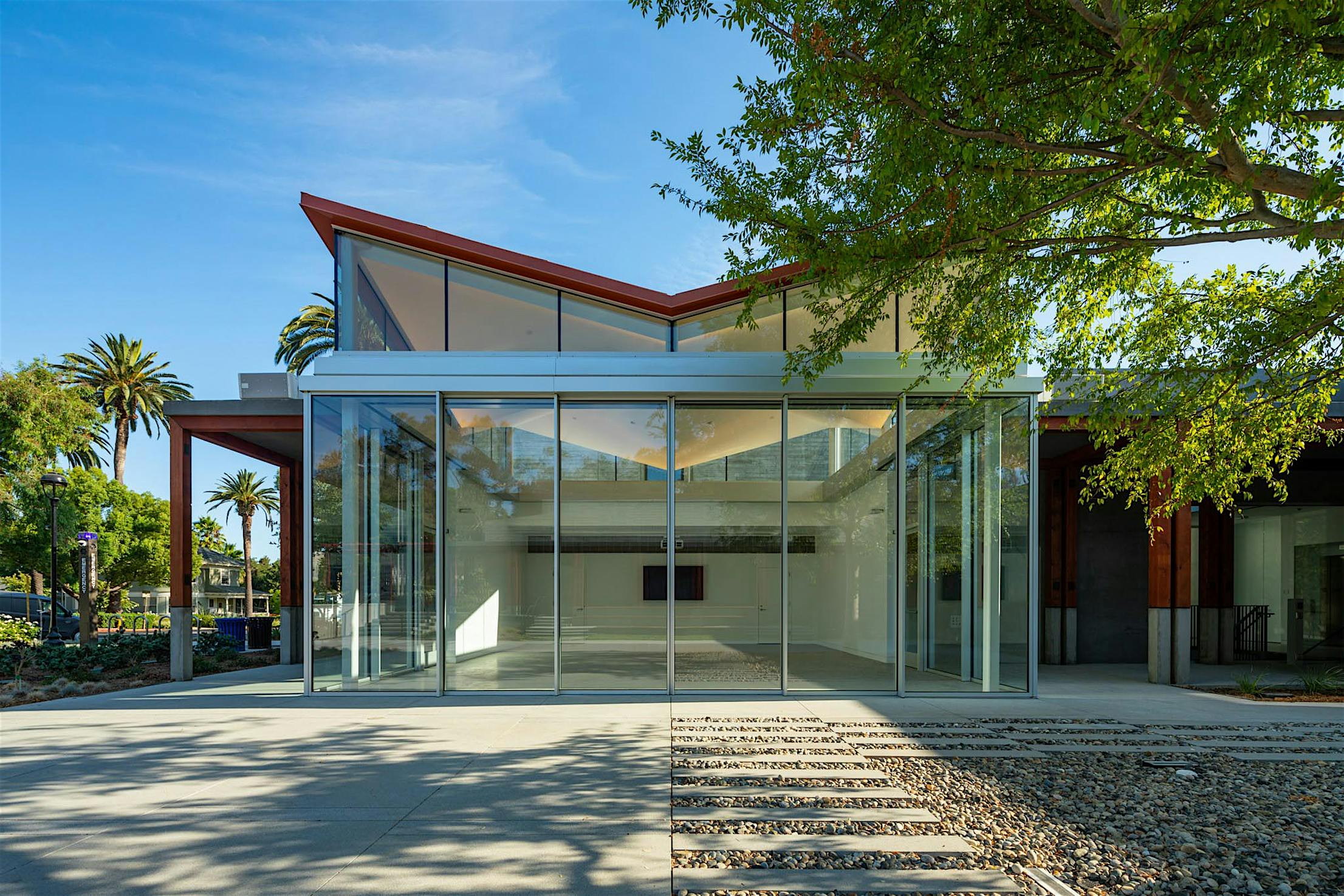
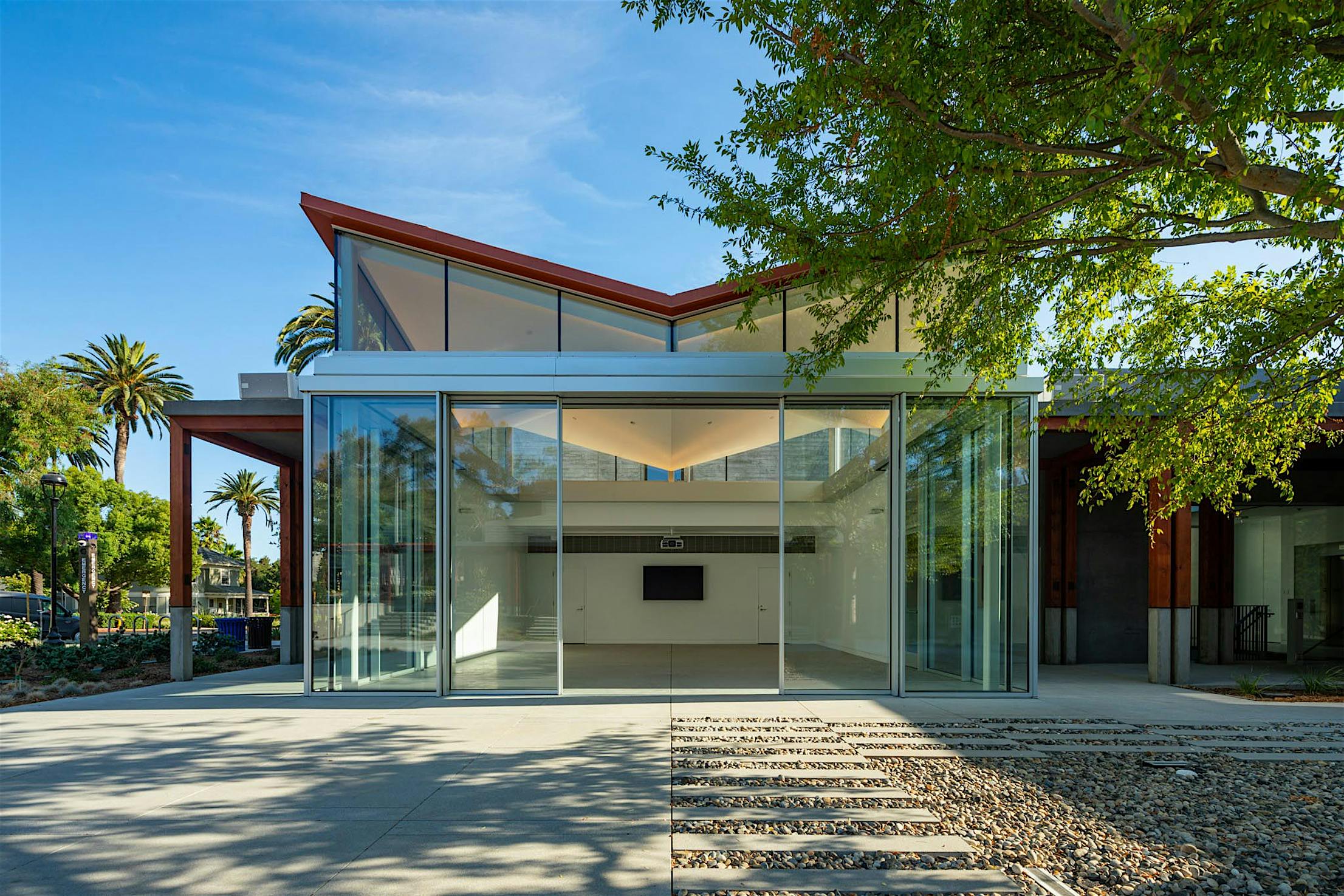
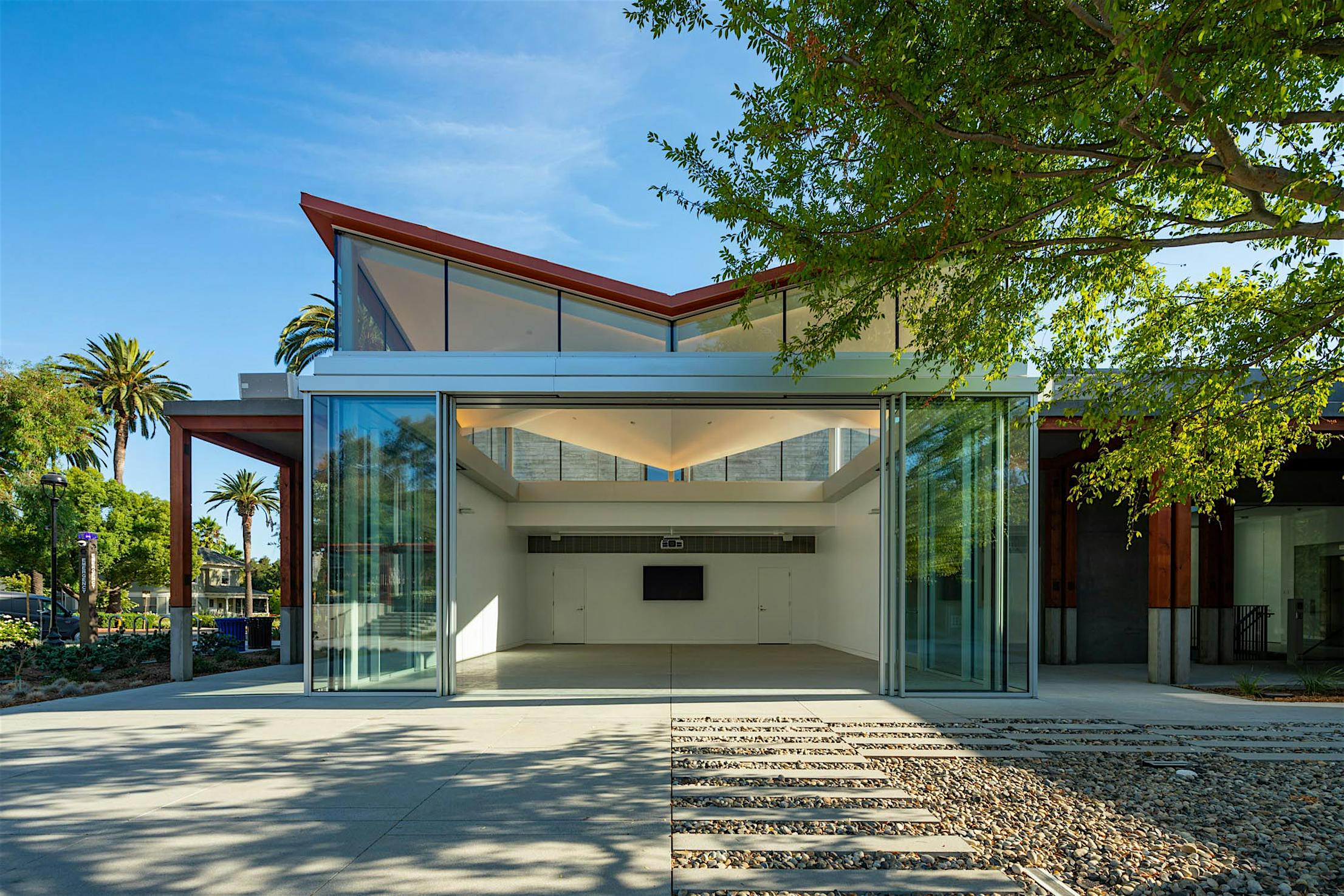
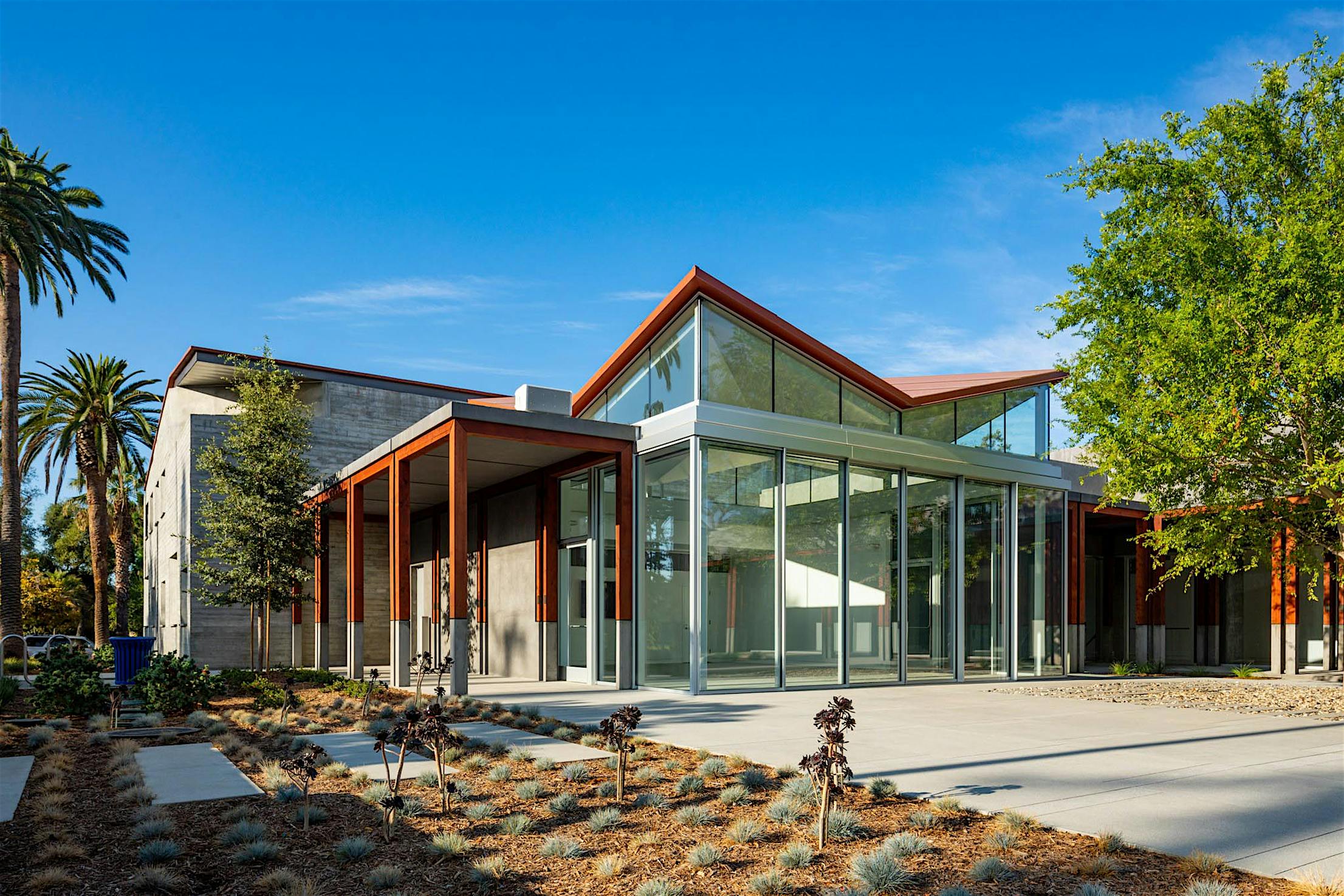
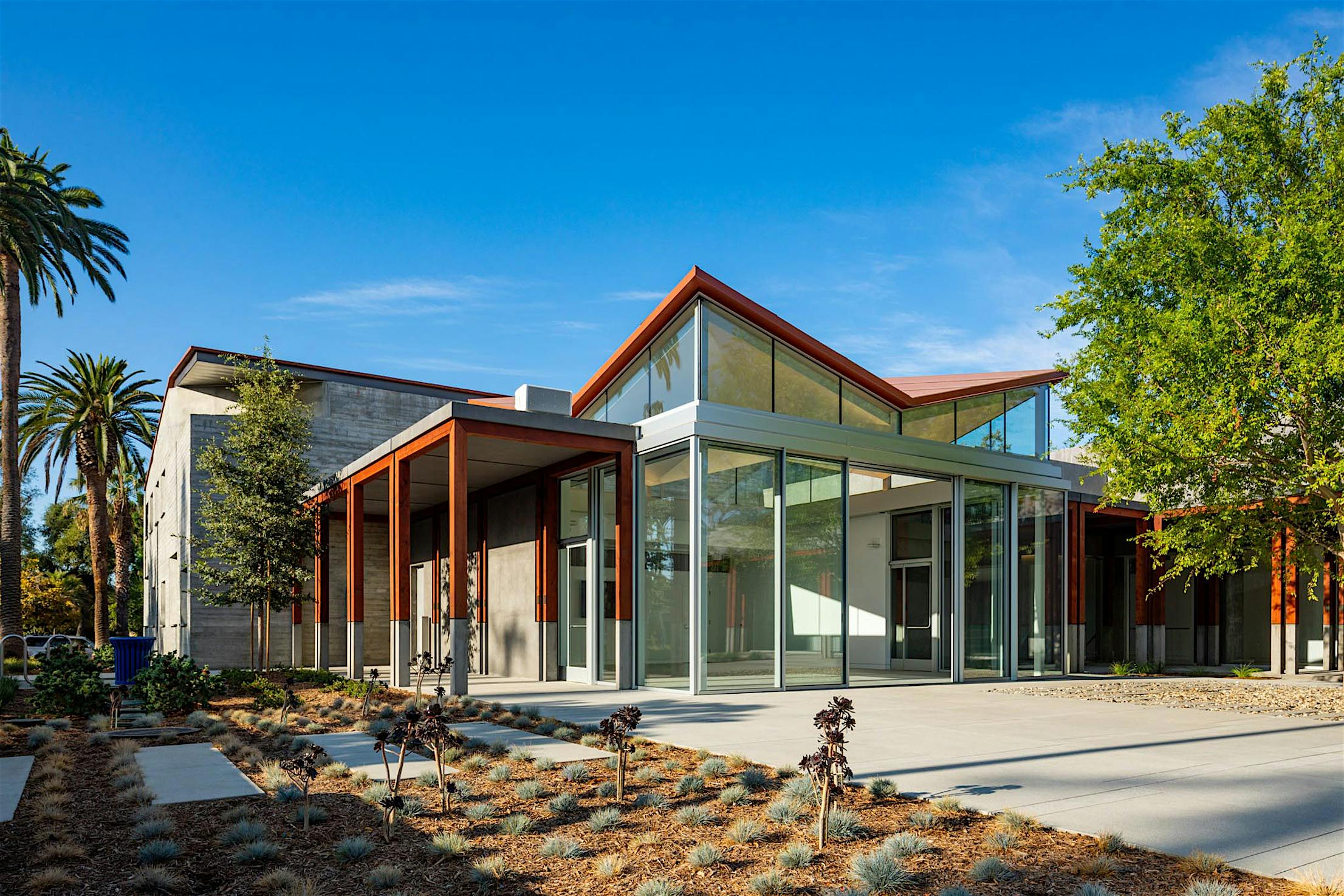
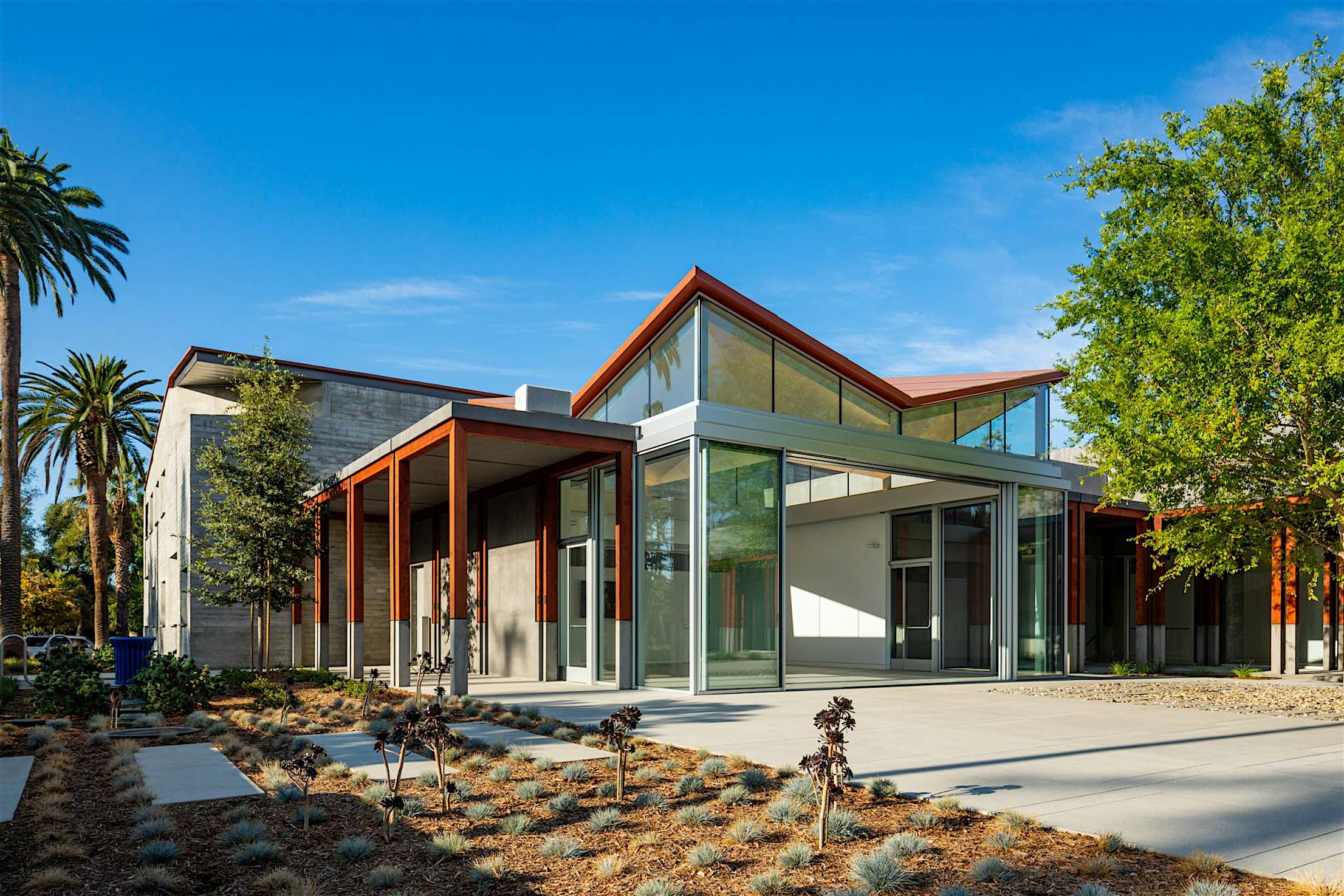
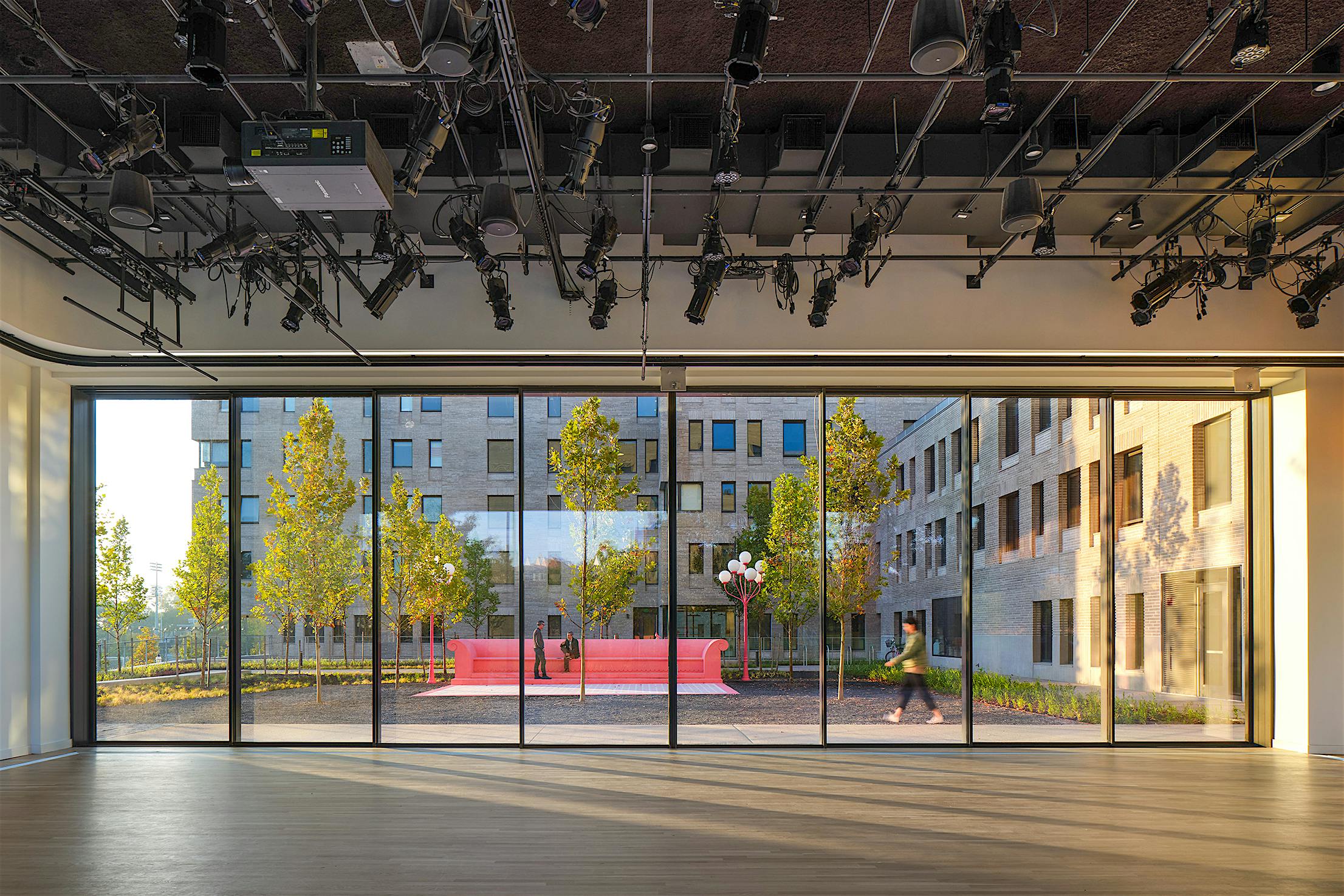
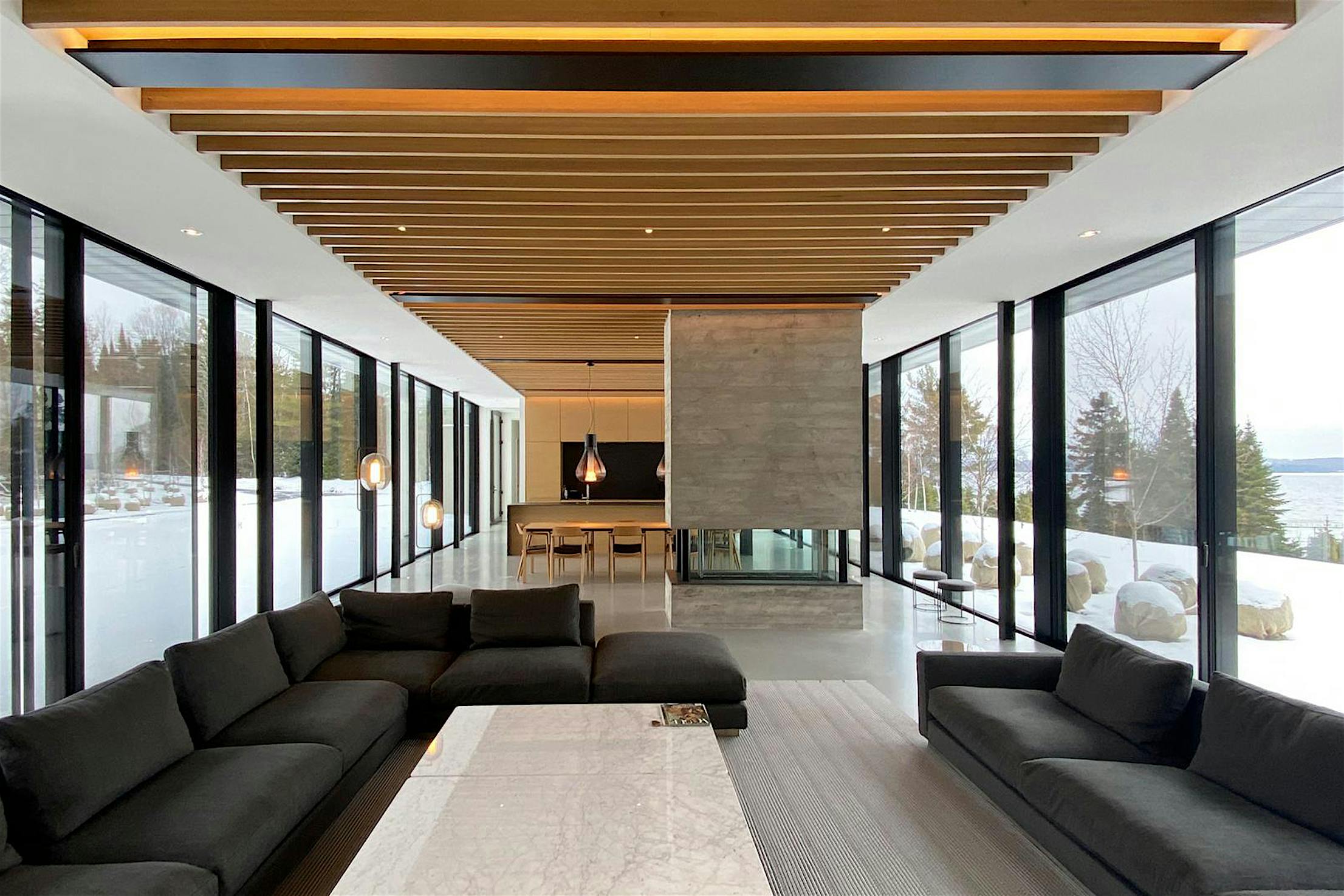
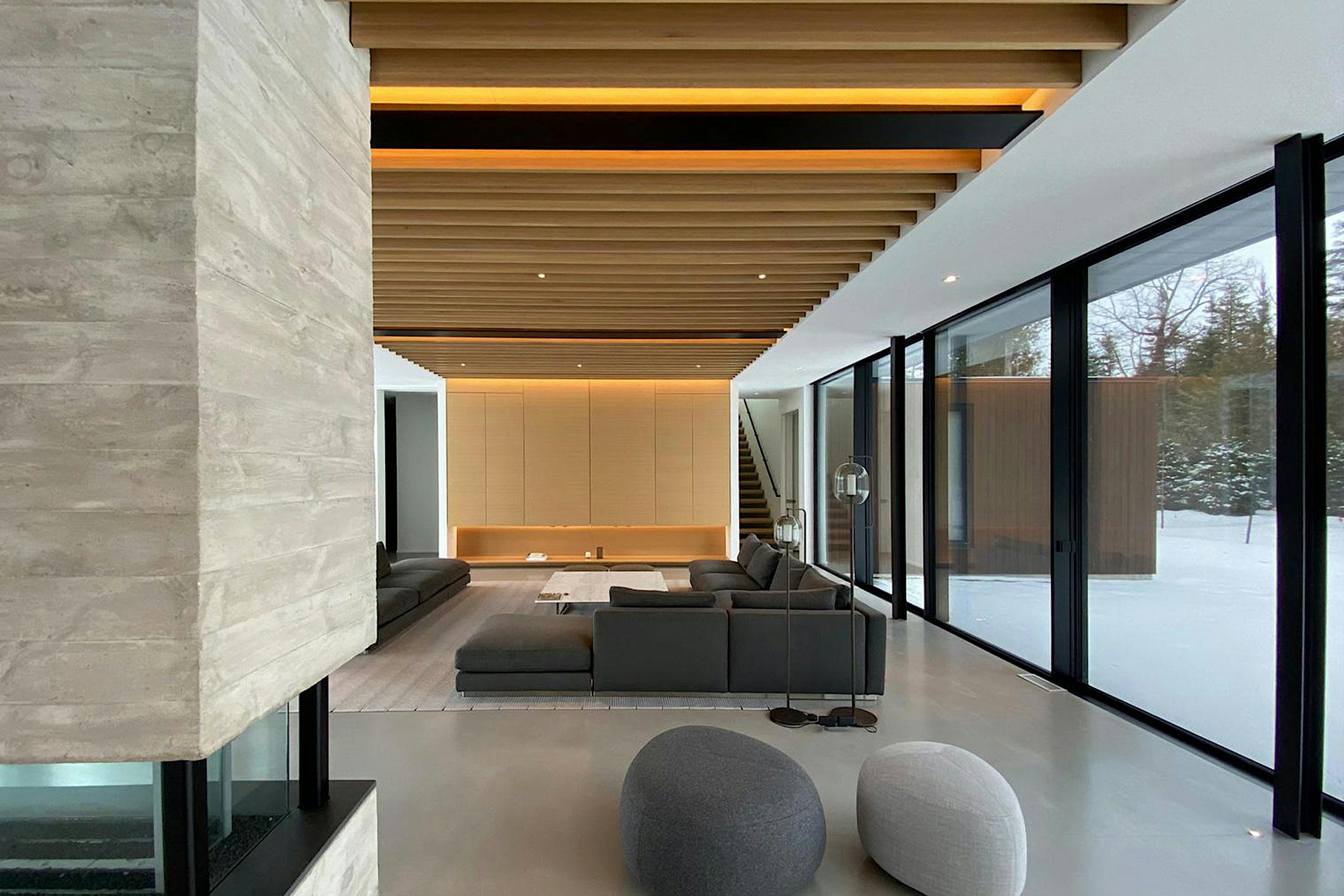

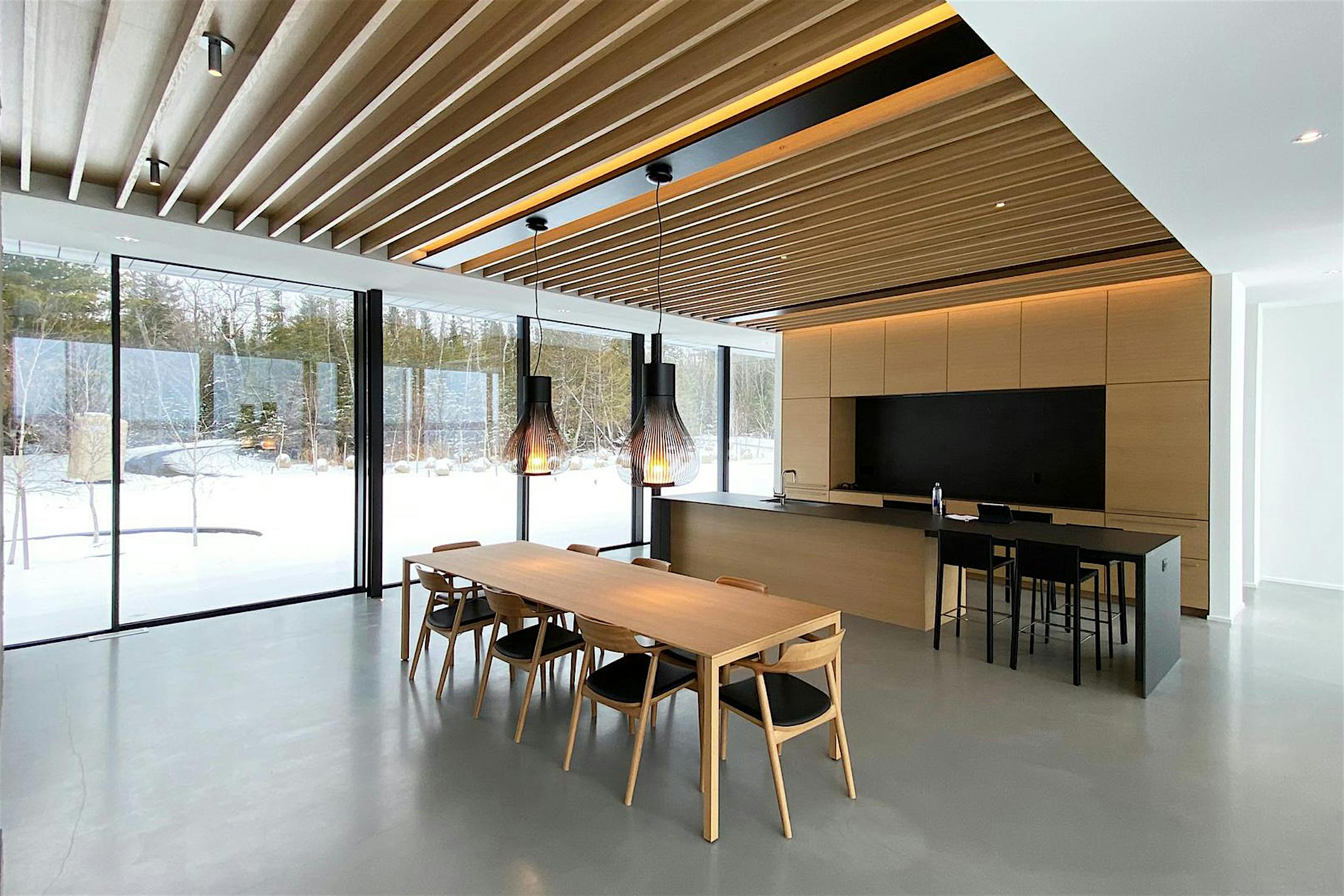
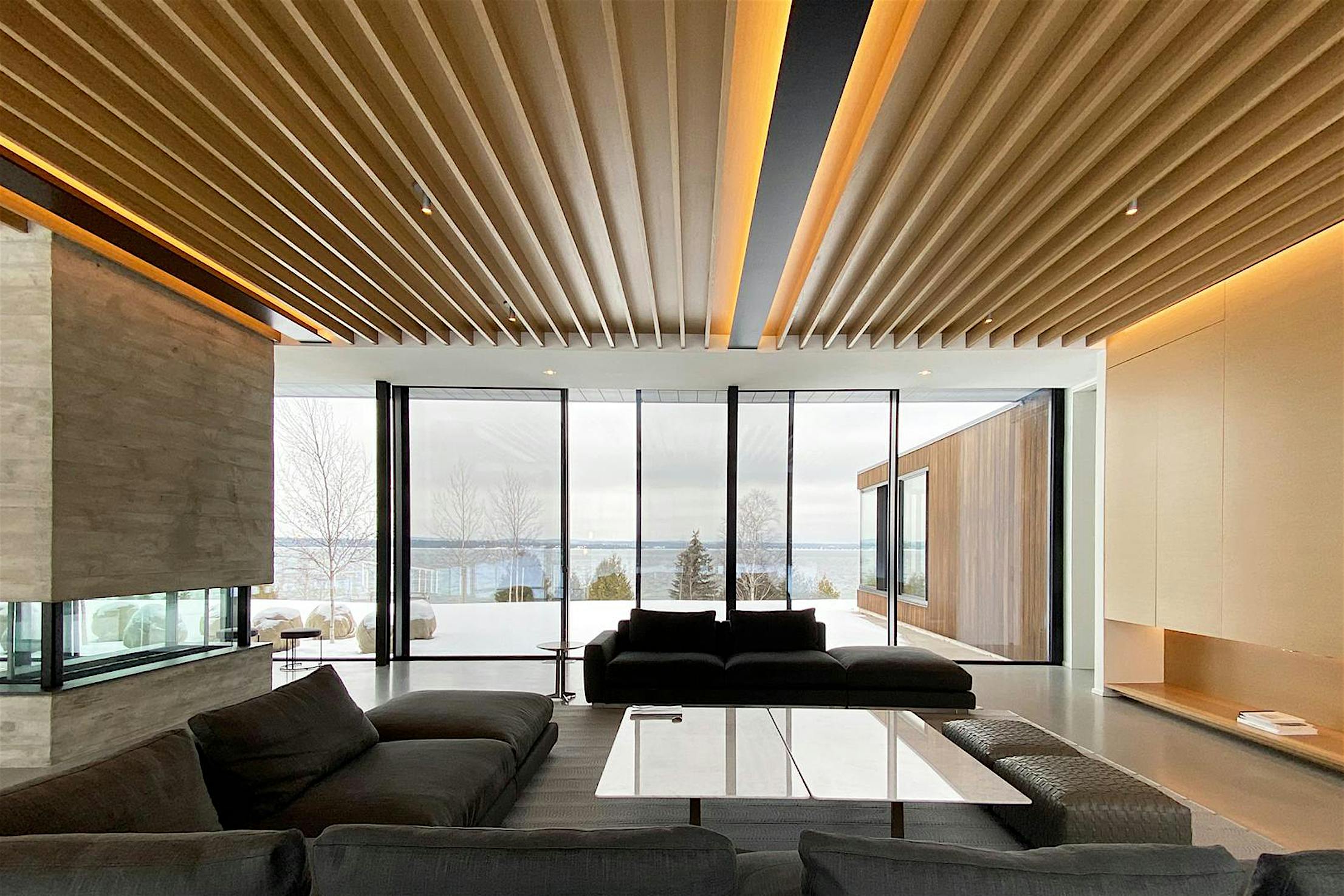
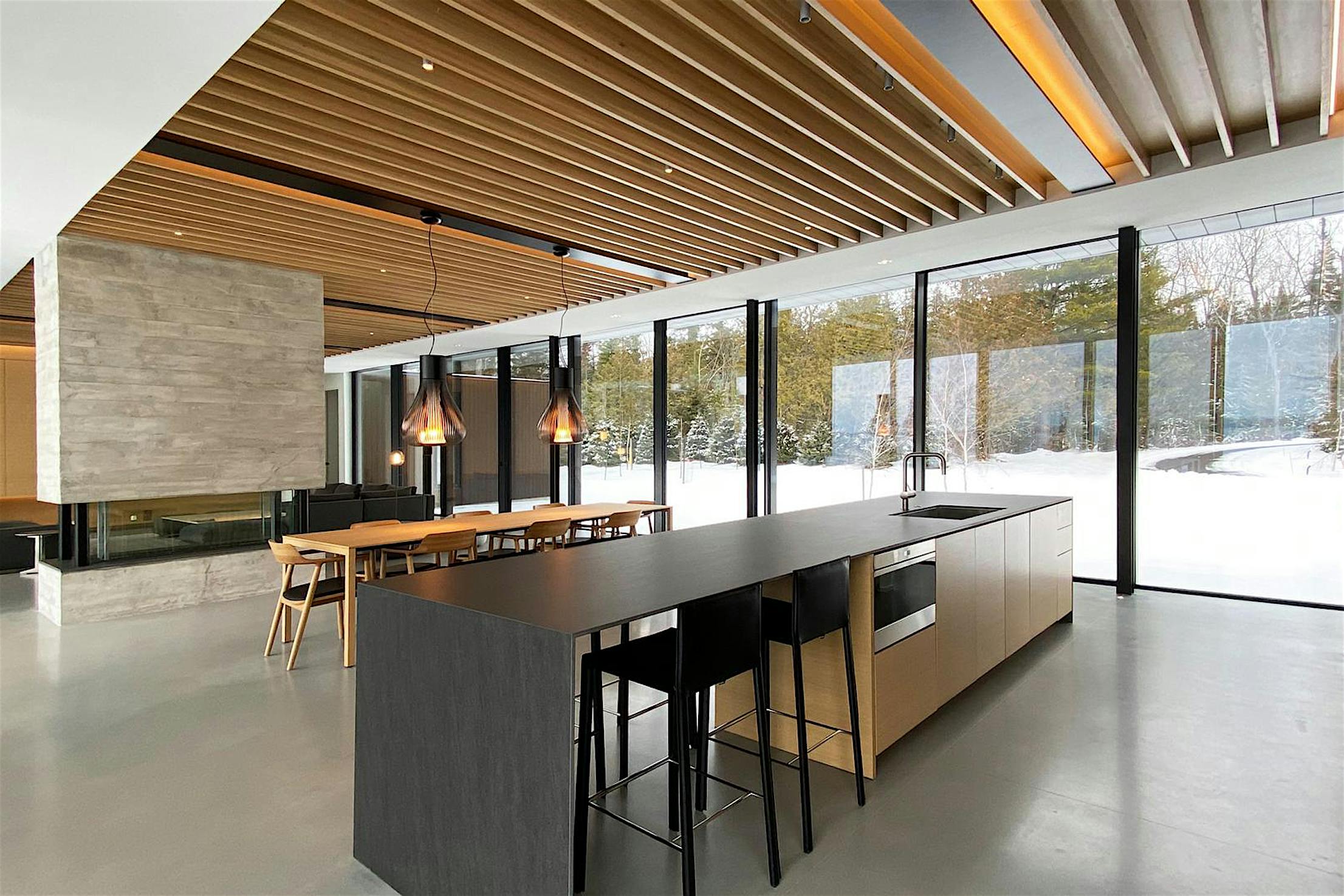
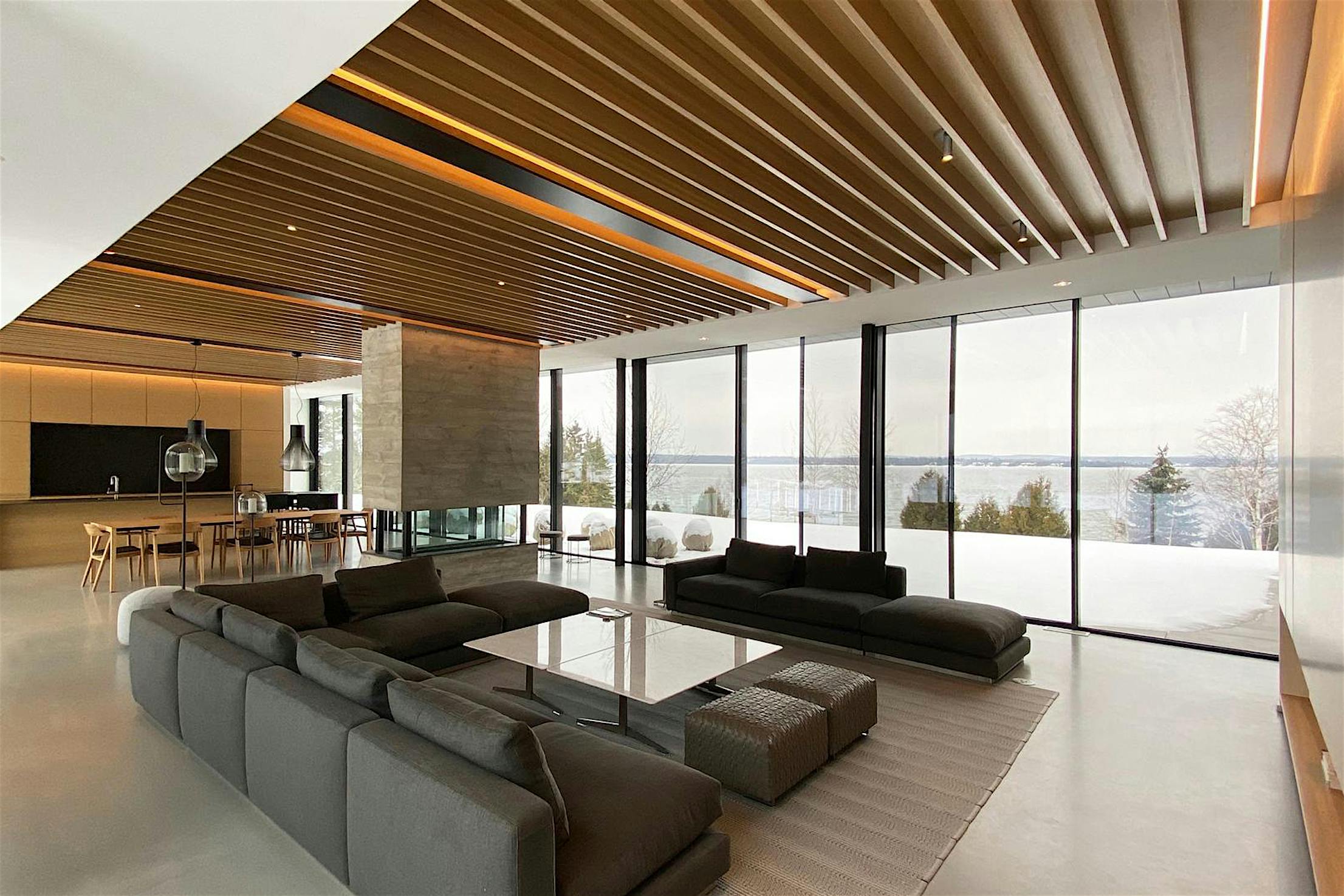
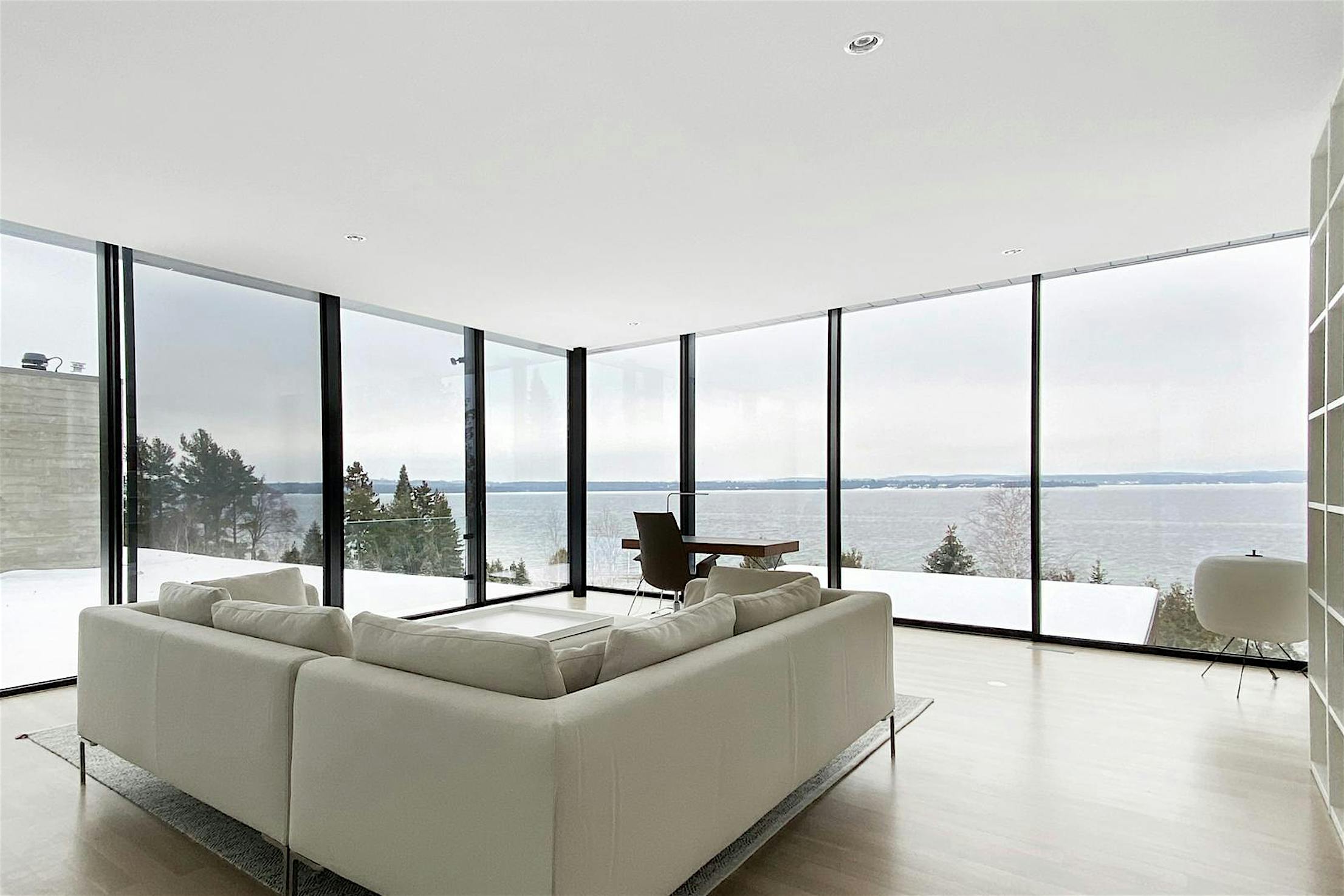
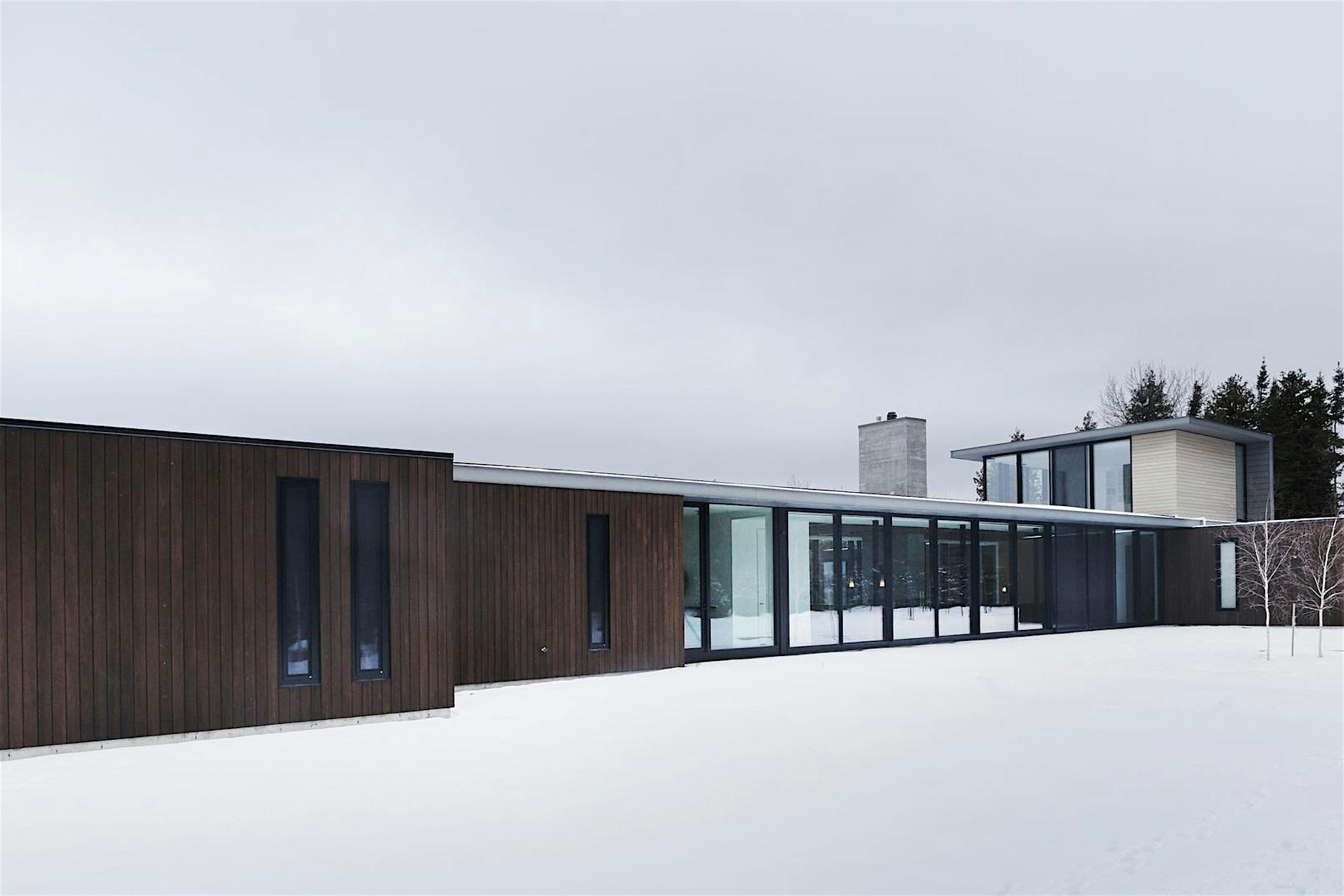
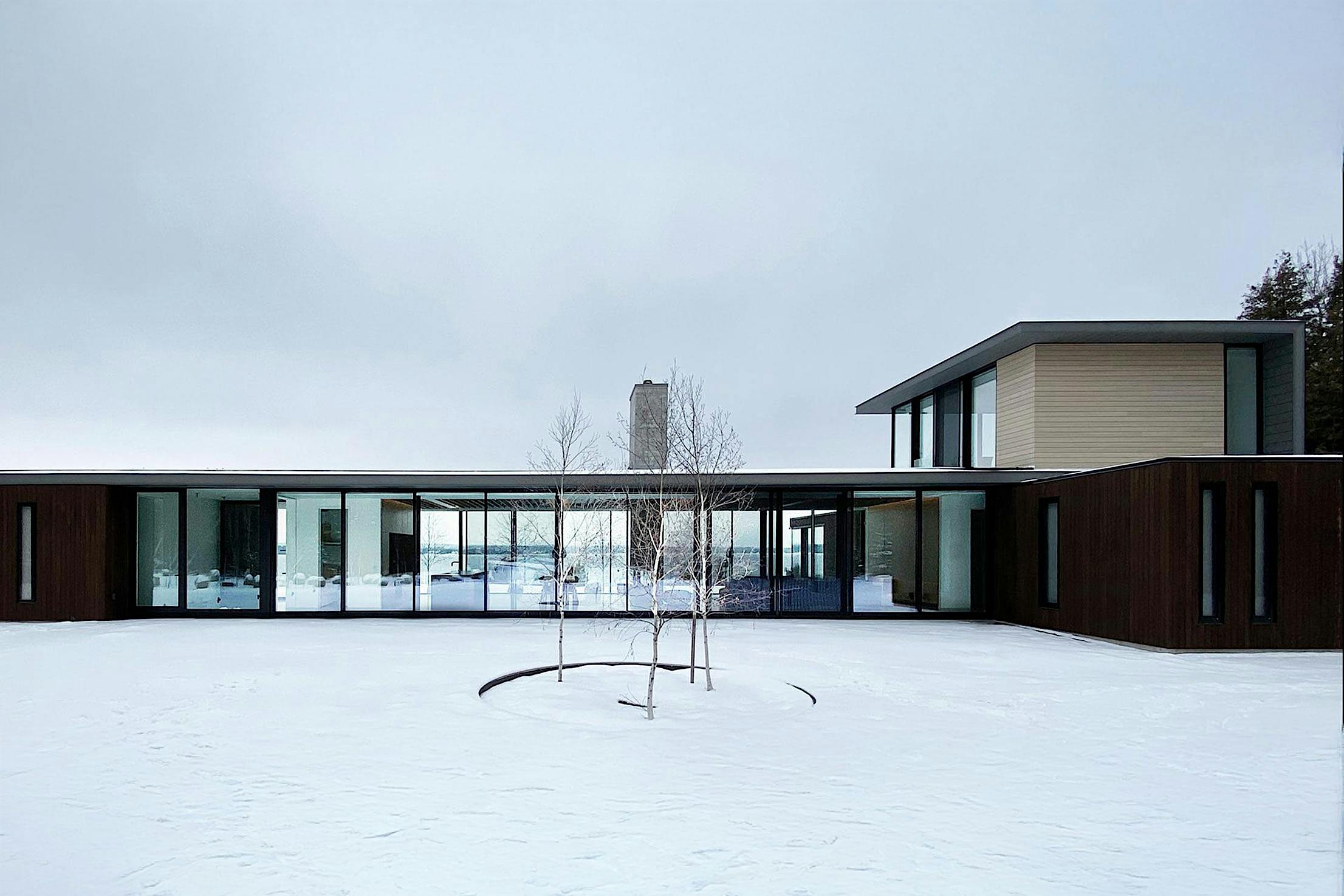
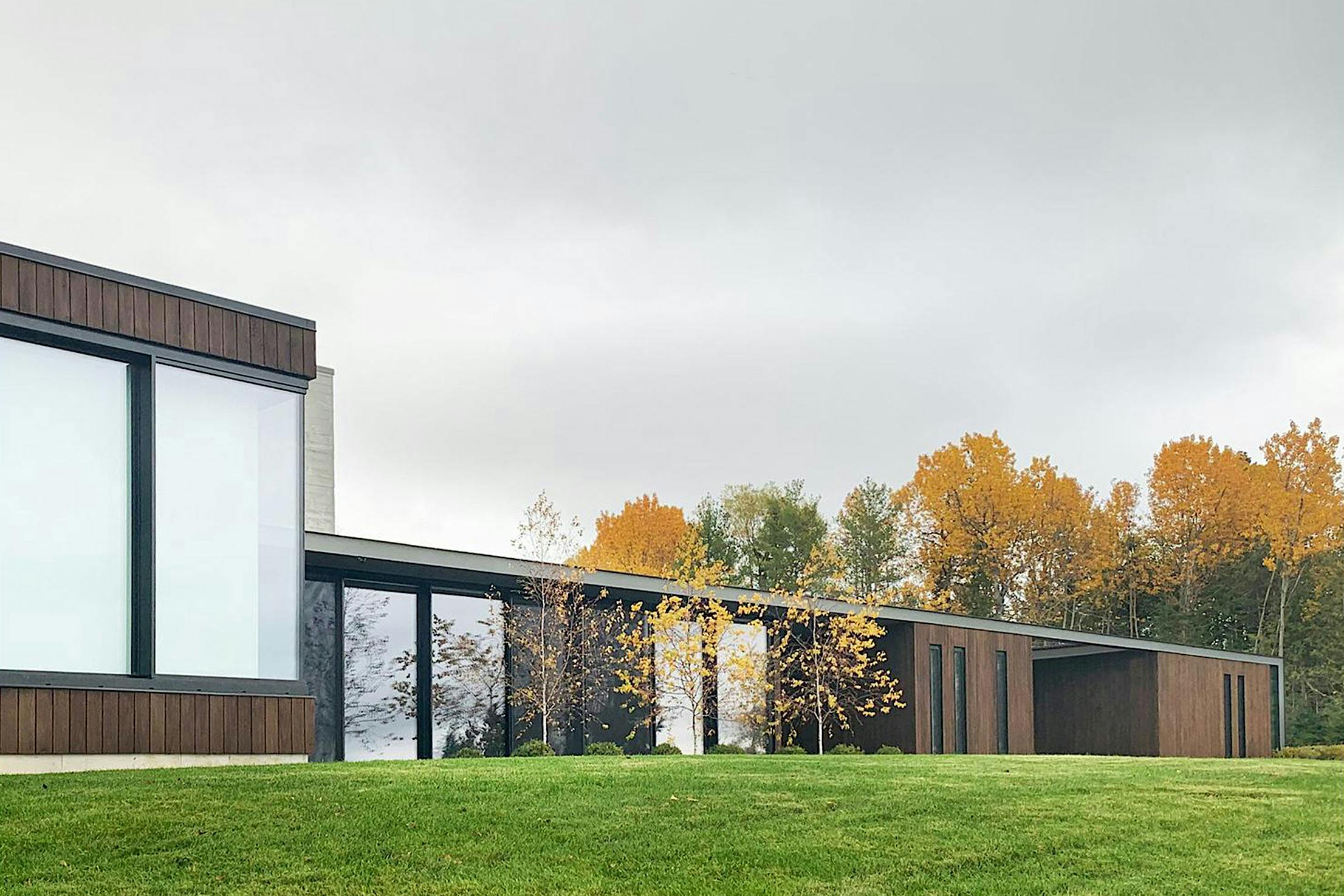
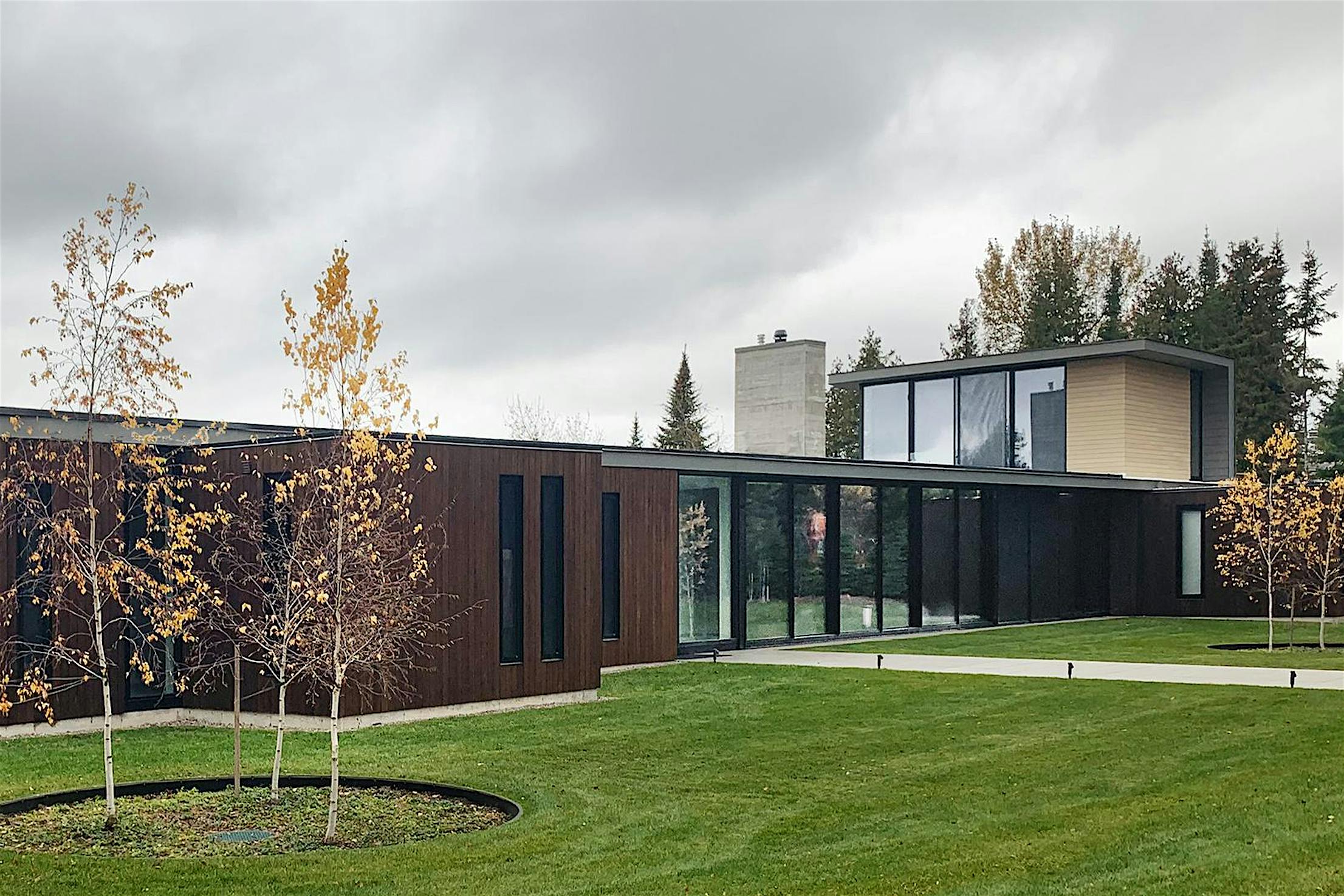
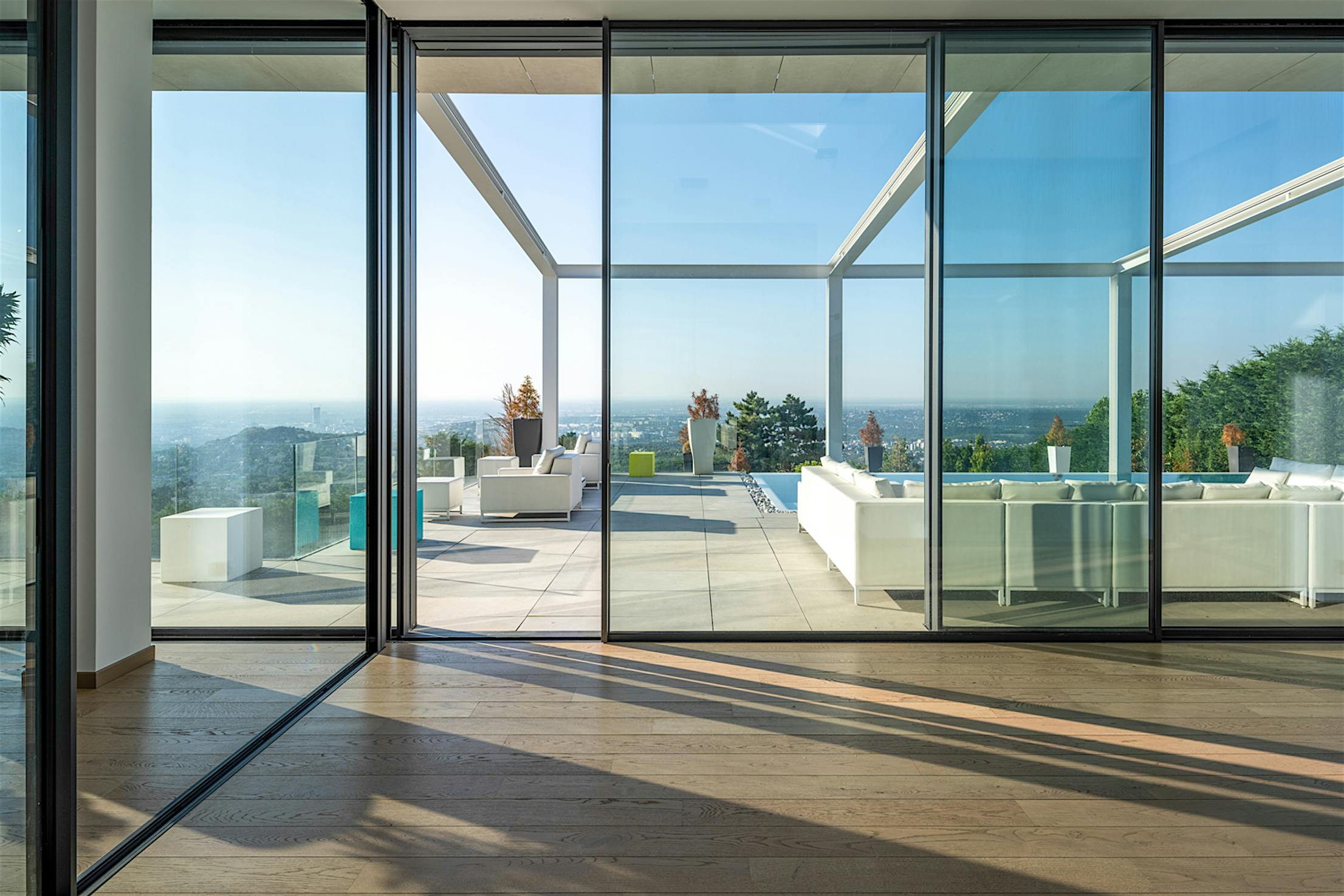
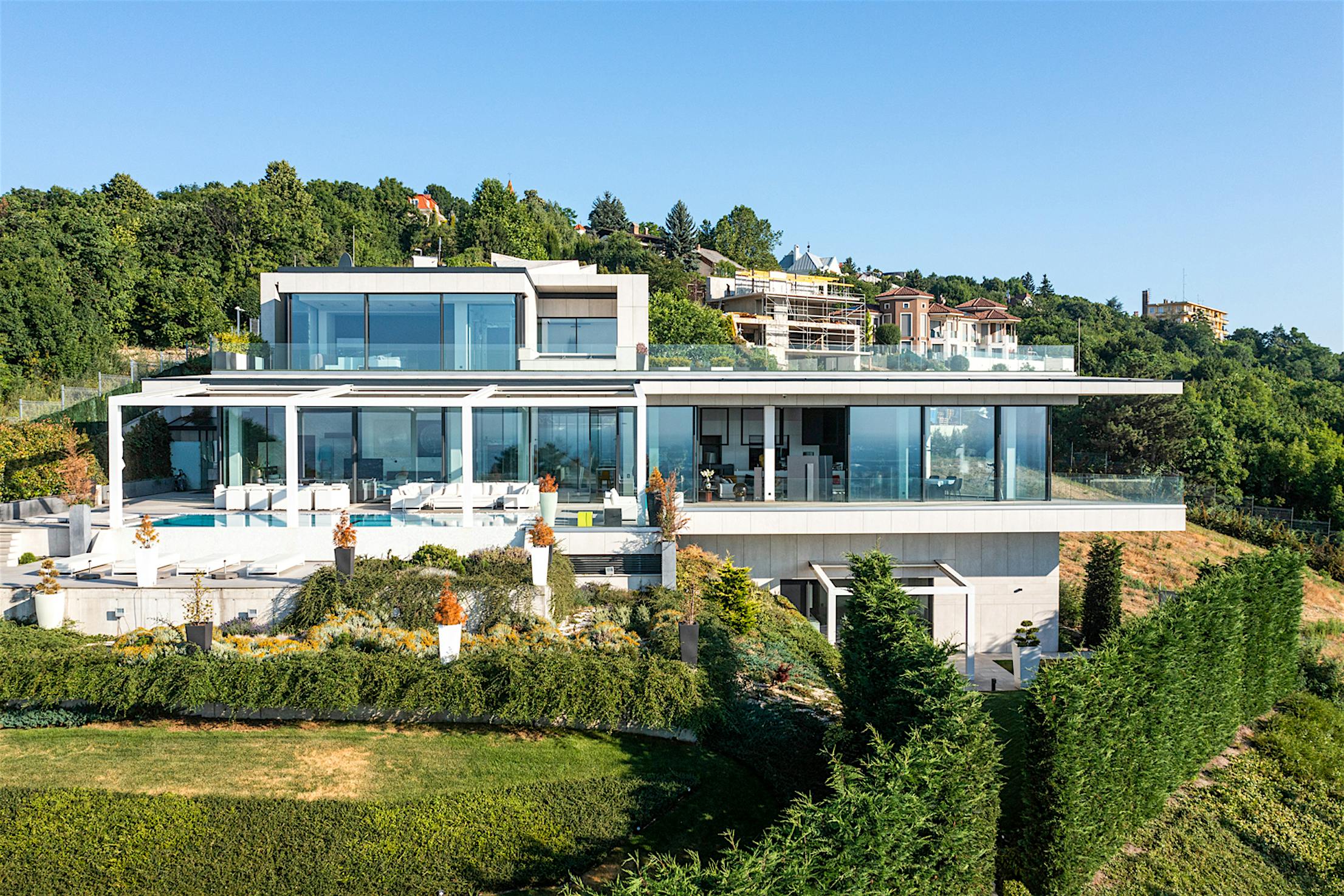
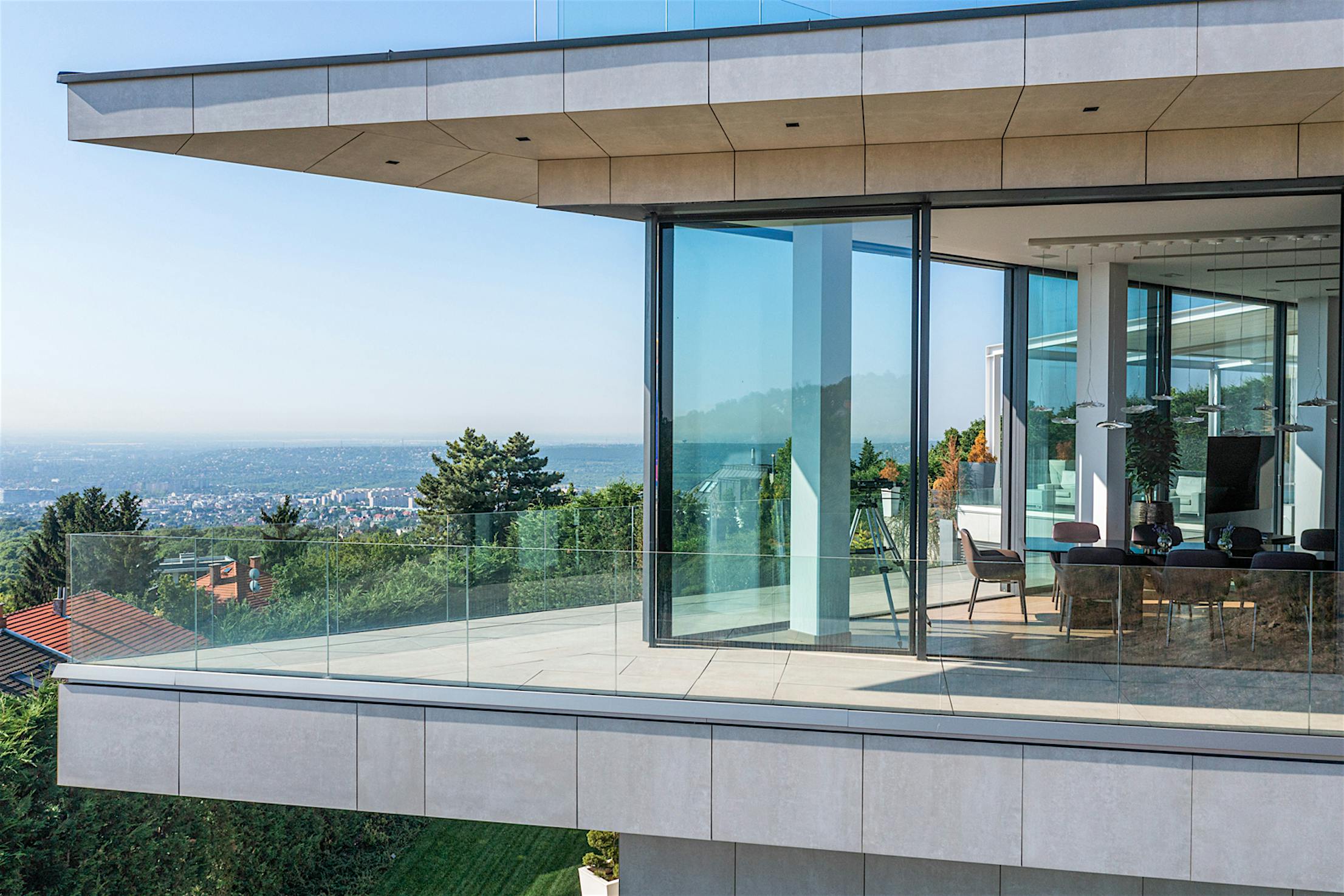
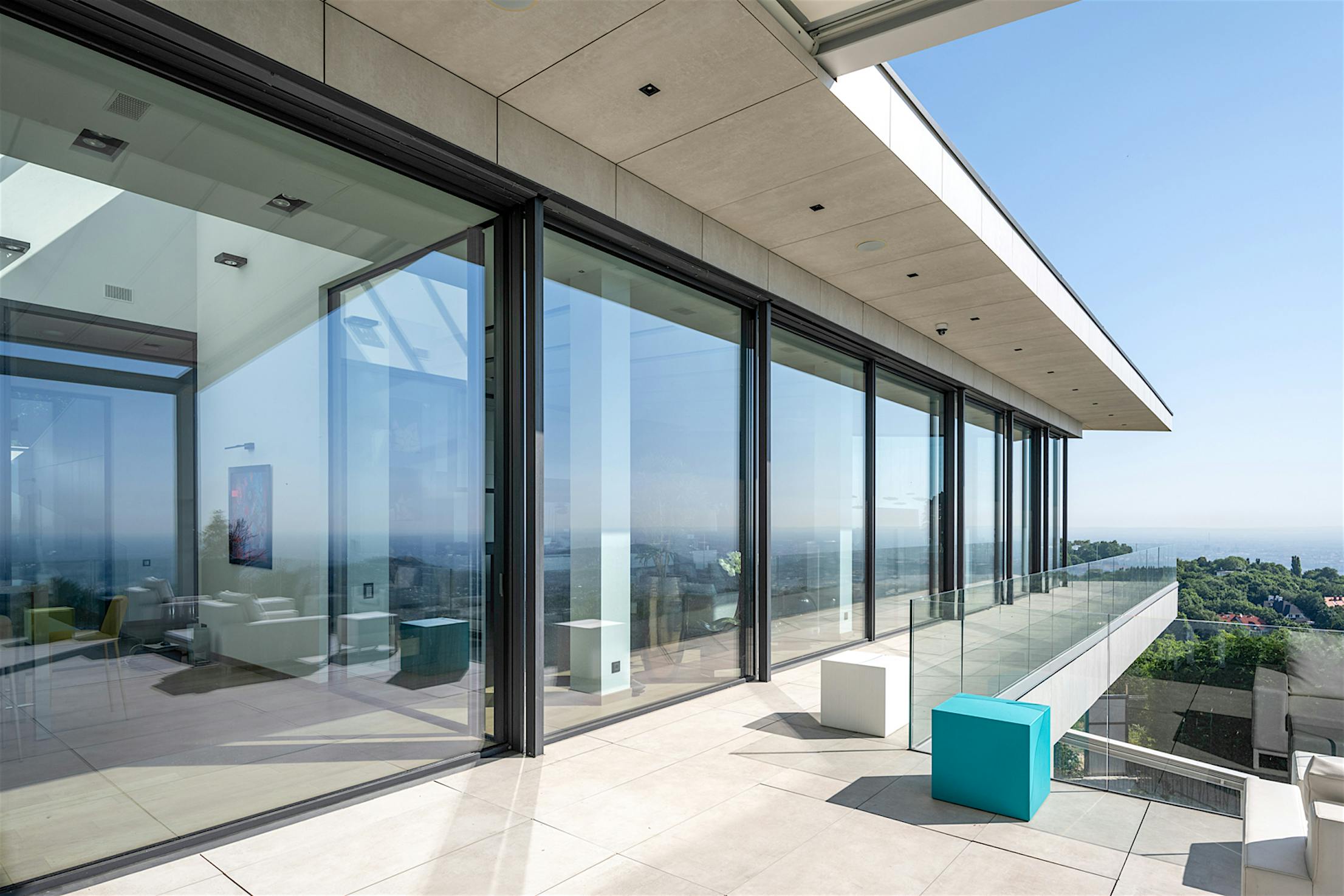
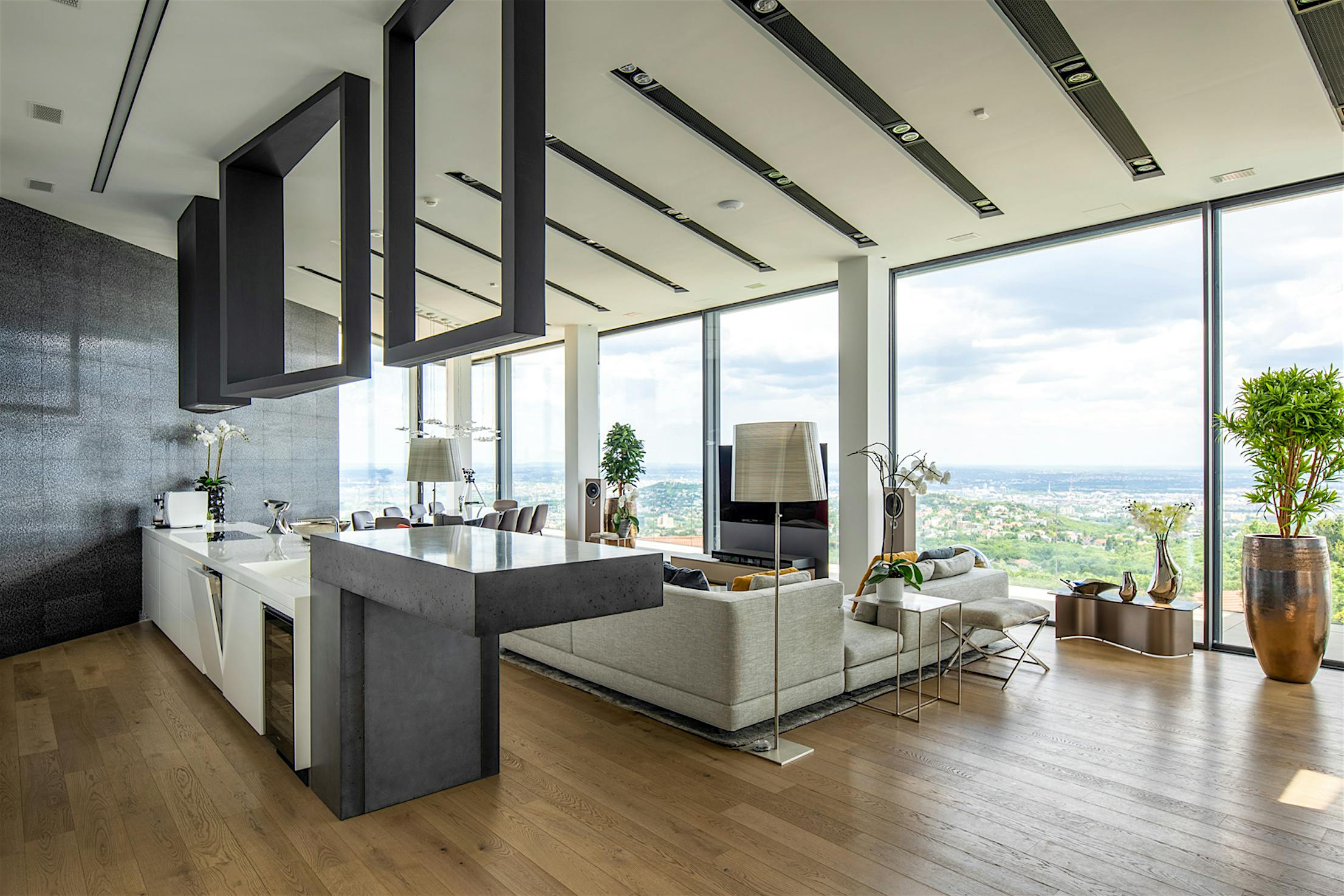

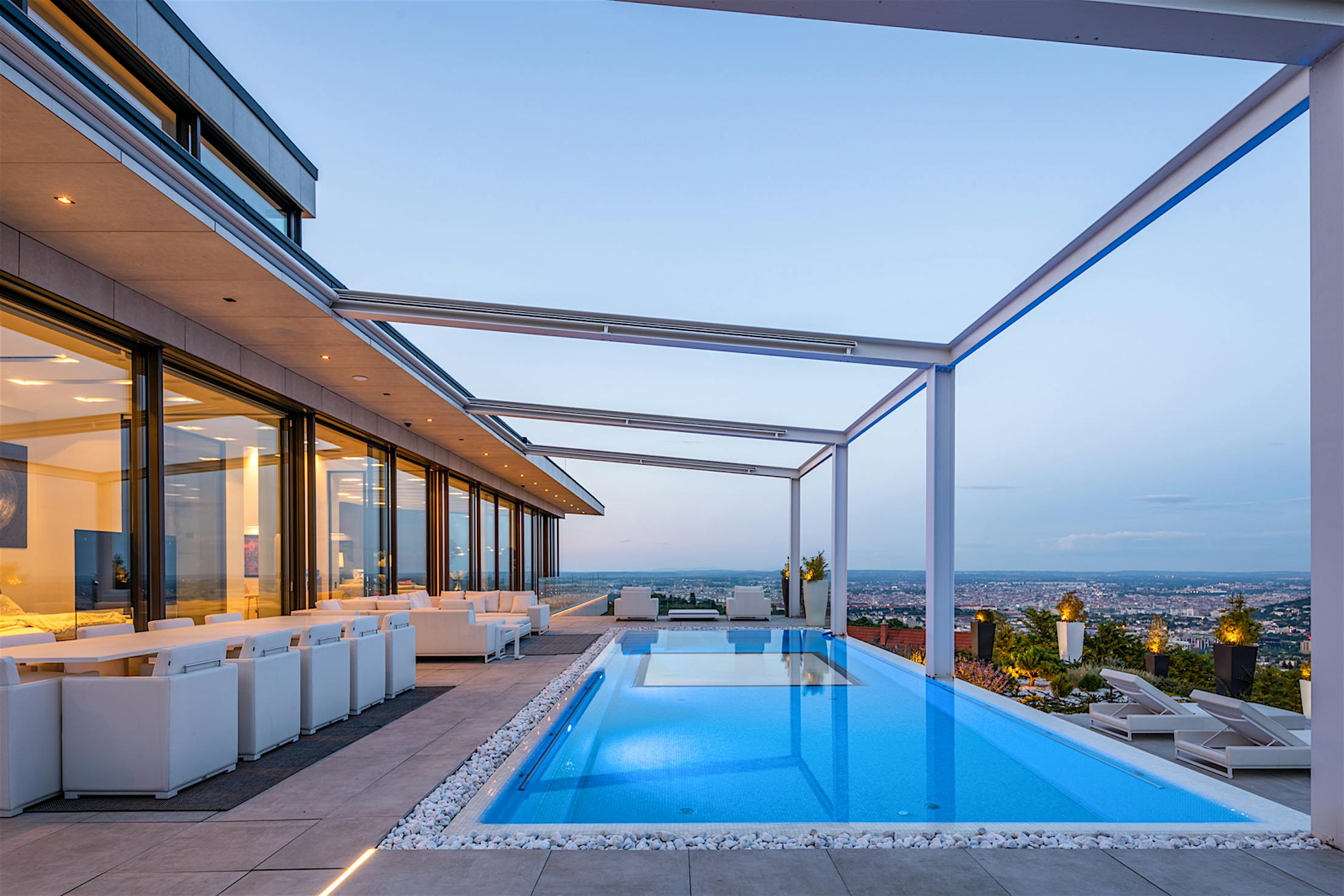
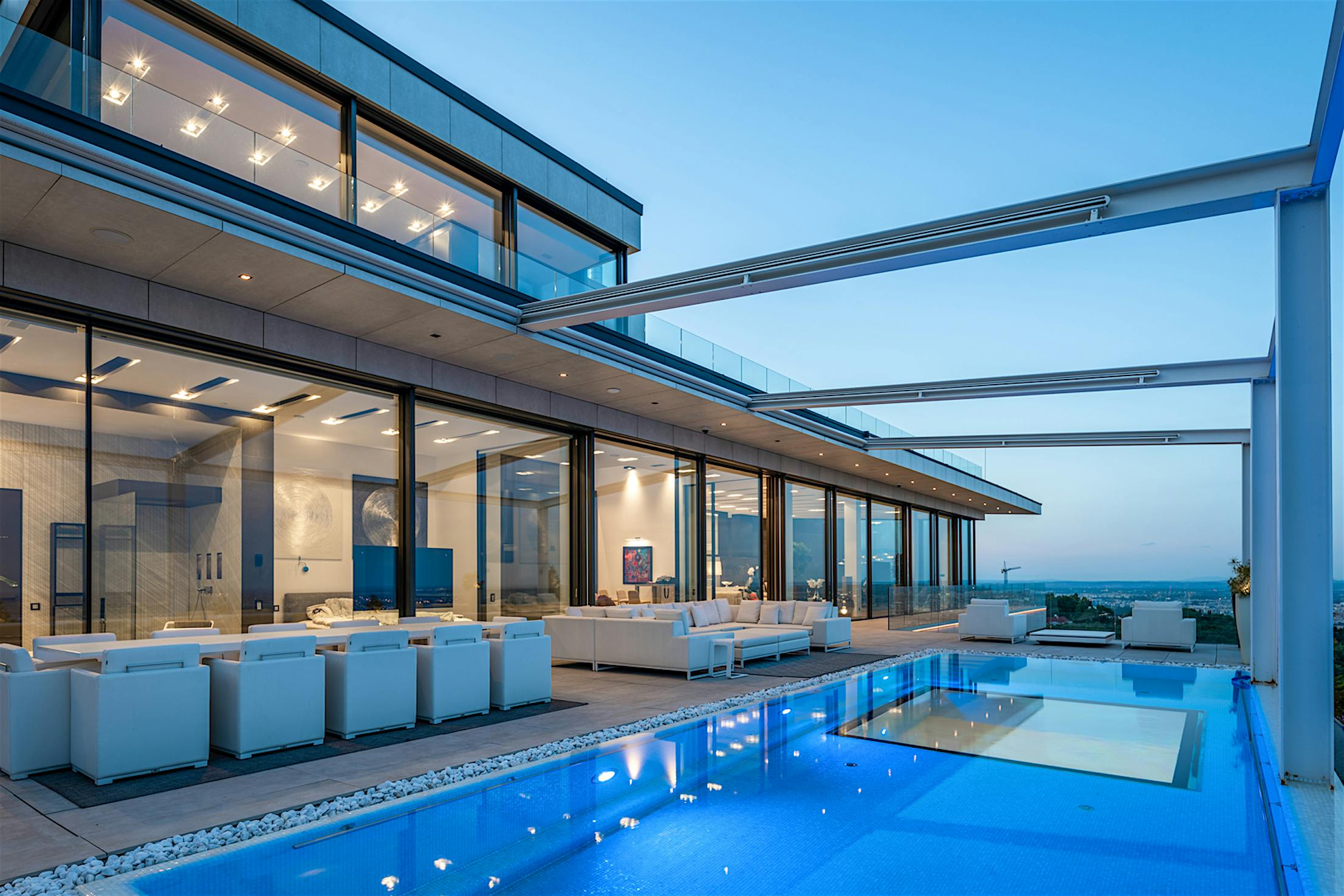

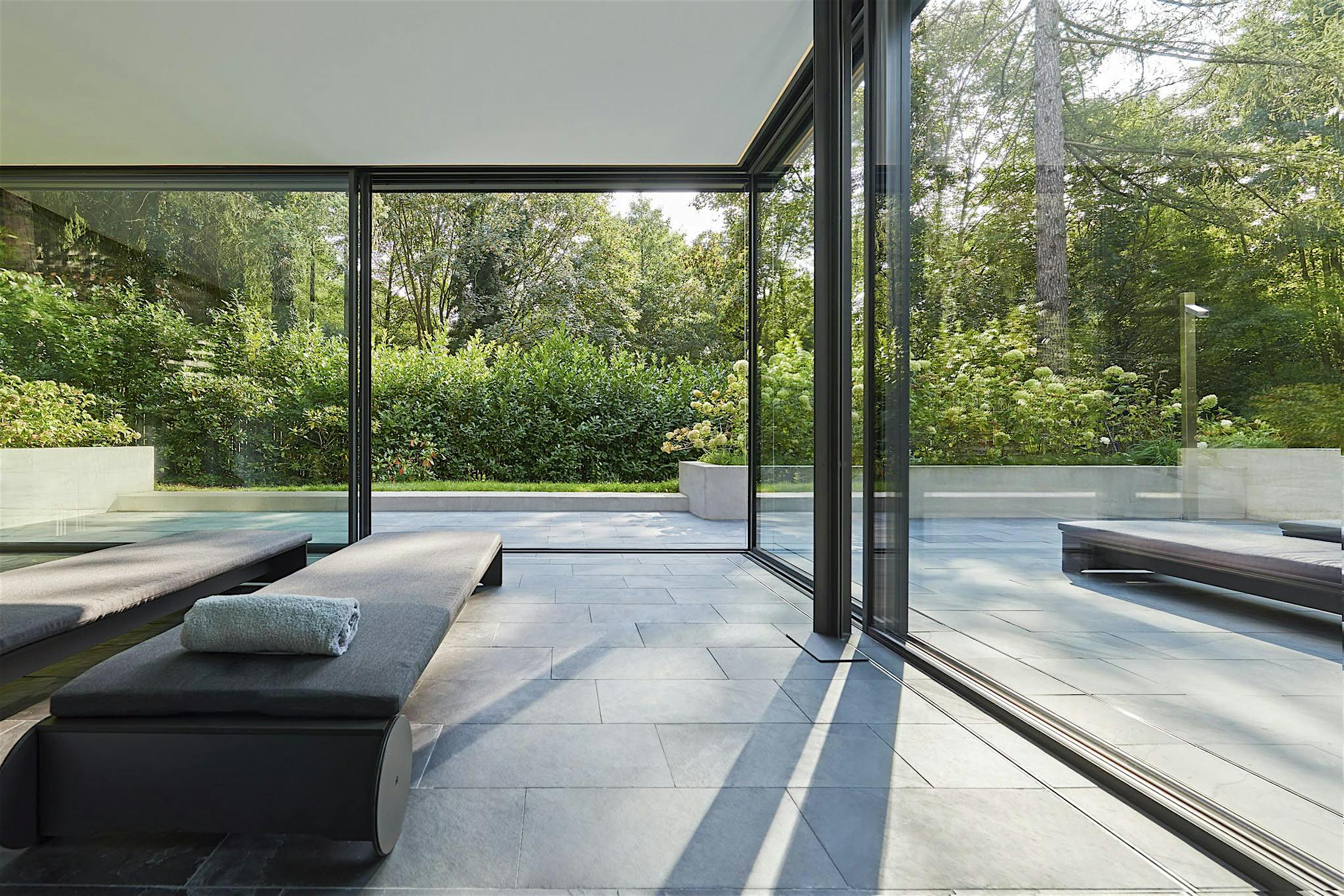
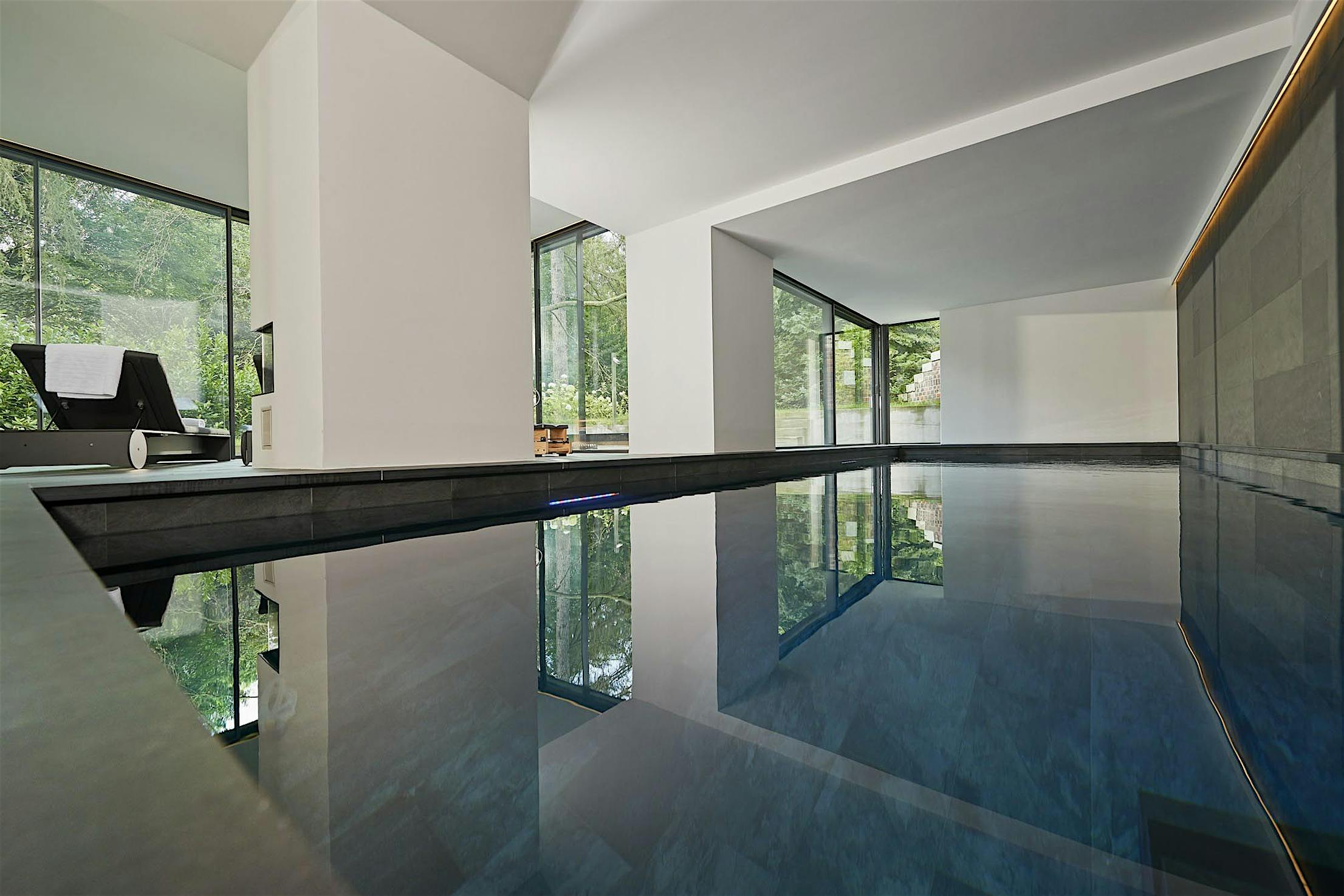
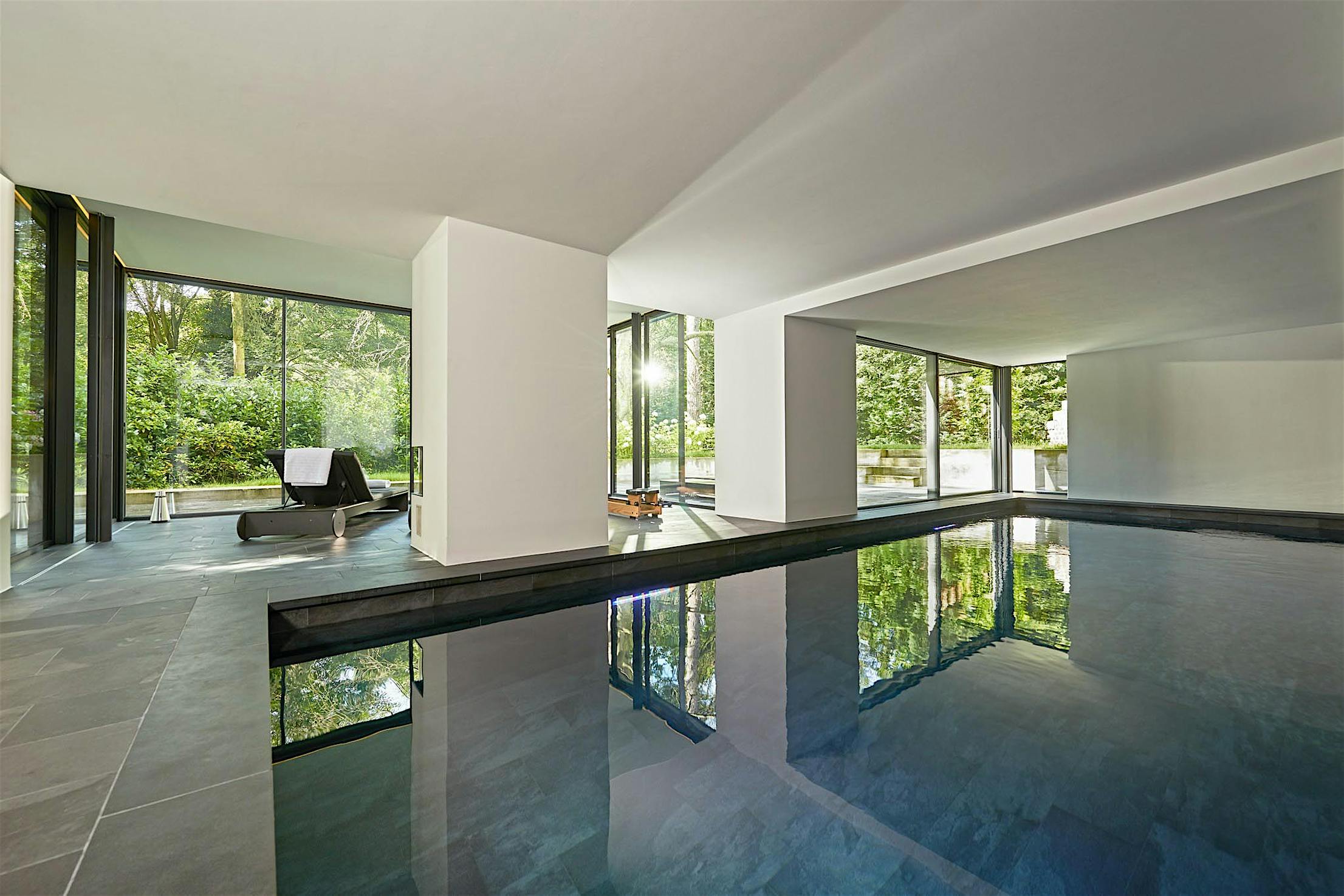

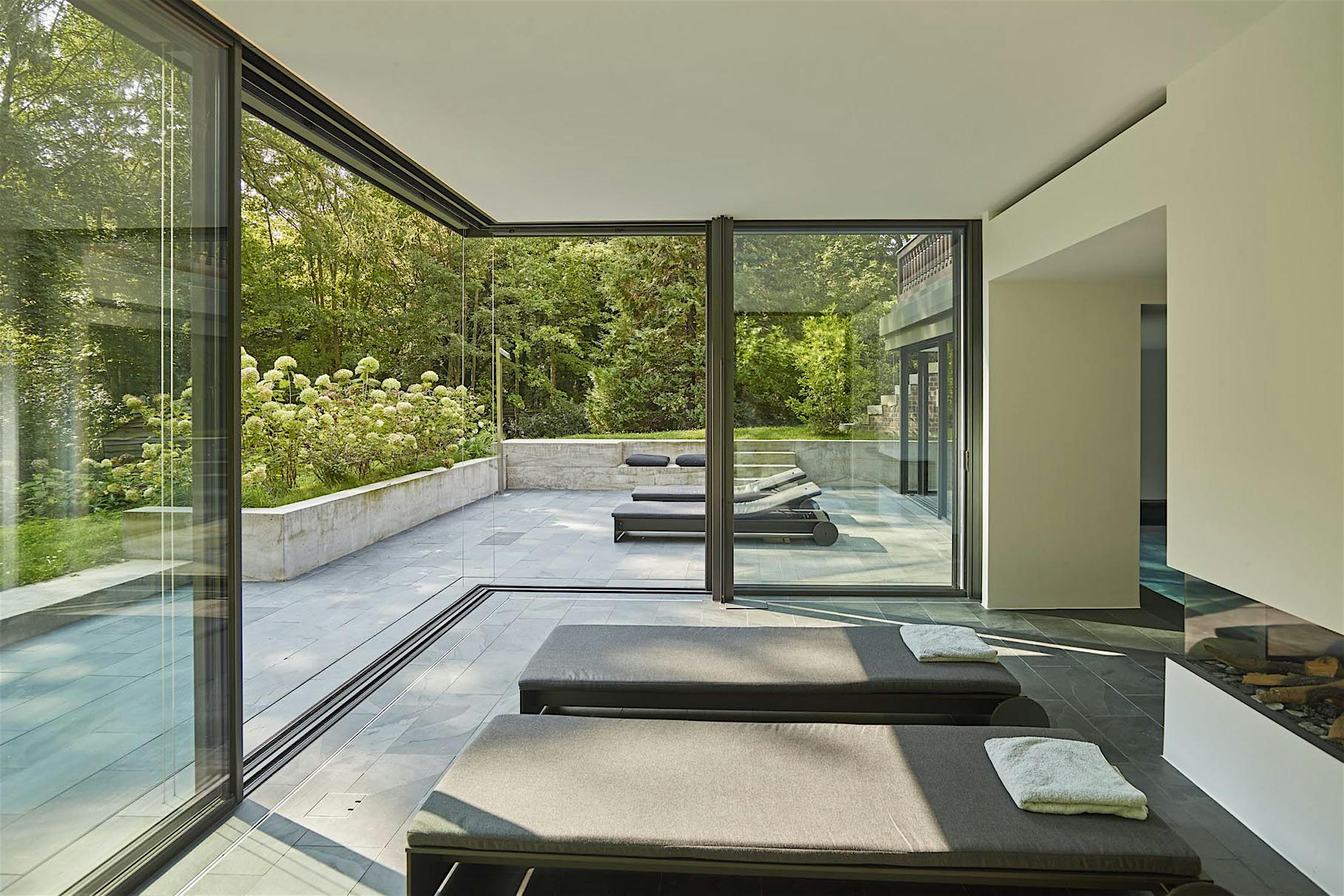
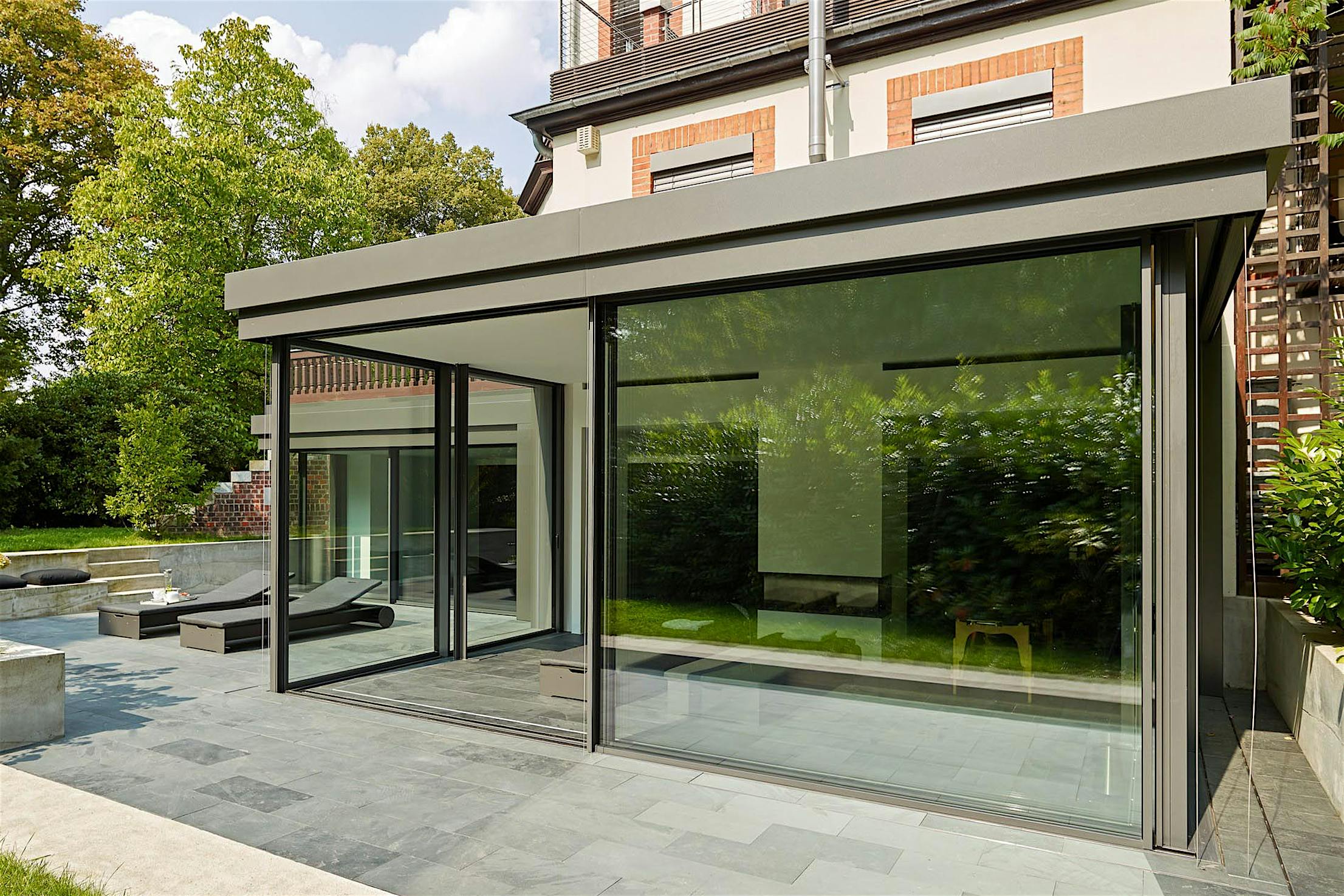
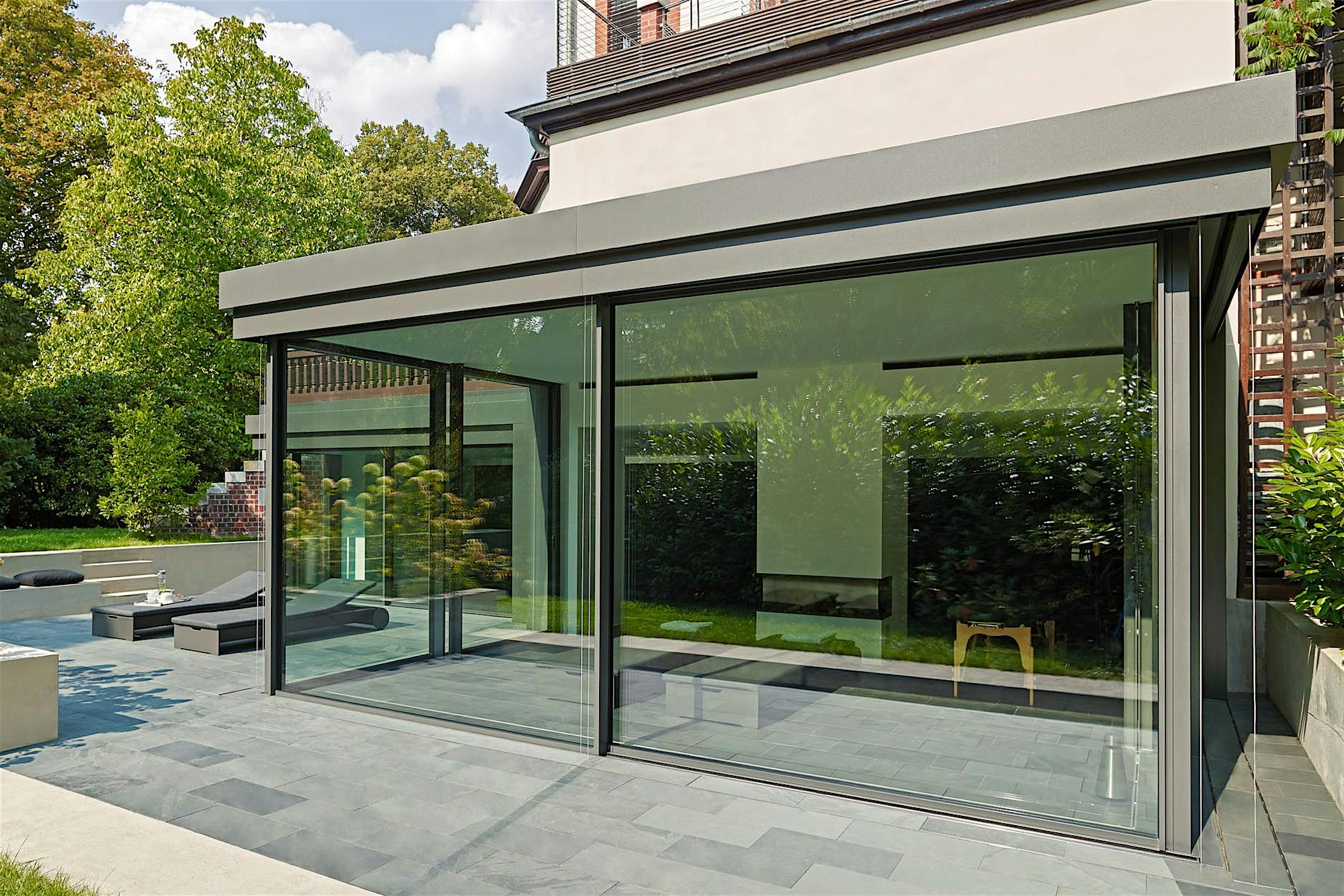
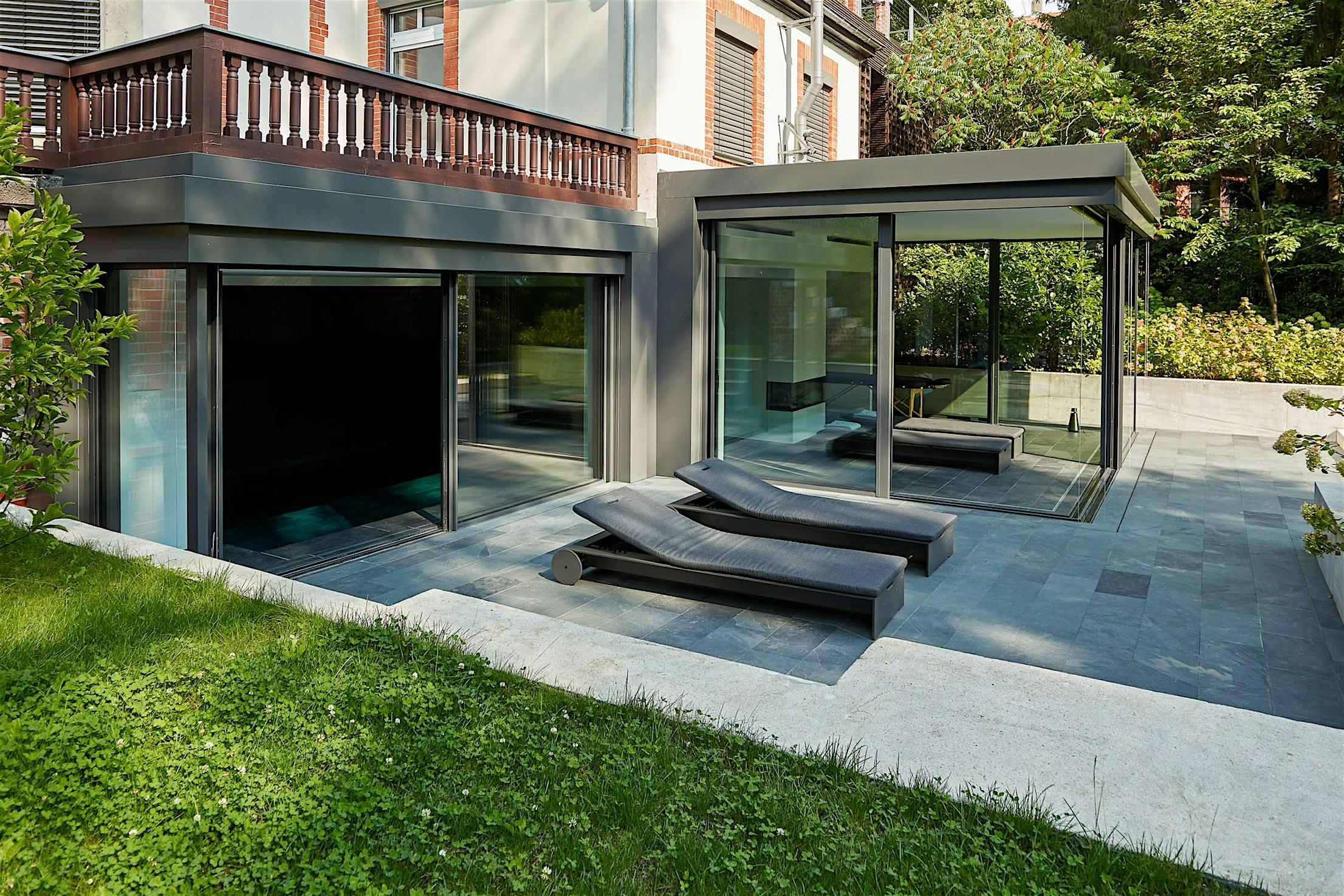
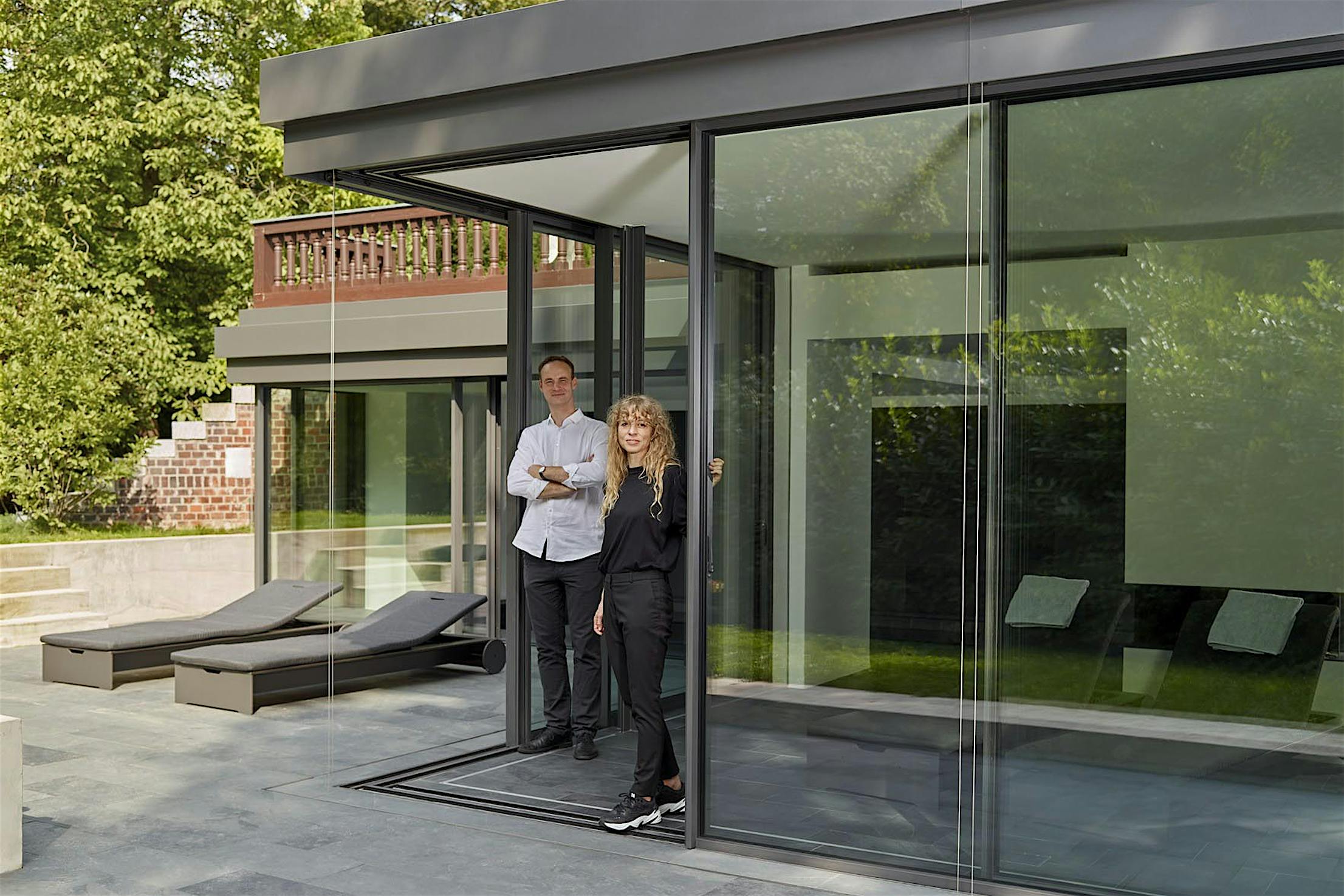
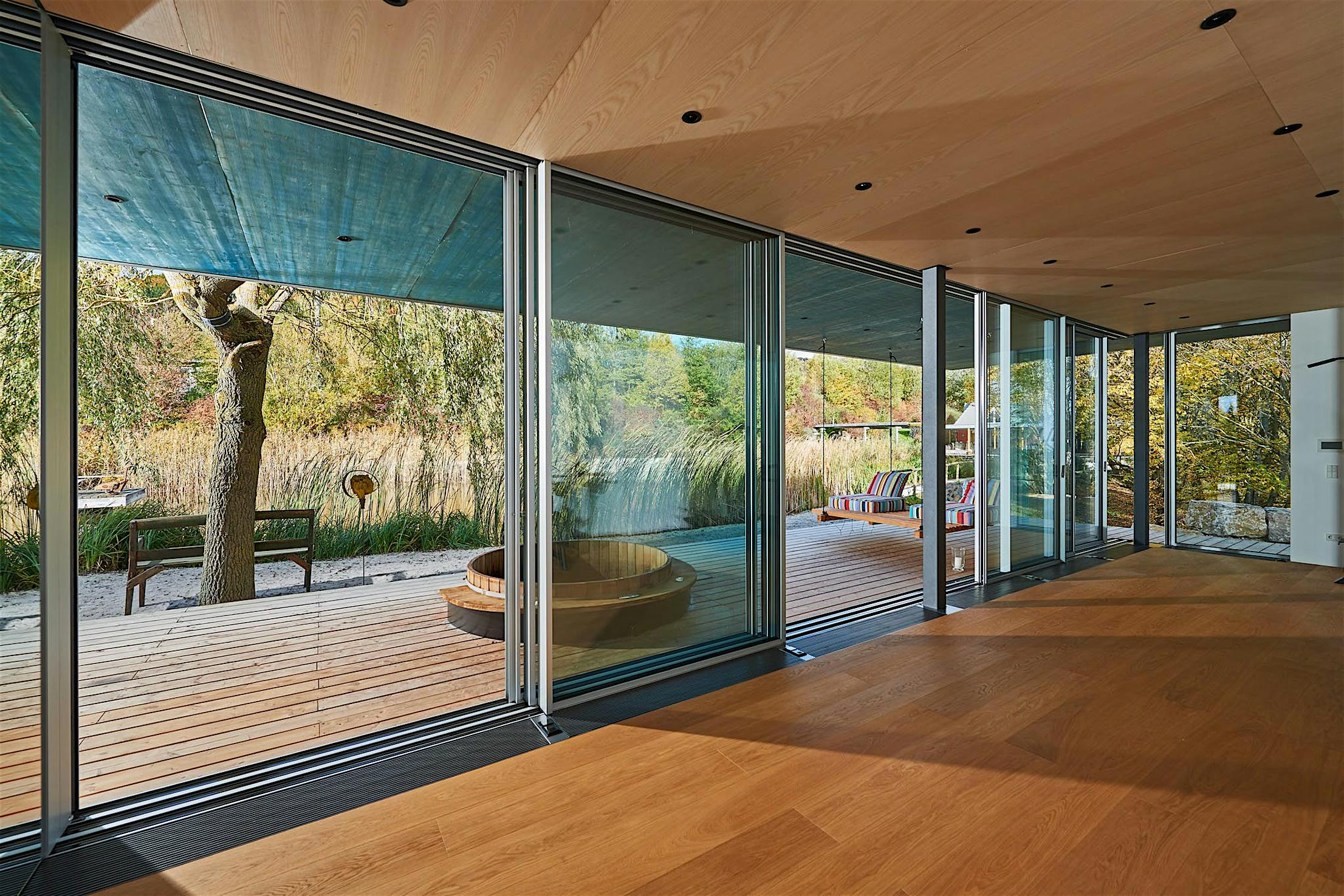
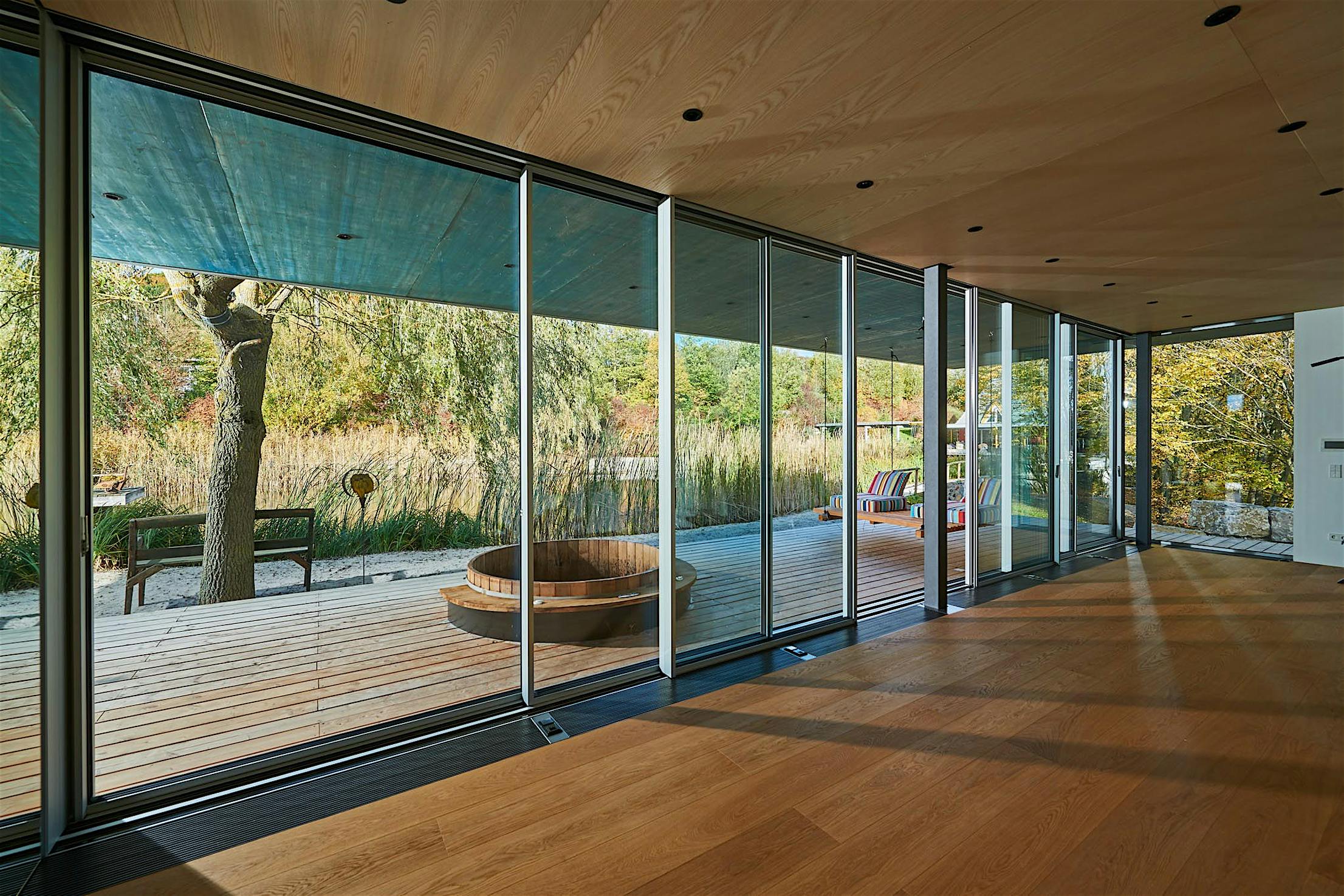
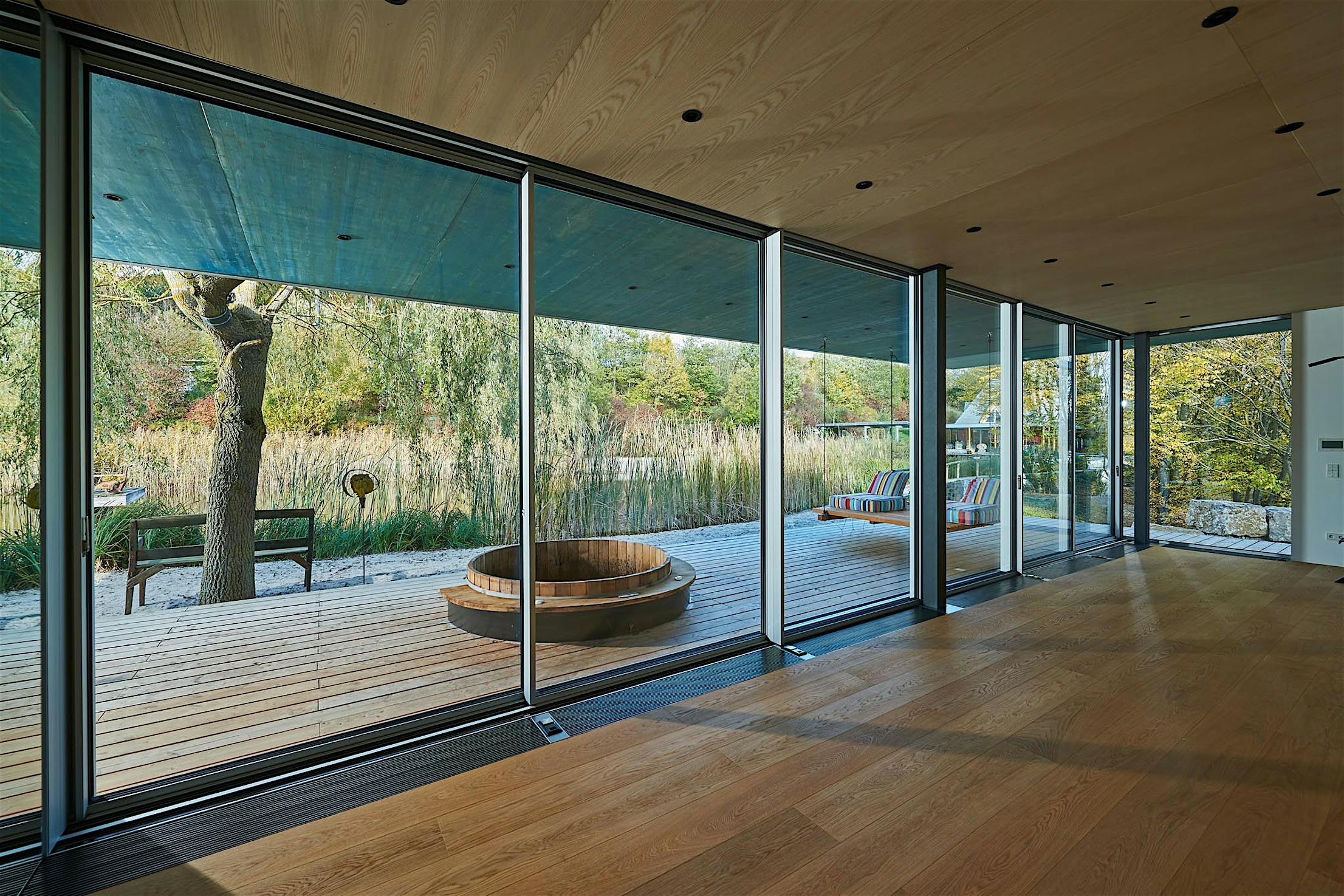
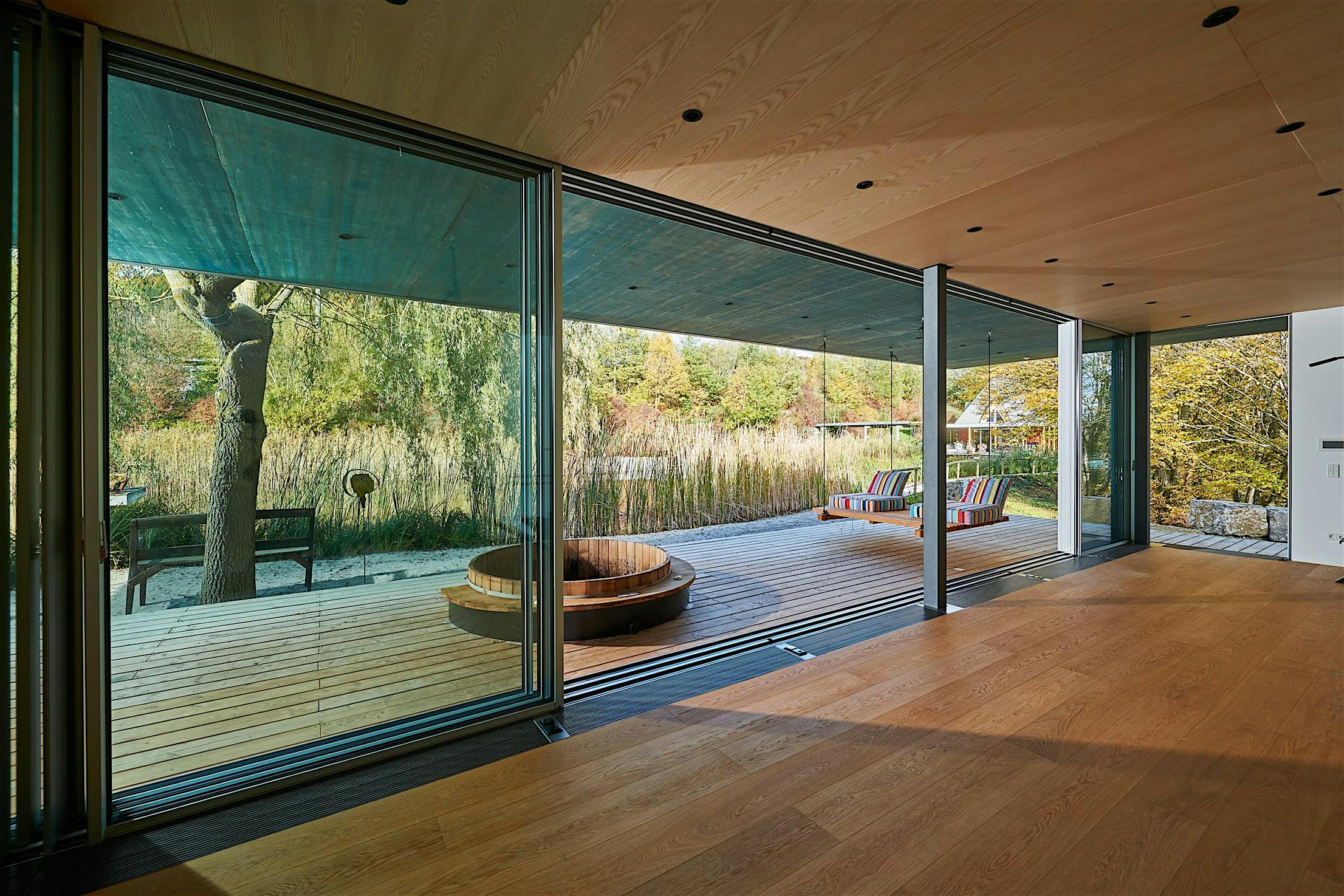
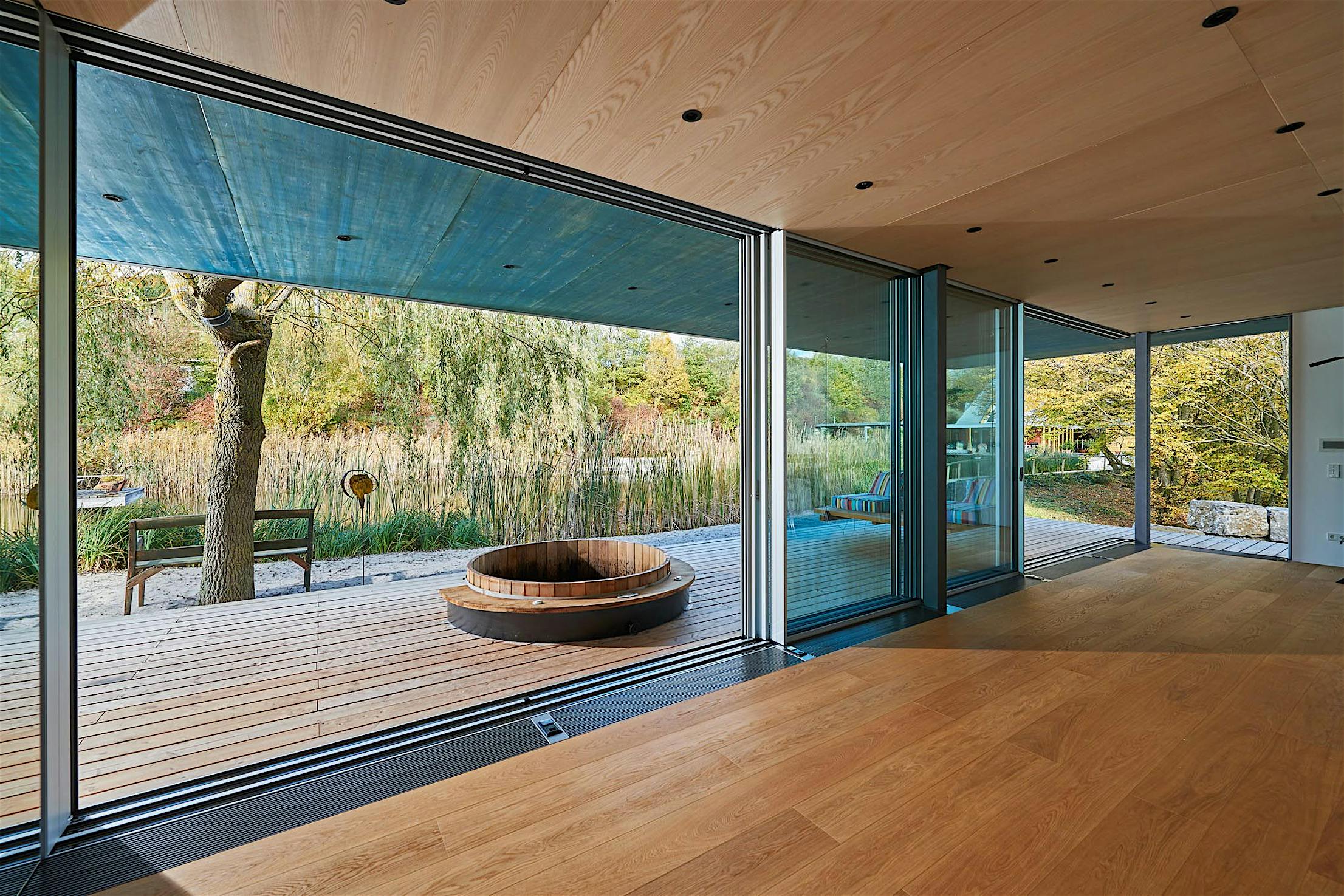
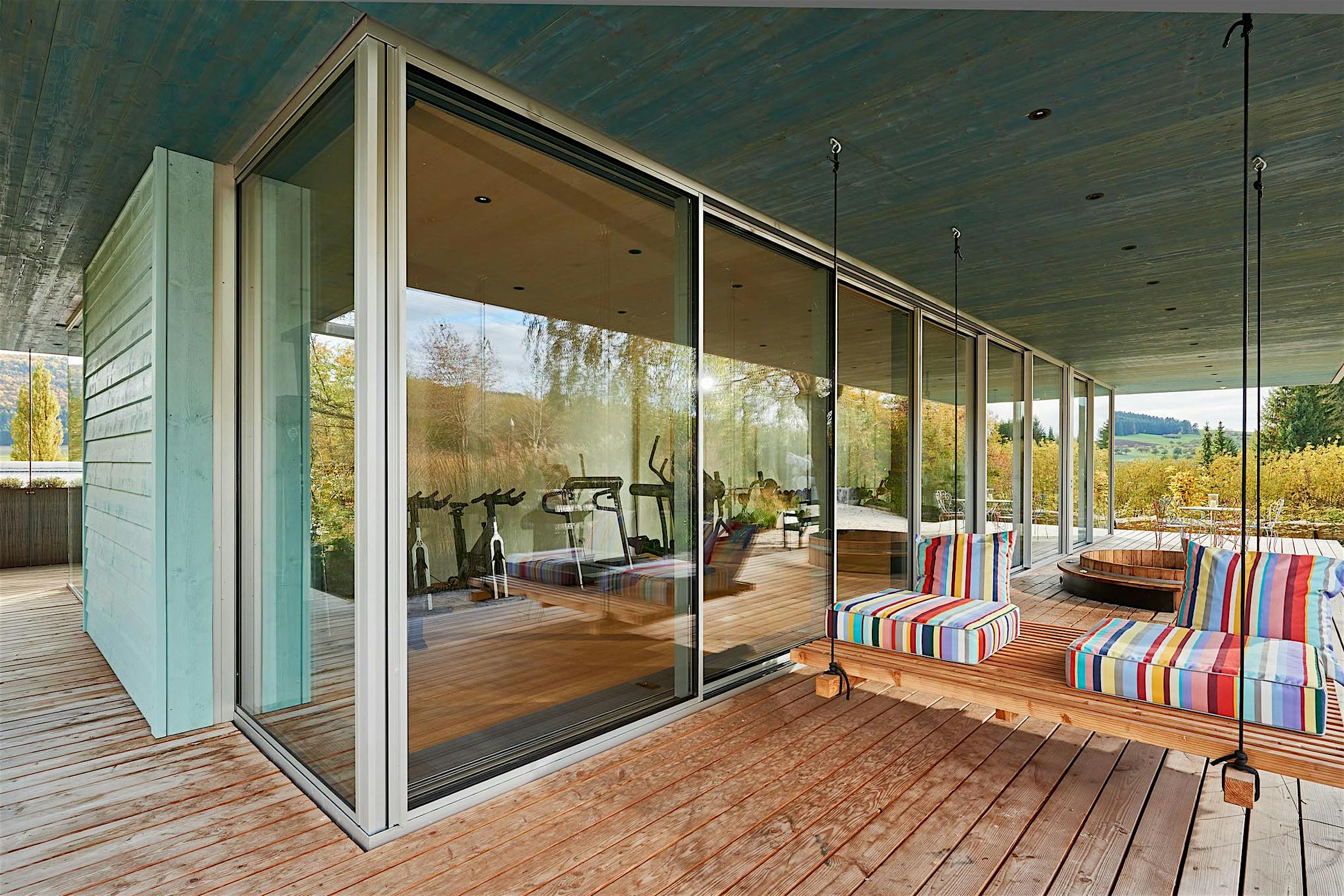
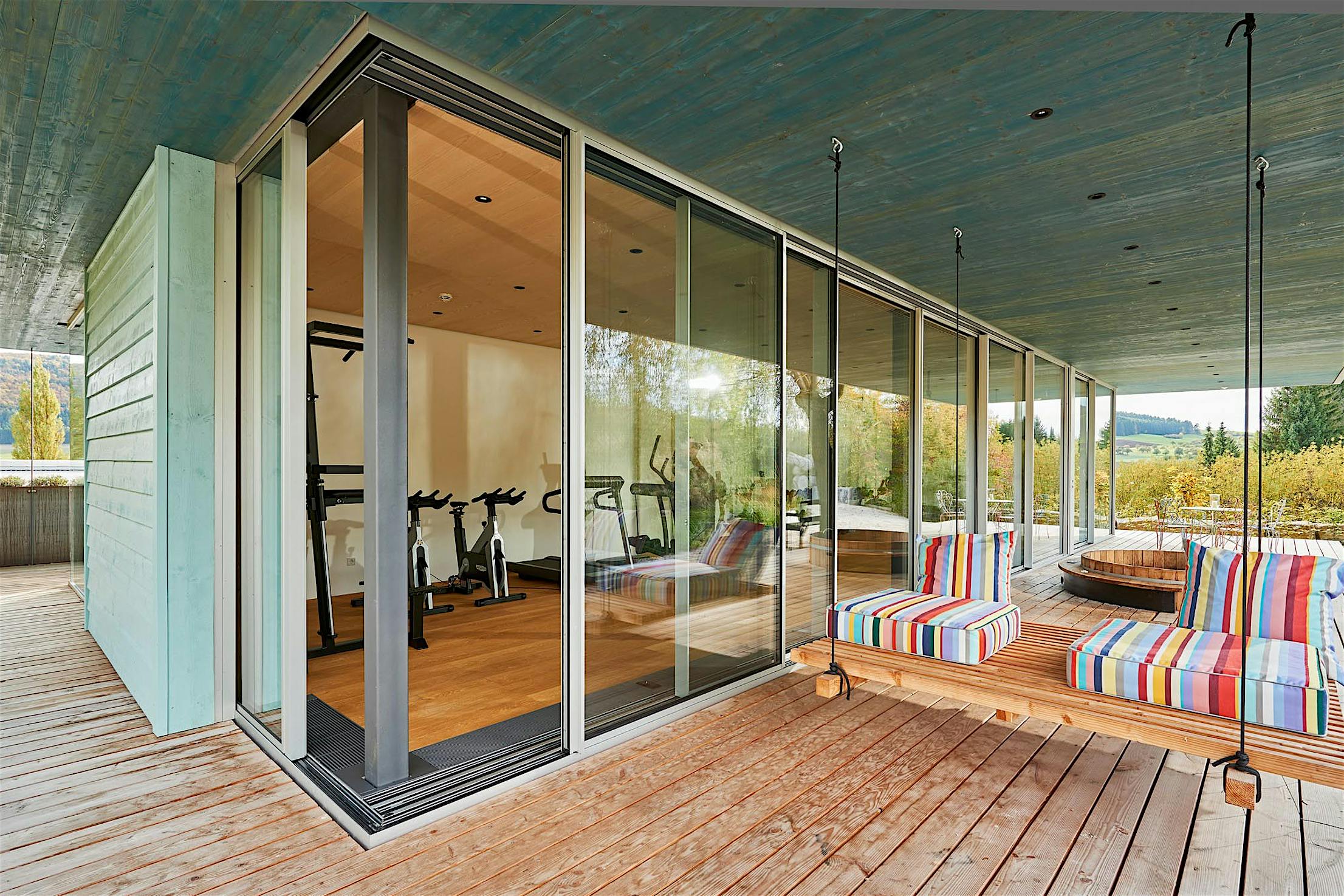
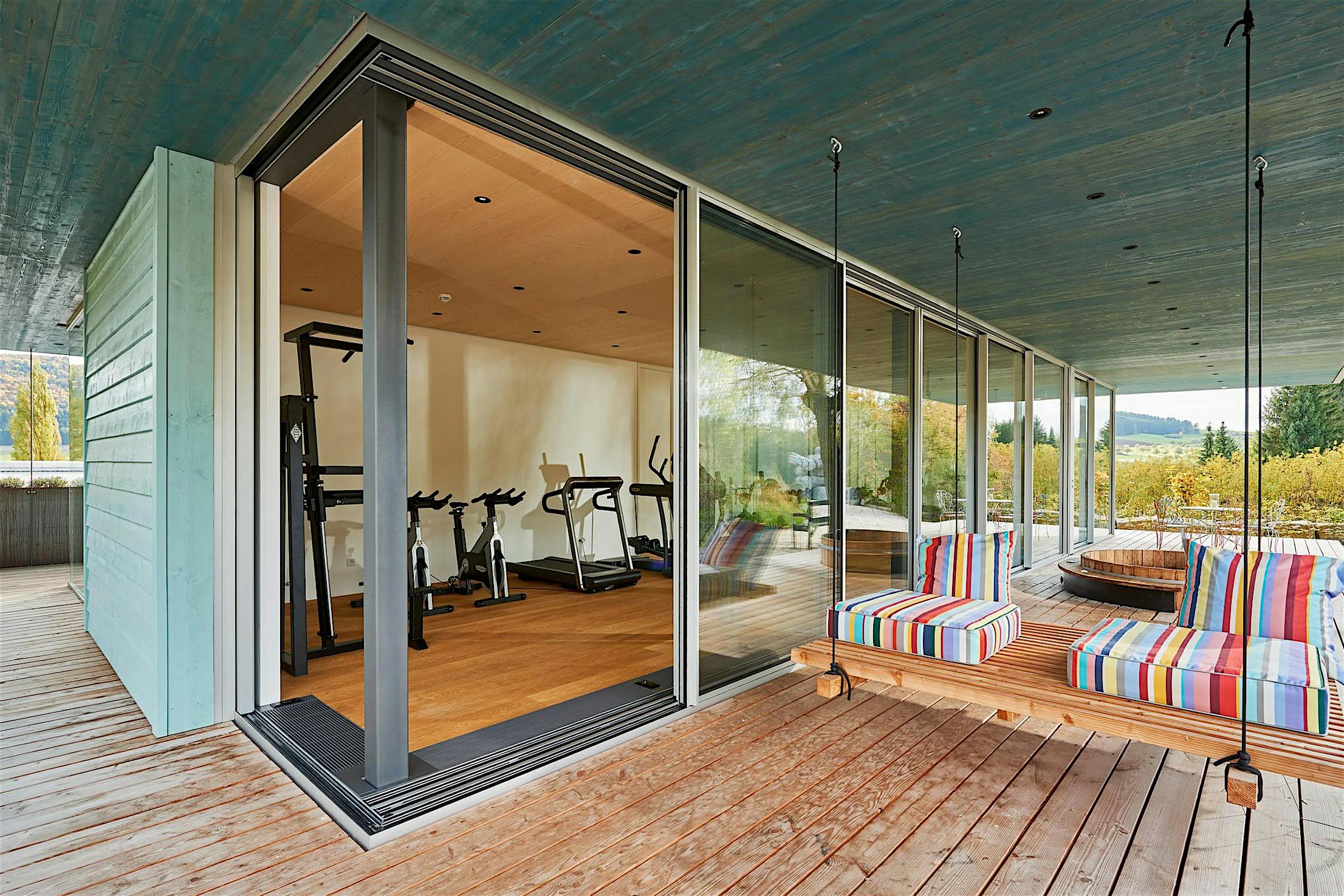

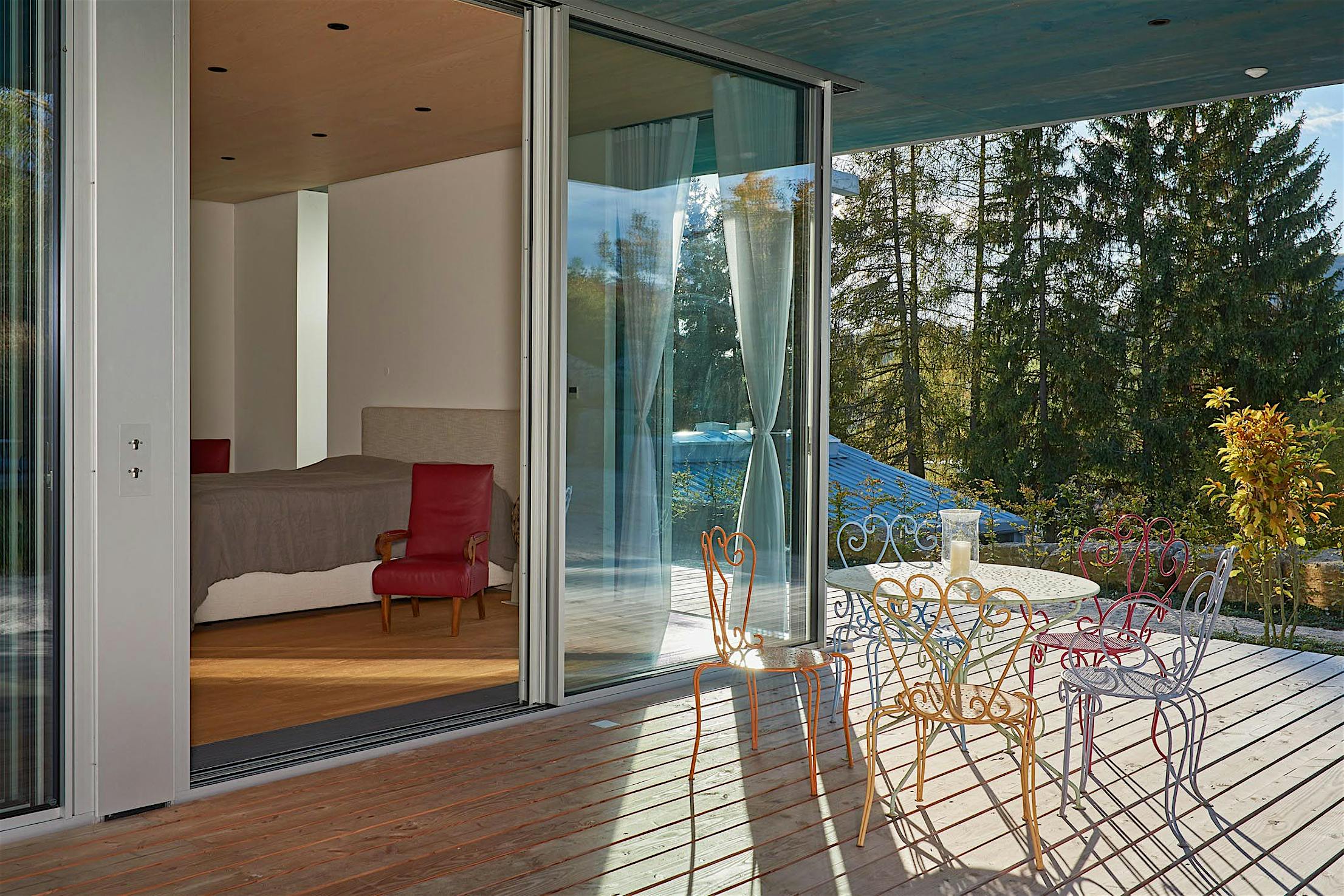
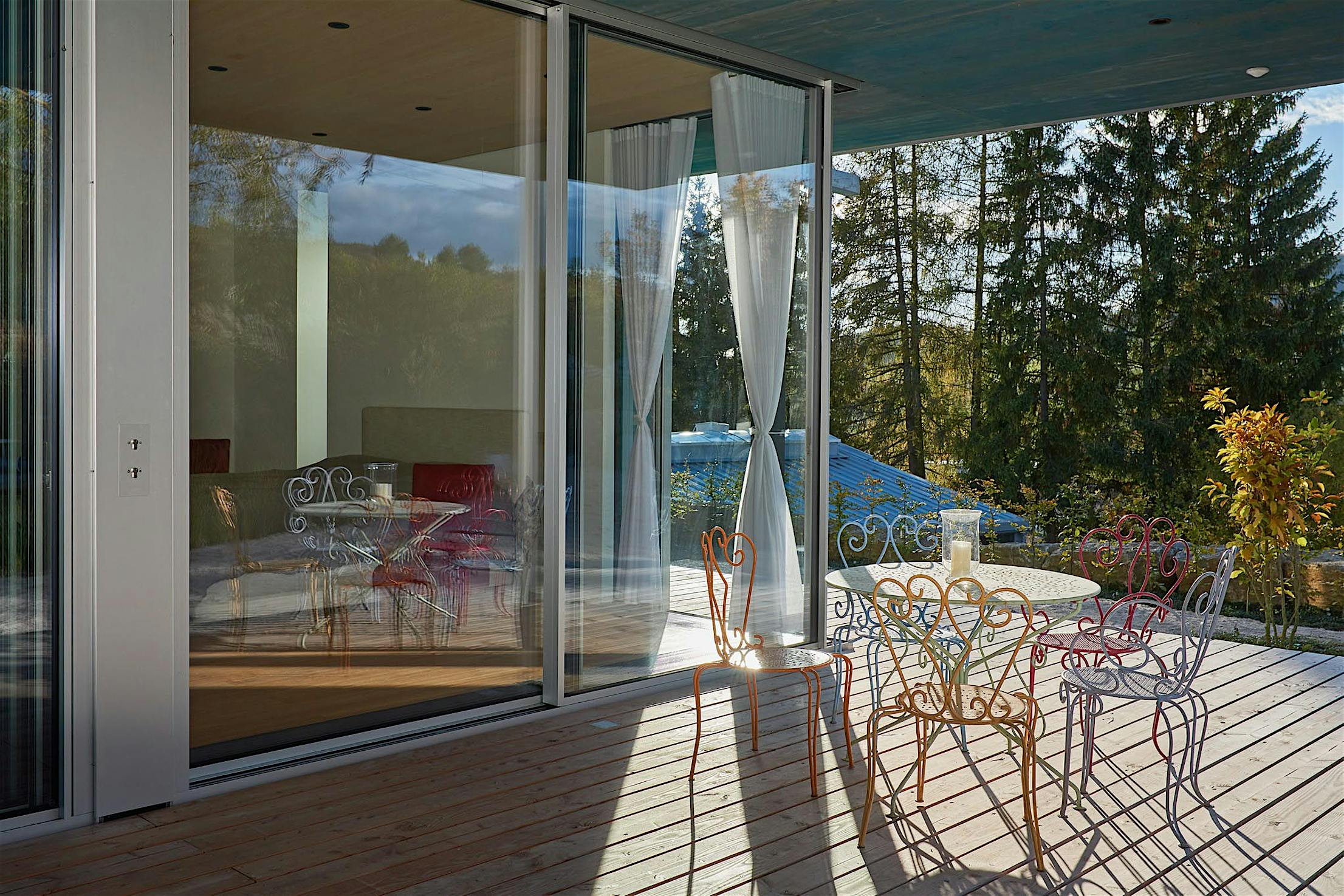
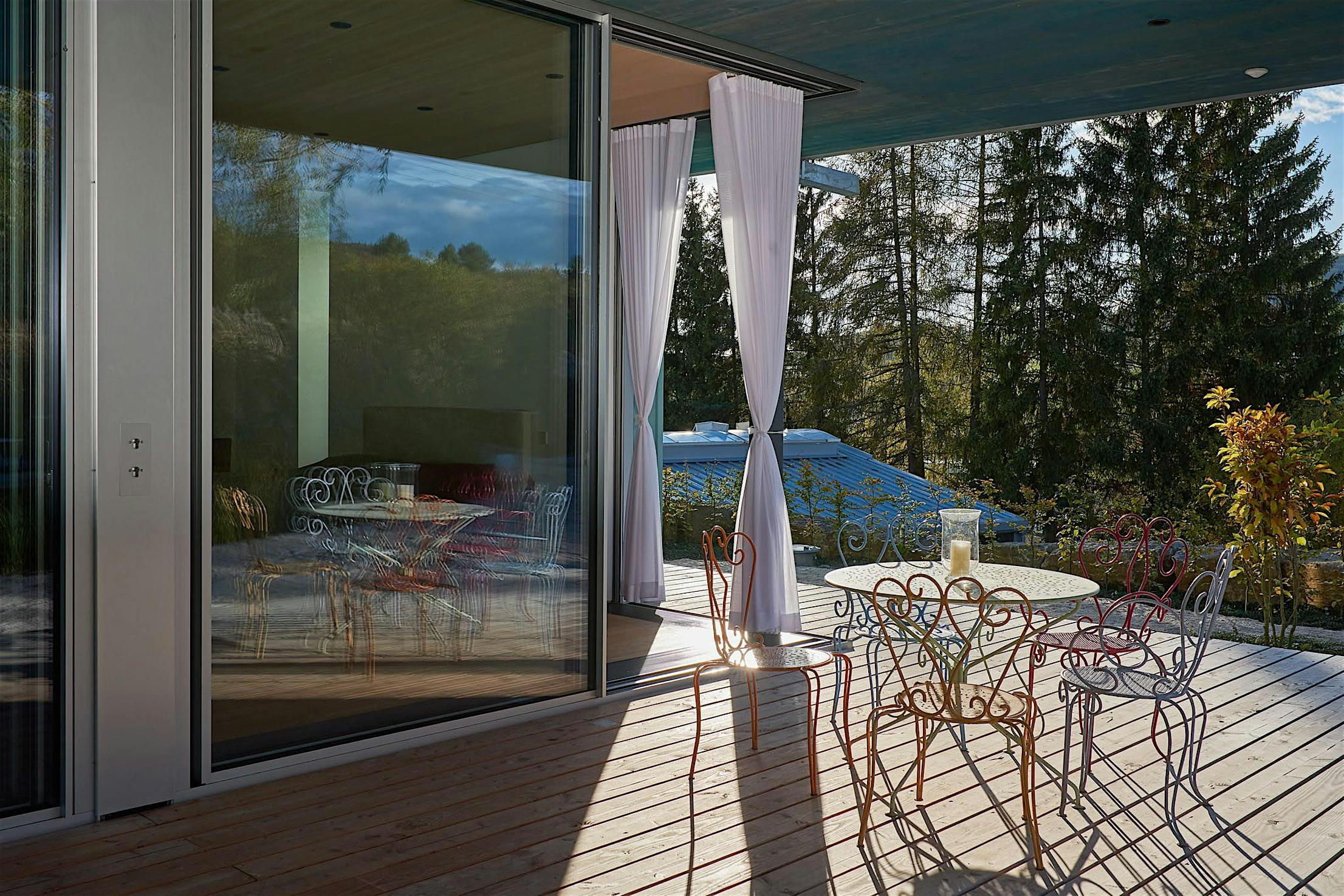
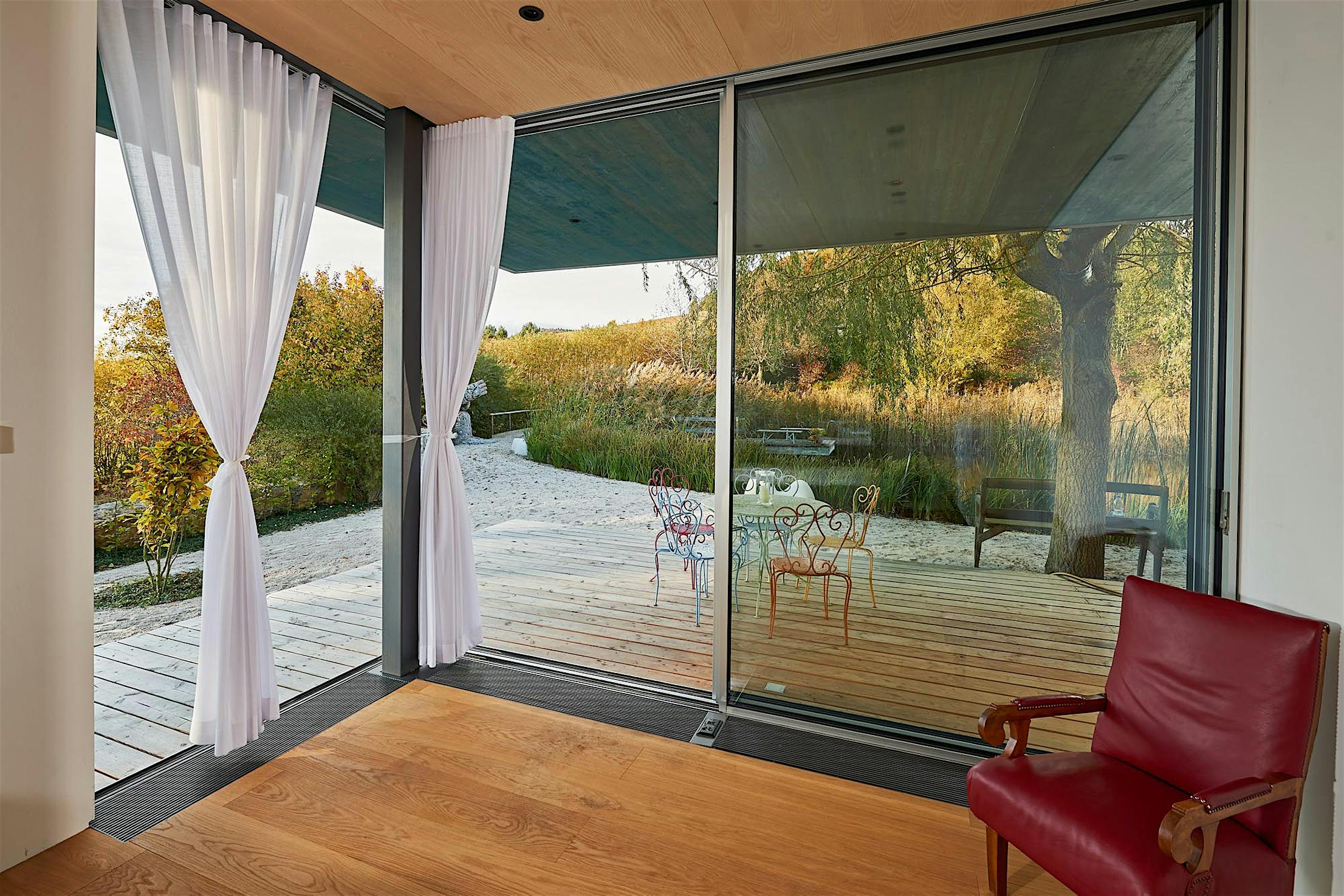
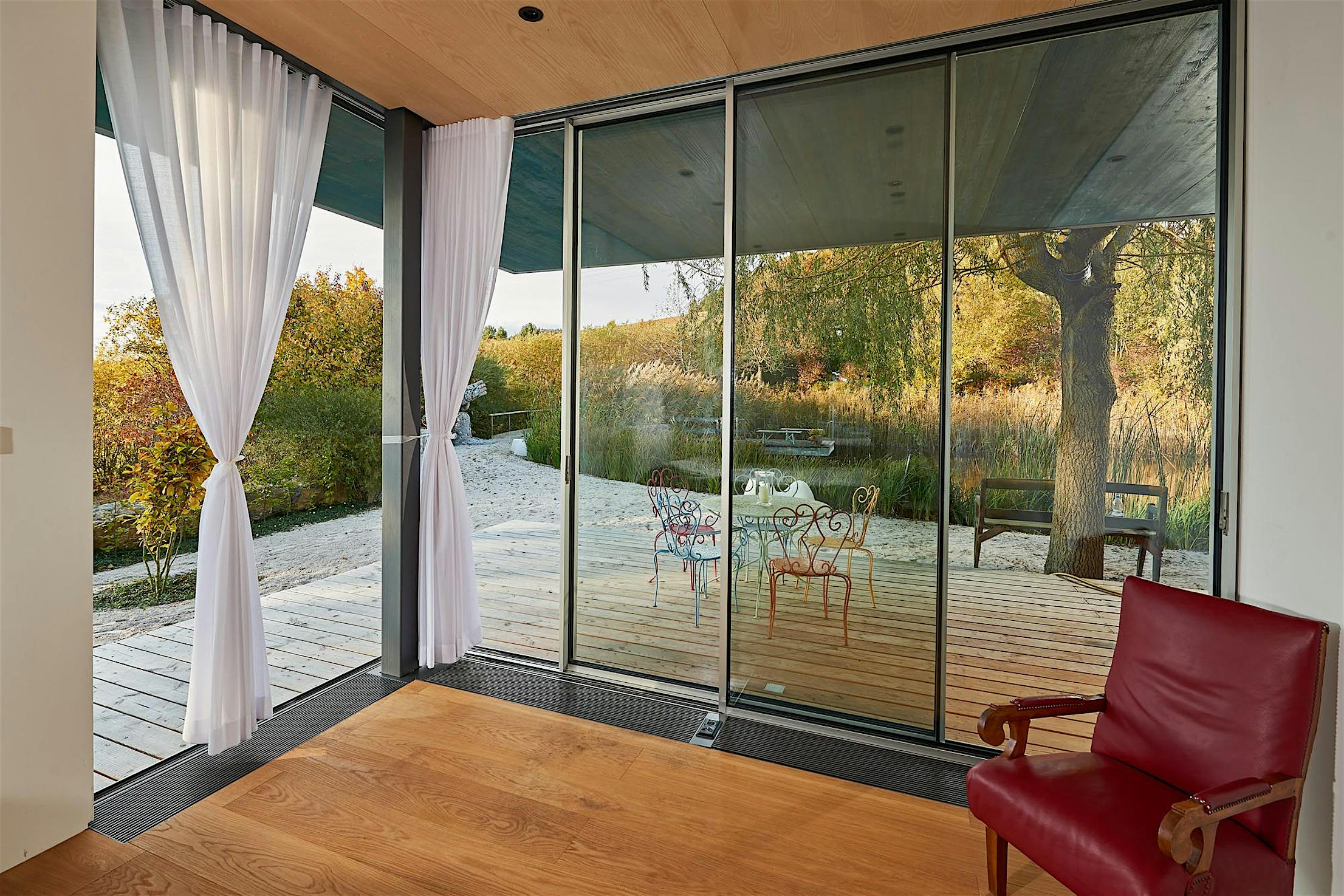
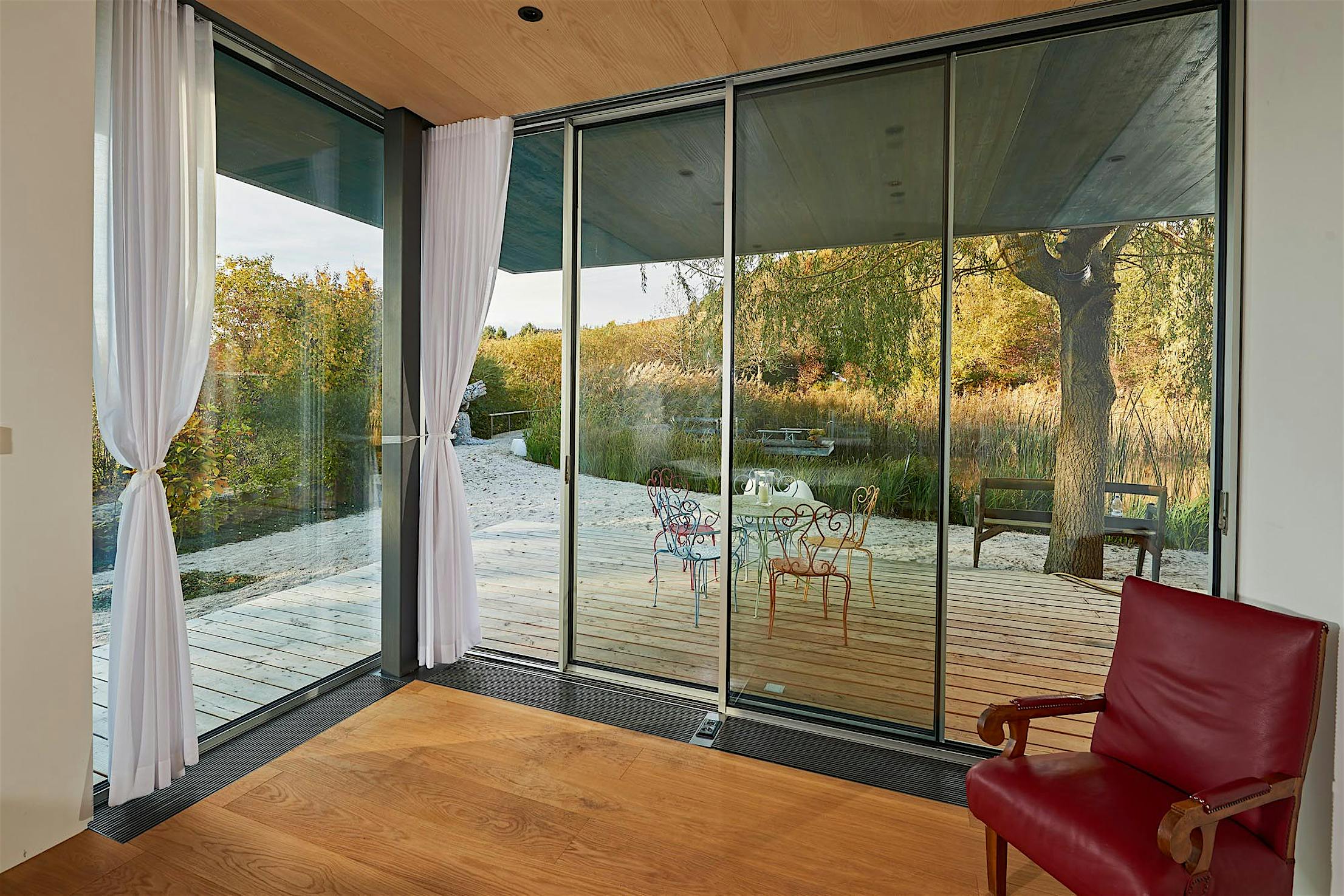
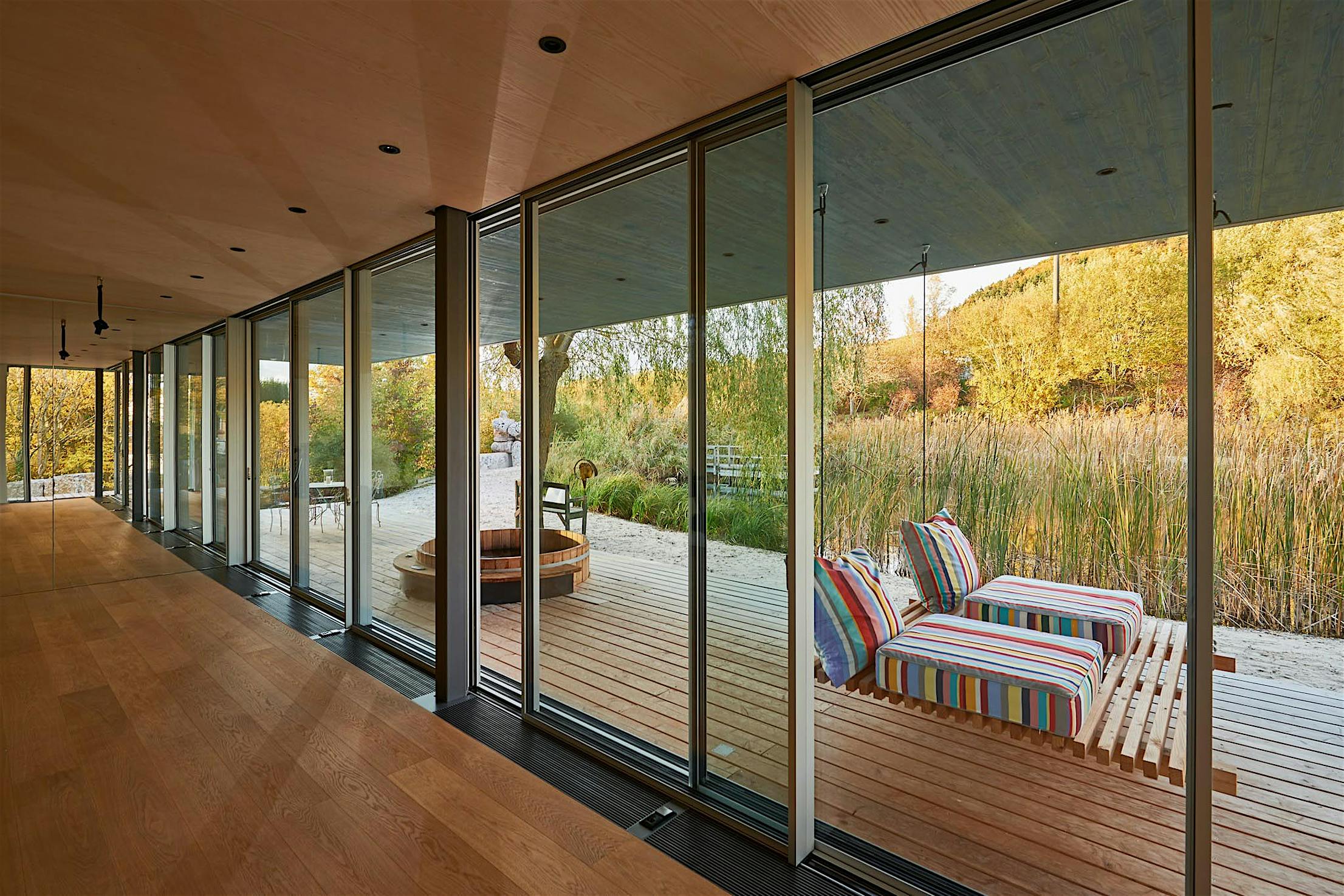
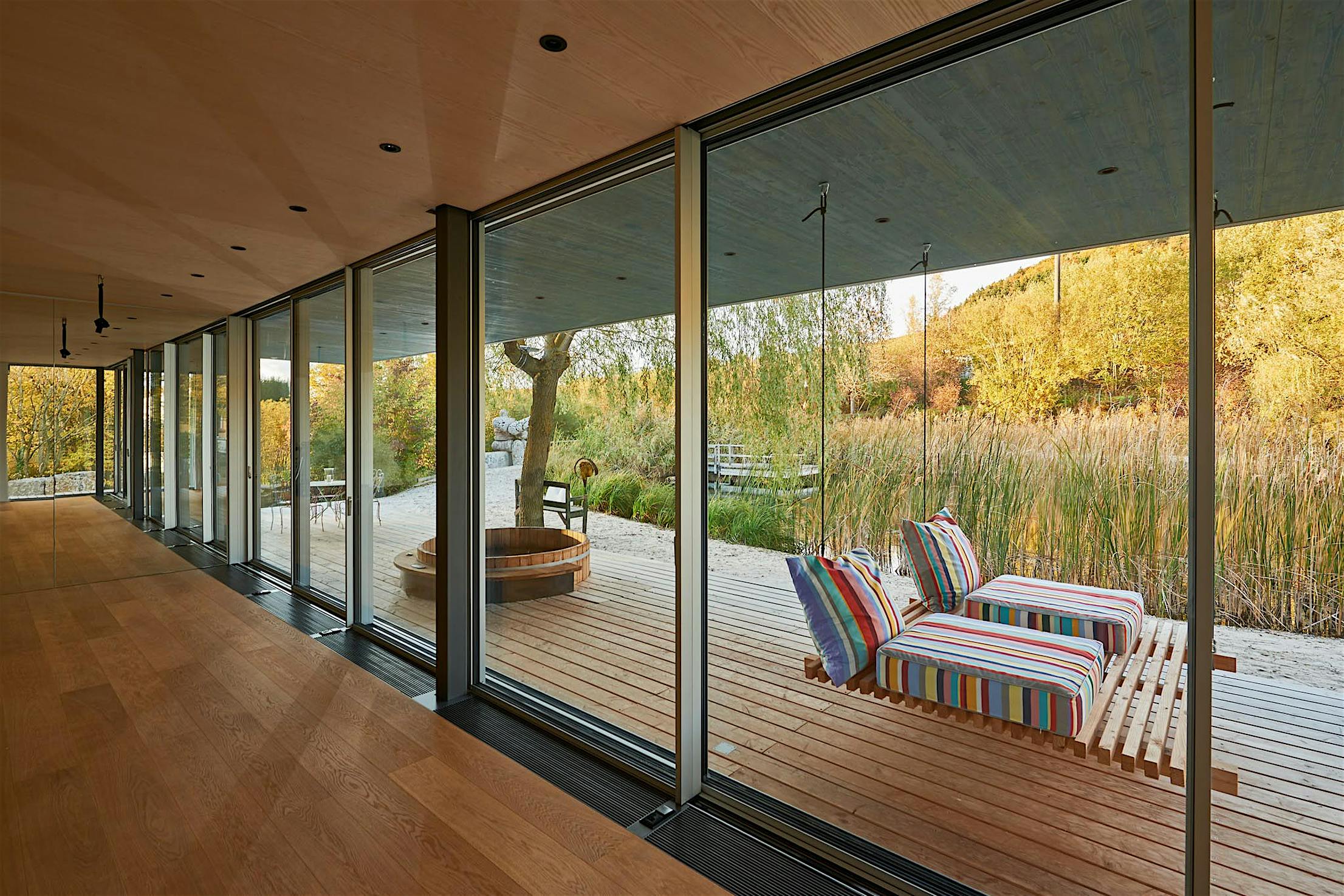

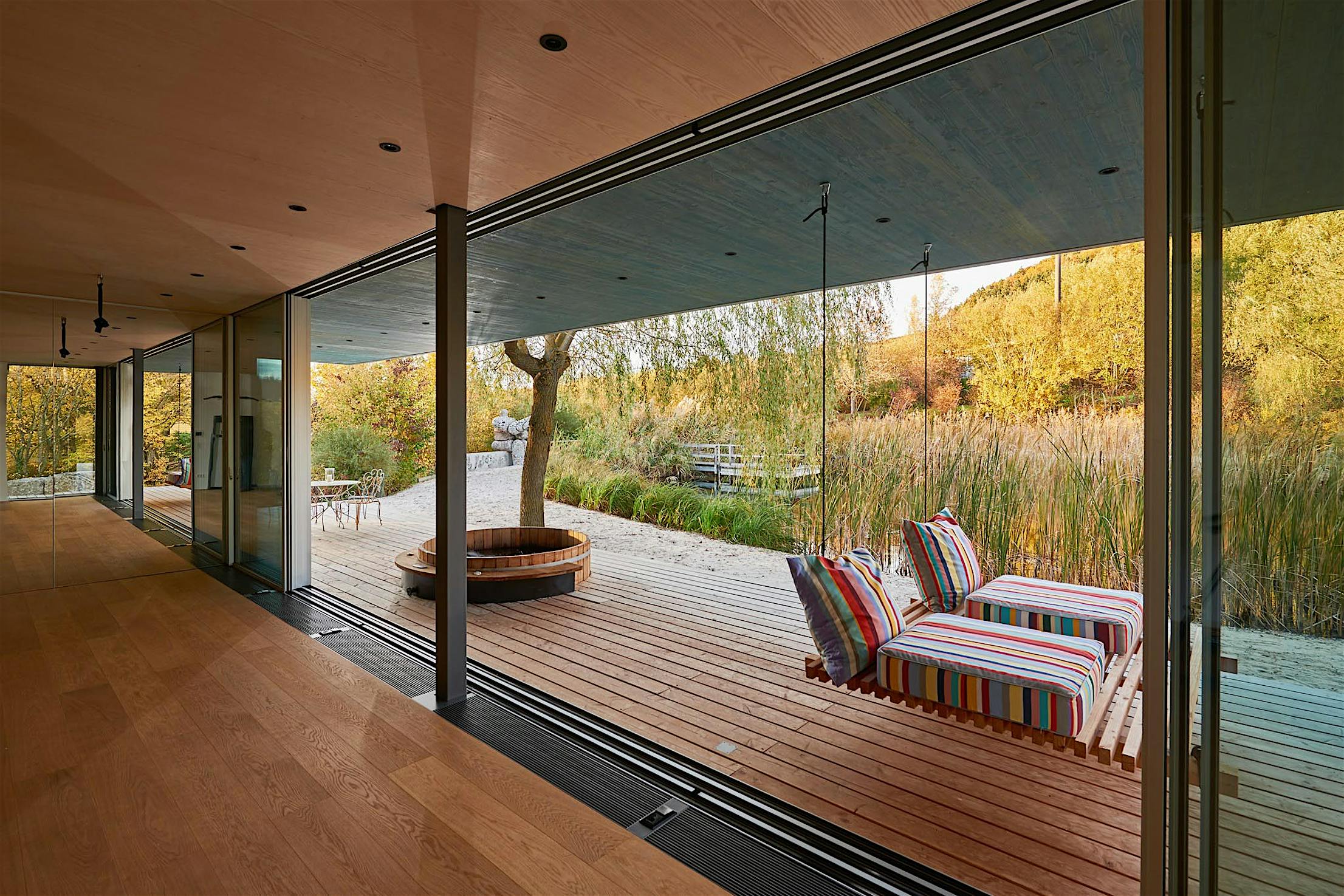
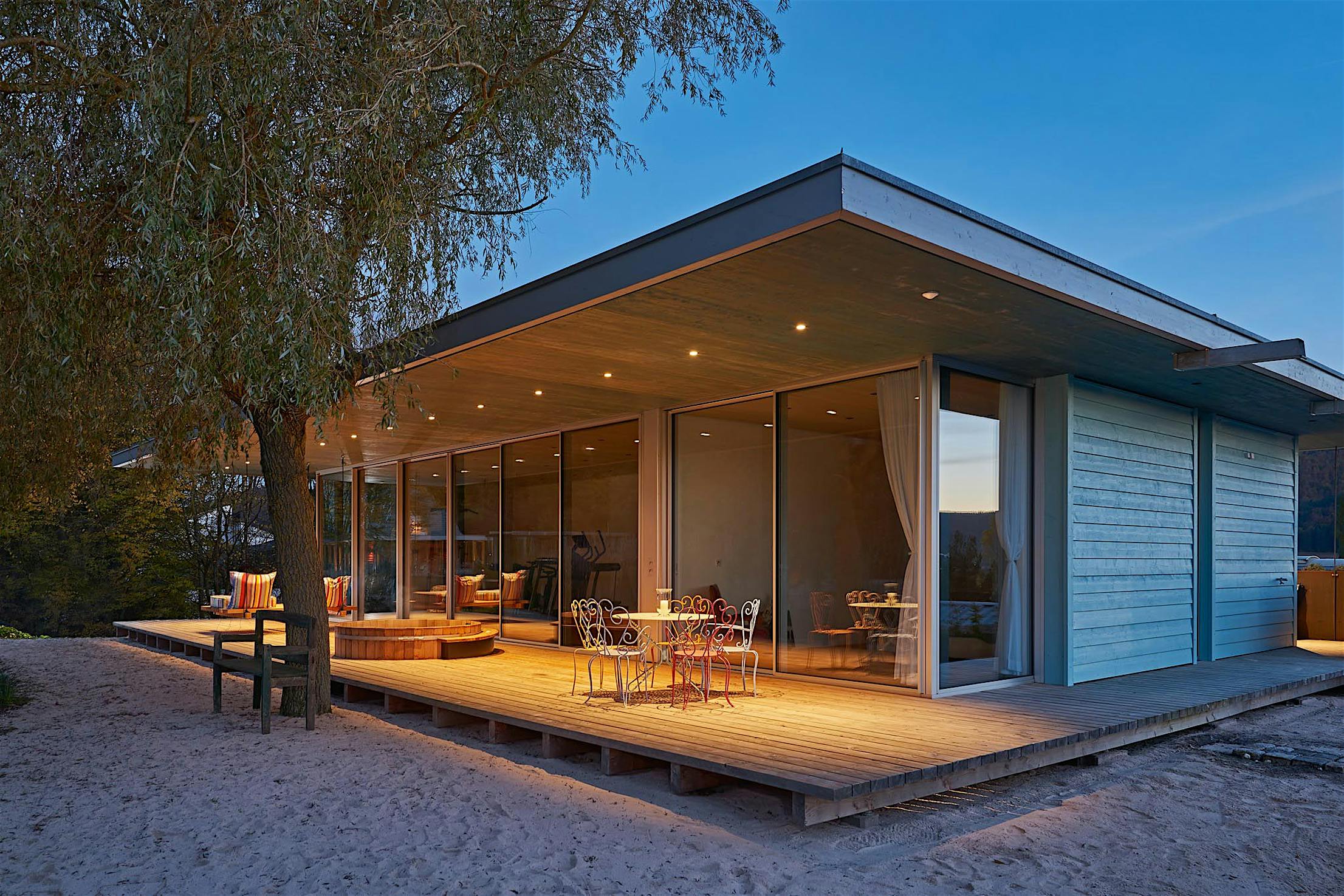
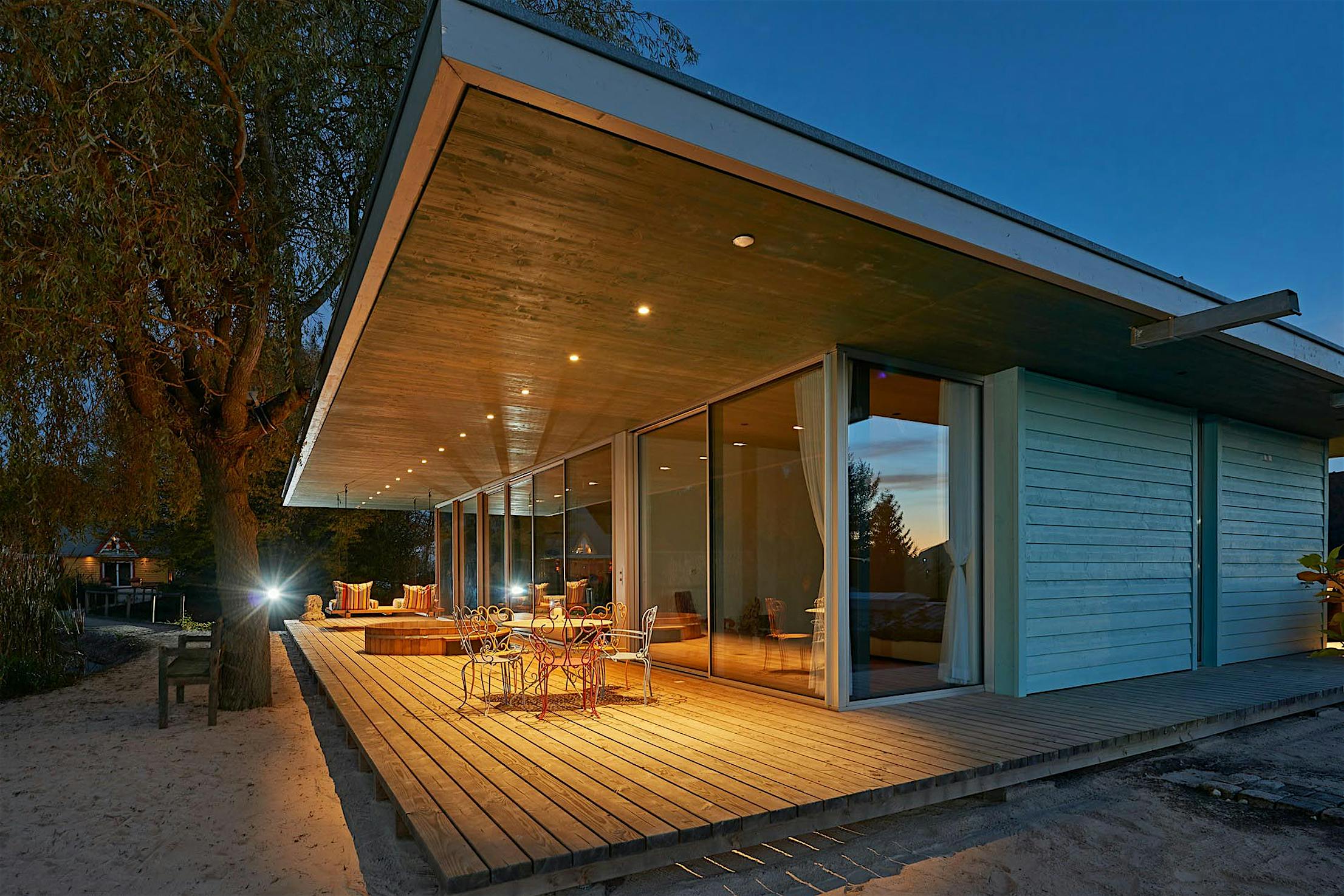
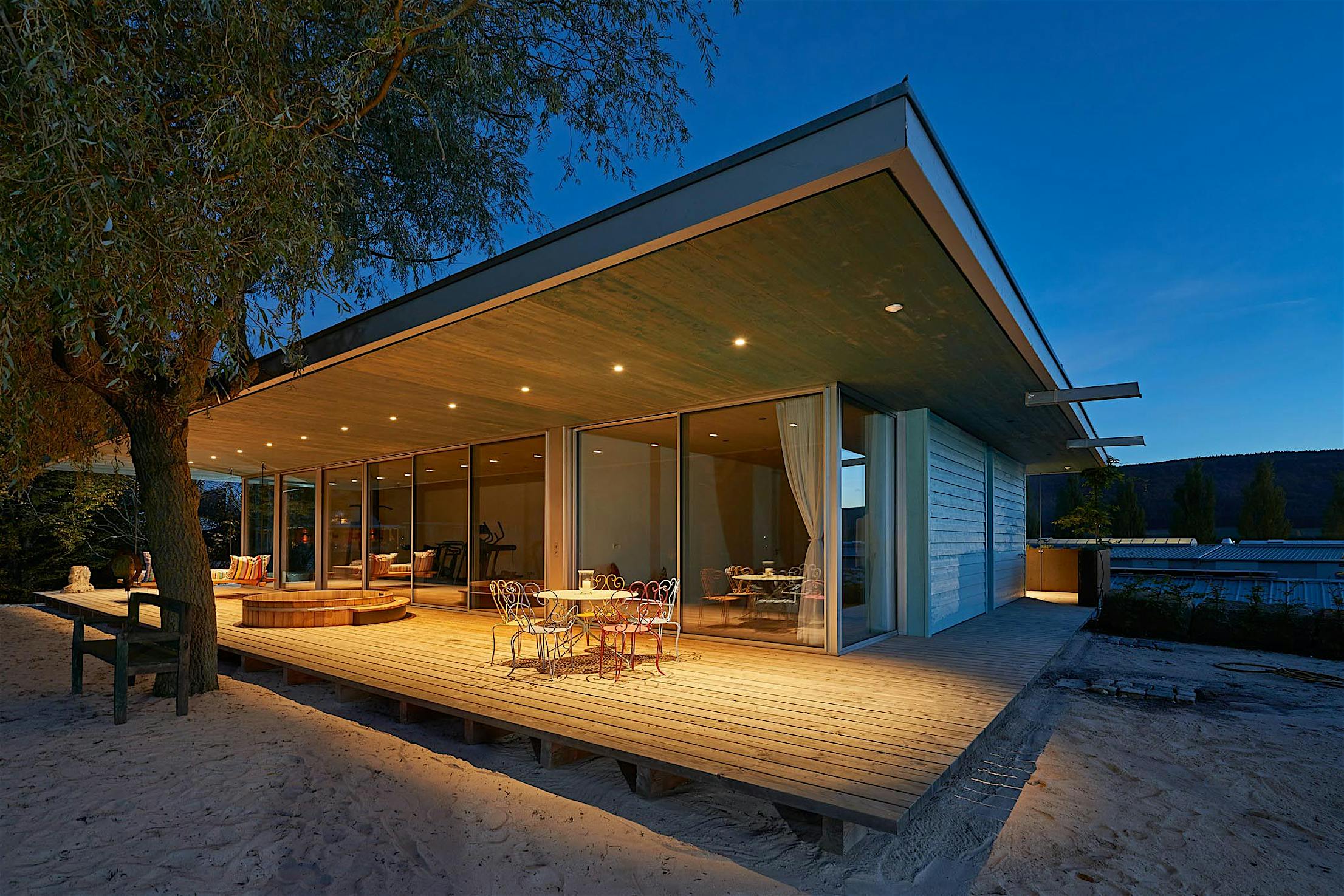
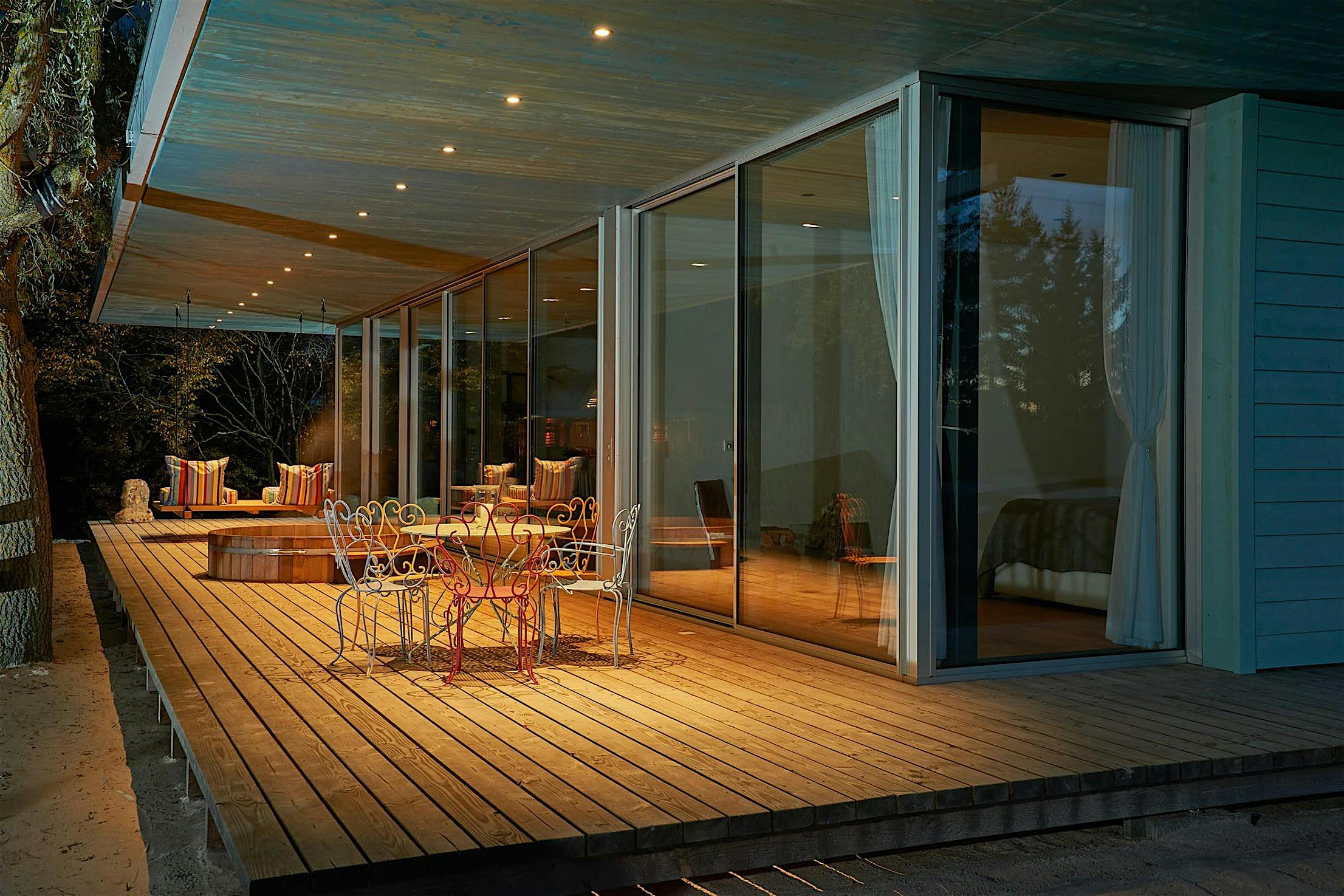
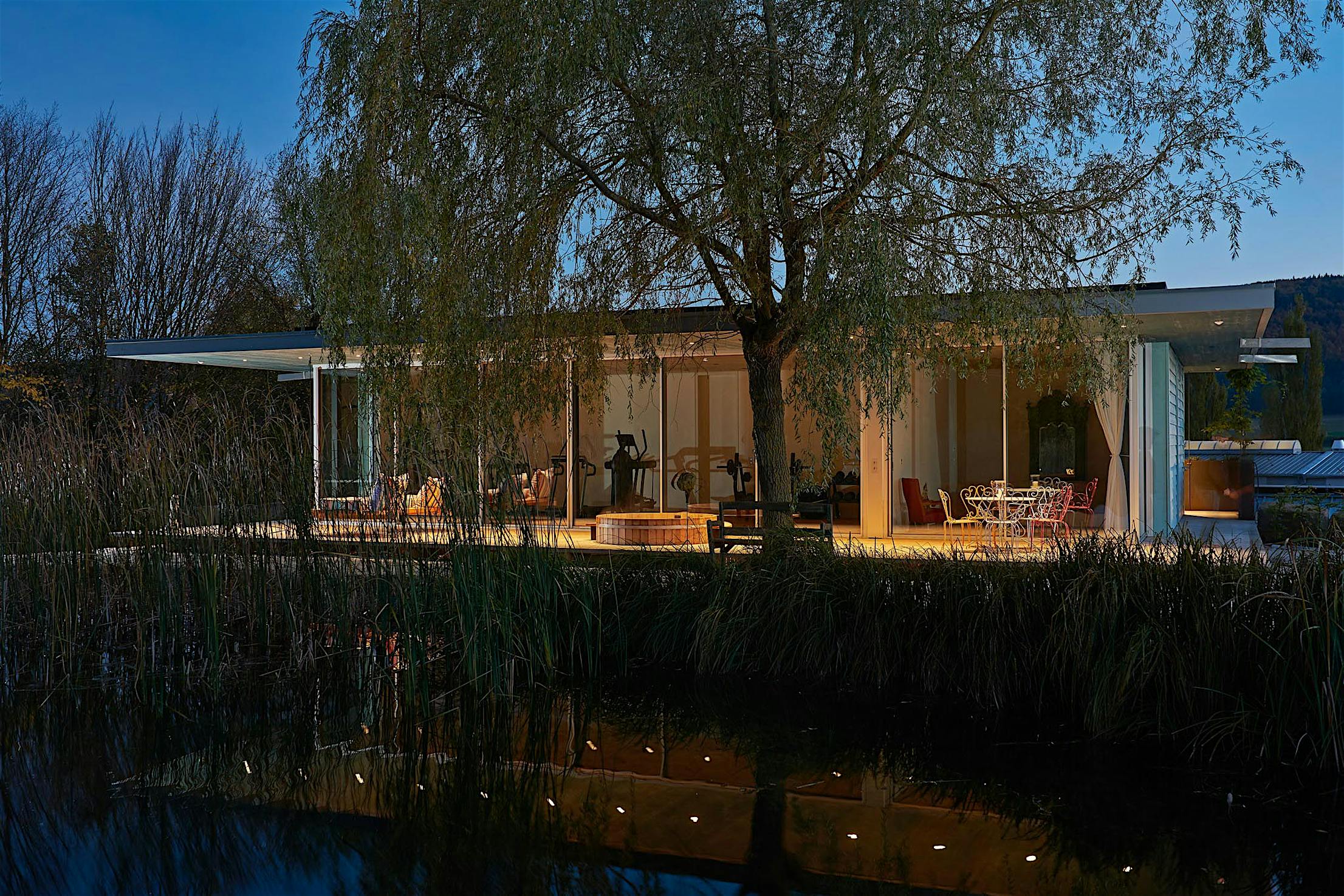
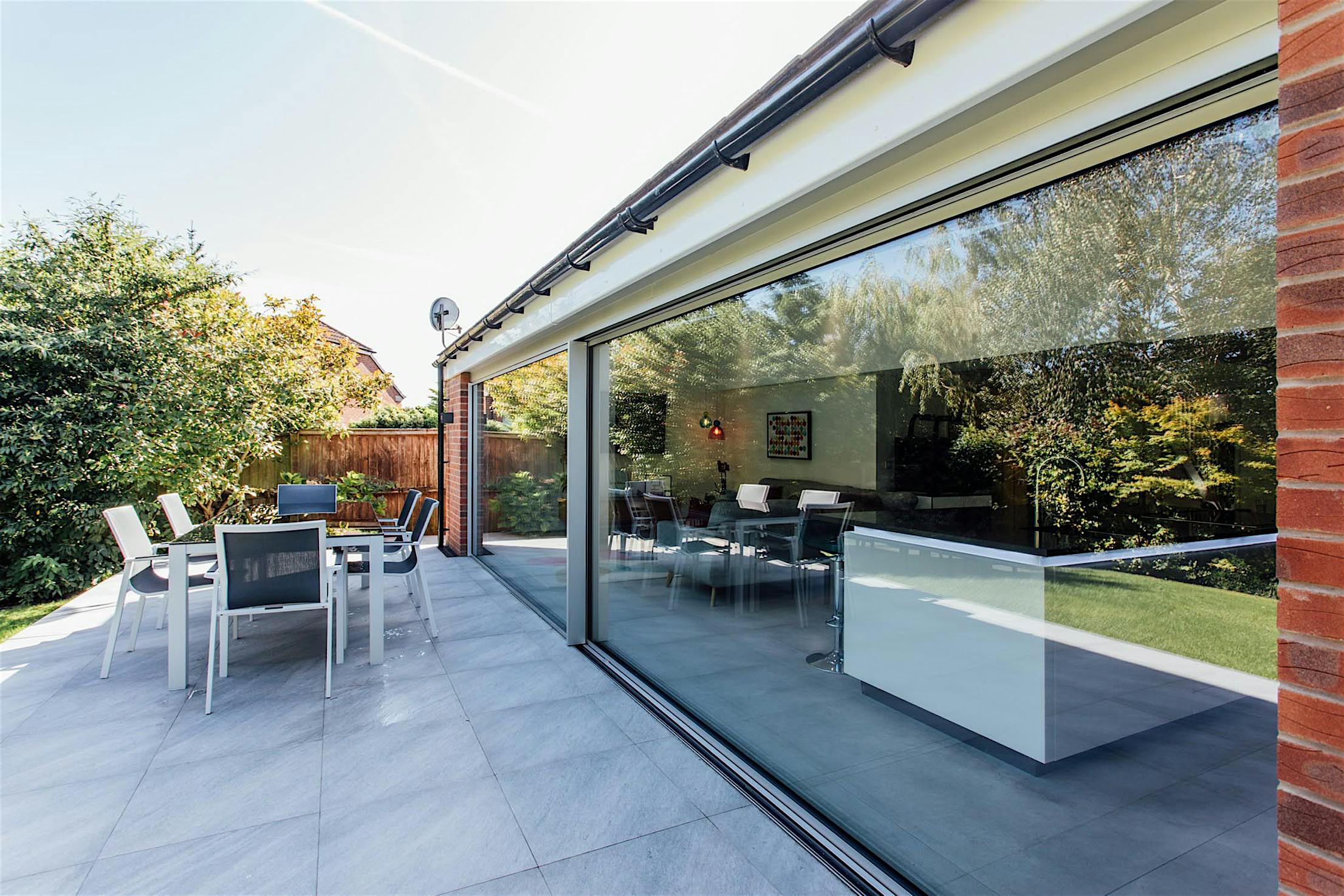
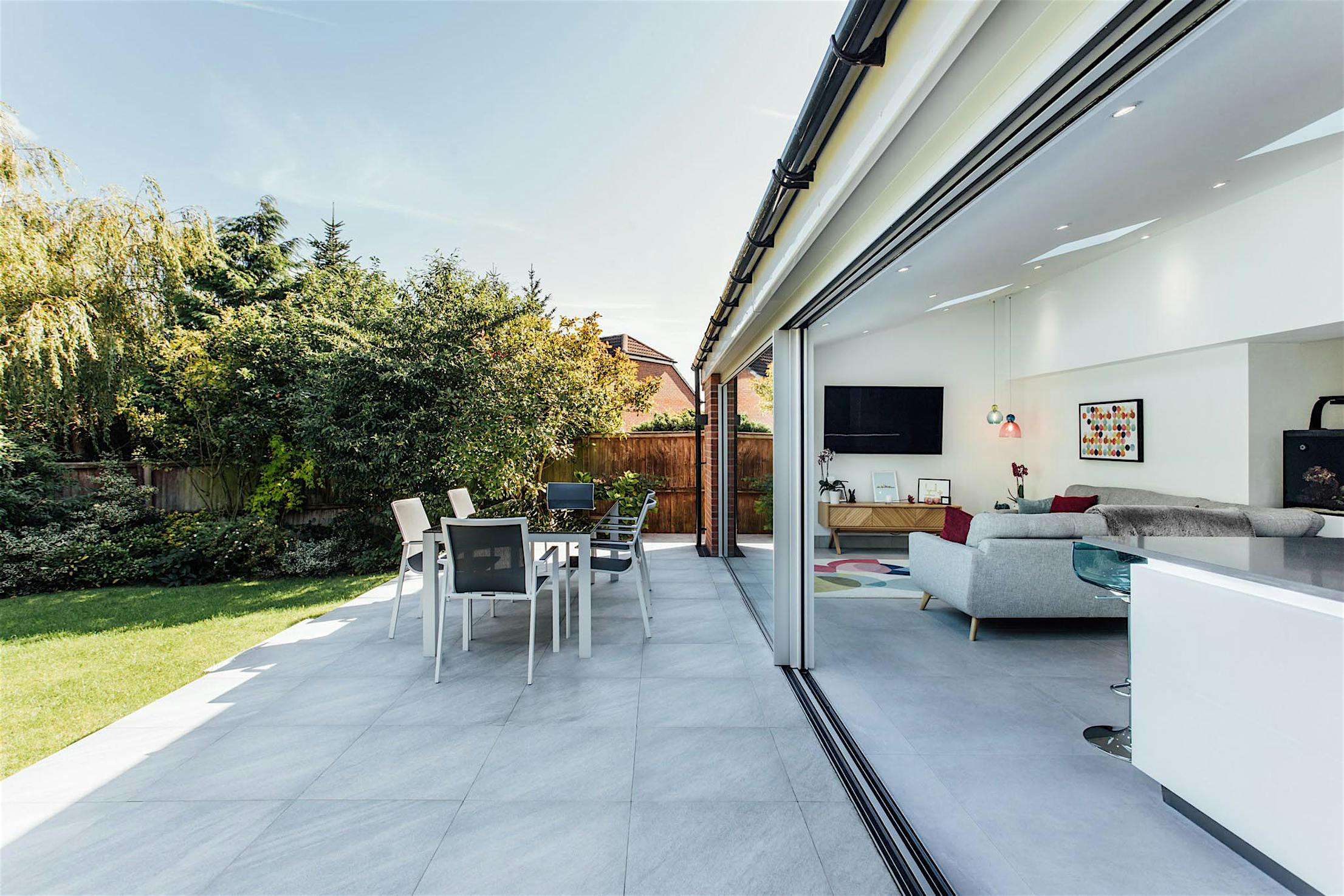

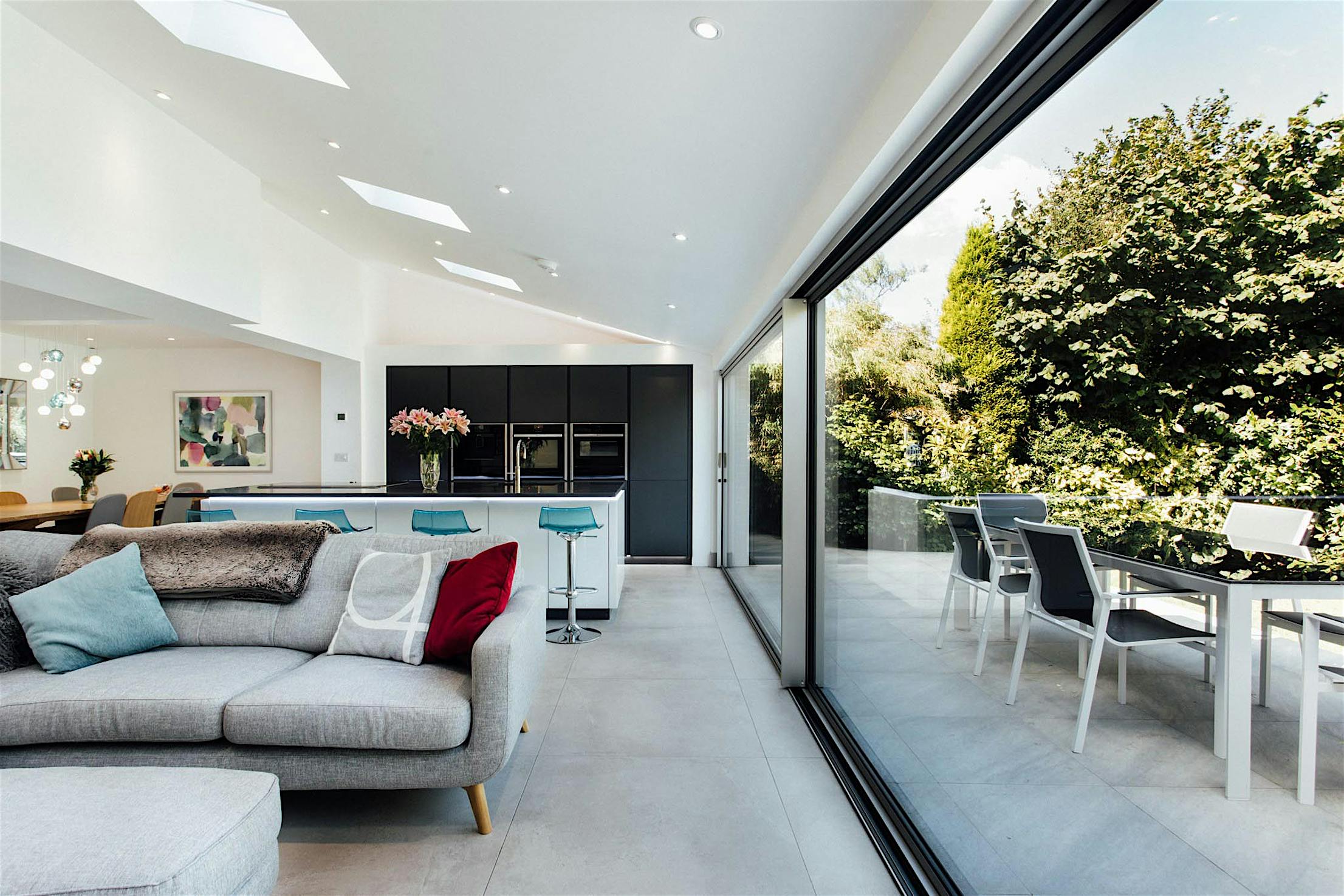
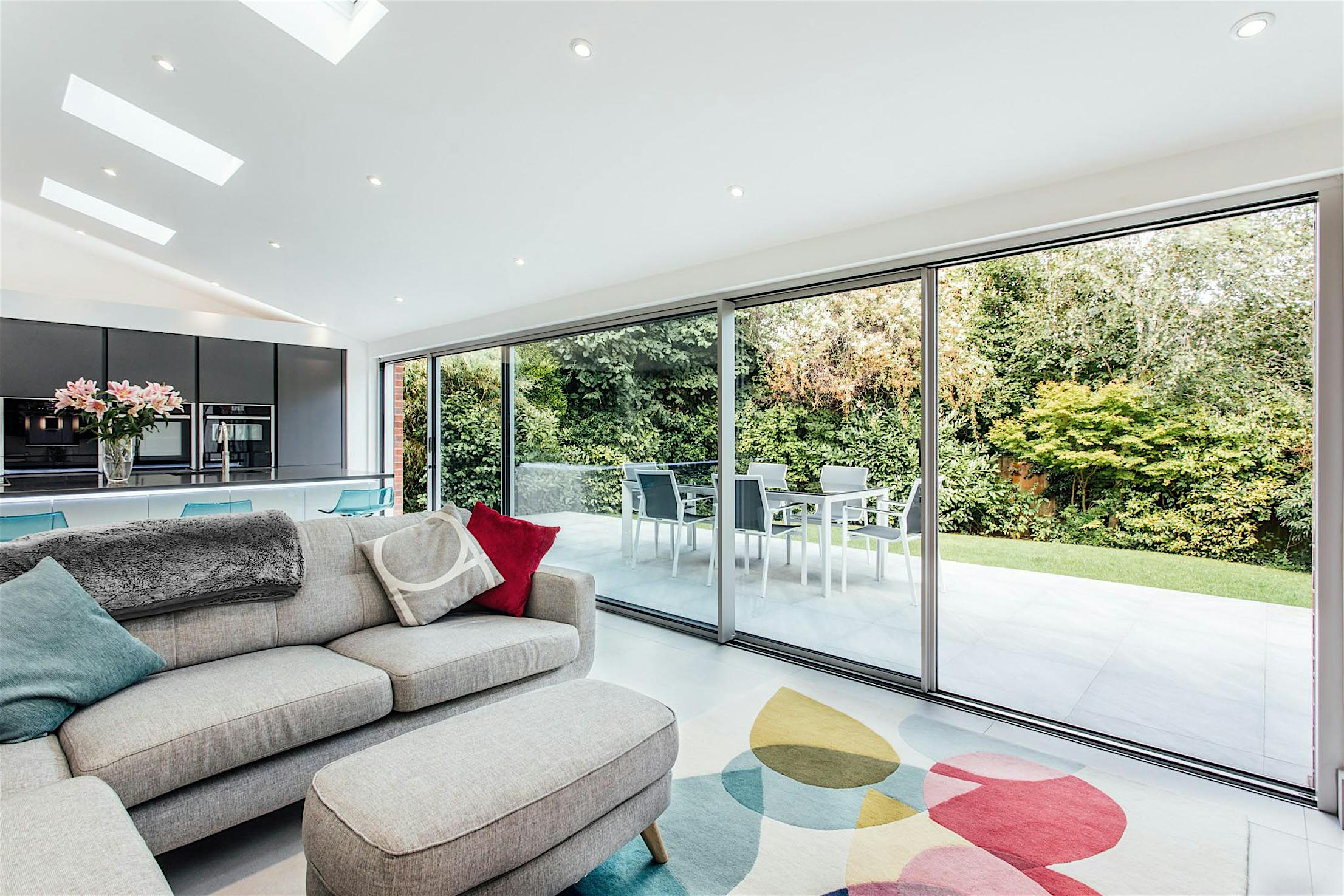
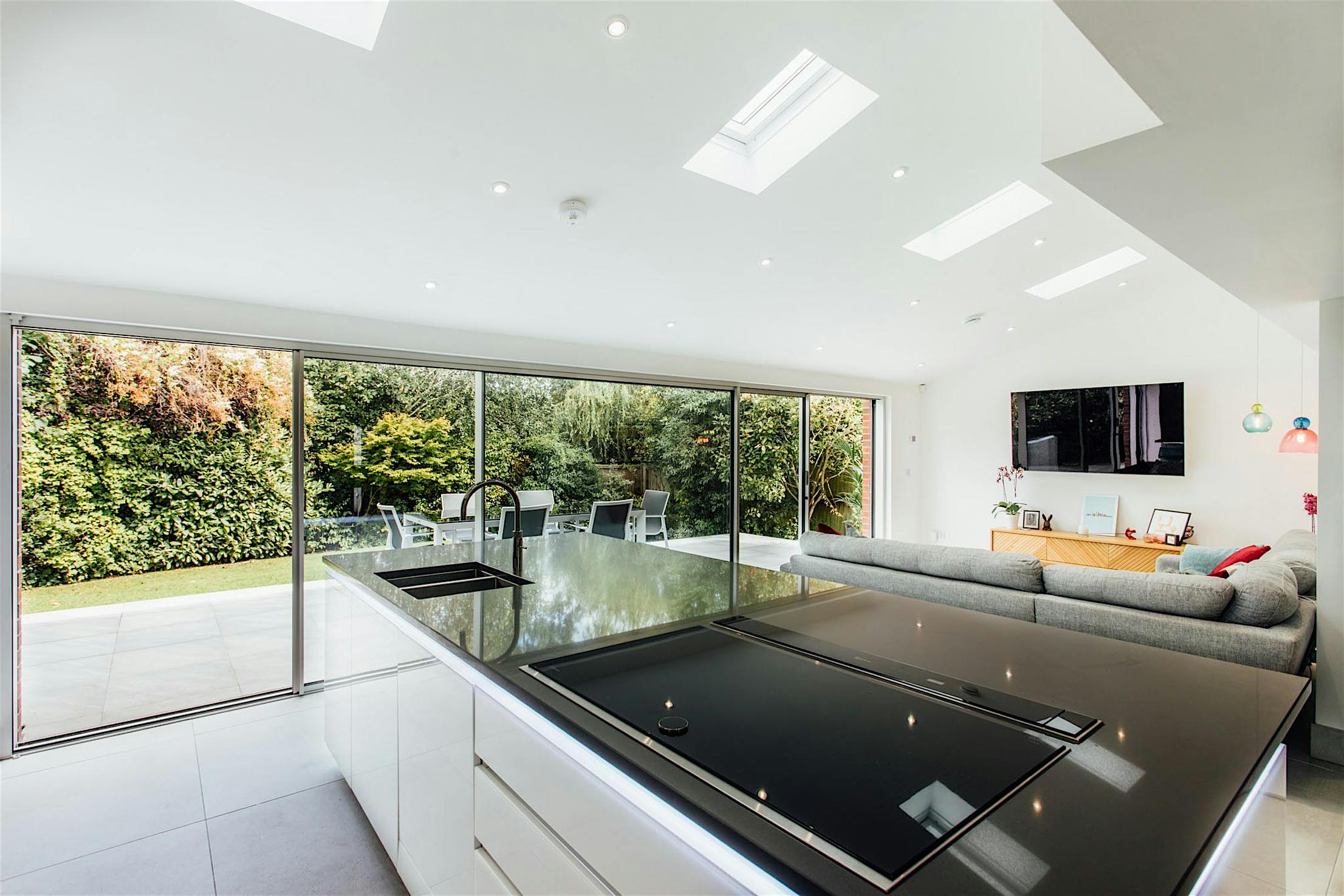
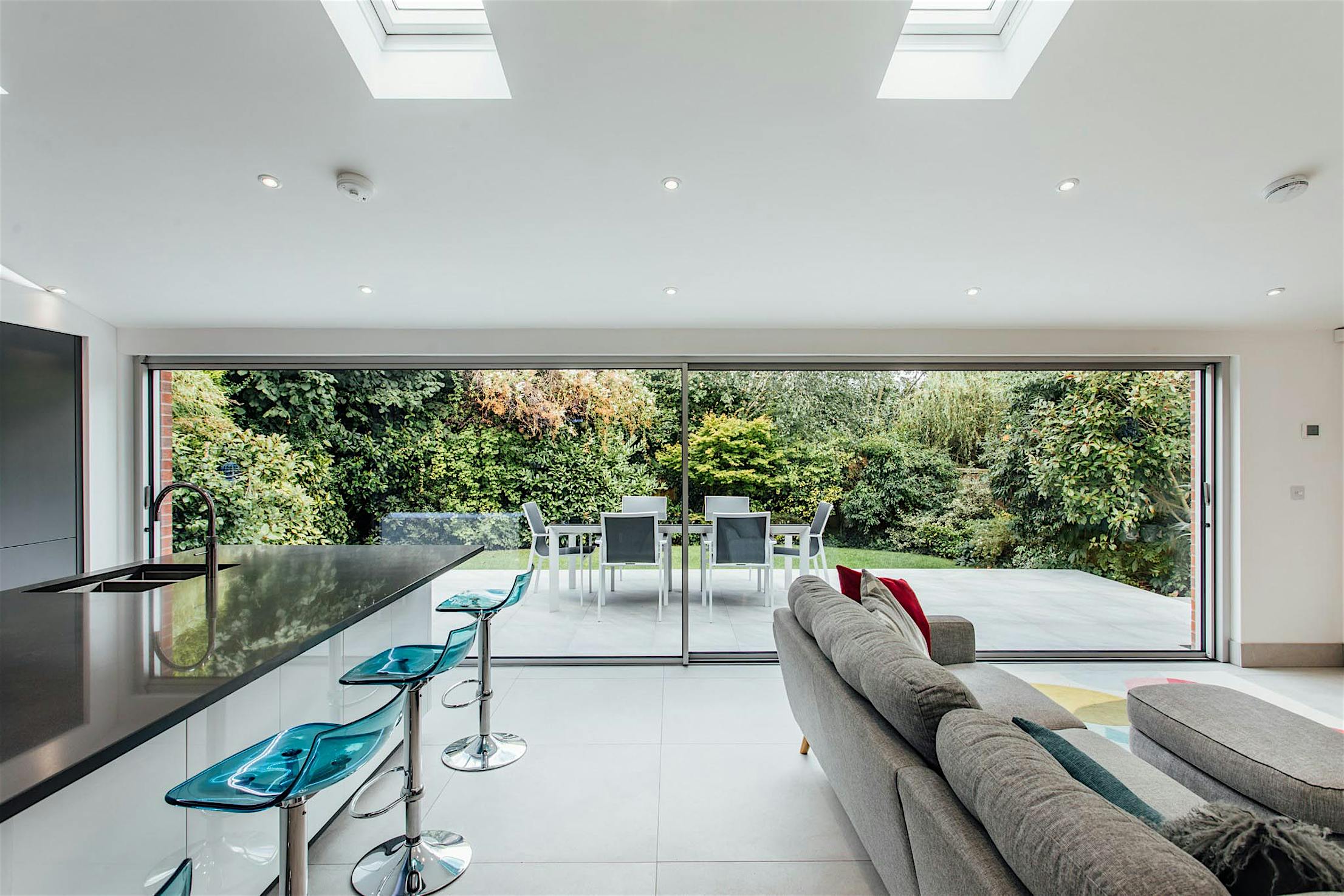
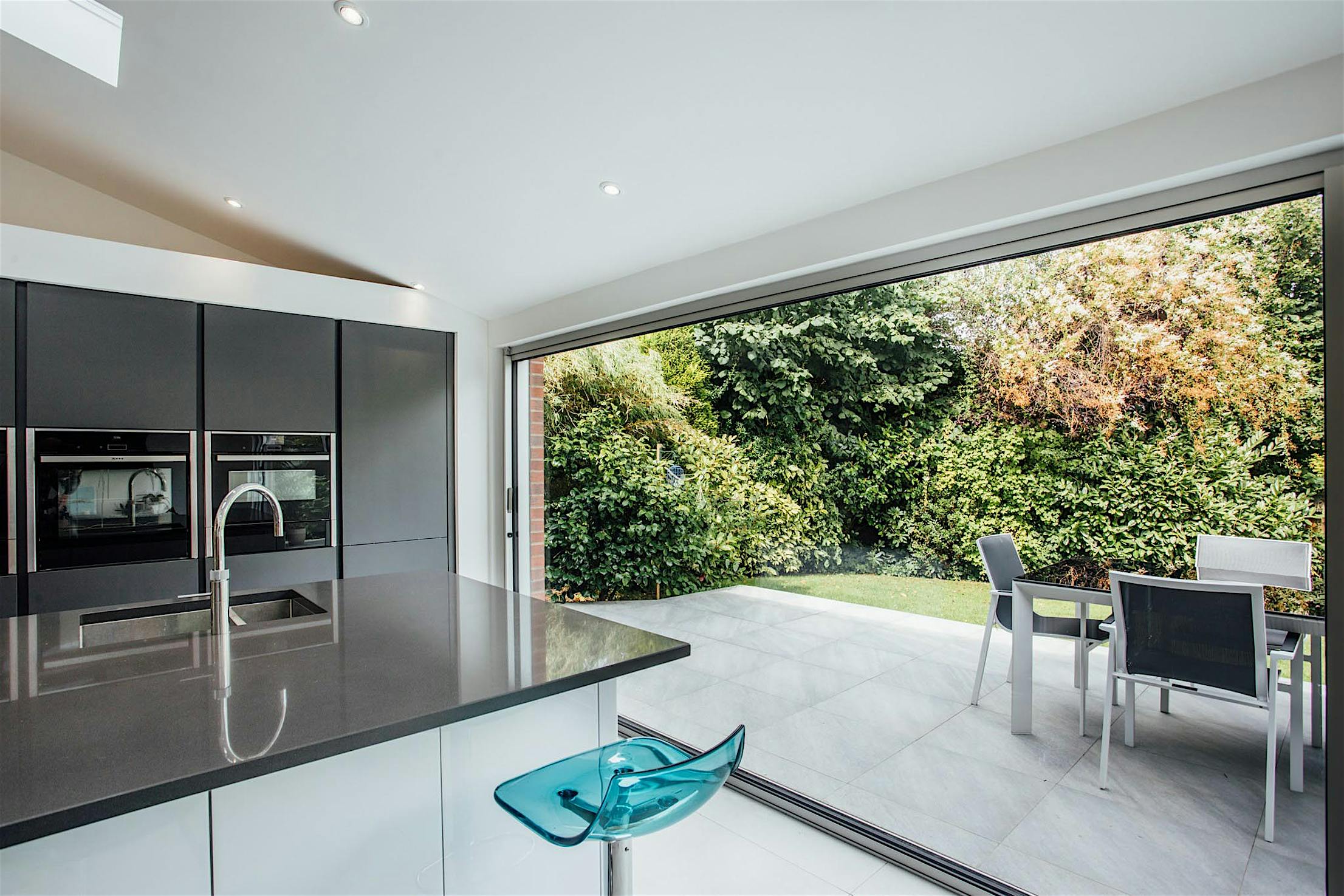
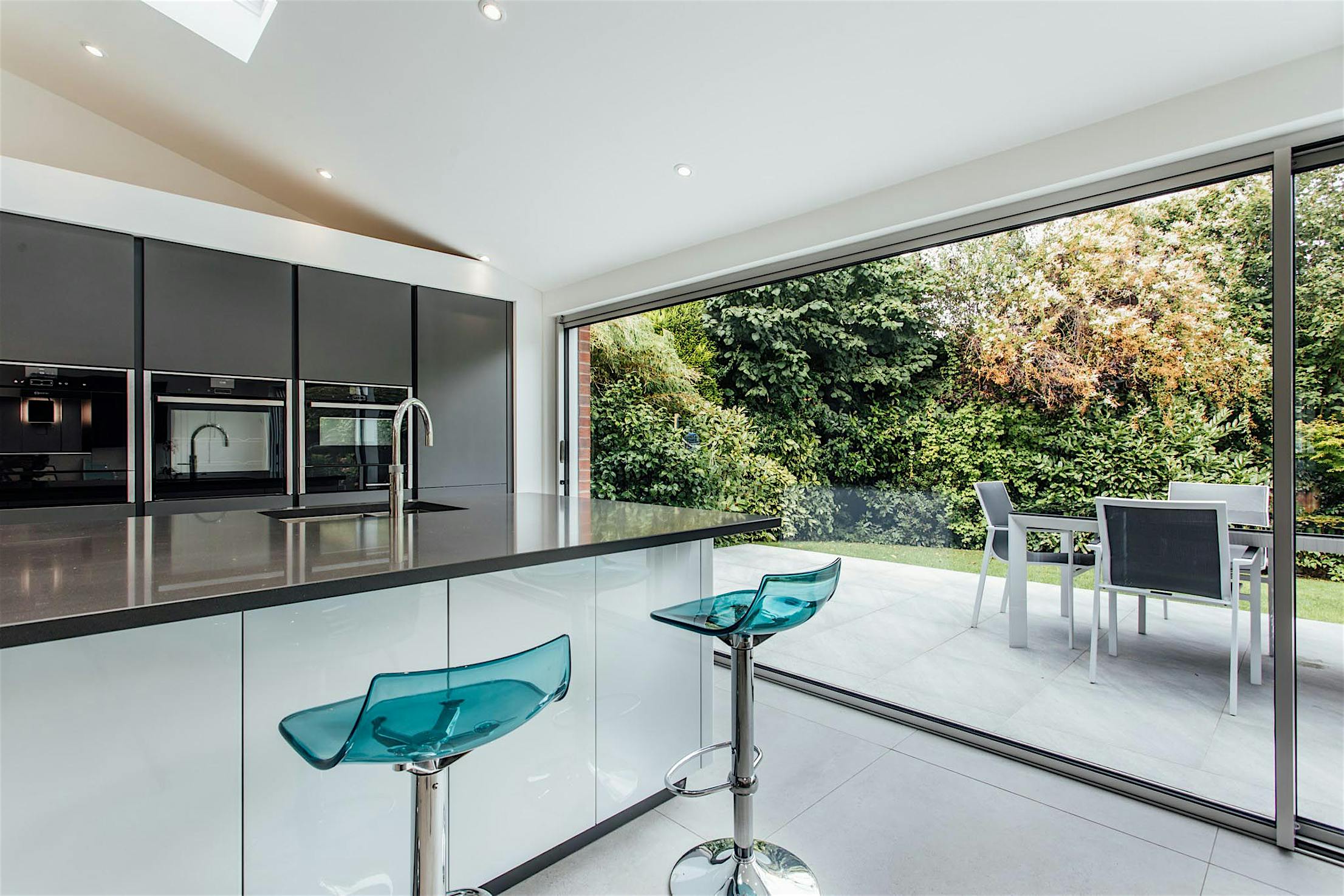

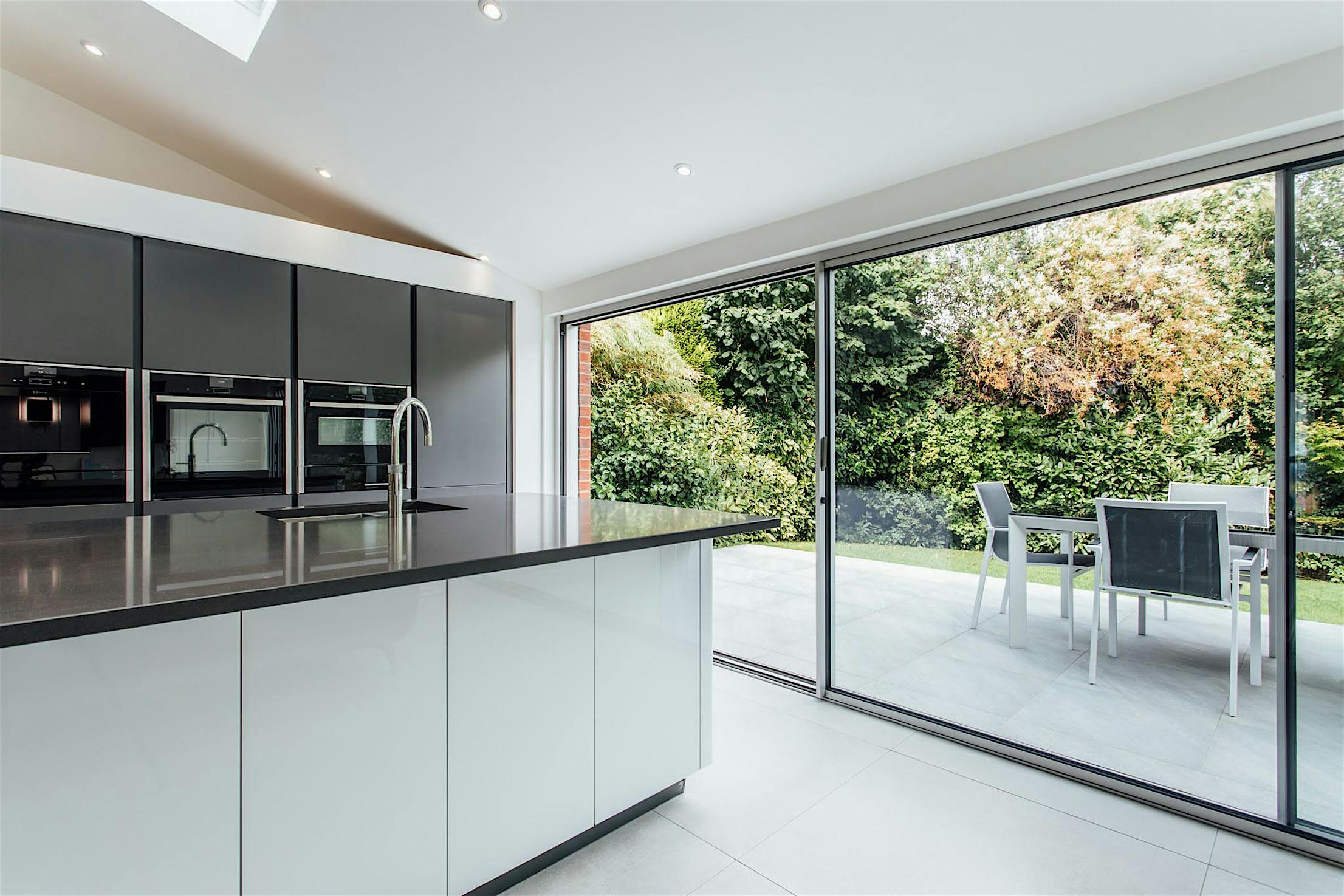
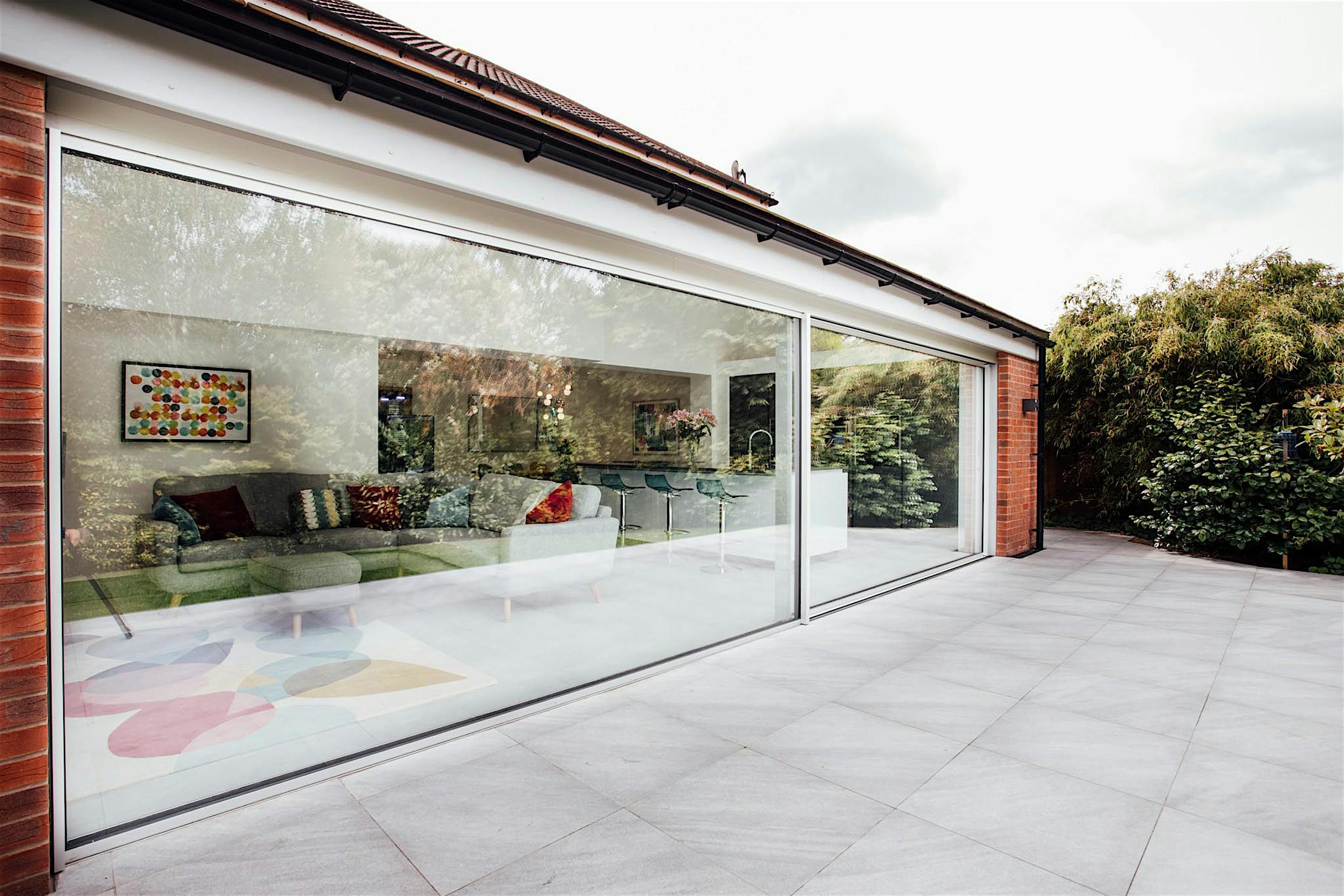
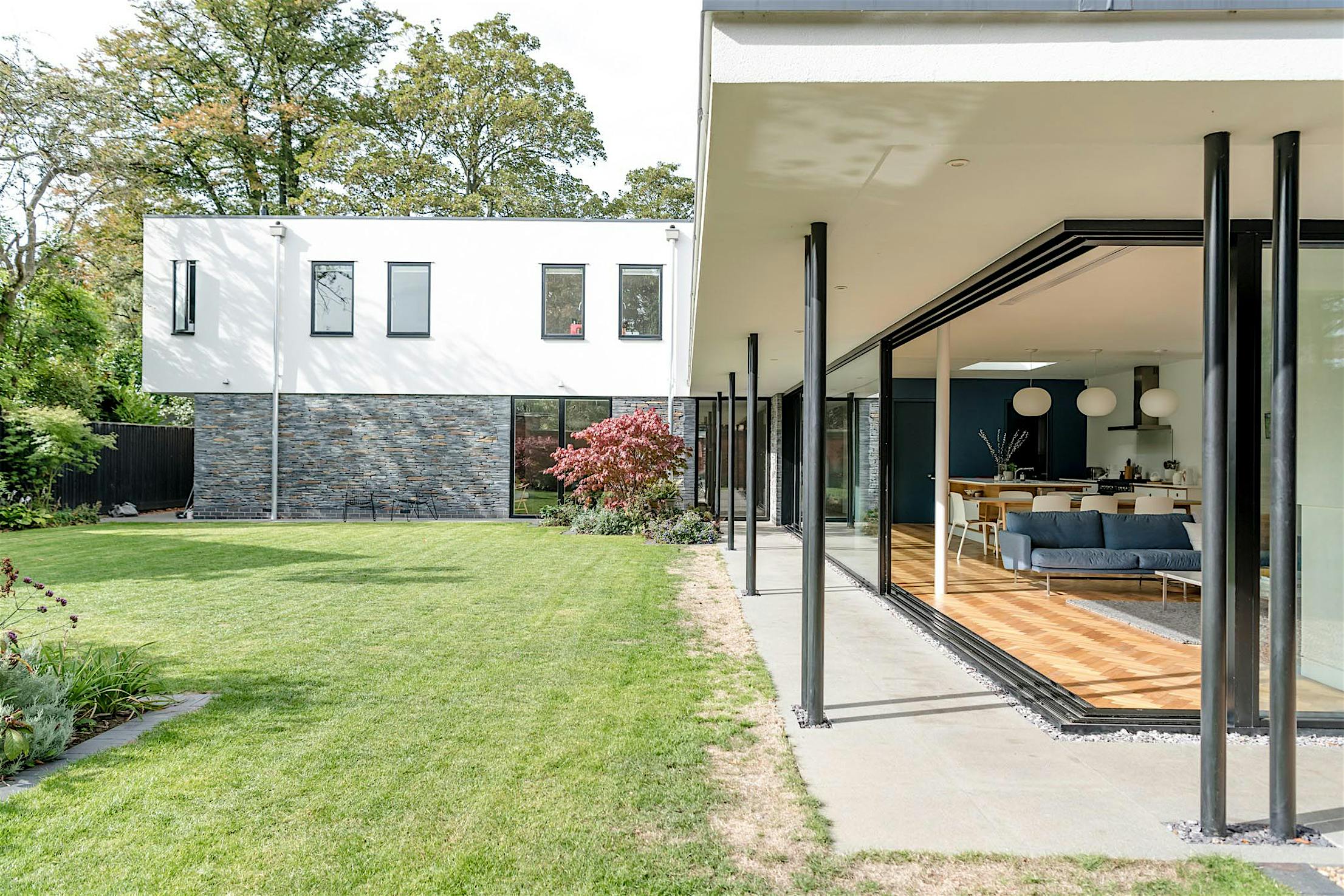
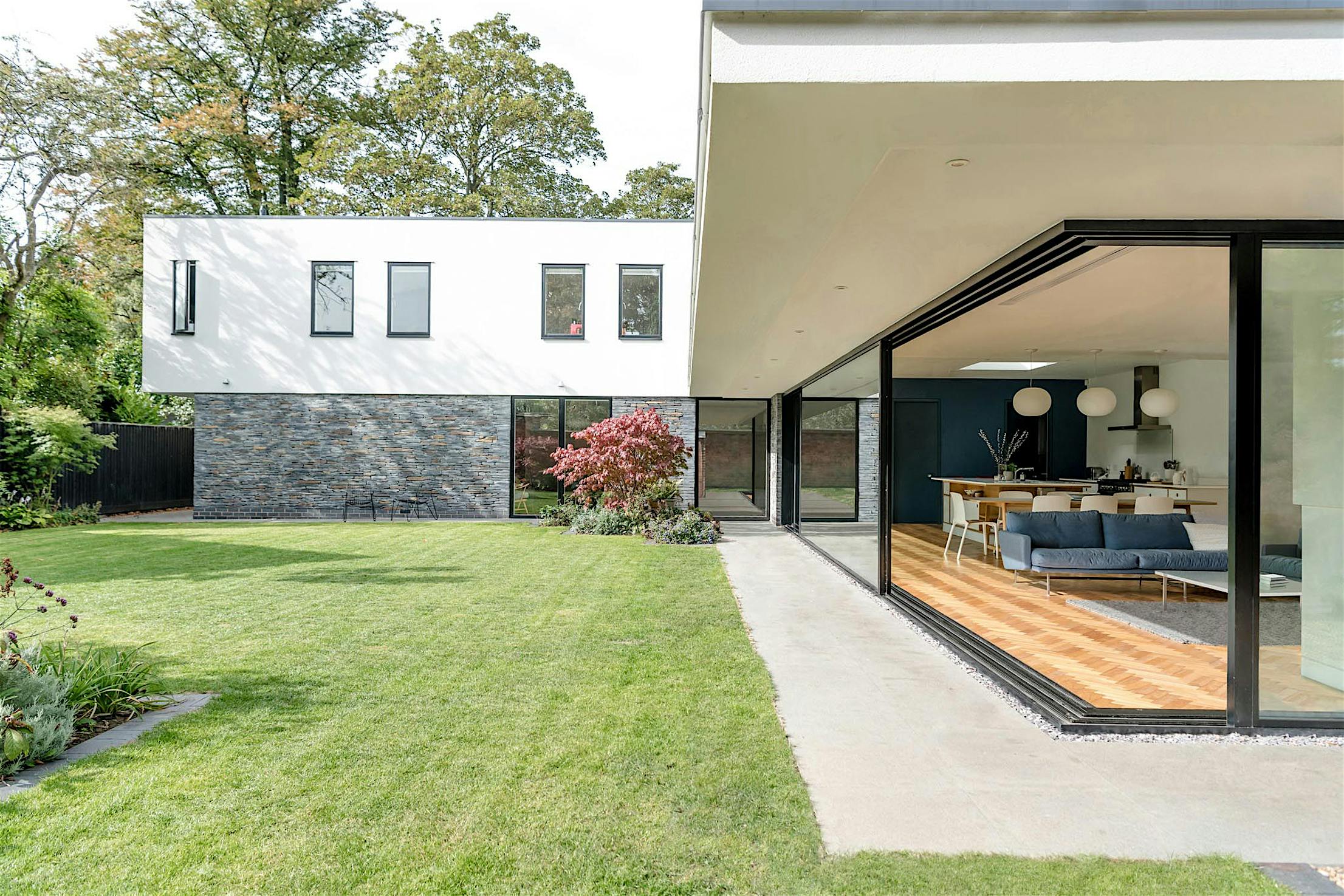
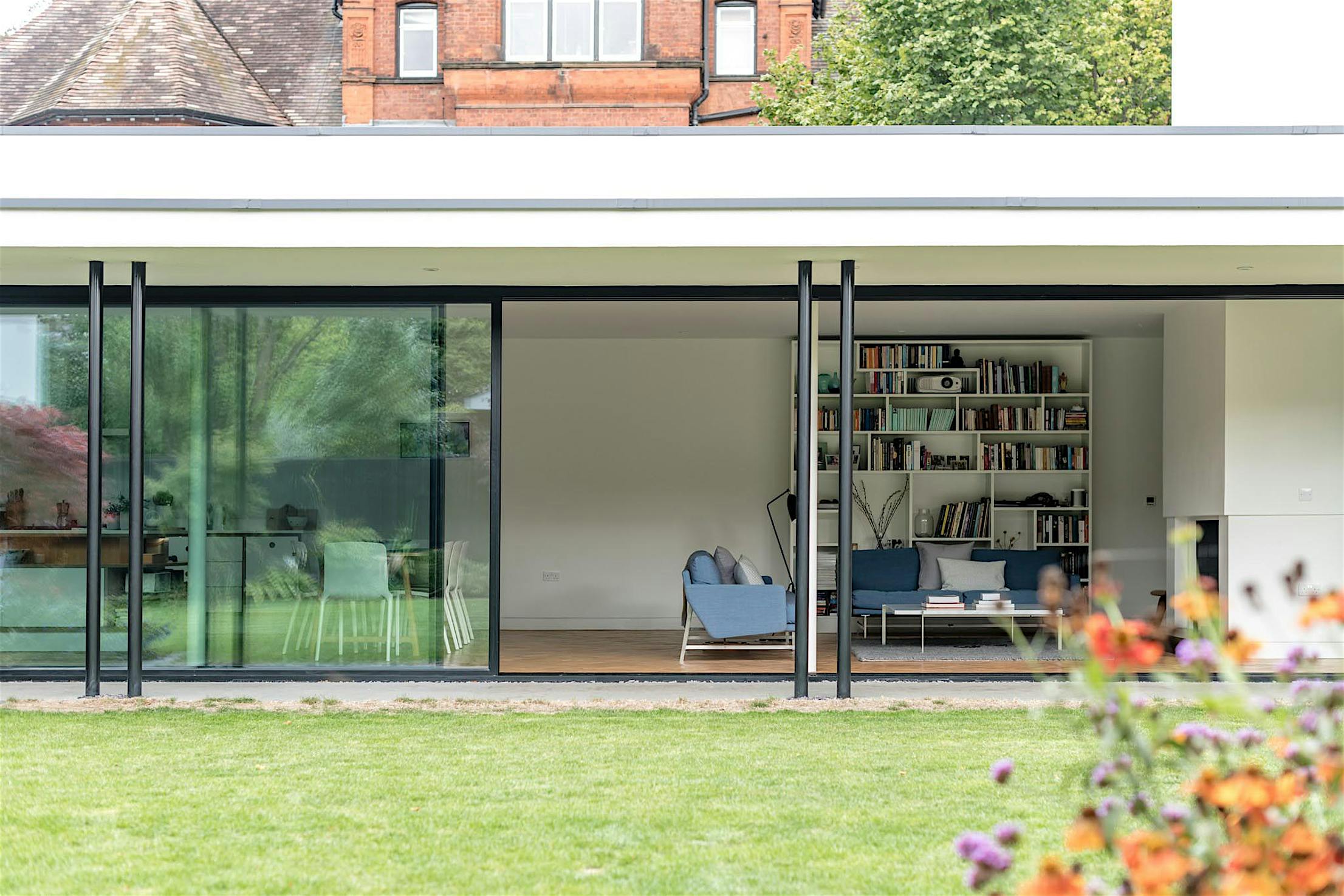
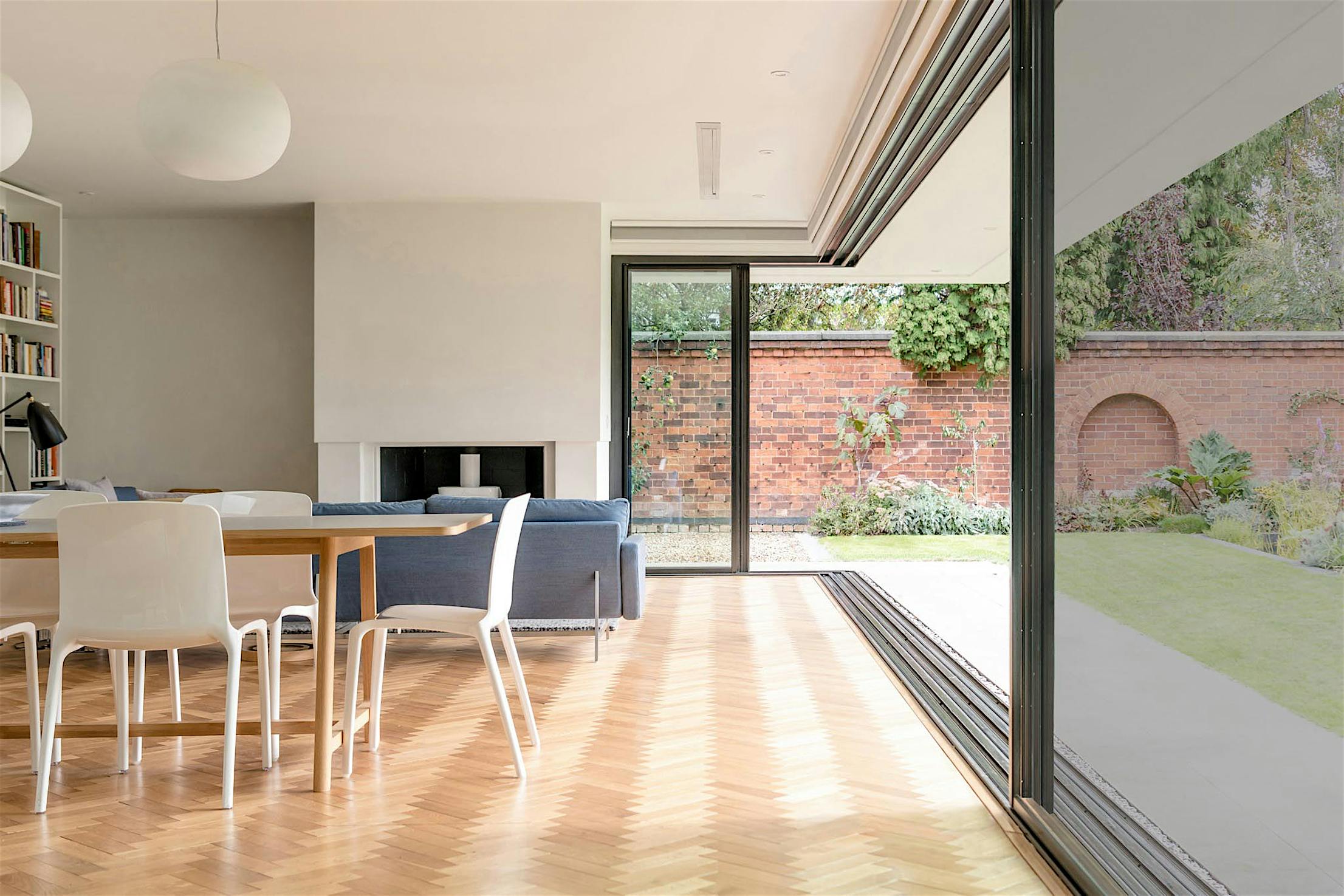
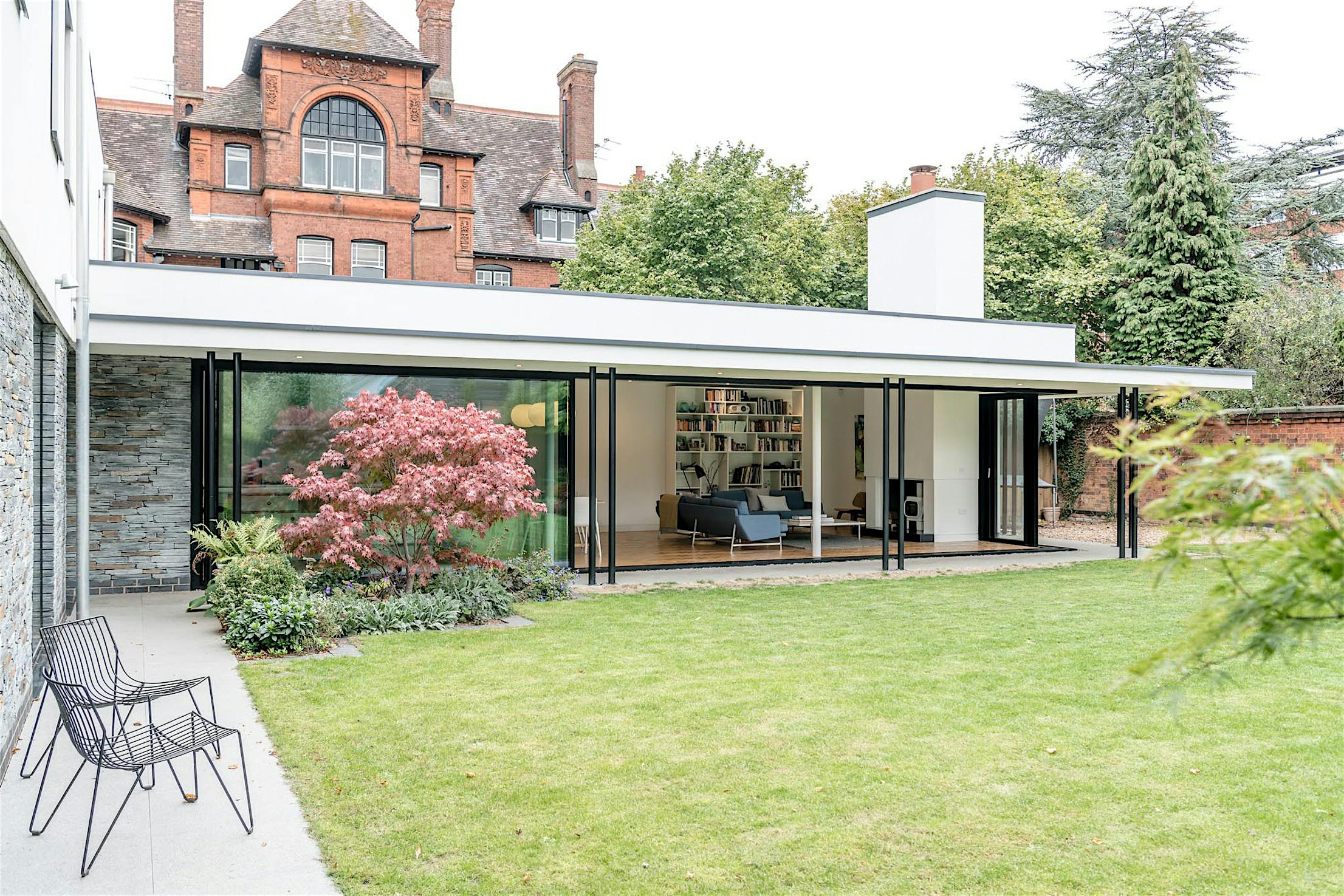
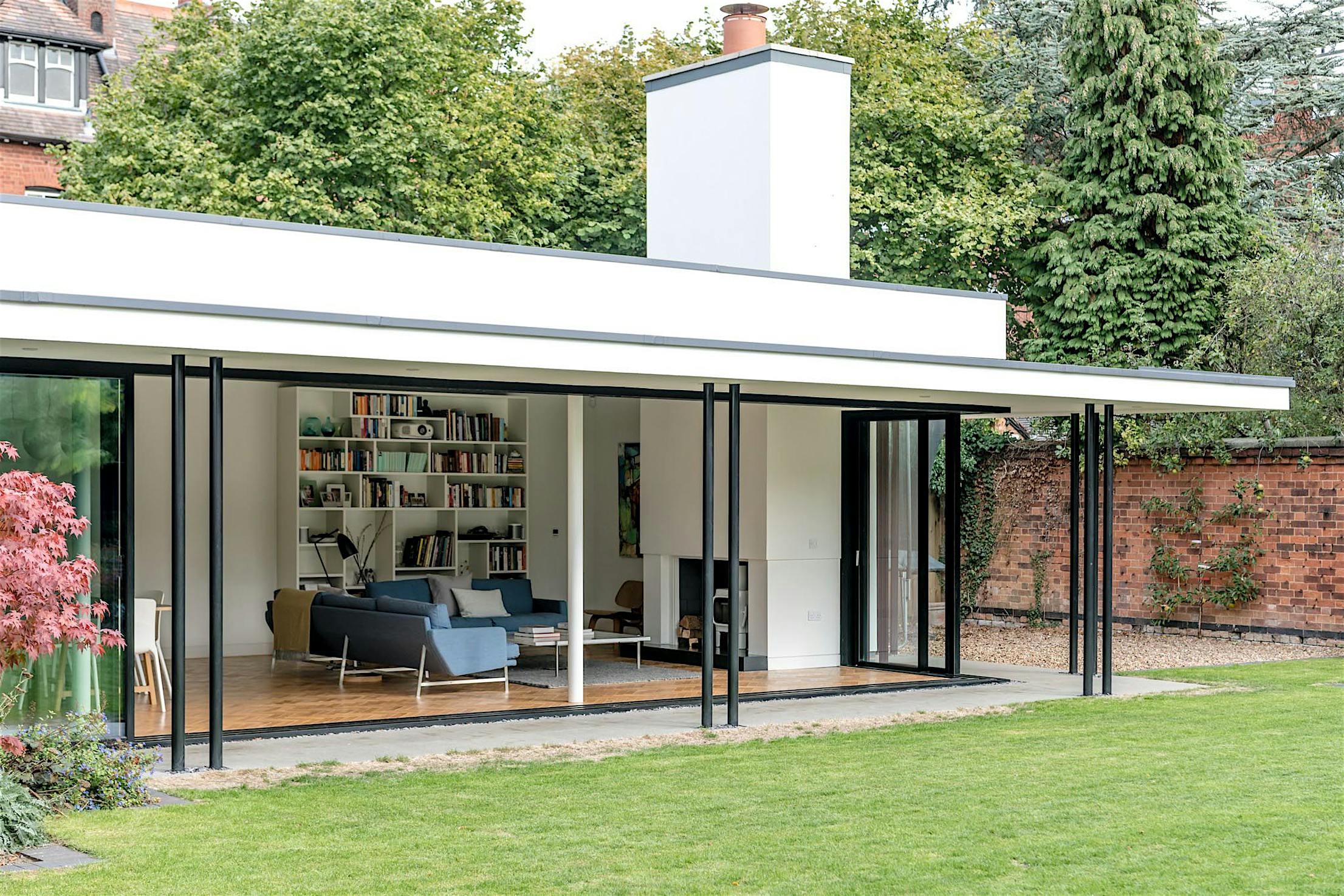

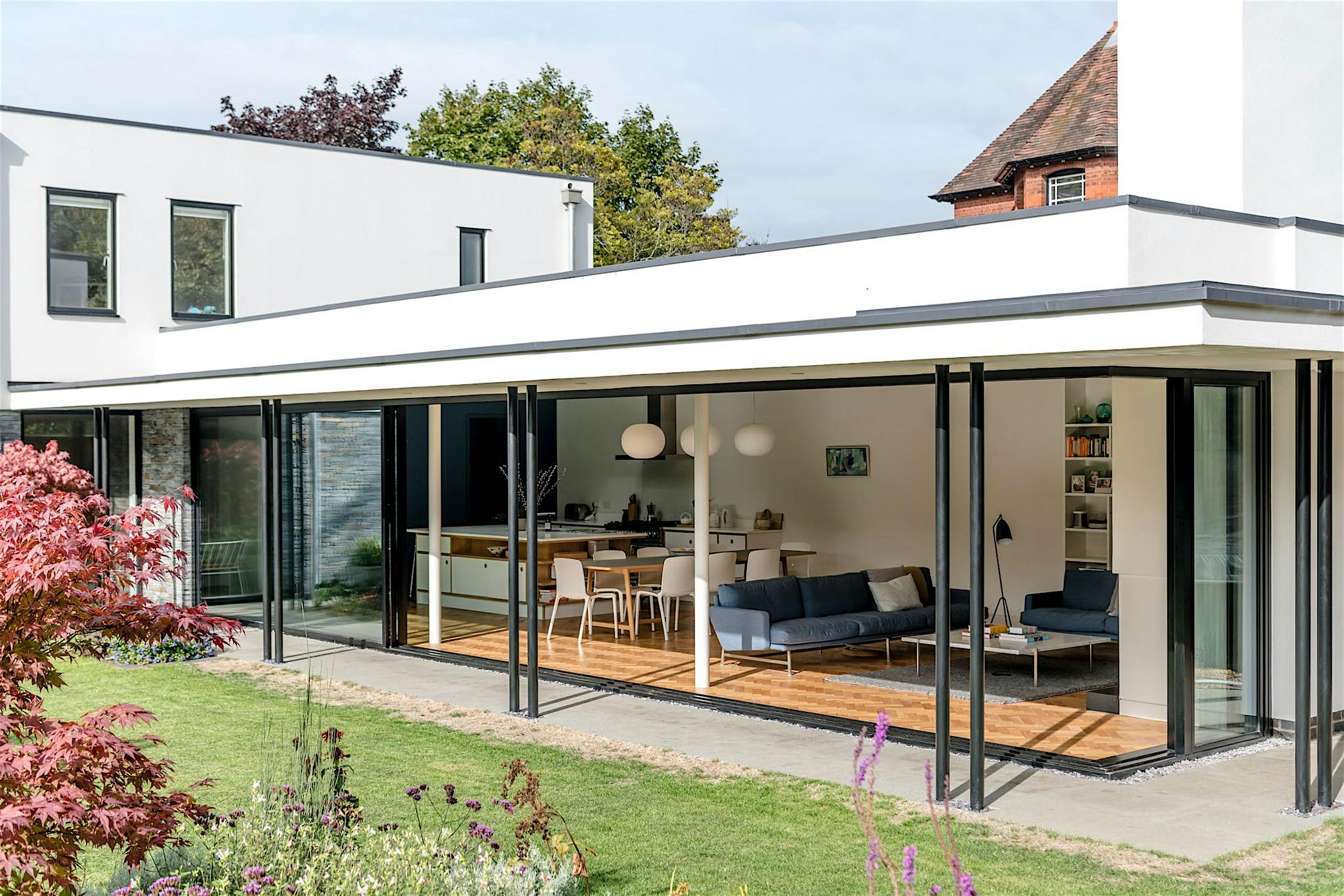
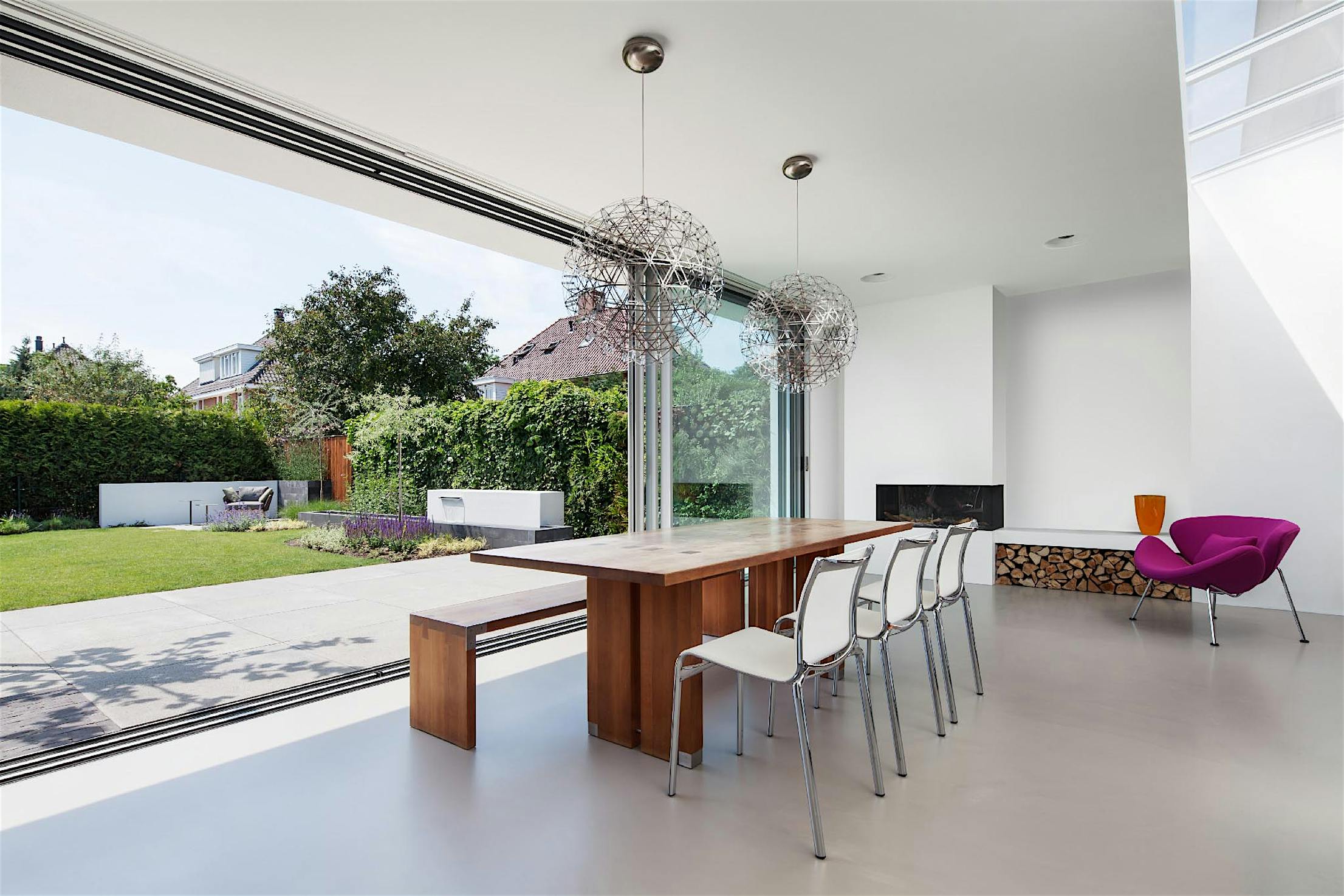
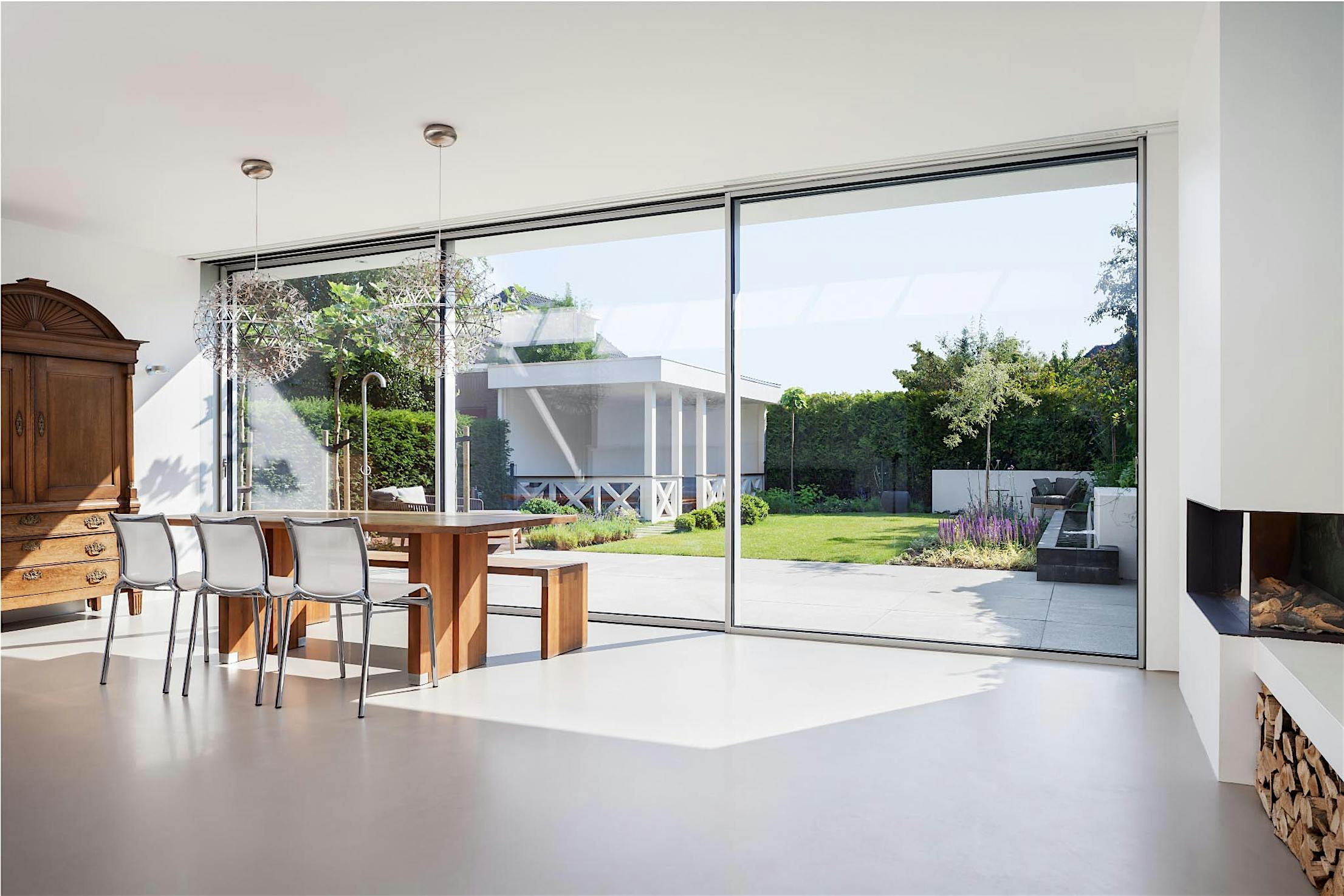
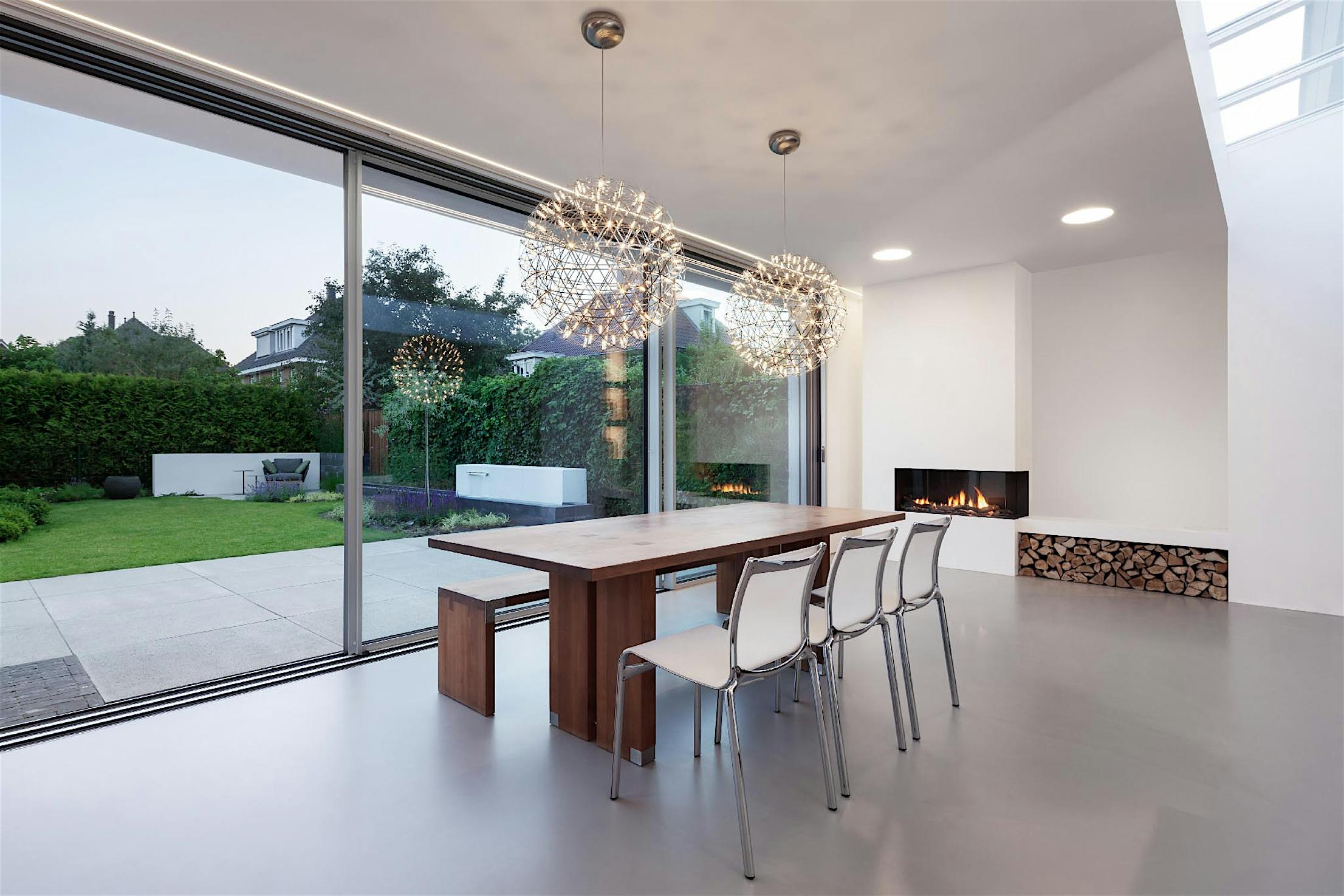
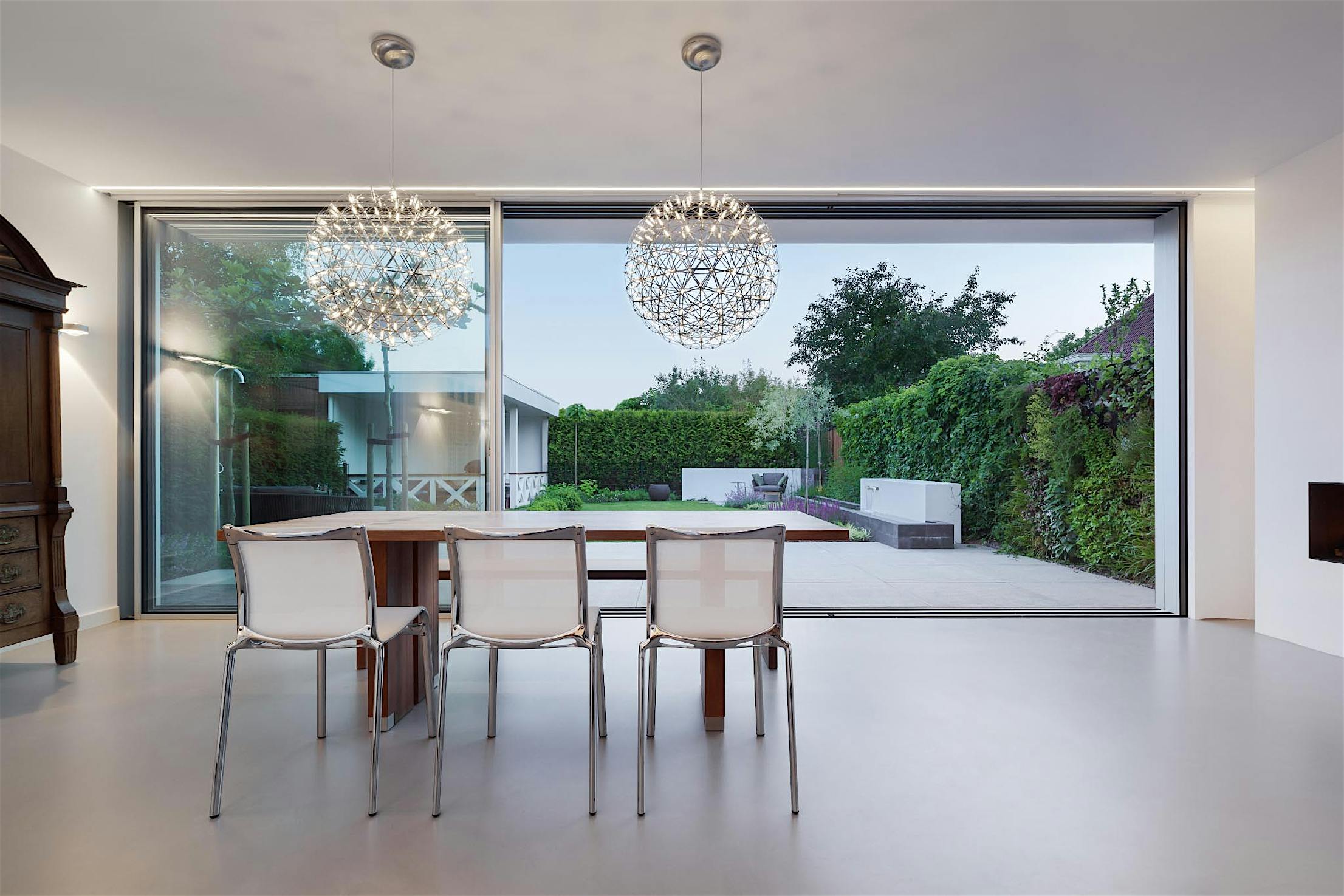
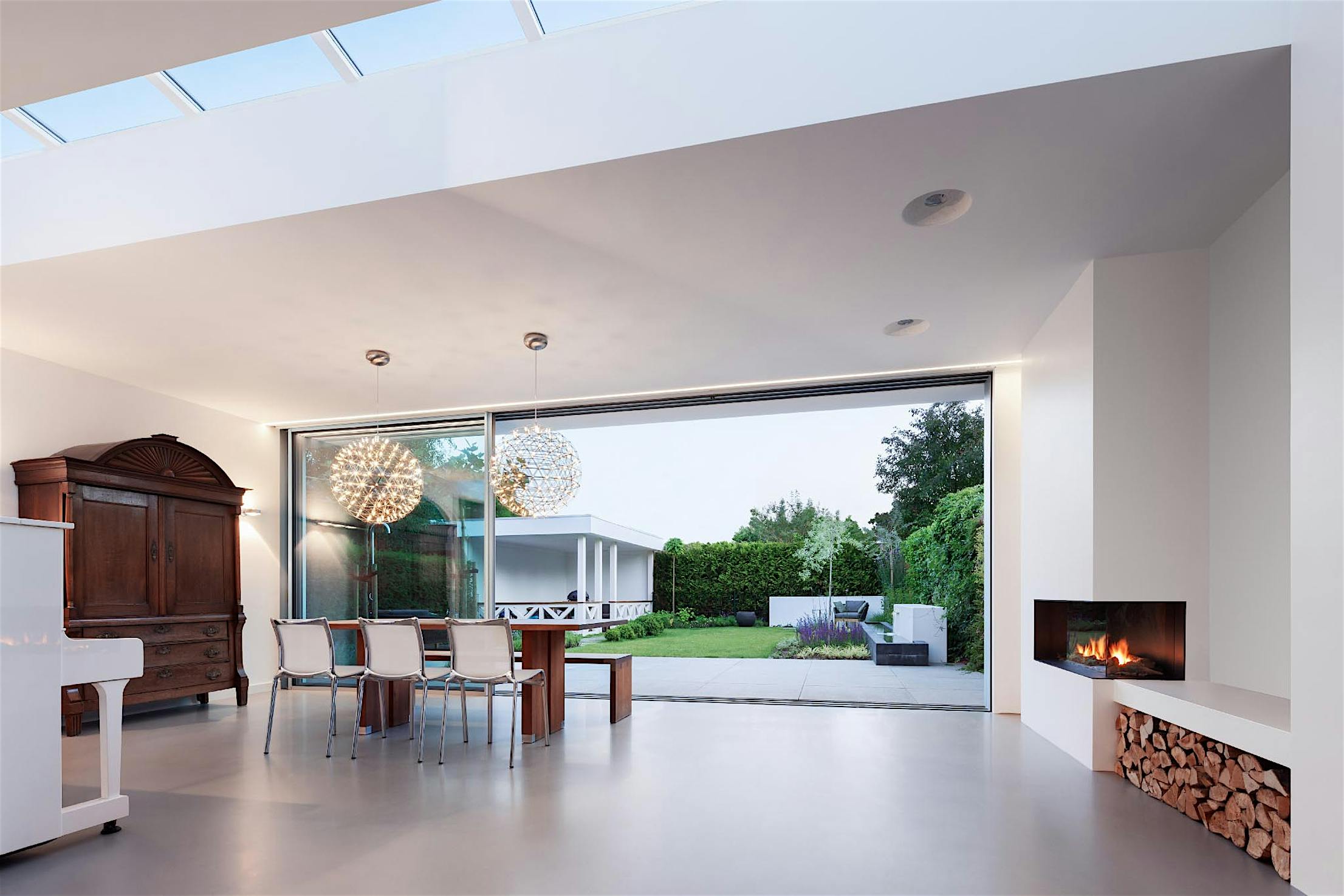
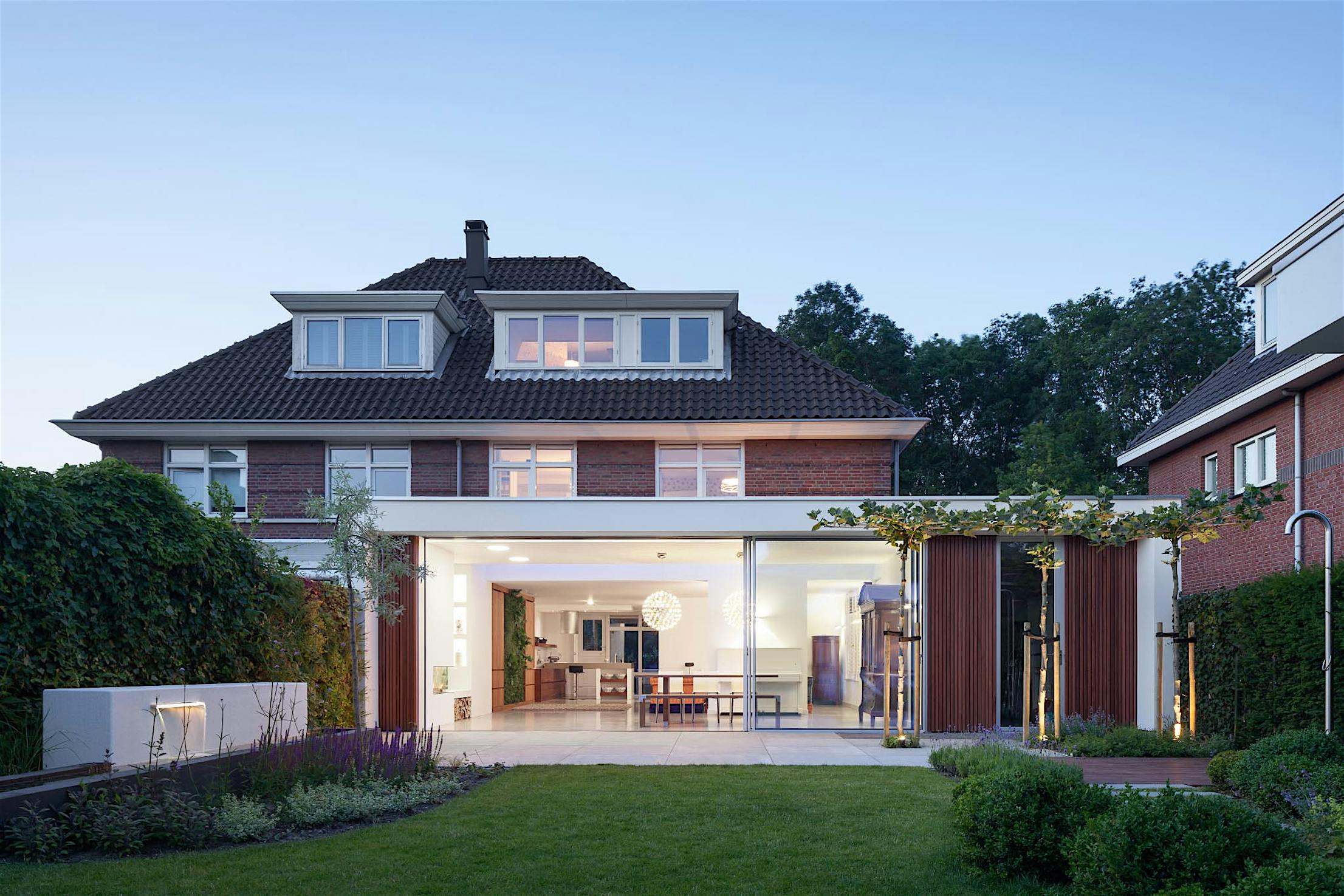
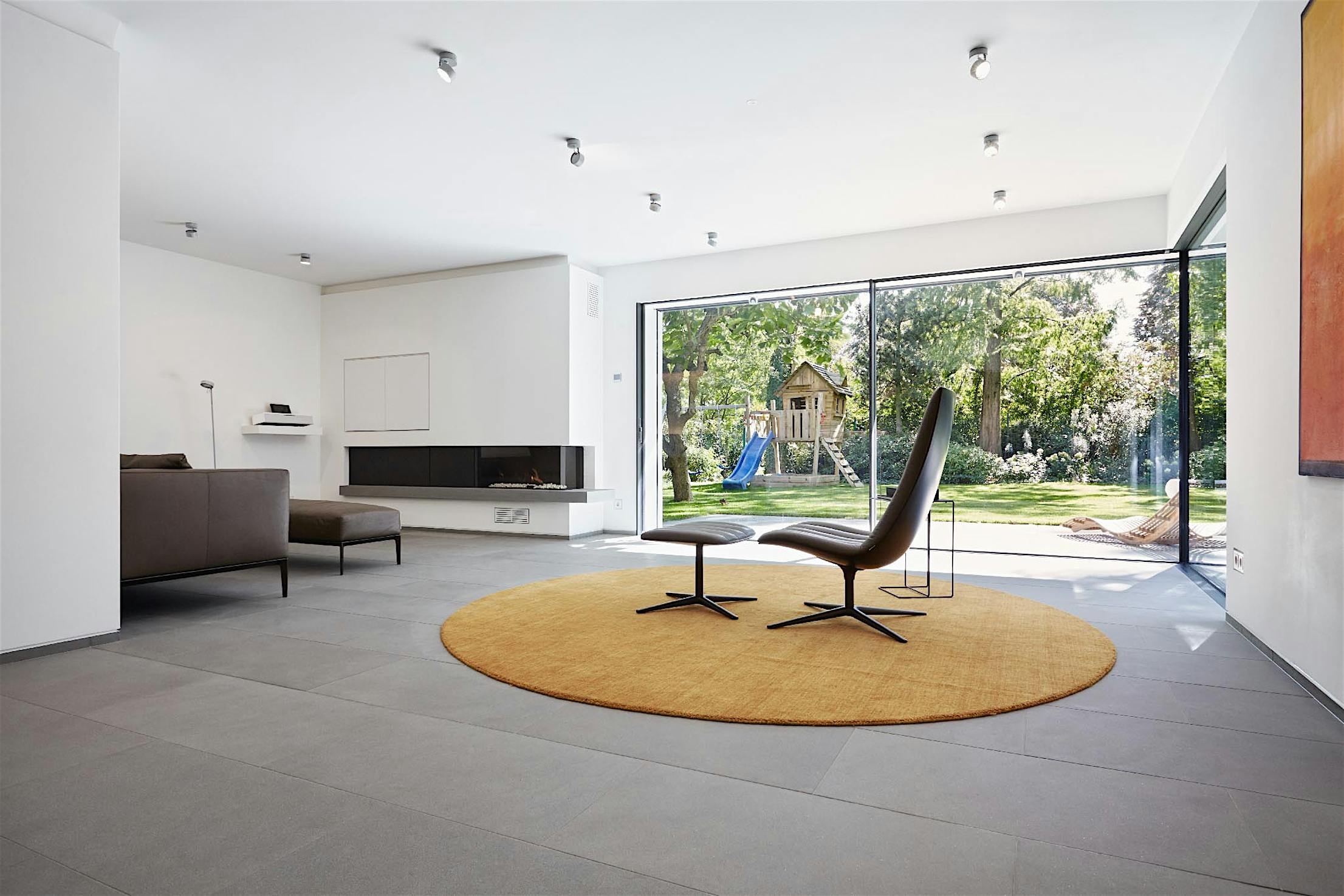
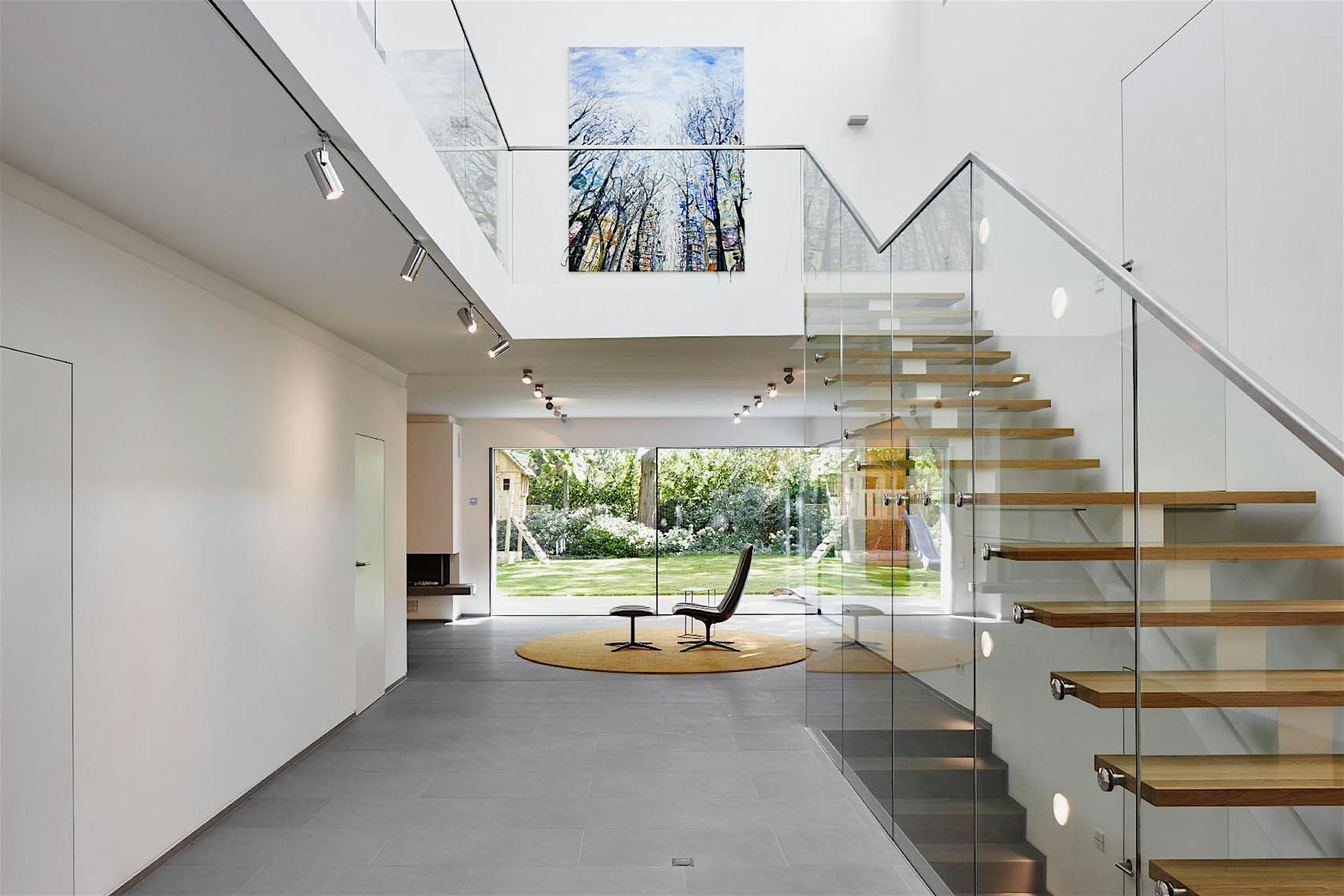
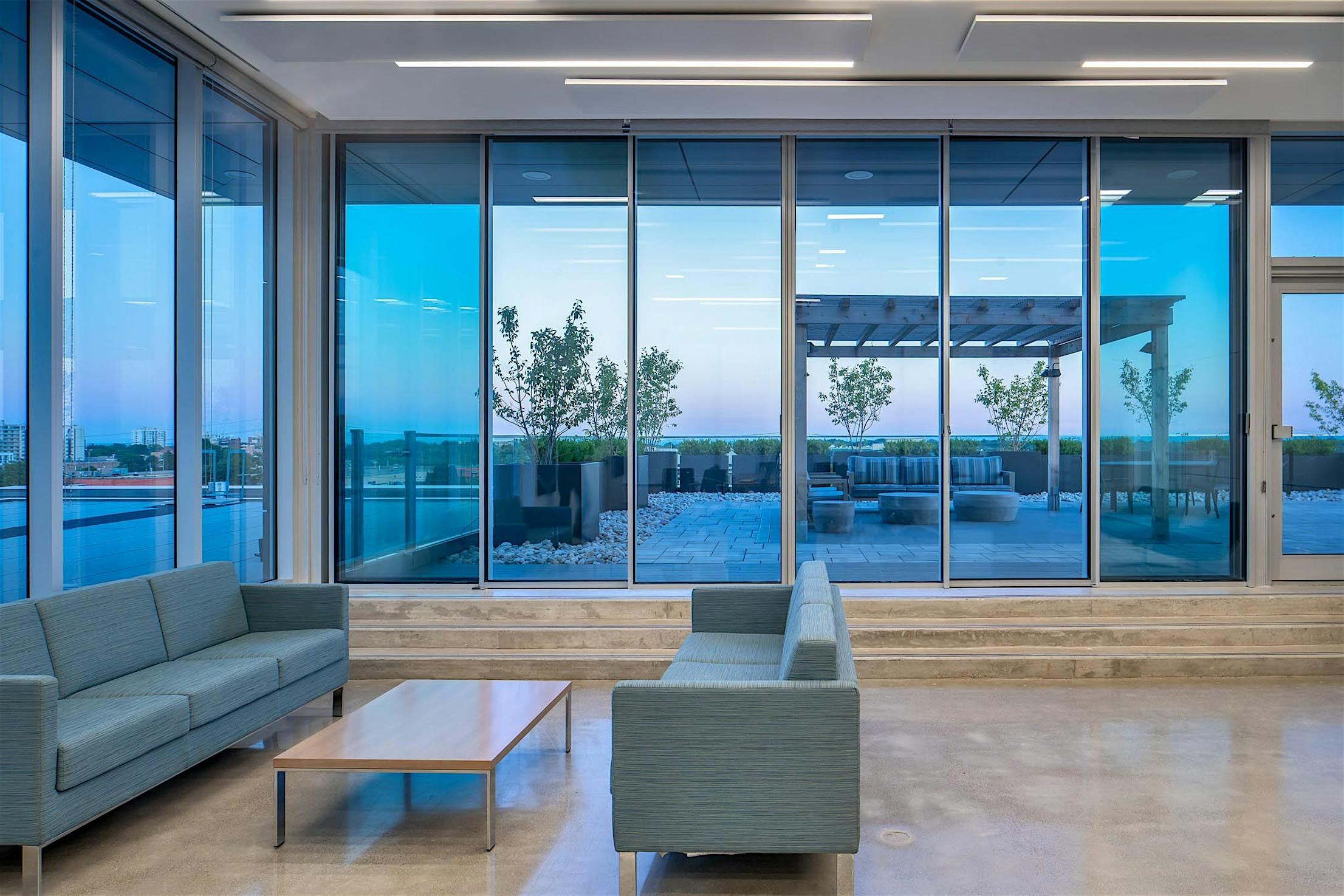
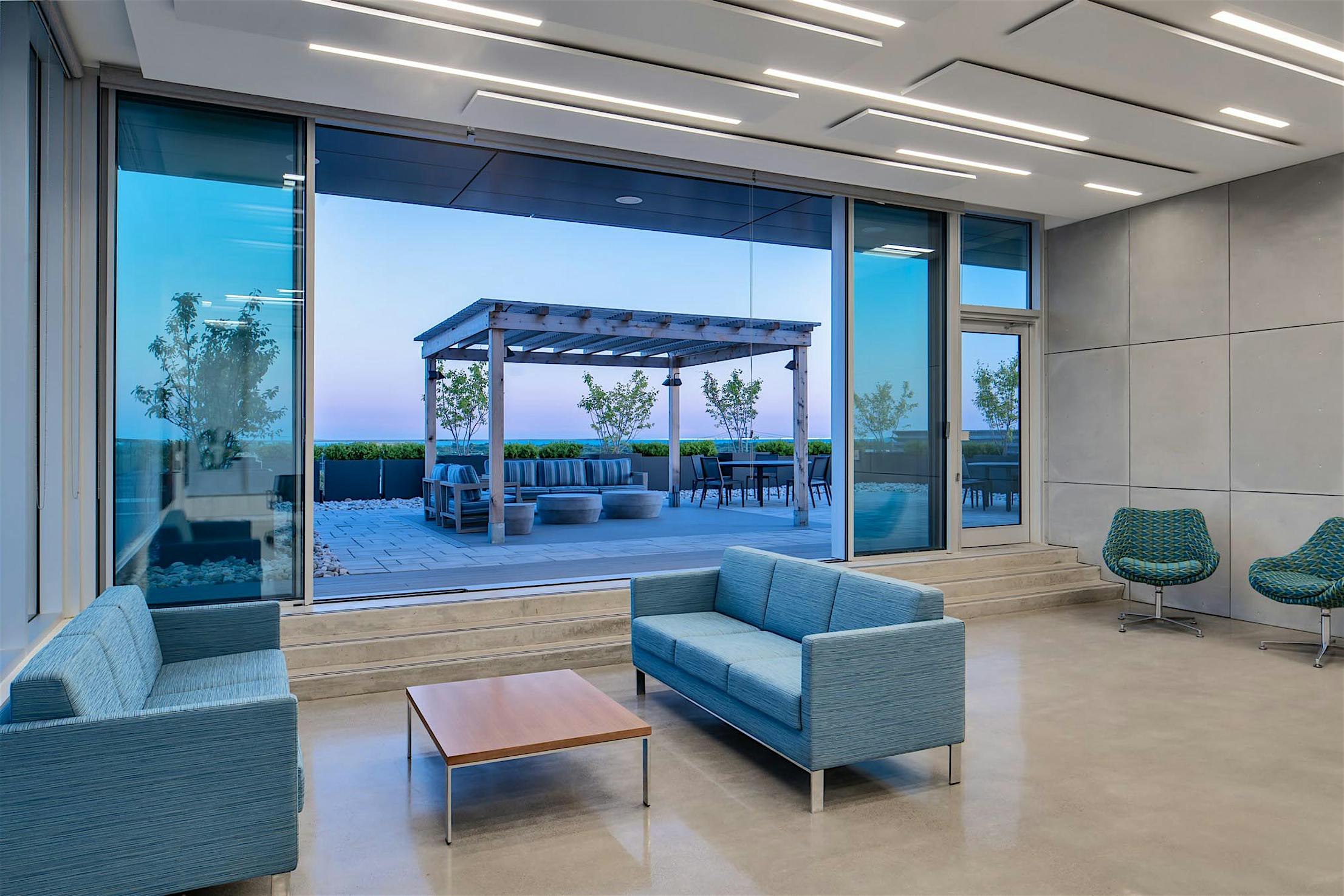
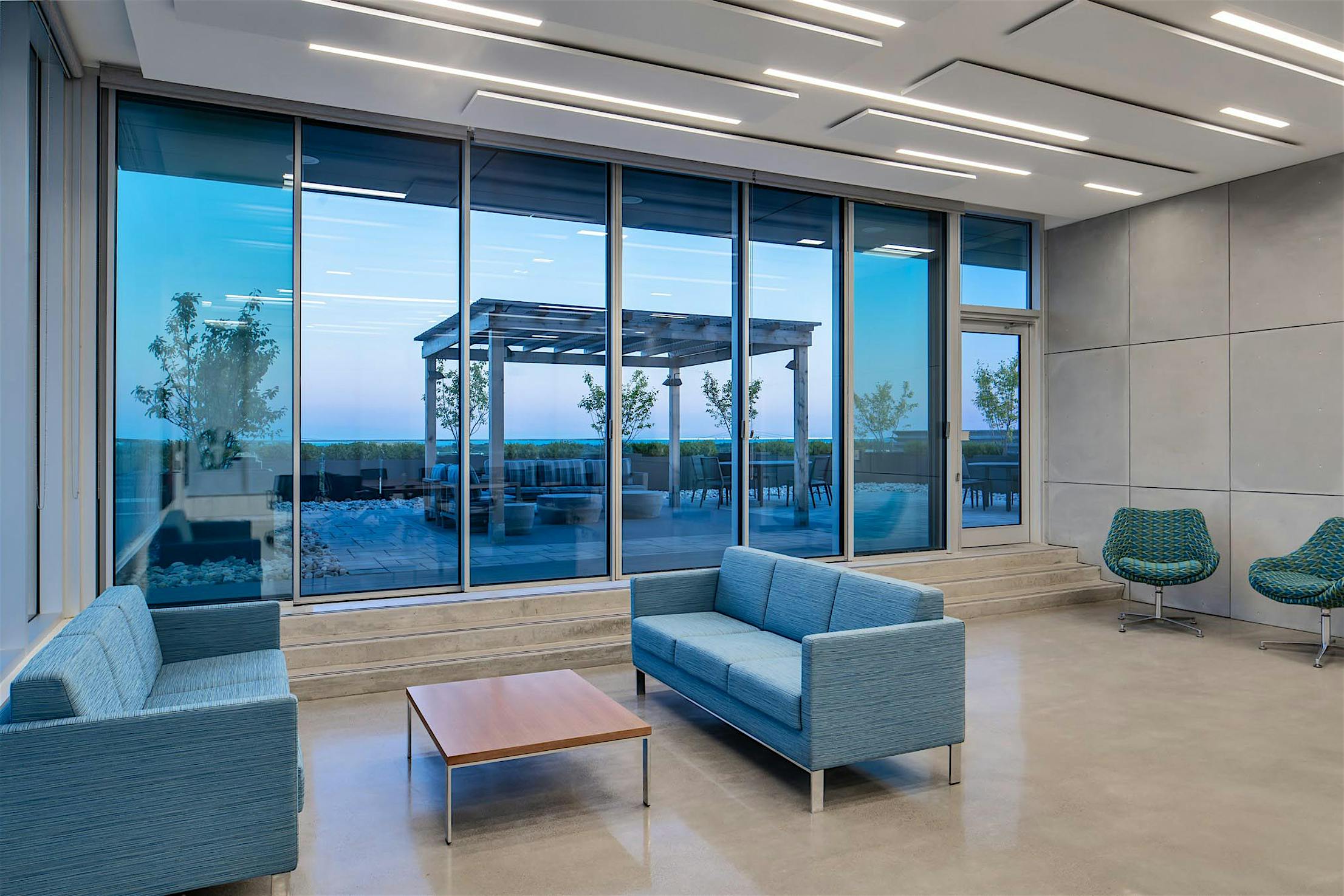

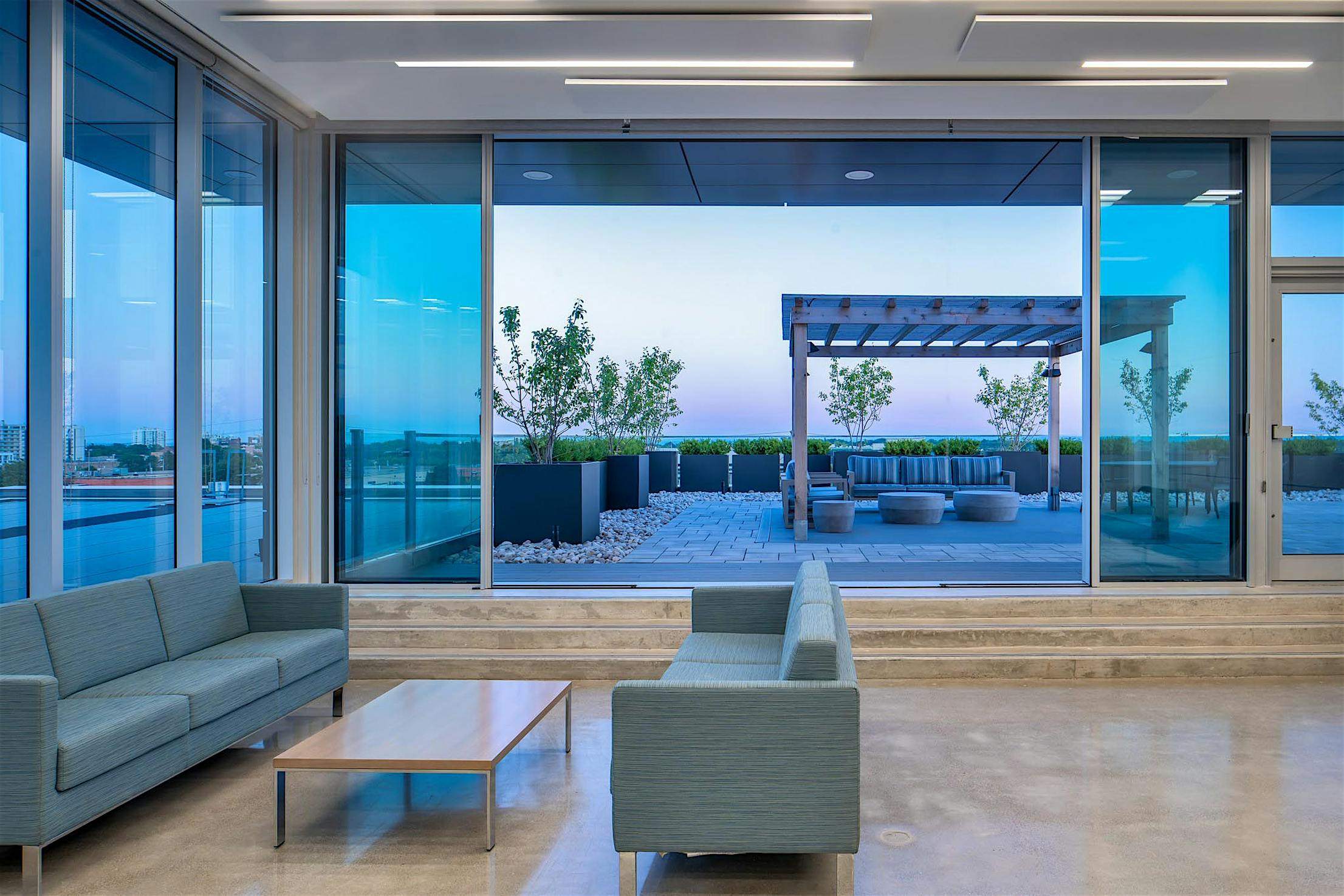
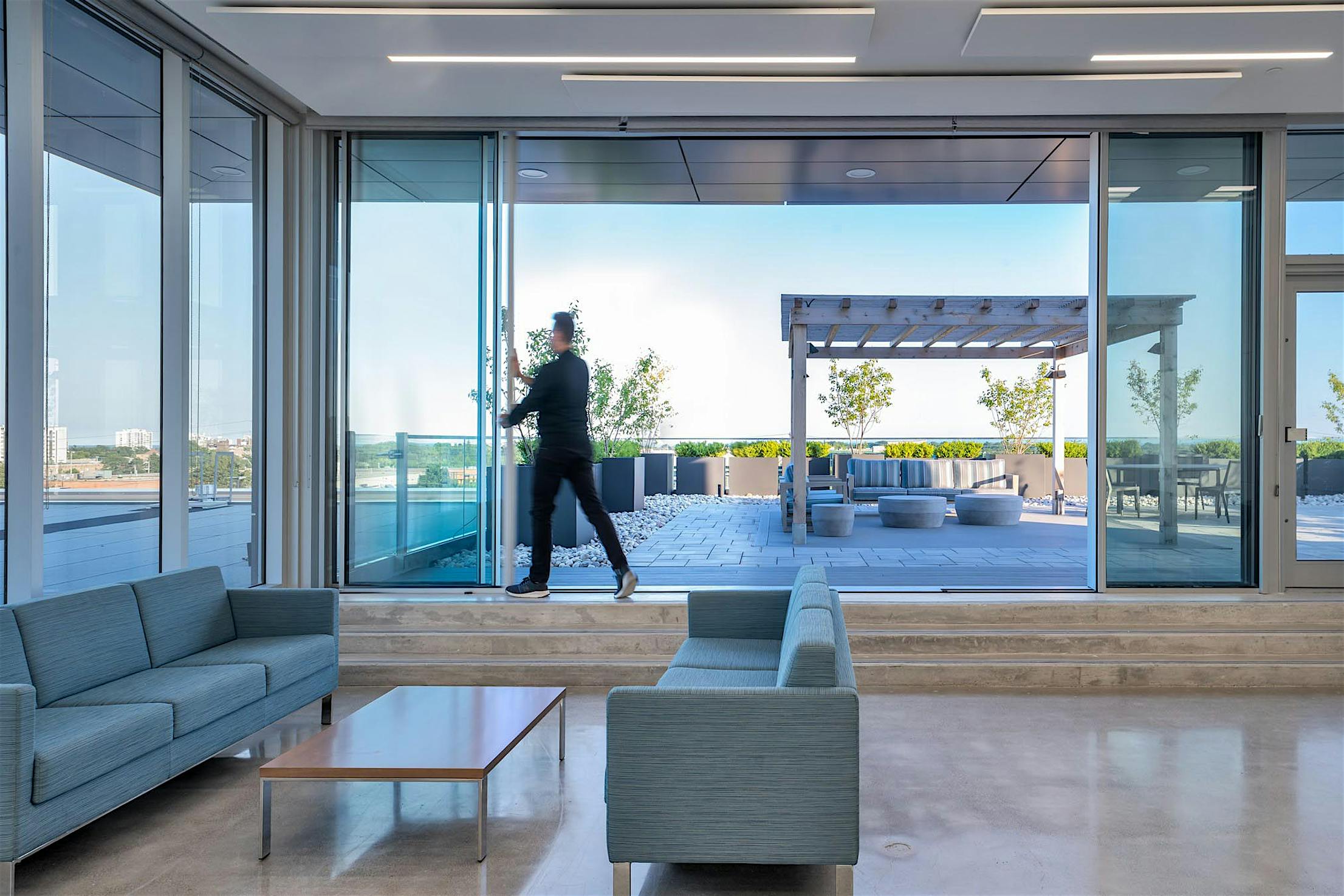
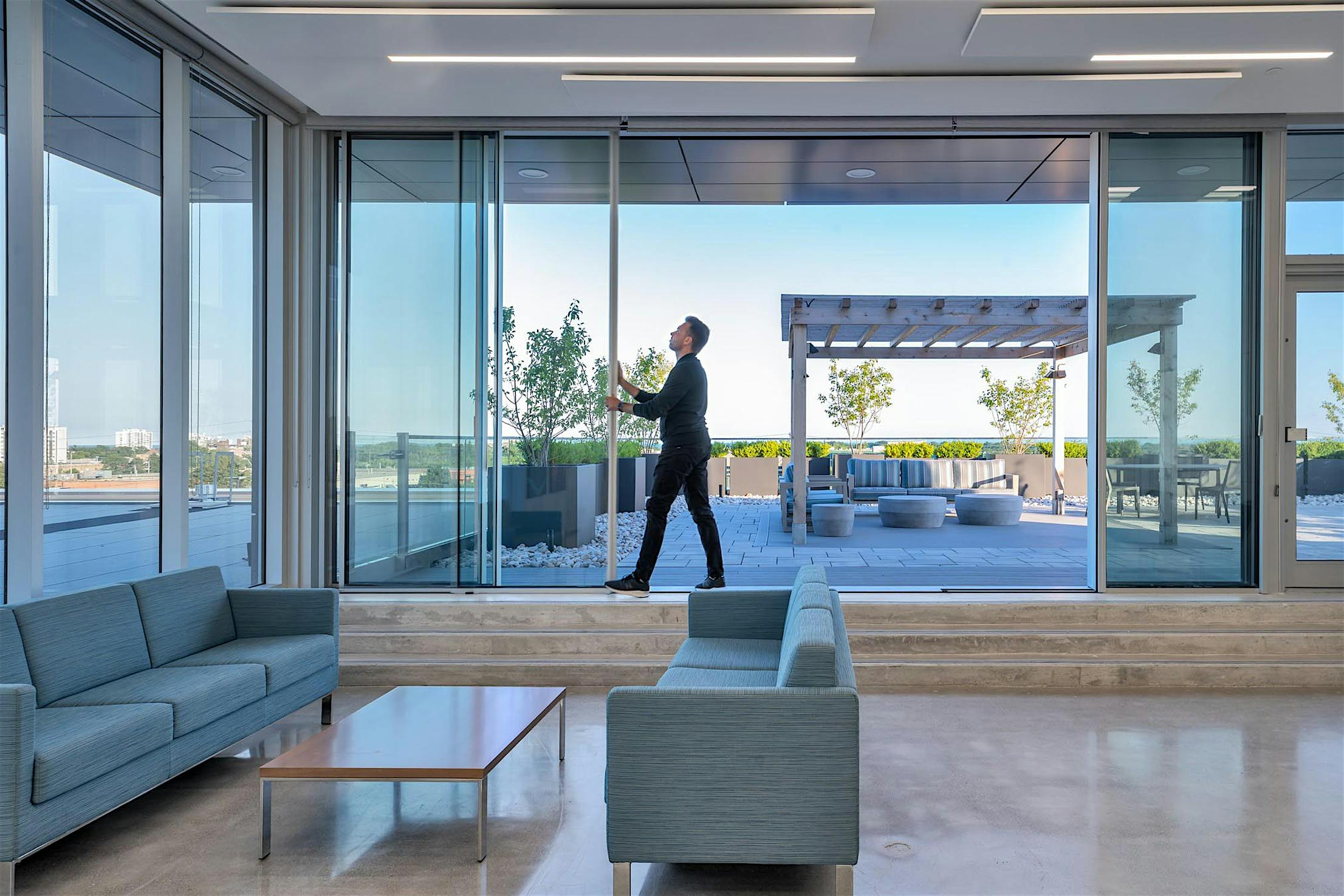
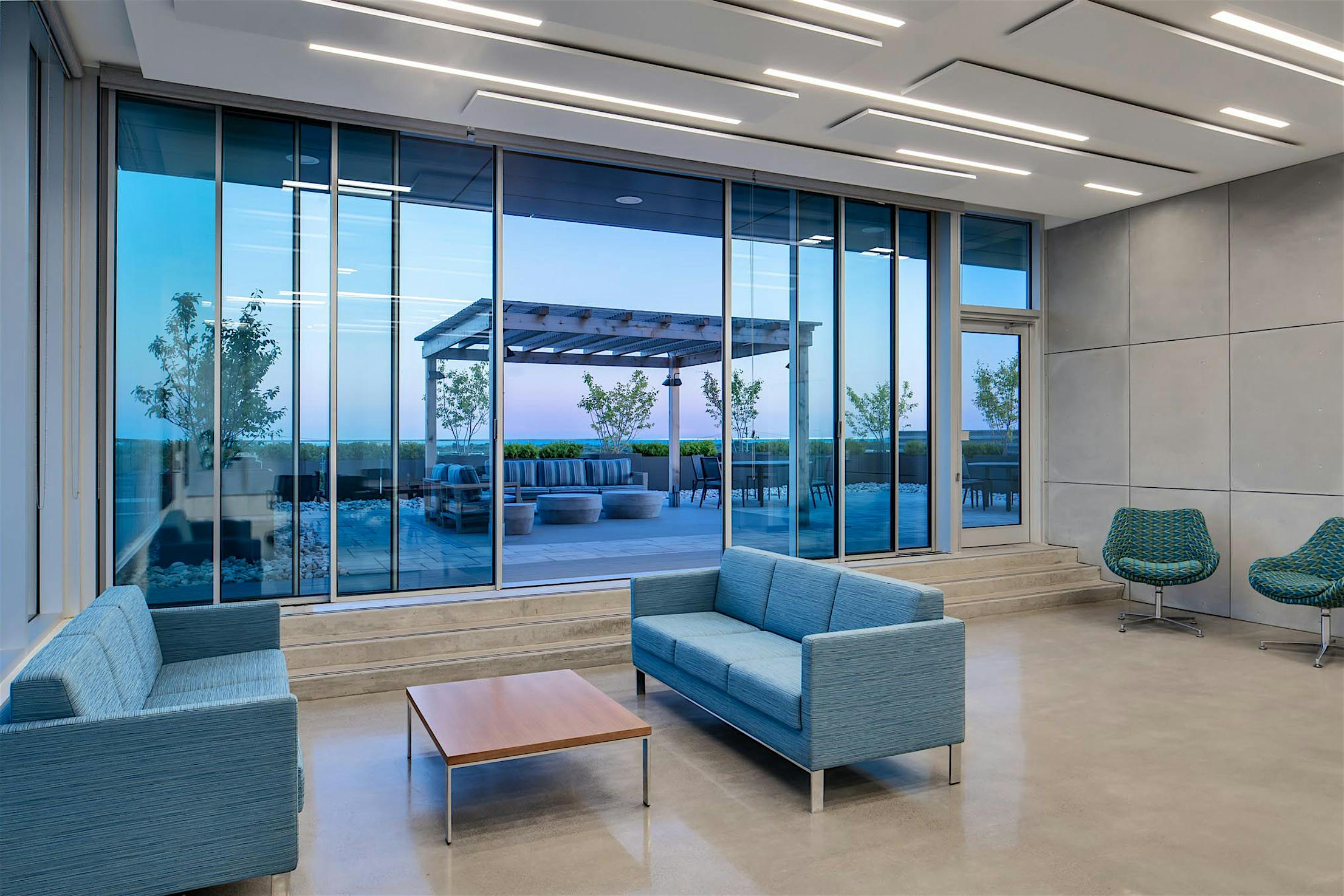
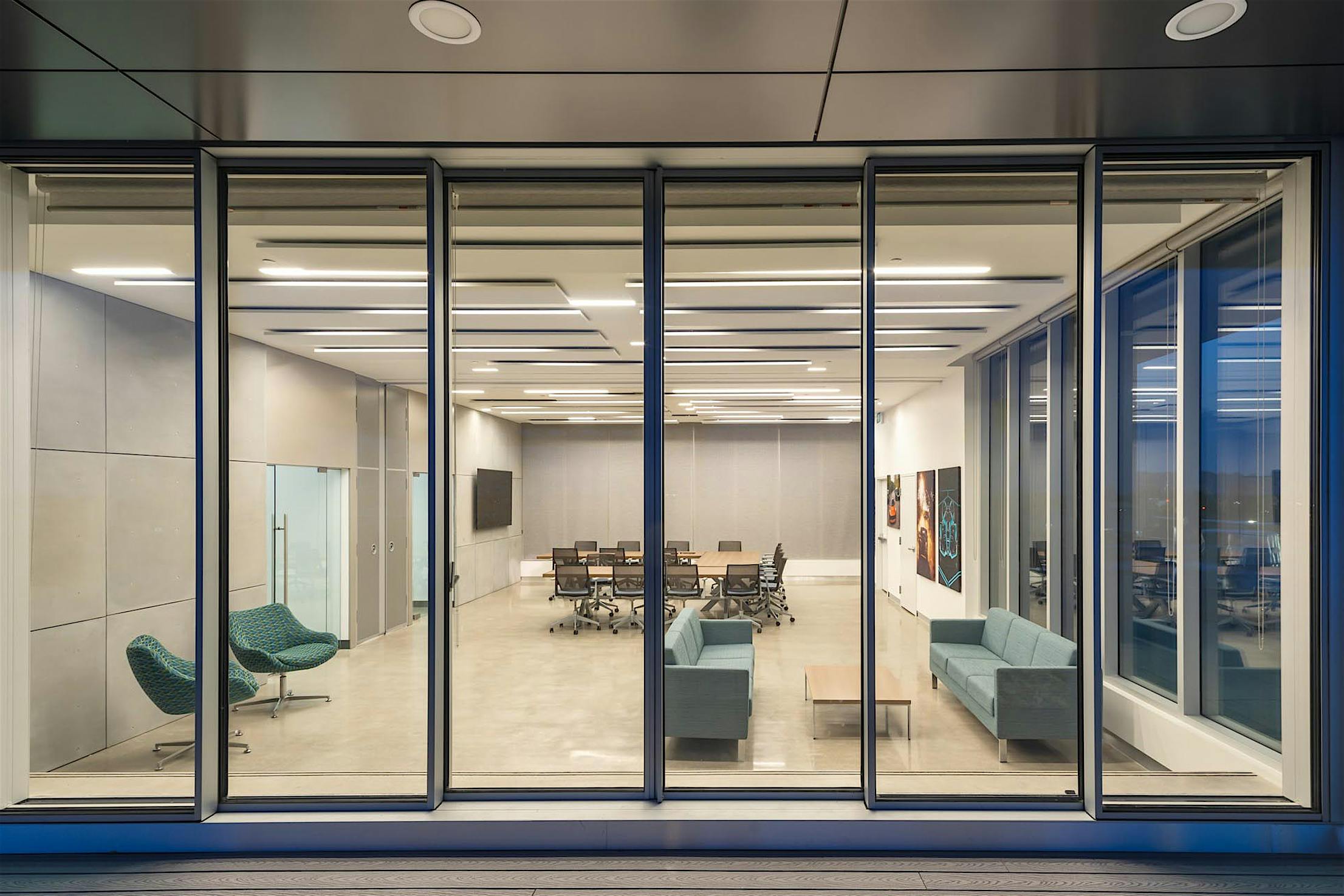
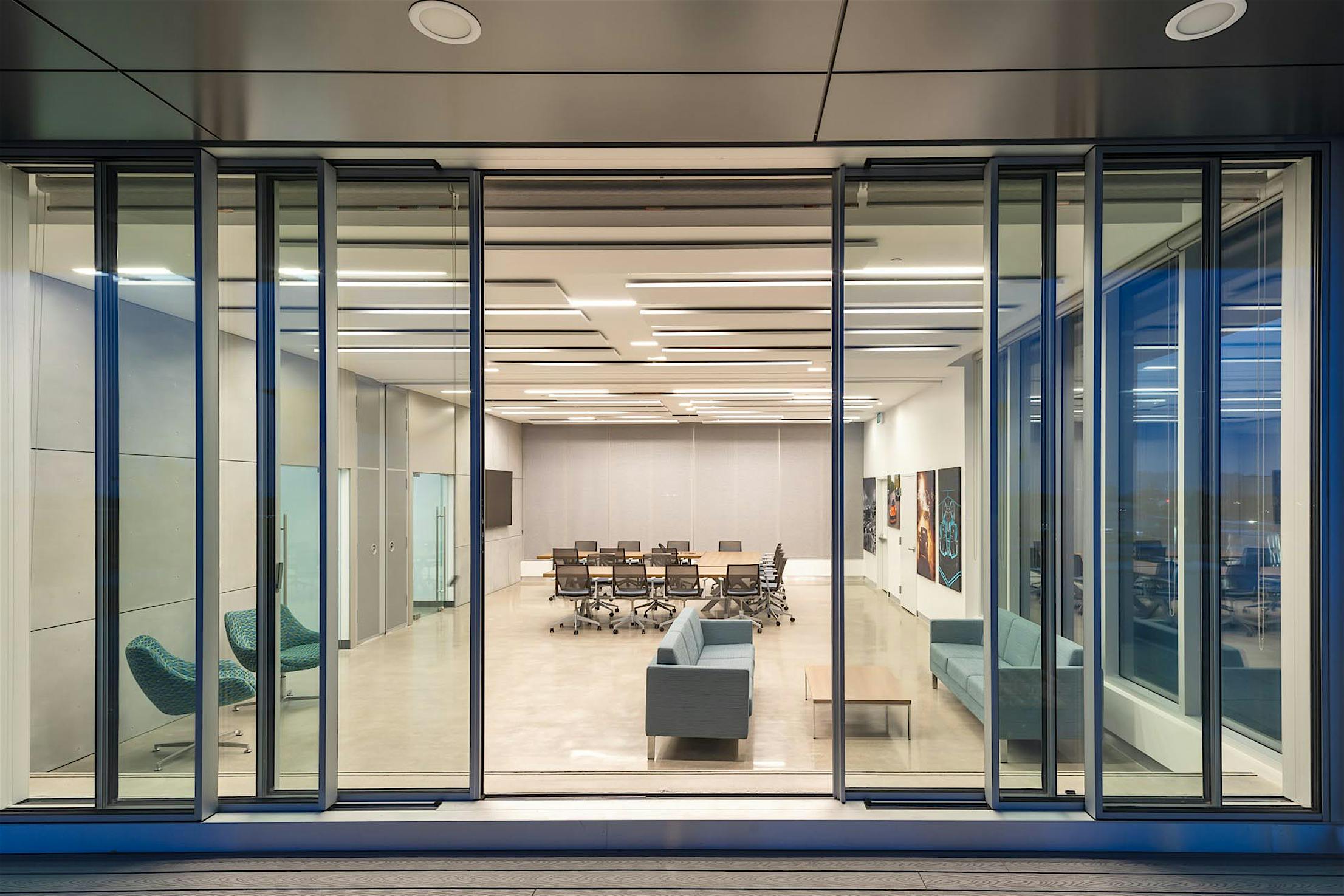
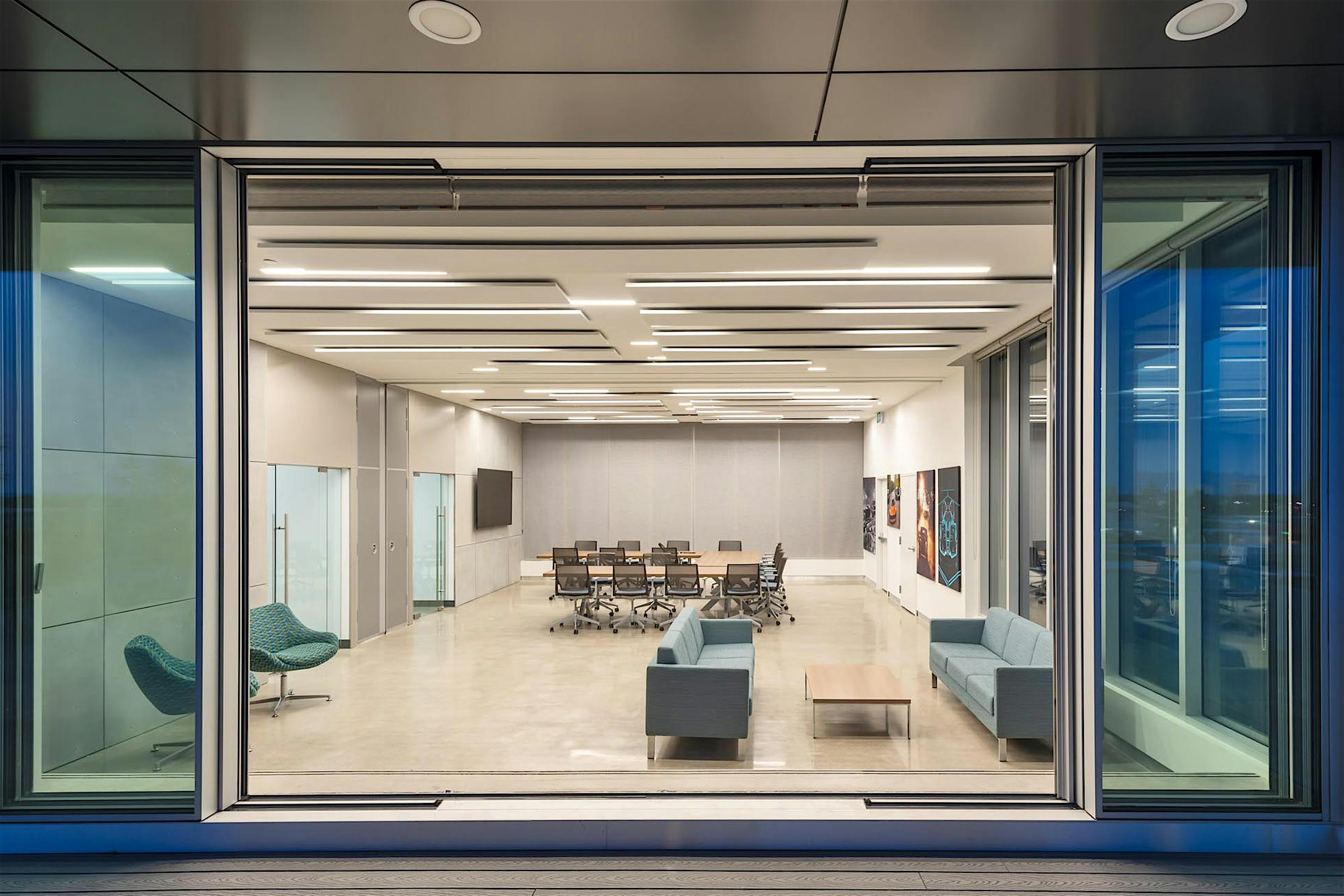
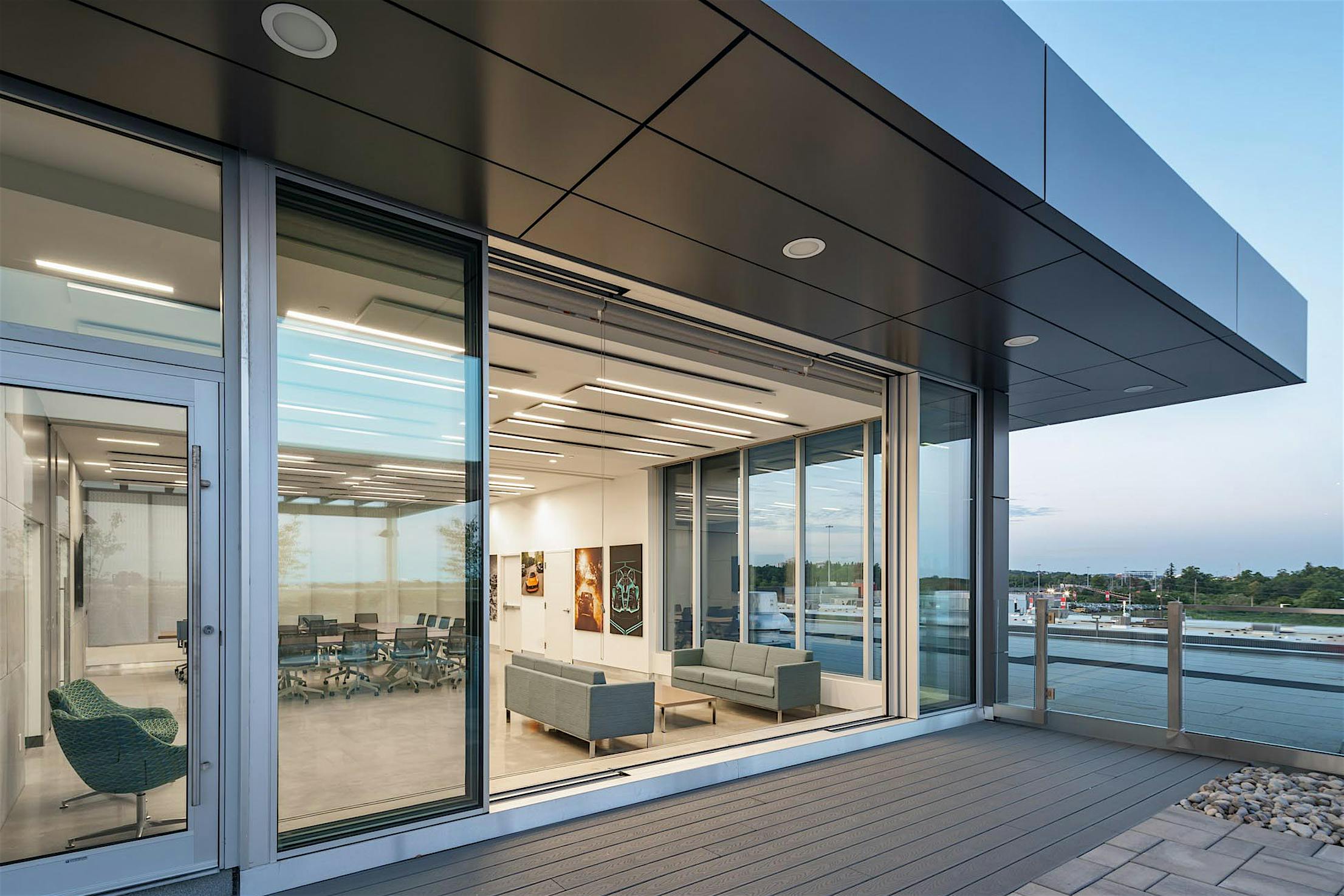
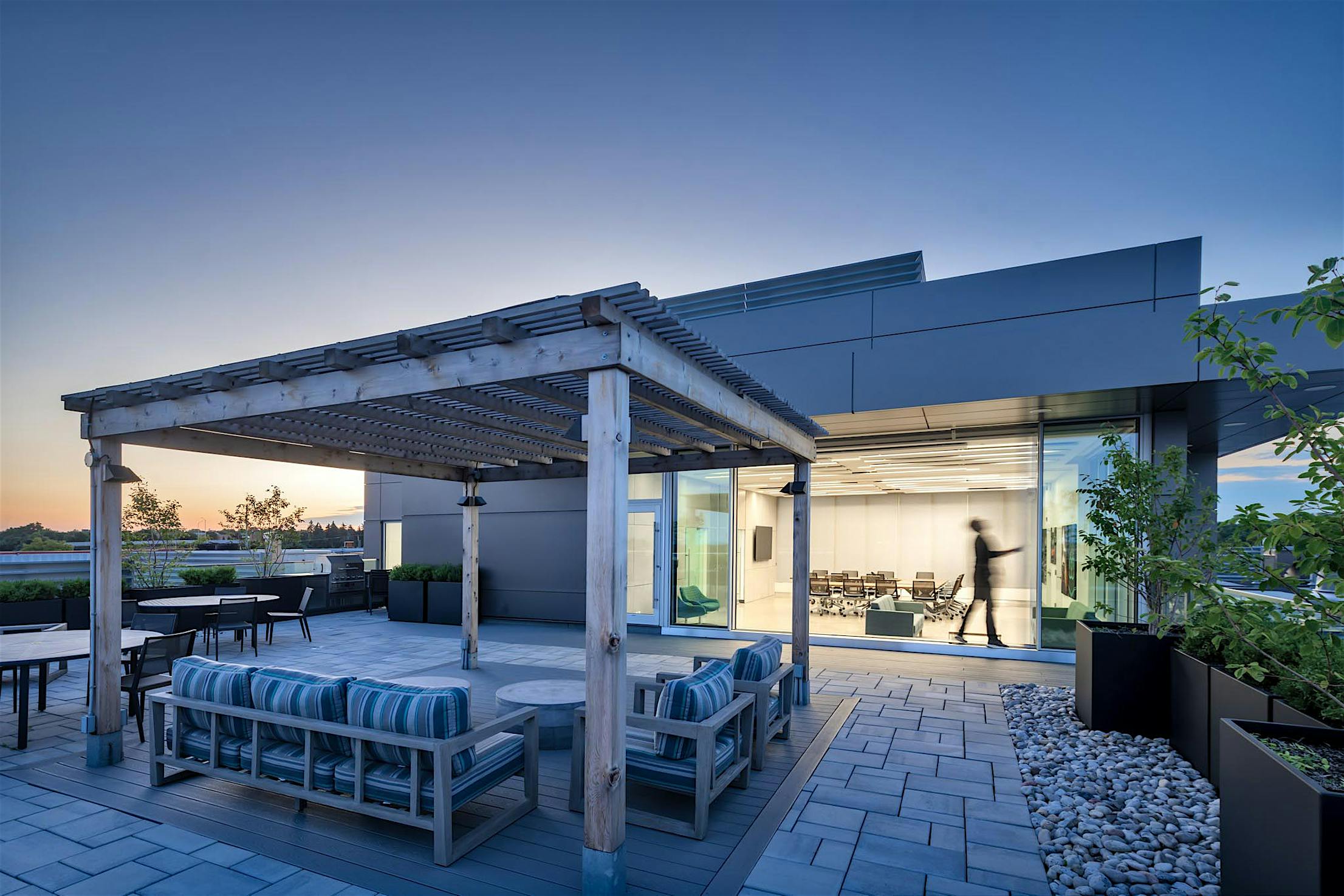
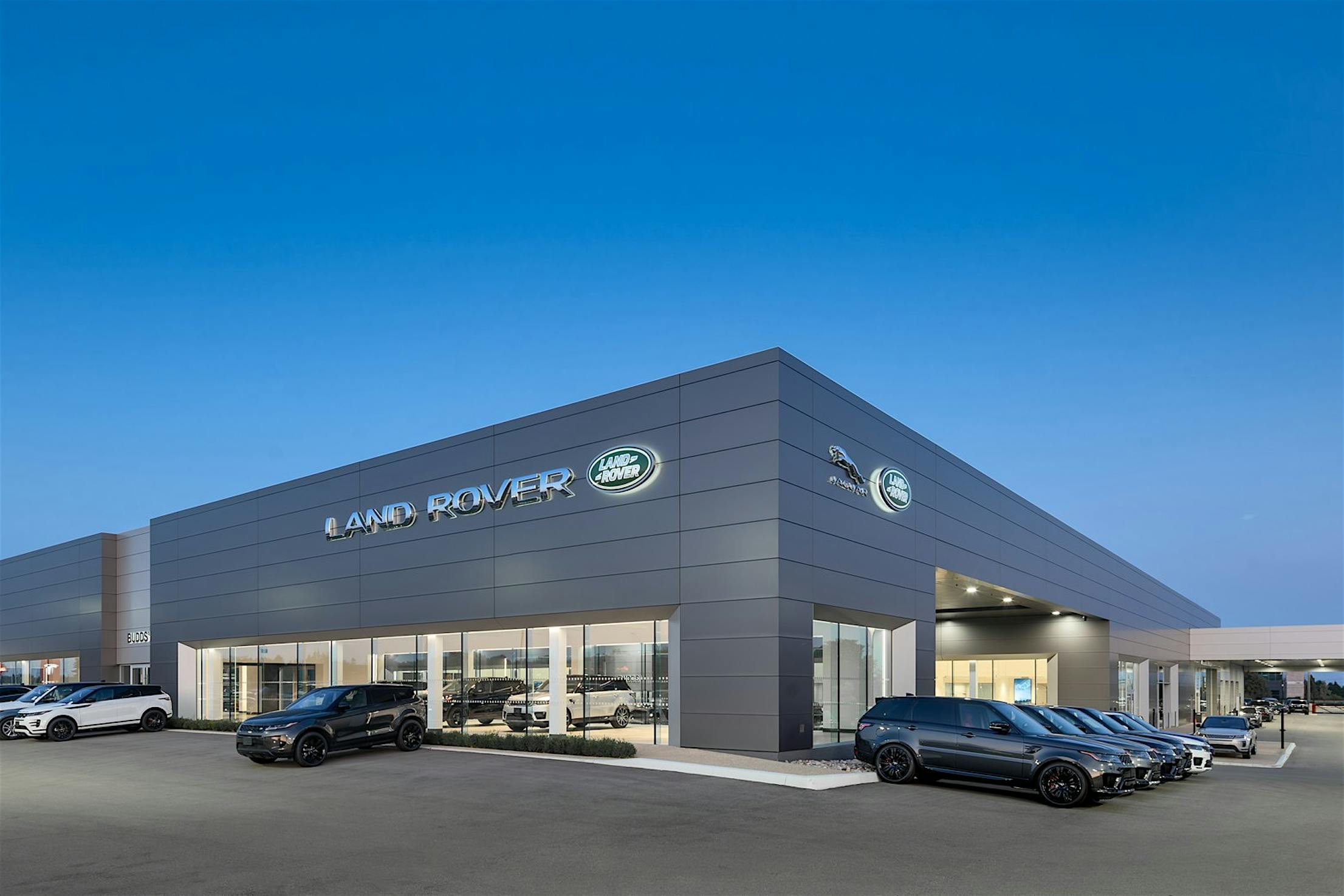
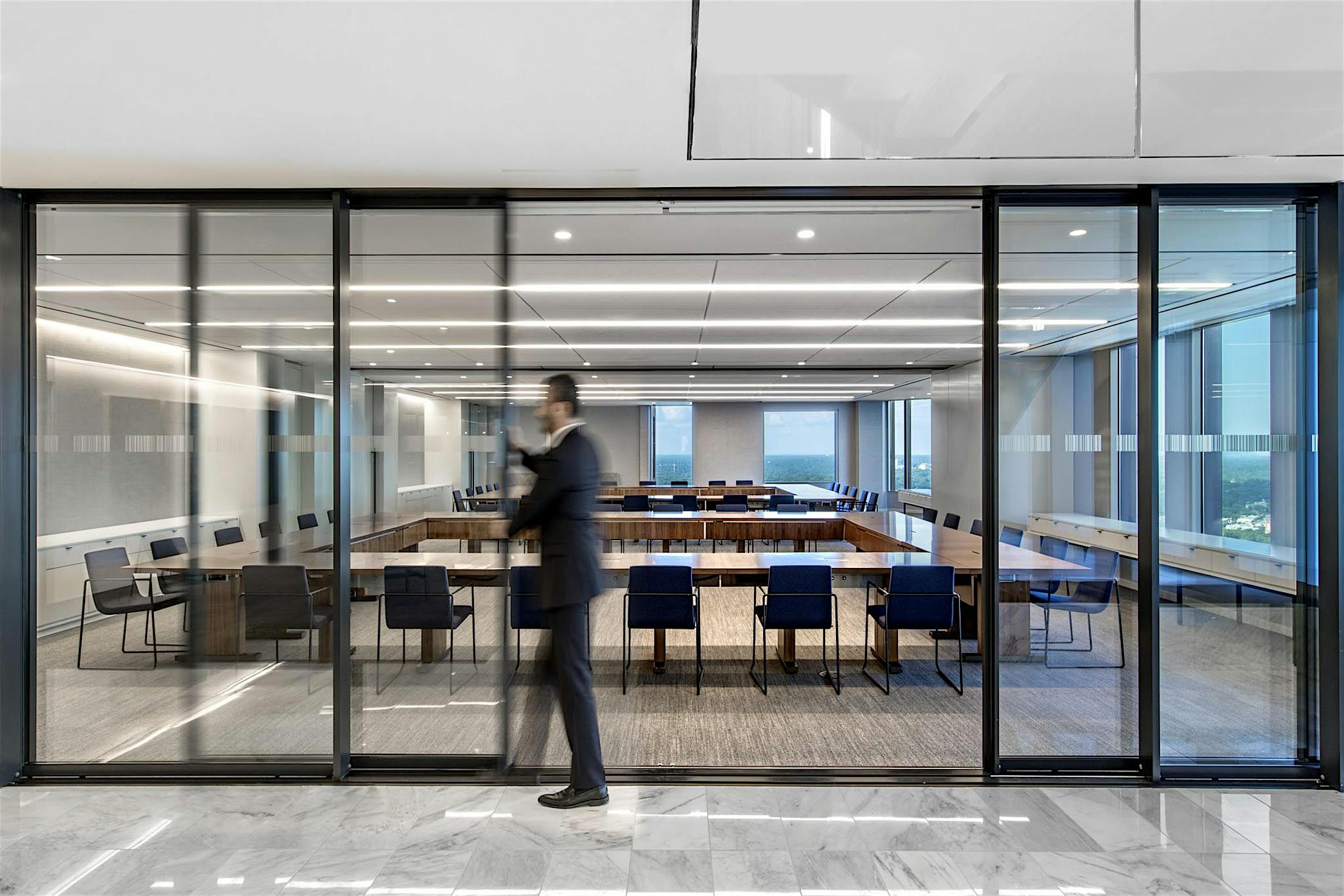
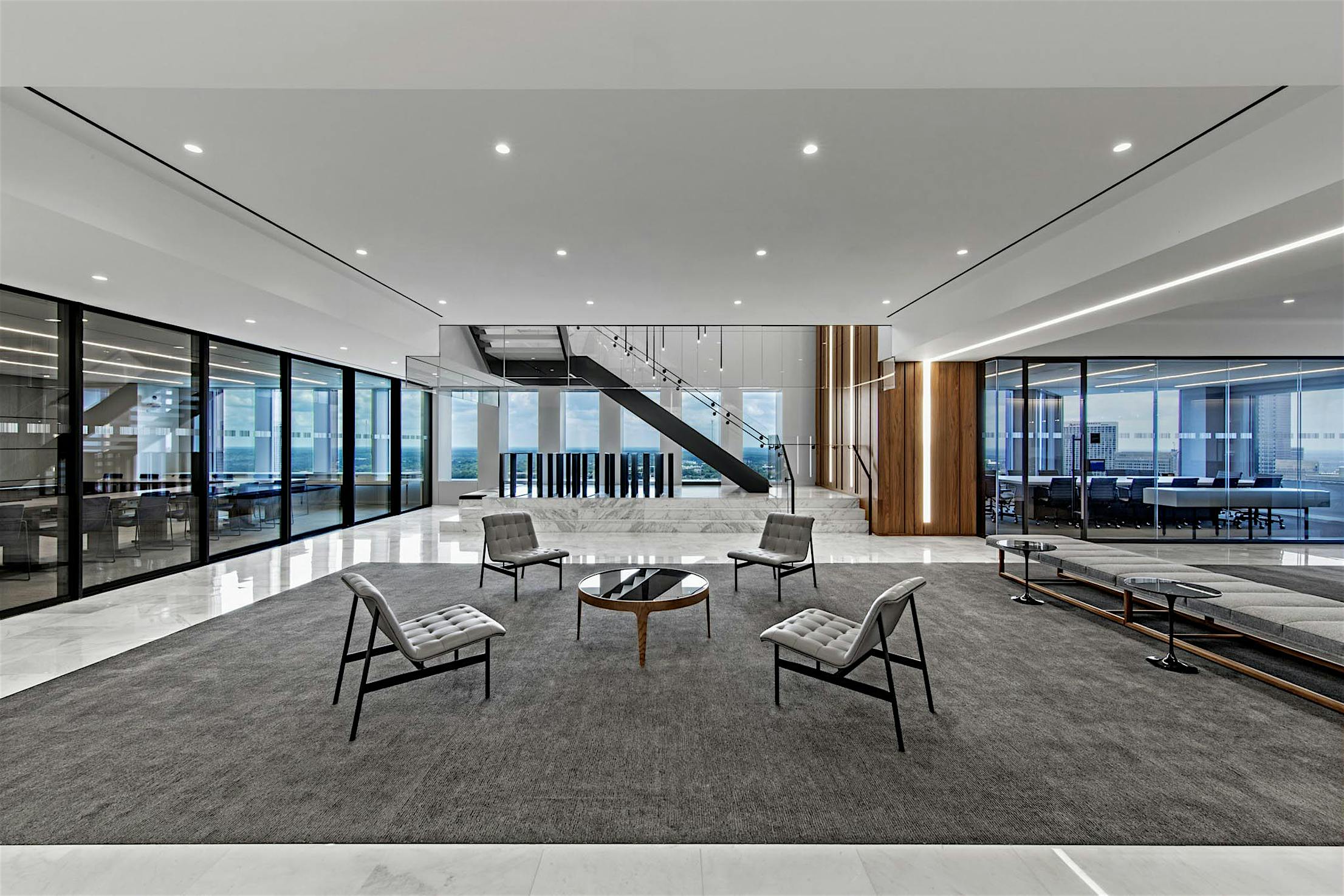
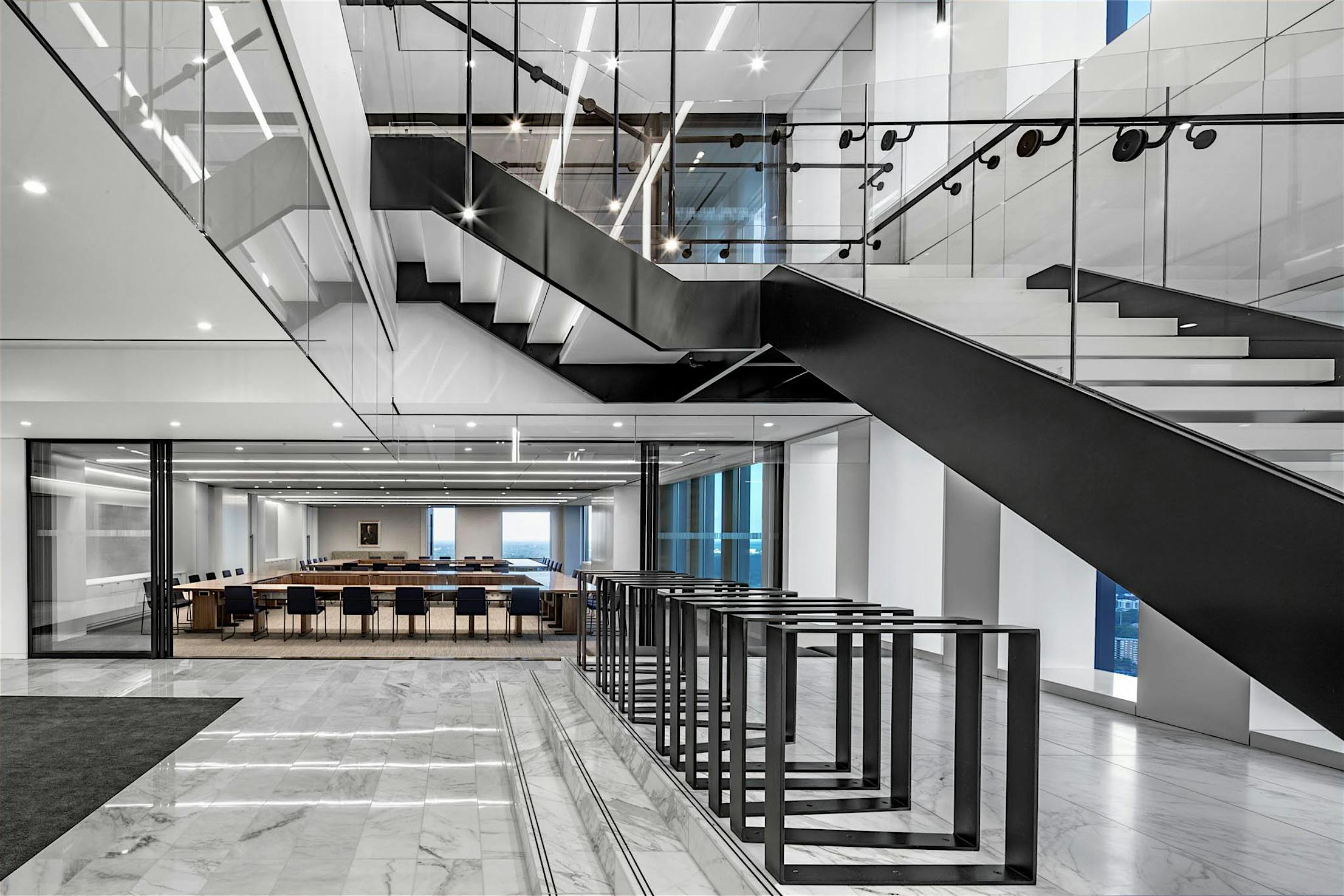
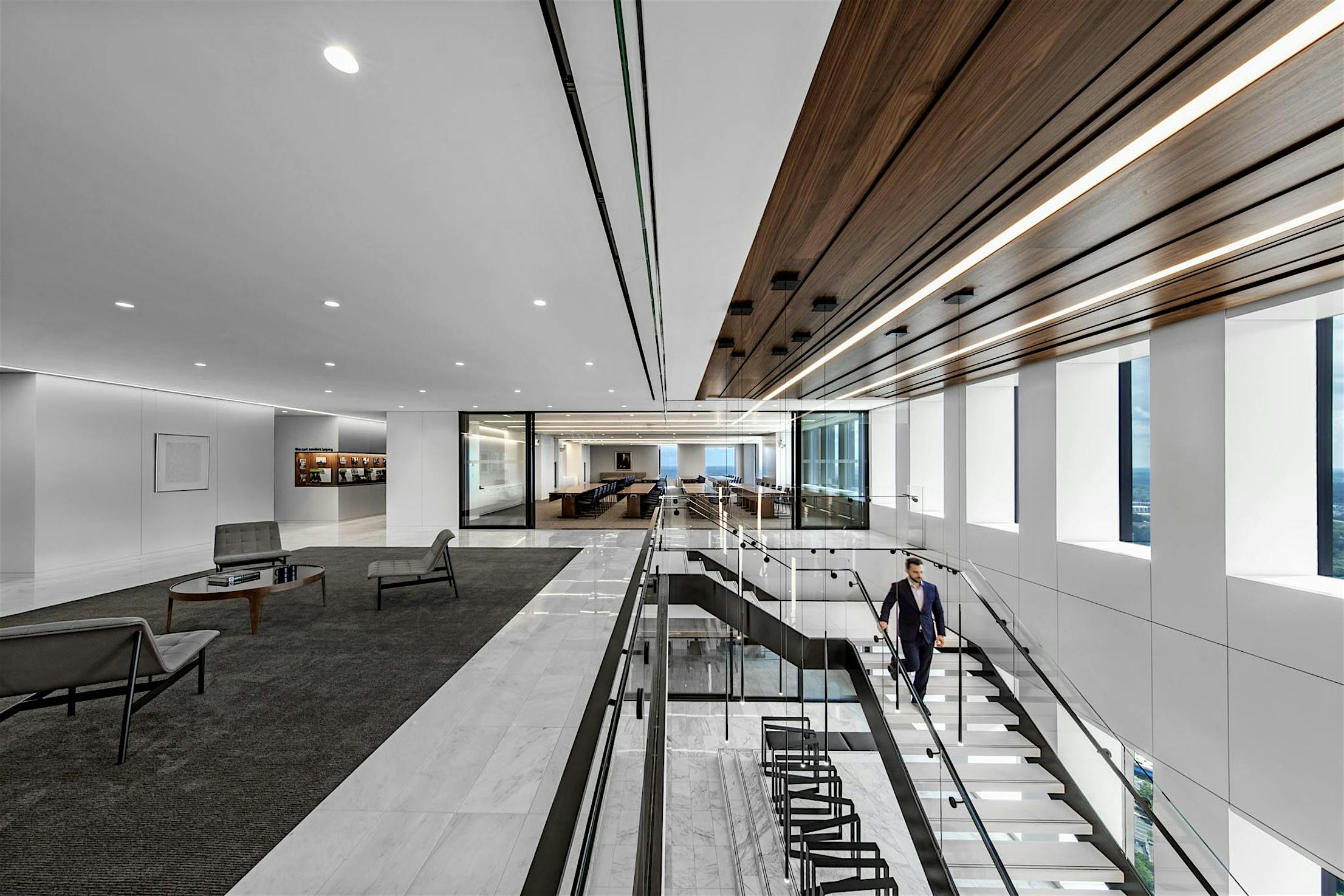

Extreme Weather Resistant
Energy-efficient by design, our glass walls keep the elements at bay, ensuring that even as seasons or temperatures change, your interior comfort will always remain the same.
Certified Testing Standards
NanaWall products endure the latest AAMA testing standards for air, water, structural, and forced entry.
Highly Energy-Efficient
Designed to keep the elements at bay, holding warmth inside while acting as a transparent barrier to the weather outside.
Sustainable Design
NanaWall products contribute to multiple LEED rating systems and potentially several credit categories.
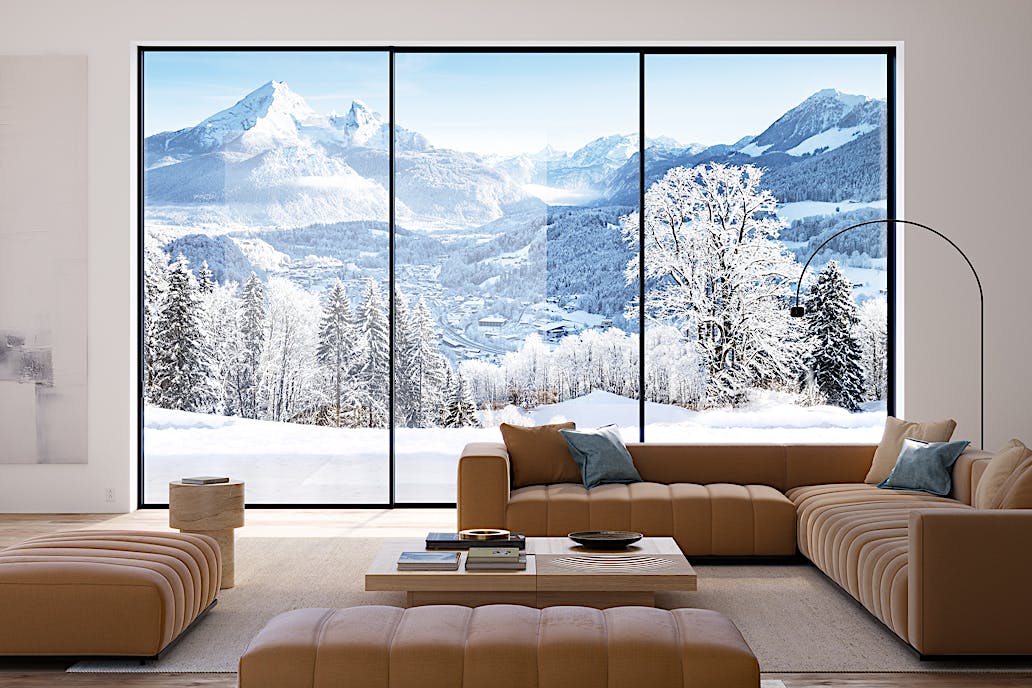
Test Results
cero is NFRC-certified, rated, and labeled and has Florida Product Approval. Additionally, cero has been put through rigorous testing at certified and accredited independent laboratories for thermal, water, air infiltration, structural load, operational force, and forced entry.
See Air, Water, Structural, Thermal, and Forced Entry Results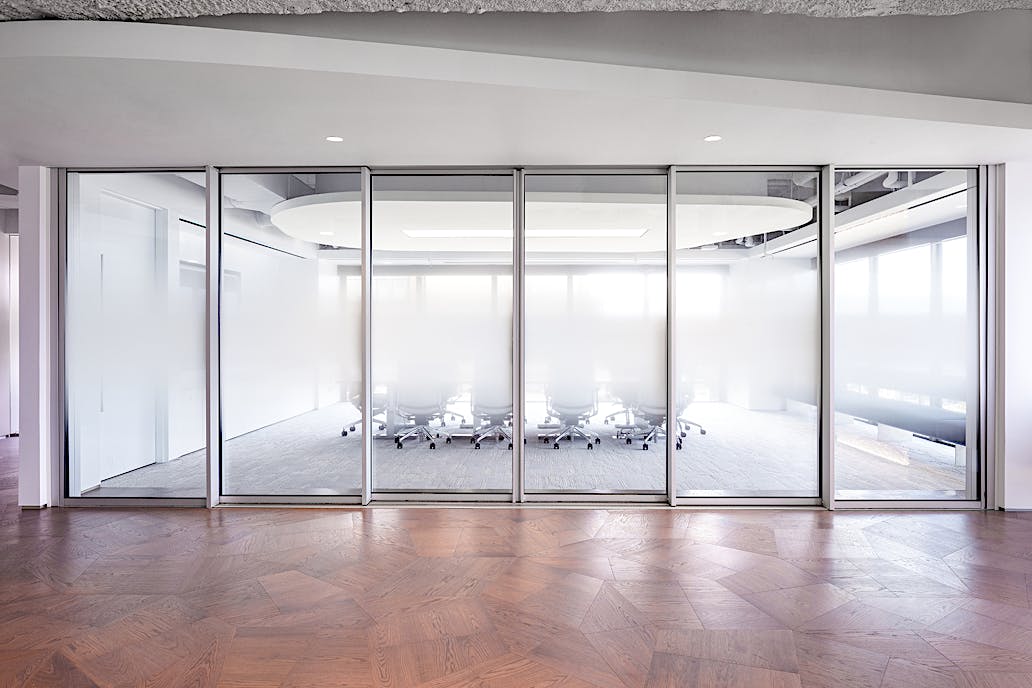
Sound Ratings – Up to Unit STC 43
cero II has been tested at an accredited and certified independent laboratory. We test our product to meet the highest standards of ASTM E90, ISO 10140-1, 2, 4, 5. STC calculations meets standards of ASTM E413, and ISO 717-1.
Acoustic Performance ResultsWhat Our Customers Have to Say
Chatham Residence
“I love the efficiency and elegance of this kitchen" — Sara Hamilton, designer at Classic Kitchens Interiors.
Visa One Market
“They love it and are extremely happy with the space. People love to walk around to soak in the view.”
West Virginia Residence: “The NanaWall sliding glass doors are transformative. It’s one thing when it’s closed, it’s a whole different experience when it's open”
— Acock Associates Architects
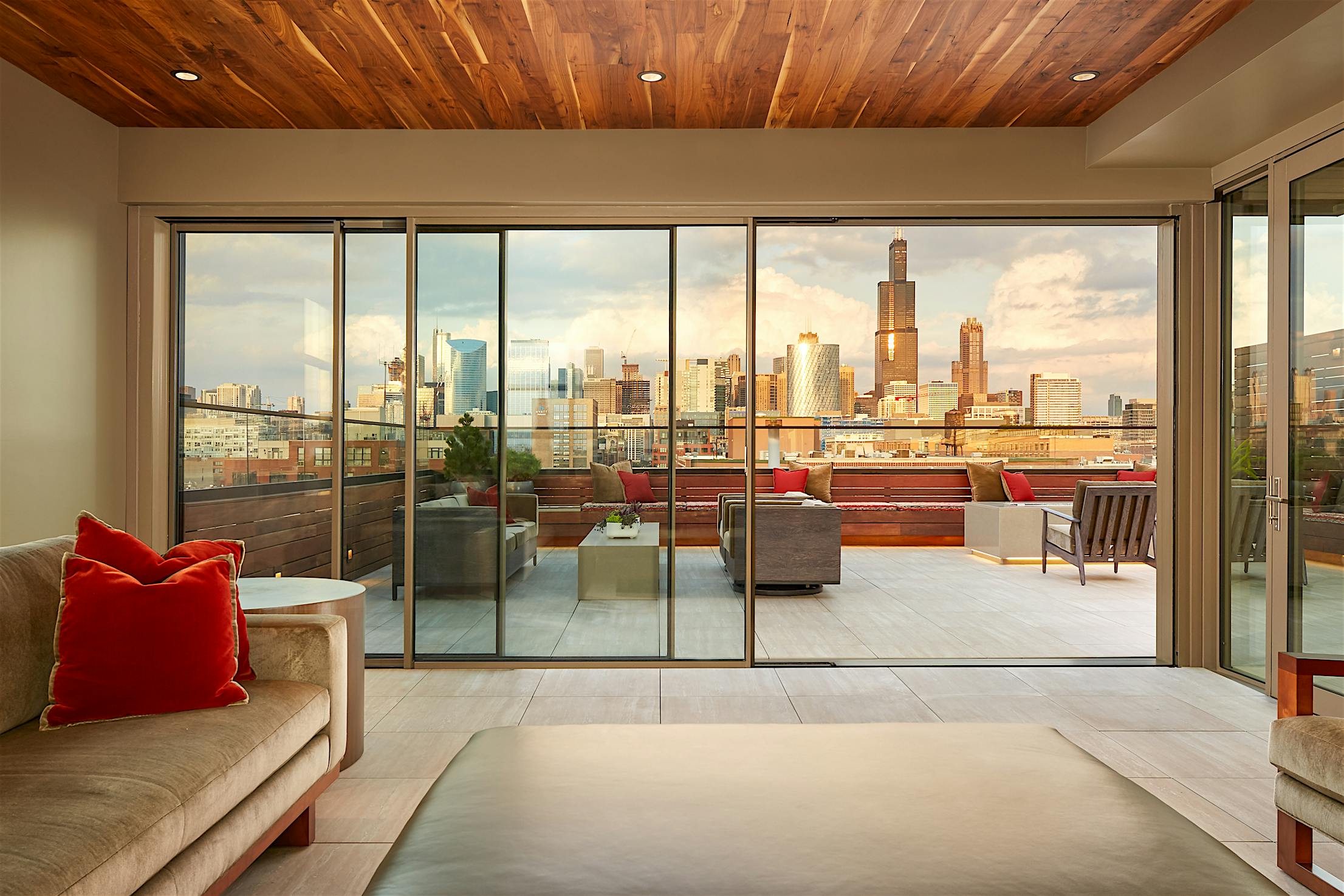
50 Standard Colors come at no additional cost, with an additional 200+ colors to choose from.
See Finish Options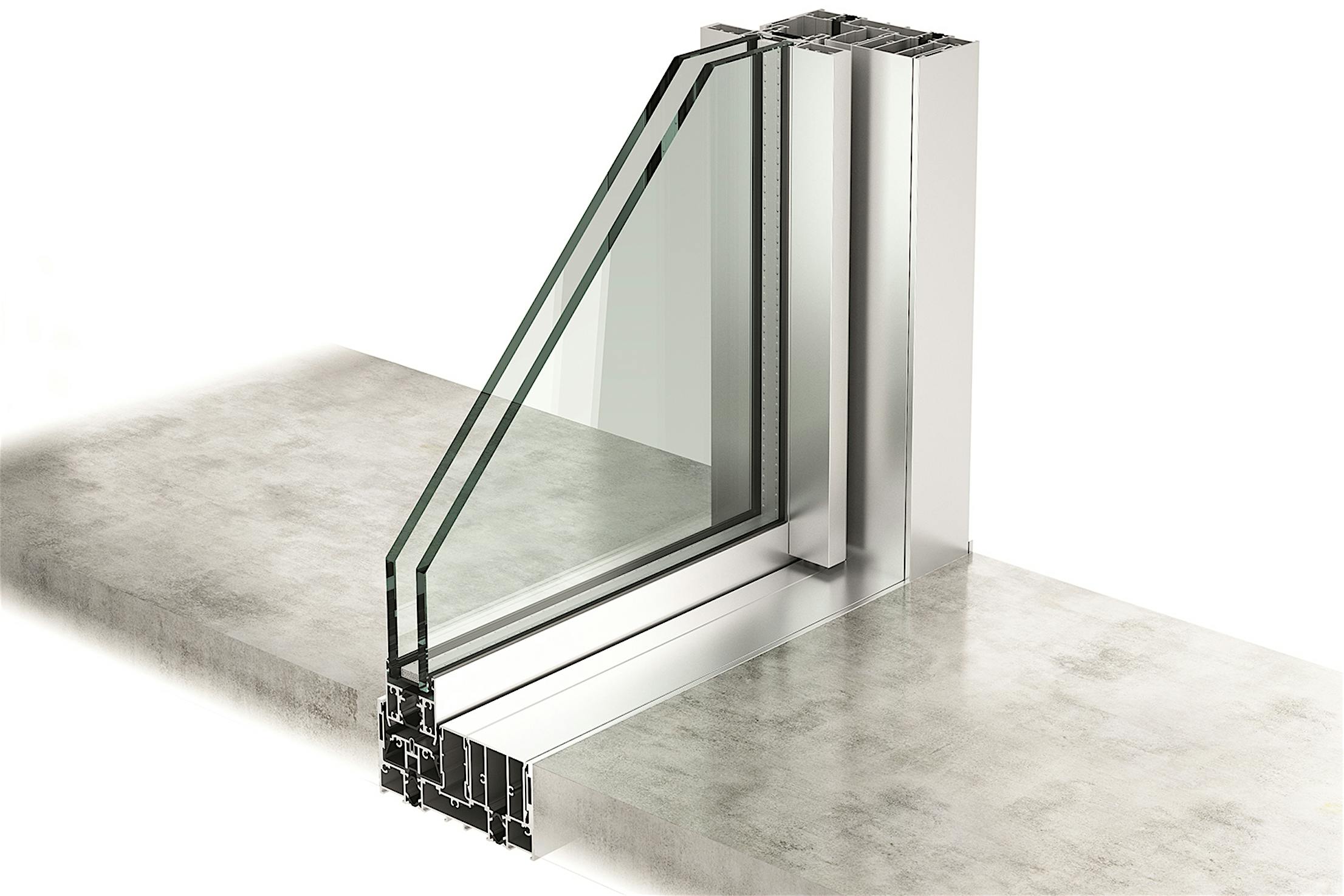
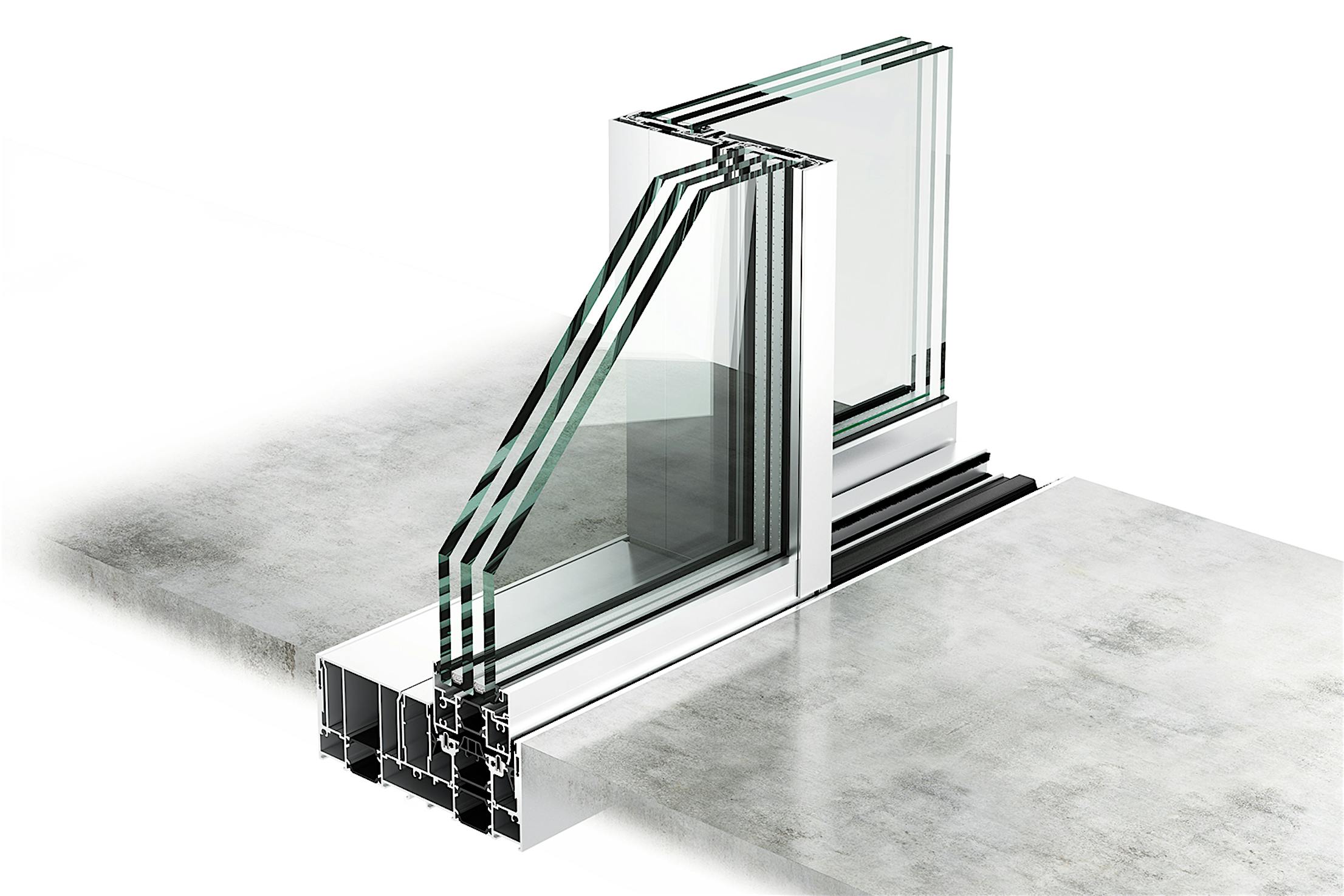
cero is available in two options depending on thermal performance needs—triple glazed cero III and double glazed cero II. All glazing is heat soaked, reduced iron (LT 89).
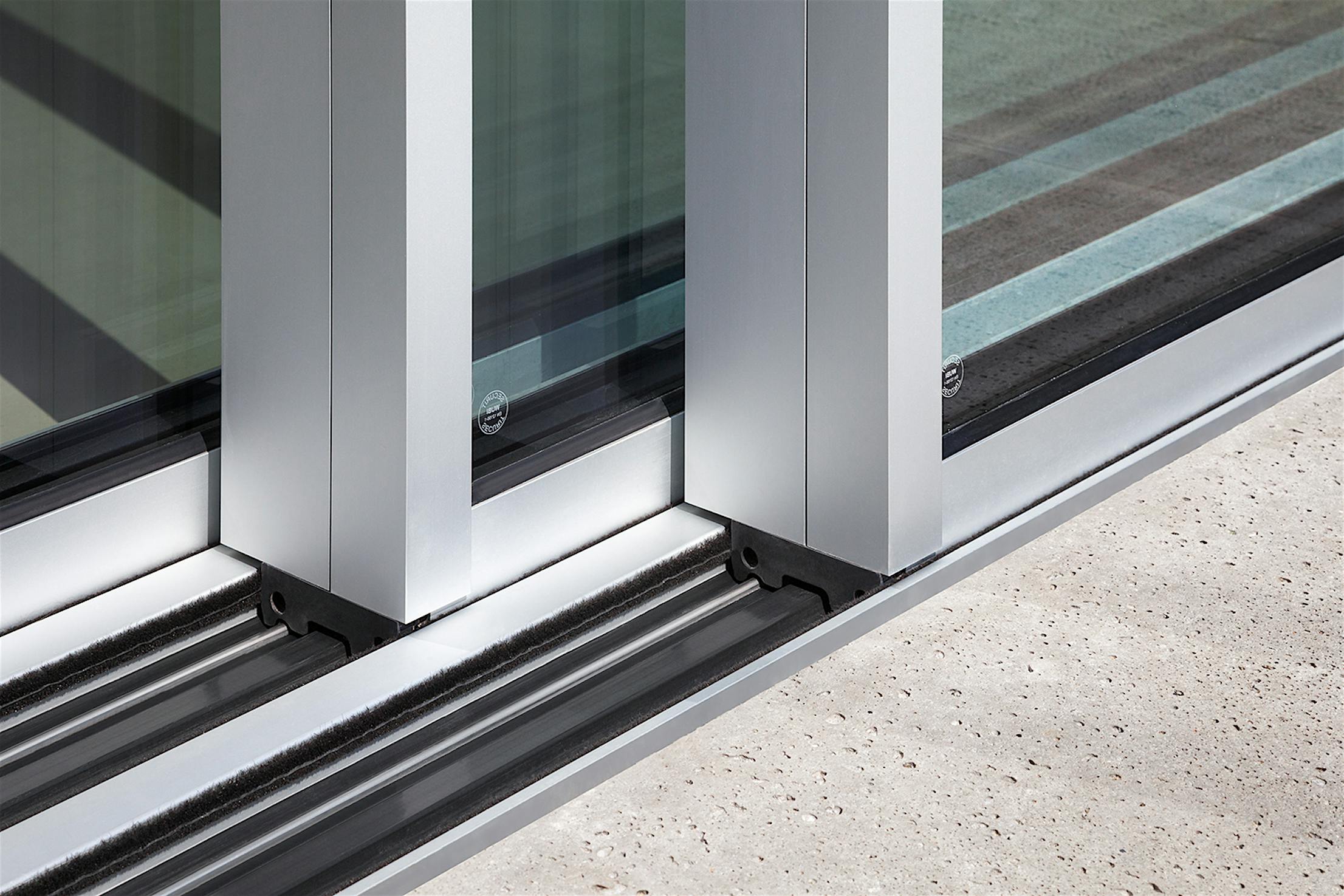
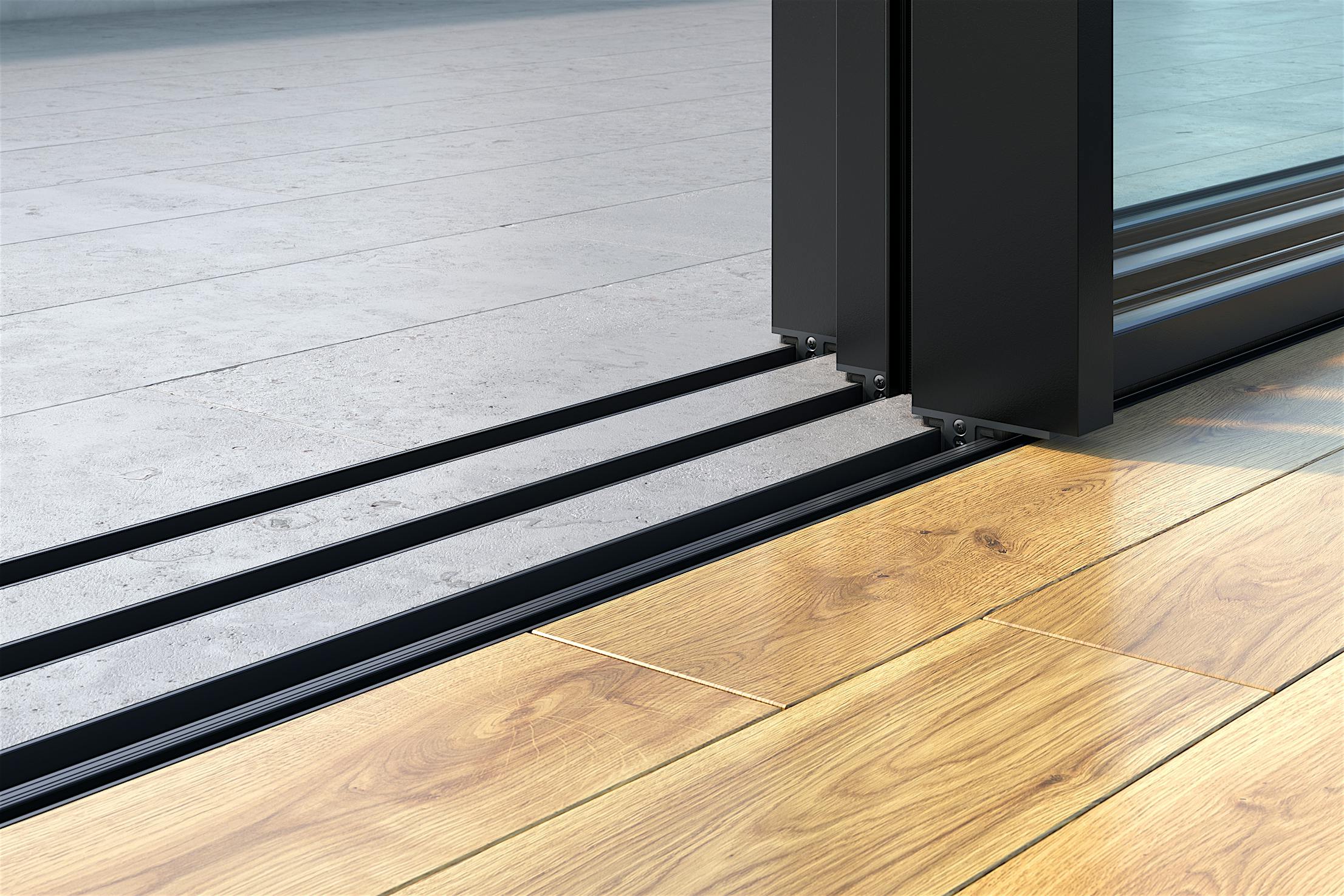
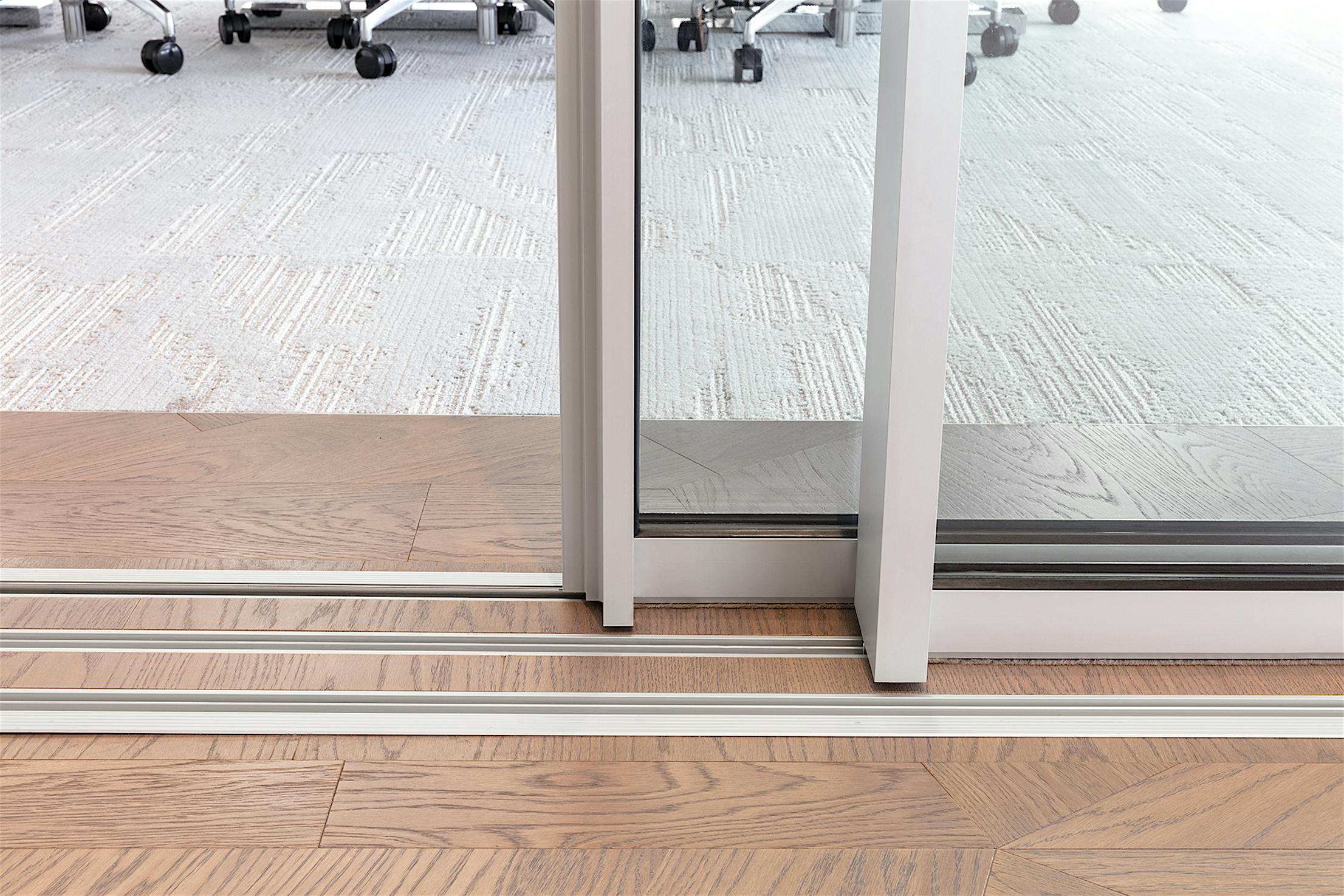
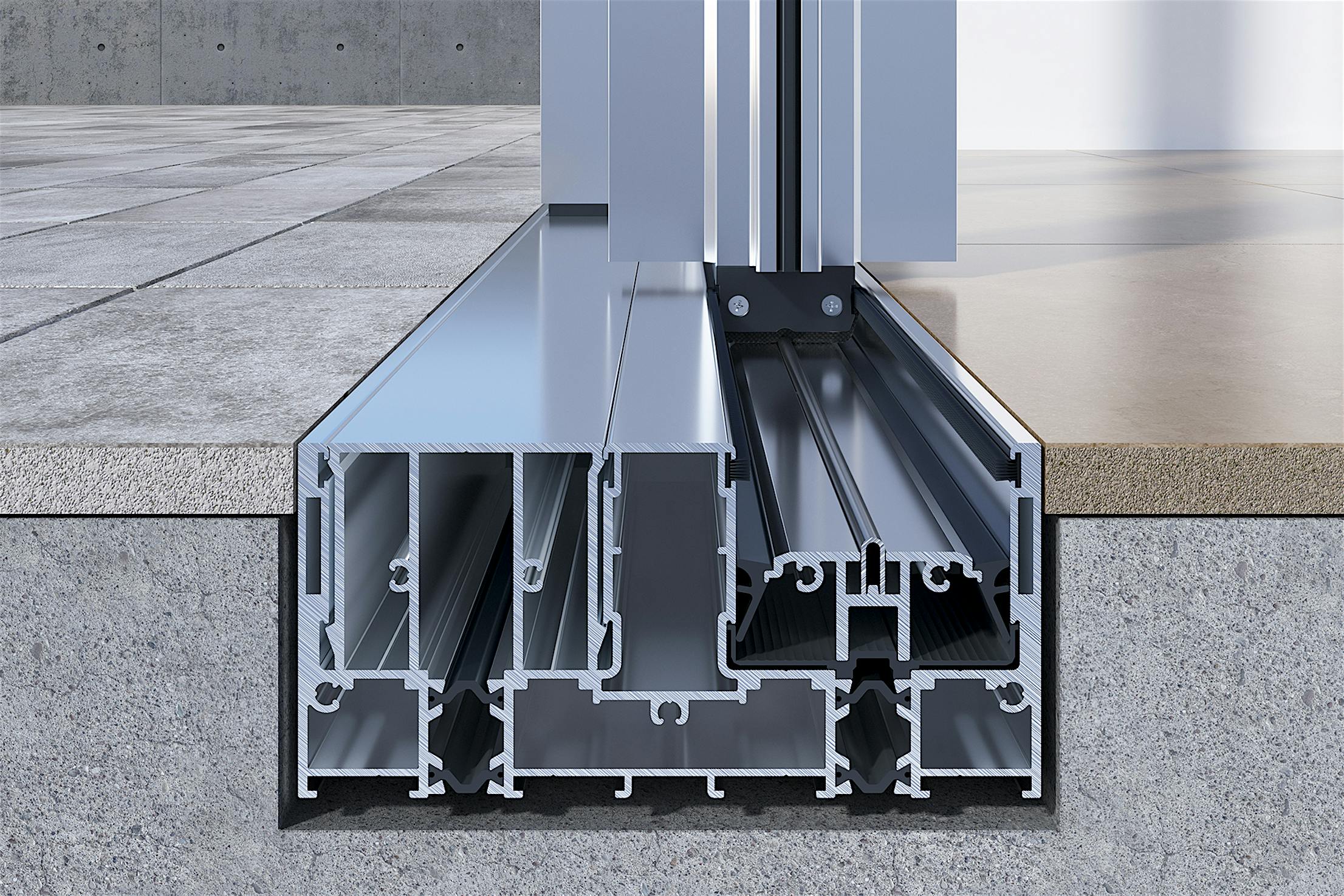
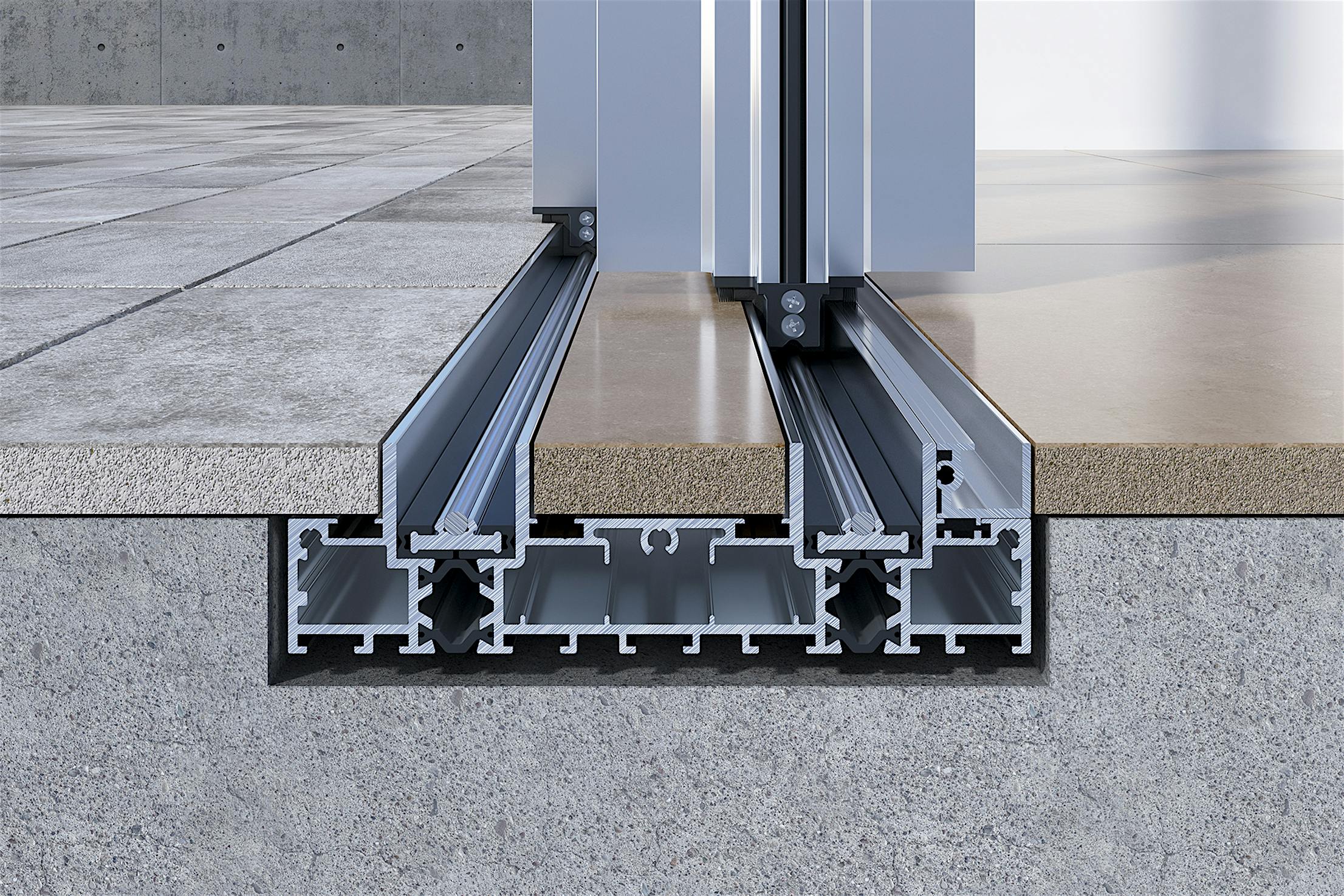
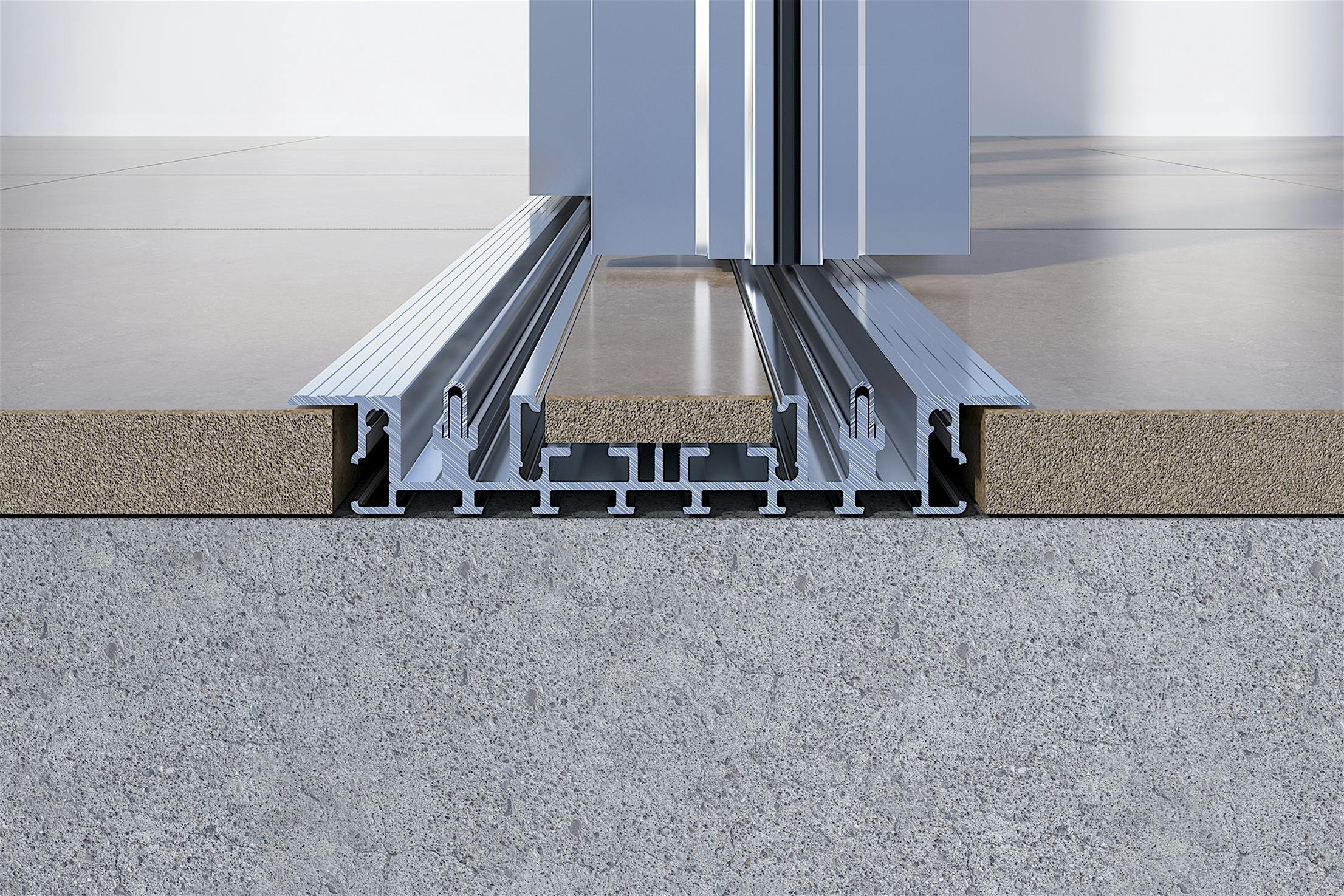
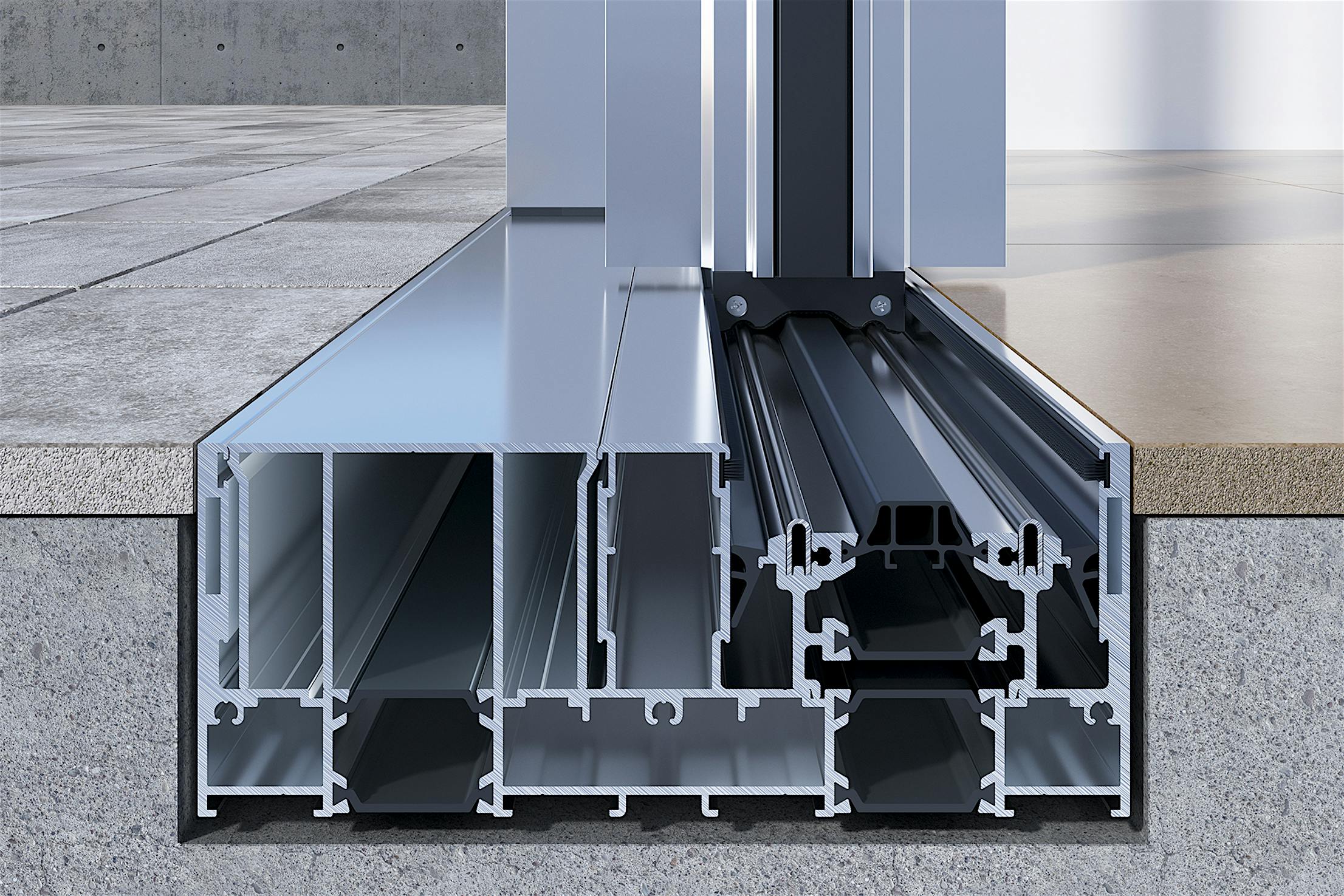
Depending on configuration, cero is available with up to seven tracks. For addition track options, please contact NanaWall. Open and fixed corners possible.
See Sill Options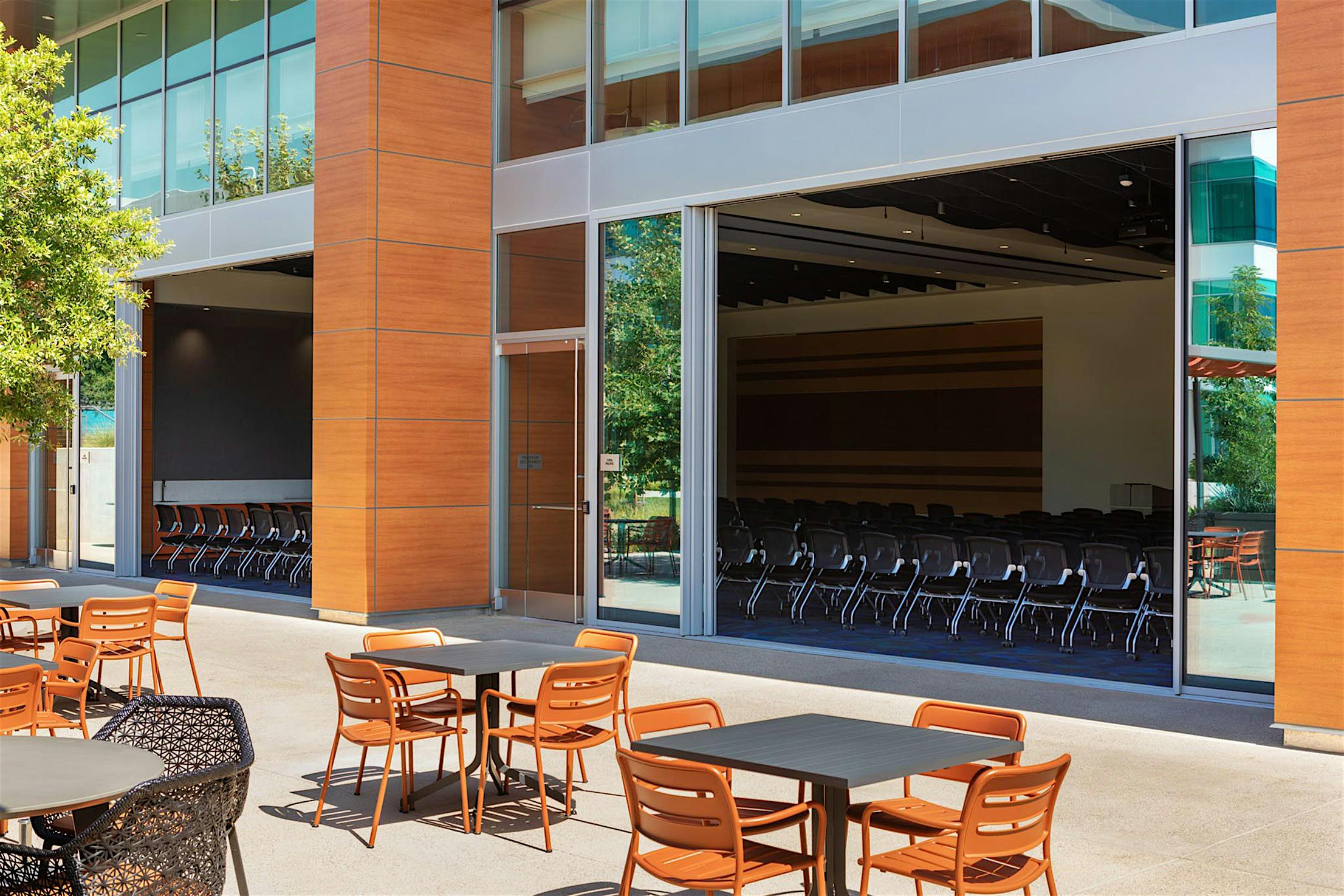
- Two-Step Safety Feature - Motion sensor provides worry free operation if people or pets walk through the opening while closing
- Magnetic Clutch - Allows for manual operation override
- Magnetic Brake - Safely secures the opening
- System Auto-lock - If cero is closed manually, the system locks automatically after one hour
- Manual Lock Detection - System knows when cero is manually locked ensuring no damage to motor or door unit
- Smart Switch - Choose between wired or wireless wall switch with phone/tablet App for ease of use
- Battery Backup - Provides 36-hour battery backup
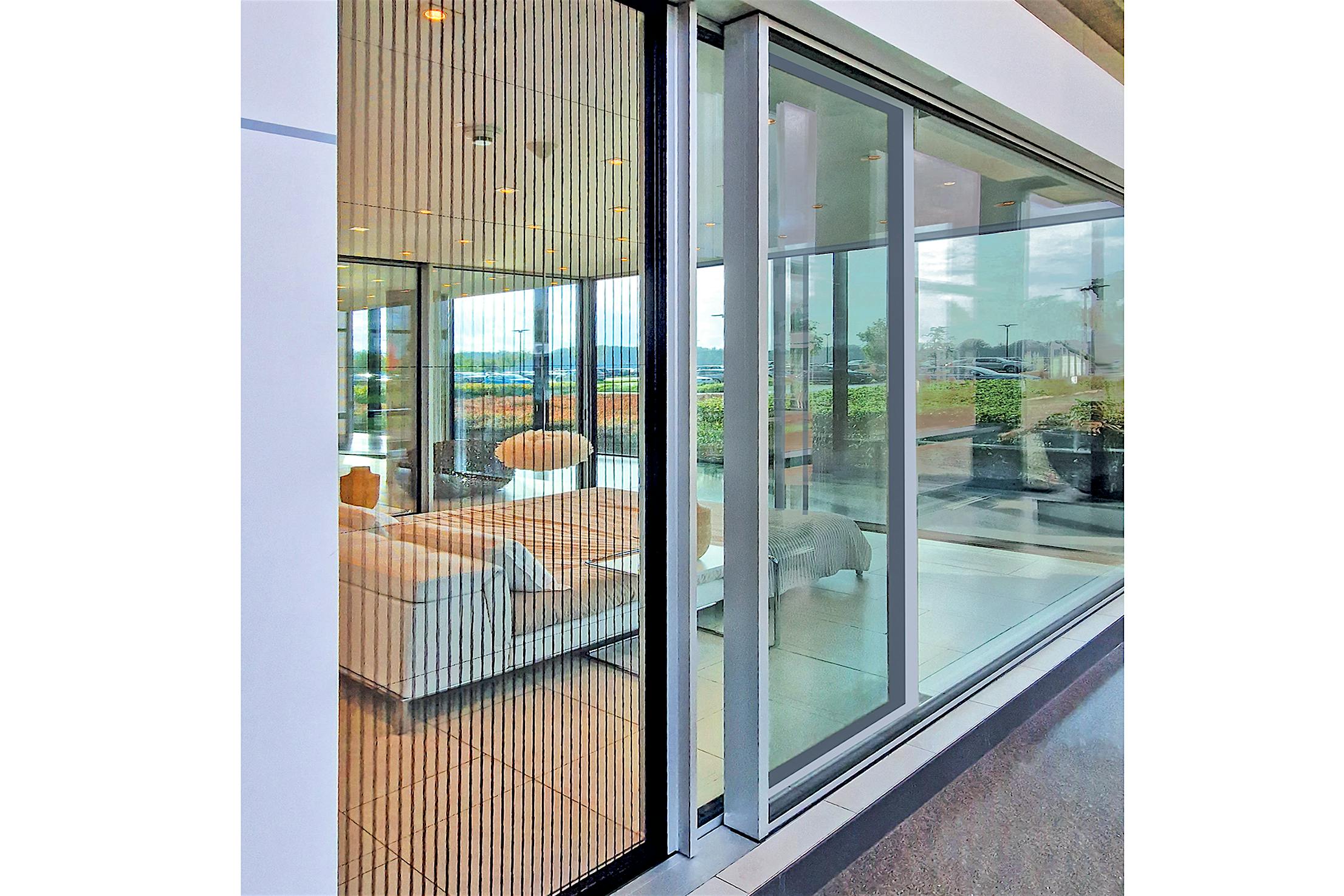
A pleated screen option is available for cero configurations that slide and meet at the jamb for units using the Performance Sill. Sizes: cero II up to 3′ 3″ x 11′ 6″ (1000 mm x 3500 mm), cero III up to 3′ 7″ x 11′ 6″ (1100 mm x 3500 mm).
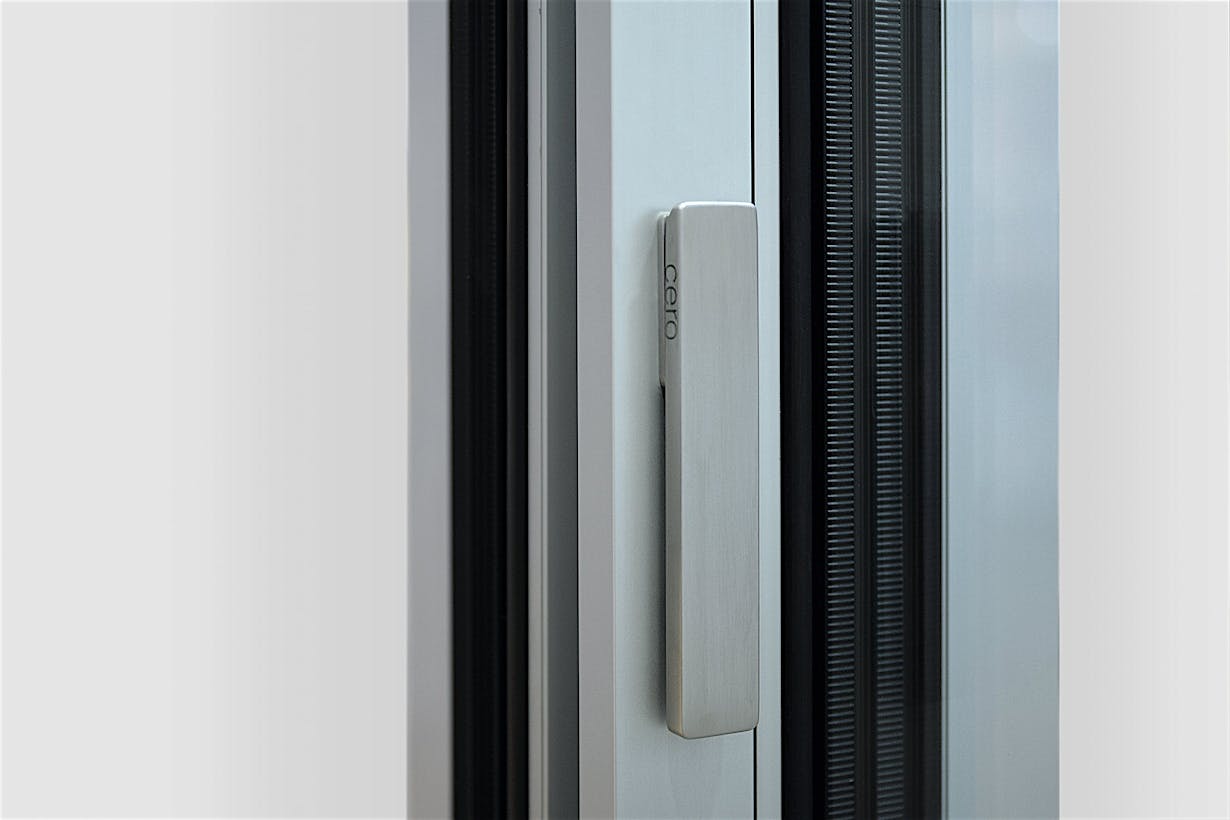
Stylish Handles Meet Security
Our stainless steel handles in two finishes are not only functional but come in a minimalist aesthetic to complement cero. The system ensures security through a two-point, tamper-resistant locking mechanism integrated into a slim 1 5/16" vertical profile stile, preserving its sleek look.
Explore cero Locking Features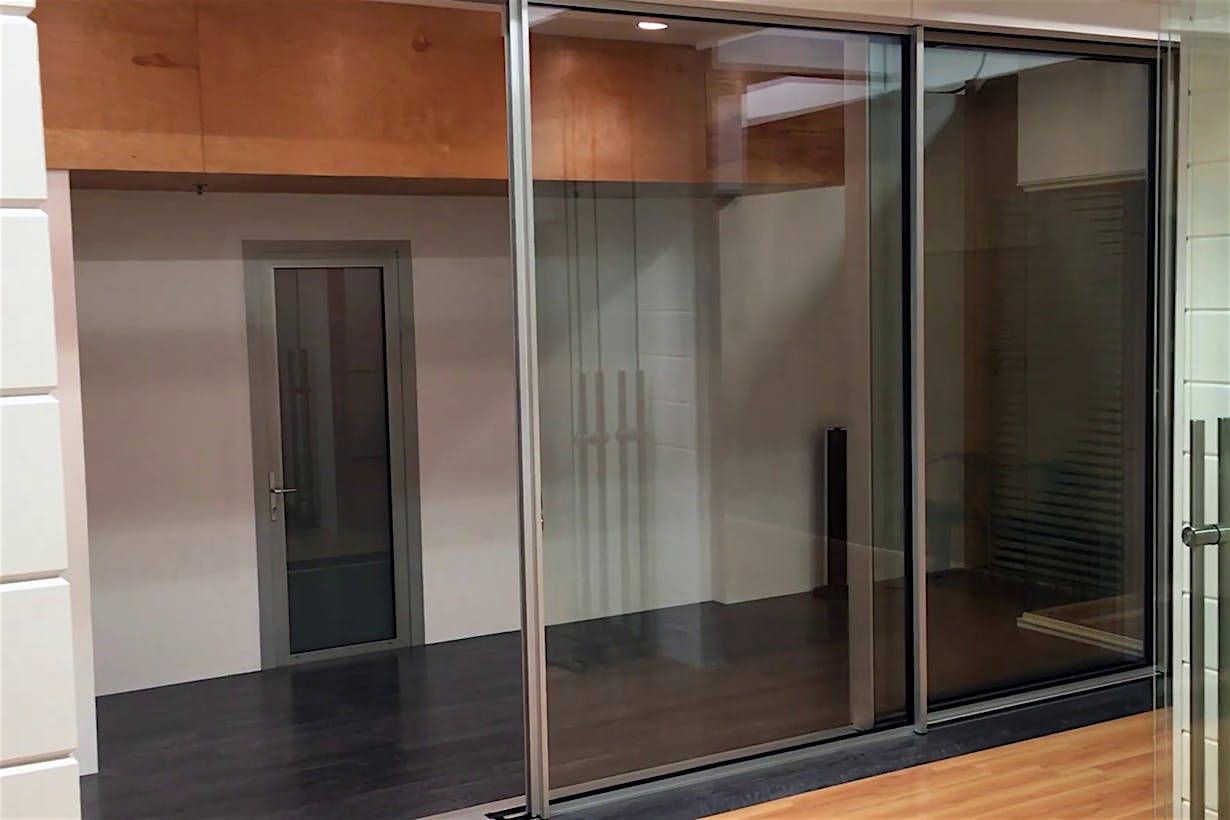
Automation for Effortless Control
cero's optional automation accessory provides effortless operation and secure locking with a simple touch of a button. This feature, supplied by others, ensures smooth, safe, and quiet operation with keypads located on the interior and/or exterior for convenience and peace of mind.
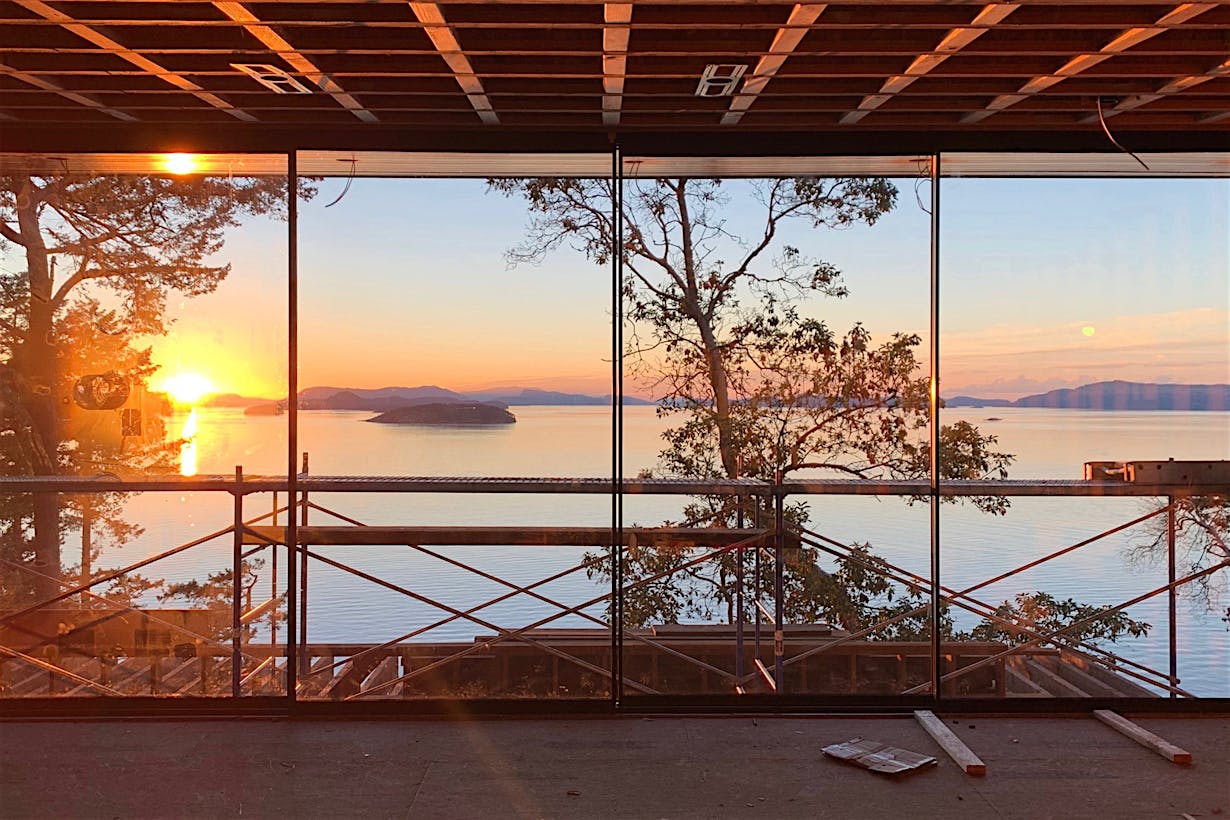
Discover Unparalleled Support
Our technical support team is here to assist in detailing large cero openings. Experienced installation managers and NanaWall certified installers across North America provide full assistance in installing large cero panels. Trust us to bring your vision to life with precision and excellence.
cero is available in numerous configurations with combinations of sliding and fixed panels. Systems are available with up to six tracks. Pocketed and open corner configurations are also available.
Explore limitless possibilities with our systems. Contact our dedicated design team for more possibilities.
More Configurations - cero II More Configurations - cero IIIExplore limitless possibilities with our systems. Contact our dedicated design team for more possibilities.
More Configurations - cero II More Configurations - cero IIIOpen corners free your space from traditional constraints, opening the door to limitless design ideas. Two open corners to create Z and U-shaped walls are also possible.
More Configurations - cero II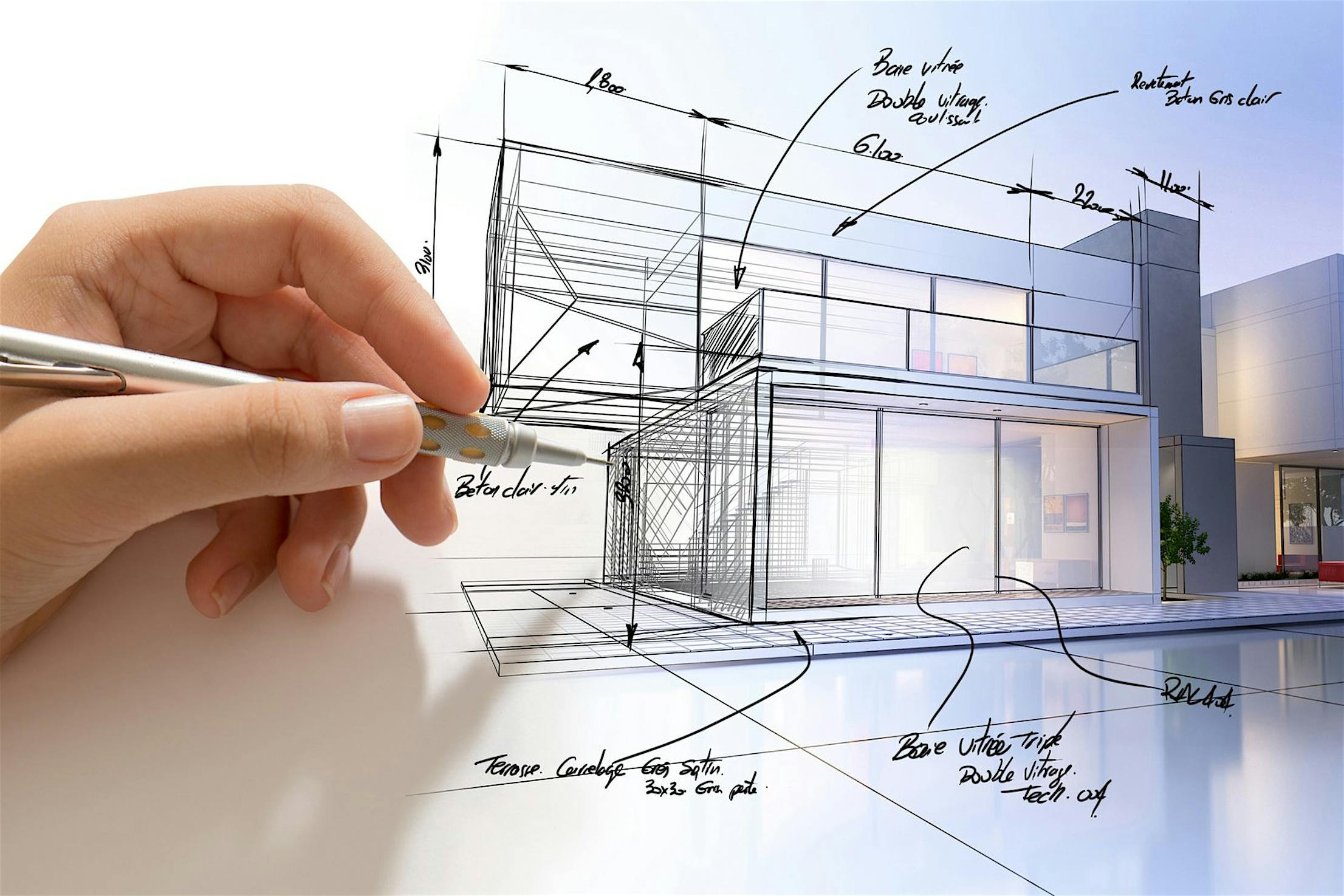
Explore limitless possibilities with our systems. Design and customize systems using our 3D CAD/Revit/Spec Configurators or contact our dedicated design team for more possibilities.
Get Design AssistanceWe consider ourselves your partners from day one. Connect immediately with a NanaWall expert to answer your questions and explore how we can support your project.
(866) 210-4285
Monday - Friday: 7 AM - 5 PM PST
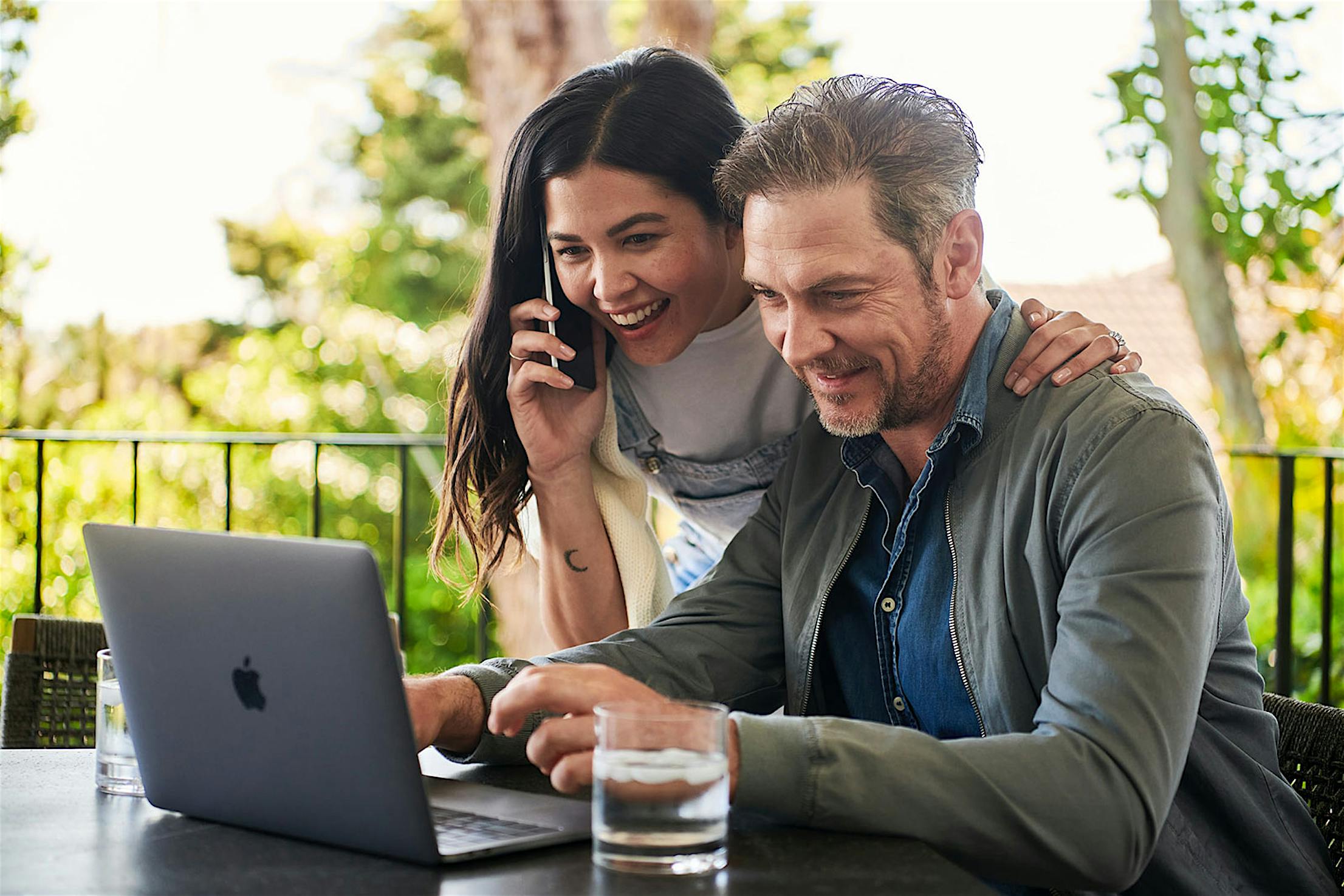
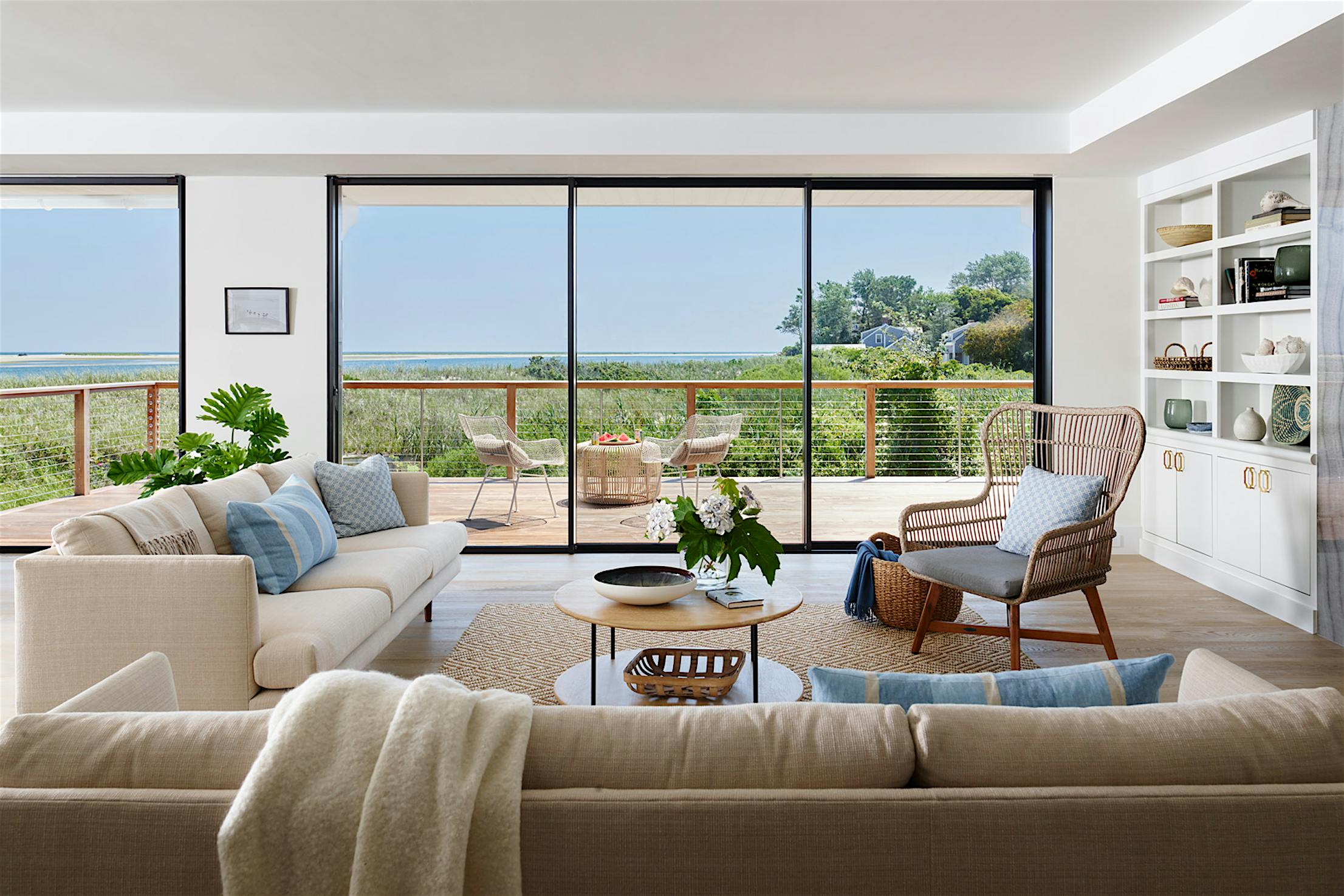
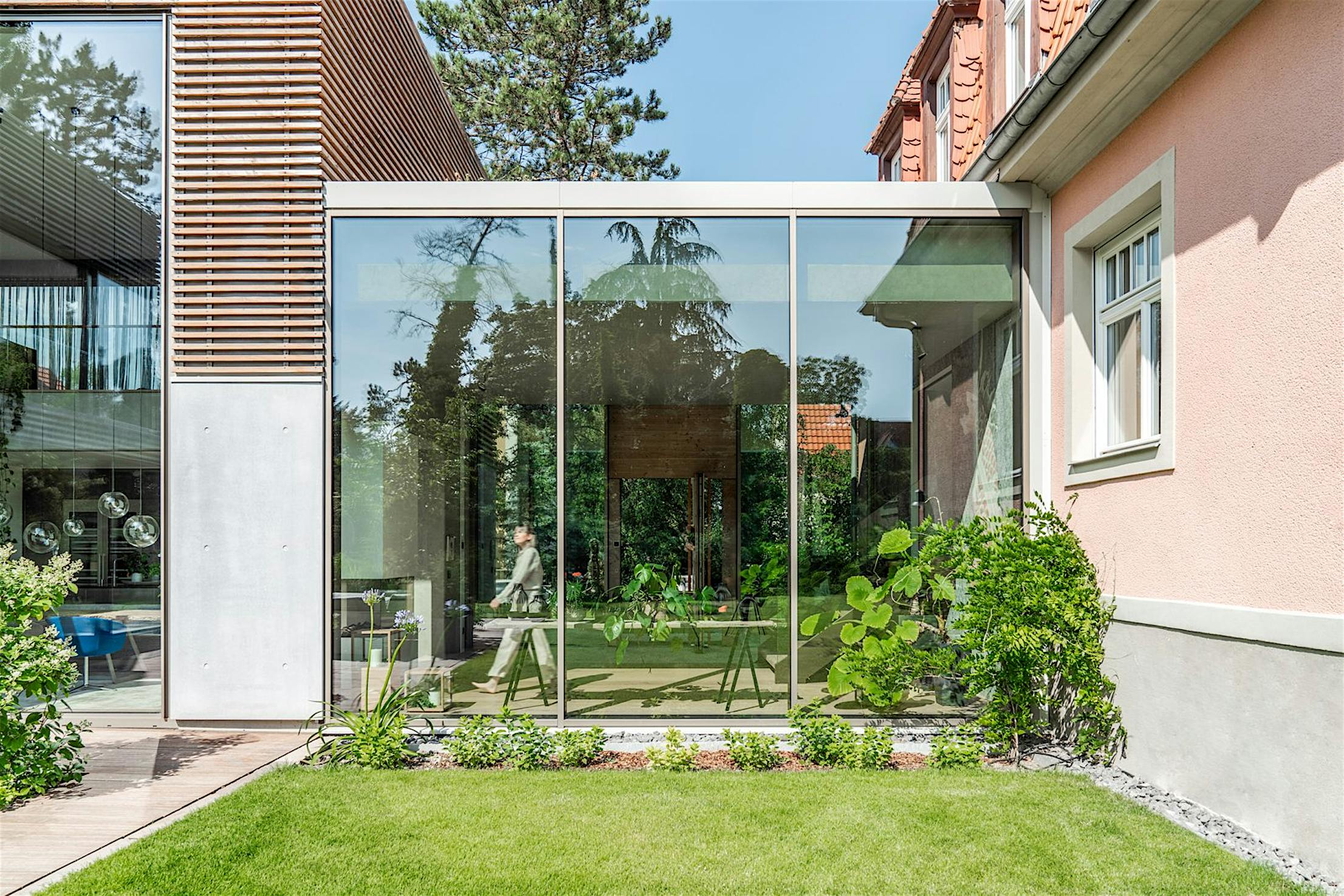
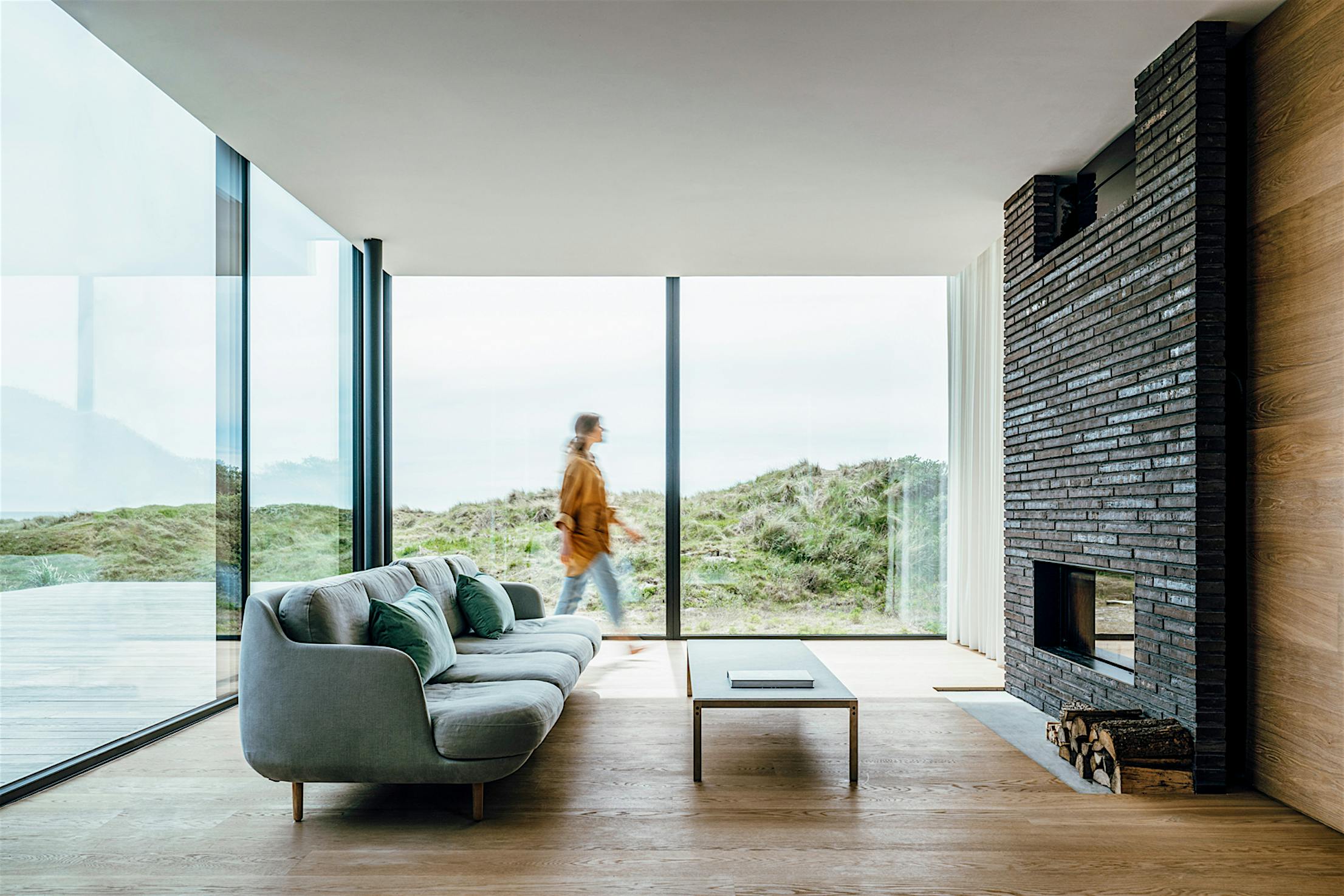